片剂裂片的原因及解决方法之令狐文艳创作
片剂裂片原因
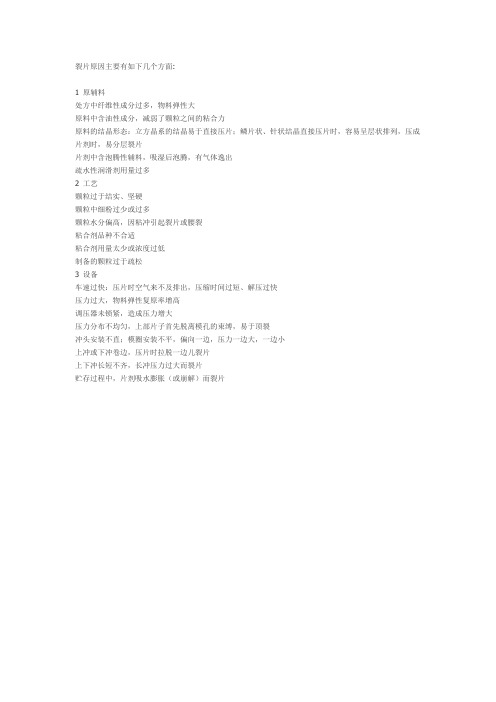
裂片原因主要有如下几个方面:
1 原辅料
处方中纤维性成分过多,物料弹性大
原料中含油性成分,减弱了颗粒之间的粘合力
原料的结晶形态:立方晶系的结晶易于直接压片;鳞片状、针状结晶直接压片时,容易呈层状排列,压成片剂时,易分层裂片
片剂中含泡腾性辅料,吸湿后泡腾,有气体逸出
疏水性润滑剂用量过多
2 工艺
颗粒过于结实、坚硬
颗粒中细粉过少或过多
颗粒水分偏高,因粘冲引起裂片或腰裂
粘合剂品种不合适
粘合剂用量太少或浓度过低
制备的颗粒过于疏松
3 设备
车速过快:压片时空气来不及排出,压缩时间过短、解压过快
压力过大,物料弹性复原率增高
调压器未锁紧,造成压力增大
压力分布不均匀,上部片子首先脱离模孔的束缚,易于顶裂
冲头安装不直;模圈安装不平,偏向一边,压力一边大,一边小
上冲或下冲卷边,压片时拉脱一边儿裂片
上下冲长短不齐,长冲压力过大而裂片
贮存过程中,片剂吸水膨胀(或崩解)而裂片。
制剂裂片的概念

制剂裂片的概念制剂裂片是指药物制剂在使用过程中,由于各种原因导致药物制剂发生裂纹、破损或破碎的情况。
制剂裂片是药物制剂的一种常见问题,可能会对患者的用药效果和安全性产生重大影响,因此需要引起人们的高度重视。
制剂裂片的产生原因可能多种多样,主要可以分为以下几类:1. 药物制剂的质量问题。
药物制剂的制造过程中可能存在不合格的原料使用、工艺参数设置不当、设备故障等问题,从而导致制剂质量问题,最终引发制剂裂片现象的发生。
2. 包装材料的质量问题。
药物制剂通常被包装在塑料瓶、铝塑复合膜袋等材料中,这些材料的质量问题也可能导致制剂裂片的发生。
比如,包装材料的耐热性不好,当药物制剂经过高温灭菌或长时间储存时,会导致包装材料变形破裂,进而影响制剂的完整性。
3. 运输、储存和使用过程中的外力作用。
药物制剂在运输、储存和使用过程中可能受到挤压、碰撞、震动等外力作用,这些外力可能会引起制剂的裂纹、破损或破碎。
比如,药物制剂被放在重物上方储存,长时间承受重压可能导致制剂裂片的发生。
4. 温度和湿度变化。
药物制剂在不同的温度和湿度条件下,可能会发生体积变化,从而引起制剂的包装材料产生应力,导致制剂的裂纹或破损。
特别是低温环境下,药物制剂中的溶剂可能会结晶并产生冷冻膨胀力,使制剂容器发生破裂。
为了避免制剂裂片的发生,可以从以下几个方面着手:1. 药物制剂的质量控制。
严格按照药典规定的工艺和质量标准进行制造,保证原料的品质和工艺参数的准确性,从而确保制剂的质量稳定性和完整性。
2. 包装材料的选择和质量把控。
选用耐热、耐压、防湿等性能良好的包装材料,避免因包装材料的问题引起制剂裂片的发生。
3. 运输、储存和使用过程中的合理处理。
在运输过程中要注意避免制剂受到外力作用,尽量选择稳固的包装方式,避免挤压、碰撞和震动。
在储存和使用过程中,要避免温度和湿度的剧烈变化,尤其是在低温环境下要采取预防措施,防止溶剂结晶引起制剂破裂。
4. 定期进行质量检查和监测。
片剂裂片的原因及解决方法

片剂裂片的原因及解决方法
裂片的原因及解决方法:
片剂受到震动或经放置后从腰间裂开称“裂片”,从顶部脱落一层称“顶裂”。
其产生原因及解决办法为:
1、压片物料细粉过多,或颗粒过粗、过细;或原料为针、片状结晶,且结晶过大,粘合剂未进入晶体内部引起裂片,可采用与松片相同的处理方法。
2、颗粒中油类成分较多或药物含纤维成分较多时易引起裂片,可分别加用吸收剂或糖粉克服。
3、颗粒过干或药物失去过多结晶水引起裂片,可喷洒适量稀乙醇湿润,或与含
水量较大的颗粒掺合后压片。
4、冲模不合要求,如模圈因磨擦而造成中间孔径大于口部直径,片剂顶出时易裂片。
冲头摩损向内卷边,上冲与模圈不吻合,压力不均匀,使片剂部分受压过大而造成顶裂,可更换冲模解决。
5、压力过大,或车速过快,颗粒中空气未逸出造成裂片,可调节压力或减慢车速克服。
裂片原因和解决方法
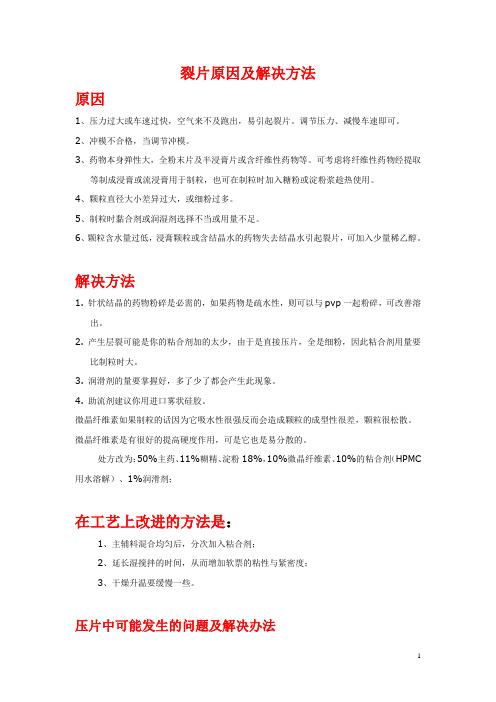
裂片原因及解决方法原因1、压力过大或车速过快,空气来不及跑出,易引起裂片。
调节压力、减慢车速即可。
2、冲模不合格,当调节冲模。
3、药物本身弹性大,全粉末片及半浸膏片或含纤维性药物等。
可考虑将纤维性药物经提取等制成浸膏或流浸膏用于制粒,也可在制粒时加入糖粉或淀粉浆趁热使用。
4、颗粒直径大小差异过大,或细粉过多。
5、制粒时黏合剂或润湿剂选择不当或用量不足。
6、颗粒含水量过低,浸膏颗粒或含结晶水的药物失去结晶水引起裂片,可加入少量稀乙醇。
解决方法1. 针状结晶的药物粉碎是必需的,如果药物是疏水性,则可以与pvp一起粉碎,可改善溶出。
2. 产生层裂可能是你的粘合剂加的太少,由于是直接压片,全是细粉,因此粘合剂用量要比制粒时大。
3. 润滑剂的量要掌握好,多了少了都会产生此现象。
4. 助流剂建议你用进口雾状硅胶。
微晶纤维素如果制粒的话因为它吸水性很强反而会造成颗粒的成型性很差,颗粒很松散。
微晶纤维素是有很好的提高硬度作用,可是它也是易分散的。
处方改为:50%主药、11%糊精、淀粉18%,10%微晶纤维素、10%的粘合剂(HPMC 用水溶解)、1%润滑剂;在工艺上改进的方法是:1、主辅料混合均匀后,分次加入粘合剂;2、延长湿搅拌的时间,从而增加软票的粘性与紧密度;3、干燥升温要缓慢一些。
压片中可能发生的问题及解决办法在压片过程中,有时会碰到裂片、松片、粘冲、崩解迟缓、片重差异等问题。
它不仅影响到片剂的外观质量,也直接影响其内在质量。
如片剂崩解迟缓,不能在药典规定的时限内完全崩解或溶解,影响药物的溶出、吸收和疗效。
而片重差异不合要求,超出药典规定的限度,也影响片剂效用的发挥。
因而,研究和探讨压片过程中可能发生的问题,对于保证药品质量,提高生产工艺水平,革新操作技术具有重要意义。
1颗粒的物理性状颗粒的物理性状与其所含药物原料的性状所含水分、所用的赋形剂有关。
而这些因素加上颗粒制成后的粒度比例分布,均可对压片工艺造成影响。
中药片剂常出现的问题

中药片剂常出现的问题一、生产素片时易出现的问题1、制粒中药材提取物若以水为润湿剂制成的软材太粘以致制粒困难。
对策:是以75%乙醇作为润湿剂,加入量1300〜1500m1∕10kg,搅拌时间一般以8〜IOmin为宜,并立即制粒。
2、裂片裂片是指素片由模空推出后发生开裂现象。
我们的经验认为,一是压力调节不当。
二是颗粒过干或过湿。
压片时压力达的部位弹性复原率高,加之颗粒大小不均(其含水量也不均),当素片出模后,受到刮粉板的轻微撞击,易裂开。
颗粒过份干燥,不易于形成固体桥,内应力低,弹性复原率高易裂片;颗粒湿度过大,即影响颗粒的流动性,也易粘冲、重片且素片毛边增加,若减少压力可致素片硬度下降,而增大压力又可导致素片的弹性内应力增加,弹性复原率增高,易裂片。
对策:一是适当减慢转速,延长压缩时间;调节适当压力,减少弹性内应力,控制硬脂酸镁的用量,降低其弹性复原率。
二是控制颗粒的含水量(以3%最为适宜)和颗粒的大小,均匀程度。
二、包糖衣时易出现的问题中草药制成素片后,大多都需要包糖衣(特别时浸膏片)。
在实际操作中常遇到如下的问题粘片多发生在包隔离层。
原因是素片表面不光华,单糖浆加入过量且温度低,水分蒸发慢,搅拌不及时,彼此粘附所致。
对策:一是糖浆应控制在40℃〜50℃,与素片的比例宜为800〜900m1∕30kg o二是糖浆的含糖量应恒定,宜为360g∕1.三是搅拌要及时,均匀,锅温保持在50℃.2、露边当颗粒含水量多,加之压力调节不当,素片多有毛边。
在加入糖浆后,素片边缘毛边部位粘附糖浆量多,经包衣锅内摩擦,糖浆渐失去,致使素片边缘显露。
对策:一是素片要充分干燥,水分控制在2%〜3%。
素片在过筛除去小颗粒时,可稍加用力,让毛边去掉。
二是适当增加包衣层数,三是适当控制锅内湿度,以免水分散发过快。
3、龟裂一是素片硬度不附合要求,上浆后,水分向素片内渗透,当素片的张力大于包衣层的表面张力时,可出现龟裂。
二是滑石粉质量差,有碳酸盐,包衣后经放置,碳酸根与酸性浸膏反应生成二氧化碳,致使片衣龟裂。
片剂生产工艺常见问题分析及解决办法

制粒工序常见问题制粒在整个片剂制备过程中起到非常关键的作用,制粒的效果直接决定着后续工序的质量,所以,制备合格的颗粒是片剂生产的核心。
表1 常见质量问题及解决办法Part 2、压片工序常见质量问题2.1裂片片剂受到震动,从片剂中间拦腰裂开或从片顶裂开。
表2 片剂裂开原因及解决办法2.2松片片剂成型后,硬度过低,手指轻轻一捏就碎裂; 片剂装袋后,稍加晃动即产生毛边或碎裂现象。
表3 松片原因及解决办法2.3黏冲片剂的表面被冲头粘去一薄层或一小部分,造成片面粗糙不平或有凹痕现象。
表4 片面粗糙或凹痕原因及解决办法2.4拉冲压片过程中由于粉末的影响,使上下冲模不能自由运转,出现卡顿现象。
表5 卡顿原因及解决办法Part3、包衣工序常见问题及解决办法用适当的药用辅料均匀地包裹片剂、颗粒剂、微丸等固体制剂表面,形成稳定衣层,使之达到预期效果,这一工艺称为包衣。
通过包衣可以提高药物的稳定性,遮盖药物的不良味道,控制药物的释放,改善美化外观。
3.1黏片由于包衣溶液的流量大于干燥能力所致,包衣液体未能及时干燥,积聚在片剂表面,最后导致相互粘连。
粘连的片芯在包衣锅的不断转动过程中被相互分开,使粘连处薄膜破裂。
表6 薄膜破裂原因及解决办法3.2表面粗糙(橘皮)由于包衣雾化效果不佳、包衣黏稠等原因,喷出的液滴受热不均或浓缩程度不均造成衣膜粗糙。
表7 衣膜粗糙原因及解决办法3.3架桥包衣后,片芯刻字部分模糊或被衣膜完全掩盖。
表8 刻字部分模糊或被完全掩盖3.4包衣膜剥落包衣后,包衣膜部分或正面剥落。
表9 包膜剥落3.5包衣片颜色不均匀包衣后,包衣膜的颜色不均匀或包衣膜未能完全掩盖片芯。
表10 衣膜问题Part4、结语我国在药品生产工艺水平上还需继续提升,精益求精,促进制药行业发展。
压片过程中的问题及解决方法
片剂制备中可能发生的问题及解决办法裂片裂片:片剂爱到震动或经放置时,有从腰间裂天的称为腰裂,从顶部裂开的称为顶裂,二者总称为裂片,原因分析及解决方法:传统的解释是颗粒中细粉多,压缩前颗粒空隙有空气,由于压缩速度较快又因为冲和模之间的间隙小,压缩过程中空气排不出去,被封闭在片子内,当压力解除后空气膨胀发生裂片。
1. 药物本身弹性较强,纤维性药物或因含油类成分较多,可加入糖粉以减少纤维弹性,加强黏合作用或增加油类药物的吸收剂,充分混匀后压片。
2. 黏合剂或润湿剂不对或用量不够,颗粒在压片时粘着力差。
3. 颗粒太干,含结晶水药物失去过多造成裂片,颗粒中含有适量的水分,可以增强颗粒的塑形并有润滑作用。
4. 有些结晶型药物,未经过充分的粉碎。
可将此类药物充分粉碎后制粒。
5. 细粉过多,润滑剂过量引起的裂片,粉末中部分空气不能及时逸出而被压在片剂内,当解除压力后,片剂内部空气膨胀造成裂片,可筛去部分细粉与造当减少润滑剂用量加以克服。
6. 压片机压力过大,反弹力大而裂片,车速过快或冲模不符合要求,冲头有长短,中部磨损,其中部大于上下部或冲头向内卷边,均可使片剂顶出时造成裂片,可适当的降低压力,压力小,弹性复原率也小。
7. 压片室室温低,湿度低,易造成裂片,特别是黏性差的药物容易产生,调节空调系统解决。
解决裂片问题的关键是换用弹性小、塑性大的辅料(可压性的淀粉),从整体上降低物料的弹性复原率。
另外,颗粒中细粉太多、颗粒过干、黏合剂黏性较弱或用量不足、片剂过厚以及加压过快也可造成裂片。
Note:一般辅料被分为脆性辅料和塑性辅料两种他们是辅料在受压时的不同表现。
脆性辅料如乳糖、磷酸氢钙等它们在压力下不容易发生形变,容易发生碎裂变成更小的粒径。
而塑性材料如部分预胶化淀粉,微晶纤维素等在压力下容易发生形变但不发生碎裂。
而塑性材料根据压力撤走后的表现又分为弹塑性和塑性。
弹塑性指压力撤走后材料又发生弹性恢复。
而塑性材料则无这种情况。
片剂制备过程中的问题分析1[1]
片剂制备过程中的问题分析一、松片1 原辅料原辅料的脆性大、可塑性差、弹性大。
如中药粉末片润滑剂用量过大,或润滑剂质重、不够细。
润滑剂用量不足,颗粒流动性不好,填充量偏低,原料中含有较多的脂肪油、挥发性粉末直接压片导致原料中的结晶水失去过多。
2 工艺1)制粒时,搅拌时间不足,软材不够湿润2)粘合剂选择不当3)粘合剂浓度偏低或用量不足4)淀粉浆粘合力不够,如未冲熟或过熟5)筛网过稀或安装过紧6)颗粒水分过高或过低7)各种原因导致的颗粒疏松3 设备上冲下降不到位或下冲上升不到位原因1)冲头与模孔间隙太大,大量细粉漏下,吸湿后造成垢冲;2)冲模清洁、润滑不够上下冲长短不齐,短冲压力不足原因:1)压力不够、调压器未锁紧、下压轮下移;2)车速过快,压缩时间过短,或颗粒来不及填满漏斗、花盘堵塞或其中颗粒架桥,颗粒流动不畅。
堵塞原因:漏斗口子太小,颗粒中有异物(布片、大块颗粒、片子、油粉团);架桥原因:颗粒偏湿、滑料太少、细粉过多等。
4 环境与贮存贮存时间过久,露置空气中,片剂吸水膨胀5 其他压轮部分磨损或断续磨损,压片时部分压力减小换品种后未调整压力二、裂片手动压片速度慢,物料有充分的弹性恢复时间,例如:物料吸附的空气可以顺利排出,物料中弹性成分的应力不会突然集中释放;机动压片时,第一,物料在压缩过程要产热,压片机模具及机体产热后,物料吸附的空气比冷机时膨胀大。
第二,产生的静电积聚,又没有及时导走,粉体因静电同性相斥。
这样可能开始机动压片不裂片,打了一会就出现裂片。
发生裂片的原因:1)传统的解释是颗粒中的细粉过多,压缩前颗粒孔隙中有空气,由于压缩速度较快,又因冲和模孔壁间的间隙很小,压缩过程中空气不能顺利排出,被封闭于片内的空隙内,当压力解除后,空气膨胀而发生裂片,但这只是裂片的其中一个因素。
手动压片时,速度较慢,相当是有一个预压的过程使空气易于排出,而电动压片速度非常快,空气不能溢出,导致裂片。
2)是颗粒的压缩行为不适合,是由于颗粒有较强的弹性,压成的药片的弹性复原率高,也可能是压力分布不均匀等引起。
片剂生产工艺常见问题分析及解决办法
制粒工序常见问题制粒在整个片剂制备过程中起到非常关键的作用,制粒的效果直接决定着后续工序的质量,所以,制备合格的颗粒是片剂生产的核心。
序号常见质量问题解决办法1颗粒粒径不符合要求:颗粒偏粗,流动性差,压出的药片片重差异大;颗粒偏细,压出的药片硬度偏小,压片机吸尘器吸走过多粉尘,收率低。
2颗粒黏性不符合要求,黏性过大或过小。
3颗粒的含水量不符合要求:水分过高。
压片过程容易粘冲;水分过少,颗粒黏性较差,压制的片子硬度偏小,易裂片、松片。
4颗粒含量均匀度不符合要求颗粒偏粗,则减少黏合剂加入的量或降低制粒的速度、时间;颗粒偏细,则适当增加黏合剂加入的量或延长制粒的时间,黏性过大,减少黏合剂加入的量或降低制粒的速度、时间;黏性过小,则适当增加黏合剂加入的量或延长制粒的时间。
水分过低,则适当降低干燥的温度、时间;水分过高,则适当降低干燥的温度、时间调整润滑剂加入的方法及用量;调整混合的转速、时间.表I常见质量问题及解决办法Part2、压片工序常见质量问题2.1裂片片剂受到震动,从片剂中间拦腰裂开或从片顶裂开。
序号可能的原因解决办法1压片机压力过大或速度过快,颗粒内的空气未及时排出。
2处方中油类成分过多,颗粒黏度差。
3环境温度、湿度过低。
4颗粒含水量过少,黏度差一5颗粒粒径差异大或细粉过多,压成的药片上下部硬度强弱不同6黏合剂或润湿剂用量不足,颗粒黏度差适当调低压力或减慢机器速度。
调整处方,替换或增加吸收剂。
适当提高空调系统温、湿度,降低干燥过程的温度或时间可适当过筛部分粗颗粒和细粉。
适当增加黏合剂或润湿剂的用量表2片剂裂开原因及解决办法2.2松片片剂成型后,硬度过低,手指轻轻一捏就碎裂;片剂装袋后,稍加晃动即产生毛边或碎裂现象。
1黏合剂或润湿剂用量不足,2颗粒含水量过少。
3压片机压力过小或运行速度过快。
4有较大团块或颗粒堵塞填粒器及下料口,影响填充量二5冲模长短不一或个别冲模过紧,片剂所受压力不同C6处方中含挥发油成分较多7颗粒流动性差,模孔内填充量不够。
片剂生产松片
片剂生产松片、裂片、粘冲与吊冲、片重差异超限的原因及解决方案在药品生产的一线,常常会遇到各种各样的小问题,而就是这些细节,往往能影响产品的质量水准。
本文从实际经验出发,对于片剂生产中出现的“病症”给与诊断分析,并给出了详实“处方”。
希望能给一线生产人员提供一定的帮助。
1:病症:松片,即片剂压成后,硬度不够,表面有麻孔,用手指轻轻加压即碎裂。
处方:①药物粉碎细度不够、纤维性或富有弹性药物或油类成分含量较多而混合不均匀。
可将药物粉碎过100目筛、选用黏性较强的黏合剂、适当增加压片机的压力、增加油类药物吸收剂充分混匀等方法加以克服。
②黏合剂或润湿剂用量不足或选择不当,使颗粒质地疏松或颗粒粗细分布不匀,粗粒与细粒分层。
可选用适当黏合剂或增加用量、改进制粒工艺、多搅拌软材、混均颗粒等方法加以克服。
③颗粒含水量太少,过分干燥的颗粒具有较大的弹性、含有结晶水的药物在颗粒干燥过程中失去较多的结晶水,使颗粒松脆,容易松裂片。
故在制粒时,按不同品种应控制颗粒的含水量。
如制成的颗粒太干时,可喷入适量稀乙醇(50%-60%),混匀后压片。
④药物本身的性质。
密度大压出的片剂虽有一定的硬度,但经不起碰撞和震摇。
如次硝酸铋片、苏打片等往往易产生松片现象;密度小,流动性差,可压性差,重新制粒。
⑤颗粒的流动性差,填入模孔的颗粒不均匀。
⑥有较大块或颗粒、碎片堵塞刮粒器及下料口,影响填充量。
⑦压片机械的因素。
压力过小,多冲压片机冲头长短不齐,车速过快或加料斗中颗粒时多时少。
可调节压力、检查冲模是否配套完整、调整车速、勤加颗粒使料斗内保持一定的存量等方法克服。
2:病症:裂片,即片剂受到震动或经放置时,从腰间裂开的称为腰裂;顶部裂开的称为顶裂,腰裂和顶裂总称为裂片。
处方:①药物本身弹性较强、纤维性药物或因含油类成分较多。
可加入糖粉以减少纤维弹性,加强黏合作用或增加油类药物的吸收剂,充分混匀后压片。
②黏合剂或润湿剂不当或用量不够,颗粒在压片时黏着力差。
- 1、下载文档前请自行甄别文档内容的完整性,平台不提供额外的编辑、内容补充、找答案等附加服务。
- 2、"仅部分预览"的文档,不可在线预览部分如存在完整性等问题,可反馈申请退款(可完整预览的文档不适用该条件!)。
- 3、如文档侵犯您的权益,请联系客服反馈,我们会尽快为您处理(人工客服工作时间:9:00-18:30)。
片剂裂片的原因及解决方法令狐文艳片剂受到震动或经放置后从腰间裂开称“裂片”,从顶部脱落一层称“顶裂”。
其产生原因及解决办法为:1、压片物料细粉过多,或颗粒过粗、过细;或原料为针、片状结晶,且结晶过大,粘合剂未进入晶体内部引起裂片,可采用与松片相同的处理方法医学教育`网搜集整理。
2、颗粒中油类成分较多或药物含纤维成分较多时易引起裂片,可分别加用吸收剂或糖粉克服。
3、颗粒过干或药物失去过多结晶水引起裂片,可喷洒适量稀乙醇湿润,或与含水量较大的颗粒掺合后压片。
4、冲模不合要求,如模圈因磨擦而造成中间孔径大于口部直径,片剂顶出时易裂片。
冲头摩损向内卷边,上冲与模圈不吻合,压力不均匀,使片剂部分受压过大而造成顶裂,可更换冲模解决。
5、压力过大,或车速过快,颗粒中空气未逸出造成裂片,可调节压力或减慢车速克服。
一:松片松片是压片时经常遇到的问题,会影响压片与包衣。
松片主要与颗粒质量、压片机运行有密切的关系。
颗粒质量是压好片子的关键,因此,制粒工艺对于片剂质量尤为重要。
影响颗粒质量的因素主要有以下几方面:1. 中药材成分的影响。
如有些中药材中含有大量的纤维成分。
由于这些药材弹性大、黏性小,致使颗粒松散、片子硬度低。
对此,在实际操作中可采用适宜的溶媒及方法,将此类药材中的有效成分提取浓缩,再进行颗粒制备,以降低颗粒弹性,提高可压性,进而提高片剂硬度;对含油脂量大的药材,压片亦易引起松片,如果这些油脂属有效成分,制粒时应加入适量吸收剂(如碳酸钙)等来吸油,如果这些油脂为无效成分,可用压榨法或其他脱脂法脱脂,减少颗粒油量,增加其内聚力,从而提高片子硬度。
2. 中药材粉碎度的影响。
如果中药材细粉不够细,制成的颗粒黏结性不强,易使片剂松散。
因此,药粉要具有一定细度,这是制好颗粒、压好药片的前提。
3. 黏合剂与湿润剂的影响。
黏合剂与湿润剂在制粒中占有重要地位,其品种的选择和用量正确与否,都直接影响颗粒质量。
选择黏合剂、湿润剂应视药粉性质而定,如是全生药粉压片,应选择黏性强的黏合剂,如是全浸膏压片,而浸膏粉中树脂黏液质成分较多,则必须选用80%以上浓度的乙醇作湿润剂。
黏合剂用量太少,则颗粒细粉过多,会产生松片。
4. 颗粒中水分的影响。
颗粒中的水分对片剂有很大影响,适量的水分能增加脆碎粒子的塑性变形,减少弹性,有利于压片,而过干的颗粒弹性大、塑性小,难以被压成片。
但如果含水量太高,也会使药片松软,甚至黏冲或堵塞料斗,从而影响压片。
故每一种中药片剂其颗粒含水量必须控制在适宜范围。
另外,如果由于压片机运行时压力不足、压片机运行转速过快、冲头长短不齐而出现松片现象,可适当调大压力或减慢转速、更换冲头。
如压力足够而仍出现松片现象,则应考虑其他原因,切勿强加压力,以免损害压片机。
二:裂片裂片是指片剂受到振动或经长时间放置而从腰间开裂或顶部脱落一层的现象。
出现裂片主要与压力调节不当、颗粒粗细的均匀程度及压片时颗粒含水量有密切关系。
压片时,压力大的部位弹性复原率高,加之颗粒的粗细、水分的影响,当素片出模后受到刮粉板轻微撞击后易开裂;颗粒过干时,因不易形成固体桥,内应力低,弹性复原率高,也易产生裂片。
若减少压片机压力,可致片子硬度下降;而增加压力,可使素片弹性内应力增加,复原率高,也易裂片。
其解决方法:一是适当减慢转速,延长压缩时间,调节适当压力,减少弹性内应力;二是严格控制颗粒含水量和颗粒大小均匀程度。
三:崩解时限崩解度不合格是影响片剂质量的主要因素之一。
《中华人民共和国药典》根据片剂作用的部位与吸收度不同,除了对含片等不作崩解检查以外,对其他片剂崩解时限均有不同要求。
崩解度不合格的主要原因是在制粒过程中黏合剂用量过大,致使颗粒过硬,片子崩解时间被延长。
此外,润滑剂对片剂的崩解亦有显著的影响。
润滑剂多为疏水性物质,可延长片剂的崩解时限,阻碍水分进入片剂内部,故用量越大、影响越大。
在生产中如遇到制成的颗粒压片后崩解时限不合格,其解决方法一是加入崩解作用较强的崩解剂(如羟甲基淀粉钠);二是在保证片剂质量的前提下,按一定比例与崩解良好的颗粒混和均匀再压片;三是先加入一定量的崩解剂,然后再与崩解良好的颗粒混合。
四:重量差异《中华人民共和国药典》对片剂的重量差异有具体的规定。
重量差异大会影响片内主药的含量。
为了保证片剂的重量差异符合要求,避免产生不合格品,在压片时往往采用严格的重量差异控制法,即在压片时每隔一定的时间抽样检查一次,检查其是否在规定限度内。
一般来说,片剂的重量差异主要是由于颗粒大小悬殊太大,压片时颗粒流速不一,以致颗粒填入模孔不均匀而造成。
如遇此情况,可筛去过多细粉或重新制粒。
在片剂生产中,除以上问题外,还可能出现黏冲、变色、麻面、迭片等问题,这需要技术人员加强对生产全过程的工作责任心,不断总结经验,根据实际情况而采取相应措施。
总结裂片原因及解决方法,看是否有用:1、压力过大或车速过快,空气来不及跑出,易引起裂片。
调节压力、减慢车速即可。
2、冲模不合格,当调节冲模。
3、药物本身弹性大,全粉末片及半浸膏片或含纤维性药物等。
可考虑将纤维性药物经提取等制成浸膏或流浸膏用于制粒,也可在制粒时加入糖粉或淀粉浆趁热使用。
4、颗粒直径大小差异过大,或细粉过多。
5、制粒时黏合剂或润湿剂选择不当或用量不足。
6、颗粒含水量过低,浸膏颗粒或含结晶水的药物失去结晶水引起裂片,可加入少量稀乙醇。
1. 针状结晶的药物粉碎是必需的,如果药物是疏水性,则可以与pvp一起粉碎,可改善溶出,我是用球磨机粉碎的,之后与其他辅料混合后压片,我做的是分散片,所以没有包衣,15分钟溶出98%。
2. 产生层裂可能是你的粘合剂加的太少,由于是直接压片,全是细粉,因此粘合剂用量要比制粒时大。
3. 润滑剂的量要掌握好,多了少了都会产生此现象4. 助流剂建议你用进口雾状硅胶。
微晶纤维素如果制粒的话因为它吸水性很强反而会造成颗粒的成型性很差,颗粒很松散。
微晶纤维素是有很好的提高硬度作用,可是它也是易分散的。
处方组成:片重 1.0克,本人现处方为:50%主药、19%糊精、20%微晶纤维素、10%的粘合剂(HPMC用水溶解)、1%润滑剂;压出来的片剂为椭圆形片,片剂的压力怎么都达不到要求,一般压力都在1-2kg左右,片剂还必须得包衣,之前我已尽本人最大努力想尽办法都无法做到,我用过直接压片糖、卡波谱、二次制粒、原料粉碎、淀粉浆制粒等方法都不行!!本人现将你的处方改为:50%主药、11%糊精、淀粉18%,10%微晶纤维素、10%的粘合剂(HPMC用水溶解)、1%润滑剂;在工艺上改进的方法是:1、主辅料混合均匀后,分次加入粘合剂;2、延长湿搅拌的时间,从而增加软票的粘性与紧密度;3、干燥升温要缓慢一些。
压片中可能发生的问题及解决办法在压片过程中,有时会碰到裂片、松片、粘冲、崩解迟缓、片重差异等问题。
它不仅影响到片剂的外观质量,也直接影响其内在质量。
如片剂崩解迟缓,不能在药典规定的时限内完全崩解或溶解,影响药物的溶出、吸收和疗效。
而片重差异不合要求,超出药典规定的限度,也影响片剂效用的发挥。
因而,研究和探讨压片过程中可能发生的问题,对于保证药品质量,提高生产工艺水平,革新操作技术具有重要意义。
本文根据药剂学的理论基础,同时荟萃多方经验。
在此基础上,结合生产实际中的亲身体会,试从生产要素诸方面,如物:颗粒的物理性状;机:压片机的机械条件;人:岗位工人的操作技能及环境空气的湿度等方面对压片中易出现的问题作一综述。
1 颗粒的物理性状颗粒的物理性状与其所含药物原料的性状所含水分、所用的赋形剂有关。
而这些因素加上颗粒制成后的粒度比例分布,均可对压片工艺造成影响。
(1)药物原料的形状对片剂的形成有一定关系。
凡属立方系的晶体一般可直接压片;而鳞片状、针状及球形晶体不易直接压片,应碎成细粉过80~100目筛后备用,否则压片中易发生裂片、松片,片剂表面不光。
特别当药物为有色物时,尤其注意粉碎过筛后制粒,以免压出的片剂表面产生斑点,致使外观不合要求。
(2)颗粒中的水分对片剂的形成及质量具有重要作用。
适量的水分能增加脆碎粒子的塑性变形,减少弹性有利于压片,硬度亦较好。
实践证明,维生素C片颗粒水分控制在1.5%~2%之间则易压片,而水分减至1%以下时,出现裂片、松片现象,即使片剂成形,通过数片板分装时,30%左右的片子出现毛角、片面松散等现象。
相反,水分超过3%时,又易产生粘冲现象。
一般解决水分过量颗粒的办法是采用去湿机,必要时重新干燥。
对完全干燥或水分不足的颗粒可根据药物本身的性质,采取自然吸湿或酌喷适宜浓度乙醇,静置或密闭吸湿5小时左右过筛后压片。
如含结晶水的药物颗粒,结晶水失去过多时出现的裂片、松片、崩解迟缓等情况则可采用此法解决。
但黄连素颗粒,由于其药物粘性大,喷洒收湿则易粘结成块状,坚硬不易均匀,会造成片重不稳及压片机受损等问题。
遇此情况,以自然吸湿或重新制粒为好。
(3)颗粒所用的赋形剂对片剂形成和质量具有密切关系。
如压片过程中,出现裂片、松片、边角毛缺等现象,这多因粘合剂选用不当或用量不足而使颗粒质松、细粉多所致,当药物为疏松性或纤维时更为明显。
对压出的片子出现崩解迟缓的情况时,除了其它因素外,粘合剂的浓度、用量是否过大都应做考虑和调整,临时解决措施为增加崩解剂的用量和减少压片机的压力。
出现裂片和松片也与颗粒中所含的油类成分的药物有关,选用吸收剂可克服之。
但吸收剂过多的加入,对药物的吸附性较大。
崩解剂选择不当,用量不足或干燥不够都直接影响片剂的崩解时限。
生产实际中,润滑剂加入量的多少,混合均匀的程度,对于纠正粘冲、解决片重差异、改善片剂外观及克服崩解迟缓都有实际参考价值。
(4)颗粒制成后,粒度与细粉的比例不当,粗粒或细粉多,都可能出现崩解迟缓、裂片、松片、片重差异或片面有斑点的现象。
根据经验,应在粘合剂的选用和制粒工艺上做调整。
2 压片机的机械条件压片机是片子成形的又一要素。
其规格型号的性能,设备运转时的机械状况及压片机某些重要部分,如冲模的磨损程度等都直接影响片剂的质量。
(1)从规格型号上看,旋转式压片机比撞击式压片机的压力大,且均匀,裂片现象容易控制。
由于加粒斗固定,机器震动较小,颗粒分层现象较少,片重准确、较稳定。
但旋转式压片机又有单轨式和双轨式多种型号。
生产中出现裂片、松片、片重差异情况时,要考虑双轨式压片机速度快,颗粒受压时间较单轨式短暂,容易产生裂片、松片现象。
此时应注意适当加大压力,减慢车速。
另外,双轨式压片机压片过程中发现片重差异时,应对双侧轨道的片重调节器、压力调节器分别进行调整。
不能单独只求轨道片重调节器和压力调节器技术参数上的一致,而应以各轨道实际调整的数据为准。
(2)符合质量要求,具备适宜流动性和可压性的颗粒压片时,也时有裂片、松片、粘片、崩解迟缓、片重差异、表面斑点等情况的出现。