粉煤气化机理
HT-L粉煤气化简介
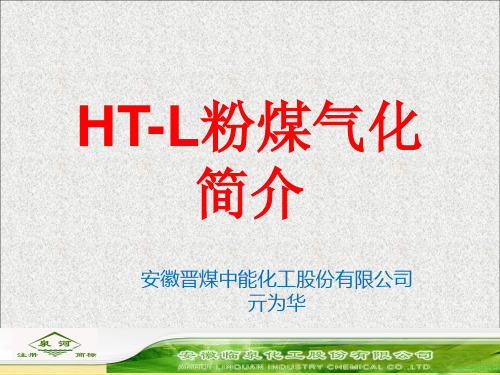
C + O2 = CO2 + 402kJ/mol
2C + O2 = 2CO + 237kJ/mol C + CO2 = 2CO - 165kJ/mol
2CO + O2 = 2CO2 + 567kJ/mol
二、煤气化的基本原理
(一)炭与氧的化学反应
反应平衡常数
lnKp = -21000/T + 21.4
二、煤气化的基本原理
(五)煤炭气化过程速率
• 当气化温度很低时, β > > K
K总= β K /( β + K )= K
此时的反应为化学动力学控制。 提高温度、压力、浓度,改善催化剂等 ,能够加快过程速率。
二、煤气化的基本原理
(五)煤炭气化过程速率
• 当气化温度很高时, K > > β
K总= β K /( β + K )= β
此时的反应为扩散控制。 提高压力、浓度,流速,减小颗粒度等 ,能够加快过程速率。
800~1200℃时CO/CO2的浓度
浓 度 CO
2
CO
距碳粒表面的距离
1200~1400℃时CO/CO2的浓度
浓 度 CO CO2
距碳粒表面的距离
三、煤炭气化工艺分类
移动床气化
• 煤料与炉体相对静止,靠重力下降 • 煤料在炉内停留时间以小时计
原料 煤仓 原煤 粉煤袋 式过滤 器 粉煤 螺旋输送机 螺旋给料器
称重给煤机
磨煤 机
惰性气体 发生器
循环风机
(一)磨煤及干燥单元
3、主要设备
原 煤 原料 煤仓 粉煤 袋式 过滤 器
原 料 煤 仓
称重给煤机
粉 煤 螺旋 输送 机
煤气化原理

报告人:吴奎
日期:2015年11月14日
1
目录
一、煤的组成及用途
二、煤气化的定义
三、煤气化的发展
四、煤气化的原理 五、三种炉型的简介
2
煤的组成及用途
煤炭:复杂的有机含碳矿物,以碳为主,主要成分为C,H,O,N,S。 根据煤中挥发分的含量,将所有的煤分为无烟煤、烟煤、褐煤。 一代炉(循环流化床)用煤为烟煤,挥发分(V)含量为29-31%,固定碳(FC)为 49-54%,灰分(A)为8-11%,水分(M)为13-14%。 二代炉(低压粉煤气流床气化炉)以循环流化床产生的飞灰为气化原料,飞灰的工 业分析:A为40-42%,FC为57-59%。(水分,挥发分含量忽略不计) 用途 能源 燃烧发电
6
煤气化的基本原理
煤的气化就是以煤、半焦或焦炭为原料,以空气、富氧(纯氧)、水蒸气、二 氧化碳为气化介质,使煤经过部分氧化和还原反应,将其中所含碳、氢等物质 转化成为一氧化碳、氢气、甲烷等可燃组分为主的气体产物的多相反应过程。
在气化炉中,煤炭一般经历干燥、干馏、气化、燃烧等过程。
7
干燥:是指煤炭的物理脱水过程,原料煤加入气化炉后,由于煤与热气流或 炽热的半焦之间发生热交换,使煤中的水分蒸发变成蒸汽进入气相。
制合成气(CO+H2)
一代炉:H2 24-25% CO 22-24% CO2 11-12% CH4 2.4-3% N2 36-38% 二代炉 : H2 5-6% CO 70-74% CO2 3-4% CH4 1.4-1.6% N2 16-17%
原料
制燃料气(CH4,CO,H2) 炼焦(冶金焦,铁合金焦)
有害物质
4
煤气化是指煤在特定的设备内,在一定的压力、温度下,用气化剂对煤进行 热化学加工,将煤中有机质转变为煤气的过程。 气化炉 供给热量
灰熔聚流化床粉煤气化技术原理

灰熔聚流化床粉煤气化技术原理摘要:煤气化是将固态煤转化为气态燃料或化工合成原料(CO+H2)的过程,由于煤炭的储量丰富,特别是我国等一些国家富煤少油贫气,煤气化技术就变的更加重要。
一、灰熔聚流化床粉煤气化技术的开发历程针对我国能源以煤为主、煤种多、烟煤多、粉煤多、煤灰份高、灰熔点高的特点,国家从“六五”计划开始投入大量人力、物力,研制开发先进煤气化技术(包括固定床、流化床、气流床)。
中科院山西煤化所积极地进行了灰熔聚流化床粉煤气化技术的研发。
八十年代,在中国科学院(重点科技攻关项目专项)、国家科委(75-10-05)攻关计划支持下,在原有煤气化和流化床技术的基础上,先后建立了φ300mm(1吨煤/天)气化试验装置、φ1000mm冷态试验装置、φ1000mm(0.1~0.5 MPa ,24吨煤/天)中间试验装置、φ145mm实验室煤种评价试验装置。
在理论研究、冷态模试、实验室小试和中试试验基础上,系统地研究了灰熔聚流化床粉煤气化过程中的理论和工程放大特性;通过对气化过程中煤化学、灰化学与气固流体力学的研究,研制了特殊结构的射流分布器,创造性地解决了强烈混合状态下煤灰团聚物与半焦选择性分离等重大技术难题;设计了独特的“飞灰”可控循环新工艺,实现了多种煤的高效流化床气化。
通过对工艺过程的系统集成和优化,在大量的实验验证基础上,取得了完整的工业放大数据和丰富的运行经验,成功开发了灰熔聚流化床粉煤气化技术。
九十年代,在中国科学院(重点科研项目)、国家计委(85-207)攻关计划支持下,建立了φ200mm(1.0~1.5MPa)加压试验装置和φ2400mm常压工业示范装置。
氧/蒸汽鼓风制化工合成气的中试研究,为工业示范装置提供了准确的工程设计方法和依据;2001年单炉配套2万吨合成氨/年规模工业示范装置成功运行,实现了该技术的工业化应用,为我国中小化肥厂改变原料路线提供了具有自主知识产权的先进煤气化技术,现已能设计单台处理量100~300吨煤/日的气化炉(0.03~0.5MPa,φ2.4米,配套2~6万吨合成氨/年)。
第二章 煤气化原理 PPT

煤气:固体燃料气化后得到的可燃 性气体。
进行气化反应的设备称煤气发生炉。
一、气化过程主要化学反应
煤炭气化过程的反应可分成两种类型。 1)非均相气体-固体反应,气相可以是最初的气化剂,
也可能是气化过程的产物,固相是指煤中的碳。虽然煤具 有很复杂的分子结构,和碳原子相连接着的还有氢、氧等 其它元素,但因为气化反应往往发生在煤裂解之后,故只 考虑煤中主要元素碳是合理的。 2)均相的气相反应,反应物可能是气化剂,也可能是反应 产物。
煤气化时发生的硫(S)和氮(N)的基本反应
元素反应 S: S+O2=SO2 SO2+3H2= H2S+2H2O SO2+2CO=S+2CO2 2H2S+SO2 =3S+2H2O C+2S=CS2 CO+S=COS
N: N2+3H2=2NH3 N2+H2O+2CO=2HCN+1.5O2 N2+xO2=2NOx
煤 加热
+o2完全氧化 燃烧
密闭 干馏
+ H2O或H2 + 部分O2 气化
干燥过程也是煤炭脱水过程,它是一个物理过程,原料煤加入气
第二章 煤气化原理 化炉后,由于煤与热气流或炽热的半焦之间发生热交换,使煤中 的水分蒸发变成蒸汽进入气相。
干馏是脱除挥发分过程,当干燥煤的温度进一步提高,挥发物
煤气化主要包括从以煤中下逸四出个。脱过除程挥:发分一般也称作煤的热分解反应,它是所
二、地面气化技术的分类 在气化过程中,煤由气化炉顶部加入,气化剂由气化炉底部
加入,煤料与气化剂逆流接触,相对于气体的上升速度而言
气化工艺

气化工艺一、煤气化的基本原理1、气化过程一般包括干燥、热解、气化及燃烧4个阶段煤气化过程中的基本化学反应序号反应方程式⊿H(298K,0.1MPa)/kJ.mol-1备注1 C+O2=CO2-393.5 碳完全燃烧2 C+1/2O2=CO -110.5 碳不完全燃烧3 C+H2O=CO+H2131.3 水蒸气气化4 C+CO2=2CO 172.5 Boudouard反应5 C+2H2=CH4-74.4 碳加氢气化6 H2+1/2O2=H2O -241.8 氢气燃烧7 CO+1/2O2=CO2-283 一氧化碳燃烧8 CO+H2O=CO2+H2-41.2 水煤气变换9 CO+3H2=CH4+H2O -205.7 甲烷化反应10 CHxOy=(1-y)C+yCO+x/2H217 煤热解11 CHxOy=(1-y-x/8)C+yCO+x/4H2+x/8CH48 煤热解此外,煤中的氮和硫也会与气化剂中的氧气和水蒸气以及反应产物之间发生一些化学反应序号反应方程式序号反应方程式1 S+O2=SO2 6 CO+S=COS2 SO2+3H2=H2S+2H2O 7 N2+3H2=2NH33 SO2+2CO=S+2CO28 2N2+2H2O+4CO=4HCN+3O24 SO2+2H2S=3S+2H2O 9 N2+xO2=2NOx5 C+2S=CS2重点的几个主要气化反应1)碳与水蒸气的反应高温下,碳与水蒸气的反应(即水蒸气气化反应主要为:C+H2O=CO+H2—Q1 (1)C+2H2O=CO2+H2—Q2 (2)这两个反应都是强吸热反应。
提高温度有利于(1)的反应,有利于提高CO的含量和降低CO2的含量。
2)碳与二氧化碳的反应碳与二氧化碳的反应(即二氧化碳的还原反应)也是强的吸热反应,反应所需吸收的热量更多,表明温度的影响更为强烈C+CO2=2CO —Q.33)碳的加氢反应碳加氢直接合成甲烷(即加氢气化反应)实枪的放热反应。
粉煤加压气化技术
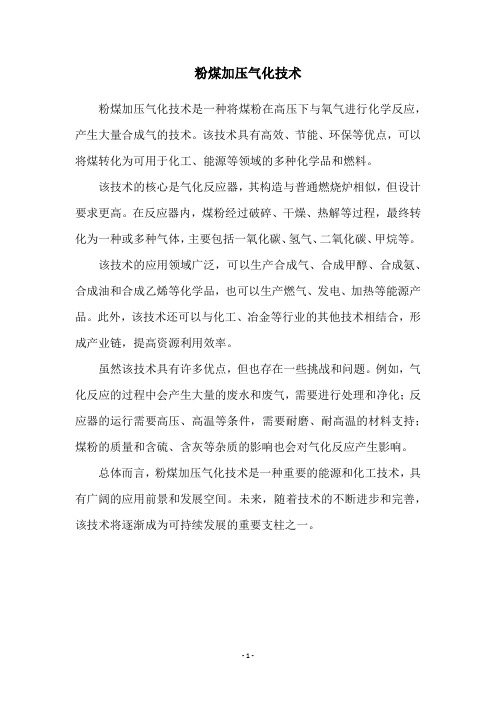
粉煤加压气化技术
粉煤加压气化技术是一种将煤粉在高压下与氧气进行化学反应,产生大量合成气的技术。
该技术具有高效、节能、环保等优点,可以将煤转化为可用于化工、能源等领域的多种化学品和燃料。
该技术的核心是气化反应器,其构造与普通燃烧炉相似,但设计要求更高。
在反应器内,煤粉经过破碎、干燥、热解等过程,最终转化为一种或多种气体,主要包括一氧化碳、氢气、二氧化碳、甲烷等。
该技术的应用领域广泛,可以生产合成气、合成甲醇、合成氨、合成油和合成乙烯等化学品,也可以生产燃气、发电、加热等能源产品。
此外,该技术还可以与化工、冶金等行业的其他技术相结合,形成产业链,提高资源利用效率。
虽然该技术具有许多优点,但也存在一些挑战和问题。
例如,气化反应的过程中会产生大量的废水和废气,需要进行处理和净化;反应器的运行需要高压、高温等条件,需要耐磨、耐高温的材料支持;煤粉的质量和含硫、含灰等杂质的影响也会对气化反应产生影响。
总体而言,粉煤加压气化技术是一种重要的能源和化工技术,具有广阔的应用前景和发展空间。
未来,随着技术的不断进步和完善,该技术将逐渐成为可持续发展的重要支柱之一。
- 1 -。
粉煤加压气化工艺流程
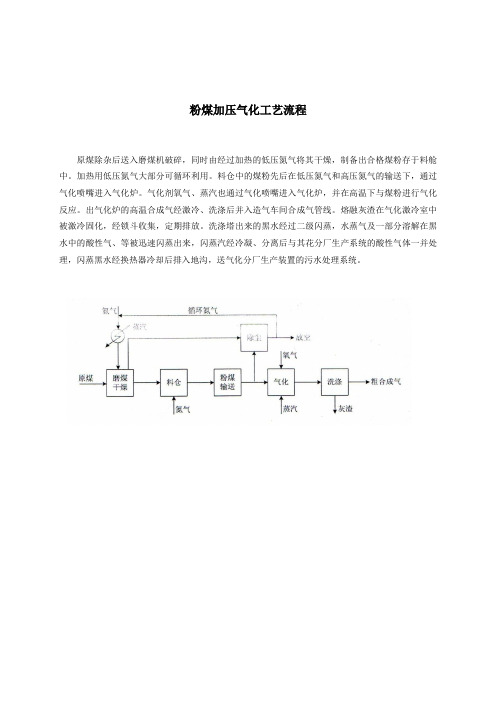
粉煤加压气化工艺流程
原煤除杂后送入磨煤机破碎,同时由经过加热的低压氮气将其干燥,制备出合格煤粉存于料舱中。
加热用低压氮气大部分可循环利用。
料仓中的煤粉先后在低压氮气和高压氮气的输送下,通过气化喷嘴进入气化炉。
气化剂氧气、蒸汽也通过气化喷嘴进入气化炉,并在高温下与煤粉进行气化反应。
出气化炉的高温合成气经激冷、洗涤后并入造气车间合成气管线。
熔融灰渣在气化激冷室中被激冷固化,经锁斗收集,定期排放。
洗涤塔出来的黑水经过二级闪蒸,水蒸气及一部分溶解在黑水中的酸性气、等被迅速闪蒸出来,闪蒸汽经冷凝、分离后与其花分厂生产系统的酸性气体一并处理,闪蒸黑水经换热器冷却后排入地沟,送气化分厂生产装置的污水处理系统。
煤炭气化原理

煤炭气化原理煤炭气化是指煤在特定的设备内,在一定温度及压力下使煤中有机质与气化剂(如蒸汽/空气或氧气等)发生一系列化学反应,将固体煤转化为含有CO、H2、CH4等可燃气体和CO2、N2等非可燃气体的过程。
煤炭气化时,必须具备三个条件,即气化炉、气化剂、供给热量,三者缺一不可。
气化原料为各种煤或焦炭。
煤炭气化包含一系列物理、化学变化。
一般包括热解和气化和燃烧四个阶段。
干燥属于物理变化,随着温度的升高,煤中的水分受热蒸发。
其他属于化学变化,燃烧也可以认为是气化的一部分。
煤在气化炉中干燥以后,随着温度的进一步升高,煤分子发生热分解反应,生成大量挥发性物质(包括干馏煤气、焦油和热解水等),同时煤粘结成半焦。
煤热解后形成的半焦在更高的温度下与通入气化炉的气化剂发生化学反应,生成以一氧化碳、氢气、甲烷及二氧化碳、氮气、硫化氢、水等为主要成分的气态产物,即粗煤气。
气化反应包括很多的化学反应,主要是碳、水、氧、氢、一氧化碳、二氧化碳相互间的反应,其中碳与氧的反应又称燃烧反应,提供气化过程的热量。
主要反应有:1、水蒸气转化反应C+H2O=CO+H2-131KJ/mol2、水煤气变换反应CO+ H2O =CO2+H2+42KJ/mol3、部分氧化反应C+0.5 O2=CO+111KJ/mol4、完全氧化(燃烧)反应C+O2=CO2+394KJ/mol5、甲烷化反应CO+2H2=CH4+74KJ/mol6、Boudouard反应C+CO2=2CO-172KJ/mol气化过程发生的反应包括煤的热解、气化和燃烧反应。
煤的热解是指煤从固相变为气、固、液三相产物的过程。
煤的气化和燃烧反应则包括两种反应类型,即非均相气-固反应和均相的气相反应。
气化过程发生的反应包括煤的热解、气化和燃烧反应。
煤的热解是指煤从固相变为气、固、液三相产物的过程。
煤的气化和燃烧反应则包括两种反应类型,即非均相气-固反应和均相的气相反应。
不同的气化工艺对原料的性质要求不同,因此在选择煤气化工艺时,考虑气化用煤的特性及其影响极为重要。
- 1、下载文档前请自行甄别文档内容的完整性,平台不提供额外的编辑、内容补充、找答案等附加服务。
- 2、"仅部分预览"的文档,不可在线预览部分如存在完整性等问题,可反馈申请退款(可完整预览的文档不适用该条件!)。
- 3、如文档侵犯您的权益,请联系客服反馈,我们会尽快为您处理(人工客服工作时间:9:00-18:30)。
粉煤气化机理一、气化反应热力学粉煤加压气化炉是气流床反应器,也称之为自热式反应器,在加压无催化剂条件下,煤和氧气发生部分氧化反应,生成以CO和H2为有效组分的粗合成气,部分氧化反应一词是相对完全氧化而言的。
整个部分氧化反应是一个复杂的多种化学反应过程。
此反应的机理目前尚不能完全作以分析。
我们只可以大致把它分为三步进行。
第一步:裂解及挥发分燃烧。
当粉煤和氧气喷入气化炉内后,迅速被加热到高温,粉煤发生干馏及热裂解,释放出焦油、酚、甲醇、树脂、甲烷等挥发分,水分变成水蒸气,粉煤变成煤焦。
由于这一区域氧气浓度高,在高温下挥发分完全燃烧,同时放出大量热量。
因此,煤气中不含有焦油、酚、高级烃等可凝聚物。
第二步:燃烧及气化。
在这一步,煤焦一方面与剩余的氧气发生燃烧反应,生成CO2和CO等气体,放出热量。
另一方面,煤焦和水蒸气和CO2发生气化反应,生成H2和CO。
在气相中,H2和CO又与残余的氧气发生燃烧反应,放出更多的热量。
第三步:气化。
此时,反应物中几乎不含有O2。
主要是煤焦、甲烷等和水蒸气、CO2发生气化反应,生成H2和CO。
其总反应可写为:C n H m + (n/2)O2 →nCO + (m/2)H2 + Q气化炉中发生的主要反应可分为:①非均相水煤气反应 C + 2H2O →2H2 + CO2 - Q②变换反应CO + H2O →CO2 + H2 + Q③甲烷化反应CO +3 H2 →H2O + CO2 + Q④加氢反应 C + 2 H2 →CH4 +Q⑤部分氧化反应 C + 1/2O2 →CO + Q⑥氧化反应 C + O2 →CO2 + Q⑦CO2还原反应 C + CO2 →2CO – Q⑧热裂解反应C n H m →(n/4)CH4 + [(4m-n)/4]C - Q气化炉内的反应相当复杂,既有气相反应,又有气-固双相反应,对于复杂物系的平衡,我们引入独立反应数的概念,只要讨论独立反应即可。
因为其他反应可通过独立反应的组合而替代。
所谓独立反应数,就是构成物系的物质数与构成物质的元素种数之差。
假定煤气化反应在气化炉出口组成达到平衡,气体中含有CO2、CO、H2、O2、H2S、CH4、COS和C等八中物质,而这些物质是由C、H、O和S等四种元素构成,因此,气化反应只有四个独立反应,也就是说,在上述的反应中,我们只要讨论其中任意四个反应就够了。
另外,对于煤气化来说,S含量很低,基本上是一确定值(对于生成H2S、COS的比值),这样独立反应数就只有三个了。
由于碳转化率在98%以上,于是独立反应数就只有两个了。
所以,对于煤气化反应,只着重讨论变换反应和甲烷化反应两个反应。
煤气化反应的化学平衡:①变换反应的化学平衡CO + H2O →CO2 + H2 + 9838Kcal/Kmol平衡常数计算式如下:K P=PCO2*PH2/PCO*PH2O 式中:K P为该反应平衡常数。
PCO2、PH2、PCO、PH2O分别表示CO2、H2、CO、H2O的平衡分压。
LgK P=2182/T – 0.0936LgT+0.000632T – 1.0806×10-7T2-2.2967式中:T 为平衡温度。
从平衡上讲,变换反应为放热反应,降低温度对平衡有利。
但在高温条件下,CO 变换反应接近平衡。
②甲烷化反应的化学平衡CO +3H2→CH4 + H2O +49.271 Kcal/Kmol平衡常数计算式如下:K P=P CH4*P H2O/P CO*P3H2 式中:K为该反应平衡常数。
P CH4、P H2O、P CO、P H2P分别表示CH4、H2O、CO、H2的平衡浓度。
LgK p=9859.6/T-8.3636LgT+2.08×10-3T-1.8716×10-7T2+11.888 式中:T 为平衡温度。
该反应为放热反应。
提高温度,甲烷浓度降低,反应有利于向生成CO和H2 的方向进行。
但增加压力,甲烷浓度也相应增加。
因为,甲烷化反应是体积缩小的反应。
煤气化总的反应是体积增大的反应,从化学平衡来讲,提高压力对平衡不利,但压力的提高增加了反应物的浓度,对提高反应速度是有利的。
二、气化过程动力学气化过程是一个复杂的过程。
它所涉及的化学反应很多,传递过程的作用也很重要。
气化反应的过程随煤种、反应时间的不同而不同。
因此对于气化过程的动力学作出唯一的明确的表述是很困难的。
只能做简要的叙述。
气化反应是气化剂(气体)与焦渣(固体)接触而发生的。
它的反应历程包括:①气化剂分子自气流向焦渣外壳扩散;②气化剂分子渗透过焦渣的外壳灰层而达到未反应的焦渣表面;③气化剂分子渗透到焦渣的毛细孔而到达焦渣的内表面;④气化剂分子与焦渣发生气化反应;⑤生成的产物循上述相反方向进行而扩散到气流中去。
气化反应速度的影响因素是很多的。
例如:气化炉内各个轴的气量,固体颗粒半径、外表面积、内表面积、孔径、孔的长度及毛细孔内所受的阻力的大小等等,因此国际上建立了许多的数学模型和相应的理论。
虽然模型和理论很多,但原则性的基础是一样的。
均认为气化剂分子在碳或焦渣表面上进行的反应过程可视为气化剂分子被吸附,吸附分子与碳反应,产品气体脱离灰层表面几步组成。
几个主要反应的动力学的讨论:①碳与氧之间的燃烧反应碳与氧之间反应,可生成CO2和CO,而CO2或CO与碳反应又可相互转化,氧与CO反应也可以生成CO2,这是个复杂反应。
其总结果可表示为:C + O2→2(λ-1)CO+(2-λ)CO2 λ是系统常数,它取决于反应条件。
从化学平衡考虑,无论是生成CO或CO2的反应都是不可逆反应。
因此随着温度的升高反应速度是加快的。
氧与碳之间的反应是氧被吸附在碳的表面进行的,因此反应速度与氧的覆盖有关。
当温度很低时,由于反应速度低,此时有可能表现出反应速度与氧分压无关,即为零级反应。
当温度升高,反应速度加快,氧的覆盖度就对反应速度起着决定作用,而显示出为氧分压的一级反应。
如果温度进一步提高,表面反应速度是如此快,决定因素是物质传递了。
此时煤的本身特性对燃烧速度就不再发生影响。
关于燃烧产物中CO和CO2的比例,尚无统一的见解,有一点是可以肯定的,氧压高,温度低,生成CO2的量就多。
燃烧反应是强放热反应,放热量与反应速度成正比,随温度的增加放热量增加特别剧烈。
另一方面,气化是自热平衡的,吸热、放热、热量损失及气体和渣等带走的热量必须相等,反应才能顺利进行,当散热量大或者原料温度很低,就会使燃烧反应速度大大下降,放热量也会下降,这样就会造成灰中残碳量增加,严重是还会熄火。
②碳与CO2的反应在气化炉内,燃烧反应的速度比气化的其它反应速度快得多,碳与CO2的反应普遍认为是由表面反应速度决定。
因此煤的特性和反应温度有决定性的影响。
煤中灰分组成与孔隙率对表观活化能也有显著的影响。
这表明毛细孔内扩散对过程有着控制作用。
CO2+C→2CO的反应是由CO2吸附、生成络合物、发生热分解、解析、生成CO几步组成。
CO2与碳的反应动力学对CO2浓度来说是由一级(浓度小时)到零级(浓度大时)之间变化。
压力大提高会使CO2的还原反应进行得更为强烈。
③碳与水蒸汽之间的反应碳与水蒸汽之间的反应在此处分为水蒸汽在碳表面的分解反应和一氧化碳变换反应。
水蒸汽在碳表面的分解反应:比较普遍的机理解释为水蒸汽被高温碳层吸附,并使水分子变形,碳和水分子中的氧形成中间络合物,氢离解析出;然后碳氧络合物依据温度的不同,形成不同比例的CO2和CO;也由于此比例的不同,而有不同的反应热效应。
研究结果表明,对于较小的粒度(d p<500µm)以及温度在1000~1200℃,则焦-H2O反应属化学动力学控制。
反应级数随水蒸汽分压而变化,当水蒸汽分压较低时,反应级数为1,当水蒸汽分压明显增加时,反应级数趋于零。
④生成甲烷的反应在气化炉内甲烷的生成是两个独立过程的总结果:一是煤的热解过程;一是煤的气化过程。
由碳生成甲烷的过程都是二次反应的结果,即依靠反应:C+2H2→CH4CO+3H2→CH4+H2OCO2+4H2→CH4+2H2O这些都是体积缩小的放热反应。
提高压力无论从平衡或反应速度都是有助于甲烷的生成。
碳生成甲烷的过程,实际上是分为两个阶段。
首先是煤热解产物中的新生碳与氢的快速甲烷化阶段,此阶段的时间是很短暂的,速度是很快的,要比气化速度快得多。
在快速生成甲烷阶段,生成速度与氢分压成正比,而与气化过程中正常情况下存在的其它气体无关。
热解时生成的碳所遭受的温度对反应活性有重大影响,温度愈高活性降低愈多,高于815℃就没有快速生成甲烷阶段。
生成甲烷的第二阶段是与水蒸汽和碳之间所进行的气化反应同时进行的。
可以认为这是高活性碳消失之后所进行的反应,其反应速度要低得多。
一般认为此阶段的反应速度与氢分压的关系在一级到二级反应之间,视氢分压的大小而定。
三、气化生产过程的强化措施工业上为了满足大规模生产煤气的需要,可采取两种方法:①增加煤气发生炉的几何尺寸或数量;②提高气化炉的气化强度。
后一种方法是最可取的,他可减少金属的消耗量和投资费用。
上述煤气化的理论基础,虽然还有一些尚不清楚的问题,但已对生产过程的强化指明了一定的方向。
不论是哪一种控制条件,减小固体粒度,即采用小颗粒煤炭,均可以提高反应速度和较快地达到高的转化率。
采用加压气化方法,较高的压力有利于提高反应物的浓度,反应速度总是随反应物的浓度增加而增加。
在加压下气化,气体体积缩小,煤气通过床层的速度减小,这就加长了各反应的反应时间,使反应接近平衡。
温度是强化生产的重要因素,一般情况下,提高温度均能急剧地增加表观速度,从而提高反应物的转化率。