数控车床编程基础知识ppt课件
合集下载
数控车床编程与操作加工PPT课件

例1 如图3-10所示的圆柱螺纹,螺纹导程为1.5mm。
G00 Z104.0 X29.3 ap1=0.35 G32 Z56.0 F1.5 G00 X40.0 Z104.0 X28.9 ap2=0.2 G32 Z56.0 F1.5 G00 X40.0 Z104.0 X28.5 ap2=0.2 …….
1.绝对编程与增量编程
(1)绝对编程
绝对值编程是根据预先设定的编程原点计算出绝对值坐标尺寸进行编程的一种方法。即采用绝对值编程时,首先要指出编程原点的位置,并用地址X,Z进行编程(X为直径值)。
增量值编程是根据与前一个位置的坐标值增量来表示位置的一种编程方法。即程序中的终点坐标是相对于起点坐标而言的。
根据试切后工件的尺寸确定刀尖的位置。
O
(a) 确定刀尖在Z向的位置
L
图3-3 数控车床的对刀
O
(a) 确定刀尖在Z向的位置
L
图3-3 数控车床的对刀
O
(b) 确定刀尖在X向的位置
d
O
(b) 确定刀尖在X向的位置
d
三、有关编程代码说明
(一)G功能
准备功能也称为G功能(或称G代码),它是用来指令机床动作方式的功能。准备功能是用地址G及其后面的数字来指令机床动作的。如用G00来指令运动坐标快速定位。表3-2为FANUC-0TD系统的准备功能G代码表。
10.刀具偏置功能 (G40/G41/G42)
1. 格式 G41 X_ Z_;G42 X_ Z_;
在刀具刃是尖利时,切削进程按照程序指定的形状执行不会发生问题。不过,真实的刀具刃是由圆弧构成的 (刀尖半径) 就像上图所示,在圆弧插补和攻螺纹的情况下刀尖半径会带来误差。
2. 偏置功能
1、非直线切削形式的定位 我们的定义是:采用独立的快速移动速率来决定每一个轴的位置。刀具路径不是直线,根据到达的顺序,机器轴依次停止在命令指定的位置。
G00 Z104.0 X29.3 ap1=0.35 G32 Z56.0 F1.5 G00 X40.0 Z104.0 X28.9 ap2=0.2 G32 Z56.0 F1.5 G00 X40.0 Z104.0 X28.5 ap2=0.2 …….
1.绝对编程与增量编程
(1)绝对编程
绝对值编程是根据预先设定的编程原点计算出绝对值坐标尺寸进行编程的一种方法。即采用绝对值编程时,首先要指出编程原点的位置,并用地址X,Z进行编程(X为直径值)。
增量值编程是根据与前一个位置的坐标值增量来表示位置的一种编程方法。即程序中的终点坐标是相对于起点坐标而言的。
根据试切后工件的尺寸确定刀尖的位置。
O
(a) 确定刀尖在Z向的位置
L
图3-3 数控车床的对刀
O
(a) 确定刀尖在Z向的位置
L
图3-3 数控车床的对刀
O
(b) 确定刀尖在X向的位置
d
O
(b) 确定刀尖在X向的位置
d
三、有关编程代码说明
(一)G功能
准备功能也称为G功能(或称G代码),它是用来指令机床动作方式的功能。准备功能是用地址G及其后面的数字来指令机床动作的。如用G00来指令运动坐标快速定位。表3-2为FANUC-0TD系统的准备功能G代码表。
10.刀具偏置功能 (G40/G41/G42)
1. 格式 G41 X_ Z_;G42 X_ Z_;
在刀具刃是尖利时,切削进程按照程序指定的形状执行不会发生问题。不过,真实的刀具刃是由圆弧构成的 (刀尖半径) 就像上图所示,在圆弧插补和攻螺纹的情况下刀尖半径会带来误差。
2. 偏置功能
1、非直线切削形式的定位 我们的定义是:采用独立的快速移动速率来决定每一个轴的位置。刀具路径不是直线,根据到达的顺序,机器轴依次停止在命令指定的位置。
数控车床编程基本学习-PPT
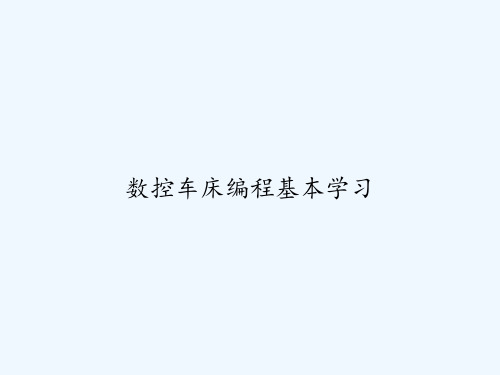
X 中间点
O
参考点R
刀尖当前位置 Z
图3-5 自动返回参考点
6、螺纹切削指令(G32)
指令格式 G32 X(U)_ Z(W)_ F(E)_ 指令功能 切削加工圆柱螺纹、圆锥螺纹和平面螺纹(涡形螺纹) 。
指令说明 1)F—公制螺纹的导程
E—英制螺纹的导程
2)F表示长轴方向的导程 如果X轴方向为长轴,F为半径值。 对于圆锥螺纹,其斜角α在450以下时,Z轴方向为长轴;
2
U
2
X
O
Z
图3-12 G94车削端面固定循环
G94指令车削圆锥面时的程序段格式如下:
G94 X(U)_Z(W)_R_F_;
其中,R为端面斜度线在Z轴的投影距离。若顺序动作2的 进给方向在Z轴的投影方向和Z轴方向一致,则R取负值;若顺 序动作2的进给方向在Z轴的投影方向和Z轴方向相反,则R取正 值。在图3-13中,因为顺序动作2的进给方向在Z轴的投影方向 和Z轴方向一致,所以R取负值。
必须注意的是,执行G27指令的前提是机床在通电后刀具 返回过一次参考点(手动返回或者用G28指令返回)。此外,使 用该指令时,必须预先取消刀具补偿的量。
执行G27指令之后,如欲使机床停止,须加入一辅助功能 指令M00,否则,机床将继续执行下一个程序段。
2) 自动返回参考点指令G28 G28指令可以使刀具从任何位置以快速点定位方式经过中间 点返回参考点。 格式:G28 X _Z _; 其中,X、Z是中间点的坐标值。 执行该指令时,刀具先快速移动到指令值所指定的中间点, 然后自动返回参考点,相应坐标轴指示灯亮。 和G27指令相同,执行G28指令前,应取消刀具补偿功能。 G28指令的执行过程如图3-5所示。
(3)参数的输入 假想刀尖的位置如下图3-10:
数控车床编程与操作PPT课件

加工结果检测
加工完成后,对工件进行检测,确保满足设计要 求和加工精度。
05 常见问题与解决方案
G代码编程常见问题与解决方案
G代码编程错误
检查G代码编程的语法和逻辑,确保指令正确无误。
刀具路径问题
检查刀具路径是否合理,避免出现干涉和碰撞。
加工参数设置不当
根据材料和加工要求,合理设置主轴转速、进给速度等加工参数。
数控车床操作常见问题与解决方案
1 2
操作界面不熟悉
熟悉数控车床的操作界面,了解各功能键的作用。
刀具安装不正确
按照规定正确安装刀具,确保刀具夹紧牢固。
3
加工区域安全问题
确保加工区域的安全防护措施到位,避免发生意 外事故。
加工过程常见问题与解决方案
加工精度不足
01
检查刀具磨损情况,及时更换刀片,确保加工精度。
遵守安全操作规程
在操作数控车床时,必须遵守安全操作规程, 确保人身安全和设备安全。
注意刀具状态
在加工过程中,应时刻关注刀具的状态,如 刀具是否松动、破损等。
禁止带手套操作
数控车床在高速旋转时,带手套操作容易发 生危险。
避免超负荷运转
在加工过程中,应避免因切削力过大而引起 的机床超负荷运转。
04 实际操作案例
表面质量不佳
02
调整切削参数和刀具角度,改善表面质量。
加工效率低下
03
优化加工参数和刀具路径,提高加工效率。
THANKS FOR WATCHING
感谢您的观看
并进行必要的编辑和修改。
加工参数设置
根据工件材料、刀具类型和加工要 求,设置合理的加工参数,如主轴 转速、进给速度、切削深度等。
自动加工
加工完成后,对工件进行检测,确保满足设计要 求和加工精度。
05 常见问题与解决方案
G代码编程常见问题与解决方案
G代码编程错误
检查G代码编程的语法和逻辑,确保指令正确无误。
刀具路径问题
检查刀具路径是否合理,避免出现干涉和碰撞。
加工参数设置不当
根据材料和加工要求,合理设置主轴转速、进给速度等加工参数。
数控车床操作常见问题与解决方案
1 2
操作界面不熟悉
熟悉数控车床的操作界面,了解各功能键的作用。
刀具安装不正确
按照规定正确安装刀具,确保刀具夹紧牢固。
3
加工区域安全问题
确保加工区域的安全防护措施到位,避免发生意 外事故。
加工过程常见问题与解决方案
加工精度不足
01
检查刀具磨损情况,及时更换刀片,确保加工精度。
遵守安全操作规程
在操作数控车床时,必须遵守安全操作规程, 确保人身安全和设备安全。
注意刀具状态
在加工过程中,应时刻关注刀具的状态,如 刀具是否松动、破损等。
禁止带手套操作
数控车床在高速旋转时,带手套操作容易发 生危险。
避免超负荷运转
在加工过程中,应避免因切削力过大而引起 的机床超负荷运转。
04 实际操作案例
表面质量不佳
02
调整切削参数和刀具角度,改善表面质量。
加工效率低下
03
优化加工参数和刀具路径,提高加工效率。
THANKS FOR WATCHING
感谢您的观看
并进行必要的编辑和修改。
加工参数设置
根据工件材料、刀具类型和加工要 求,设置合理的加工参数,如主轴 转速、进给速度、切削深度等。
自动加工
数控车床编程及其应用基础(ppt 27页)
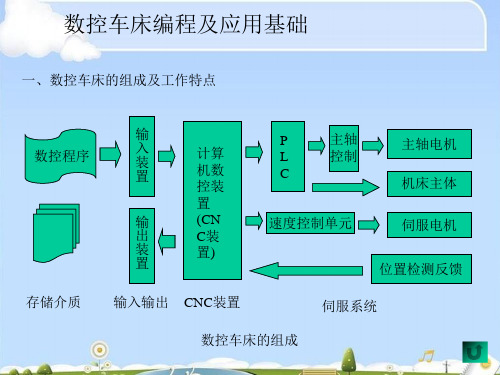
数控车床编程及应用基础
5、改善劳动条件 数控机床加工前经调整好后,输入程序并启动,机床就能自动连续地进 行加工,直至加工结束。操作者要做的只是程序的输入、编辑、零件装 卸、加工状态的观测、零件的检验等工作,劳动强度大大降低,机床操 作者的劳动趋于智力型工作。另外,机床一般是封闭加工的,既清洁, 又安全。
代码
功能字
代码
功能字
M00
程序停止
M08
开冷却泵
M02
程序结束
M09
关冷却泵
M03
主轴顺时针旋转 M12
程序暂停
M04
主轴逆时针旋转 M30
程序停止并返回开始处
M05
主轴旋转停止
M92
程序无条件跳转
数控车床编程及应用基础
2、进给量指令 (F功能) 指令格式 F_ 指令功能 F表示进給地址符。 指令说明 F表示主轴每转进给量,单位为mm/r;也可以表示进给速度, 单位为 mm/min。其量纲通过G指令设定。 有两种使用方法: ⑴、每转进给量:G99 F_ 例:G99 F0.2表示进给量为0.2mm/r ⑵、每分钟进给量:G98 F_ 例:G98 F100表示进给量为100mm/min 注:G98可省略。
2、加工精度高 数控机床的加工精度一般可达0.005~0.1mm,数控机床是按数字信号形 式控制的,数控装置每输出一个脉冲信号,机床移动部件移动一个脉冲 当量(一般为0.001mm),而且机床进给传动链的反向间隙与丝杆螺距平 均误差可由数控装置进行补偿,因此,数控机床定位精度比较高。
数控车床编程及应用基础
数控车床编程及应用基础
⑵、选择可转位刀片型号
选择刀片断屑槽型 :根据工件材料的切削性能选用合适的刀片断屑槽型
数控编程教程(共95张PPT)

因此,这种格式具有程序简单、可读性强,易于检查等优点。
第二节 数控编程常用的指令及其格式
主程序、子程序
在一个零件的加工程序 中,若有一定量的连续 的程序段在几处完全重 复出现,则可将这些重 复的程序串单独抽出来, 按一定的格式做成子程 序。
11/7/2023
-25-
第二节 数控编程常用的指令及其格式
码的程序段中有效; ● 模态M功能(续效代码):一组可相互注销的 M功
能,这些功能在被同一组的另一个功能注销前一直 有效。
第三章 数控系统编程指令体系
模态 M功能组中包含一个缺省功能,系统上电时 将被初始化为该功能。
M 功能还可分为前作用 M 功能和后作用 M 功能二类。 ● 前作用 M 功能:在程序段编制的轴运动之前执行; ● 后作用 M 功能:在程序段编制的轴运动之后执行。
迹生成功能进行数控编程。
4.后置代码生成 后置处理的目的是形成数控指令文件,利用CAM系统提供的后置
处理器可方便地生成和特定机床相匹配的加工代码。
5.加工代码输出
第一节 数控编程的几何基础
1.1 机床坐标系 为了确定机床个运动部件的运动方向和移动距离,需要
在机床上建立一个坐标系,这个坐标系就叫做机床坐标系 1.2 机床坐标轴及其方向
常用地址码的含义如表所示
机能 程序号 顺序号 准备机能
坐标指令
进给机能 主轴机能 刀具机能
辅助机能
补偿 暂停 子程序调用 重复 参数
地址码
O N G X.Y.Z A.B.C.U.V.W R I.J.K F S T
M B
H.D P.X
I P.Q.R
意义
程序编号 顺序编号 机床动作方式指令 坐标轴移动指令 附加轴移动指令 圆弧半径 圆弧中心坐标 进给速度指令 主轴转速指令 刀具编号指令
第二节 数控编程常用的指令及其格式
主程序、子程序
在一个零件的加工程序 中,若有一定量的连续 的程序段在几处完全重 复出现,则可将这些重 复的程序串单独抽出来, 按一定的格式做成子程 序。
11/7/2023
-25-
第二节 数控编程常用的指令及其格式
码的程序段中有效; ● 模态M功能(续效代码):一组可相互注销的 M功
能,这些功能在被同一组的另一个功能注销前一直 有效。
第三章 数控系统编程指令体系
模态 M功能组中包含一个缺省功能,系统上电时 将被初始化为该功能。
M 功能还可分为前作用 M 功能和后作用 M 功能二类。 ● 前作用 M 功能:在程序段编制的轴运动之前执行; ● 后作用 M 功能:在程序段编制的轴运动之后执行。
迹生成功能进行数控编程。
4.后置代码生成 后置处理的目的是形成数控指令文件,利用CAM系统提供的后置
处理器可方便地生成和特定机床相匹配的加工代码。
5.加工代码输出
第一节 数控编程的几何基础
1.1 机床坐标系 为了确定机床个运动部件的运动方向和移动距离,需要
在机床上建立一个坐标系,这个坐标系就叫做机床坐标系 1.2 机床坐标轴及其方向
常用地址码的含义如表所示
机能 程序号 顺序号 准备机能
坐标指令
进给机能 主轴机能 刀具机能
辅助机能
补偿 暂停 子程序调用 重复 参数
地址码
O N G X.Y.Z A.B.C.U.V.W R I.J.K F S T
M B
H.D P.X
I P.Q.R
意义
程序编号 顺序编号 机床动作方式指令 坐标轴移动指令 附加轴移动指令 圆弧半径 圆弧中心坐标 进给速度指令 主轴转速指令 刀具编号指令
数控机床及编程PPT课件

02
建立数学模型
根据加工工艺,建立被加工零件的几何模型,并转换 为数控机床能够识别的坐标系。
03
编写加工程序
根据建立的数学模型和加工要求,利用数控编程语言 编写加工程序。
04
程序校验与修改
将编写好的加工程序输入数控机床进行校验,根据校 验结果修改程序。
05
加工与检测
将校验通过的加工程序输入数控机床进行加工,并对 加工后的零件进行检测。
02
数控编程基础
数控编程的基本概念
数控编程定义
数控编程是利用计算机编程语言对数控机床进行控 制的过程,以实现自动化加工。
数控编程的优点
提高加工精度、加工效率、降低劳动强度、实现复 杂零件的加工。
数控编程的适用范围
广泛应用于机械、汽车、航空、轻工等领域。
数控编程的步骤与流程
01
确定加工工艺
根据零件图纸和加工要求,确定加工工艺,包括加工 方法、加工顺序、刀具选择等。
对加工后的零件进行质量 检测和控制,确保达到预 期的加工精度和质量要求 。
数控加工工艺参数的选择与优化
主轴转速
根据加工材料、刀具材料和切削用量等参数,合 理选择主轴转速,确保切削效率和加工质量。
进给速度
根据切削用量和刀具参数,合理选择进给速度, 以获得良好的切削效果和求和刀具参数,合理选择切削深度与 宽度,以提高加工效率和刀具寿命。
冷却方式与切削液
根据加工要求和材料特性,选择适当的冷却方式 和切削液,以降低切削温度、减小刀具磨损并提 高表面质量。
04
数控机床的操作与维护
数控机床的操作规程与注意事项
操作规程
在操作数控机床之前,必须熟悉机床的操作规程,包括开机、关 机、急停等步骤。
数控车床培训PPT幻灯片(精)
学习氛围浓厚,收获颇丰。
03
建议和意见
部分学员提出,希望今后能增加更多实际操作的机会,以便更好地掌握
数控车床的操作技能;还有学员建议加强数控编程方面的培训,提高编
程水平。
行业发展趋势分析预测
智能化发展
随着人工智能技术的不断发展,数控 车床将实现更高程度的智能化,提高 加工精度和效率。
绿色环保
环保意识的提高将促使数控车床行业 朝着更加环保的方向发展,如采用环 保材料、降低能耗等。
复合加工技术
复合加工技术将成为未来数控车床发 展的重要趋势,实现一台机床完成多 种加工任务,提高加工效率。
高精度、高速度
随着制造业对加工精度和效率的要求 不断提高,高精度、高速度的数控车 床将成为市场主流。
THANKS.
案例二
箱体类组合件加工
难点与问题
箱体类组合件结构复杂,需要保证较高的形位公差和配合 精度。
解决方案
采用高精度数控车床进行加工,使用CAD/CAM技术进行 编程和仿真。合理安排加工工艺和切削参数,保证加工精 度和效率。同时采用专用夹具和测量设备来保证定位和测 量精度。
数控车床维护与保
04
养
设备日常检查内容及方法
案例二:模具型腔加工
在此添加您的文本16字
难点与问题:模具型腔形状复杂,精度要求高。
在此添加您的文本16字
解决方案:采用高精度数控车床和专用刀具进行加工,使 用CAD/CAM技术进行编程和仿真。
组合件加工案例
案例一
轴承座与轴承盖组合件加工
难点与问题
组合件需要保证较高的配合精度和位置精度。
解决方案
采用一次装夹完成多个面的加工方式,使用专用夹具保证 定位精度和重复定位精度。同时合理安排加工工艺和切削 参数,保证加工精度和效率。
《数控车床编程基础》PPT课件
2、1 数控车床编程特点 一、坐标系统
机床坐标系:是数控机床安装调试时便设定好的一固定的坐标系统。机
床原点在主轴端面中心,参考点在X轴和Z轴的正向极限位置处
编程坐标系:是在对图纸上零件编程时就建立的,程序数据便是基于该
坐标系的坐标值。
工件坐标系时编程坐标系在机床上的具体体现。由相应的编程指令建
立。
由对刀操作建立三者之间的精相选p互pt 联系
❖编程方式可由指令指定。也可由参数设定。
❖一般默认直径方式。
如:华中数控 G36|—直径编程 G37—半径编程
精选ppt
15
西门子 G22—直径编程 G23—半径编程
三、进刀和退刀方式
❖进刀时采用快速走刀接近工件切削起点附
近的某个点,再改用切削进给,以减少空走 刀的时间,提高加工效率。
➢ 切削起点的确定与工件毛坯余量大小有关,应以刀具快
定位置。
➢G54~G59 方式在机床坐标系中直接设定工件
原点,与起刀点的位置无关。
精选ppt
26
说明
➢1、G54~G59是系统预置的六个坐标系,可根据
需要选用。
➢2、G54~G59建立的工件坐标原点是相对于机床
原点而言的,在程序运行前已设定好,在程序运行 中是无法重置的。
➢3、G54~G59预置建立的工件坐标原点在机床坐
为什么要用恒线速度和限制主轴最高转速?
精选ppt
33
五、进给功能F
➢F 指令表示刀具相对于工件的合成进给速度,F
的单位有两种:
每分钟进给 G94 (G98) :mm/min
每转进给 G95 (G99) :r/mm
➢实际进给速度可借助机床控制面板上的进给倍率
数控编程(共113张PPT)
说明: (1)G00指令刀具相对于工件从当前位置以各轴预先设定的 快移进给速度移动到程序段所指定的下一个定位点; (2)G00指令中的快进速度由机床参数对各轴分别设定,不能用
程序规定。由于各轴以各自速度移动,不能保证各轴同时到达终点, 因而联动直线轴的合成轨迹并不总是直线。
(3)快移速度可由面板上的快速修调旋钮修正。
G01Z0F0.1;
X60.Z-30.;
W-20.; G02U40.W-20.R2X120.; G00X200.Z100.;
M05;
M30;
第四节 车削固定循环
例7
T0202 S800M03
G00X28.Z2.
G71P10Q20 N10G41G00X46.
U-4.Z-2.
G01X32. G01Z-70.
N20G40G01X28.
M05
M30
第四节 车削固定循环
2.端面车削固定循环(G72)
1)格式 G72W(△d)R(e) G72P(ns)Q(nf)U(△u)W(△w)F(f)S(s)T(t)
△t,e,ns,nf, △u, △w,f,s及t的含义与G71相同
第四节 车削固定循环
2)功能 如果在下图用程序决定A至A’至B的精加工形状,用△d(切削深度) 车掉指定的区域,留精加工预留量△u/2及△w。
第四节 车削固定循环
例6
R20
20 40 30
φ110 φ60 φ40
T0101; S800M03; G00X120.Z2.;
N10G42G00X40.;
量,为零时可省略。
第二节 数控车床的基本指令
5.暂停指令G04
格式:G04 X(P) ,
说明: (1) G04在前一程序段的速度降到零之后才开始暂停动作。
程序规定。由于各轴以各自速度移动,不能保证各轴同时到达终点, 因而联动直线轴的合成轨迹并不总是直线。
(3)快移速度可由面板上的快速修调旋钮修正。
G01Z0F0.1;
X60.Z-30.;
W-20.; G02U40.W-20.R2X120.; G00X200.Z100.;
M05;
M30;
第四节 车削固定循环
例7
T0202 S800M03
G00X28.Z2.
G71P10Q20 N10G41G00X46.
U-4.Z-2.
G01X32. G01Z-70.
N20G40G01X28.
M05
M30
第四节 车削固定循环
2.端面车削固定循环(G72)
1)格式 G72W(△d)R(e) G72P(ns)Q(nf)U(△u)W(△w)F(f)S(s)T(t)
△t,e,ns,nf, △u, △w,f,s及t的含义与G71相同
第四节 车削固定循环
2)功能 如果在下图用程序决定A至A’至B的精加工形状,用△d(切削深度) 车掉指定的区域,留精加工预留量△u/2及△w。
第四节 车削固定循环
例6
R20
20 40 30
φ110 φ60 φ40
T0101; S800M03; G00X120.Z2.;
N10G42G00X40.;
量,为零时可省略。
第二节 数控车床的基本指令
5.暂停指令G04
格式:G04 X(P) ,
说明: (1) G04在前一程序段的速度降到零之后才开始暂停动作。
《数控车床编程基础》PPT课件讲义
加工步骤:选择机床;机床回零;安装零件;输入程序;检查运行轨迹; 安装刀具;对刀;设置参数;自动加工。
数控程序
…… G03X26.0Z-29.09R20.0 G02Z-44.09R15.61 G01Z-54.09 X26.0 Z-64.09 ……
小结
一、数控编程概述 二、编程方法(G00、G01、G02、G03) 三、实例与加工 四、思考题
G70
G90
02
04
01 G71
G91
G22 03 G23
(1)快速定位指令
G00 X—Z—; 用于非切削快速定位,移动 速度由系统内部参数确定。
(2)直线插补指令(G01)
G01 X—Z—F— 用于刀具的切削过程,刀具的轨迹为 直线,移动的速度由F指令和操作面板 上的倍率开关决定。
绝对坐标编程:G90G01Z-49F30 绝对坐标编程:G90G01X30Z-25F100 相对坐标编程:G91G01Z-50F30 相对坐标编程:G91G01X20Z-27F100
N100G01X50.205F100M03S100;
语句号 地址符程序字
数字符 程序段
数G字准符备有功整能数和实数两种形式
结束符
整M数辅型助用功于功能地址; 实能数型用于坐标字,是否必须写小数点, 取F进决给于速机度床参数的设定
S主轴转速
4、坐标系和坐标轴的命名
机床坐标系:出厂已设定,其原点称为机械 原点,是主轴旋转中心与卡盘后端面的交 点。
Thank you.
演讲结速,谢谢观赏!
PPT常用编辑图使用方法
1.取消组合
2.填充颜色
3.调整大小
选择您要用到的图标单击右键选择“ 取消组 合”
右键单击您要使用的图标选择“填充 ”,选 择任意 颜色
数控程序
…… G03X26.0Z-29.09R20.0 G02Z-44.09R15.61 G01Z-54.09 X26.0 Z-64.09 ……
小结
一、数控编程概述 二、编程方法(G00、G01、G02、G03) 三、实例与加工 四、思考题
G70
G90
02
04
01 G71
G91
G22 03 G23
(1)快速定位指令
G00 X—Z—; 用于非切削快速定位,移动 速度由系统内部参数确定。
(2)直线插补指令(G01)
G01 X—Z—F— 用于刀具的切削过程,刀具的轨迹为 直线,移动的速度由F指令和操作面板 上的倍率开关决定。
绝对坐标编程:G90G01Z-49F30 绝对坐标编程:G90G01X30Z-25F100 相对坐标编程:G91G01Z-50F30 相对坐标编程:G91G01X20Z-27F100
N100G01X50.205F100M03S100;
语句号 地址符程序字
数字符 程序段
数G字准符备有功整能数和实数两种形式
结束符
整M数辅型助用功于功能地址; 实能数型用于坐标字,是否必须写小数点, 取F进决给于速机度床参数的设定
S主轴转速
4、坐标系和坐标轴的命名
机床坐标系:出厂已设定,其原点称为机械 原点,是主轴旋转中心与卡盘后端面的交 点。
Thank you.
演讲结速,谢谢观赏!
PPT常用编辑图使用方法
1.取消组合
2.填充颜色
3.调整大小
选择您要用到的图标单击右键选择“ 取消组 合”
右键单击您要使用的图标选择“填充 ”,选 择任意 颜色
- 1、下载文档前请自行甄别文档内容的完整性,平台不提供额外的编辑、内容补充、找答案等附加服务。
- 2、"仅部分预览"的文档,不可在线预览部分如存在完整性等问题,可反馈申请退款(可完整预览的文档不适用该条件!)。
- 3、如文档侵犯您的权益,请联系客服反馈,我们会尽快为您处理(人工客服工作时间:9:00-18:30)。
第三节 数控车床编程基础知识 一、数控机床的坐标系
1.机床坐标系
(1)机床坐标系的定义 为了确定机床的运动方向和移动距离,就要在机床上建立一
个坐标系,这个坐标系就叫机床坐标系,又称标准坐标系。
1
(2)机床坐标系中的规定 1)确定机床坐标系的方向时规定:永远假定刀具相对于静 止的工件而运动。 2)对于机床坐标系的方向,统一规定增大工件与刀具间距 离的方向为正方向。 3)数控机床的坐标系采用符合右手定则规定的笛卡儿坐标 系。
例 O0000; G98 G40 G21; T0101;
……
(程序号) (程序初始化) 跳跃 有时,在程序段的前面有“/”符号,该符号称为斜杠跳 跃符号,该程序段称为可跳跃程序段。
例 /N10 G00 X100.0;
16
(4)程序段注释 为了方便检查、阅读数控程序,在许多数控系统中允许 对程序进行注释,注释可以作为对操作者的提示显示在屏幕 上,但注释对机床动作没有丝毫影响。
O0001;
程序号
N10 G99 G40 G21;
N20 T0101;
N30 G00 X100.0 Z100.0; 程序内容
N40 M03 S800;
……
N200 G00 X100.0 Z100.0;
N210 M30;
程序结束
8
(2)程序内容 程序内容是整个加工程序的核心,它由许多程序段组成, 每个程序段由一个或多个指令构成,它表示数控机床中除程序 结束外的全部动作。
O0001;
程序号
N10 G99 G40 G21;
N20 T0101;
N30 G00 X100.0 Z100.0; 程序内容
N40 M03 S800;
……
N200 G00 X100.0 Z100.0;
N210 M30;
程序结束
10
2.程序段的组成
(1)程序段基本格式
N G X Y Z F S T M LF
工件坐标系原点
6
(2)工件坐标系原点 工件坐标系原点又称编程原点,指工件装夹完成后, 选择工件上的某一点作为编程或工件加工的基准点。工件 坐标系原点在图中以符号“ ”表示。
工件坐标系原点
7
二、数控加工程序的格式与组成
1.程序的组成
(1)程序号 每一个存储在系统存储器中的程序都需要指定一个程序号 以相互区别,这种用于区别零件加工程序的代号称为程序号。
14
对于图中的直线刀具轨迹,其程序段可写成如下格式: N10 G90 G01 X100.0 Z60.0 F100 S300 T01 M03; 如果在该程序段前已指定了刀具功能、转速功能、辅助功能, 则该程序段可写成: N10 G01 X100.0 Z60.0 F100;
15
3)程序段结束 程序段以结束标记“CR(或LF)”结 束,实际使用时,常用符号“;”或“*”表示“CR(或 LF)”。
程序 准备 段号 功能
尺寸字
进给 主轴 刀具 辅助 结束 功能 功能 功能 功能 标记
13
例 如图所示,为了将刀具从P1点移到P2点,必须在程序段中 明确以下几点:
①移动的目标是那里? ②沿什么样的轨迹移动? ③移动速度有多快? ④刀具的切削速度是多少? ⑤选择哪一把刀移动? ⑥机床还需要哪些辅助动作?
2
(3)机床坐标系的方向
1)Z坐标方向 Z坐标的运动由主要传递切削动力的主轴所决定。 2)X坐标方向 X坐标一般为水平方向并垂直于Z轴。 3)Y坐标方向 Y坐标垂直于X、Z坐标轴。 4)旋转轴方向 旋转坐标A、B、C对应表示其轴线分别平行于X、 Y、Z坐标轴的旋转坐标。
b)
数控车床的坐标系 a)前置刀架式数控车床的坐标系 b)后置刀架式数控车床的坐标系 3
机床参考点与机床原点的距离由系统参数设定,其值可 以是零,如果其值为零则表示机床参考点和机床零点重合。
机床原点与参考点
O—机床原点 O1—机床参考点
5
2.工件坐标系
(1)工件坐标系的定义 为了便于尺寸计算与检查,加工程序的坐标原点一般都尽 量与零件图样的尺寸基准相一致。这种针对某一工件并根据零 件图样建立的坐标系称为工件坐标系(又称编程坐标系)。
12
2)程序段内容 程序段的中间部分是程序段的内容,程 序内容应具备六个基本要素:
➢准备功能字 ➢尺寸功能字 ➢进给功能字 ➢主轴功能字 ➢刀具功能字 ➢辅助功能字
但并不是所有程序段都必须包含所有功能字,有时一个 程序段内仅包含其中一个或几个功能字也是允许的。
N G X Y Z F S T M LF
尺寸字
进给 主轴 刀具 辅助 结束 功能 功能 功能 功能 标记
在大部分系统中,程序段号仅作为“跳转”或“程序检索” 的目标位置指示。它的大小及次序可以颠倒,也可以省略。程 序段号省略时,该程序段将不能作为“跳转”或“程序检索” 的目标程序段。
程序段号也可以由数控系统自动生成,程序段号的递增量 可以通过 “机床参数”进行设置,一般可设定增量值为10。
(4)机床原点与机床参考点 1)机床原点 机床原点(又称为机床零点)是机床上设
置的一个固定的点,即机床坐标系的原点。它是一个固定的 点。机床原点是数控机床进行加工或位移的基准点。
机床原点的位置
a)机床原点位于卡盘中心
b)机床原点位于刀架正向运动极限点
4
2)机床参考点 数控车床的第一参考点一般位于刀架正 向移动的极限点位置,并由机械挡块来确定其具体的位置。
程序 准备 段号 功能
尺寸字
进给 主轴 刀具 辅助 结束 功能 功能 功能 功能 标记
例 N50 G01 X30.0 Z30.0 F100 S800 T01 M03;
11
(2)程序段的组成 1)程序段号 程序段号由地址符“N”开头,其后为若干位
数字。
N G X Y Z F S T M LF
程序 准备 段号 功能
O0001;
程序号
N10 G99 G40 G21;
N20 T0101;
N30 G00 X100.0 Z100.0; 程序内容
N40 M03 S800;
……
N200 G00 X100.0 Z100.0;
N210 M30;
程序结束
9
(3)程序结束 结束部分由程序结束指令构成,它必须写在程序的最后。 可以作为程序结束标记的M指令有M02和M30,它们代表零 件加工程序的结束。
1.机床坐标系
(1)机床坐标系的定义 为了确定机床的运动方向和移动距离,就要在机床上建立一
个坐标系,这个坐标系就叫机床坐标系,又称标准坐标系。
1
(2)机床坐标系中的规定 1)确定机床坐标系的方向时规定:永远假定刀具相对于静 止的工件而运动。 2)对于机床坐标系的方向,统一规定增大工件与刀具间距 离的方向为正方向。 3)数控机床的坐标系采用符合右手定则规定的笛卡儿坐标 系。
例 O0000; G98 G40 G21; T0101;
……
(程序号) (程序初始化) 跳跃 有时,在程序段的前面有“/”符号,该符号称为斜杠跳 跃符号,该程序段称为可跳跃程序段。
例 /N10 G00 X100.0;
16
(4)程序段注释 为了方便检查、阅读数控程序,在许多数控系统中允许 对程序进行注释,注释可以作为对操作者的提示显示在屏幕 上,但注释对机床动作没有丝毫影响。
O0001;
程序号
N10 G99 G40 G21;
N20 T0101;
N30 G00 X100.0 Z100.0; 程序内容
N40 M03 S800;
……
N200 G00 X100.0 Z100.0;
N210 M30;
程序结束
8
(2)程序内容 程序内容是整个加工程序的核心,它由许多程序段组成, 每个程序段由一个或多个指令构成,它表示数控机床中除程序 结束外的全部动作。
O0001;
程序号
N10 G99 G40 G21;
N20 T0101;
N30 G00 X100.0 Z100.0; 程序内容
N40 M03 S800;
……
N200 G00 X100.0 Z100.0;
N210 M30;
程序结束
10
2.程序段的组成
(1)程序段基本格式
N G X Y Z F S T M LF
工件坐标系原点
6
(2)工件坐标系原点 工件坐标系原点又称编程原点,指工件装夹完成后, 选择工件上的某一点作为编程或工件加工的基准点。工件 坐标系原点在图中以符号“ ”表示。
工件坐标系原点
7
二、数控加工程序的格式与组成
1.程序的组成
(1)程序号 每一个存储在系统存储器中的程序都需要指定一个程序号 以相互区别,这种用于区别零件加工程序的代号称为程序号。
14
对于图中的直线刀具轨迹,其程序段可写成如下格式: N10 G90 G01 X100.0 Z60.0 F100 S300 T01 M03; 如果在该程序段前已指定了刀具功能、转速功能、辅助功能, 则该程序段可写成: N10 G01 X100.0 Z60.0 F100;
15
3)程序段结束 程序段以结束标记“CR(或LF)”结 束,实际使用时,常用符号“;”或“*”表示“CR(或 LF)”。
程序 准备 段号 功能
尺寸字
进给 主轴 刀具 辅助 结束 功能 功能 功能 功能 标记
13
例 如图所示,为了将刀具从P1点移到P2点,必须在程序段中 明确以下几点:
①移动的目标是那里? ②沿什么样的轨迹移动? ③移动速度有多快? ④刀具的切削速度是多少? ⑤选择哪一把刀移动? ⑥机床还需要哪些辅助动作?
2
(3)机床坐标系的方向
1)Z坐标方向 Z坐标的运动由主要传递切削动力的主轴所决定。 2)X坐标方向 X坐标一般为水平方向并垂直于Z轴。 3)Y坐标方向 Y坐标垂直于X、Z坐标轴。 4)旋转轴方向 旋转坐标A、B、C对应表示其轴线分别平行于X、 Y、Z坐标轴的旋转坐标。
b)
数控车床的坐标系 a)前置刀架式数控车床的坐标系 b)后置刀架式数控车床的坐标系 3
机床参考点与机床原点的距离由系统参数设定,其值可 以是零,如果其值为零则表示机床参考点和机床零点重合。
机床原点与参考点
O—机床原点 O1—机床参考点
5
2.工件坐标系
(1)工件坐标系的定义 为了便于尺寸计算与检查,加工程序的坐标原点一般都尽 量与零件图样的尺寸基准相一致。这种针对某一工件并根据零 件图样建立的坐标系称为工件坐标系(又称编程坐标系)。
12
2)程序段内容 程序段的中间部分是程序段的内容,程 序内容应具备六个基本要素:
➢准备功能字 ➢尺寸功能字 ➢进给功能字 ➢主轴功能字 ➢刀具功能字 ➢辅助功能字
但并不是所有程序段都必须包含所有功能字,有时一个 程序段内仅包含其中一个或几个功能字也是允许的。
N G X Y Z F S T M LF
尺寸字
进给 主轴 刀具 辅助 结束 功能 功能 功能 功能 标记
在大部分系统中,程序段号仅作为“跳转”或“程序检索” 的目标位置指示。它的大小及次序可以颠倒,也可以省略。程 序段号省略时,该程序段将不能作为“跳转”或“程序检索” 的目标程序段。
程序段号也可以由数控系统自动生成,程序段号的递增量 可以通过 “机床参数”进行设置,一般可设定增量值为10。
(4)机床原点与机床参考点 1)机床原点 机床原点(又称为机床零点)是机床上设
置的一个固定的点,即机床坐标系的原点。它是一个固定的 点。机床原点是数控机床进行加工或位移的基准点。
机床原点的位置
a)机床原点位于卡盘中心
b)机床原点位于刀架正向运动极限点
4
2)机床参考点 数控车床的第一参考点一般位于刀架正 向移动的极限点位置,并由机械挡块来确定其具体的位置。
程序 准备 段号 功能
尺寸字
进给 主轴 刀具 辅助 结束 功能 功能 功能 功能 标记
例 N50 G01 X30.0 Z30.0 F100 S800 T01 M03;
11
(2)程序段的组成 1)程序段号 程序段号由地址符“N”开头,其后为若干位
数字。
N G X Y Z F S T M LF
程序 准备 段号 功能
O0001;
程序号
N10 G99 G40 G21;
N20 T0101;
N30 G00 X100.0 Z100.0; 程序内容
N40 M03 S800;
……
N200 G00 X100.0 Z100.0;
N210 M30;
程序结束
9
(3)程序结束 结束部分由程序结束指令构成,它必须写在程序的最后。 可以作为程序结束标记的M指令有M02和M30,它们代表零 件加工程序的结束。