热轧带钢甩尾原因分析及控制
热轧质量缺陷及产生原因
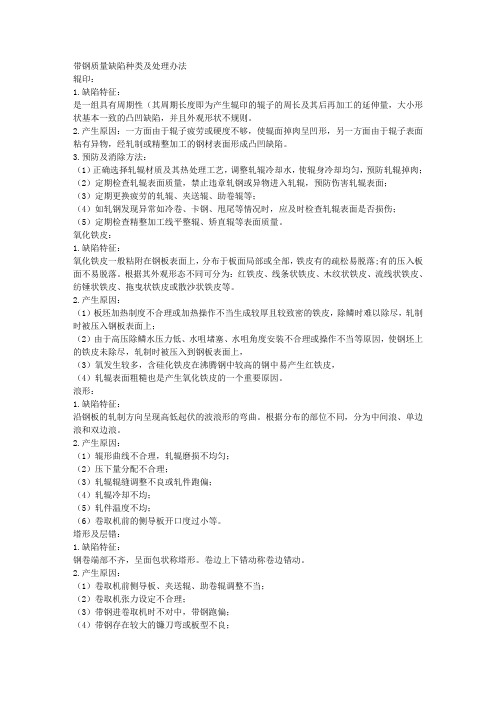
带钢质量缺陷种类及处理办法辊印:1.缺陷特征:是一组具有周期性(其周期长度即为产生辊印的辊子的周长及其后再加工的延伸量,大小形状基本一致的凸凹缺陷,并且外观形状不规则。
2.产生原因:一方面由于辊子疲劳或硬度不够,使辊面掉肉呈凹形,另一方面由于辊子表面粘有异物,经轧制或精整加工的钢材表面形成凸凹缺陷。
3.预防及消除方法:(1)正确选择轧辊材质及其热处理工艺,调整轧辊冷却水,使辊身冷却均匀,预防轧辊掉肉;(2)定期检查轧辊表面质量,禁止违章轧钢或异物进入轧辊,预防伤害轧辊表面;(3)定期更换疲劳的轧辊、夹送辊、助卷辊等;(4)如轧钢发现异常如冷卷、卡钢、甩尾等情况时,应及时检查轧辊表面是否损伤;(5)定期检查精整加工线平整辊、矫直辊等表面质量。
氧化铁皮:1.缺陷特征:氧化铁皮一般粘附在钢板表面上,分布于板面局部或全部,铁皮有的疏松易脱落;有的压入板面不易脱落。
根据其外观形态不同可分为:红铁皮、线条状铁皮、木纹状铁皮、流线状铁皮、纺锤状铁皮、拖曳状铁皮或散沙状铁皮等。
2.产生原因:(1)板坯加热制度不合理或加热操作不当生成较厚且较致密的铁皮,除鳞时难以除尽,轧制时被压入钢板表面上;(2)由于高压除鳞水压力低、水咀堵塞、水咀角度安装不合理或操作不当等原因,使钢坯上的铁皮未除尽,轧制时被压入到钢板表面上,(3)氧发生较多,含硅化铁皮在沸腾钢中较高的钢中易产生红铁皮,(4)轧辊表面粗糙也是产生氧化铁皮的一个重要原因。
浪形:1.缺陷特征:沿钢板的轧制方向呈现高低起伏的波浪形的弯曲。
根据分布的部位不同,分为中间浪、单边浪和双边浪。
2.产生原因:(1)辊形曲线不合理,轧辊磨损不均匀;(2)压下量分配不合理;(3)轧辊辊缝调整不良或轧件跑偏;(4)轧辊冷却不均;(5)轧件温度不均;(6)卷取机前的侧导板开口度过小等。
塔形及层错:1.缺陷特征:钢卷端部不齐,呈面包状称塔形。
卷边上下错动称卷边错动。
2.产生原因:(1)卷取机前侧导板、夹送辊、助卷辊调整不当;(2)卷取机张力设定不合理;(3)带钢进卷取机时不对中,带钢跑偏;(4)带钢存在较大的镰刀弯或板型不良;(5)卷取机卸卷时将钢卷头部拽出。
热连轧机带钢甩尾现象的减防性研究

同时 , 必要时我们采用大 凸度轧制 。有效 防
l甩 尾 。 E
活 套 实
活套 角 活 套 张 抗 抖 防 甩
图 4 活 套 工 作 的 进 程
当在抛 尾过程 中落套过慢或过快 , 导致 张力异 常 , 在机 架 间活套 自由辊位 置过 高 , 轧 件 出了前机架导致突然失张 , 容易发生甩尾 ,
防止此类型甩尾发生 的方法是确保位置传感 器和套活正 常工 作 , 在轧制 薄规 格 ( ≤2 h .
O n 时 可 以根 据 轧 制状 态 适 当 的 调 整 立 辊 m )
的宽度 , 采用轧边模式使立辊咬住轧件 , 从而 得 到一个 稳定 的 张力 , 减小 因失 张 而 导 致 的
热连轧机带钢甩尾现 象的减防性研究
一
炼 轧 厂
摘
郁盛 富
要
甩 尾是热连轧带钢生产 中常见的不 正常抛 尾现象 , 文分 析了导致甩尾 现象 产生 的原因 本 并 找出有效减 防甩尾发生 的方法 , 具有降低 生产成本 、 稳定产品质量 、 稳顺生产的意义。
1 前言
涟 钢是 我 国较 早 引进薄 板坯 连铸连 轧生
目
~
一 一
49 3
*
—一 —
tP m s
…一一 ~一— 一 —
n m
其 要控 制好 尾 部 的温 度 , 保证 好 尾 形 和 切 尾 要 干净 , 时 , 合理 分 配 好 轧 制 力 , 同 要 遵循 前 机 架保 证厚 度 , 后机 架保 证板形 的原 则 。
4 0—7 5
调平操作时通过抬高或压低操作侧来控 制 已出现 或 有 出 现 趋 势 的跑 偏 或 浪 形 及 时有效地调平操作有效减防甩尾发生的最直 接方式 , 总结起来主要有以下几点 :
热轧带钢生产工艺及常见质量问题探讨
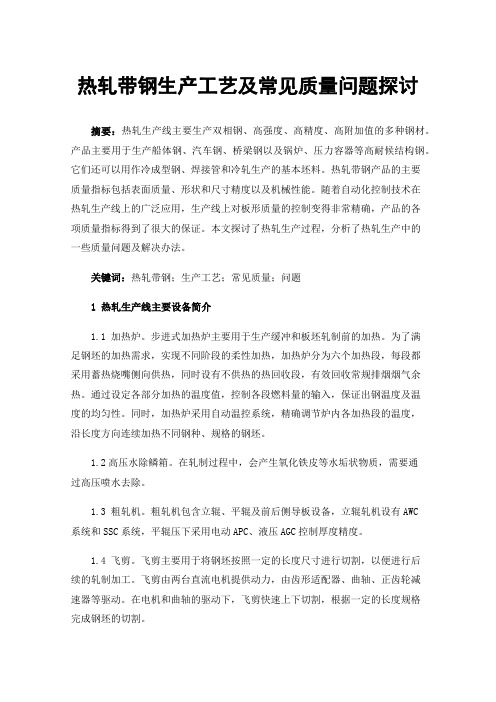
热轧带钢生产工艺及常见质量问题探讨摘要:热轧生产线主要生产双相钢、高强度、高精度、高附加值的多种钢材。
产品主要用于生产船体钢、汽车钢、桥梁钢以及锅炉、压力容器等高耐候结构钢。
它们还可以用作冷成型钢、焊接管和冷轧生产的基本坯料。
热轧带钢产品的主要质量指标包括表面质量、形状和尺寸精度以及机械性能。
随着自动化控制技术在热轧生产线上的广泛应用,生产线上对板形质量的控制变得非常精确,产品的各项质量指标得到了很大的保证。
本文探讨了热轧生产过程,分析了热轧生产中的一些质量问题及解决办法。
关键词:热轧带钢;生产工艺;常见质量;问题1热轧生产线主要设备简介1.1 加热炉。
步进式加热炉主要用于生产缓冲和板坯轧制前的加热。
为了满足钢坯的加热需求,实现不同阶段的柔性加热,加热炉分为六个加热段,每段都采用蓄热烧嘴侧向供热,同时设有不供热的热回收段,有效回收常规排烟烟气余热。
通过设定各部分加热的温度值,控制各段燃料量的输入,保证出钢温度及温度的均匀性。
同时,加热炉采用自动温控系统,精确调节炉内各加热段的温度,沿长度方向连续加热不同钢种、规格的钢坯。
1.2高压水除鳞箱。
在轧制过程中,会产生氧化铁皮等水垢状物质,需要通过高压喷水去除。
1.3 粗轧机。
粗轧机包含立辊、平辊及前后侧导板设备,立辊轧机设有AWC系统和SSC系统,平辊压下采用电动APC、液压AGC控制厚度精度。
1.4 飞剪。
飞剪主要用于将钢坯按照一定的长度尺寸进行切割,以便进行后续的轧制加工。
飞剪由两台直流电机提供动力,由齿形适配器、曲轴、正齿轮减速器等驱动。
在电机和曲轴的驱动下,飞剪快速上下切割,根据一定的长度规格完成钢坯的切割。
1.5 精轧机。
精轧机是一种高精度轧制工艺,利用液压AGC等自动控制和补偿系统,通过液压系统和轧辊轧制板坯。
它主要由电动机、联轴器、减速器等驱动和传动,以获得高精度的轧制件外观和尺寸。
1.6卷取机。
采用全液压三助卷辊强力卷取机,采用了无极涨缩试卷筒和自动踏步控制AJC系统。
1780mm热轧带钢热卷箱开尾销动作异常问题分析与控制

:
后
一
道 次 轧制 后
,
由
输 送 辊 道 经 过 热 卷 箱 人 口 侧 导 ① 当 计 划 轧 制 较 软 的 材 质 时 要 适 当 放 大 人 口
, ,
板 进 人 热 卷 箱 成 卷 区 将 热 中 间 坯 卷 成热 带 钢 卷 开
卷 器 下 落 开 卷 后 再将 热 带 钢 运 送 至
。
关 键词 热 卷 箱
:
开尾 销
异 常动 作
1
引
言 2
,
设备 结 构 和 工艺 特点
.
热 卷箱 是 提 高 热 连 轧 产 品 质 量 的 关 键 设备 开
,
2
1
设备 结 构 及 用 途
1
卷 过 程 中 开 尾 销 正 常 插 人 是 保 证 钢 卷 完 全 开 卷 必 热 卷 箱 主 要 设 备 组 成 如 图
, ,
,
,
于 实 际 卷 径 机造 成 叠 轧 以 及 节 奏 废 钢 处 理 不 当 更 造成 长 时 间
;
,
② 钢 卷 材 质 较软
,
,
中 间 坯较 薄 以 及 主 动 移 送 功
3#
;
的 热 停 机 严 重影 响 整 个 生 产 线 的 稳 定 性 运 行
,
由两个 固
。
后导致尾部折叠现象 造成飞 剪高负荷工作 进人 轧 机 造 成 尾 部 叠 轧 若处 理不 当 将 会 造 成 长 时 间 热
,
定 在推 板 上 的 液压 缸驱 动 销轴 可 沿轴 向 伸 缩
尾 销 和 液 压缸 可 随 导 卫
一
开
起 运动
热轧带钢常见质量缺陷及其控制措施分析

热轧带钢常见质量缺陷及其控制措施分析作者:弓习峰来源:《中国科技博览》2017年第33期[摘要]对于企业而言,板材的轧制板材质量对其的经济效益有着直接的影响,更是体现了轧钢的水平现状,本文针对热轧带钢常见质量缺陷及其控制措施进行了论述,希望有一定的参考价值。
[关键词]热轧带钢;质量缺陷;控制措施中图分类号:TG335.11 文献标识码:A 文章编号:1009-914X(2017)33-0135-01前言社会的发展,促进了行业的进步和发展,也使得生产市场竞争越来越激烈,怎么对生产用原料的生产成本进行降低,让原料引起的质量问题的发生率减少,提升带钢质量,避免出现带钢镰刀弯,这是目前非常重要的研究课题。
通过对热轧带钢在生产的过程中出现的的质量问题的原因进行深入的分析和探究,运用有效的措施对这些问题进行合理的解决,这对提高热轧带钢产品质量有着十分重要的意义。
一、概述通常情况下,热轧带钢的具体质量要求包括:成品规格、凸度等方面允许的偏差,其中,卷形缺陷指标具体有塔型、镰刀弯等方面的偏差值,带钢表面和内部缺陷的要求具体有表面洁净度、折叠、气泡、铁皮压入、气泡、折叠等,其中还包括带头带尾精度指标、几何尺寸要求。
但是,在实际的生产当中,成品质量依然和理想标准不相符。
这就要求我们对常见的热轧带钢质量缺陷采取有效的控制措施,采用分类分析的方法,制定出系统的控制方案。
文中结合热轧生产线的设备特性及生产工艺流程,重点分析和阐述了带钢氧化铁皮压入及带钢镰刀弯两种质量缺陷成因及控制改进实践方案。
二、邯钢2250热轧生产线的设备特性及生产工艺流程邯钢2250热轧的粗轧机组是双四辊可逆式粗轧机组布置,可以在R1和R2两架粗轧机上实现3+3、3+5或0+7道次的可逆轧制,把板坯轧制成35 mm-60 mm厚的目标中间坯。
双四辊可逆式粗轧机组的优越性在于能够实现大压下量轧制,充分释放粗轧机R1的能力。
粗轧高温大压下的工艺设置可以有效破碎铸坯树枝状晶,从而改善组织的均匀性;四辊轧机比二辊轧机轧制更稳定,对板坯的轧制控制精度更高,更利于生产出高精度的中间坯[1]。
1450轧机热轧带钢甩尾原因分析及预防

陷
, 因此 , 避 免甩 尾 事 故 发 生 , 有 着 十 分 重要 的
轧制 中心线 行走 , 而是 在 某 一 机 架偏 向轧 机 的传 动 侧( 以下 简称 “ DS侧 ” ) 或 操作侧 ( 以下 简 称 “ OS
意义 。
2 甩尾 现 象 轧制 过程 中 , 由于板 形控 制操 作不 当等 原 因 , 轧 件偏 离轧 制 中心线 , 沿宽 度方 向两 侧延 伸不 均 , 抛 钢
1
引 言
的瞬 间机架 内轧 件突 然失去 张力 , 使轧 件跑 偏 加剧 ,
造 成轧 件尾 部打在 入 口导板 上折 入轧机 或 尾部 翻转 进入 轧 机, 从 而 出现轧 件尾 部 折迭 、 尾 部 破 碎 的
现象。
唐 山国丰热 轧薄 板 厂 一 车 间 1 4 5 0 l n m 生 产 线 是 国 内先 进 的连 铸 连 轧 生 产 线 ,2 0 0 6年 1月 份 投 产, 产 品厚 度范 围 1 . 2~1 2 . 7 mm, 主要 以 ≤3 . 5 ml T l 薄规 格为 主 。近 年来 由于 设 备 老 化等 原 因 , 生 产 过 程 中甩 尾事 故频 繁发 生 。而带 钢尾 部板 形控 制 是生 产过 程 中的难 点 , 甩 尾现 象直 接影 响带钢 表 面质 量 , 同时甩 尾 引起 轧机辊 系 中产生 的带 钢碎 片粘 压 在轧 辊上 , 造 成 轧 辊 损 伤 并 引 发 后 续 带 钢 表 面 质 量 缺
l e v e l m od e l ,r o l l i ng s p e c i ic f a t i on,p r o po s e d p r e v e nt i o n me as u r e s . Ke y Wo r ds:h ot—r o l l i n g s t r i p s t e e l ;t a i l wh i p p i n g;r e a s on; m e a s u r e s
浅谈热轧钢管尾部内折产生的原因及控制措施

浅谈热轧钢管尾部内折产生的原因及控制措施发布时间:2021-12-24T02:15:32.200Z 来源:《建筑科技》2021年11月中32期作者:张忠文[导读] 热轧钢管的生产技术以与冷轧钢管相对,前者指的是在结晶温度以上进行加工,而后者指的是在结晶温度以下进行施工。
热轧钢管在制作阶段会破坏钢管的结构组织,使得钢材结构中的晶粒细化,消除显微组织中的缺陷,进而使得钢管的结构和质量更加密实,在后续使用中的承载力、稳定性得到大幅度提升,是钢材加工中的重要技术之一。
天津钢管集团股份有限公司张忠文天津市东丽区摘要:热轧钢管的生产技术以与冷轧钢管相对,前者指的是在结晶温度以上进行加工,而后者指的是在结晶温度以下进行施工。
热轧钢管在制作阶段会破坏钢管的结构组织,使得钢材结构中的晶粒细化,消除显微组织中的缺陷,进而使得钢管的结构和质量更加密实,在后续使用中的承载力、稳定性得到大幅度提升,是钢材加工中的重要技术之一。
但是,现如今在热轧钢管制造加工中出现尾部内折的现象十分显著,使得生产加工企业承担的成本风险和技术风险进一步增加,不利于钢材制造企业的稳步发展,也制约了我国钢结构生产加工的技术提升。
在本文的研究中将针对钢管尾部内折现象出现的原因进行详细分析,并且提出相应的解决办法,力求为相关企业和技术人员提供借鉴与参考。
关键词:热轧钢管;尾部内折;产生原因;控制措施热轧钢管尾部内折现象产生的基本原理是钢管在加工阶段出现严重的不均匀受力、或者不均匀加热现象,导致其尾部出现了残余应力,与内外力作用水平之间的差异性较为明显,影响了钢管结构的内外部平衡现象,导致钢管加工之后尾部极易出现内折情况。
鉴于此,则需要对加工阶段的设备温度、加热时间、加热工具等进行研究,力求能够优化设备使用、产品生产的效果。
1管尾内折形貌和产生原因分析1.1管尾内折形状热轧钢管尾部出现内折的主要区域集中在钢管尾部的800mm-1500mm之间,内折情况并不严重时,则呈现出锯齿形状,而更为严重的则呈现出外翻现象。
热轧带钢尾部轧破分析及控制方法探讨

热轧带钢尾部轧破分析及控制方法探讨【摘要】热轧带钢尾部轧破主要有跑偏轧破、甩尾轧破、中浪轧破等,生产现场最多的就是跑偏轧破,引起跑偏轧破的各种因素较多,相互间有叠加影响,多因素的轧破严重制约生产。
通过对热轧带钢各类尾部轧破进行详细的成因分析,介绍了减少带钢尾部轧破相应的控制方法及措施。
【关键词】热轧带钢尾部轧破1.前言热连轧带钢生产,精轧在轧制薄规格(1.5*1035/2.0*1250/2.5*1500等以下)、硬质钢种宽轧件带钢时带钢尾部运行极不稳定,控制不好、操作不当不到位,非常容易发生带钢尾部轧破事故。
轧破给生产造成很大的危害,尾部破碎或折断很容易损伤辊面,造成产品的凹凸块缺陷,迫使更换轧辊;破碎残片如与轧件接触,又往往造成轧件表面刮伤或轧废堆钢事故;破碎残片带入卷取机内,轻者要影响卷取机的正常生产,重者还会损坏卷取机各辊面。
因此轧破破坏了精轧的轧制稳定性、连续性,严重时将影响合同完成率、事故辊耗加大,增加了工序制造成本。
随着八钢1750热轧产线轧制品种的多元化,每月生产硬质薄规格批量不断增大,造成带钢在精轧轧制稳定性存在较大问题,尾部轧破事故显得尤为突出,预防、减少带钢尾部轧破成为技术人员和操作人员的重点、难点工作。
2.带钢尾部轧破成因分析及控制方法2.1轧破定义“带钢轧破”,是指在正常生产过程中带钢在穿带、通板、抛钢时跑偏或甩尾的带钢边部或中部折叠进入下游机架,成品带钢表面出现多层重叠或轧穿、撕裂等现象称带钢轧破(如图1)。
图1 带钢轧破外观2.2带钢尾部轧破分类带钢尾部在精轧机内轧破表现形式较多,只有分清轧破各种表现形式,对症分析,才能制定有效的控制方法和操作思路。
(1) 按轧破宽度方向部位分:沿宽度方向尾部轧破形式分为边部(工作侧或传动侧)轧破和中间轧破两种,如图2。
A、边部轧破B、中间轧破图2 尾部轧破部位(2) 按轧破原因分:轧破原因较多,按轧破主要原因分为跑偏轧破、甩尾轧破、中浪或1/4浪叠轧轧破等各种形式,如图3。
- 1、下载文档前请自行甄别文档内容的完整性,平台不提供额外的编辑、内容补充、找答案等附加服务。
- 2、"仅部分预览"的文档,不可在线预览部分如存在完整性等问题,可反馈申请退款(可完整预览的文档不适用该条件!)。
- 3、如文档侵犯您的权益,请联系客服反馈,我们会尽快为您处理(人工客服工作时间:9:00-18:30)。
950热轧带钢甩尾原因分析特钢公司王洪立摘要:介绍川威950热轧带钢在轧制薄规格时精轧机组甩尾的现象,阐述了操作、导板、温度、负荷分配、活套及设备等对甩尾的影响,对其影响原理进行分析,并提出了以上各种原因引起甩尾的调整方法和解决措施。
关键词:精轧甩尾原因分析解决措施前言950热连轧带钢甩尾一般多发生于3.0mm到1.5mm下规格时,甩尾现象是热轧带钢生产中常见的超常现象,是影响热轧带钢生产的一个比较突出的问题,因而引起生产者的普遍重视。
当出现甩尾现象时,带钢尾部折叠破碎,很容易使轧辊表面出现辊印,造成成品表面辊印缺陷;严重甩尾时,尾部出现断带现象,引起工艺事故,影响轧制节奏;破碎的残片若在轧机中未被发现,下一块钢轧制时,极易导致废钢;破碎的残片或断尾带入卷取机内,轻者影响卷取机的正常工作,重则使设备受损,导致废钢。
1、甩尾的定义:轧件在精轧机组中轧制时,尾部出轧机后,不能正常运行,而出现摆甩、抖动、翻转现象,又在这种状态下进入下一架轧机轧制,造成尾部折叠,破碎、断带现象,生产上称这种现象叫甩尾。
2.甩尾产生的原因以及预防2.1操作控制方面造成的甩尾就其实质而言,甩尾现象应属板形控制范畴。
因为板形控制不当,引起板形不良,加上抛钢瞬间速度控制失当,活套抖动问题,往往会引起甩尾现象的出现,甩尾现象与板形不良常常是同时出现的。
由于操作控制方面造成带钢在宽度方向上秒流量不均(如图1 V DS>V WS)偏离轧制中心线,在机架间突然失去张力的一瞬间,跑偏加剧,造成尾部打在入口导板上折叠进入下一机架,或尾部翻转进入下一机架,而出现甩尾现象。
一般情况下都是由于轧辊没有调平造成的甩尾。
如图1所示,传动侧(DS)辊缝大,则带钢秒流量大、张图1力大,而操作侧(WS)辊缝小,带钢秒流量小、张力小,这样造成带钢宽度方向上张力分布不均匀。
在落小套及抛钢瞬间传动侧张力大,又由于张力具有纠偏的作用,传动侧的大张力使带钢向操作侧偏移(如图2,T DS大于T WS),严重时便产生甩尾。
在抛钢时将该机架传动侧辊缝根据跑偏情况上抬0.1—0.2mm,跑偏越严重,抬的越多,就能够有效防止甩尾的发生,实际生产中,也证明了这一点。
同时,对于轧制薄格规时将精轧各机架,特别是后段机架的活套落套补偿转速加大,使尾部具有较大的张力,以次来平衡传动侧和操作侧的张力差,达到防止尾部跑偏的目的。
对于来料楔形可视同辊缝楔形进行调整。
图1图 22.2侧导板余量及其对中侧导板的开口度的设定是成品宽度加上热膨胀以及富余量来控制的。
有:B=B0(1+α)+B i式中:B——侧导板设定植B0——成品宽度B i——余量(F2~3取30mm,F4~7取35mm)α——热膨胀系数(取0.01)设定侧导板的原则应是F1——F7从大到小,后面机架设定值也不应过小,应根据钢的实际宽度来确定。
一般情况下侧导板的作用就是对中,防止轧件跑偏,如果对中性不好或侧导板开口度过大,到后机架,都是造成甩尾的原因。
一般的原则是防止带钢穿钢和抛钢时跑偏为原则,使抛钢瞬间Bi值越小越好,但带钢和侧导板必须有间隙即轻微的小火花。
合理使用侧导板对中性是解决甩尾防止重要手段之一。
当侧导板出现开口度过大时,侧导板对带钢的夹持作用便没有了,带钢跑偏时的偏量增大,且各机架间具有跑偏放大的效果。
实际生产中便出现:前段轻微跑偏,到后机架就严重跑偏的现象。
侧导板不对中,带钢进入轧机时,便偏移了轧制中心线,出现带钢宽度方向上厚度不对称(如图3),再进入下一机架时,传动侧和工作侧的延伸不均匀,引起甩尾。
在实际生产中由于各种原因的影响,侧导板的实际开口度与显示开口度存在一定差异,在生产薄规格前,应当对精轧所有侧导板以及E2进行实测、标定,保证显示值与实际差控制在2mm以内;对中控制在2mm以内。
E2的齐边作用在轧制薄规格时现的很重要,首先保证了头部扇形的消除,也增加了坯料进入F1的对中,一般E2开口度采用B=B0+B i,B i=25~30。
热卷箱的箱前导板、稳定器、剪前导板夹送辊的对中性也是影响甩尾的原因之一。
图 32.3温度不均及负荷分配不当当温度不均匀、负荷分配过重时,轧制压力明显增加,变形时的不均匀变形增加,特别是到了后机架,轧制压力越大,不均匀变形的敏感性就越强,带钢在机架间的稳定性降低,带钢尾部的跑偏更加严重,直接导致甩尾。
同时,温度的不均匀还会引起AGC 动作量大,使活套角度不稳、负荷状态不稳定,从而引起甩尾的产生。
2.4轧辊磨损影响精轧机在生产中由于液压及控制等故障率太高,没有投入窜辊功能。
在生产薄规格时,轧制一个宽度规格较多时,由于速度快、轧制压力大、长度长等,容易对轧辊产生槽形磨损。
轧制50块薄材磨损量d=0.15~0.2(如图5)。
槽形严重时,轧件跑偏到磨损槽外,产生单边大浪同时将严重跑偏,造成甩尾,严重时还会导致废钢。
所以在编制轧制计划时,在宽度过度上严格按照由宽到窄、由薄到厚、由硬到软的原则,且同一宽度规格数量尽量不超过100块,严格控制轧制公里数;如果发现槽形较严重时,更换精轧F5~F7工作辊。
在换工作辊后的过渡材或过渡材较少便轧制主体材时,轧辊的热凸度的建立过程中,轧辊凸度不稳定,轧件板形不稳定,也容易引起甩尾,但当热凸度稳定不再发生变化时,这种现象基本消除。
图42.5粗轧来料的影响粗轧采用的是万能式轧机,电动压下,板形控制上存在一定难度,且粗轧出口没有测厚仪,对于粗轧末道次的断面形状、尺寸不能在线准确的反映,所以只能通过头部的形状来推测其断面。
一般来说,粗轧头部弯向传动侧,那么那传动侧的厚度大于工作侧,这种来料楔形在精轧可以视为辊缝楔形来调整,尾部时将F1操作侧抬0.2~0.4mm,F2操作侧抬0.1~0.2mm,进入下一机架时楔形得到控制。
在热卷投用时,粗轧的头部成为精轧的尾部,粗轧头部旁弯为精轧尾部跑偏产生影响,因此,要保证粗轧头部形状良好。
2.6活套的设定高度和落小套。
活套设定主要是活套落小套时太慢,轧制速度过高造成的,如图5所示,小套的0位角过高在抛钢的瞬间带钢尾部离轧制线过高,易碰撞到侧导板上的护板产生甩尾,即抛钢时带钢部(虚线)被侧导板上护板划伤而折乱,严重时极易损坏设备,所以小套的0位在后机架越小越好,但必须和带钢接触。
后机架活套的设定高度过高也容易甩尾,主要是由于速度过高和突然的失张引起的。
2.7设备引起的甩尾侧导板对中偏移,后段机轧辊轴线不平行,后段活套辊不同心上下跳动,测厚仪射有异物,AGC动作大,除鳞水,各种冷却水不均匀引起的轧件宽度方向温度分布不均匀,轧辊某一侧有油污,引起轧辊宽度方向表面粗糙度不一致,影响延伸;粗轧板形呈蛇行,无法调整时,在精轧机架间轧制不稳定,跑偏严重,此种甩尾较难调整,只有更换R1彻底解决;F1与热卷之间没有形成微张力或者之间有套量产生,就有助于轧件的跑偏,就需要把热卷1#托卷辊、夹送辊、地辊的滞后率增大。
3、操作上的控制要点。
1、注意检查轧辊冷却水、除鳞水,确认侧导板的对中情况,如果不对中要从新进行标定。
2、根据轧制稳定状态情况,合理的修正轧机负荷分配,尽量减少后机架的负荷,因为后机架负荷越重,不均匀变形的敏感性就越强,从而引起甩尾的现象出现。
3、粗轧要保证为精轧提供尺寸与板形合格的中间坯,热卷箱应投入,飞剪应切头切尾,切尾的作用主要是为了防止带钢尾部温度过低,而甩尾。
4、精轧轧制速度、活套高度、张力的设定要适当,落套补偿也要合理。
5、注意观察F1的出口板形,观看工作侧与传动侧那一边的延伸大,如果工作侧的延伸大,那么后机架F5到F7到了尾部就要抬传动侧,根据延伸的大小来抬几手(一手为5道)。
如果传动侧延伸大,则反之。
如果几个机架都在甩尾,那么就先调整前机架,当前机架不甩时,在调整后机架。
6、在带钢抛尾时,有时会出现翻转,经过操作实践证明,带钢尾部翻那边。
就台相反方向。
7、带钢尾部那边有浪抬那边,尾部被甩亮、甩碎、就抬相反方向,就可能解决,这主要是根据经验来抬几手。
8、如果在轧制当中,每一块钢在F7都要甩,而且是向一个方向甩时,可以预先抬工作侧或传动侧,这样在F7执钢时就不会甩尾。
9、长时间停轧后,在轧钢时板形不好控制,也容易引起甩尾,主要是因为轧辊随着停轧时间的延缓,温度下降,热度凸度变小,再轧钢时,轧辊热凸度又随着温度的增加热凸度增大,造成轧制不稳定状态,轧件头到尾受热凸度的影响,压下量在不断的变化,轧件中间部位的延伸系数也在不断的变化,这样影响轧件纵横向延伸不一致,到了尾部也容易产生甩尾。
10、应科学、合理的安排生产计划,应有适量的烫辊材与过渡材,应合理的安排品种、规格的衔接与过度。
总而言之,甩尾是由于不均匀变形引起的,只要减少了带钢的不均匀变形,甩尾也就能得到控制,但是在生产过程当中要做到这一点是很难的。
只能采取有效的措施让甩尾减少和得到控制。
4.结语甩尾现象的产生与操作控制,设备状况、来料质量及生产计划安排等到有直接关系。
所以影响甩尾因素多,但是如果设备状况良好,能保证工艺要求,来料质量好,生产计划安排得科学、合理的话,再采用上述操作上的措施是可以防止甩尾现象的发生的。
起码可以减少,减轻甩尾现象对生产的危害。
[参考文献]:[1]陈连生,朱红一,任吉堂.热轧薄板生产技术[M].北京:冶金工业出版社.2006.[2]曲克.轧钢工艺学[M].北京:冶金工业出版社.1991。