系统布置设计(SLP)模式
物流工程系统布置设计(SLP)

3、详细布置:确定各个作业单位或各个
设施的具体位置.
4、施工安装:编制计划,进行施工安装 .
布置设计四阶段
阶
Ⅰ确定位置:工厂的总体位置
段
Ⅱ总体区分:初步规划基本物流模式和总体布局
Ⅲ详细布置:确定各作业单位的具体位置
Ⅳ实施:编制施工计划,进行施工安装
时间
原始资料:P、Q、R、S、T及作业单位
工厂布局设计
机械与运载工程学院
固定式布置缺点:
场地空间有限; 不同的工作时期,物料和人员需求不一样,这给生产组 织和管理带来较大困难; 物料需求量是动态的。
系统化布置
工厂布置的方法和技术,一直是工业工程领域 不断探索的问题.自工业革命以来研究出了许多手 工设计、数字分析和图解技术,60年代以来,又发 展了计算机辅助工厂布置,在众多的布置方法中, 以R·缪瑟提出的系统布置设计SLP(System Layout Planning)最为著名,应用十分普遍;这种方法不仅 适用于工厂和生产系统设计,还可以用于医院、学 校,百货商店、办公楼等设施设计。
1.工厂布局的形式 (1)产品原则布置(流水线布置) 当产品品种少批量大时,应当按照产品的加工工艺过程顺 序来配置设备,形成流水生产线或装配线。
图1 产品原则布置示意图
图2 汽车后桥加工生产线
图3 汽车装配生产线
图4 汽车焊接生产线
产品原则布置的基础
标准化及作业分工。整个产品被分解成一系列标准化的作 业,由专门的人力及加工设备来完成。
部门由工作中心(Work Center)组成,若是工厂这些工作中心可 以是工段或班组,如车床工段;也可以是柔性制造单元(FMS)。
工作中心由工作站(Workstation)组成。工作站也称工作地,是 最小作业单位,它一般由一台机器和/或一个作业人员组成。 8
SLP资料
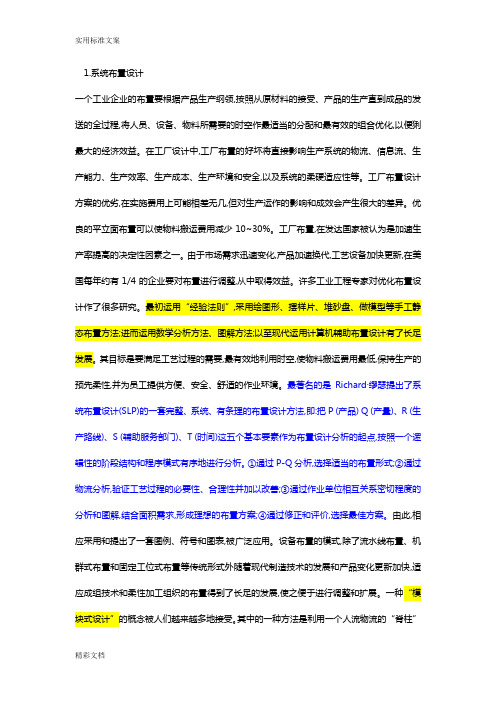
1.系统布置设计一个工业企业的布置要根据产品生产纲领,按照从原材料的接受、产品的生产直到成品的发送的全过程,将人员、设备、物料所需要的时空作最适当的分配和最有效的组合优化,以便猁最大的经济效益。
在工厂设计中,工厂布置的好坏将直接影响生产系统的物流、信息流、生产能力、生产效率、生产成本、生产环境和安全,以及系统的柔硬适应性等。
工厂布置设计方案的优劣,在实施费用上可能相差无几,但对生产运作的影响和成效会产生很大的差异。
优良的平立面布置可以使物料搬运费用减少10~30%。
工厂布置,在发达国家被认为是加速生产率提高的决定性因素之一。
由于市场需求迅速变化,产品加速换代,工艺设备加快更新,在美国每年约有1/4的企业要对布置进行调整,从中取得效益。
许多工业工程专家对优化布置设计作了很多研究。
最初运用“经验法则”,采用绘图形、摆样片、堆砂盘、做模型等手工静态布置方法;进而运用数学分析方法、图解方法;以至现代运用计算机辅助布置设计有了长足发展。
其目标是要满足工艺过程的需要,最有效地利用时空,使物料搬运费用最低,保持生产的预先柔性,并为员工提供方便、安全、舒适的作业环境。
最著名的是Richard·缪瑟提出了系统布置设计(SLP)的一套完整、系统、有条理的布置设计方法,即:把P (产品) Q (产量)、R (生产路线)、S (辅助服务部门)、T (时间)这五个基本要素作为布置设计分析的起点,按照一个逻辑性的阶段结构和程序模式有序地进行分析。
①通过P-Q分析,选择适当的布置形式;②通过物流分析,验证工艺过程的必要性、合理性并加以改善;③通过作业单位相互关系密切程度的分析和图解,结合面积需求,形成理想的布置方案;④通过修正和评价,选择最佳方案。
由此,相应采用和提出了一套图例、符号和图表,被广泛应用。
设备布置的模式,除了流水线布置、机群式布置和固定工位式布置等传统形式外随着现代制造技术的发展和产品变化更新加快,适应成组技术和柔性加工组织的布置得到了长足的发展,使之便于进行调整和扩展。
系统化布置设计SLP

8、实际制约
作业单位位置相关图
SLP详解目录
01
布置修正
02
布置方案的评价与选择
03
Please add content 3
04
Please add content 4
05
Please add content 4
06
Please add content 6
输入数据(P、Q、R、S、T)? 影响布置设计的因素众多,基本要素可以归纳为5项:P产品(或材料或服务)、Q数量、R生产路线(工艺过程)、S辅助服务部门、T时间(或时间安排)。 五个要素分别回答以下问题: P——Product 生产什么? Q——Quantity 生产多少? R——Routing 怎么生产? S——Supporting service用什么支持生产? T——Time 何时生产?
关系表布局法
计算机化布置方法(第7章)
(1)试错法
*
Muther的SLP用线型图来试错生成空间关系。 ①线型图表示法:A:4条平行线;E:3;I:2; O:1; U:不表示; X:用折线表示。 ②先将A、E级关系的部门放入布置图;相同级别的关系用相同长度的线段表示。调整,使E级关系的线段长度约为A级关系的2倍。随后,按同样的规则布置I级关系。若部门较多,线段混乱,可以不必画出O级关系。但X级必须表示。 ③调整各部门的位置,以满足关系的亲疏程度。最后,将各个部门的面积表示进布置图中,生成空间关系图。经过评价、修改,便获得最终布置。
Ⅰ确定位置:工厂的总体位置
Ⅱ总体区分:初步规划基本物流模式和总体布局
Ⅲ详细布置:确定各作业单位的具体位置
Ⅳ实施:编制施工计划,进行施工安装
阶 段
时间
系统布置设计方法
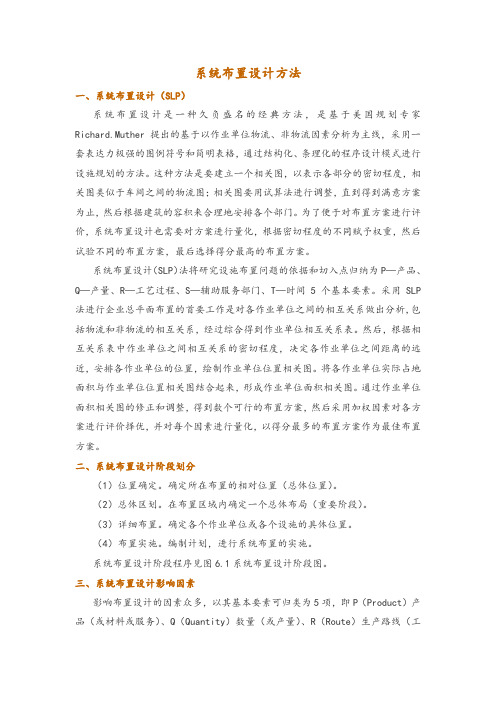
系统布置设计方法一、系统布置设计(SLP)系统布置设计是一种久负盛名的经典方法,是基于美国规划专家Richard.Muther提出的基于以作业单位物流、非物流因素分析为主线,采用一套表达力极强的图例符号和简明表格,通过结构化、条理化的程序设计模式进行设施规划的方法。
这种方法是要建立一个相关图,以表示各部分的密切程度,相关图类似于车间之间的物流图;相关图要用试算法进行调整,直到得到满意方案为止,然后根据建筑的容积来合理地安排各个部门。
为了便于对布置方案进行评价,系统布置设计也需要对方案进行量化,根据密切程度的不同赋予权重,然后试验不同的布置方案,最后选择得分最高的布置方案。
系统布置设计(SLP)法将研究设施布置问题的依据和切入点归纳为P—产品、Q—产量、R—工艺过程、S—辅助服务部门、T—时间5个基本要素。
采用SLP 法进行企业总平面布置的首要工作是对各作业单位之间的相互关系做出分析,包括物流和非物流的相互关系,经过综合得到作业单位相互关系表。
然后,根据相互关系表中作业单位之间相互关系的密切程度,决定各作业单位之间距离的远近,安排各作业单位的位置,绘制作业单位位置相关图。
将各作业单位实际占地面积与作业单位位置相关图结合起来,形成作业单位面积相关图。
通过作业单位面积相关图的修正和调整,得到数个可行的布置方案,然后采用加权因素对各方案进行评价择优,并对每个因素进行量化,以得分最多的布置方案作为最佳布置方案。
二、系统布置设计阶段划分(1)位置确定。
确定所在布置的相对位置(总体位置)。
(2)总体区划。
在布置区域内确定一个总体布局(重要阶段)。
(3)详细布置。
确定各个作业单位或各个设施的具体位置。
(4)布置实施。
编制计划,进行系统布置的实施。
系统布置设计阶段程序见图6.1系统布置设计阶段图。
三、系统布置设计影响因素影响布置设计的因素众多,以其基本要素可归类为5项,即P(Product)产品(或材料或服务)、Q(Quantity)数量(或产量)、R(Route)生产路线(工艺过程)、S(Supporting Service)辅助服务部门、T(Time)时间(或时间安排)。
课件--系统布置设计(SLP)及案例分享

按产品产量多少
多品种小批量生产
生
产 类
按产品产量的连续程度
型
按产品预测程度分
定制生产 单件小批生产
成批生产 大量生产 订货生产 存货生产
第三节 系统布置设计(SLP)模式
• 一、阶段结构与程序模式 • 二、系统布置设计的基本要素 • 三、产品产品分析(P-Q分析) • 四、物流分析(R分析) • 五、作业单位相互关系分析 • 六、作业单位位置相关图 • 七、面积的确定 • 八、布置设计 • 九、布置方案的评价与选择
二、设施规划与设计的研究范围
• 设施规划的内容
– 厂(场)址选择
就是对可供选择的地区和具体位置的有关影响因素进行分析和评价,达 到厂(场)址最优化。
二、设施规划与设计的研究范围
• 设施规划的内容
– 设施布置设计
就是通过对系统物流、人流、信息流进行分析,对建筑物、机器、设备、 运输通道和场地作出有机的组合与合理配置,达到系统布置最优化。 对系统的各组成部分进行位置布置是设施规划与设计的中心内容。
272
包装
ABC128 128
成品
0
合计 0 104 188 252 592 560 192 128 2016
四、物流分析
• 物流分析与物流相关表
–P-Q关系决定了所采用的初步物流分析的方式: 当产品品种很少但产量很大时,应采用工艺过 程图进行物流分析;
–随着产品品种增加,可以利用多种产品工艺过 程表或从-至表来统计具体物流量大小。
1.物流
3.相互关系图解
2.作业单位相互关系
作业单位位 置相关图
作业单位关系密 级及相互关系表
分析阶段
4.所需面积
5.可用面积
SLP资料
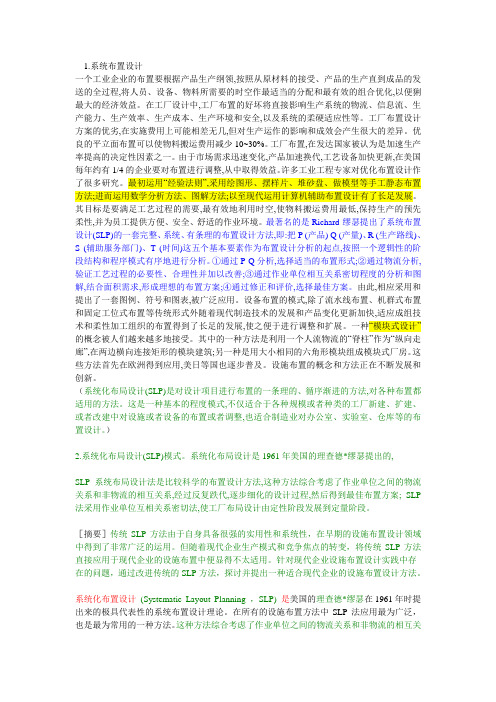
1.系统布置设计一个工业企业的布置要根据产品生产纲领,按照从原材料的接受、产品的生产直到成品的发送的全过程,将人员、设备、物料所需要的时空作最适当的分配和最有效的组合优化,以便猁最大的经济效益。
在工厂设计中,工厂布置的好坏将直接影响生产系统的物流、信息流、生产能力、生产效率、生产成本、生产环境和安全,以及系统的柔硬适应性等。
工厂布置设计方案的优劣,在实施费用上可能相差无几,但对生产运作的影响和成效会产生很大的差异。
优良的平立面布置可以使物料搬运费用减少10~30%。
工厂布置,在发达国家被认为是加速生产率提高的决定性因素之一。
由于市场需求迅速变化,产品加速换代,工艺设备加快更新,在美国每年约有1/4的企业要对布置进行调整,从中取得效益。
许多工业工程专家对优化布置设计作了很多研究。
最初运用“经验法则”,采用绘图形、摆样片、堆砂盘、做模型等手工静态布置方法;进而运用数学分析方法、图解方法;以至现代运用计算机辅助布置设计有了长足发展。
其目标是要满足工艺过程的需要,最有效地利用时空,使物料搬运费用最低,保持生产的预先柔性,并为员工提供方便、安全、舒适的作业环境。
最著名的是Richard·缪瑟提出了系统布置设计(SLP)的一套完整、系统、有条理的布置设计方法,即:把P (产品) Q (产量)、R (生产路线)、S (辅助服务部门)、T (时间)这五个基本要素作为布置设计分析的起点,按照一个逻辑性的阶段结构和程序模式有序地进行分析。
①通过P-Q分析,选择适当的布置形式;②通过物流分析,验证工艺过程的必要性、合理性并加以改善;③通过作业单位相互关系密切程度的分析和图解,结合面积需求,形成理想的布置方案;④通过修正和评价,选择最佳方案。
由此,相应采用和提出了一套图例、符号和图表,被广泛应用。
设备布置的模式,除了流水线布置、机群式布置和固定工位式布置等传统形式外随着现代制造技术的发展和产品变化更新加快,适应成组技术和柔性加工组织的布置得到了长足的发展,使之便于进行调整和扩展。
系统布置设计(SLP)模式
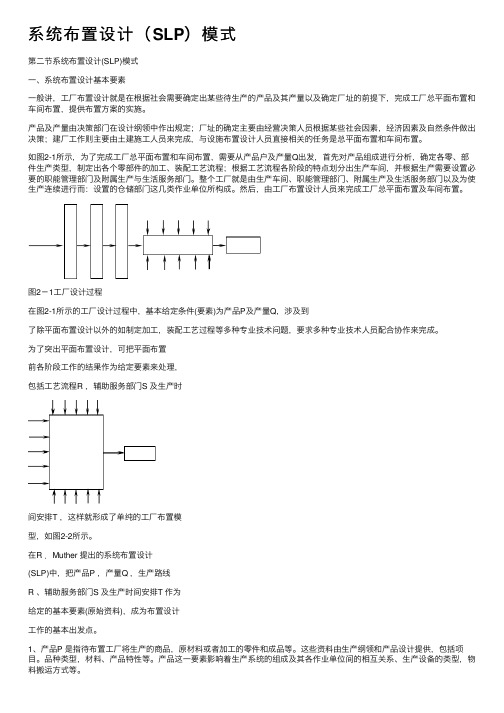
系统布置设计(SLP)模式第⼆节系统布置设计(SLP)模式⼀、系统布置设计基本要素⼀般讲,⼯⼚布置设计就是在根据社会需要确定出某些待⽣产的产品及其产量以及确定⼚址的前提下,完成⼯⼚总平⾯布置和车间布置,提供布置⽅案的实施。
产品及产量由决策部门在设计纲领中作出规定;⼚址的确定主要由经营决策⼈员根据某些社会因素,经济因素及⾃然条件做出决策;建⼚⼯作则主要由⼟建施⼯⼈员来完成,与设施布置设计⼈员直接相关的任务是总平⾯布置和车间布置。
如图2-1所⽰,为了完成⼯⼚总平⾯布置和车间布置,需要从产品户及产量Q出发,⾸先对产品组成进⾏分析,确定各零、部件⽣产类型,制定出各个零部件的加⼯、装配⼯艺流程;根据⼯艺流程各阶段的特点划分出⽣产车间,并根据⽣产需要设置必要的职能管理部门及附属⽣产与⽣活服务部门。
整个⼯⼚就是由⽣产车间、职能管理部门、附属⽣产及⽣活服务部门以及为使⽣产连续进⾏⽽:设置的仓储部门这⼏类作业单位所构成。
然后,由⼯⼚布置设计⼈员来完成⼯⼚总平⾯布置及车间布置。
图2-1⼯⼚设计过程在图2-1所⽰的⼯⼚设计过程中,基本给定条件(要素)为产品P及产量Q,涉及到了除平⾯布置设计以外的如制定加⼯,装配⼯艺过程等多种专业技术问题,要求多种专业技术⼈员配合协作来完成。
为了突出平⾯布置设计,可把平⾯布置前各阶段⼯作的结果作为给定要素来处理,包括⼯艺流程R ,辅助服务部门S 及⽣产时间安排T ,这样就形成了单纯的⼯⼚布置模型,如图2-2所⽰。
在R .Muther 提出的系统布置设计(SLP)中,把产品P ,产量Q ,⽣产路线R 、辅助服务部门S 及⽣产时间安排T 作为给定的基本要素(原始资料),成为布置设计⼯作的基本出发点。
1、产品P 是指待布置⼯⼚将⽣产的商品,原材料或者加⼯的零件和成品等。
这些资料由⽣产纲领和产品设计提供,包括项⽬。
品种类型,材料、产品特性等。
产品这⼀要素影响着⽣产系统的组成及其各作业单位间的相互关系、⽣产设备的类型,物料搬运⽅式等。
基于SLP方法的钢铁物流园区平面布置规划

基于SLP方法的钢铁物流园区平面布置规划一、概述随着全球经济的持续发展和产业结构的不断调整,钢铁行业作为国民经济的重要支柱,其物流运作的效率和成本对整个行业的竞争力具有决定性影响。
钢铁物流园区作为钢铁产业供应链的重要环节,其平面布置规划的合理性直接关系到园区的物流运作效率、成本控制以及可持续发展能力。
对钢铁物流园区的平面布置规划进行优化,成为提升钢铁产业整体竞争力的关键。
基于SLP(Systematic Layout Planning,系统布置设计)方法的钢铁物流园区平面布置规划,是一种科学、系统的规划方法。
SLP 方法通过对园区的物流活动、物料流量、作业单位之间的相互关系进行深入分析,结合定性和定量的分析方法,为园区的平面布置提供优化方案。
这种方法既考虑了园区的当前运营需求,也兼顾了未来的发展潜力,为钢铁物流园区的可持续发展奠定了坚实基础。
本文旨在探讨基于SLP方法的钢铁物流园区平面布置规划的理论基础、实施步骤以及实际应用效果。
通过深入分析钢铁物流园区的特点和需求,结合国内外相关研究的最新成果,构建适用于钢铁物流园区的SLP规划模型。
同时,结合具体案例,对规划模型的应用效果进行评估,以期为钢铁物流园区的平面布置规划提供有益的参考和借鉴。
二、系统布置设计(SLP)方法概述系统布置设计(Systematic Layout Planning,SLP)是一种久负盛名的经典方法,广泛应用于各种设施规划中,包括工厂、物流园区等。
SLP方法的基本原理是通过系统分析、模拟和评估,以最小化物流流程中不必要的距离、时间和能量消耗为目标,从而提高物流效率。
在SLP方法中,首先需要建立一个相关图,用于表示各部门之间的密切程度。
相关图类似于车间之间的物流图,需要使用试算法进行调整,直到得到满意的方案为止。
根据建筑的容积来合理安排各个部门的位置。
为了便于对布置方案进行评价,SLP方法还需对方案进行量化,根据密切程度的不同赋予权重,然后试验不同的布置方案,最后选择得分最高的布置方案。
- 1、下载文档前请自行甄别文档内容的完整性,平台不提供额外的编辑、内容补充、找答案等附加服务。
- 2、"仅部分预览"的文档,不可在线预览部分如存在完整性等问题,可反馈申请退款(可完整预览的文档不适用该条件!)。
- 3、如文档侵犯您的权益,请联系客服反馈,我们会尽快为您处理(人工客服工作时间:9:00-18:30)。
第二节系统布置设计(SLP)模式
一、系统布置设计基本要素
一般讲,工厂布置设计就是在根据社会需要确定出某些待生产的产品及其产量以及确定厂址的前提下,完成工厂总平面布置和车间布置,提供布置方案的实施。
产品及产量由决策部门在设计纲领中作出规定;厂址的确定主要由经营决策人员根据某些社会因素,经济因素及自然条件做出决策;建厂工作则主要由土建施工人员来完成,与设施布置设计人员直接相关的任务是总平面布置和车间布置。
如图2-1所示,为了完成工厂总平面布置和车间布置,需要从产品户及产量Q出发,首先对产品组成进行分析,确定各零、部件生产类型,制定出各个零部件的加工、装配工艺流程;根据工艺流程各阶段的特点划分出生产车间,并根据生产需要设置必要的职能管理部门及附属生产与生活服务部门。
整个工厂就是由生产车间、职能管理部门、附属生产及生活服务部门以及为使生产连续进行而:设置的仓储部门这几类作业单位所构成。
然后,由工厂布置设计人员来完成工厂总平面布置及车间布置。
图2-1工厂设计过程
在图2-1所示的工厂设计过程中,基本给定条件(要素)为产品P及产量Q,涉及到
了除平面布置设计以外的如制定加工,装配工艺过程等多种专业技术问题,要求多种专业技术人员配合协作来完成。
为了突出平面布置设计,可把平面布置
前各阶段工作的结果作为给定要素来处理,
包括工艺流程R ,辅助服务部门S 及生产时
间安排T ,这样就形成了单纯的工厂布置模
型,如图2-2所示。
在R .Muther 提出的系统布置设计
(SLP)中,把产品P ,产量Q ,生产路线
R 、辅助服务部门S 及生产时间安排T 作为
给定的基本要素(原始资料),成为布置设计
工作的基本出发点。
1、产品P 是指待布置工厂将生产的商品,原材料或者加工的零件和成品等。
这些资料由生产纲领和产品设计提供,包括项目。
品种类型,材料、产品特性等。
产品这一要素影响着生产系统的组成及其各作业单位间的相互关系、生产设备的类型,物料搬运方式等。
2、产量Q
产量指所生产的产品的数量,也由生产纲领和产品设计提供,可用件数,重量、体积等来表示。
产量Q 这一要素影响着生产系统的规模,设备的数量、运输量、建筑物面积的大小等。
3、生产路线R
为了完成产品的加工,必须制定加工工艺艺流程,形成生产路线,可用工艺过程表(卡)、工艺过程图、设备表等表示,它影响着各作业单位之间的关系、物料搬运路线、仓库及堆放地的位置等。
4、辅助服务部门S
在实施系统布置工作以前,必须对生产系统的组成情况有一个总体的规划,可以大体上分为生产车间、职能管理部门、辅助生产部门,生活服务部门及仓储部门等;可以把除生产车间以外的所有作业单位统称为辅助服务部门S ,包括工具,维修、动力、收货、发运、铁路专用路线、办公室、食堂等,这些作业单位构成生产系统的生产支持系统部分,在某种意义上加强了生产能力。
有时,辅助服务部门的占地总面积接近甚至大于生产车间所占面积,所以布置设计时应给予
定量约束条件
定性约束条件 图2-2 工厂布置模型
足够的重视。
5、时间T
时间要素是指在什么时侯,用多少时间生产出产品,包括各工序的操作时间,更换批量的次数。
在工艺过程设计中,根据时间因素确定生产所需各类设备的数量,占地面积的大小和操作人员数量,来平衡各工序的生产时间。
二、系统布置设计模式
任何一种系统设计过程都是反复迭代,逐步细化的寻求最优解的过程,工厂布置设计更是如此.设计步骤的正确与否往往是工厂布置设计能否成功的关键,系统布置设计SLP模式就是一种人们广为采用的、成功的设计方法。
系统布置设计是一种逻辑性强、条理清楚的布置设计方法,分为确定位置、总体区划、详细布置及实施4个阶段,在总体区划和详细布置两个阶段采用相同的SLP设计程序。
1、确定位置(阶段工)
在新建、扩建或改建工厂或车间时,首先应确定出新厂房坐落的地区位置。
在这个阶段中,首先要明确待建工厂的产品、计划生产能力,参考同类工厂确定待建工厂的规模,从待选的新地区或现有工厂中确定出可供利用的厂址。
2、总体区划(阶段Ⅱ)。
总体区划又叫区域划分,就是在巳确定的厂址上规划出一个总体布局。
此阶段中,首先应明确各生产车间,职能管理部门、辅助服务部门及仓储部门等作业单位的工作任务与功能,确定其总体占地面积及外形尺寸。
在确定了各作业单位之间的相互关系后,把基本物流模式和区域划分结合起来进行布置。
3、详细布置(阶段Ⅲ)
详细布置一般是指一个作业单位内部机器及设备的布置。
在详细布置阶段,要根据每台设备、生产单元及公用、服务单元的相互关系,确定出各自的位置。
4,实施(阶段Ⅳ)
在完成详细布置设计后,经上级批准可以进行施工设计,绘制大量的详细安装图,编制搬迁,安装计划,按计划进行机器设备及辅助装置的搬迁、安装施工工作。
在系统布置设计过程中,上述4个阶段的顺序交叉进行。
在确定位置阶段,就必须大体确定各主要部门的外形尺寸,以便确定工厂总体形状柑占地面积;在总体区划阶段,就有必要对某些影响重大的作业单位进行较详细的布置。
整个设计过程中,随着阶段的进展,数据资料逐步齐全,从而能发现前期设计中存在的问题,通过调整修正,逐步细化完善设计。
在系统布置设计4个阶段中,阶段I与阶段Ⅳ由其它专业人员负责,系统布置设计人员应积极参与;阶段Ⅱ和阶段Ⅲ由系统布置设计人员来完成。
因此,可以说工厂布置包括工厂总平面布置(总体区划)及车间布置或车间平面布置(详细布置)两项内容。
在系统布置设计阶段Ⅱ和阶段Ⅲ,采用相同的设计步骤——系统布置设计SLP程序。
在SLP程序中,一般经过下列步骤:
(1)准备原始资料在系统布置设计开始时,首先必须明确给出基本要素——产品P,产量Q、生产工艺过程R、辅助服务部门S及时间安排T等这些原始资料,同时也需要对作业单位的划分情况进行分析,通过分解与合并,得到最佳的作业单位划分状况。
所有这些均作为系统布置设计的原始资料。
(2)物流分析与作业单位相互关系分析针对某些以生产流程为主的工厂,物料移动是工艺过程的主要部分时,如一般的机械制造厂,物流分析是布置设计中最重要的方面;对某些辅助服务部门或某些物流量较小的工厂,各作业单位之间的相互关系(非物流联系):对布置设计就显得更重要;介于上述两者之间的情况,则需要综合考虑作业单位之间物流与非物流的相互关系。
物流分析的结果可以用物流强度等级及物流相关表来表示。
非物流的作业单位间的相互关系可以用关系密级及相互关系表来表示。
在需要综合考虑作业单位间物流与非物流的相互关系时,可以采用简单加权的方法将物流相关表及作业单位间相互关系表综合成综合相互关系表。
(3)绘制作业单位位置相关图根据物流相关表与作业单位相互关系表,考虑每对作业单位间相互关系等级的高低,决定两作业单位相对位置的远近,得出各作业单位之间的相对位置关系,有些资料上也称之为拓朴关系。
这时并未考虑各作业单位具体的占地面积,从而得到的仅是作业单位位置相关图。
(4)作业单位占地面积计算各作业单位所需占地面积与设备、人员、通道及辅助装置等有关,计算出的面积应与可用面积相适应。
.(5)绘制作业单位面积相关图把各作业单位占地面积附加到作业单位位置相关图上,就形成了作业单位面积相关图。
(6)修正作业单位面积相关图只是一个原始布置图,还需要根据其它因素进行调整与修正。
此时需要考虑的修正因素包括物料搬运方式、操作方式、储存周期等,同时还需要考虑实际限制条件,如成本、安全和职工倾向等方面是否允许。
考虑了各种修正因素与实际限制条件后,对面积图进行调整,得出数个有价值的可行方案。
(7)方案评价与择优针对得到的数个方案,需要进行费用及其他因素评价。
通过对各方案的比较评价,选出或修正设计方案,得到布置方案图。