金相组织 评定标准
金相组织 评定标准.

施加拉伸和压缩轴向力时检测框架和样件对准的验证的标准规范版本:05翻译:杜巧琳日期:2008.10.26校对:日期:批准:日期:施加拉伸和压缩轴向力时检测框架和样件对准的验证的标准规范1此规范使用固定代码E 1012:紧跟代码之后的数字表示原始采用的年份,或版本修改时表示最后一次修改的年份。
括号中的数字表示最后一次重新批准的年份。
右上角的epsilon(ε)表示在最后一次修改或者重新批准后有编辑修改。
1. 范围1.1 此规范包含的方法,覆盖了对有凹口和无凹口检测样件在弹性范围内施加拉力和压力至塑性应变小于0.002时产生的弯曲量的确定。
这些方法尤其适用于通常用于拉伸试验,蠕变检测和非轴向疲劳测试的力的施加速率。
2. 参考文件2.1 ASTM标准:2E 6,与机械检测方法相关的术语E 8,金属材料拉伸试验的检测方法E 83,伸长计系统的验证和分类规范E 251,金属粘结电阻应变计性能特性的检测方法E 466,金属材料进行受控力等幅波轴向疲劳测试的规范E 1237,安装粘结电阻应变计的指南3. 术语3.1 机械测试常用数据定义:3.1.1 此规范中使用的、材料机械测试常用的术语定义见术语E 6。
3.1.2 有凹口截面——与样件几何纵轴垂直的截面,其中横截面面积故意保持为最小值,以作为应力集中区。
3.1.3 有凹口样件的名义百分弯曲——平均横截面的假设(无凹口)样件中的百分弯曲——等于有凹口样件的最小横截面,在假设的,以及有凹口的样件上施加的力的偏心率相同。
(见11.1.5)(此定义不针对凹口根部的应变。
)3.1.4 折算截面——圆角之间的样件长度。
3.2 此规范专用术语的定义3.2.1 对准——一台检测设备和夹具(包括检测样件)在施加拉力或压力时可以对样件引进挠矩的状态。
3.2.1.1 讨论——这是对准的整体状态,包括设备和样件部件。
3.2.2 仪器——用于检测的设备部件和夹具。
包括多种测试中重复用到的所有部件。
各种材料金相组织参考标准
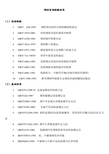
钢材金相检验标准(1) 低倍检验1 GB/T 226-1991 钢的低倍组织及缺陷酸蚀检验法2 GB/T 1979-2001 结构钢低倍组织缺陷评级图3 GB/T 4236-1984 钢的硫印检验方法4 GB/T 1814-1979 钢材断口检验法5 GB/T 2971-1982 碳素钢和低合金钢断口检验方法6 YB/T 731-19870 塔型车削发纹检验法7 YB/T 4002-1992 连铸钢方坯低倍组织缺陷评级图8 YB/T 4003-1991 连铸钢板坯缺陷硫印评级图9 YB/T 4061-1991 铁路机车、车轴用车轴(含硫印缺陷评级图)10 CB/T 3380-1991 船用钢材焊接接头宏观组织缺陷酸蚀试验法(2) 基础标准1 GB/T/T13298-91 金属显微组织检验方法2 GB/T224-1987 钢的脱碳层深度测定法3 GB/T10561-1988 钢中非金属夹杂物显微评定方法4 GB/T 6394-2002 金属平均晶粒度测定方法5 GB/T/T13299-1991 钢的显微组织(游离渗碳体、带状组织及魏氏组织)评定方法6 GB/T/T13302-1991 钢中石黑碳显微评定方法7 GB/T4335-1984 低碳钢冷轧薄板铁素体晶粒度测定法8 JB/T/T5074-1991 低、中碳钢球化体评级9 ZBJ36016-1990 中碳钢与中碳合金结构钢马氏体等级10 DL/T 652-1998 金相复型技术工艺导则(3) 不锈钢1 GB/T6401-86 铁素体奥氏体型双相不锈钢α-相面积含量金相测定法2 GB/T1223-75 不锈耐酸钢晶间腐蚀倾向试验方3 GB/T1954-80 铬镍奥氏体不锈钢焊缝铁素体含量测量方法4 GB/T/T13305-91 奥氏体不锈钢中α-相面积含量金相测定法(4) 铸钢1 GB/T8493-87 一般工程用铸造碳钢金相2 TB/T/T2451-93 铸钢中非金属夹杂物金相检验3 TB/T/T2450-93 ZG230-450铸钢金相检验4 GB/T/T13925-92 高锰钢铸件金相5 GB/T5680-85 高锰钢铸件技术条件(含金相组织检验)6 YB/T/T036.4-92 冶金设备制造通用技术条件高锰钢铸件(高锰钢金相组织检验)7 JB/T/GQ0614-88 熔模铸钢ZG310-570正火组织金相检验(5) 化学热处理及感应淬火1 GB/T11354-89 钢铁零件渗氮层深度测定和金相组织检验2 GB/T9450-88 钢件渗碳淬火有效硬化层深度的测定和校核3 QCn29018-91 汽车碳氮共渗齿轮金相检验4 JB/T4154-85 25MnTiBXt钢碳氮共渗齿轮金相检验标准5 NJ251-81 20MnTiBRe钢渗碳齿轮金相组织检验6 ZB/T04001-88 汽车渗碳齿轮金相检验7 TB/T/T2254-91 机车牵引用渗碳淬硬齿轮金相检验8 JB/T/T6141.1-92 重载齿轮渗碳层球化处理后金相检验9 JB/T/T6141.3-92 重载齿轮渗碳金相检验10 JB/T/T6141.4-92 重载齿轮渗碳表面碳含量金相判别法11 GB/T5617-85 钢的感应淬火或火焰淬火有效硬化层深度的测定12 GB/T9451-88 钢件薄表面总硬化层深度或有效硬化层深度的测定13 ZB/J36009-88 钢件感应淬火金相检验14 ZB/J36010-88 珠光体球墨铸铁零件感应淬火金相检验15 NJ304-83 渗碳齿轮感应加热淬火金相检验16 JB/T2641-79 汽车感应淬火零件金相检验17 CB/T3385-91 钢铁零件渗氮层深度测定方法(6) 轴承钢1. YJZ84 高碳铬轴承钢(含酸浸低倍组织、非金属夹杂物、显微孔隙、退火组织、碳化物不均匀性、碳化物带状、碳化物液析评级图)2. GB/T9-68 铬轴承钢技术条件(含低倍缺陷、非金属夹杂物、退火组织、碳化物网状、碳化物液析评级图)3 GB/T3086-82 高碳铬不锈轴承钢技术条件(含酸浸低倍组织、火组织、共晶碳化物不均匀度、非金属夹杂物、微孔隙评级图)4 YB/T688-76 高温轴承钢Cr4Mo4V技术条件(含碳化物不均匀度评级图)5 JB/T1255-91 高碳铬轴承钢滚动轴承零件热处理技术条件(含退火组织、淬回火组织、碳化物网状、断口评级图)6 ZB/J36001-86 滚动轴承零件渗碳热处理质量标准(含粗大碳化物、渗碳表面层淬回火组织、心部组织、网状碳化物评级图)7 JB/T1460-92 高碳铬不锈钢滚动轴承零件热处理技术条件(含退火组织、淬回火组织、断口评级图)8 JB/T2850-92 Cr4Mo4V高温轴承钢滚动轴承零件热处理技术条件(含淬火组织、淬回火组织评级图)9 JB/T/T6366-92 55SiMoV A钢滚动轴承零件热处理技术条件(含退火组织、淬回火组织、渗碳淬回火组织评级图)(7) 工具钢1 GB/T1298-77 碳素工具钢技术条件(含珠光体组织、网状碳化物评级图)2 GB/T1299-85 合金工具钢技术条件(含珠光体组织、网状碳化物、共晶碳化物不均匀)3 YB/T12-77 高速工具钢技术条件(含低倍碳化物剥落、共晶碳化物不均匀度评级图)4 ZB/J36003-87 工具热处理金相检验标准5 GB/T4462-84 高速工具钢大块碳化物评级图(8) 零部件专用标准1 GB/T/T13320-91 钢质模锻件金相组织评级图及评定方法2 ZB/J18004-89 传动用精密滚子链和套筒链零件金相检验3 ZB/J26001-88 60Si2Mn钢螺旋弹簧金相检验4 ZB/J94007-88 柴油机喷嘴偶件、喷油泵柱塞偶件、喷油泵出油阀偶件金相检验5 JB/T3782-84 汽车钢板弹簧金相检验标准6 NJ309-83 内燃机连杆螺柱金相检验标准7 NJ326-84 内燃机活塞销金相检验标准8 JB/T/T6720-93 内燃机排气门金相检验标准9 JB/T/NQ180-88 内燃机气门座金相检验10 JB/T/GQ1050-84 45、40Cr钢淬火马氏体金相检验11 JB/T/GQ1148-89 机床用40Cr钢调质组织金相检验12 JB/T/GQ·T1150-89 机床用38CrMoAl钢验收技术条件及调质后金相检验13 JB/T/GQ·T1151-89 机床用45钢调质组织金相检验14 NJ396-86 低淬透性含钛优质碳素结构钢齿轮金相检验15 JB/T/T5664-91 重载齿轮失效判据16 CJ/T 31-1999 液化石油气钢瓶金相组织评定。
调质后金相组织的评定标准

调质后金相组织的评定标准使用金相显微镜来观察和评定材料的金相组织是材料科学研究和工程应用中常见的方法之一。
金相显微镜是一种特殊的光学显微镜,能够通过对材料进行磨削、腐蚀、观察等处理,从而获取关于材料内部组织和成分特征的信息。
在评定调质后金相组织时,我们需要考虑几个关键因素,包括颗粒尺寸、晶粒形状和分布、非金属夹杂物的含量和尺寸等。
本文将介绍调质后金相组织的评定标准。
一、颗粒尺寸在调质处理后,材料的微观结构会发生显著变化,颗粒的尺寸是评定材料金相组织的重要参数之一。
一般来说,颗粒尺寸越小,材料的强度和硬度往往越高。
通过金相显微镜的观察,可以测量和评定金相组织中颗粒的平均尺寸,并与预期的理想尺寸进行比较。
二、晶粒形状和分布在调质后,材料的晶粒会发生重新长大和重新排列的过程。
晶粒的形状和分布对材料的力学性能和耐腐蚀性能有着重要影响。
观察材料金相组织时,需要关注晶粒的形状是否规则,分布是否均匀。
可以通过计算晶粒的平均晶粒尺寸和晶粒的尺寸分布来评定材料金相组织。
三、非金属夹杂物的含量和尺寸非金属夹杂物是指材料中的一些杂质,如气泡、氧化物、硫化物等。
这些夹杂物会对材料的力学性能和腐蚀性能产生负面影响。
通过金相显微镜,可以观察和评定非金属夹杂物的含量和尺寸。
通常情况下,夹杂物的含量越低,夹杂物的尺寸越小,材料的性能越好。
以上是调质后金相组织的主要评定标准。
通过金相显微镜的观察和评定,我们可以获取关于调质后材料金相组织的详细信息,从而了解材料的性能和品质。
这些信息对于材料科学研究和工程应用都具有重要意义,能够指导工程师和科研人员进行材料的选择、设计和优化。
需要注意的是,在评定调质后金相组织时,我们应该遵循一定的实验规范和操作流程,以确保观察结果的准确性和可重复性。
比如,我们需要选择合适的磨削和抛光工艺,以提高样品的表面质量;还需要选择适当的显微镜放大倍数,以保证观察到所关注的细节。
除了金相显微镜之外,还有一些其他常用的表征方法可以结合使用,对调质后金相组织进行全面评定。
金相评级标准
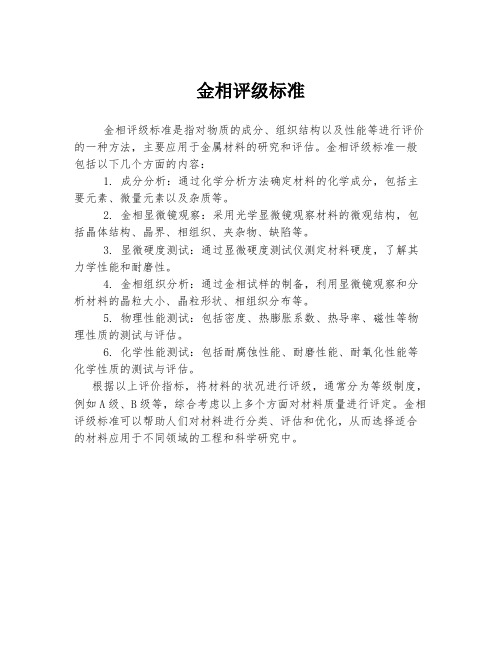
金相评级标准
金相评级标准是指对物质的成分、组织结构以及性能等进行评价的一种方法,主要应用于金属材料的研究和评估。
金相评级标准一般包括以下几个方面的内容:
1. 成分分析:通过化学分析方法确定材料的化学成分,包括主要元素、微量元素以及杂质等。
2. 金相显微镜观察:采用光学显微镜观察材料的微观结构,包括晶体结构、晶界、相组织、夹杂物、缺陷等。
3. 显微硬度测试:通过显微硬度测试仪测定材料硬度,了解其力学性能和耐磨性。
4. 金相组织分析:通过金相试样的制备,利用显微镜观察和分析材料的晶粒大小、晶粒形状、相组织分布等。
5. 物理性能测试:包括密度、热膨胀系数、热导率、磁性等物理性质的测试与评估。
6. 化学性能测试:包括耐腐蚀性能、耐磨性能、耐氧化性能等化学性质的测试与评估。
根据以上评价指标,将材料的状况进行评级,通常分为等级制度,例如A级、B级等,综合考虑以上多个方面对材料质量进行评定。
金相评级标准可以帮助人们对材料进行分类、评估和优化,从而选择适合的材料应用于不同领域的工程和科学研究中。
金相检验标准

金相检验标准金相检验是金属材料工程中非常重要的一项检测工作,它可以帮助工程师和科研人员了解金属材料的组织结构、性能特点以及内在缺陷,从而指导材料的选用和加工工艺的优化。
金相检验标准是进行金相检验必须遵循的规范,它涵盖了金相检验的各个方面,包括样品的制备、试样的切割、研磨和腐蚀处理,金相显微镜的使用和金相组织的评定等内容。
本文将对金相检验标准进行详细介绍,以便读者更好地了解金相检验的相关知识。
首先,金相检验标准对样品的制备提出了明确的要求。
在进行金相检验之前,需要对待检材料进行切割、研磨和腐蚀处理,以便观察金相组织。
样品的制备质量直接影响着金相检验结果的准确性,因此必须严格按照标准操作,确保样品的制备达到要求。
其次,金相检验标准规定了金相显微镜的使用方法和金相组织的评定标准。
金相显微镜是进行金相检验的关键设备,它能够放大样品的微观组织结构,使人们能够清晰地观察到金属材料的晶粒、晶界、夹杂物等微观结构。
金相组织的评定标准则是根据金相显微镜下观察到的组织结构特征,对材料的组织类型、晶粒尺寸、夹杂物含量等进行评定,从而判断材料的质量和性能特点。
除了以上内容,金相检验标准还包括了金相检验的一些特殊要求,比如对特殊材料的金相检验方法、金相显微镜的技术指标要求、金相检验结果的记录和报告等。
这些内容都是金相检验过程中不可或缺的环节,对于保证金相检验结果的准确性和可靠性具有重要意义。
总的来说,金相检验标准是进行金相检验必须遵循的规范,它涵盖了金相检验的各个方面,对于确保金相检验结果的准确性和可靠性具有重要意义。
希望通过本文的介绍,读者能够更好地了解金相检验标准的相关知识,从而在实际工作中更好地进行金相检验工作,为材料的选用和加工工艺的优化提供有力的支持。
调质后金相组织的评定标准
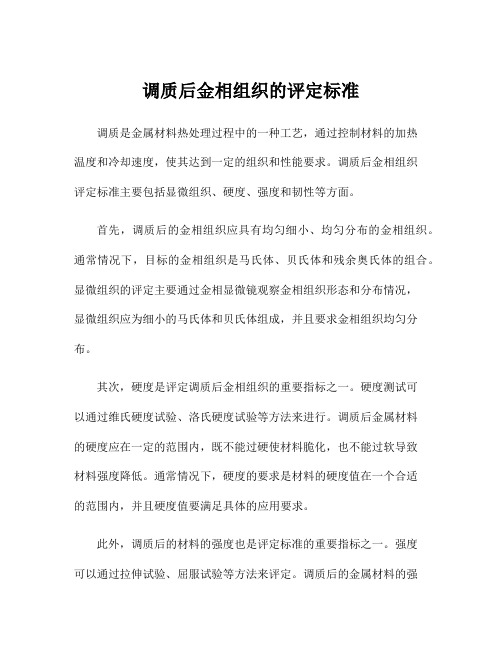
调质后金相组织的评定标准调质是金属材料热处理过程中的一种工艺,通过控制材料的加热温度和冷却速度,使其达到一定的组织和性能要求。
调质后金相组织评定标准主要包括显微组织、硬度、强度和韧性等方面。
首先,调质后的金相组织应具有均匀细小、均匀分布的金相组织。
通常情况下,目标的金相组织是马氏体、贝氏体和残余奥氏体的组合。
显微组织的评定主要通过金相显微镜观察金相组织形态和分布情况,显微组织应为细小的马氏体和贝氏体组成,并且要求金相组织均匀分布。
其次,硬度是评定调质后金相组织的重要指标之一。
硬度测试可以通过维氏硬度试验、洛氏硬度试验等方法来进行。
调质后金属材料的硬度应在一定的范围内,既不能过硬使材料脆化,也不能过软导致材料强度降低。
通常情况下,硬度的要求是材料的硬度值在一个合适的范围内,并且硬度值要满足具体的应用要求。
此外,调质后的材料的强度也是评定标准的重要指标之一。
强度可以通过拉伸试验、屈服试验等方法来评定。
调质后的金属材料的强度应达到一定的要求,保证材料具有足够的强度来承受外部载荷,使得材料在使用过程中不易变形和断裂。
最后,调质后金属材料还需要具有一定的韧性。
韧性是指材料在受到外力作用下能够抵抗损坏和变形的能力。
韧性的评定可以通过冲击试验等方法进行。
调质后金属材料的韧性应满足要求,以保证材料耐冲击、耐疲劳、抗裂纹扩展等性能,从而使得材料在使用过程中更加可靠和安全。
综上所述,调质后金相组织的评定标准主要包括显微组织、硬度、强度和韧性等方面。
通过合理的热处理工艺控制,可以使金属材料达到特定的组织和性能要求,从而保证材料在使用过程中具有足够的强度和韧性。
调质后金相组织的评定标准对于保证材料的质量和可靠性具有重要的意义。
调质后金相组织的评定标准
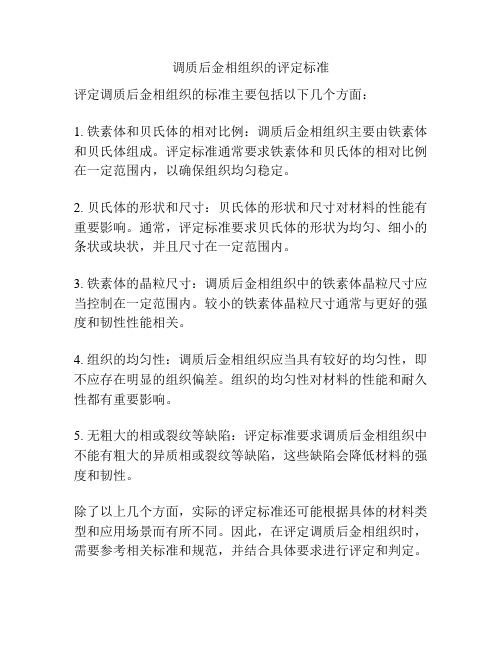
调质后金相组织的评定标准
评定调质后金相组织的标准主要包括以下几个方面:
1. 铁素体和贝氏体的相对比例:调质后金相组织主要由铁素体和贝氏体组成。
评定标准通常要求铁素体和贝氏体的相对比例在一定范围内,以确保组织均匀稳定。
2. 贝氏体的形状和尺寸:贝氏体的形状和尺寸对材料的性能有重要影响。
通常,评定标准要求贝氏体的形状为均匀、细小的条状或块状,并且尺寸在一定范围内。
3. 铁素体的晶粒尺寸:调质后金相组织中的铁素体晶粒尺寸应当控制在一定范围内。
较小的铁素体晶粒尺寸通常与更好的强度和韧性性能相关。
4. 组织的均匀性:调质后金相组织应当具有较好的均匀性,即不应存在明显的组织偏差。
组织的均匀性对材料的性能和耐久性都有重要影响。
5. 无粗大的相或裂纹等缺陷:评定标准要求调质后金相组织中不能有粗大的异质相或裂纹等缺陷,这些缺陷会降低材料的强度和韧性。
除了以上几个方面,实际的评定标准还可能根据具体的材料类型和应用场景而有所不同。
因此,在评定调质后金相组织时,需要参考相关标准和规范,并结合具体要求进行评定和判定。
金相浅析及完整检验标准

金相浅析及完整检验标准金相金属或合金内部结构指金属或合金的化学成分以及各种成分在合金内部的物理状态和化学状态。
金相组织是反映金属金相的具体形态,如马氏体,奥氏体,铁素体,珠光体等等。
广义的金相组织是指两种或两种以上的物质在微观状态下的混合状态以及相互作用状况。
金相组织金属材料的内部结构,只有在显微镜下才能观察到。
在显微镜下看到的内部组织结构称为显微组织或金相组织。
钢材常见的金相组织有:铁素体、奥氏体、渗碳体、珠光体等金相显微镜金相显微镜是将光学显微镜技术、光电转换技术、计算机图像处理技术完美地结合在一起而开发研制成的高科技产品,可以在计算机上很方便地观察金相图像,从而对金相图谱进行分析,评级等以及对图片进行输出、打印。
众所周知,合金的成分、热处理工艺、冷热加工工艺直接影响金属材料的内部组织、结构的变化,从而使机件的机械性能发生变化。
因此用金相显微镜来观察检验分析金属内部的组织结构是工业生产中的一种重要手段。
金相显微镜主要由光学系统、照明系统、机械系统、附件装置(包括摄影或其它如显微硬度等装置)组成。
根据金属样品表面上不同组织组成物的光反射特征,用显微镜在可见光范围内对这些组织组成物进行光学研究并定性和定量描述。
它可显示500~0.2m尺度内的金属组织特征。
早在1841年,俄国人(п.п.Ансов)就在放大镜下研究了大马士革钢剑上的花纹。
至1863年,英国人(H.C.Sorby)把岩相学的方法,包括试样的制备、抛光和腐刻等技术移植到钢铁研究,发展了金相技术,后来还拍出一批低放大倍数的和其他组织的金相照片。
索比和他的同代人德国人(A.Martens)及法国人(F. Osmond)的科学实践,为现代光学金相显微术奠定了基础。
至20世纪初,光学金相显微术日臻完善,并普遍推广使用于金属和合金的微观分析,迄今仍然是金属学领域中的一项基本技术。
金相显微镜是用可见光作为照明源的一种显微镜可分为正立式和倒置式两种。
- 1、下载文档前请自行甄别文档内容的完整性,平台不提供额外的编辑、内容补充、找答案等附加服务。
- 2、"仅部分预览"的文档,不可在线预览部分如存在完整性等问题,可反馈申请退款(可完整预览的文档不适用该条件!)。
- 3、如文档侵犯您的权益,请联系客服反馈,我们会尽快为您处理(人工客服工作时间:9:00-18:30)。
施加拉伸和压缩轴向力时检测框架和样件对准的验证的标准规范版本:05翻译:杜巧琳日期:2008.10.26校对:日期:批准:日期:施加拉伸和压缩轴向力时检测框架和样件对准的验证的标准规范1此规范使用固定代码E 1012:紧跟代码之后的数字表示原始采用的年份,或版本修改时表示最后一次修改的年份。
括号中的数字表示最后一次重新批准的年份。
右上角的epsilon(ε)表示在最后一次修改或者重新批准后有编辑修改。
1. 范围1.1 此规范包含的方法,覆盖了对有凹口和无凹口检测样件在弹性范围内施加拉力和压力至塑性应变小于0.002时产生的弯曲量的确定。
这些方法尤其适用于通常用于拉伸试验,蠕变检测和非轴向疲劳测试的力的施加速率。
2. 参考文件2.1 ASTM标准:2E 6,与机械检测方法相关的术语E 8,金属材料拉伸试验的检测方法E 83,伸长计系统的验证和分类规范E 251,金属粘结电阻应变计性能特性的检测方法E 466,金属材料进行受控力等幅波轴向疲劳测试的规范E 1237,安装粘结电阻应变计的指南3. 术语3.1 机械测试常用数据定义:3.1.1 此规范中使用的、材料机械测试常用的术语定义见术语E 6。
3.1.2 有凹口截面——与样件几何纵轴垂直的截面,其中横截面面积故意保持为最小值,以作为应力集中区。
3.1.3 有凹口样件的名义百分弯曲——平均横截面的假设(无凹口)样件中的百分弯曲——等于有凹口样件的最小横截面,在假设的,以及有凹口的样件上施加的力的偏心率相同。
(见11.1.5)(此定义不针对凹口根部的应变。
)3.1.4 折算截面——圆角之间的样件长度。
3.2 此规范专用术语的定义3.2.1 对准——一台检测设备和夹具(包括检测样件)在施加拉力或压力时可以对样件引进挠矩的状态。
3.2.1.1 讨论——这是对准的整体状态,包括设备和样件部件。
3.2.2 仪器——用于检测的设备部件和夹具。
包括多种测试中重复用到的所有部件。
3.2.2.1 讨论——当应变计检测过的样件不用于接下来的样件检测时,它包括在仪器之中。
3.2.3 轴向应变——在样件几何纵轴对面表面上,用位于与折算截面同样纵向位置上的多个应变感应装置测得的纵向应变的平均值。
3.2.3.1 讨论——此定义仅适用于此标准。
术语用在机械检测的其他章节里。
3.2.4 弯曲应变——表面应变与轴向应变之间的差(见图1)。
通常,弯曲应变会环绕并沿着样件的折算截面,因点的不同而不同。
弯曲应变的计算见11部分。
(略)备注1:弯曲应变±B是附加在轴向应变a上的,第轴向应变(或压力)见(a),高轴向应变(或压力)见(b)。
对于同样的弯曲应变±B,高百分应变见(a)低百分应变见(b)。
图1 可能伴随非轴向载荷而出现的弯曲应变的图示3.2.5 偏心率——施加的力的作用线,与样件在与样件纵轴垂直的平面的几何轴线之间的距离。
3.2.6 设备对准——检测设备和负荷训练的所有刚体的一个状态,可以在接下来的施加力的过程中可以引进挠距给样件的。
3.2.7 最大弯曲应变——在测量弯曲的、直的无凹口样件的折算截面,沿着其长度位置上的弯曲应变的最大值。
(凹口样件见4.9)3.2.8 百分弯曲——弯曲应变乘以100除以轴向应变。
3.2.9 额定力——测量对准的力。
3.2.10 样件对准——包括夹具和样件定位的非刚体在内的检测样件位于可以在接下来的施加力的过程中引进挠距给1此规范受ASTM委员会E28的管辖,针对机械测试,是附属委员会E28.04在非轴向检测方面的直接责任。
目前的版本是2005年6月1日批准,2005年7月发布的。
最初在1989年批准。
最近一次在1999年修改为E 1012-99。
2对于参考到的ASTM规范,请访问ASTM网站,或者联系ASTM客户服务service@。
对于ASTM标准手册的卷册信息,参考ASTM网站上标准的文件汇总页。
样件的状态。
4. 意义与使用4.1 已经表明,施加拉力和压力过程中由于施加的力和样件中之间的未对准而不经意产生的弯曲力可以影响检测结果。
在识别此影响时,某些检测方法包含了一个生命,限制了允许的不对准。
此规范的目的就是为了给那些施加拉力或压力时要求较高对准要求的检测方法和规范提供一个参考。
目标就是为了实现有夹具和检测样件的检测设备的验证和对准中常用术语和方法的使用。
4.2 除非另有规定,否则当进行检测来验收材料的最小强度和展延性要求时,轴对称性要求和验证是选择性地。
这是因为,任何影响,尤其是过度弯曲导致的影响,都回降低强度和展延性并给出保守的结果。
检测高展延性材料以确定是否符合最低特性时,改善的轴对称性可能不会有什么溢出。
是否改善轴对称性应当由材料生产商和使用者商讨决定。
5. 对准的验证5.1 为了在其他规范,检测方法和产品规范中便于参考,验证对准的最常用方法见第6部分。
5.2 对准的数量化要求应当规定力,样件尺寸和进行测量时的温度。
当应变水平特别重要时可采取的替代方法可以按照规范E466的规定来使用。
当使用该方法时,数量化要求应当规定应变水平,样件尺寸和进行测量的温度。
5.2.1 规定弯曲应变的力可以表示为屈服强度或其他名义样件压力。
备注1:对一个未对准的负荷训练而言,百分弯曲通常会随着施加的力的增加而减小。
(见图2中的曲线A,B和C)但是,在某些严重情况下,百分弯曲可以随着施加的力的增加而增加(见图2曲线D)。
(略)备注1:曲线A,设备1,螺纹夹头(11)备注2:曲线B,设备2,镦头夹头(11)备注3:曲线C,设备3,带通用耦合的夹头(7)备注4:曲线D,共心未对准负荷训练的可能反应的图示(16)图2 不同检测设备和夹持方法下施加的力对百分弯曲的影响5.3 对准要求和结果可以指整个检测设备能力或特定检测。
这种区别应该在结果中备注出来。
5.3.1 整个检测设备能力的验证应当使用设计和材料与检测中使用的类似的样件的仪器来进行,但是样件凹口可以不要。
同样的样件可以用于连续验证。
材料和设计应当保证在额定力时只有弹性应变。
如果预期的检测样件材料未知,使用良好的工程判定来选择常用材料制成的样件来验证。
备注2:为了避免对验证样件造成损伤,轴向应变之和以及最大弯曲应变应当不得超过弹性极限。
5.3.2 对准程序之后的、对要变成检测样件的特定眼见的验证应该在检测前或检测中在待测样件上进行,不要将样件从检测设备上移掉,也不要进行任何可能影响验证和检测之间的对准的其他调整。
这些类型的验证提供了特定检测样件上的最佳真是弯曲测量。
备注3:可能需要在验证和检测之间在样件上保持一个小力,以保持无刚性夹持的检测设备上的对准。
6. 对准的验证方法6.1 使用这种方法来进行设备对准的验证,以及在特定检测中或规定的检测状态下进行样件对准的测量。
6.1.1 设备对准——方法的这部分描述了装夹刚体的初次对准。
在第一次安装一台检测设备时,以及在一台检测设备上设置一种特定类型的刚性装夹结构时,要先建立设备对准。
当它不会随着时间发生一点变化时,负荷训练(夹具或检测样件)的灾难性故障或磨损可能就需要测量并重新调整设备对准。
设备对准应当在要求刚性夹具发生变化的任何时候都要进行。
设备对准通常视作“粗略”的对准。
6.1.2 样件对准——方法的这部分描述了样件以及负荷训练中所有非刚性夹具的定位和接下来的对准。
要求使用应变计检测过的、特定几何结构的样件,或利用其他类型位移计来测量施加给样件的应变的机械对准夹具。
应变计检测过的样件见第8部分。
机械对准夹具见第7部分。
对准测量结构类型的描述(也就是,应变计检测过的样件,或机械对准夹具)应当包含在报告中。
应变计检测过的样件通常可以比对准夹具提供更好的应变读数分辨率,尤其是在低水平时,因此它们更常用于这种测量方法。
样件对准通常视作“精密”的对准。
7. 仪器7.1 当按照6.1.2所述使用多个应变感应器时,样件尺寸限制可能要求使用电阻应变计,而不是使用机械联系的伸长计或对准夹具。
应变传感器,诸如机械的,光学的,或电子伸长计,以及导线电阻应变计或箔式应变计,可以提供有用的位移数据。
相应标准或规范要求的位移测量的灵敏度取决于允许的弯曲的量。
7.2 对于使用6.1.2的对准夹具的验证,可以使用非平均类型的单个伸长计,在连续的施力中将其绕着周长旋转至各个位置并重复10.5中描述的测量。
通常,对接近屈服的应变水平重复施加力不是良好的实验室规范,因为它们可能会让样件变形或疲劳从而影响接下来的测量结果。
备注4:绕着样件重新定位伸长计通常不会给出最高精度和可再现的结果,但是仍然是一种探测大量弯曲的有用技术。
7.3 样件上应变测量的机械装夹可能是测量并考虑到现场调整来改善检测商品上的对准。
附在样件肩部并测量圆柱形样件周长上四个等距位置的位移的夹具可以有效地用于此目的。
位移测量装以需要有足够的分辨率可以探测到环绕样件的位移的很小变化。
如果使用此方法,在应用弯曲计算之前必须将这些位移转换成应变。
应变应当使用ASTM E21中描述的有效计量长度来计算。
备注5:使用多个伸长计时,可以通过求输出的算术平均值来确定应变。
通常认为电子输出比机械输出更加准确和可再现。
7.4 其他设备和装夹的考虑:7.4.1 制作不好的部件和负荷训练中的多个分界面可以在对准检测系统时引起重大困难。
负荷训练中的全部部件都应当在现代设备现场规范的范围内进行加工,要注意垂直度,同心度,平面度和表面光洁度。
部件的数量应该保持最低。
7.4.2 可能会出现某个特定设备,夹具和样品不能对准的情况。
在这种情况下,可能需要对某些部件进行重新设计和制造以达到合格的对准。
8. 检测样件8.1 此规范针对圆柱样件,厚的矩形样件和薄的矩形样件。
实际样件几何结构取决于用到的检测标准。
这些样件通常呈现一个有折算截面的沙漏形状,但是其他用于压缩试验的样件也是可以的。
8.2 此规范对金属和非金属检测样件有效。
8.3 检测样件的加工质量很重要。
重要特性包括直线度,同心度,平面度和表面光洁度。
尤其是用于压缩试验的样件类型,可以使用两个平行板对样件的端面施加压力。
在这种情况下,根据ASTM方法E9的规定,样件端面的平行度是非常重要的。
8.4 应变计检测过的样件的设计应当遵从标准检测样件的设计方针。
对于静态(拉伸,压缩和蠕变)检测,符合检测方法E8的样件比较合适。
对于疲劳测试,符合ASTM E606要求的样件比较合适。
应变计检测过的样件应当在尺寸上尽可能接近预期检测样件,这样检测中使用的夹头和夹具就可以在对准中也使用了。
应变计检测过的样品的材料应当尽可能与预期检测样件的材料接近。
如果预期检测材料未知,也可以使用与预期检测材料具有相似弹性特性的常用材料的样件。
应用应变计之前对准样件应当仔细检查并记录尺寸。