全泥氰化炭浆工艺讲解学习
全泥氰化炭浆工艺选金的成本核算

全泥氰化炭浆工艺选金的成本核算
全泥氰化炭浆工艺是一种常用于选金的工艺,它主要包括以下几个方面的成本核算:
1. 设备投资成本:全泥氰化炭浆工艺需要相应的设备和设施来进行金的提取和浓缩,例如氰化槽、搅拌机、过滤器等。
这些设备的购置和安装费用将是成本核算的一部分。
2. 药剂成本:全泥氰化炭浆工艺需要使用氰化剂、炭和药剂等化学品来进行金的提取和浓缩。
这些化学品的采购和使用费用将是成本核算的一部分。
3. 劳动力成本:全泥氰化炭浆工艺需要一定的人力资源来进行操作和管理。
这些人员的薪资和福利费用将是成本核算的一部分。
4. 能源消耗成本:全泥氰化炭浆工艺需要消耗一定的能源,例如电力和燃料。
这些能源的购买费用将是成本核算的一部分。
5. 维护和修理成本:全泥氰化炭浆工艺设备的维护和修理费用将是成本核算的一部分。
6. 废物处理成本:全泥氰化炭浆工艺会产生一定的废物和废水,这些废物和废水的处理费用将是成本核算的一部分。
以上是全泥氰化炭浆工艺选金的成本核算的一些主要方面。
在
实际核算中,还需要考虑具体的生产规模、工艺参数、原材料价格等因素来进行细化计算。
全泥氰化炭浆工艺

全泥氰化炭浆法提金冶炼工艺是指将金矿石全部磨碎泥化制成矿浆(一200目含量占90一95%以上)后,先进行氰化浸出,再用活性炭直接从矿浆中吸附已溶金载金、炭解吸电积金泥直接分离提纯熔炼的工艺方法.包括原料准备、搅拌氰化浸出活性炭逆流吸附、载金炭解吸电积、金泥分离提纯熔炼铸锭、活性炭活化再生和含氰污水处理等七个作业阶段.破碎阶段ﻫ一般采用两段开路破碎或两段一闭路破碎流程(图2).含金物料经过预先筛分,筛上粗物料进入一段破碎,破碎后再经二段筛分破碎后即进入磨矿作业。
作业的目的主要控制各段破碎比和保证二段破碎产品的粒度,采用二段一闭路流程更能严格保证破碎物的粒度。
一般各段破碎比为3~5,太大或太小均不利于提高破碎效率、降低成本和保护设备。
二段破碎产品粒度应小于1~1.5cm,最大不超过3cm,可以通过调节破碎机排矿口尺寸来控制。
生产中要贯彻“预先筛分,多破少磨"的原则。
磨矿阶段多采用两段两闭路磨矿流程。
第一段闭路磨矿分级流程由格子型球磨机和螺旋分级机组成。
第二段闭路磨矿分级流程由溢流型球磨机和水力旋流器组成。
将第二段闭路磨矿分级流程的预先分级和检查分级合并在一起有利于提高磨矿效率和保证产品细度。
破碎好的含金物料经过第一段闭路磨矿分级流程后,矿浆中一200目含量为55%一65%。
再经过第二段闭路磨矿分级流程后矿浆中一200目物料含量就可达90%一95%以上,符合全泥氰化工艺的细度要求.本段作业主要控制磨矿浓度、溢流浓度和溢流细度。
一般磨矿浓度:第一段为75%一80%,第二段为60%~65%;溢流浓度:第一段为25%~30%,第二段为14%一20%;溢流细度(一200目含量):第一段为55%~65%,第二段为90写一95%以上.磨矿浓度的控制主要通过调节给水量、给矿量和返砂比等,若磨矿浓度偏高,则增加给水量、减少给图3两段两闭路磨矿流程矿量,增大返砂比等,反之亦然。
溢流浓度的控制可以通过调节溢流给水量,溢流堰高低,进矿口,排矿口、溢流口大小等,而溢流细度的控制则要调节溢流堰高低、溢流口大小及钢球量、钢球配比、返砂比,磨矿浓度,溢流浓度等。
全泥氰化炭浆法提金生产中几个常见问题的探讨

2一・CaC03
在矿浆中所形成的碳酸钙、氢氧化镁、氢氧 化镁等易被炭颗粒吸附,矿浆中天然的石英颗粒、 黏土颗粒以及焙砂颗粒也极易被炭吸附,堵塞炭 微孔;矿浆中的氰根离子进入炭微孔并固定在活 性点上,使炭“中毒”,活性降低。 2)有机物的污染。矿浆中混有的油类(润滑 油、机油等)以及一些化学药剂(絮凝剂等)覆 盖在炭表面,堵塞炭微孔,使其活性降低。 3)活性炭长期使用造成自身微孔内活性点的 减少或者变形,使其活性降低。 因此,在生产中想要保证正常生产,必须及 时对活性炭进行活化再生,恢复其活性。 活性炭的再生主要需以下几个步骤: 1)酸洗。酸洗可以解决无机物对活性炭的污 染,常用2%~5%、2倍炭床体积的稀盐酸或稀硝 酸溶液浸泡活性炭,一般浸泡0.5~1h,以除去钙、 镁等化合物。CaCO,-4-H+一Ca2++H。o-4-C()2十 Mg(0H)24-H+一M92++H20 Si()2+H+一Si‘++H20 炭污染严重时,可使用90~95℃的热酸浸泡 活性炭。然后先用水冲洗,再用1%的氢氧化钠溶 液浸泡至中性。经酸洗后,活性炭的活性可以恢 复30%~50%左右。
使炭微孑L得到恢复。 3)再生的炭经过快速冷却后再经筛分出去碎 炭,然后用蒸馏水浸泡12h左右,返回流程中。
5
结语
氰化炭浆法提金工艺存在的问题如果不及时 解决,极易造成金的流失,影响企业经济效益。 在生产中要加强现场管理,保证工艺过程的稳定, 以保证企业的经济效益。
参考文献 [1] 徐小军.百荣林。等.黄金及二次资源分选与提取技术 [M].北京:化学丁业出版社。2009. [2] 张明朴.氰化炭浆法提金生产技术[M].北京:冶金出版 社。1994. [3] 李永聪,等.选矿操作技术解疑FMl.石家庄:科学技术 出版社.1998. [4] 刘学杰.等.全泥氰化提金工艺设计与实践[J].黄
姚安金矿全泥氰化—炭浆法提金实验研究
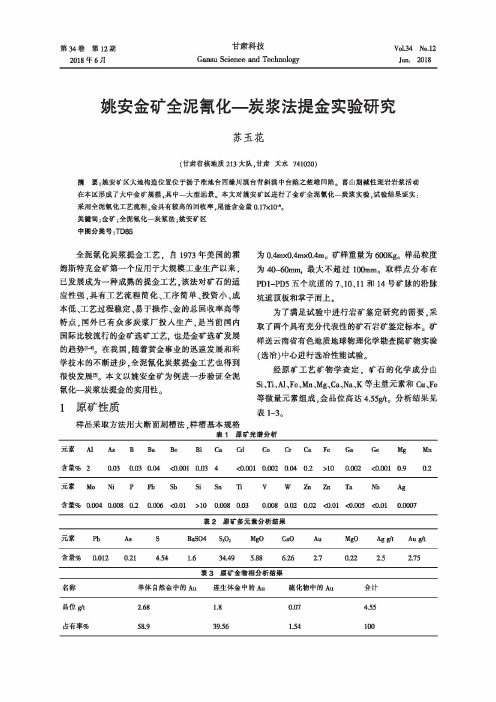
应性强,具有工艺流程筒化、工序简单、投资小、戚 本低、工艺过程稳定、易于操作、金的总回收率高等 特点,国外已有众多炭浆厂投入生产,是当前国内 国际比较流行的金矿选矿工艺,也是金矿选矿发展 的趋势[叫。在我国,随着黄金事业的迅速发展和科 学技木的不断进步,全泥氟化炭浆提金工艺也得到 很快发展阴。本文以姚安金矿为例进一步验证全泥 氯化一炭浆法提金的实用性。
第 34 卷第 12 期 2018 年 6 月
甘肃科技 Gansu Science and Technology
Vol.34 No.l2 Jun. 2018
姚安金矿全泥氨化一炭浆法提金实验研究
苏玉花
(甘肃省核地质 213 大队,甘肃夭水 741020)
摘 要 z 姚安矿区太地掏造位置位于扬子准地台西缘川滇台背斜漠中台陷之楚雄凹陷。喜山期碱性斑岩岩浆活动 在本区形成了太中金矿规模,具中一大型远景。本文对姚安矿区进行了金矿全泥佩化一炭浆实验,试验结果证实 l 采用全泥氟化工艺流程,金具有校高的回收率,尾渣含金量 0.17xlo-t'. 关键词:金矿;全泥氟化一炭浆法;姚安矿区 中圄分类号 :TD85
IIS
8.l 0.7
16 9:1
拍
电品
9'
8.2 0.6
8s
8.z也.6
便越衔幡}
91届 '童画画
93.90 9:1.60
2.4钝
9'
毒品
销
93$1电
‘ 8.2 Q.6 9 .07
试磁飨巢表明,在圈'矿领.-O.0074mm.含量占 优协-9!i弛,石灰用意4(附蝴惆4 值:::1 1啡,液团比 3:1 ,
全呢氧化炭浆提金工艺,自 1973 年美国的霍 为 O.4mxO.4mx0.4m。矿样重量为 6∞Kg。样品粒度
全泥氰化工艺
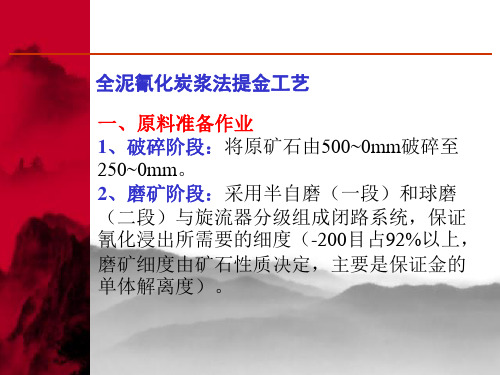
二、搅拌氰化浸出阶段 矿浆在搅拌槽中进行预浸(3槽,氰化钠溶 液提前加入磨矿机中也属预浸)。关键是控 制CN-浓度(万分之5~5.5)和氧含量(充气 量0.02m3/m3· min和充气压力100kPa,调节各 气阀门),矿浆表面均匀弥散5~15mm直径气 泡为宜。
三、活性炭逆流吸附阶段 边浸边吸作业,即活性炭的加炭、串炭和 提炭操作经提炭器的运移方向与矿浆流向相 反。 1、矿浆氰根浓度:万分之3~5,且沿矿浆流 向降低,由各槽氰化钠用量控制。 2炭逆流吸附阶段 5、串炭量:为保持吸附系统金总量平衡和各 槽内槽间炭吸附性能,串炭量一般占槽内总 量的10~20%,通过调节串炭时间来控制。 6、炭载金量:为综合回银,控制炭载金量在 900~1000g/t,通过调节提炭量来控制。
三、活性炭逆流吸附阶段 7、尾液含金量:控制尾液含金量在0.07g/m3 以下,过高则说明活性炭吸附率降低了,可 通过增加底炭密度、降低载金炭含量和缩短 串炭时间等来控制。 8、尾矿品位:要求一厂小于0.24g/t、二厂小 于0.22g/t,原则上可通过提高磨矿细度、降低 矿浆浓度、减少处理量和延长浸出时间等来 控制。
四、尾矿尾水处理 尾矿→压滤→ 尾矿库(堆存) →尾水(压滤水、澄清水)→ 生 产高位水池(回用)
全泥氰化炭浆法提金工艺 一、原料准备作业 1、破碎阶段:将原矿石由500~0mm破碎至 250~0mm。 2、磨矿阶段:采用半自磨(一段)和球磨 (二段)与旋流器分级组成闭路系统,保证 氰化浸出所需要的细度(-200目占92%以上, 磨矿细度由矿石性质决定,主要是保证金的 单体解离度)。
一、原料准备作业 3、除屑作业:遵循由粗到细除屑的原则进行 多级除屑流程,破碎前人工捡出木屑杂物, 磨机出料口设圆筒筛,渣浆泵池前设细筛网 (一般20目),旋流器溢流设圆筒筛(24~28 目)。 4、调浆阶段:在浓密机中进行,满足氰化的 条件:控制浓度35%~38%、pH值10~11(浓 度由浓密机底流量和添加絮凝剂用量控制, pH值由原矿中石灰用量和浓密机中氢氧化钠 用量控制)。
氰化法提金工艺讲解

• 国外先进技术和设备的引进消化(如美国的高效 浓密机,双螺旋搅拌浸出槽,日本的马尔斯泵,
带式过滤机等),使我国黄金生产在装备水平和
技术水平上又有了进一步的提高,同时也促进了
我国黄金生产设备向高效、节能、大型化、自动
化方向发展。在硫脲提金、硫代硫酸盐提金,预
氧化细菌浸出,加压催化浸出,树脂吸附等新工 艺的科学研究方面,近年来也有新的进展。1979 年长春黄金研究所进行硫脲提金试验获得成功, 并于1984年在广西龙水矿建成一座日处理浮选金 精矿10~20t的硫脲提金车间(1987年通过部级 鉴定)。其他工艺虽处于试验研究阶段和正准备
不断降低,并使浸出率逐渐趋近于某一极限值。
杂质离子的影响
• 金通常是以自然金、银金矿、碲金矿等存在,共生金属矿物有黄铁矿、砷黄 铁矿、方铅矿、闪锌矿、黄铜矿、毒砂、辉铋矿等。脉石矿物有石英、长石 等、在氰化物溶液中,多数的伴生矿物都不同程度地溶解,给金的浸出带来 影响。其中金属矿物的影响比较严重,有的会加速金的溶解,而有的会阻滞 金的溶解 增速效应:适量的铅、汞、铋和铊的存在,对金的溶解是有利的。
• 矿浆浓度的高低,表明单位数量矿浆中固体矿物的多少。当矿浆浓度提高时,液体与 固体的比值就会降低,这时氰化液中金的品位和其他杂质的浓度就会提高,从而降低 了氰化物溶液的溶金活性。采用低浓度浸出时,虽然对金的浸出有利,但由于矿浆体 积的增加,在浸出时间与药剂浓度相同的条件下,增加了浸出设备的数量和药耗。同 时,液体量的增加,还会给后继的作业增加负荷。
• 例如,铅离子(Pb+2),当加入适量的铅盐时,对金的溶解有增速效应。这 是由于铅与金构成原电池,金在原电池中为阳极,而促进金转入溶液。
• 阻滞效应:在氰化物溶液中,由于某些杂质的存在,对金的溶解会带来不良 的影响。
第七章氰化实践汇编资料.
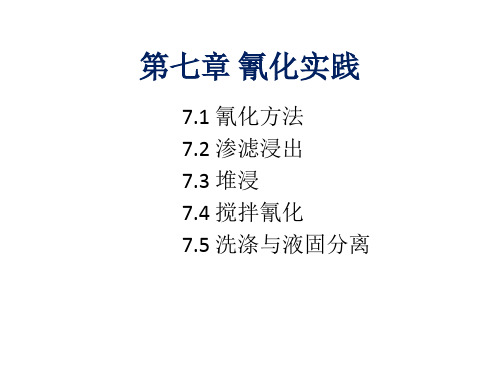
故障少,操作简便;
缺点:要增置空气压缩机,为防止
突然停电要有备用电源;
4
适用:细颗粒、高浓度矿浆的全
1
泥氰化浸出;
规格:Ф(3~11)×(11~23)m
1-中心循环管; 2-进料管; 3-主压缩空气管; 4-辅助压缩空气管; 5-矿浆排料管; 6-挡板;
图7-6 空气搅拌浸出槽
Ф3 mm
H 11 m
选,渗滤氰化法仅用来处理贫矿或不值得建 厂的小矿,且发展为堆浸法。
7.2 渗滤浸出
渗滤浸出:将含矿物原料置于渗滤槽中进行浸出的过程。 适用:从矿砂、疏松多孔的含金矿物原料、焙砂及烧渣中提金。
矿石粒度范围:-10 ~ + 0.074 mm 的含金物料。
氰化试剂的消耗较少;
特点: 动力消耗低;
省去了固液分离,直接得到澄清的浸出液。
适用:低品位金银矿、早期采矿废石等。 特点:工艺简单、易操作、设备投资少、生产成本低、
对矿石的性质、品位、数量的适应性强、经济效益高。
堆浸法分为:
((21)) 常制规粒堆堆浸浸
金的浸出率: 一般 50 %~80 % 。
7
(1) 常规堆浸
(1) 建 造 堆 浸 场 :平场(3% ~ 5%坡度) — 夯实 — 防渗 — 集液沟 — 防洪沟
4
2 渗滤浸出操作
(1)
装料
干 湿法 法装 装料 料
操作:(2)
氰化液(加苛性碱,
先浓后稀)供排
下 上进 进上 下出 出
(3)
卸出浸出渣 干 湿法 法卸 卸渣 渣
5
3 提高渗滤浸出率的方法
渗滤浸出时,提高金的浸出率的方法有: 矿石磨碎后,要很好分级,按级渗滤; 干法装料,应尽量把矿砂中的水分降低,以利充气; 氰化之前,先用水、酸或碱洗涤矿砂,除去有害杂质; 氰化溶液在浸出之前,应预先充气,以提高含氧量; 将压缩空气鼓入矿砂层。
全泥氰化流程

全泥氰化炭浆法提金工艺流程及特点全泥氰化炭浆法提金工艺是氰化提金的方法之一。
是含金物料氰化浸出完成之后,一价金氰化物〔KAu(CN)2〕进行炭吸附的工艺过程。
人们早已发现活性炭可以从溶液中吸附贵金属的特性,开始只从清液中吸附金,将载金炭熔炼以回收金。
由于氰化矿浆须经固液分离得到清液和活性炭不能返回使用,此法在工业上无法与广泛使用的锌置换法竞争。
后来用活性炭直接从低化矿浆中吸附金,这样就省去了固液分离作业;载金活性炭用氢氧化钠和氰化钠混合液解吸金银,活性炭经过活化处理可以返回使用。
因此近年来炭浆法提金发展成为提金新工艺,我国在河南省灵湖金矿和吉林省赤卫沟金矿等建成了应用炭浆法提金工艺的生产工厂。
炭浆法提金工艺过程包括原料制备及活性炭再生等主要作业组成,其工艺流程见图8-2(1)原料制备把含金物料碎磨至适于氰化粒度,一般要求小于28目并除去木屑等杂质,经浓缩脱水使浸出矿浆浓度达到45~50%为宜;(2)搅拌浸出与常规氰化法相同,一般为5~8个搅拌槽。
(3)炭吸附氰化矿浆进入搅拌吸附槽(炭浆槽),河南省灵湖金矿在吸浆僧中装有格式筛和矿浆提升器,用它实现活性炭和矿浆逆向流动,吸附矿浆中已溶的金,桥式筛可以减少活性炭的磨损。
目前桥式筛的筛孔易被活性炭堵塞,要用压缩空气清扫。
(4)载金炭解吸目前可用四种方法解吸:(1)热苛性氰化钠溶液解吸;(2)除浓度苛性氰化钠溶液加酒精解吸;(3)在加温加压条件下用苛性氰化钠溶液解吸;(4)高浓度苛性氰化钠溶液解吸。
(5)电积法或常规锌粉置换沉淀金载金炭解吸可得到含金达600克/米3的高品位贵液,经电积卖锌置换法得到金粉,并送熔炼得到金锭。
(6)活性炭的再生利用解吸后的活性炭先用稀硫酸(硝酸)酸洗,以除去碳酸盐等聚积物,经几次返回使用后需进行热力活化以恢复炭的吸附活性。
炭浆法提金主要适用于矿泥含量高的含金氧化矿石,由矿石含泥高,固液分离困难,现有的过滤机不能使贵液和矿渣有效分离,因此常规的氰化法不能得到较好的技术经济指标。
- 1、下载文档前请自行甄别文档内容的完整性,平台不提供额外的编辑、内容补充、找答案等附加服务。
- 2、"仅部分预览"的文档,不可在线预览部分如存在完整性等问题,可反馈申请退款(可完整预览的文档不适用该条件!)。
- 3、如文档侵犯您的权益,请联系客服反馈,我们会尽快为您处理(人工客服工作时间:9:00-18:30)。
全泥氰化炭浆工艺全泥氰化炭浆工艺 - 概述全泥氰化炭浆法提金冶炼工艺是指将金矿石全部磨碎泥化制成矿浆(一200目含量占90一95%以上)后,先进行氰化浸出,再用活性炭直接从矿浆中吸附已溶金载金、炭解吸电积金泥直接分离提纯熔炼的工艺方法。
包括原料准备、搅拌氰化浸出活性炭逆流吸附、载金炭解吸电积、金泥分离提纯熔炼铸锭、活性炭活化再生和含氰污水处理等七个作业阶段。
破碎阶段一般采用两段开路破碎或两段一闭路破碎流程(图2)。
含金物料经过预先筛分,筛上粗物料进入一段破碎,破碎后再经二段筛分破碎后即进入磨矿作业。
作业的目的主要控制各段破碎比和保证二段破碎产品的粒度,采用二段一闭路流程更能严格保证破碎物的粒度。
一般各段破碎比为3~5,太大或太小均不利于提高破碎效率、降低成本和保护设备。
二段破碎产品粒度应小于1~1.5cm,最大不超过3cm,可以通过调节破碎机排矿口尺寸来控制。
生产中要贯彻“预先筛分,多破少磨”的原则。
磨矿阶段多采用两段两闭路磨矿流程。
第一段闭路磨矿分级流程由格子型球磨机和螺旋分级机组成。
第二段闭路磨矿分级流程由溢流型球磨机和水力旋流器组成。
将第二段闭路磨矿分级流程的预先分级和检查分级合并在一起有利于提高磨矿效率和保证产品细度。
破碎好的含金物料经过第一段闭路磨矿分级流程后,矿浆中一200目含量为55%一65%。
再经过第二段闭路磨矿分级流程后矿浆中一200目物料含量就可达90%一95%以上,符合全泥氰化工艺的细度要求。
本段作业主要控制磨矿浓度、溢流浓度和溢流细度。
一般磨矿浓度:第一段为75%一80%,第二段为60%~65%;溢流浓度:第一段为25%~30%,第二段为14%一20%;溢流细度(一200目含量):第一段为55%~65%,第二段为90写一95%以上。
磨矿浓度的控制主要通过调节给水量、给矿量和返砂比等,若磨矿浓度偏高,则增加给水量、减少给图3两段两闭路磨矿流程矿量,增大返砂比等,反之亦然。
溢流浓度的控制可以通过调节溢流给水量,溢流堰高低,进矿口,排矿口、溢流口大小等,而溢流细度的控制则要调节溢流堰高低、溢流口大小及钢球量、钢球配比、返砂比,磨矿浓度,溢流浓度等。
总之,在磨矿作业中各项技术参数都是互相联系,相辅相成、相互制约的,因此在调节控制的过程中要综合考虑,协调作用。
除屑作业多级除屑流程。
第一级除屑作业设在碎矿前,要人工捡出原矿中木屑等杂物。
第二级除屑作业设在螺旋分级机的溢流处,采用孔径为2~3mm的平面筛板。
第三级除屑作业设在水力旋流器给矿前,采用20目的平面筛网。
第四级除屑作业设在浓缩脱水前,采用24~28目的弧形筛。
本段作业须及时清除筛上杂物,并经常检查筛网使用情况,发现损坏及时更换,以保证矿浆的除屑质量。
矿浆在氰化浸出前需要严格除屑是因为原矿带进的木屑,砂砾、导火线、编织袋的碎片、渣子等杂物,容易造成水力旋流器的进浆口及沉砂口,浓缩机的排矿口、管道、级间筛等部位的堵塞;砂砾的存在会增大活性炭的磨损;木屑等的存在会吸附已溶金而造成金的流失,木屑还可能在再生窑中转变为易碎炭而降低金的实收率。
因此,除屑作业非常重要,要按由粗到细的顺序尽可能地多设除屑筛网层级。
制浆阶段主要在浓缩机中进行,多采用高效浓密机、单层浓缩机或多层浓缩机。
符合全泥氰化炭浆法提金工艺条件的矿浆,其矿浆浓度为40%一45%,矿浆PH值为10一11,而由磨矿作业输送来的矿浆浓度为14%一20%,PH值为7~10。
本段作业需通过调节浓缩机底流量和絮凝剂用量来控制矿浆浓度,通过调节加入球磨机中的石灰量或加入浓缩机中的氢氧化钠量来控制矿浆的PH值,使之符合下一步浸出吸附作业要求。
搅拌氰化浸出又称预浸作业,一般由两个高效节能浸出槽(l号槽和2号槽)串联组成。
矿浆由上段作业输送到1号槽,再由1号槽自流进入2号槽。
本段作业主要是控制浸出矿浆中氰根离子浓度和氧含量。
适宜的氰根离子浓度为0.05%一0.08%,通过调节氰化钠的给药量来控制。
矿浆中氧含量通常用充气量和充气压力来表示,一般充气量为0.02m3/m3·min,充气压力为100KPa。
生产中通常以矿浆表面均匀弥散5~15mm直径的小气泡为宜,通过调节气泵总阀门和各槽的充气阀门加以控制。
矿浆氰根浓度比搅拌氰化浸出阶段略低,为0.02%一0.05%,而且由3号槽向以后各槽逐渐降低,7号槽最低为0.02%一0.03%。
通过调整氰化钠的添加量来控制。
矿浆氧含量比搅拌浸出阶段略低,通过调节各槽充气阀门控制。
底炭密度底炭密度即为每升矿浆中活性炭的含量,一般为10~15g/L。
为了保证金的回收率,通常7号槽的底炭密度略高,为15一20g/L。
底炭密度可以通过调节加炭量、串炭量、提炭量来控制。
串炭速度串炭速度又称串炭频率,是指单位时间内的串炭次数。
根据对吸附系统中金的质量平衡研究,串炭速度与炭载金量的乘积是一个常数。
为保持适宜的炭载金量,就要选择一定的串炭速度,一般为一天串炭一次。
串炭量为保持吸附系统金总量平衡,保持槽内或槽之内炭的吸附性能,串炭量应与槽中储存的活性炭量之间有一个适宜的百分比,这个比值一般为10一20%。
调节串炭时间的长短可以控制串炭量的大小。
炭载金量在确保吸附率的前提下,炭载金量尽可能高,但炭载金量越高,金在吸附系统中的储存量就越多,资金周转就会受到影响,因此适宜的炭载金量、合理的串炭制度,对炭浆厂来说是非常重要的。
一般最终载金炭金含量为4~69/kg,可以通过调节提炭量来控制。
尾液金含量尾矿浆溶液中金含量一般为0.02~0.1g/m3,超过这一数值时则说明活性炭吸附有问题,吸附率降低了,可以通过增加底炭密度、降低载金炭含量、缩短串炭时间等方法来控制。
尾矿品位一般为0.2~0.3g/t,最高不超过0.5g/t。
此技术指标的调节控制较为复杂,在现有的设备工艺上可以通过提高磨矿细度、降低矿浆浓度、减少处理量、延长浸出时间等方法综合调节控制。
总之,上述各项技术指标都不是孤立的,而是互相联系的、统一的有机整体,任何一种调节方法所起的作用也不是单方面的,所以在生产操作中要根据具体情况,综合考虑,找出最佳的调控措施,以提高金的总回收率,达到最好的经济效益。
载金炭的解吸电积作业多采用加温加压解吸、高温常压电积联合闭路循环工艺流程,有较成熟的自动化控制程度较高的解吸电积装置。
解吸电积液的配制:1%浓度的NaOH和1%浓度的NaCN混合溶液。
电积槽阳极为带孔的不锈钢板,阴极为专用的优质钢棉。
在生产操作中只要经常观察设备上的各种仪表并触动或旋动设备上的各种按钮或旋扭以控制解吸电积作业的温度、压力、流量、电压和解吸电积时间即可达到较理想的解吸电积效果。
一般解吸温度为105℃,压力为2000Kpa,时间为14~16h(当解吸柱温度达到70℃时开始计时)。
电积温度为70℃一80℃,电压为3~4V,电积液流量为300L/h。
以上各项技术参数较容易控制而且比较稳定,例如烟台鑫海公司矿山设计院就是根据全泥氰化炭浆法来处理金矿,并加入一些创新工艺,最后所得金的品位有保证并且回收率有很大提高,受高度好评。
全泥氰化炭浆工艺 - 金泥的分离提纯、熔炼铸锭阶本阶段作业需在严格的监督和保卫条件下进行。
按金银冶炼的正规方法应先将电积金泥进行火法粗炼,使其中的金银形成粗金银锭,然后再集中从金银锭中进一步分离提纯金和银。
但是,为了加快资金周转,也可以采用把电积金泥直接分离提纯、熔炼铸锭的方法。
金泥的分离提纯(酸法)l)先在金泥中加入一定量的盐酸,充分反应以除去残余钢毛和部分其它溅金属,过滤洗涤后再加入一定量的硝酸,充分反应除去大部分银和其它溅金属,再过滤洗涤。
本步骤主要是控制酸的加入量、反应时间及洗涤程度。
酸的用量与金泥含杂质多少有关,反应时间要根据反应条件和实际反应情况确定,但一般反应时应不少于.2一3h。
洗涤程度至关重要,每次洗涤都必须达到中性,用热水洗涤要快些。
2)向洗涤好的金泥中分次加入3一4倍重量的王水,搅拌溶金,后期加热煮沸,使金以离子状态进入溶液中,过滤得含金溶液和沉渣。
本步骤应注意初加王水时反应剧烈,要防止金液外溢。
溶金反应时间,一般不低于2~3h,要注意观察沉渣颜色的变化。
3)向含金溶液中加入过量的无水亚硫酸钠即可得到海棉金。
在此之前首先要把含金溶液赶酸至PH一6~7。
加无水亚硫酸钠时要小量逐渐地加,直至过量,同时还要不断加热搅拌。
海棉金的熔炼铸锭(焦炭炉)1)在海棉金中加入硼砂10%~15%、碳酸钠5%~10%、玻璃粉3%~5%,混匀后装入经过预热的石墨增祸内,置入炉中熔炼。
熔炼总时间1.5~2.0h,熔炼温度1200~1300℃。
本步要注意控制炉温和熔炼时间,并经常观察钳竭放置情况及竭内物料熔化情况。
2)熔化充分后,用夹钳取出增涡,将熔体倒入铸模内。
本步骤应注意铸模须经过预热,并在内面均匀熏一层厚lmm的黑烟。
浇铸时应注意先慢再快后慢顺序,浇铸时间10秒钟。
取出金锭后先在稀硝酸或盐酸溶液中浸泡约5一10min,再用清水洗去酸,然后在酒精中浸泡片刻、取出擦干即可,金锭成色99.9%。
酸法活化再生活性炭每使用一个循环—吸附~解吸—都要进行酸法活化再生。
具体操作是用3%一5%浓度的盐酸溶液与脱金炭在酸洗容器中搅拌1.5~2h后用清水洗涤,再用1%浓度的NaOH溶液冲洗直到中性为止。
酸法活化再生主要是除去吸附在活性炭上的钙、镁、钠等酸溶物。
应该注意在酸处理过程中会产生剧毒的氢氰酸,必须采取适当的措施以保证安全。
火法活化再生一般活性炭每使用5一10个循环就进行一次火法活化再生处理。
火法活化再生是在钢管窖中进行的,钢管窖的加热区有两个。
第一加热区温度为600℃,产生蒸汽气氛。
第二加热区温度在650℃以上,炭在此区完成活化再生。
具体操作是把湿炭从钢管窖的给料端加入,钢管在旋转过程中把炭输送到排料端排出,炭经空气冷却后即可投入使用。
火法活化再生主要是通过热处理的办法来消除有机物结垢对炭的活性影响。
本段作业由两个污水处理槽串联组成,采用碱氯法处理。
即在碱性条件下直接把漂白粉加入污水处理槽,搅拌、氧化分解污水中的氰化物,从而达到解毒、净化、消除污染的目的。
实际生产中通过调节漂白粉用量来使污水中氰根浓度低于0.5mg/L,然后将污水泵入沉淀池或尾矿库进行自然降解。
全泥氰化炭浆法提金冶炼工艺对矿石的适应性强,具有工艺流程简化、工序简单、投资小、成本低、工艺过程稳定、易于操作、金的总回收率高等特点,是当前国内国际比较流行的金矿选矿工艺,也是金矿选矿发展的趋势。