片剂质量问题
(生产管理知识)制剂生产过程中常见问题和处理方法

制剂生产过程中常见问题和处理方法一、质量问题制剂生产过程由于种种原因造成制剂的质量不合格,尤其是在片剂生产中,造成片剂质量问题的因素更多。
现仅对片剂、胶囊剂及注射剂生产中可能产生质量问题的原因及解决方法作介绍。
(一)片剂生产过程中可能发生问题的分析及解决方法1.松片片剂压成后,硬度不够,表面有麻孔,用手指轻轻加压即碎裂,原因分析及解决方法:①药物粉碎细度不够、纤维性或富有弹性药物或油类成分含量较多而混合不均匀。
可将药物粉碎过100目筛、选用黏性较强的黏合剂、适当增加压片机的压力、增加油类药物吸收剂充分混匀等方法加以克服。
②黏合剂或润湿剂用量不足或选择不当,使颗粒质地疏松或颗粒粗细分布不匀,粗粒与细粒分层。
可选用适当黏合剂或增加用量、改进制粒工艺、多搅拌软材、混均颗粒等方法加以克服。
③颗粒含水量太少,过分干燥的颗粒具有较大的弹性、含有结晶水的药物在颗粒干燥过程中失去较多的结晶水,使颗粒松脆,容易松裂片。
故在制粒时,按不同品种应控制颗粒的含水量。
如制成的颗粒太干时,可喷入适量稀乙醇(50%—60%),混匀后压片。
④药物本身的性质。
密度大压出的片剂虽有一定的硬度,但经不起碰撞和震摇。
如次硝酸铋片、苏打片等往往易产生松片现象;密度小,流动性差,可压性差,重新制粒。
⑤颗粒的流动性差,填入模孔的颗粒不均匀。
⑥有较大块或颗粒、碎片堵塞刮粒器及下料口,影响填充量。
⑦压片机械的因素。
压力过小,多冲压片机冲头长短不齐,车速过快或加料斗中颗粒时多时少。
可调节压力、检查冲模是否配套完整、调整车速、勤加颗粒使料斗内保持一定的存量等方法克服。
2.裂片片剂受到震动或经放置时,有从腰间裂开的称为腰裂;从顶部裂开的称为顶裂,腰裂和顶裂总称为裂片,原因分析及解决方法:①药物本身弹性较强、纤维性药物或因含油类成分较多。
可加入糖粉以减少纤维弹性,加强黏合作用或增加油类药物的吸收剂,充分混匀后压片。
②黏合剂或润湿剂不当或用量不够,颗粒在压片时粘着力差。
片剂质量问题
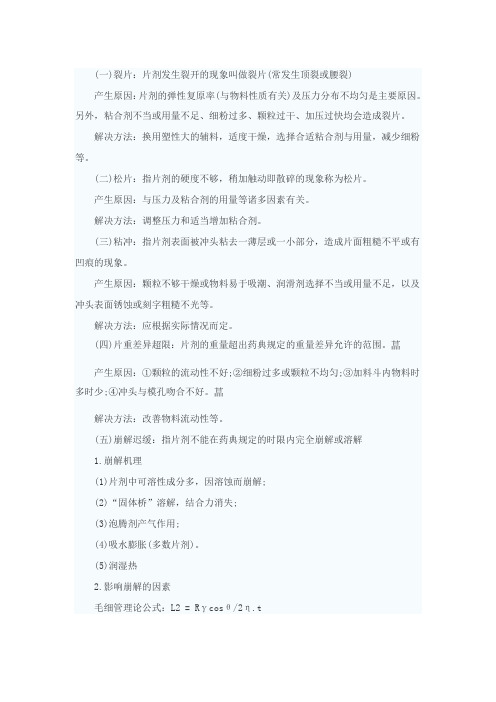
(一)裂片:片剂发生裂开的现象叫做裂片(常发生顶裂或腰裂)产生原因:片剂的弹性复原率(与物料性质有关)及压力分布不均匀是主要原因。
另外,粘合剂不当或用量不足、细粉过多、颗粒过干、加压过快均会造成裂片。
解决方法:换用塑性大的辅料,适度干燥,选择合适粘合剂与用量,减少细粉等。
(二)松片:指片剂的硬度不够,稍加触动即散碎的现象称为松片。
产生原因:与压力及粘合剂的用量等诸多因素有关。
解决方法:调整压力和适当增加粘合剂。
(三)粘冲:指片剂表面被冲头粘去一薄层或一小部分,造成片面粗糙不平或有凹痕的现象。
产生原因:颗粒不够干燥或物料易于吸潮、润滑剂选择不当或用量不足,以及冲头表面锈蚀或刻字粗糙不光等。
解决方法:应根据实际情况而定。
(四)片重差异超限:片剂的重量超出药典规定的重量差异允许的范围。
产生原因:①颗粒的流动性不好;②细粉过多或颗粒不均匀;③加料斗内物料时多时少;④冲头与模孔吻合不好。
解决方法:改善物料流动性等。
(五)崩解迟缓:指片剂不能在药典规定的时限内完全崩解或溶解1.崩解机理(1)片剂中可溶性成分多,因溶蚀而崩解;(2)“固体桥”溶解,结合力消失;(3)泡腾剂产气作用;(4)吸水膨胀(多数片剂)。
(5)润湿热2.影响崩解的因素毛细管理论公式:L2 = Rγcosθ/2η.t式中L:液体渗入毛细管的距离;R:毛细管半径;γ:液体的表面张力;θ:液体与毛细管的接触角;η:液体的黏度,t:时间。
由公式可知,影响介质渗入的主要参数有:毛细管数量(孔隙率)、毛细管半径、液体表面张力与接触角。
对四参数产生影响的主要因素是以下几方面(1)原辅料的可压性:原辅料的可压性好,片剂的崩解性能差,适量加入淀粉可增大片剂的空隙率,增加吸水性,有利于片剂的崩解;(2)颗粒的硬度:颗粒的硬度小影响片剂的孔隙率,近而影响片剂的崩解;(3)压片力:压力大,片剂的孔隙率及孔隙径小,片剂崩解速度慢;(4)表面活性剂:加入表面活性剂,改变物料的疏水性,增加润湿性,有利于片剂的崩解;(5)润滑剂:使用疏水性强的润滑剂,水分不易进入片剂,不利于片剂的崩解,硬脂酸镁;(6)粘合剂与崩解剂:粘合力越大,崩解时间越长,黏合剂粘合力大小顺序:明胶>阿拉伯胶>糖浆>淀粉浆。
片剂常见问题
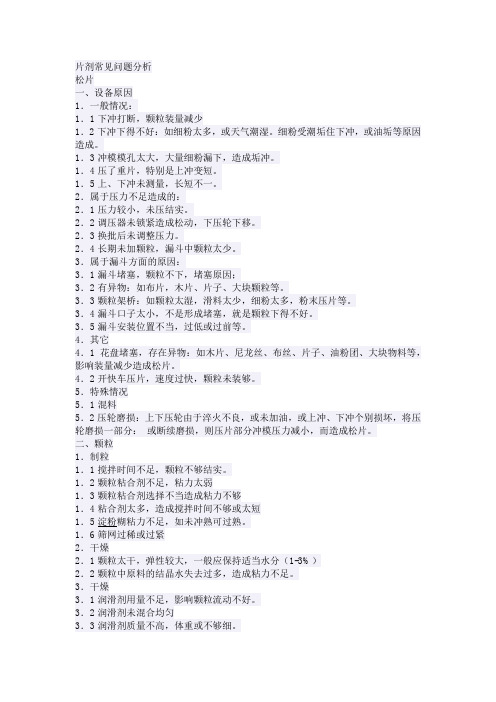
片剂常见问题分析松片一、设备原因1.一般情况:1.1下冲打断,颗粒装量减少1.2下冲下得不好:如细粉太多,或天气潮湿。
细粉受潮垢住下冲,或油垢等原因造成。
1.3冲模模孔太大,大量细粉漏下,造成垢冲。
1.4压了重片,特别是上冲变短。
1.5上、下冲未测量,长短不一。
2.属于压力不足造成的:2.1压力较小,未压结实。
2.2调压器未锁紧造成松动,下压轮下移。
2.3换批后未调整压力。
2.4长期未加颗粒,漏斗中颗粒太少。
3.属于漏斗方面的原因:3.1漏斗堵塞,颗粒不下,堵塞原因;3.2有异物:如布片,木片、片子、大块颗粒等。
3.3颗粒架桥:如颗粒太湿,滑料太少,细粉太多,粉末压片等。
3.4漏斗口子太小,不是形成堵塞,就是颗粒下得不好。
3.5漏斗安装位置不当,过低或过前等。
4.其它4.1花盘堵塞,存在异物:如木片、尼龙丝、布丝、片子、油粉团、大块物料等,影响装量减少造成松片。
4.2开快车压片,速度过快,颗粒未装够。
5.特殊情况5.1混料5.2压轮磨损:上下压轮由于淬火不良,或未加油,或上冲、下冲个别损坏,将压轮磨损一部分:或断续磨损,则压片部分冲模压力减小,而造成松片。
二、颗粒1.制粒1.1搅拌时间不足,颗粒不够结实。
1.2颗粒粘合剂不足,粘力太弱1.3颗粒粘合剂选择不当造成粘力不够1.4粘合剂太多,造成搅拌时间不够或太短1.5淀粉糊粘力不足,如未冲熟可过熟。
1.6筛网过稀或过紧2.干燥2.1颗粒太干,弹性较大,一般应保持适当水分(1-3%)2.2颗粒中原料的结晶水失去过多,造成粘力不足。
3.干燥3.1润滑剂用量不足,影响颗粒流动不好。
3.2润滑剂未混合均匀3.3润滑剂质量不高,体重或不够细。
4.原料4.1植物纤维性颗粒,存在弹性,解压后片子膨胀。
4.2颗粒细粉太多,如粉末直压颗粒。
裂片一、设备原因1.冲模1.1中模长期使用受压处凹进一圈1.2上冲或下冲卷边。
造成拉脱一边而裂片。
1.3上下冲长短不一,太长的造成压力过大而裂片1.4冲头位置不直,或模圈略偏,使压力一边大,一边小,特别是活络冲头。
影响片剂质量的主要原因及解决方法
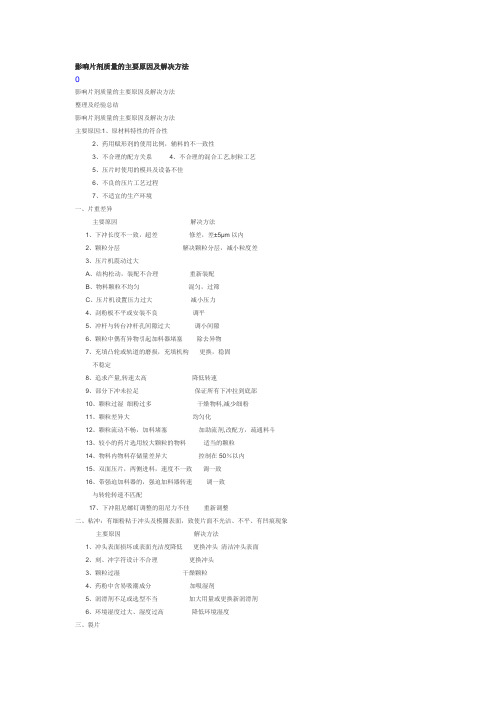
影响片剂质量的主要原因及解决方法影响片剂质量的主要原因及解决方法整理及经验总结影响片剂质量的主要原因及解决方法主要原因:1、原材料特性的符合性2、药用赋形剂的使用比例,辅料的不一致性3、不合理的配方关系4、不合理的混合工艺,制粒工艺5、压片时使用的模具及设备不佳6、不良的压片工艺过程7、不适宜的生产环境一、片重差异主要原因解决方法1、下冲长度不一致,超差修差,差±5μm以内2、颗粒分层解决颗粒分层,减小粒度差3、压片机震动过大A、结构松动,装配不合理重新装配B、物料颗粒不均匀混匀,过筛C、压片机设置压力过大减小压力4、刮粉板不平或安装不良调平5、冲杆与转台冲杆孔间隙过大调小间隙6、颗粒中偶有异物引起加料器堵塞除去异物7、充填凸轮或轨道的磨损,充填机构更换,稳固不稳定8、追求产量,转速太高降低转速9、部分下冲未拉足保证所有下冲拉到底部10、颗粒过湿细粉过多干燥物料,减少细粉11、颗粒差异大均匀化12、颗粒流动不畅,加料堵塞加助流剂,改配方,疏通料斗13、较小的药片选用较大颗粒的物料适当的颗粒14、物料内物料存储量差异大控制在50%以内15、双面压片,两侧进料,速度不一致调一致16、带强迫加料器的,强迫加料器转速调一致与转轮转速不匹配17、下冲阻尼螺钉调整的阻尼力不佳重新调整二、粘冲:有细粉粘于冲头及模圈表面,致使片面不光洁、不平、有凹痕现象主要原因解决方法1、冲头表面损坏或表面光洁度降低更换冲头清洁冲头表面2、刻、冲字符设计不合理更换冲头3、颗粒过湿干燥颗粒4、药粉中含易吸潮成分加吸湿剂5、润滑剂不足或选型不当加大用量或更换新润滑剂6、环境湿度过大、湿度过高降低环境湿度三、裂片主要原因解决方法1、压片时有空气存在于药片当中调整压力、减慢车速、增加预压时间或用有预压的工艺2、冲模磨损严重更换冲模3、黏结剂选型不当或不足更换黏结剂或加量4、颗粒含水量过低增加含水量5、颗粒过细或过粗调整颗粒粒度6、颗粒中油类成分较多加吸油剂7、模具间隙太小、不能顺利排气更换模具四、松片主要原因解决方法1、压力不够增加压力2、受压时间太少、转速快延长受压时间、增加预压、减低转速3、冲头长短不齐调整冲头4、活络冲冲头发生松动进行紧固5、下冲杆掉冲紧固6、黏结剂选型不当或太少更换黏合剂或加量7、颗粒中润滑剂比例不当调节比例8、颗粒太干燥增加颗粒水分9、物料粉碎粒度不够、纤维性或高弹性粉碎粒度过100目筛、加强黏合剂、药物或油类成分多,混合不均吸油剂10、药片压制后,置空气中过久,受潮缩短放置时间五、变色及斑点主要原因解决方法1、颗粒受油脂或其他杂质污染杜绝油脂及杂质污染2、颗粒过硬或含糖品种及有色降低颗粒硬度、有色片剂用片剂颗粒易出现乙醇为润滑剂制粒3、颗粒过大或过小颗粒适宜4、冲模型面出现锈斑清除锈斑5、加料器与转台表面摩擦有金属细粉调节加料器高度随颗粒进入模孔6、冲头与模圈内壁发生摩擦调节模圈致有色金属粉末进入颗粒六、崩解迟缓主要原因解决方法1、黏结剂粘性太强或用量过多, 更换黏结剂或降低用量颗粒过硬过粗2、崩解剂选型不当、用量不足更换崩解剂或加量疏水性润滑剂太多降低疏水性润滑剂3、压力过大、片子过硬减低压力七、刻字或线条不清晰主要原因解决方法1、冲模的字符设计、布置不合理更换字符2、冲模型面磨损或破坏更换冲模3、冲模尺寸过大或不够更换冲模4、预压力过大降低预压力粉末直接压片粉末直接压片的应用方法及其注意事项由于粉末直接压片具有较明显的优点,如工艺过程比较简单,不必制粒、干燥,产品崩解或溶出快,成品质量稳定,在国外约有40%的片剂品种已采用这种工艺生产。
中药片剂常出现的问题
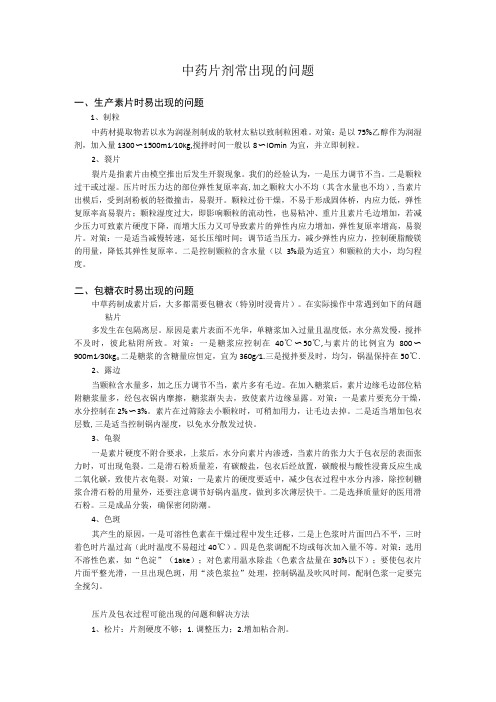
中药片剂常出现的问题一、生产素片时易出现的问题1、制粒中药材提取物若以水为润湿剂制成的软材太粘以致制粒困难。
对策:是以75%乙醇作为润湿剂,加入量1300〜1500m1∕10kg,搅拌时间一般以8〜IOmin为宜,并立即制粒。
2、裂片裂片是指素片由模空推出后发生开裂现象。
我们的经验认为,一是压力调节不当。
二是颗粒过干或过湿。
压片时压力达的部位弹性复原率高,加之颗粒大小不均(其含水量也不均),当素片出模后,受到刮粉板的轻微撞击,易裂开。
颗粒过份干燥,不易于形成固体桥,内应力低,弹性复原率高易裂片;颗粒湿度过大,即影响颗粒的流动性,也易粘冲、重片且素片毛边增加,若减少压力可致素片硬度下降,而增大压力又可导致素片的弹性内应力增加,弹性复原率增高,易裂片。
对策:一是适当减慢转速,延长压缩时间;调节适当压力,减少弹性内应力,控制硬脂酸镁的用量,降低其弹性复原率。
二是控制颗粒的含水量(以3%最为适宜)和颗粒的大小,均匀程度。
二、包糖衣时易出现的问题中草药制成素片后,大多都需要包糖衣(特别时浸膏片)。
在实际操作中常遇到如下的问题粘片多发生在包隔离层。
原因是素片表面不光华,单糖浆加入过量且温度低,水分蒸发慢,搅拌不及时,彼此粘附所致。
对策:一是糖浆应控制在40℃〜50℃,与素片的比例宜为800〜900m1∕30kg o二是糖浆的含糖量应恒定,宜为360g∕1.三是搅拌要及时,均匀,锅温保持在50℃.2、露边当颗粒含水量多,加之压力调节不当,素片多有毛边。
在加入糖浆后,素片边缘毛边部位粘附糖浆量多,经包衣锅内摩擦,糖浆渐失去,致使素片边缘显露。
对策:一是素片要充分干燥,水分控制在2%〜3%。
素片在过筛除去小颗粒时,可稍加用力,让毛边去掉。
二是适当增加包衣层数,三是适当控制锅内湿度,以免水分散发过快。
3、龟裂一是素片硬度不附合要求,上浆后,水分向素片内渗透,当素片的张力大于包衣层的表面张力时,可出现龟裂。
二是滑石粉质量差,有碳酸盐,包衣后经放置,碳酸根与酸性浸膏反应生成二氧化碳,致使片衣龟裂。
口服片剂生产过程中的质量风险管理报告
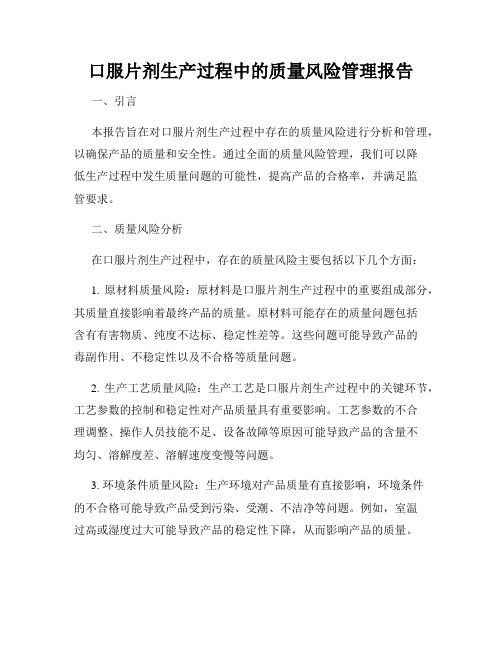
口服片剂生产过程中的质量风险管理报告一、引言本报告旨在对口服片剂生产过程中存在的质量风险进行分析和管理,以确保产品的质量和安全性。
通过全面的质量风险管理,我们可以降低生产过程中发生质量问题的可能性,提高产品的合格率,并满足监管要求。
二、质量风险分析在口服片剂生产过程中,存在的质量风险主要包括以下几个方面:1. 原材料质量风险:原材料是口服片剂生产过程中的重要组成部分,其质量直接影响着最终产品的质量。
原材料可能存在的质量问题包括含有有害物质、纯度不达标、稳定性差等。
这些问题可能导致产品的毒副作用、不稳定性以及不合格等质量问题。
2. 生产工艺质量风险:生产工艺是口服片剂生产过程中的关键环节,工艺参数的控制和稳定性对产品质量具有重要影响。
工艺参数的不合理调整、操作人员技能不足、设备故障等原因可能导致产品的含量不均匀、溶解度差、溶解速度变慢等问题。
3. 环境条件质量风险:生产环境对产品质量有直接影响,环境条件的不合格可能导致产品受到污染、受潮、不洁净等问题。
例如,室温过高或湿度过大可能导致产品的稳定性下降,从而影响产品的质量。
4. 设备设施质量风险:生产设备和设施的质量状况直接关系到产品质量的稳定性和可靠性。
设备质量问题和设施的不合理布局可能导致生产过程中发生交叉污染、操作不便等问题,进而影响产品质量。
三、质量风险管理措施为有效管理和控制口服片剂生产过程中的质量风险,我们采取以下措施:1. 严格选择和管理原材料供应商:对原材料供应商进行严格的审核和评估,确保其提供的原材料符合质量标准和相关法规要求。
与供应商建立长期的合作关系,进行定期的质量检查和风险评估,及时发现和解决存在的质量问题。
2. 建立完善的质量管理体系:建立符合国家法规和标准要求的质量管理体系,明确质量管理职责、流程和要求,从源头上控制质量风险。
并结合实际情况,进行持续改进和优化,确保质量管理体系的有效实施。
3. 加强生产工艺的监控和控制:通过建立完善的工艺控制流程和标准操作规程,明确关键工艺参数,加强对生产工艺的监控和控制。
论述片剂压片中常见的问题及原因
论述片剂压片中常见的问题及原因《片剂压片中常见问题及原因》随着科技的进步,片剂作为一种常见的制剂形式,在医药领域中占有重要地位。
然而,片剂压片过程中常会遇到一些问题,这些问题可能会影响片剂的质量和稳定性。
本文将讨论片剂压片中常见问题及其原因。
首先,常见的问题之一是片厚度和硬度不均匀。
这意味着片剂在质量和形状上存在差异,可能会导致剂量的浮动或药效不一致。
造成这一问题的原因可能是压片机的不均匀力量分布,或者药物混合时没有均匀分散。
其次,片剂可能会在压片过程中出现断裂现象。
这一问题可能与原料的物理性质、药物与辅料之间的不良相互作用或制剂工艺有关。
例如,药物本身可能具有脆弱性,容易在压片过程中发生断裂。
另外,制剂工艺中的温度、压力和湿度等因素也可以影响片剂的断裂性质。
此外,片剂中可能存在空洞、裂纹或劣化现象。
这可能是由于原料粉末颗粒粒径分布不均,或者压片时药物与辅料之间发生了化学反应。
药物颗粒的大小和形状不一致可能导致空洞或裂纹的产生,而化学反应则可能导致药物劣化,降低药效。
最后,片剂在贮存过程中可能会出现退化现象。
片剂的退化可能是由于空气、光线、湿度等外界因素与片剂中的药物相互作用所致。
药物在暴露于不适宜的环境条件下容易发生物理和化学变化,从而导致片剂质量下降或发生降解。
综上所述,片剂压片中常见的问题包括片厚度和硬度不均匀、片剂断裂、空洞和裂纹以及片剂的退化现象。
这些问题的产生原因可能是压片机的力量分布不均、原料的物理性质不一致、药物与辅料之间的相互作用或环境因素的影响。
为了解决这些问题,制药厂商需要密切关注片剂制备过程中的每个环节,并采取相应的措施来提高片剂的质量和稳定性。
制剂生产过程中常见问题及处理方法
制剂生产过程中常见问题和处理方法一、质量问题制剂生产过程由于种种原因造成制剂的质量不合格,尤其是在片剂生产中,造成片剂质量问题的因素更多。
现仅对片剂、胶囊剂及注射剂生产中可能产生质量问题的原因及解决方法作介绍。
(一)片剂生产过程中可能发生问题的分析及解决方法1.松片片剂压成后,硬度不够,表面有麻孔,用手指轻轻加压即碎裂,原因分析及解决方法:①药物粉碎细度不够、纤维性或富有弹性药物或油类成分含量较多而混合不均匀。
可将药物粉碎过100目筛、选用黏性较强的黏合剂、适当增加压片机的压力、增加油类药物吸收剂充分混匀等方法加以克服。
②黏合剂或润湿剂用量不足或选择不当,使颗粒质地疏松或颗粒粗细分布不匀,粗粒与细粒分层。
可选用适当黏合剂或增加用量、改进制粒工艺、多搅拌软材、混均颗粒等方法加以克服。
③颗粒含水量太少,过分干燥的颗粒具有较大的弹性、含有结晶水的药物在颗粒干燥过程中失去较多的结晶水,使颗粒松脆,容易松裂片。
故在制粒时,按不同品种应控制颗粒的含水量。
如制成的颗粒太干时,可喷入适量稀乙醇(50%—60%),混匀后压片。
④药物本身的性质。
密度大压出的片剂虽有一定的硬度,但经不起碰撞和震摇。
如次硝酸铋片、苏打片等往往易产生松片现象;密度小,流动性差,可压性差,重新制粒。
⑤颗粒的流动性差,填入模孔的颗粒不均匀。
⑥有较大块或颗粒、碎片堵塞刮粒器及下料口,影响填充量。
⑦压片机械的因素。
压力过小,多冲压片机冲头长短不齐,车速过快或加料斗中颗粒时多时少。
可调节压力、检查冲模是否配套完整、调整车速、勤加颗粒使料斗内保持一定的存量等方法克服。
2.裂片片剂受到震动或经放置时,有从腰间裂开的称为腰裂;从顶部裂开的称为顶裂,腰裂和顶裂总称为裂片,原因分析及解决方法:①药物本身弹性较强、纤维性药物或因含油类成分较多。
可加入糖粉以减少纤维弹性,加强黏合作用或增加油类药物的吸收剂,充分混匀后压片。
②黏合剂或润湿剂不当或用量不够,颗粒在压片时粘着力差。
制剂生产过程中常见问题和处理方法(1)
制剂生产过程中常见问题和处理方法一、质量问题制剂生产过程由于种种原因造成制剂的质量不合格,尤其是在片剂生产中,造成片剂质量问题的因素更多。
现仅对片剂、胶囊剂及注射剂生产中可能产生质量问题的原因及解决方法作介绍。
(一)片剂生产过程中可能发生问题的分析及解决方法1.松片片剂压成后,硬度不够,表面有麻孔,用手指轻轻加压即碎裂,原因分析及解决方法:①药物粉碎细度不够、纤维性或富有弹性药物或油类成分含量较多而混合不均匀。
可将药物粉碎过100目筛、选用黏性较强的黏合剂、适当增加压片机的压力、增加油类药物吸收剂充分混匀等方法加以克服。
②黏合剂或润湿剂用量不足或选择不当,使颗粒质地疏松或颗粒粗细分布不匀,粗粒与细粒分层。
可选用适当黏合剂或增加用量、改进制粒工艺、多搅拌软材、混均颗粒等方法加以克服。
③颗粒含水量太少,过分干燥的颗粒具有较大的弹性、含有结晶水的药物在颗粒干燥过程中失去较多的结晶水,使颗粒松脆,容易松裂片。
故在制粒时,按不同品种应控制颗粒的含水量。
如制成的颗粒太干时,可喷入适量稀乙醇(50%—60%),混匀后压片。
④药物本身的性质。
密度大压出的片剂虽有一定的硬度,但经不起碰撞和震摇。
如次硝酸铋片、苏打片等往往易产生松片现象;密度小,流动性差,可压性差,重新制粒。
⑤颗粒的流动性差,填入模孔的颗粒不均匀。
⑥有较大块或颗粒、碎片堵塞刮粒器及下料口,影响填充量。
⑦压片机械的因素。
压力过小,多冲压片机冲头长短不齐,车速过快或加料斗中颗粒时多时少。
可调节压力、检查冲模是否配套完整、调整车速、勤加颗粒使料斗内保持一定的存量等方法克服。
2.裂片片剂受到震动或经放置时,有从腰间裂开的称为腰裂;从顶部裂开的称为顶裂,腰裂和顶裂总称为裂片,原因分析及解决方法:①药物本身弹性较强、纤维性药物或因含油类成分较多。
可加入糖粉以减少纤维弹性,加强黏合作用或增加油类药物的吸收剂,充分混匀后压片。
②黏合剂或润湿剂不当或用量不够,颗粒在压片时粘着力差。
片剂及其生产过程中常见问题和处理方法
片剂及其生产过程中常见问题和处理方法片剂是一种常见的药物制剂形式,其以固体形式存在,适合口服给药。
然而,在片剂的生产过程中常会遇到一些问题,需要及时处理以保证片剂的质量和稳定性。
首先,常见的问题之一是片剂的压制不良。
这可能是由于颗粒的大小和形状不均匀,或者是由于药物成分没有充分混合导致的。
为了解决这个问题,可以通过优化颗粒的制备过程,确保颗粒的均匀性。
此外,在混合药物成分时,可以使用合适的混合设备,并控制好混合的时间和速度,以确保药物成分的均匀分布。
其次,片剂可能会出现分层现象,即药物成分在片剂中分布不均匀。
这可能是由于药物成分的溶解度不同,或者是由于片剂中的粘结剂不够均匀导致的。
为了解决这个问题,可以选择适当的粘结剂,并确保在制备过程中充分混合。
此外,可以考虑使用涂膜技术,将药物成分包裹在薄膜中,以避免分层现象的发生。
另外,片剂的溶解性也是一个需要注意的问题。
某些药物在水中的溶解性较差,可能会导致片剂在口腔中不能充分溶解,从而影响其吸收。
为了解决这个问题,可以选择适当的溶解助剂,并进行预溶解处理,以增加药物在水中的溶解度。
此外,片剂的稳定性也是一个需要关注的问题。
某些药物在制剂过程中可能会发生化学变化或降解,导致片剂的药效降低。
为了解决这个问题,可以选择合适的辅料,如抗氧化剂或稳定剂,来保护药物的稳定性。
此外,可以对片剂进行包衣处理,以增加其稳定性。
总之,片剂的生产过程中常见的问题包括压制不良、分层现象、溶解性较差和稳定性问题。
通过优化制剂工艺、选择合适的辅料和采取适当的措施,可以有效解决这些问题,确保片剂的质量和稳定性。
- 1、下载文档前请自行甄别文档内容的完整性,平台不提供额外的编辑、内容补充、找答案等附加服务。
- 2、"仅部分预览"的文档,不可在线预览部分如存在完整性等问题,可反馈申请退款(可完整预览的文档不适用该条件!)。
- 3、如文档侵犯您的权益,请联系客服反馈,我们会尽快为您处理(人工客服工作时间:9:00-18:30)。
(一)裂片:片剂发生裂开的现象叫做裂片(常发生顶裂或腰裂)
产生原因:片剂的弹性复原率(与物料性质有关)及压力分布不均匀是主要原因。
另外,粘合剂不当或用量不足、细粉过多、颗粒过干、加压过快均会造成裂片。
解决方法:换用塑性大的辅料,适度干燥,选择合适粘合剂与用量,减少细粉等。
(二)松片:指片剂的硬度不够,稍加触动即散碎的现象称为松片。
产生原因:与压力及粘合剂的用量等诸多因素有关。
解决方法:调整压力和适当增加粘合剂。
(三)粘冲:指片剂表面被冲头粘去一薄层或一小部分,造成片面粗糙不平或有凹痕的现象。
产生原因:颗粒不够干燥或物料易于吸潮、润滑剂选择不当或用量不足,以及冲头表面锈蚀或刻字粗糙不光等。
解决方法:应根据实际情况而定。
(四)片重差异超限:片剂的重量超出药典规定的重量差异允许的范围。
产生原因:①颗粒的流动性不好;②细粉过多或颗粒不均匀;③加料斗内物料时多时少;④冲头与模孔吻合不好。
解决方法:改善物料流动性等。
(五)崩解迟缓:指片剂不能在药典规定的时限内完全崩解或溶解
1.崩解机理
(1)片剂中可溶性成分多,因溶蚀而崩解;
(2)“固体桥”溶解,结合力消失;
(3)泡腾剂产气作用;
(4)吸水膨胀(多数片剂)。
(5)润湿热
2.影响崩解的因素
毛细管理论公式:L2 = Rγcosθ/2η.t
式中L:液体渗入毛细管的距离;R:毛细管半径;γ:液体的表面张力;θ:液体与毛细管的接触角;η:液体的黏度,t:时间。
由公式可知,影响介质渗入的主要参数有:毛细管数量(孔隙率)、毛细管半径、液体表面张力与接触角。
对四参数产生影响的主要因素是以下几方面
(1)原辅料的可压性:原辅料的可压性好,片剂的崩解性能差,适量加入淀粉可增大片剂的空隙率,增加吸水性,有利于片剂的崩解;
(2)颗粒的硬度:颗粒的硬度小影响片剂的孔隙率,近而影响片剂的崩解;
(3)压片力:压力大,片剂的孔隙率及孔隙径小,片剂崩解速度慢;
(4)表面活性剂:加入表面活性剂,改变物料的疏水性,增加润湿性,有利于片剂的崩解;
(5)润滑剂:使用疏水性强的润滑剂,水分不易进入片剂,不利于片剂的崩解,硬脂酸镁;
(6)粘合剂与崩解剂:粘合力越大,崩解时间越长,黏合剂粘合力大小顺序:明胶>阿拉伯胶>糖浆>淀粉浆。
(7)崩解剂:见崩解剂部分。
(8)贮存条件:贮存环境的温度与湿度影响片剂的崩解。
(六)溶出超限:片剂在规定的时间内未能溶出规定量的药物,即为溶出超限或称为溶出度不合格。
溶出理论:溶出服从Noyes-Whitney方程:dc/dt=kSCs
dc/dt为溶出速度;k为溶出速度常数;s为溶出质点暴露于介质的表面积;cs为药物的溶解度。
由公式说明,产生溶出超限的原因是:崩解迟缓;药物难溶。
解决方法:
(1)物微粉化:s值增大;
(2)制备研磨混合物:疏水性药物与水溶性或亲水性材料研磨混合,改变药物的润湿性;
(3)制成固体分散体:改变药物的粉散状态,s值增大,有利于药物的溶出;
(4)吸附于载体后压片:药物以分子态形式被吸附在载体表面,有利于溶出。
(七)片剂含量不均匀
所有造成片重差异过大的因素,均可造成片剂中药物含量不均匀,此外小剂量片药物含量不均匀的主要原因是:
1.混合不均匀
(1)主药与辅料量的配比悬殊:
(2)主药与辅料粒子大小相差悬殊:
(3)粒子的表面粗糙不易混匀:
(4)由于颗粒大小不等而对药液的吸收量不同。
2.可溶性成分在干燥过程中的迁移。