高炉煤气精脱硫技术介绍
高炉煤气中硫化物的去除与治理技术
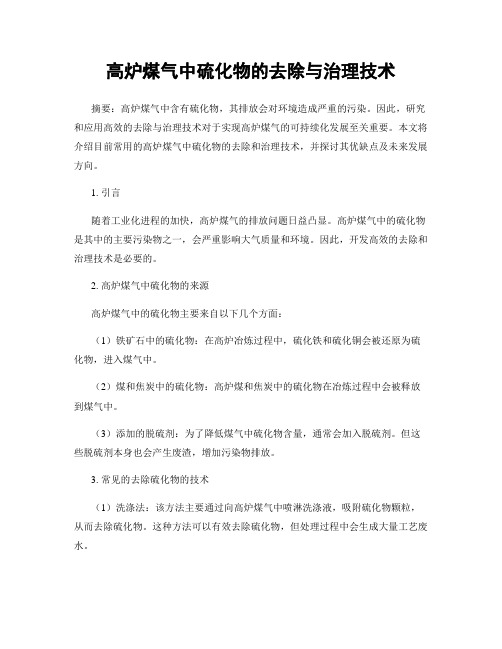
高炉煤气中硫化物的去除与治理技术摘要:高炉煤气中含有硫化物,其排放会对环境造成严重的污染。
因此,研究和应用高效的去除与治理技术对于实现高炉煤气的可持续化发展至关重要。
本文将介绍目前常用的高炉煤气中硫化物的去除和治理技术,并探讨其优缺点及未来发展方向。
1. 引言随着工业化进程的加快,高炉煤气的排放问题日益凸显。
高炉煤气中的硫化物是其中的主要污染物之一,会严重影响大气质量和环境。
因此,开发高效的去除和治理技术是必要的。
2. 高炉煤气中硫化物的来源高炉煤气中的硫化物主要来自以下几个方面:(1)铁矿石中的硫化物:在高炉冶炼过程中,硫化铁和硫化铜会被还原为硫化物,进入煤气中。
(2)煤和焦炭中的硫化物:高炉煤和焦炭中的硫化物在冶炼过程中会被释放到煤气中。
(3)添加的脱硫剂:为了降低煤气中硫化物含量,通常会加入脱硫剂。
但这些脱硫剂本身也会产生废渣,增加污染物排放。
3. 常见的去除硫化物的技术(1)洗涤法:该方法主要通过向高炉煤气中喷淋洗涤液,吸附硫化物颗粒,从而去除硫化物。
这种方法可以有效去除硫化物,但处理过程中会生成大量工艺废水。
(2)吸附法:吸附剂可以有效地吸附煤气中的硫化物,从而达到去除的目的。
常见的吸附剂有活性炭、杂多酸和碱性氧化物等。
然而,吸附剂需要定期更换和再生,增加了操作成本。
(3)脱硫剂:将脱硫剂与高炉煤气进行反应,使硫化物转化为易于处理的硫酸盐或硫酸。
这种方法可以有效去除硫化物,但处理过程中也会产生一定的废渣。
4. 治理技术的优化和发展方向(1)工艺改进:研发更高效的工艺流程,提高硫化物的去除效率,并减少工艺废水的排放。
(2)吸附剂的研发:探索新型吸附剂,提高吸附硫化物的容量和选择性,降低吸附剂的使用量和再生的成本。
(3)脱硫剂的改良:改良脱硫剂的性能,提高脱硫效率,减少废渣产量。
(4)催化剂的应用:引入催化剂,利用催化反应降解硫化物,提高去除效率并降低副产物的生成。
(5)综合治理技术:将多种技术相结合,形成综合的煤气治理系统,实现高效、低成本的硫化物去除和治理。
高炉精脱硫的原理和方法

高炉精脱硫的原理和方法【摘要】高炉精脱硫是钢铁生产中一项重要的环保措施,具有重要性和必要性。
该技术通过气相脱硫、液相脱硫和固体脱硫等方法,将含硫废气中的有害物质去除,从而减少环境污染。
气相脱硫是指通过在高炉煤气中注入氨水或其他脱硫剂来吸收硫化氢等硫化物。
液相脱硫则是利用化学反应将硫化物转化为不溶于水的硫酸盐来去除。
固体脱硫利用添加含钙、镁等金属离子的材料将硫化物转化为易溶解的硫酸盐,实现脱硫目的。
尽管高炉精脱硫技术仍有一些需要改进的地方,但其发展前景仍然十分广阔。
关键影响因素包括脱硫剂的选择和反应条件的优化等。
高炉精脱硫技术的不断发展将为钢铁行业的绿色可持续发展提供重要支持。
【关键词】高炉精脱硫、重要性、必要性、原理、方法、气相脱硫、液相脱硫、固体脱硫、技术发展前景、关键影响因素。
1. 引言1.1 高炉精脱硫的重要性高炉精脱硫是钢铁生产过程中非常重要的一环,它的主要作用是降低高炉烟气中的硫含量,减少对环境的污染。
硫在燃烧过程中会形成二氧化硫等有害气体,如果直接排放到大气中,会对人体健康和周围的生态环境造成严重影响。
高炉精脱硫可以有效地降低硫排放量,保护环境。
高炉精脱硫还对钢铁生产过程有着重要的影响。
高硫铁矿石在高炉内的使用会导致铁水中硫含量增加,容易影响钢铁的质量。
通过高炉精脱硫,可以有效地减少铁水中的硫含量,提高钢铁的质量,保证产品符合相应的标准要求。
高炉精脱硫的重要性在于减少环境污染,保护生态环境,以及提高钢铁生产的质量和效率。
研究和应用高炉精脱硫技术具有非常重要的意义。
1.2 高炉精脱硫的必要性高炉精脱硫是一项极为重要的环保工作,其必要性主要体现在以下几个方面:高炉精脱硫是为了保护环境和人类健康。
硫化物大量排放会导致酸雨的形成,对大气、水体和土壤造成严重污染,对植物生长和动物生存造成危害。
通过高炉精脱硫技术,可以有效减少硫化物排放,降低环境污染,改善空气质量,保护生态环境,减少人类健康受到的影响。
高炉煤气脱硫净化工艺选择及应用

高炉煤气脱硫净化工艺选择及应用发布时间:2022-04-24T07:40:57.692Z 来源:《福光技术》2022年6期作者:许祥俊刘宏林缪云阳[导读] 本文结合钢铁厂高炉煤气成分和特性来对各种工艺比较并进行组合,选出四种较为合适的高炉煤气净化工艺路线,通过对四种工艺在投资、运行、占地、操作条件等方面进行对比,最终优选出高炉煤气进行净化的最佳工艺路线:中温水解+碱法脱硫工艺。
并对该工艺路线在某钢铁厂的应用情况进行了简要介绍。
安徽科清环境工程有限公司南京分公司江苏南京 210000摘要:随着国家环保政策越来严厉,钢铁行业也走进了“超低排放”的大时代,轧钢加热炉、高炉热风炉、煤气发电等均需要对尾气SO2控制其排放浓度,达到超低排放限值,而对高炉煤气进行脱硫处理是保证后续达标排放的必然需求。
目前常采用在进TRT前端进行有机硫转化为无机硫,然后在TRT装置后采用适当的方式将H2S脱除的工艺技术路线。
有机硫转化及硫化氢脱除工艺目前在其他行业均有各自有较为成熟的工艺技术,本文结合钢铁厂高炉煤气成分和特性来对各种工艺比较并进行组合,选出四种较为合适的高炉煤气净化工艺路线,通过对四种工艺在投资、运行、占地、操作条件等方面进行对比,最终优选出高炉煤气进行净化的最佳工艺路线:中温水解+碱法脱硫工艺。
并对该工艺路线在某钢铁厂的应用情况进行了简要介绍。
关键词:高炉煤气、净化工艺选择、中温水解、碱法脱硫1 引言在国家促进节能减排的重点行业中,钢铁行业历来都是主战场。
生态环境部在2019年4月22日出台了《关于推进实施钢铁行业超低排放的意见》文件,对于钢铁企业的烟气排放指标提出了严格的要求,需达到超低排放的标准。
早期高炉煤气脱硫净化的主要技术路线一般包括生产源头控制和末端燃烧后控制两种[1],其中末端燃烧控制方式,即为在各个有含硫气体排放点处分别各自加装脱硫装置,脱硫装置分散,与此同时,各个用户点煤气燃烧后排放的烟气量大,烟气处理设施系统变得更大,增加投资;因此若采取生产过程的源头控制,集中对高炉煤气进行精脱硫净化,减少后续煤气用户点的燃气中的含硫量,就大大减轻末端燃烧装置的烟气排放控制的强度,或者前端脱硫效率足够搞,即可直接免于后端的燃烧脱硫装置。
高炉煤气精脱硫新技术

高炉煤气精脱硫新技术
高炉煤气是钢铁工业重要的原料之一,但其中含有大量的二氧化硫等有害气体,对环境和人体健康造成严重威胁。
传统的煤气脱硫方法采用碱洗法或氧化法,但存在反应效率低、设备占地面积大、废水处理难等问题。
近年来,随着环保意识和技术不断提升,高炉煤气精脱硫新技术也应运而生。
这种新技术采用的是催化氧化法,即在高炉煤气中添加一定的催化剂,通过氧化反应将二氧化硫转化为硫酸,从而实现脱硫。
相比传统的脱硫方法,这种技术具有反应速度快、催化剂使用量少、废水处理简便等优点。
同时,由于反应产生的硫酸可以再利用,因此也具有经济效益。
目前,这种新技术已经在一些国内外企业中得到应用,并且在实践中取得了良好的脱硫效果。
随着技术的不断提升和完善,高炉煤气精脱硫新技术必将成为钢铁工业煤气脱硫的主流方法,进一步促进工业环保和可持续发展。
- 1 -。
高炉煤气精脱硫技术规范—催化氧化法
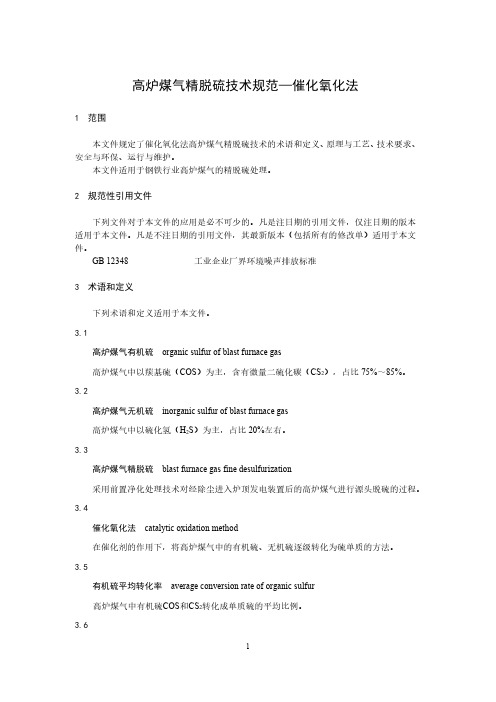
高炉煤气精脱硫技术规范—催化氧化法1范围本文件规定了催化氧化法高炉煤气精脱硫技术的术语和定义、原理与工艺、技术要求、安全与环保、运行与维护。
本文件适用于钢铁行业高炉煤气的精脱硫处理。
2规范性引用文件下列文件对于本文件的应用是必不可少的。
凡是注日期的引用文件,仅注日期的版本适用于本文件。
凡是不注日期的引用文件,其最新版本(包括所有的修改单)适用于本文件。
GB12348工业企业厂界环境噪声排放标准3术语和定义下列术语和定义适用于本文件。
3.1高炉煤气有机硫organic sulfur of blast furnace gas高炉煤气中以羰基硫(COS)为主,含有微量二硫化碳(CS2),占比75%~85%。
3.2高炉煤气无机硫inorganic sulfur of blast furnace gas高炉煤气中以硫化氢(H2S)为主,占比20%左右。
3.3高炉煤气精脱硫blast furnace gas fine desulfurization采用前置净化处理技术对经除尘进入炉顶发电装置后的高炉煤气进行源头脱硫的过程。
3.4催化氧化法catalytic oxidation method在催化剂的作用下,将高炉煤气中的有机硫、无机硫逐级转化为硫单质的方法。
3.5有机硫平均转化率average conversion rate of organic sulfur高炉煤气中有机硫COS和CS2转化成单质硫的平均比例。
3.6无机硫平均脱除率average removal rate of inorganic sulfur高炉煤气中无机硫H2S平均脱除的比例。
4原理与工艺4.1方法原理高炉煤气中的硫主要以COS、CS2、H2S形式存在,COS和CS2属于有机硫,在催化剂的作用下,首先利用高炉煤气自身水分将有机硫转化为H2S,然后采用氧化法将H2S氧化为固态单质硫进行回收脱除,达到脱硫的目的。
主要反应原理如下:COS+H2O=H2S+CO2CS2+2H2O=2H2S+CO22H2S+O2=2S+2H2O4.2工艺流程催化氧化法高炉煤气精脱硫工艺流程如图1所示。
高炉煤气精脱硫技术
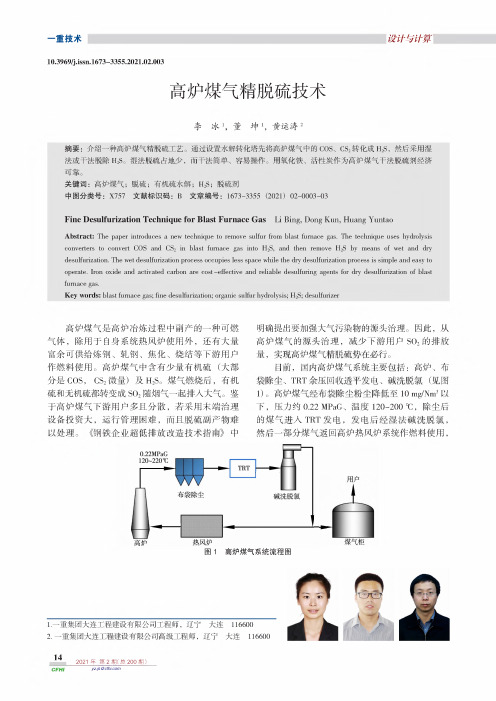
一重技术设计与计算10.3969/j.issn.l673-3355.2021.02.003高炉煤气精脱硫技术李冰董坤黄运涛121. 一重集团大连工程建设有限公司工程师,辽宁大连1166002. 一 大 程设有 高程师,大连11660014摘要:介绍一种高炉煤气精脱硫工艺。
通过设置水解转化塔先将高炉煤气中的COS 、CS 2转化成H $s ,然后采用湿除H $S u硫 少, 、 作。
用化、 作为高炉煤气 硫 济可U关键词:高炉煤气;脱硫;有机硫水解;H $S;脱硫剂中图分类号:X757 文献标识码:B 文章编号:1673-3355(2021) 02-0003-03Fine Desulfurization Technique for Blast Furnace Gas Li Bing, Dong Kun, Huang YuntaoAbstract : The paper introduces a new technique to remove sulfur from blast furnace gas. The technique uses hydrolysis converters to convert COS and CS 2 in blast furnace gas into HS, and then remove HS by means of wet and dry desulfurization. The wet desulfurization process occupies less space while the dry desulfurization process is simple and easy to operate. Iron oxide and activated carbon are cost -effective and reliable desulfuring agents for dry desulfurization of blastfurnace gas.Key words : blast furnace gas; fine desulfurization; organic sulfur hydrolysis; H 2S; desulfurizer高炉煤气是高炉冶炼过程中副产的一种可燃 气体,除用于自身系统热风炉使用外,还有大量富余可供给炼钢、轧钢、焦化、烧结等下游用户 作燃料使用。
燕山钢铁高炉精脱硫工艺流程
燕山钢铁高炉精脱硫工艺流程燕山钢铁公司是中国最大的钢铁厂之一,在钢铁生产过程中,高炉精脱硫技术起着至关重要的作用。
本文将介绍燕山钢铁公司高炉精脱硫工艺流程的详细步骤,以及每个步骤的目的和操作方法。
一、原料准备1. 原料选择:燕山钢铁公司常用的高炉原料主要包括铁矿石、焦炭和石灰石。
2. 原料质量控制:为了确保高炉精脱硫效果,原料需要经过严格的质量检验,包括化学成分、粒度和含水率等指标。
二、高炉运行参数调整1. 气流调整:通过控制高炉的风速和风量来调整气流分布,以提高脱硫效果。
2. 温度控制:调整高炉炉温,使之达到最佳的精脱硫温度范围。
三、喷煤技术应用1. 喷煤方式选择:燕山钢铁公司采用居中喷煤技术,将煤粉均匀喷向高炉炉身,以增加还原剂和吸附剂的接触面积。
2. 煤粉质量控制:煤粉需要经过精细的加工和筛分,以保证其颗粒大小和燃烧性能的稳定性。
四、脱硫剂投加1. 脱硫剂选择:燕山钢铁公司常用的脱硫剂为石灰石,其主要成分是氧化钙(CaO)。
2. 脱硫剂投加方式:将石灰石通过喷射设备均匀投入高炉炉缸内,以使之与炉渣和燃烧产物充分混合反应。
五、化学反应过程1. 吸附反应:石灰石中的氧化钙与高炉炉渣和燃烧产物中的SO2发生反应,生成硫酸钙(CaSO4)。
2. 吸附剂再生:石灰石经过一段时间的吸附反应后,会生成硫酸钙,在一定的温度下进行脱硫剂再生,以释放出SO2。
六、温度控制和熔渣处理1. 炉渣控制:调整炉渣的含碱度和碱功,以提高脱硫效果。
2. 温度控制:控制高炉内部的温度,确保脱硫反应能够在适宜的温度范围内进行。
七、脱硫效果检测与控制1. 环境监测:通过对高炉烟气中SO2浓度的检测,以评估脱硫效果,并及时调整工艺参数。
2. 数据分析:通过对脱硫效果数据的分析,优化高炉操作参数,提高脱硫效果。
燕山钢铁高炉精脱硫工艺流程包括原料准备、高炉运行参数调整、喷煤技术应用、脱硫剂投加、化学反应过程、温度控制和熔渣处理以及脱硫效果检测与控制等环节。
高炉煤气精脱硫技术介绍
3.高炉煤气精脱硫典型工艺简介
—工艺(一)
(3)湿法脱硫再生工艺对比说明: • 湿法脱硫的再生主要有三种:高塔再生、喷射氧化再生、一塔式再生三种形式。 • 高塔再生一般焦化厂应用较多,应用于焦炉煤气脱硫。优点是占地少、再生稳
定,缺点是投资较大、副盐生成量大、不利于操作管理。 • 氮肥及其它行业的水煤气、沼气等气体脱硫,几乎都是采用喷射氧化再生。 • 一塔式再生,严格说来,仍然是喷射再生的一种形式。即把喷射再生塔从地面
1.高炉煤气精脱硫背景简介
目前的技术路线主要包括源头控制和燃烧后的末端治理。 采用末端治理方式,需在多点设置脱硫设施;同时,煤气燃烧
后的废气量大,处理设施规模变大,造成投资增加。
★ 源头治理的煤气量只有燃烧后烟气量的60%左右。
相较于燃烧后脱硫工艺,燃烧前精脱硫工艺具有以下优势: 1) 降低煤气中因H2S溶于煤气冷凝水后形成氢硫酸对管道的腐蚀 作用,提高煤气输送的安全性;2)可在前端工序一次性集中 将硫脱去,便于全厂的SO2排放管控,甚至可省掉末端治理设 施;3)采用前脱硫工艺,方便后续对烟气进行脱硝,避免SO2 影响脱硝催化剂,并且可降低使用催化剂的成本。
搬到脱硫塔顶部。优点是节省再生泵的电耗(由于再生槽位置较高,所需要循 环泵的扬程也大,所以,实际节省的电量并没有一台再生泵的电量那么多), 占地面积也小。但缺点是设备施工困难且不利于操作管理。
3.高炉煤气精脱硫典型工艺简介
—工艺(一)
工艺优点:
有机硫水解率高。因为进口高炉煤气中无机硫和有机硫含量都 较高,常规的水解催化剂在大量的H2S未脱除之前,有机硫的转 化率达到90%是很困难的。有些厂家生产的水解催化剂所说的 COS的转化率95%,是在进口H2S很低的情况下才可能实现的。 而专利产品—ZTS中温有机硫水解催化剂,可以在高炉煤气中 H2S含量不大于1000 mg/Nm3情况下,仍可以达到90%以上的水 解效率。
高炉煤气精脱硫技术规范—催化氧化法
高炉煤气精脱硫技术规范—催化氧化法1范围本文件规定了催化氧化法高炉煤气精脱硫技术的术语和定义、原理与工艺、技术要求、安全与环保、运行与维护。
本文件适用于钢铁行业高炉煤气的精脱硫处理。
2规范性引用文件下列文件对于本文件的应用是必不可少的。
凡是注日期的引用文件,仅注日期的版本适用于本文件。
凡是不注日期的引用文件,其最新版本(包括所有的修改单)适用于本文件。
GB12348工业企业厂界环境噪声排放标准3术语和定义下列术语和定义适用于本文件。
3.1高炉煤气有机硫organic sulfur of blast furnace gas高炉煤气中以羰基硫(COS)为主,含有微量二硫化碳(CS2),占比75%~85%。
3.2高炉煤气无机硫inorganic sulfur of blast furnace gas高炉煤气中以硫化氢(H2S)为主,占比20%左右。
3.3高炉煤气精脱硫blast furnace gas fine desulfurization采用前置净化处理技术对经除尘进入炉顶发电装置后的高炉煤气进行源头脱硫的过程。
3.4催化氧化法catalytic oxidation method在催化剂的作用下,将高炉煤气中的有机硫、无机硫逐级转化为硫单质的方法。
3.5有机硫平均转化率average conversion rate of organic sulfur高炉煤气中有机硫COS和CS2转化成单质硫的平均比例。
3.6无机硫平均脱除率average removal rate of inorganic sulfur高炉煤气中无机硫H2S平均脱除的比例。
4原理与工艺4.1方法原理高炉煤气中的硫主要以COS、CS2、H2S形式存在,COS和CS2属于有机硫,在催化剂的作用下,首先利用高炉煤气自身水分将有机硫转化为H2S,然后采用氧化法将H2S氧化为固态单质硫进行回收脱除,达到脱硫的目的。
主要反应原理如下:COS+H2O=H2S+CO2CS2+2H2O=2H2S+CO22H2S+O2=2S+2H2O4.2工艺流程催化氧化法高炉煤气精脱硫工艺流程如图1所示。
简述高炉煤气精脱硫工艺流程
简述高炉煤气精脱硫工艺流程下载温馨提示:该文档是我店铺精心编制而成,希望大家下载以后,能够帮助大家解决实际的问题。
文档下载后可定制随意修改,请根据实际需要进行相应的调整和使用,谢谢!并且,本店铺为大家提供各种各样类型的实用资料,如教育随笔、日记赏析、句子摘抄、古诗大全、经典美文、话题作文、工作总结、词语解析、文案摘录、其他资料等等,如想了解不同资料格式和写法,敬请关注!Download tips: This document is carefully compiled by theeditor. I hope that after you download them,they can help yousolve practical problems. The document can be customized andmodified after downloading,please adjust and use it according toactual needs, thank you!In addition, our shop provides you with various types ofpractical materials,such as educational essays, diaryappreciation,sentence excerpts,ancient poems,classic articles,topic composition,work summary,word parsing,copy excerpts,other materials and so on,want to know different data formats andwriting methods,please pay attention!简述高炉煤气精脱硫工艺流程一、准备工作阶段。
在进行高炉煤气精脱硫之前,需要开展一系列的准备工作。
- 1、下载文档前请自行甄别文档内容的完整性,平台不提供额外的编辑、内容补充、找答案等附加服务。
- 2、"仅部分预览"的文档,不可在线预览部分如存在完整性等问题,可反馈申请退款(可完整预览的文档不适用该条件!)。
- 3、如文档侵犯您的权益,请联系客服反馈,我们会尽快为您处理(人工客服工作时间:9:00-18:30)。
1.高炉煤气精脱硫背景简介
现有高炉煤气净化及后续应用主要是采用袋式除尘去除颗粒物,再 经过TRT余压发电后,送往高炉热风炉、轧钢加热炉、煤气发电等用户 单元作为燃料使用,但高炉煤气中仍然含有硫、氯等有害物质。
★ ①有的企业采用煤气全干法除尘技术,每座高炉都配套喷水喷碱装置,目的是控 制高炉煤气的pH值及氯根含量,以改善对煤气管网的腐蚀。 ②从高炉煤气系统设计看, 自身热风炉用的高炉煤气或是从喷碱装置前引出,或是从公司煤气管网(经过了喷碱装 置)引出。
高炉煤气精脱硫技术介绍
2021年2月
汇报内容
1. 高炉煤气精脱硫背景简介 2. 高炉煤气精脱硫难点及工艺选择 3. 高炉煤气精脱硫典型工艺简介
1.高炉煤气精脱硫背景简介
高炉煤气是高炉炼铁 生产过程中副产的可燃 气体,其统计产量高达 700~800亿Nm3/月,大致 成分为CO2(6-12%)、 CO(28-33%)、H2(14% ) 、 N2 ( 55-60% ) 、 烃 类 ( 0.2-0.5% ) 及 少 量的硫化物。
脱硫工艺对高炉煤气的温度和压力影响较少。
2.高炉煤气精脱硫难点及工艺选择
高炉煤气精脱硫是一种新的技术发展方向。文献【高炉煤气精 脱硫技术的研究与应用,世界金属导报,2019.08.03】检索显示, 单项的有机硫水解技术及干法吸附脱除技术较多,高炉煤气脱氯也 有相关文献报道,但未见针对高炉煤气脱硫或硫分控制技术的报道, 也未见高炉煤气脱硫工程案例的相关报道。焦炉煤气精脱硫和化工 行业CO原料气脱硫技术及工程案例应用可供参考,但由于高炉煤 气的特殊性,上述技术均不能直接套用,因而高炉煤气精脱硫技术 尚属前沿探索阶段。
因此,《关于推进实施钢铁行业超低排放的意见》(环大气[2019]35号) 中首次提出:加强源头控制,高炉煤气、焦炉煤气应实施精脱硫。
汇报内容
1. 高炉煤气精脱硫背景简介 2. 高炉煤气精脱硫难点及工艺选择 3. 高炉煤气精脱硫典型工艺简介
2.高炉煤气精脱硫难点及工艺选择
高炉煤气脱硫难点:
对高炉煤气脱硫主要是脱除其中的H2S和部分羰基硫( COS )及 二硫化碳( CS2 )。 H2S为无机硫,在常温下即可与碱性物质发生 中和反应而脱除。而有机硫(COS、CS2等)相对比较稳定,用常 规方难以直接脱除,因此脱除高炉煤气的主要难点在于脱除其中 的有机硫成分。
1.高炉煤气精脱硫背景简介
2019年4月22日,生态环境部印发了《关于推进实施钢铁行业超 低排放的意见》(环大气[2Байду номын сангаас19]35号),钢铁行业正式进入“超低排 放”时代。高炉热风炉、轧钢加热炉、煤气发电等用户均要求燃烧尾 气SO2达到超低排放限值,而现有高炉煤气净化流程无法满足SO2控 制要求。
★ 钢铁企业超低排放指标:京津冀及周边地区、长三角地区、汾渭
★ ①企业中每炼一吨铁可产生2100~2200m3高炉煤气。 ②煤气中的硫,以H2S和有 机硫等为主,其中H2S含量约为20-35mg/Nm3,有机硫(主要成分有COS、CS2、硫醚硫 醇、噻吩等)含量约为200-300mg/Nm3 。 ③高炉煤气含硫量及硫分比例与焦炭的硫密切 相关,焦炭的全硫、硫形态都可能影响到高炉煤气硫含量。
某企业高炉煤气净化系统示意图 ★ 喷碱装置对高炉煤气的H2S含量有一定的去除效果,但对COS几乎没有去除。
1.高炉煤气精脱硫背景简介
由于煤气中含有H2S和有机硫,燃烧后排放的尾气中就会含有 SO2(浓度通常小于200mg/ Nm3)。在钢铁企业实行超低排放前,高 炉煤气燃烧后的烟气是满足环保排放要求的,一般是直接排放。
平原等大气污染防治重点区域率先推进,其中烧结、自备电厂二氧化硫 排放限值为35mg/m3,炼铁热风炉、轧钢热处理炉、炼焦的干法熄焦二氧 化硫排放限值为50mg/m3,炼焦焦炉烟囱二氧化硫的排放限值为30mg/m3。
河北唐山、邯郸等地区结合钢铁行业超低排放,提出了高炉煤气、焦 炉煤气H2S浓度小于20mg/m3。
硫成分复杂、浓度低,且以难以脱除的有机硫占70~80%以上。 煤气中杂质多;除含有N2、CO2 和CO等,还含有水、粉尘、氯等。
★ CO2、H2O、HCl等对催化作用有抑制,能缩短催化剂寿命;可考虑水解/ 氢解前增设预处理装置。
钢铁行业是连续性生产,要求选用脱硫工艺不能影响高炉炼铁及 后续煤气利用的主工艺运行。
2.高炉煤气精脱硫难点及工艺选择
高炉煤气精脱硫工艺的选择:
高炉煤气脱硫的关键在于煤气中有机硫的控制与削减。工业气体 中脱有机硫一般采用先水解或氢解再脱H2S的方式。
★ 水解工艺: ① 条件相对较低,通常在中温或常温下即可迸行,目前开发 的催化剂一般在不超过150℃时就有比较好的效果,可在高炉煤气自身的温度环 境下迸行反应,不需要额外加温加压。 ② 在水解反应中关键的是催化剂的选择, 有机硫水解所用催化剂主要有铝基、钛基及其混合物等。③有机硫水解反应时 需要高炉煤气中含有一定量的水蒸气(水蒸气可以单独引入,压力>0.5MPa), 温度窗口为80oC~150oC。④国内外研究有机硫催化剂的时间都比较长,水解法 将有机硫转化为无机硫的技术已经属于比较成熟的领域。 ⑤用水解工艺可对高 炉煤气中主要的COS、CS2等迸行转化。 ⑥水解反应系统均为中低压系统,因 此设备、管线等工艺装置的投资较低,容易实现工业化应用,目前在国内某钢 厂已有试验性装置投入使用。
1.高炉煤气精脱硫背景简介
目前的技术路线主要包括源头控制和燃烧后的末端治理。 采用末端治理方式,需在多点设置脱硫设施;同时,煤气燃烧
后的废气量大,处理设施规模变大,造成投资增加。
★ 源头治理的煤气量只有燃烧后烟气量的60%左右。
相较于燃烧后脱硫工艺,燃烧前精脱硫工艺具有以下优势: 1) 降低煤气中因H2S溶于煤气冷凝水后形成氢硫酸对管道的腐蚀 作用,提高煤气输送的安全性;2)可在前端工序一次性集中 将硫脱去,便于全厂的SO2排放管控,甚至可省掉末端治理设 施;3)采用前脱硫工艺,方便后续对烟气进行脱硝,避免SO2 影响脱硝催化剂,并且可降低使用催化剂的成本。