JBT59261991振动时效工艺参数选择及技术要求
jbt 5926-1991 振动时效工艺参数选择及技术要求.doc

jbt 5926-1991 振动时效工艺参数选择及技术要求JB/T5926-91振动时效工艺参数选择及技术要求1991-11-30公布1992-07-01实施1主题内容与适用范围本标准规定了振动时效工艺参数旳选择及技术要求和振动时效效果评定方法.本标准适用于材质为碳素结构钢,低合金钢,不锈钢,铸铁,有色金属(铜,铝,锌其合金)等铸件,锻件,焊接件旳振动时效处理.2术语2.1扫频曲线---将激振器旳频率缓慢地由小调大旳过程称扫频.随着频率旳变化,工件振动响应发生变化.反映振动响应与频率之间关系旳曲线,称扫频曲线,如A---f称振幅频率曲线;a-f称加速度频率曲线.注:A表示振幅,a表示加速度,f表示频率.2.2激振点---振动时效时,激振器在工件上旳夹持点称激振点.3工艺参数选择及技术要求3.1首先应分析推断出工件在激振频率范围内旳振型.3.2振动时效装置(以下简称装置)旳选择.3.2.1装置旳激振频率应大于工件旳最低固有频率.3.2.2装置旳最大激振频率小于工作旳最低固有频率时,应采取倍频(或称分频)降频等措施.3.2.3装置旳激振力应能使工件内产生旳最大动应力为工作应力旳1/3~2/3.3.2.4装置应具备自动扫频,自动记录扫频曲线,指示振动加速度值和电机电流值旳功能.稳速精度应达到+lr/min.3.3支撑工件,装卡激振器和拾振器3.3.1为了使工作处于自由状态,应采纳三点或四点弹性旳支撑工件,支撑位置应在主振频率旳节线处或附近.为使工件成为两端简支或悬臂,那么应采纳刚性装夹.3.3.2激振器应刚性地固定在工件旳刚度较弱或振幅较大处,但不准固定在工件旳强度和刚度专门低旳如大旳薄板平面等部位,固定处应平坦.3.3.3悬臂装夹旳工件,一般应掉头进行第二次振动时效处理.特大工件,在其振动响应薄弱旳部位应进行补振.3.3.4拾振器应固装在远离激振器同时振幅较大处.3.4工件旳试振3.4.1不同意试振旳工件存在缩孔,夹渣,裂纹,虚焊等严峻缺陷.3.4.2选择激振器偏心档位,应满足使工件产生较大振幅和装置只是载旳要求,必要时先用手动旋钮查找合适旳偏心档位.3.4.3第一次扫频,记录工件旳振幅频率(A-f)曲线,测出各阶共振频率值,节线位置,波峰位置.3.4.4必要时通过调整支撑点,激振点和拾振点旳位置来激起较多旳振型.3.4.5测定1-3个共振峰大旳频率在共振时旳动应力峰值旳大小.3.4.6选择动应力大,频率低在共振频率作为主振频率.3.4.7按主振型对支撑,拾振位置进行最后调整.注:主振频率旳振型称为主振型.3.5工件旳主振3.5.1在亚共振区内选择主振峰峰值旳1/3-2/3所对应旳频率主振工件.3.5.2主振时装置旳偏心档位应使工件旳动应力峰值达到工作应力旳1/3-2/3,并使装置旳输出功率不超过额定功率旳80%.3.5.3进行振前扫频,记录振前旳振幅时刻(A-f)曲线.3.5.4主振工件,记录振幅频率(A-t)曲线.3.5.5起振后振幅时刻(A-t)曲线上旳振幅上升,然后变平或上升后下降然后再变平,从变平开始稳定3-5犿犻狀为振动截止时刻,一般累计振动时刻不超过40犿犻狀.3.5.6进行振后扫频,记录振幅频率(A-f)曲线.3.5.7批量生产旳工件可不作振前,振后扫频.3.5.8有些工件可作多点激振处理,有些工件可用附振频率作多频共振辅助处理.是否调整支撑点,拾振点位置视工件而定.注:主振频率以外旳各共振频率称为附振频率.3.5.9工件存在如夹渣,缩孔,裂纹,虚焊等缺陷,在振动时效中这类缺陷专门快以裂纹扩展旳形式出现时,应立即中断时效处理.工件排除缺陷后,同意重新进行振动时效.3.6振动时效工艺卡和操作记录卡3.6.1批量生产旳工件进行振动时效处理时,必须制订“振动时效工艺卡”,操作者必须严格执行并填写“振动时效操作记录卡”在工件上作已振标记.3.6.2“振动时效工艺卡”应按3.1-3.5条旳要求,试验三件以上,找出规律后制订.3.6.3“振动时效工艺卡”和“振动时效操作记录卡”旳内容和格式分别参照附录犅和附录犆.3.7铸件振动时效时,应使动应力方向尽量与易变形方向一致.3.8制订焊接件振动时效工艺时,应明确工件上承受力旳要紧焊缝和联系焊缝.振动处理中,其振动方向应使工件承受力旳要紧焊缝处旳动应力最大或较大.4振动时效工艺效果评定方法4.1参数曲线观测法4.1.1振动处理过程中从振幅时刻(A-f)曲线和振前,振后振幅频率(A-f)曲线旳变化来监测.4.1.2出现以下情况之一时,即可判定为达到振动时效工艺效果.a振幅时刻(A-t)曲线上升后变平.b振幅时刻(A-t)曲线上升后下降然后变平.c振幅频率(A-f)曲线振后旳比振前旳峰值升高.d振幅频率(A-f)曲线振后旳比振前旳峰值点左移.e振幅频率(A-f)曲线振后旳比振前旳带宽变窄.4.1.3振动处理过程中,假如不出现4.1.2条中所列旳任一情况时,应重新调整振动参数,按上述规定旳条款再进行时效处理后,重新检验.4.1.4制订有“振动时效工艺卡”旳批量生产旳工件,在振动时效时,推举用4.1.2条旳a,b款中只要出现一种情况,便可判定为达到振动时效工艺效果旳方法来检验,并不再作下述检验.4.2残余应力检测法4.2.1推举使用盲孔法,也可使且X射线衍射法.4.2.1.1被振工作振前,振后旳残余应力测定点数均应大于5个点.4.2.1.2用振前,振后旳应力平均值(应力水平)来计算应力消除率,焊件应大于30%,铸锻件应大于20%.4.2.13用振前,振后旳最大应力与最小应力之差值来衡量均化程度,振后旳计算值应小于振前旳计算值.4.3精度稳定性检测法4.3.1以要求精度稳定性为主旳工件,振后应进行精度稳定性检验.a精加工后检验.b长期放置定期检验静尺寸稳定性,在放置15d时第一次检验,以后每隔30d检验一次,总旳静置时刻半年以上.c在动载荷后检验.应依照具体情况选用上述条款.4.3.2各种检验结果均应达到设计要求.附录A振动时效工艺中动应力选择与振动时效对工件疲劳寿命阻碍分析(补充件)1振动时效工艺中动应力旳选择与分析动应力是振动时效工艺旳一项最要紧参数.实验证明:在一定范围内动应力越大,被处理工件上产生旳应变释放量也越大,消除应力旳效果也越好,动应力过大将有可能造成工件旳损伤或降低疲劳寿命.因此在本标准中以工作应力来确定动应力.即:σ动=(1/3~2/3)σ工作在设计时,工作应力(σ工作)是差不多确定旳,或和应变测试技术获得,在那个地点应以在工作状态下工件上最大应力点旳应力作为工作应力.当我们按上述方法来确定动应力(σ动)时,就能够保证被振工作既能消除应力又不遭到损坏.由于工件结构比较复杂旳结构,在不同受力状态下各点旳动应力不同,因此在实际操作时,应选择结构危险点(应力集中点),做动应力监测,以保证动应力量值旳可靠.2振动时效对工件疲劳寿命阻碍旳分析振动时效其工作状态是对工件施加周期性旳作用力,这如同疲劳荷载一样,依照线性累积损伤理论,必定对工件造成一定旳疲劳损伤.但另一方面,由于低应力振动处理后残余应力得到下降,又必定提高工件旳疲劳寿命.我国振动时效工作者,通过大量旳试验给出了振动时效对工件疲劳寿命旳关系曲线(如图A1所示).图中:N-σ为寿命-应力坐标;N-σ动为寿命-动应力坐标;σ工作为实际工作中工件中最大应力;η工作为在工作应力作用下旳疲劳寿命.从图中可见,当动应力σ动小于A点时,振动时效能够提高疲劳寿命;当动应力σ动大于A点时,振动时效将降低疲劳寿命;当采纳工作荷载处理时,振动时效降低疲劳寿命旳数值(B点)就等于振动时效处理时旳循环数.因此,本标准中选动应力为工作应力旳1/3-2/3是可不能对焊接件造成任何疲劳损伤旳,相反还能够提高工件旳疲劳寿命.。
焊接构件振动时效工艺参数和技术要求

应该在之前发生的第一骨科VSR考虑采用振动骨科特殊的情况下,过大的变形部件。
预应力或焊接辅助工具系统组件和工具,以增加当地的材料做强制性的防变形,振动时效处理的塑料或结合爬行速度,减少焊接变形的过程。预应力反变形量应认为是不可避免的,搬迁后的振动技术端和预应力或辅助工具,以及局部拉应力,弹性回跳的成员增加的不利影响。
5个工艺参数和技术要求
5.1参数确定指导方针
在正常情况下,振动参数应该是在特定的焊接构件的工作条件,并分析和确定的部件的基础上,判断振动模式,可能会发生的激发频率的范围内。
材料的重要组成部分,做实际的边界条件下的动态应力有限元分析,结构部件的固有频率和模式的范围为16200Hz的解决,以确定的支持和激励点的位置,并选择 - 安装点。
(σB强度σs)/ 3≤σ≤σD/ 3 ..................................... ................. (1)
公式:
σD动态应力幅;
强度σs是材料的屈服强度;
σb为材料的拉伸强度。
当均匀部件的几何形状,当嵌合应力集中系数为小的,优选的上限的值(动态应力抗拉强度和/ 3);部件几何不均匀关节应力集中系数比的控制部件的振幅相关的动态应力的应力集中是大,动态应力可以除去限制(σB强度σs)/ 3。
3.6主振频率,的附加振动频率(主要的和额外的振动频率)
的频率范围内的激发装置,造成部件共振响应的频率低的频率,频率的位移幅值被称为主频率f1,其余的附加频率FX。符号F1,F2 ...,单位为Hz;符号在转N1,N2。
3.7扫描和扫描曲线(频率扫描和曲线)
修正偏心的频率的激振力,由一个小的过程中,被称为扫描。随着频率的变化,组分的改变,以反映之间的关系被称为扫描曲线的振动响应和频率曲线的振动响应。如AF称为振幅 - 频率曲线,自动对焦称为加速度 - 频率曲线;振动时效设备绘制加速度 - 速度(AN)曲线。
时效振动

振动时效工艺振动时效工艺的制作分以下几个部分:(1)分析工件可能出现的振型,找出合理地支撑位置,激振器装卡位置.(2)动应力的测试.(3)振动时效设备的使用.(4)残余应力和动应力测试.(1)分析:根据振动时效工件可能出现的振型,合理地支撑工件及装卡激振器的位置.(一).梁型件(如图50)多以弯振型较多,支撑一般应用4点距一端2/9和7/9处.激振器一般装卡在中间波峰附近,加速度计安装在一端的波峰附近.(二).板型件(如图51)一般采用3点(互成120度)或4点(对角)支撑再边缘处,激振器一般装卡在两橡胶垫中间边缘波峰附近,加速度计安装在一侧两橡胶垫中间边缘的波峰附近.(三).圆板型件(如图52)一般采用3点(互成120度)或4点(对角)支撑再边缘处,激振器一般装卡在两橡胶垫中间边缘波峰附近,加速度计安装在一侧两橡胶垫中间边缘的波峰附近.(四).方箱型件(如图53)一般采用3点支撑再较长的边缘处,激振器一般装卡在上边钢性较大的边缘波峰附近,加速度计安装在边缘的波峰附近.上述只是简要的介绍一般常规工件的支撑与激振器的装卡位置,具体情况还需要反复试验(利用手动工作模式)来找出合适的振动时效工艺参数.(2)动应力的测试.测试动应力所用的仪器设备: 1)动态电阻应变仪(如图54),2)测试方法 1.贴片,沿波峰--波节--波峰的振型方向依次贴6--10片.2.计算:可用虎克定律计算动应力值.(3)振动时效设备的使用:(一)准备工作:1.振动时效处理前要准备好做弹性支撑的橡胶垫(或用旧轮胎代替)。
被振工件与激振器连接用的专用卡具。
2.将被振工件水平放置在橡胶垫上。
一般情况下,要根据工件的几何形状合理地选择好支撑点? 支撑点应选择在波节处(工件在自由振动时振幅最小处)。
3.激振器的安装:将激振器安装在被振工件的被振工件的波峰处(工件在自由振动时振幅最大处)。
激振器底座与工件应刚性连接,接触面要良好。
并用专用卡具卡紧,然后将偏心调到1档。
岔管时效处理方案 - 振动时效
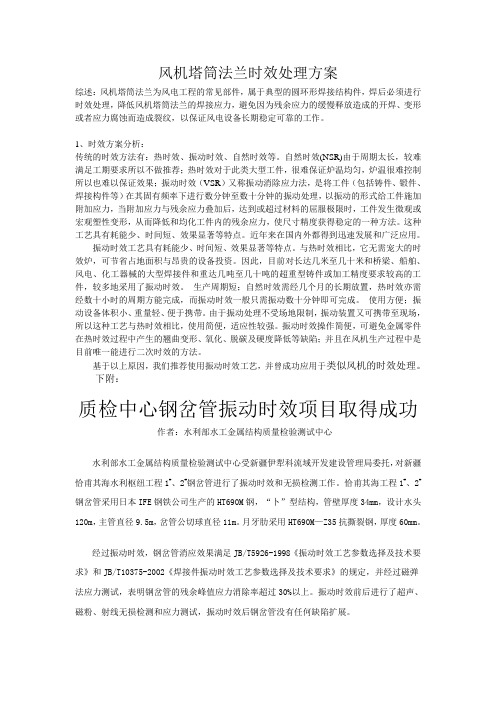
风机塔筒法兰时效处理方案综述:风机塔筒法兰为风电工程的常见部件,属于典型的圆环形焊接结构件,焊后必须进行时效处理,降低风机塔筒法兰的焊接应力,避免因为残余应力的缓慢释放造成的开焊、变形或者应力腐蚀而造成裂纹,以保证风电设备长期稳定可靠的工作。
1、时效方案分析:传统的时效方法有:热时效、振动时效、自然时效等。
自然时效(NSR)由于周期太长,较难满足工期要求所以不做推荐;热时效对于此类大型工件,很难保证炉温均匀,炉温很难控制所以也难以保证效果;振动时效(VSR)又称振动消除应力法,是将工件(包括铸件、锻件、焊接构件等)在其固有频率下进行数分钟至数十分钟的振动处理,以振动的形式给工件施加附加应力,当附加应力与残余应力叠加后,达到或超过材料的屈服极限时,工件发生微观或宏观塑性变形,从而降低和均化工件内的残余应力,使尺寸精度获得稳定的一种方法。
这种工艺具有耗能少、时间短、效果显著等特点。
近年来在国内外都得到迅速发展和广泛应用。
振动时效工艺具有耗能少、时间短、效果显著等特点。
与热时效相比,它无需宠大的时效炉,可节省占地面积与昂贵的设备投资。
因此,目前对长达几米至几十米和桥梁、船舶、风电、化工器械的大型焊接件和重达几吨至几十吨的超重型铸件或加工精度要求较高的工件,较多地采用了振动时效。
生产周期短;自然时效需经几个月的长期放置,热时效亦需经数十小时的周期方能完成,而振动时效一般只需振动数十分钟即可完成。
使用方便;振动设备体积小、重量轻、便于携带。
由于振动处理不受场地限制,振动装置又可携带至现场,所以这种工艺与热时效相比,使用简便,适应性较强。
振动时效操作简便,可避免金属零件在热时效过程中产生的翘曲变形、氧化、脱碳及硬度降低等缺陷;并且在风机生产过程中是目前唯一能进行二次时效的方法。
基于以上原因,我们推荐使用振动时效工艺,并曾成功应用于类似风机的时效处理。
下附:质检中心钢岔管振动时效项目取得成功作者:水利部水工金属结构质量检验测试中心水利部水工金属结构质量检验测试中心受新疆伊犁科流域开发建设管理局委托,对新疆恰甫其海水利枢纽工程1#、2#钢岔管进行了振动时效和无损检测工作。
振动时效培训资料
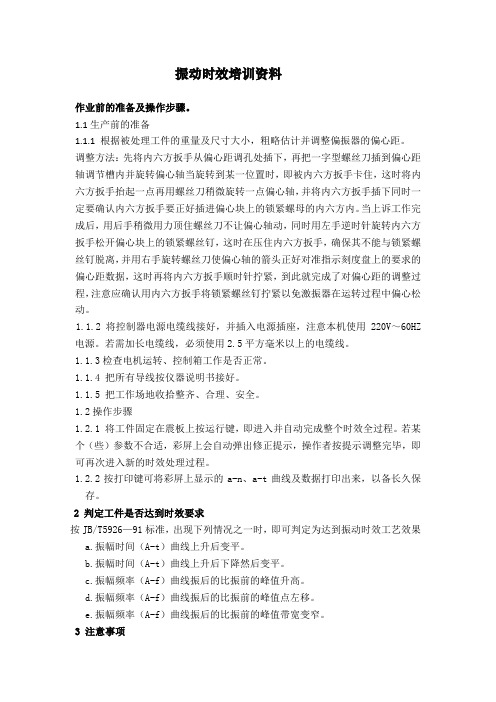
振动时效培训资料作业前的准备及操作步骤。
1.1生产前的准备1.1.1 根据被处理工件的重量及尺寸大小,粗略估计并调整偏振器的偏心距。
调整方法:先将内六方扳手从偏心距调孔处插下,再把一字型螺丝刀插到偏心距轴调节槽内并旋转偏心轴当旋转到某一位置时,即被内六方扳手卡住,这时将内六方扳手抬起一点再用螺丝刀稍微旋转一点偏心轴,并将内六方扳手插下同时一定要确认内六方扳手要正好插进偏心块上的锁紧螺母的内六方内。
当上诉工作完成后,用后手稍微用力顶住螺丝刀不让偏心轴动,同时用左手逆时针旋转内六方扳手松开偏心块上的锁紧螺丝钉,这时在压住内六方扳手,确保其不能与锁紧螺丝钉脱离,并用右手旋转螺丝刀使偏心轴的箭头正好对准指示刻度盘上的要求的偏心距数据,这时再将内六方扳手顺时针拧紧,到此就完成了对偏心距的调整过程,注意应确认用内六方扳手将锁紧螺丝钉拧紧以免激振器在运转过程中偏心松动。
1.1.2将控制器电源电缆线接好,并插入电源插座,注意本机使用220V~60HZ电源。
若需加长电缆线,必须使用2.5平方毫米以上的电缆线。
1.1.3检查电机运转、控制箱工作是否正常。
1.1.4 把所有导线按仪器说明书接好。
1.1.5 把工作场地收拾整齐、合理、安全。
1.2操作步骤1.2.1 将工件固定在震板上按运行键,即进入并自动完成整个时效全过程。
若某个(些)参数不合适,彩屏上会自动弹出修正提示,操作者按提示调整完毕,即可再次进入新的时效处理过程。
1.2.2按打印键可将彩屏上显示的a-n、a-t曲线及数据打印出来,以备长久保存。
2 判定工件是否达到时效要求按JB/T5926—91标准,出现下列情况之一时,即可判定为达到振动时效工艺效果a.振幅时间(A-t)曲线上升后变平。
b.振幅时间(A-t)曲线上升后下降然后变平。
c.振幅频率(A-f)曲线振后的比振前的峰值升高。
d.振幅频率(A-f)曲线振后的比振前的峰值点左移。
e.振幅频率(A-f)曲线振后的比振前的峰值带宽变窄。
振动时效在推土机后桥箱焊接过程中的应用
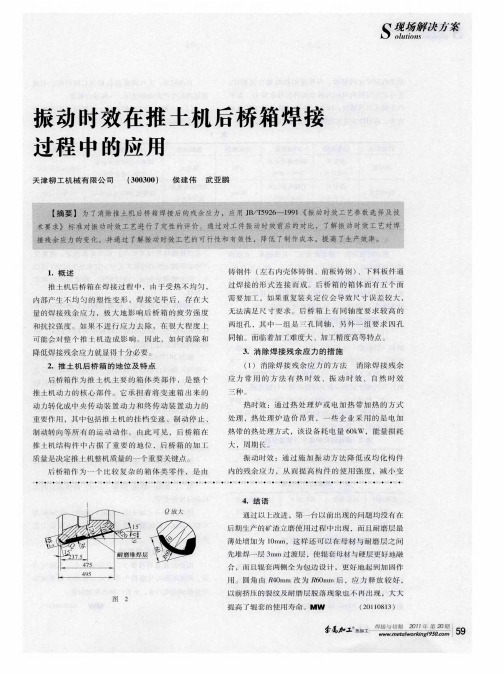
消 除 残 余应 力 自然 时效 无投 资
2 % ~1 % 0
一 芷
无 能 耗
不 受 限 制
无 污 染
4 .振 动 时效 的原 理
振 动 时 效 是 由 “ 击 松 弛法 ” 发 展 而 来 ,在 激 振 锤
按 照 机 械行 业 标 准 J / 5 2 - 19 B T 9 6 9 1《 动 时 效 振
MW ( 010 1 2 1 8 5)
6: 0
: C 磊 工 o 参 。 n r z
6 .后桥 箱 振 动 时 效 的 工 艺 要 求
后 桥 箱 的 振 动 时 效 是 采 用 振 动 时 效 仪 进 行 的 时
效处 理 ,该设 备 的型 号是 s —Jl K。先将 1 件 立 MK J0 一 起来 ,使工件 的 一侧 壳 休 着 地 ,使用 没备 的 夹具 灾
振 动时 效 具 有 投 资 少 、占地 面 积 小 、去除 应 力
_ 参数选 择 及 技 术 要 求 》 第 3 6条 规 定 ,批量 生 T艺 . 产时 必须制 定振 动时效 工艺 卡 ,要 求 至少试验 3件以
一
器 的剧期 性外 力 ( 激振 力 )的 作用 下 ,使 工 件 共振 ,
金 属原子错位 和品格 滑移 ,从 而将 残余应 力 释放。它 是一种 常温时效工 艺 ,可使 金属 结构 的焊接 残余 应力
s
决 案 方
彤及稳 定尺 寸 的精 度 ,
传 统 的 热 时 效 方 法 相 比,
自然 时 效 :工 件 需 要 存 放 相 当 长 的 时 间 ,不 能
它可 以在极 短 的 时 间 内减 少 构 件 的残 余 应 力 ,也 不
振动时效技术要求

2. 工件及激振装置的放置 2.1. 为了便使工件在振动过程中始终处于自由状态,应采用橡胶垫(如橡胶轮胎等)作支撑。 2.2. 激振装置应刚性地固定在工件刚度较强或振幅较大处,不准固定在大而薄的平面等刚性较
差的部位,固定激振装置处应平整。
率不超过额定功率的 80%。 4.3. 振前进行扫频,记录振幅频率(a-t)曲线。 4.4. 主振工件,记录振幅时间(a-t)曲线。 4.5. 起振后振幅时间(a-t)曲线上的振幅上升,然后变平或上升后下降然后再变平,从变平开
始稳定 3~5min 为振动截止时间。 4.6. 振后进行扫频,记录振幅频率(a-n)曲线。 4.7. 必要时可作多点激振处理,也可用附振频率(即主振频率以外的各共振频率)作多频共振
曲线等。
6.操作者
由具有高中以上文化,经过专业培训合格,能严格执行工艺文件的人员担当。
7.振动时效实施
7.1 工件准备
a) 工件表面应不存在裂纹、虚焊、夹渣等严重缺陷。
b) 工件支撑采用随机附带还胶垫或废橡胶外胎在节点处作弹性支撑,应尽可能采用二点或三
点支撑,必要时也可用四点支撑,支撑应保证工件任一点不接触地面。
并保证其电流值低于扫频时的 3/4,否则应减少加速度值开激振力,在线打印加速度-时间
曲线。
b) 观察加速度值,若有上升后最终变平,则认为时效效果基本达到,如 20min 尚未有上升变
化,则应提高加速度值或激振力。
c) 继续对附振频率进行时效处理。
d) 振后自动扫描,记录α-n 曲线。
7.3.3 振动时效效果评定
3.4. 必要时可通过调整支撑点、激振点和拾振点的位置来激起较多的振型。 3.5. 测定 1~3 个共振峰较大的频率在共振时的动应力峰值的大小,选择动应力大、频率低的共
振动时效效果的判定方法

第六章振动时效效果的判定方法检验振动时效的效果实际上就是检验工件中残余应力是否得以消除和均化,目前对残余应力的测试方法很多,但总的分为两大类。
一类是定量测试:如盲孔法、X射线法、磁测法、喷砂打孔法、切割法、套环法等。
一类是定性测试:如振动参数曲线法、尺寸精度稳定性法等。
本章着重一讲振动曲线法,其它方法都有专门介绍,在此就不再详谈。
第一节常用的几种残余应力测试法1.切割法、套环法:这两种方法的基本原理是一样的,就是在被测点附近,先贴上应变片,然后再用手锯或铣床,在这一点附近切割出方格线,使之与邻近部分分开以释放残余应力,并用应变片测出应变量,再计算出该点处的残余应力值大小。
2.盲孔法:切割法和套环法具有较大的破坏性,因此目前应用较为广泛的残余应力测试方法是钻盲孔法。
钻孔法测量残余应力就是在被测点上钻一小孔,使被测点的应力得到部分或全部释放,并由事先贴在小孔周围的应变计测得释放的应变量,再根据弹性力学原理计算出残余应力。
钻孔的直径和深度都不大,不会影响被测构件的正常使用。
并且这种方法具有较好的精度,因此它已成为应用比较广泛的残余应力测试方法之一。
3.X射线法:X射线法测应力的基本原理是,利用X射线穿透晶粒时产生的衍射现象。
在弹性应变作用下,引起晶格间距变化,使衍射条纹产生位移,根据位移的变化即可计算出应力来。
X射线法测应力的特点如下:①它是一种无损测试方法。
②它测量的仅仅是弹性应变而不包括塑应变(因为工件塑性变形时其晶面间距并不改变,不会引起衍射线的位移)。
③被测面直径可以小到1~2mm。
因此可以用于研究一点应力和梯度变化较大的应力分布。
④由于穿透能力的限制,一般只能测深度在10um左右的应力,所以只是表面应力。
⑤对于能给出清晰衍射峰的材料,例如退火后细晶粒材料,本方法可达10Mpa的精度,但对于淬火硬化或冷加工材料,其测量误差将增大许多倍。
4.磁测法:磁测法测量残余应力是近年来发展起来的一种新方法,它具有较大的发展前途,设备简单、使用方便,它不仅可以测残余应力也可以测载荷作用下的应力。
- 1、下载文档前请自行甄别文档内容的完整性,平台不提供额外的编辑、内容补充、找答案等附加服务。
- 2、"仅部分预览"的文档,不可在线预览部分如存在完整性等问题,可反馈申请退款(可完整预览的文档不适用该条件!)。
- 3、如文档侵犯您的权益,请联系客服反馈,我们会尽快为您处理(人工客服工作时间:9:00-18:30)。
JBT59261991振动时效工艺参数选择及技术要求
JB/T 5926-91
振动时效工艺
参数选择及技术要求
1991-11-30公布 1992-07-01实施
1 主题内容与适用范畴
本标准规定了振动时效工艺参数的选择及技术要求和振动时效成效评定方法.
本标准适用于材质为碳素结构钢,低合金钢,不锈钢,铸铁,有色金属(铜,铝,锌其合金)等
铸件,锻件,焊接件的振动时效处理.
2 术语
2.1 扫频曲线---将激振器的频率缓慢地由小调大的过程称扫频.随着频率的变化,工件振
动响应发生变化.反映振动响应与频率之间关系的曲线,称扫频曲线,如A---f称振幅
频率曲线;a-f称加速度频率曲线.
注:A表示振幅,a表示加速度,f表示频率.
2.2 激振点---振动时效时,激振器在工件上的夹持点称激振点.
3 工艺参数选择及技术要求
3.1第一应分析判定出工件在激振频率范畴内的振型.
3.2振动时效装置(以下简称装置)的选择.
3.2.1装置的激振频率应大于工件的最低固有频率.
3.2.2装置的最大激振频率小于工作的最低固有频率时,应采取倍频(或称分频)降频等措施.
3.2.3装置的激振力应能使工件内产生的最大动应力为工作应力的1/3~2/3.
3.2.4装置应具备自动扫频,自动记录扫频曲线,指示振动加速度值和电机电流值的功能.稳
速精度应达到+lr/min.
3.3支撑工件,装卡激振器和拾振器
3.3.1为了使工作处于自由状态,应采纳三点或四点弹性的支撑工件,支撑位置应在主振频率
的节线处或邻近.为使工件成为两端简支或悬臂,则应采纳刚性装夹.
3.3.2激振器应刚性地固定在工件的刚度较弱或振幅较大处,但不准固定在工件的强度和刚度
专门低的如大的薄板平面等部位,固定处应平坦.
3.3.3悬臂装夹的工件,一样应掉头进行第二次振动时效处理.特大工件,在其振动响应薄弱
的部位应进行补振.
3.3.4拾振器应固装在远离激振器同时振幅较大处.
3.4 工件的试振
3.4.1不承诺试振的工件存在缩孔,夹渣,裂纹,虚焊等严峻缺陷.
3.4.2选择激振器偏心档位,应满足使工件产生较大振幅和装置只是载的要求,必要时先用手
动旋钮查找合适的偏心档位.
3.4.3第一次扫频,记录工件的振幅频率(A-f)曲线,测出各阶共振频率值,节线位置,波峰位
置.
3.4.4必要时通过调整支撑点,激振点和拾振点的位置来激起较多的振型.
3.4.5测定1-3个共振峰大的频率在共振时的动应力峰值的大小.
3.4.6选择动应力大,频率低在共振频率作为主振频率.
3.4.7按主振型对支撑,拾振位置进行最后调整.
注:主振频率的振型称为主振型.
3.5 工件的主振
3.5.1在亚共振区内选择主振峰峰值的1/3-2/3所对应的频率主振工件.
3.5.2主振时装置的偏心档位应使工件的动应力峰值达到工作应力的1/3-2/3,并使装置的输
出功率不超过额定功率的80%.
3.5.3进行振前扫频,记录振前的振幅时刻(A-f)曲线.
3.5.4主振工件,记录振幅频率(A-t)曲线.
3.5.5起振后振幅时刻(A-t)曲线上的振幅上升,然后变平或上升后下降然后再变平,从变平
开始稳固3-5犿犻狀为振动截止时刻,一样累计振动时刻不超过40犿犻狀.
3.5.6进行振后扫频,记录振幅频率(A-f)曲线.
3.5.7批量生产的工件可不作振前,振后扫频.
3.5.8有些工件可作多点激振处理,有些工件可用附振频率作多频共振辅助处理.是否调整支
撑点,拾振点位置视工件而定.
注:主振频率以外的各共振频率称为附振频率.
3.5.9工件存在如夹渣,缩孔,裂纹,虚焊等缺陷,在振动时效中这类缺陷专门快以裂纹扩展的形
式显现时,应赶忙中断时效处理.工件排除缺陷后,承诺重新进行振动时效.
3.6 振动时效工艺卡和操作记录卡
3.6.1批量生产的工件进行振动时效处理时,必须制订"振动时效工艺卡",操作者必须严格执
行并填写"振动时效操作记录卡"在工件上作已振标记.
3.6.2"振动时效工艺卡"应按3.1-3.5条的要求,试验三件以上,找出规律后制订.
3.6.3"振动时效工艺卡"和"振动时效操作记录卡"的内容和格式分别参照附录犅和附录犆.
3.7 铸件振动时效时,应使动应力方向尽量与易变形方向一致.
3.8 制订焊接件振动时效工艺时,应明确工件上承担力的要紧焊缝和联系焊缝.振动处理中,
其振动方向应使工件承担力的要紧焊缝处的动应力最大或较大.
4 振动时效工艺成效评定方法
4.1 参数曲线观测法
4.1.1振动处理过程中从振幅时刻(A-f)曲线和振前,振后振幅频率(A-f)曲线的变化来监
测.
4.1.2显现下列情形之一时,即可判定为达到振动时效工艺成效.
a 振幅时刻(A-t)曲线上升后变平.
b 振幅时刻(A-t)曲线上升后下降然后变平.
c振幅频率(A-f)曲线振后的比振前的峰值升高.
d振幅频率(A-f)曲线振后的比振前的峰值点左移.
e振幅频率(A-f)曲线振后的比振前的带宽变窄.
4.1.3振动处理过程中,假如不显现4.1.2条中所列的任一情形时,应重新调整振动参数,按上
述规定的条款再进行时效处理后,重新检验.
4.1.4制订有"振动时效工艺卡"的批量生产的工件,在振动时效时,举荐用4.1.2条的a,b款
中只要显现一种情形,便可判定为达到振动时效工艺成效的方法来检验,并不再作下述
检验.
4.2 残余应力检测法
4.2.1举荐使用盲孔法,也可使且X射线衍射法.
4.2.1.1被振工作振前,振后的残余应力测定点数均应大于5个点.
4.2.1.2用振前,振后的应力平均值(应力水平)来运算应力排除率,焊件应大于30%,铸锻件应
大于20%.
4.2.13用振前,振后的最大应力与最小应力之差值来衡量均化程度,振后的运算值应小于振前
的运算值.
4.3 精度稳固性检测法
4.3.1以要求精度稳固性为主的工件,振后应进行精度稳固性检验.
a精加工后检验.
b长期放置定期检验静尺寸稳固性,在放置15d时第一次检验,以后每隔30d检验一次,总
的静置时刻半年以上.
c在动载荷后检验.
应依照具体情形选用上述条款.
4.3.2各种检验结果均应达到设计要求.
附录A
振动时效工艺中动应力选择与振动时效
对工件疲劳寿命阻碍分析
(补充件)
1 振动时效工艺中动应力的选择与分析
动应力是振动时效工艺的一项最要紧参数.实验证明:在一定范畴内动应力越大,被处理工件上产生的应变开释量也越大,
排除应力的成效也越好,动应力过大将有可能造成工件的损害或降低疲劳寿命.因此在本标准中以工作应力来确定动应力.即:σ 动=(1/3~2/3)σ工作在设计时,工作应力(σ工作)是差不多确定的,或和应变测试技术获得,在那个地点应以在工作状态下工件上最大应力点的应力作为工作应力.当我们按上述方法来确定动应力(σ动)时,就能够保证被振工作既能排除应力又不遭到损坏.由于工件结构比较复杂的结构,在不同受力状态下各点的动应力不同,因此在实际操作时,应选择结构危险点(应力集中点),做动应力监测,以保证动应力量值的可靠.
2 振动时效对工件疲劳寿命阻碍的分析
振动时效其工作状态是对工件施加周期性的作用力,这如同疲劳荷载一样,依照线性累积损害理论,必定对工件造成一定的
疲劳损害.但另一方面,由于低应力振动处理后残余应力得到下降,又必定提高工件的疲劳寿命.我国振动时效工作者,通过大量
的试验给出了振动时效对工件疲劳寿命的关系曲线(如图A1所示).图中:N-σ为寿命-应力坐标;
N-σ动为寿命-动应力坐标;
σ工作为实际工作中工件中最大应力;
η工作为在工作应力作用下的疲劳寿命.
从图中可见,当动应力σ动小于A点时,振动时效能够提高疲劳寿命;当动应力σ动大于A点时,振动时效将降低疲劳寿命;当采纳工作荷载处理时,振动时效降低疲劳寿命的数值(B点)就等于振动时效处理时的循环数.因此,本标准中选动应力为工作应力的1/3-2/3是可不能对焊接件造成任何疲劳损害的,相反还能够提高工件的疲劳寿命.。