焙烧培训教材PPT课件
合集下载
焙烧-课件(PPT-精)PPT67页
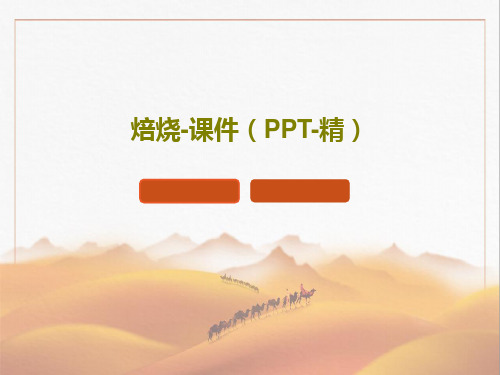
❖ 知识就是财富 ❖ 丰富你的人生
71、既然我已经踏上这条道路,那么,任何东西都不应妨碍我沿着这条路走下去。——康德 72、家庭成为快乐的种子在外也不致成为障碍物但在旅行之际却是夜间的伴侣。——西塞罗 73、坚持意志伟大的事业需要始终不渝的精神。——伏尔泰 74、路漫漫其修道远,吾将上下而求索。——屈原 75、内外相应,言行相称。——韩非
பைடு நூலகம்
焙烧-课件(PPT-精)
31、园日涉以成趣,门虽设而常关。 32、鼓腹无所思。朝起暮归眠。 33、倾壶绝余沥,窥灶不见烟。
34、春秋满四泽,夏云多奇峰,秋月 扬明辉 ,冬岭 秀孤松 。 35、丈夫志四海,我愿不知老。
谢谢你的阅读
71、既然我已经踏上这条道路,那么,任何东西都不应妨碍我沿着这条路走下去。——康德 72、家庭成为快乐的种子在外也不致成为障碍物但在旅行之际却是夜间的伴侣。——西塞罗 73、坚持意志伟大的事业需要始终不渝的精神。——伏尔泰 74、路漫漫其修道远,吾将上下而求索。——屈原 75、内外相应,言行相称。——韩非
பைடு நூலகம்
焙烧-课件(PPT-精)
31、园日涉以成趣,门虽设而常关。 32、鼓腹无所思。朝起暮归眠。 33、倾壶绝余沥,窥灶不见烟。
34、春秋满四泽,夏云多奇峰,秋月 扬明辉 ,冬岭 秀孤松 。 35、丈夫志四海,我愿不知老。
谢谢你的阅读
硫化锌精矿的焙烧课件
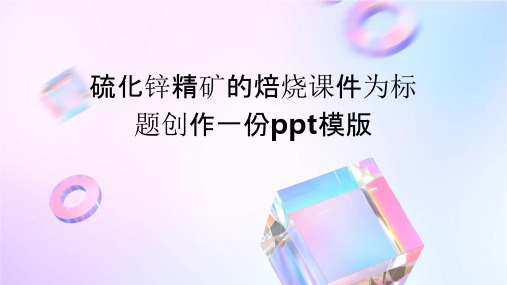
未展望
分析硫化锌精矿焙烧设备与技术 的发展趋势,如设备大型化、智 能化、绿色化等,为未来的研究
和应用提供参考。
04
焙烧过程中的环境保护与 可持续发展
焙烧过程的环保问题
大气污染
焙烧过程中产生的废气可 能含有二氧化硫、氮氧化 物等有害气体,对大气环 境造成污染。
水体污染
焙烧废水中可能含有重金 属离子、有机物等污染物, 未经妥善处理直接排放将 影响水环境质量。
设备构造
详细介绍设备的构造,包 括进料系统、燃烧系统、 排气系统等。
设备工作原理
解释设备的工作原理,以 及如何在焙烧过程中实现 硫化锌精矿的转化。
焙烧设备的操作与维护
设备操作
阐述设备的启动、运行、停车 等操作步骤,以及操作过程中
需要注意的事项。
设备维护
介绍设备的日常维护内容,包括设 备清洁、润滑、紧固等,以及定期 维护项目,如更换磨损件、检修燃 烧系统等。
• 停留时间:物料在焙烧炉内的停留时间也是影响焙烧效果的关键因素之一。过短的停留时间可能导致反应不充 分,而过长的停留时间则可能导致氧化锌的进一步分解或过度氧化。因此,需要根据物料性质和反应条件,合 理控制物料在焙烧炉内的停留时间。
03
焙烧设备与技术
焙烧设备介绍
01
02
03
设备类型
常用的硫化锌精矿焙烧设 备包括回转窑、沸腾炉、 固定床炉等。
加强与国际先进企业和研究机构的合作与 交流,引进先进技术和管理经验,促进我 国硫化锌精矿焙烧工艺的持续发展。
感谢您的观看
THANKS
原理
焙烧过程中的氧化反应是一个放热反应,其反应速率受温度、气氛、物料粒度等因素的影响。在适宜 的温度和气氛条件下,硫化锌可以与氧气发生反应,生成氧化锌和二氧化硫。同时,二氧化硫可以通 过进一步的氧化反应,生成三氧化硫,再与水反应生成硫酸,实现硫资源的回收利用。
焙烧ppt课件
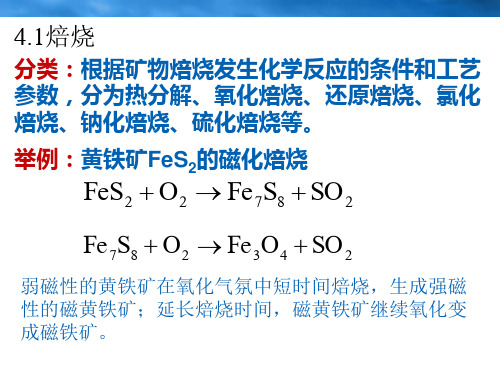
4.1焙烧
分类:根据矿物焙烧发生化学反应的条件和工艺 参数,分为热分解、氧化焙烧、还原焙烧、氯化 焙烧、钠化焙烧、硫化焙烧等。 举例:黄铁矿FeS2的磁化焙烧
FeS2 O2 Fe7S8 SO 2
Fe7S8 O2 Fe3O4 SO 2
弱磁性的黄铁矿在氧化气氛中短时间焙烧,生成强磁 性的磁黄铁矿;延长焙烧时间,磁黄铁矿继续氧化变 成磁铁矿。
4.1.2焙烧之氧化焙烧
硫化物经焙烧转变为氧化物或硫酸盐的反应:
2MS 3O2 2MO 2SO 2 2SO 2 O 2 2SO 3 MO SO 3 MSO 4
可逆反应
1 若炉气中SO3分压小于MSO4的分解压, MSO4分解,MS 氧化为MO,即硫化矿物全部脱硫焙烧; —氧化焙烧 2 若炉气中SO3分压大于MSO4的分解压, MS便氧化为 MSO4,即硫化矿物部分脱硫焙烧。—硫酸化焙烧 硫酸化焙烧是在氧化焙烧生成金属氧化物的基础上,使金 属氧化物转变成可溶性硫酸盐,再用水浸出的分离过程。
氧化焙烧
还原焙烧
MS
MO
氧化
还原气氛 氧化或还原
空气/氧气 硫酸化焙烧
粉煤/焦炭 硫化焙烧/煤气 硫化剂 氯气/氯化 氯化离析 氢/氯化钠
氯化焙烧 MO/MS
钠化焙烧
MO
氧化或还原
钠盐
—
钒钨铬等
—
磁化焙烧 弱磁性矿物 中性、氧化或还原
焙烧设备:沸腾炉、多膛炉、回转窑、竖炉等。
硫化挥发法-中国云锡公司 锡中矿烟化炉 还原挥发法-高温烟化炉,锌、铅气态金属挥发
4.1.4焙烧之氯化焙烧
氯化焙烧是矿物原料与氯化剂在氧化或还原 气氛中加热并发生化学反应,生成可溶性或气 态金属氯化物的过程。
分类:根据矿物焙烧发生化学反应的条件和工艺 参数,分为热分解、氧化焙烧、还原焙烧、氯化 焙烧、钠化焙烧、硫化焙烧等。 举例:黄铁矿FeS2的磁化焙烧
FeS2 O2 Fe7S8 SO 2
Fe7S8 O2 Fe3O4 SO 2
弱磁性的黄铁矿在氧化气氛中短时间焙烧,生成强磁 性的磁黄铁矿;延长焙烧时间,磁黄铁矿继续氧化变 成磁铁矿。
4.1.2焙烧之氧化焙烧
硫化物经焙烧转变为氧化物或硫酸盐的反应:
2MS 3O2 2MO 2SO 2 2SO 2 O 2 2SO 3 MO SO 3 MSO 4
可逆反应
1 若炉气中SO3分压小于MSO4的分解压, MSO4分解,MS 氧化为MO,即硫化矿物全部脱硫焙烧; —氧化焙烧 2 若炉气中SO3分压大于MSO4的分解压, MS便氧化为 MSO4,即硫化矿物部分脱硫焙烧。—硫酸化焙烧 硫酸化焙烧是在氧化焙烧生成金属氧化物的基础上,使金 属氧化物转变成可溶性硫酸盐,再用水浸出的分离过程。
氧化焙烧
还原焙烧
MS
MO
氧化
还原气氛 氧化或还原
空气/氧气 硫酸化焙烧
粉煤/焦炭 硫化焙烧/煤气 硫化剂 氯气/氯化 氯化离析 氢/氯化钠
氯化焙烧 MO/MS
钠化焙烧
MO
氧化或还原
钠盐
—
钒钨铬等
—
磁化焙烧 弱磁性矿物 中性、氧化或还原
焙烧设备:沸腾炉、多膛炉、回转窑、竖炉等。
硫化挥发法-中国云锡公司 锡中矿烟化炉 还原挥发法-高温烟化炉,锌、铅气态金属挥发
4.1.4焙烧之氯化焙烧
氯化焙烧是矿物原料与氯化剂在氧化或还原 气氛中加热并发生化学反应,生成可溶性或气 态金属氯化物的过程。
第七章-焙烧工艺-《炭素材料》教学课件

(1)根据产品在焙烧过程中的变化规律制定焙烧曲线 焙烧曲线应该与沥青挥发分的排出速度和沥青焦化的物理化学变化相适应。这是制 定焙烧曲线的理论根据。
(2)根据产品的种类和规格制定曲线
①炭块不经石墨化,烧成温度略高于电极的温度,即1300℃。电极需经石墨化,烧成 温度为1200℃。炭电阻棒要求电阻率大,故最高温度控制在1000℃。 ②大直径的制品截面大,内外温差大,为了减少裂纹废品,曲线则要求长些,升温速 度要慢些,小直径的产品则相反。
图5-1 从温度范围概观加热变化
第四阶段:(900℃以上,化学变化停止,物理变化深度继续)
焙烧温度超过900℃,挥发分已基本排尽,再继续加热,制品本身的化学变化 逐渐停止,外部与内部收缩微弱。为了使焦化程度更加完善,进一步提高各项 理化指标(如真密度、气孔率以及强度、硬度和导电性等),因此,产品温度 还要继续升高到1000~1200℃。这阶段升温速度可以加快一些不致影响产品 的质量,并在达到最高温度后还要保温15~20h。
4)氧化 (1)产品装炉时生坯周围填充料未填实或焙烧时填充料局部沉陷,致使 产品局部暴露在高温中。 (2)顶部填充料厚度不够。 (3)产品出炉后未及时散开,聚集在一起而导致温度升高。 (4)炉箱砌体有裂缝,高温气体进入料箱接触产品。 (5)重复焙烧,氧气透过填充料,使表面氧化。
(5)根据不同的压型品制定焙烧曲线
生制品中骨料颗粒大小、油量多少、压型方式不同,焙烧时所用曲线 也不同。
①生制品体积密度大的制品,升温速度要慢些;体积密度小的制品, 升温速度要快些。
②粘结剂用量不同的制品,升温速度也不同,用量偏大,升温速度可 快些;用量偏小,升温速度可慢些。众所周知,压型品粘结剂含量小,焙 烧品易开裂不易变形,反之易变形不易开裂。
精选焙烧生产工艺培训课件

电收尘及返灰系统
电收尘及返灰系统
在电收尘器内安装有多排平板和导线,它们分别接至高压直流电源的正极和负极,称其为阳极板和阴极线。电收尘内的阳极板为集尘极,阴极线为电晕极,在两极间产生不均匀电场。当电压升高到一定程度时,在阴极附近的电场强度促使气体发生碰撞电离,形成正、负离子。随着电压继续增高至某值时,在阴极线附近发生电晕放电,这时气体生成大量离子,绝大部分粉尘与飞翔的阴离子相撞带负电,飞向集尘极,只有极少量粉尘沉积于电晕极。定期振打集尘极及电晕极,使积尘掉落,从下部灰斗排出。
0.02
0.5
1.0
AO-2
98.5
0.04
0.02
0.6
1.0
AO-3
98.4
0.06
0.03
0.7
1.0
一、氧化铝的化学纯度
电解用铝的要求
焙烧的目的
二、氧化铝的物理性质安息角:物料在光滑平面上自然堆积的倾角。 安息角大的氧化铝在电解质中易溶解,在电解过程中能够很好地覆盖于电解质结壳上,飞扬损失也小。
引风机
引风机:是保证焙烧系统安全燃烧的主要设备,引风机故障会造成整个系统自动停车。
工艺流程及知识点
P02上升管处安装有掺风调节阀V10。当烘炉或故障时将P02T2过高的温度(≥300℃)降下来。P01T1长期作业温度不宜超过250℃,避免电收尘内极板、极线高温烘烤变形短路。
工艺流程及知识点
CO含量高于0.2%电收尘跳停;O2含量低于1.5%电收尘跳停。燃烧站仪表风压<0.45Mpa燃烧站停;鼓风机运行,才能启动燃烧站;V08没有火焰监测信号,燃烧站停。燃气压力高报低报,燃烧站停。
焙烧的原理
脱除附着水:当温度高于100℃时AH中的附着水被蒸发。Al(OH)3·H2O →Al(OH)3 + H2O↑脱除结晶水:结晶水的脱除分两步进行,250℃~300℃时,它失去两个分子的结晶水,在500~560℃的温度下,它失去最后一个分子的结晶水,而成为γ-Al2O3。 2 Al(OH)3 →Al2O3·H2O +2H2O ↑ Al2O3·H2O → γ-Al2O3 +H2O ↑晶型转变:γ-Al2O3在950℃开始晶型转变,逐渐由γ-Al2O3转变为α-Al2O3 γ-Al2O3 →α-Al2O3(12~15%)
电收尘及返灰系统
在电收尘器内安装有多排平板和导线,它们分别接至高压直流电源的正极和负极,称其为阳极板和阴极线。电收尘内的阳极板为集尘极,阴极线为电晕极,在两极间产生不均匀电场。当电压升高到一定程度时,在阴极附近的电场强度促使气体发生碰撞电离,形成正、负离子。随着电压继续增高至某值时,在阴极线附近发生电晕放电,这时气体生成大量离子,绝大部分粉尘与飞翔的阴离子相撞带负电,飞向集尘极,只有极少量粉尘沉积于电晕极。定期振打集尘极及电晕极,使积尘掉落,从下部灰斗排出。
0.02
0.5
1.0
AO-2
98.5
0.04
0.02
0.6
1.0
AO-3
98.4
0.06
0.03
0.7
1.0
一、氧化铝的化学纯度
电解用铝的要求
焙烧的目的
二、氧化铝的物理性质安息角:物料在光滑平面上自然堆积的倾角。 安息角大的氧化铝在电解质中易溶解,在电解过程中能够很好地覆盖于电解质结壳上,飞扬损失也小。
引风机
引风机:是保证焙烧系统安全燃烧的主要设备,引风机故障会造成整个系统自动停车。
工艺流程及知识点
P02上升管处安装有掺风调节阀V10。当烘炉或故障时将P02T2过高的温度(≥300℃)降下来。P01T1长期作业温度不宜超过250℃,避免电收尘内极板、极线高温烘烤变形短路。
工艺流程及知识点
CO含量高于0.2%电收尘跳停;O2含量低于1.5%电收尘跳停。燃烧站仪表风压<0.45Mpa燃烧站停;鼓风机运行,才能启动燃烧站;V08没有火焰监测信号,燃烧站停。燃气压力高报低报,燃烧站停。
焙烧的原理
脱除附着水:当温度高于100℃时AH中的附着水被蒸发。Al(OH)3·H2O →Al(OH)3 + H2O↑脱除结晶水:结晶水的脱除分两步进行,250℃~300℃时,它失去两个分子的结晶水,在500~560℃的温度下,它失去最后一个分子的结晶水,而成为γ-Al2O3。 2 Al(OH)3 →Al2O3·H2O +2H2O ↑ Al2O3·H2O → γ-Al2O3 +H2O ↑晶型转变:γ-Al2O3在950℃开始晶型转变,逐渐由γ-Al2O3转变为α-Al2O3 γ-Al2O3 →α-Al2O3(12~15%)
磁化焙烧原理PPT课件

其办法是:从焙烧产品中取代表性试样,用一定数量 作化学分析,主要分析全铁含量。另外一定量试样用 磁性分析仪进行磁性成分含量分析,得出磁性产品作 化学分析,算出磁性铁含量,再进一步计算出磁性率( 即磁化率=MFe/TFe×100%,MFe为磁性铁含量,TFe为 全铁含量)。很显然,此法能准确反映出焙烧矿的质量 。这种方法多用于从稀有金属精来自中用焙烧磁选的方法 分离出硫铁矿。
2.2 磁化焙烧的原理
以上三种焙烧方法,是按照不同矿物所采用的。实 际上,矿石的铁矿物组成往往不是单一的铁矿物,而是 同时含有几种铁矿物。根据矿石中成分的不同,磁化焙 烧时可将几种焙烧方法结合使用。常用的有中性还原焙 烧、氧化还原焙烧、还原氧化焙烧。
通入少量空气: 4FeCO3+O2=2Fe2O3+4CO2↑ (300~400℃) 3Fe2O3+CO=2Fe3O4+CO2↑ (300~400℃)
2.2 磁化焙烧的原理
3 氧化焙烧 氧化焙烧是专门对黄铁矿而言的,其反应如下:
7FeS2+6O2=Fe7S8+6SO2↑ 延长焙烧时间,磁黄铁矿发生下列反应变成磁铁矿: 3Fe7S8+38O2=7Fe3O4+24SO2↑
还原度表示还原焙烧矿中氧化亚铁(FeO)和全铁(TFe )含量百分比,以下式表示:
R=TeO/TFe×100% 式中 R———还原度,% ;
FeO———还原焙烧矿中FeO的含量,% ; TFe———还原焙烧矿中全铁的含量,% 。
2.3.1理论鉴别
在理想情况下矿石中的Fe203全部还原为Fe304时,还原度为: R=(5+16)×100%/(56×3)=42.8%
2.2 磁化焙烧的原理
氧化还原焙烧 含有菱铁矿、赤铁矿或褐铁矿的铁矿石,在菱铁矿
与赤铁矿的比值小于1时,在氧化气氛中加热到一定程 度,菱铁矿可氧化成赤铁矿,然后再在还原气氛中将其 与矿石中原有赤铁矿一并还原成磁铁矿。
2.2 磁化焙烧的原理
以上三种焙烧方法,是按照不同矿物所采用的。实 际上,矿石的铁矿物组成往往不是单一的铁矿物,而是 同时含有几种铁矿物。根据矿石中成分的不同,磁化焙 烧时可将几种焙烧方法结合使用。常用的有中性还原焙 烧、氧化还原焙烧、还原氧化焙烧。
通入少量空气: 4FeCO3+O2=2Fe2O3+4CO2↑ (300~400℃) 3Fe2O3+CO=2Fe3O4+CO2↑ (300~400℃)
2.2 磁化焙烧的原理
3 氧化焙烧 氧化焙烧是专门对黄铁矿而言的,其反应如下:
7FeS2+6O2=Fe7S8+6SO2↑ 延长焙烧时间,磁黄铁矿发生下列反应变成磁铁矿: 3Fe7S8+38O2=7Fe3O4+24SO2↑
还原度表示还原焙烧矿中氧化亚铁(FeO)和全铁(TFe )含量百分比,以下式表示:
R=TeO/TFe×100% 式中 R———还原度,% ;
FeO———还原焙烧矿中FeO的含量,% ; TFe———还原焙烧矿中全铁的含量,% 。
2.3.1理论鉴别
在理想情况下矿石中的Fe203全部还原为Fe304时,还原度为: R=(5+16)×100%/(56×3)=42.8%
2.2 磁化焙烧的原理
氧化还原焙烧 含有菱铁矿、赤铁矿或褐铁矿的铁矿石,在菱铁矿
与赤铁矿的比值小于1时,在氧化气氛中加热到一定程 度,菱铁矿可氧化成赤铁矿,然后再在还原气氛中将其 与矿石中原有赤铁矿一并还原成磁铁矿。
焙烧生产工艺素材课件

器、燃油燃烧器等。
燃烧室设计
合理的燃烧室设计,能够确保燃 料充分燃烧,提高能源利用效率
。
废气处理装置
为减少对环境的污染,需配备废 气处理装置,如除尘器、脱硫脱
硝装置等。
供风与排烟设备
鼓风机与引风机
提供炉膛内所需的风量和风压,确保物料燃烧所 需的氧气供应和废气的排出。
烟囱与烟道
用于排放炉膛内的废气,设计时应考虑废气的处 理和排放标准。
03
安装火灾报警系统和自动灭火装置,提高应对火灾 等突发事件的反应速度。
“三废”处理与环保措施
对焙烧过程中产生的废气、废水和固体 废弃物进行分类处理。
废水需经过沉淀、中和、生化处理等工 序,达到排放标准后才能排放。
采用先进的废气处理技术,如活性炭吸 附、催化燃烧等,降低废气排放。
对固体废弃物进行资源化利用或无害化 处理,减少对环境的影响。
对产品质量的影响。
气氛控制
02
调节焙烧过程中的气氛,如氧气浓度、惰性气体等,以优化产
品的物理和化学性质。
时间控制
03
合理安排焙烧时间,确保物料在焙烧过程中充分反应,提高产
品的性能和稳定性。
产品检测与质量评定
外观检测
检查产品的外观质量,如颜色、形 状、表面光洁度等是否符合标准要
求。
物理性能检测
测试产品的物理性能指标,如密度 、硬度、耐磨性等,以确保产品性
除尘设备
为减少烟尘对环境的影响,需配备除尘设备,如 旋风除尘器、布袋除尘器等。
检测与控制设备
温度传感器
实时监测炉膛内的温度变化,为控制提 供依据。
流量计与液位计
监测各工艺管道中的物料流量和液位高 度,为工艺控制提供数据支持。
燃烧室设计
合理的燃烧室设计,能够确保燃 料充分燃烧,提高能源利用效率
。
废气处理装置
为减少对环境的污染,需配备废 气处理装置,如除尘器、脱硫脱
硝装置等。
供风与排烟设备
鼓风机与引风机
提供炉膛内所需的风量和风压,确保物料燃烧所 需的氧气供应和废气的排出。
烟囱与烟道
用于排放炉膛内的废气,设计时应考虑废气的处 理和排放标准。
03
安装火灾报警系统和自动灭火装置,提高应对火灾 等突发事件的反应速度。
“三废”处理与环保措施
对焙烧过程中产生的废气、废水和固体 废弃物进行分类处理。
废水需经过沉淀、中和、生化处理等工 序,达到排放标准后才能排放。
采用先进的废气处理技术,如活性炭吸 附、催化燃烧等,降低废气排放。
对固体废弃物进行资源化利用或无害化 处理,减少对环境的影响。
对产品质量的影响。
气氛控制
02
调节焙烧过程中的气氛,如氧气浓度、惰性气体等,以优化产
品的物理和化学性质。
时间控制
03
合理安排焙烧时间,确保物料在焙烧过程中充分反应,提高产
品的性能和稳定性。
产品检测与质量评定
外观检测
检查产品的外观质量,如颜色、形 状、表面光洁度等是否符合标准要
求。
物理性能检测
测试产品的物理性能指标,如密度 、硬度、耐磨性等,以确保产品性
除尘设备
为减少烟尘对环境的影响,需配备除尘设备,如 旋风除尘器、布袋除尘器等。
检测与控制设备
温度传感器
实时监测炉膛内的温度变化,为控制提 供依据。
流量计与液位计
监测各工艺管道中的物料流量和液位高 度,为工艺控制提供数据支持。
焙烧培训教材

P01
P02
P03
P04 图3-3
锁气翻板阀:
P01
翻板阀
在PO1的下料管靠近PO1锥部处有一个锁气 翻板阀,其作用是防止气流通过下料管走短 路直接从PO1的锥部进入,由中心管抽走。 如果出现这种情况,将引起至少两个方面的 负面影响。首先,改变了系统的气流分布, 气流不能和物料进行充分的热交换;其次, 从下料管上升的气流阻碍了PO1的物料流动, 会引起PO1锥部积流。当积于阀板上的物料 对阀板的压力力矩超过配重的力矩时,翻板 阀打开,物料下滑,然后又重新建立新的平 衡。当然,实际生产中其动作过程很快,翻 板阀只起一个节流的作用。其作用原理如图 3-3示。
T12启动燃烧站
T12燃烧站本身所配置的主要设备有:供空气用的风机; 点火枪;火焰探测器;煤气控制管路。
T12煤气控制管路工艺流程图如下: 连接法兰 T1 P1 P1 放散阀
v05
P 2
截止 V04
手动阀 F1 调节阀 截止阀 阀 V01 V02 V03
软管 连 接 法 兰管烧咀
燃烧空气管
2.8.2热发生器T11
PO4中焙烧后的物料由气流带入与PO4相连通的热 分离旋风筒PO3,在PO3中焙烧后的AL2O3完成最终的 晶型转变过程,并进行气固分离,分离后的高温烟气去 预热系统,经 PO2 、AO2 、PO1、P11、P17、P18后排 空。物料由PO3物料管下溜入系统的冷却部分,路径是 CO1 CO2 CO3 CO4,高温AL2O3在其经过冷却旋 风筒的过程中,与其逆流而行的空气进行热交换,最终 经过空气冷却的物料进入流化床冷却器KO1,经过预热 的空气进入PO4炉膛,以实现系统热量的充分利用。
二.反应过程
110-120 ℃,2Al(OH)3+附水→Al2O3.3H2O+H2O↑ 200-250 ℃,失去两个结晶水转变为一水原铝石: Al2O3.3H2O →Al2O3.H2O+2H2O↑ 550 ℃左右,一水铝石转变为无水: Al2O3.H2O → γ –Al2O3 +H2O↑
- 1、下载文档前请自行甄别文档内容的完整性,平台不提供额外的编辑、内容补充、找答案等附加服务。
- 2、"仅部分预览"的文档,不可在线预览部分如存在完整性等问题,可反馈申请退款(可完整预览的文档不适用该条件!)。
- 3、如文档侵犯您的权益,请联系客服反馈,我们会尽快为您处理(人工客服工作时间:9:00-18:30)。
Al2O3.H2O → γ –Al2O3 +H2O↑ 900 ℃以上转变为不吸湿的:γ –Al2O3 → α - Al2O3
5
三、工艺流程及设备
1、流程的简述
进系统的AH首先进入给料仓L01中,再由电子定量给料秤F01称量 后进入给料螺旋A01,由给料螺旋A01塞入文丘里干燥器A02,带一定 附水的AH在文丘里干燥器中由来自焙烧炉的高温烟气干燥,并由高温 烟气提升至预热旋风筒PO1中。
电解车间氢氧化铝焙烧1
焙烧工序及流程简介
焙烧车间是氧化铝生产的最后一个车间主 要将分解车间送过来的料浆经平盘过滤得到的合 格氢氧化铝,之后经悬浮焙烧炉高温焙烧成氧化 铝,将焙烧过的氧化铝经冷却流化床、风动溜槽 、浓相输送把AO送至电解区域供电解使用。
2
流 程 简 介
11
2.1、给料系统
含一定附水的氢氧化铝由计量皮带F01从系统小料仓 L01中拉取,L01小料仓底部有一棒条闸门,其作用调节下 料流量,并支撑料仓中物料的重量,以免物料全部压在F01 皮带上,将皮带压死。生产中有时因为料放置时间过长或物 料中附水含量过高,L01中的料容易被棒条闸门的棒条架空, 不能落到F01皮带,这时,F01就不能从L01中取料,遇到这 种情况时,要将棒条闸门的支撑棒条间隔地抽稀,使物料下 落。在对L01的料位控制时,为防止料仓冒料以及料仓拉空, 同时为防止氢氧化铝供料出现故障而影响焙烧炉GSC的正常 供料,一般在L01中保持一定的缓冲物料,为此,在L01仓 顶设有料位计,仓满时发出报警
从PO2中心管出来的烟气,经过一段水平段后,下 拐弯从顶楼一直贯穿到最低层,拐弯后入文丘里干燥器 AO2,再由AO2出口连通到PO1,从PO2下拐后,就没 有内衬,为防止烟道受高
9
温烟气的温度变化影响而引起形变,以致损坏。在烟 道上设置了温度调节装置,当烟气温度过高时,向烟 道内进冷空气,以降低烟气温度。
PO1中进行气固分离后的烟气入电收尘器P11,分离开的并经过预热 脱水的物料由PO1的下料管进入第二级预热旋风筒PO2,在PO2中进 行预焙烧。PO2气固分离后的烟气通过PO2的下降烟道入文丘里干燥 器,经过预焙烧后的物料由PO2下料管进进入主炉PO4进行焙烧,在 主炉PO4中由煤气燃烧提供的热量来完成AL2(OH)3到AL2O3的化学反 应。
12
信号,L01料位情况即时地反应到主控室的中心计算 机上,以便操作人员根据实际生产情况对料位进行 控制。
在给料系统设备的开停时,一定要注意启动的
7
在预热部分的文丘里干燥器AO2入口处,设置一个 热 发 生 器 T11 , 当 给 料 中 附 水 含 量 高 , 文 丘 里 干 燥 器 AO2的出口温度AO2T1低于145℃时,将T11投入运行, 对系统补充热量,以提高系统的烟气温度。
经过第一阶段空气冷却的物料由CO4下料管进入 流化床冷却器KO1,在KO1中由冷却水进行间接冷却, 最终将AO2冷却到适于输送和进行下序作业的温度。流 化床由罗茨风机中的任一台提供的流化风对物料也进行 冷却,但流化风带走的热量较少,进入流化床的流化风 最终由流化床的尾气管排入系统的AO7吸风口。
风动溜槽
大气 烟囱
超浓相输送
电解车间
3
氢氧化铝焙烧
一.焙烧原理
焙烧是将氢氧化铝置于高温环境中脱除其附着水和 结晶水,并完成部分γ-AL2O3向α-AL2O3转变,生成物理 和化学性质符合电解要求的氧化铝。电解用的氧化铝要求 氧化铝在电解质中溶解度大﹑溶解速度快﹑流动性好﹑粉 尘量小﹑具有较好的表面活性,能够有效吸附HF气体, 这些性能的好坏主要决定于焙烧条件。
8
前面已提及到,PO4中产生的燃烧产物(高温烟气) 在经过分离旋风筒PO3后,进入系统的冷却部分,分别在 PO2、AO2、PO1中与AH进行热交换,烟气本身被冷却, 而物料温度被升高,冷却后并在分离旋风PO1中气固分离 后的烟气进入静电收尘器 (electrostatic precipitator, 简称ESP)中收尘净化,最终的烟气排尘浓度为小于 50mg/Nm3,电收尘P11收采的粉尘由返灰系统P12、 P13、P14返回冷却旋风筒CO2中。
焙烧装置采用的是气态旋风焙烧炉,运用流态化技术 完成干燥、预热和预焙烧、焙烧以及冷却等工艺过程,具 有气固传热效率高、热耗低等许多优点。
4
二.反应过程
110-120 ℃,2Al(OH)3+附水 →Al2O3.3H2O+H2O↑ 200-250 ℃,失去两个结晶水转变为一水原铝石:
Al2O3.3H2O →Al2O3.H2O+2H2O↑ 550 ℃左右,一水铝石转变为无水:
烟气 物料
T11主燃烧器 V08/V19燃烧器
T12主燃烧器 空气进口
成品过滤来氢氧化铝 LO1小料仓 电子皮带秤 A01喂料螺旋 A02文丘里 P01旋风筒 P02旋风筒 P04旋风筒 P03旋风筒 C01冷却器 C02冷却器 C03冷却器 C04冷却器 流化床冷却器 成品氧化铝
电除尘 风动溜槽 气力提升泵
6
PO4中焙烧后的物料由气流带入与PO4相连通的 热分离旋风筒PO3,在PO3中焙烧后的AL2O3完成最终 的晶型转变过程,并进行气固分离,分离后的高温烟气 去预热系统,经 PO2 、AO2 、PO1、P11、P17、 P18后排空。物料由PO3物料管下溜入系统的冷却部分, 路径是CO1 CO2 CO3 CO4,高温AL2O3在其经 过冷却旋风筒的过程中,与其逆流而行的空气进行热交 换,最终经过空气冷却的物料进入流化床冷却器KO1, 经过预热的空气进入PO4炉膛,以实现系统热量的充分 利用。
整个系统的气体流动,以及气体带动物料的流动 的动力来自主风机P17,风量的大小由调节P17的转 速来控制,在生产中直接的参考参数是系统中过剩氧 气含量PO2A1,不管什么情况,什么时候,PO2A1 都不能小于0.5%。
10
2.系统的主要组成部分
氢氧化铝给料 文丘里干燥器 悬浮焙烧 四级旋风冷却器 流化床冷却器 收尘及返尘系统 气力输送和产品贮运
5
三、工艺流程及设备
1、流程的简述
进系统的AH首先进入给料仓L01中,再由电子定量给料秤F01称量 后进入给料螺旋A01,由给料螺旋A01塞入文丘里干燥器A02,带一定 附水的AH在文丘里干燥器中由来自焙烧炉的高温烟气干燥,并由高温 烟气提升至预热旋风筒PO1中。
电解车间氢氧化铝焙烧1
焙烧工序及流程简介
焙烧车间是氧化铝生产的最后一个车间主 要将分解车间送过来的料浆经平盘过滤得到的合 格氢氧化铝,之后经悬浮焙烧炉高温焙烧成氧化 铝,将焙烧过的氧化铝经冷却流化床、风动溜槽 、浓相输送把AO送至电解区域供电解使用。
2
流 程 简 介
11
2.1、给料系统
含一定附水的氢氧化铝由计量皮带F01从系统小料仓 L01中拉取,L01小料仓底部有一棒条闸门,其作用调节下 料流量,并支撑料仓中物料的重量,以免物料全部压在F01 皮带上,将皮带压死。生产中有时因为料放置时间过长或物 料中附水含量过高,L01中的料容易被棒条闸门的棒条架空, 不能落到F01皮带,这时,F01就不能从L01中取料,遇到这 种情况时,要将棒条闸门的支撑棒条间隔地抽稀,使物料下 落。在对L01的料位控制时,为防止料仓冒料以及料仓拉空, 同时为防止氢氧化铝供料出现故障而影响焙烧炉GSC的正常 供料,一般在L01中保持一定的缓冲物料,为此,在L01仓 顶设有料位计,仓满时发出报警
从PO2中心管出来的烟气,经过一段水平段后,下 拐弯从顶楼一直贯穿到最低层,拐弯后入文丘里干燥器 AO2,再由AO2出口连通到PO1,从PO2下拐后,就没 有内衬,为防止烟道受高
9
温烟气的温度变化影响而引起形变,以致损坏。在烟 道上设置了温度调节装置,当烟气温度过高时,向烟 道内进冷空气,以降低烟气温度。
PO1中进行气固分离后的烟气入电收尘器P11,分离开的并经过预热 脱水的物料由PO1的下料管进入第二级预热旋风筒PO2,在PO2中进 行预焙烧。PO2气固分离后的烟气通过PO2的下降烟道入文丘里干燥 器,经过预焙烧后的物料由PO2下料管进进入主炉PO4进行焙烧,在 主炉PO4中由煤气燃烧提供的热量来完成AL2(OH)3到AL2O3的化学反 应。
12
信号,L01料位情况即时地反应到主控室的中心计算 机上,以便操作人员根据实际生产情况对料位进行 控制。
在给料系统设备的开停时,一定要注意启动的
7
在预热部分的文丘里干燥器AO2入口处,设置一个 热 发 生 器 T11 , 当 给 料 中 附 水 含 量 高 , 文 丘 里 干 燥 器 AO2的出口温度AO2T1低于145℃时,将T11投入运行, 对系统补充热量,以提高系统的烟气温度。
经过第一阶段空气冷却的物料由CO4下料管进入 流化床冷却器KO1,在KO1中由冷却水进行间接冷却, 最终将AO2冷却到适于输送和进行下序作业的温度。流 化床由罗茨风机中的任一台提供的流化风对物料也进行 冷却,但流化风带走的热量较少,进入流化床的流化风 最终由流化床的尾气管排入系统的AO7吸风口。
风动溜槽
大气 烟囱
超浓相输送
电解车间
3
氢氧化铝焙烧
一.焙烧原理
焙烧是将氢氧化铝置于高温环境中脱除其附着水和 结晶水,并完成部分γ-AL2O3向α-AL2O3转变,生成物理 和化学性质符合电解要求的氧化铝。电解用的氧化铝要求 氧化铝在电解质中溶解度大﹑溶解速度快﹑流动性好﹑粉 尘量小﹑具有较好的表面活性,能够有效吸附HF气体, 这些性能的好坏主要决定于焙烧条件。
8
前面已提及到,PO4中产生的燃烧产物(高温烟气) 在经过分离旋风筒PO3后,进入系统的冷却部分,分别在 PO2、AO2、PO1中与AH进行热交换,烟气本身被冷却, 而物料温度被升高,冷却后并在分离旋风PO1中气固分离 后的烟气进入静电收尘器 (electrostatic precipitator, 简称ESP)中收尘净化,最终的烟气排尘浓度为小于 50mg/Nm3,电收尘P11收采的粉尘由返灰系统P12、 P13、P14返回冷却旋风筒CO2中。
焙烧装置采用的是气态旋风焙烧炉,运用流态化技术 完成干燥、预热和预焙烧、焙烧以及冷却等工艺过程,具 有气固传热效率高、热耗低等许多优点。
4
二.反应过程
110-120 ℃,2Al(OH)3+附水 →Al2O3.3H2O+H2O↑ 200-250 ℃,失去两个结晶水转变为一水原铝石:
Al2O3.3H2O →Al2O3.H2O+2H2O↑ 550 ℃左右,一水铝石转变为无水:
烟气 物料
T11主燃烧器 V08/V19燃烧器
T12主燃烧器 空气进口
成品过滤来氢氧化铝 LO1小料仓 电子皮带秤 A01喂料螺旋 A02文丘里 P01旋风筒 P02旋风筒 P04旋风筒 P03旋风筒 C01冷却器 C02冷却器 C03冷却器 C04冷却器 流化床冷却器 成品氧化铝
电除尘 风动溜槽 气力提升泵
6
PO4中焙烧后的物料由气流带入与PO4相连通的 热分离旋风筒PO3,在PO3中焙烧后的AL2O3完成最终 的晶型转变过程,并进行气固分离,分离后的高温烟气 去预热系统,经 PO2 、AO2 、PO1、P11、P17、 P18后排空。物料由PO3物料管下溜入系统的冷却部分, 路径是CO1 CO2 CO3 CO4,高温AL2O3在其经 过冷却旋风筒的过程中,与其逆流而行的空气进行热交 换,最终经过空气冷却的物料进入流化床冷却器KO1, 经过预热的空气进入PO4炉膛,以实现系统热量的充分 利用。
整个系统的气体流动,以及气体带动物料的流动 的动力来自主风机P17,风量的大小由调节P17的转 速来控制,在生产中直接的参考参数是系统中过剩氧 气含量PO2A1,不管什么情况,什么时候,PO2A1 都不能小于0.5%。
10
2.系统的主要组成部分
氢氧化铝给料 文丘里干燥器 悬浮焙烧 四级旋风冷却器 流化床冷却器 收尘及返尘系统 气力输送和产品贮运