MEMS工艺(9腐蚀技术)
mems 工艺
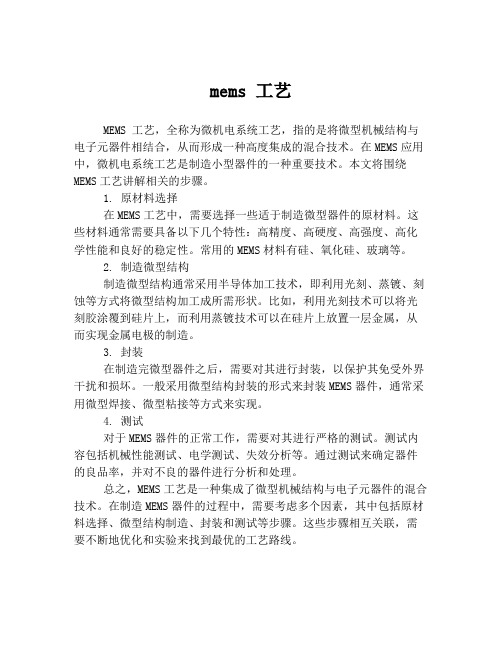
mems 工艺
MEMS 工艺,全称为微机电系统工艺,指的是将微型机械结构与电子元器件相结合,从而形成一种高度集成的混合技术。
在MEMS应用中,微机电系统工艺是制造小型器件的一种重要技术。
本文将围绕MEMS工艺讲解相关的步骤。
1. 原材料选择
在MEMS工艺中,需要选择一些适于制造微型器件的原材料。
这些材料通常需要具备以下几个特性:高精度、高硬度、高强度、高化学性能和良好的稳定性。
常用的MEMS材料有硅、氧化硅、玻璃等。
2. 制造微型结构
制造微型结构通常采用半导体加工技术,即利用光刻、蒸镀、刻蚀等方式将微型结构加工成所需形状。
比如,利用光刻技术可以将光刻胶涂覆到硅片上,而利用蒸镀技术可以在硅片上放置一层金属,从而实现金属电极的制造。
3. 封装
在制造完微型器件之后,需要对其进行封装,以保护其免受外界干扰和损坏。
一般采用微型结构封装的形式来封装MEMS器件,通常采用微型焊接、微型粘接等方式来实现。
4. 测试
对于MEMS器件的正常工作,需要对其进行严格的测试。
测试内容包括机械性能测试、电学测试、失效分析等。
通过测试来确定器件的良品率,并对不良的器件进行分析和处理。
总之,MEMS工艺是一种集成了微型机械结构与电子元器件的混合技术。
在制造MEMS器件的过程中,需要考虑多个因素,其中包括原材料选择、微型结构制造、封装和测试等步骤。
这些步骤相互关联,需要不断地优化和实验来找到最优的工艺路线。
mems工艺技术路线
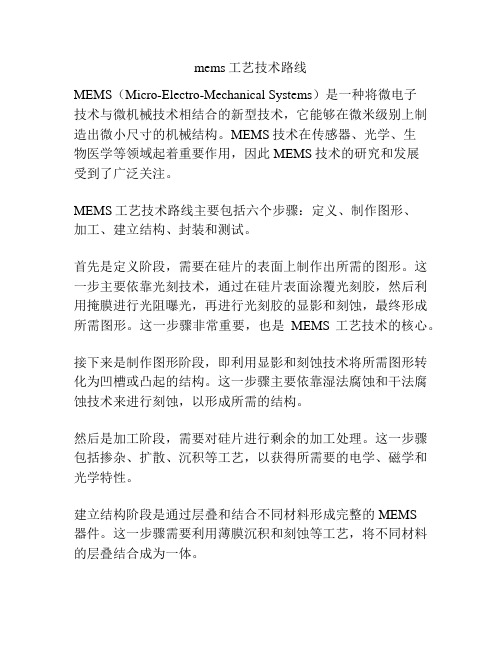
mems工艺技术路线MEMS(Micro-Electro-Mechanical Systems)是一种将微电子技术与微机械技术相结合的新型技术,它能够在微米级别上制造出微小尺寸的机械结构。
MEMS技术在传感器、光学、生物医学等领域起着重要作用,因此MEMS技术的研究和发展受到了广泛关注。
MEMS工艺技术路线主要包括六个步骤:定义、制作图形、加工、建立结构、封装和测试。
首先是定义阶段,需要在硅片的表面上制作出所需的图形。
这一步主要依靠光刻技术,通过在硅片表面涂覆光刻胶,然后利用掩膜进行光阻曝光,再进行光刻胶的显影和刻蚀,最终形成所需图形。
这一步骤非常重要,也是MEMS工艺技术的核心。
接下来是制作图形阶段,即利用显影和刻蚀技术将所需图形转化为凹槽或凸起的结构。
这一步骤主要依靠湿法腐蚀和干法腐蚀技术来进行刻蚀,以形成所需的结构。
然后是加工阶段,需要对硅片进行剩余的加工处理。
这一步骤包括掺杂、扩散、沉积等工艺,以获得所需要的电学、磁学和光学特性。
建立结构阶段是通过层叠和结合不同材料形成完整的MEMS器件。
这一步骤需要利用薄膜沉积和刻蚀等工艺,将不同材料的层叠结合成为一体。
封装是将MEMS器件封装到特定的封装中,保护器件并提供良好的电气和机械性能。
这一步骤主要包括背面研磨、切割、粘接等工艺。
最后是测试阶段,对制造好的MEMS器件进行各种测试。
这一步骤主要包括电学测试、机械测试、光学测试等,以确保器件的性能符合设计要求。
总的来说,MEMS工艺技术路线是一个复杂而精细的过程,需要运用各种微加工和微细结构制造技术。
这一技术路线的研究与发展为MEMS技术的进一步应用和推广提供了重要的支持。
同时,MEMS工艺技术路线也需要不断地进行改进和创新,以适应不断发展的科技需求。
芯片MEMS工艺技术
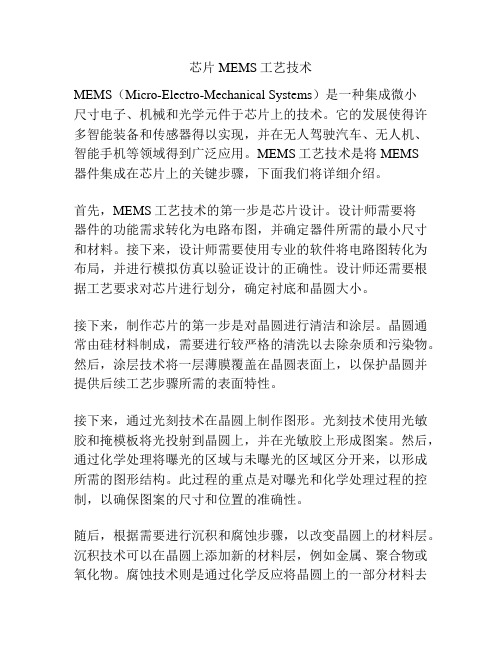
芯片MEMS工艺技术MEMS(Micro-Electro-Mechanical Systems)是一种集成微小尺寸电子、机械和光学元件于芯片上的技术。
它的发展使得许多智能装备和传感器得以实现,并在无人驾驶汽车、无人机、智能手机等领域得到广泛应用。
MEMS工艺技术是将MEMS器件集成在芯片上的关键步骤,下面我们将详细介绍。
首先,MEMS工艺技术的第一步是芯片设计。
设计师需要将器件的功能需求转化为电路布图,并确定器件所需的最小尺寸和材料。
接下来,设计师需要使用专业的软件将电路图转化为布局,并进行模拟仿真以验证设计的正确性。
设计师还需要根据工艺要求对芯片进行划分,确定衬底和晶圆大小。
接下来,制作芯片的第一步是对晶圆进行清洁和涂层。
晶圆通常由硅材料制成,需要进行较严格的清洗以去除杂质和污染物。
然后,涂层技术将一层薄膜覆盖在晶圆表面上,以保护晶圆并提供后续工艺步骤所需的表面特性。
接下来,通过光刻技术在晶圆上制作图形。
光刻技术使用光敏胶和掩模板将光投射到晶圆上,并在光敏胶上形成图案。
然后,通过化学处理将曝光的区域与未曝光的区域区分开来,以形成所需的图形结构。
此过程的重点是对曝光和化学处理过程的控制,以确保图案的尺寸和位置的准确性。
随后,根据需要进行沉积和腐蚀步骤,以改变晶圆上的材料层。
沉积技术可以在晶圆上添加新的材料层,例如金属、聚合物或氧化物。
腐蚀技术则是通过化学反应将晶圆上的一部分材料去除,形成所需的结构。
这些步骤通常需要多次重复,以逐渐构建复杂的器件结构。
最后,进行测试和封装。
在MEMS制造过程的最后阶段,芯片需要进行严格的电学和机械测试来验证其性能。
测试包括电气性能、结构的运动范围和灵敏度等方面。
通过测试后,芯片需要进行封装,以保护芯片上的器件,并为其提供电连接。
封装也可以提供机械支撑和环境保护。
总结而言,MEMS工艺技术是一项复杂的制造过程,需要准确的设计和精确的控制。
它的发展为各种智能装备和传感器的实现提供了可能,推动了现代科技的发展。
MEMS工艺(9腐蚀技术)

1.KOH system
溶剂:水,也有用异丙醇(IPA) 溶液:20% - 50% KOH 温度: 60 – 80º C 速率:~1um/分钟 特点:镜面,易于控制,兼容性差
Si H 2O 2KOH K 2 SiO3 2H
2
KOH的刻蚀机理
2.EDP system
腐蚀技术概述
因为缺乏对工件形状的控制手段,各向同性腐蚀 在微加工生产中总是很难达到技术要求
体硅腐蚀包括:各向异性腐蚀和 各向同性腐蚀
各向异性腐蚀的不足:
腐蚀速率比各项同性腐蚀慢,速率仅能 达到1um/min 腐蚀速率受温度影响 在腐蚀过程中需要将温度升高到100℃左 右,从而影响到许多光刻胶的使用
薄膜残余应力问题
薄膜应力引起结构破裂的问题,主要分为两 大类:
第一类是制造过程的残留热应力、高温淀积后回 归常温,由于热膨胀系数不同所产生的残留热应 力;这种残留热应力可由高温退火的方式达到一 定消除;
第二类是薄膜间因膨胀系数不同造成的残余应力
凸角腐蚀补偿
凸角腐蚀是指在硅岛或硅梁的腐蚀成型过 程中,凸角部分被腐蚀掉的现象,体硅各 向异性腐蚀时经常出现,这是因为对(100) 晶面的硅片体硅腐蚀时,凸角的边缘与[110] 方向平行,而腐蚀液对此方向的腐蚀速度 较快。若要腐蚀出带凸角的整齐的台面结 构,必须采取凸角补偿。
2 、重掺杂自停止腐蚀技术
KOH对硅的腐蚀在掺杂浓度超过阈值浓 N0(约为5×1019CM-3)时,腐蚀速率很小, 轻掺杂与重掺杂硅的腐蚀速率之比高达数 百倍,可以认为KOH溶液对重掺杂硅基本 上不腐蚀。
高掺杂硼有两个缺点:
与标准的CMOS工艺不兼容
导致高应力,使得材料易碎或弯曲
重掺杂硼的硅腐蚀自停止效应比重掺杂磷的 硅明显,所以工艺中常采用重掺杂硅作为硅 腐蚀的自停止材料。
mems硅微加工技术

mems硅微加工技术
MEMS(Micro-Electro-Mechanical Systems)是一种将微型机
械元件、微型传感器、微型执行器和微型电子元件集成在一起的技术。
MEMS硅微加工技术是制造MEMS器件的关键技术之一,它主要
包括光刻、腐蚀、沉积、离子注入、热处理等步骤。
首先,光刻是MEMS硅微加工技术中的重要步骤之一。
通过光刻
技术,可以在硅片上制作出微细的图案和结构,为后续的加工步骤
奠定基础。
其次,腐蚀技术是利用化学溶液对硅片进行局部腐蚀,
形成所需的微结构和微孔洞。
而沉积技术则是在硅片表面沉积金属、氧化物或多晶硅等材料,用于制作电极、传感器和执行器等部件。
离子注入是通过控制离子注入的能量和剂量,改变硅片的导电
性能和机械性能,实现器件的性能调控。
热处理则是通过高温处理,使得材料的晶格结构发生改变,从而改善器件的性能和稳定性。
除了上述技术,MEMS硅微加工还涉及到表面微纳米加工、微结
构的制备和封装技术等。
通过这些技术的综合应用,可以实现微型
机械元件和微型传感器的高精度制造和集成,从而推动MEMS技术在
加速计、压力传感器、微型惯性器件等领域的应用。
总的来说,MEMS硅微加工技术是一项复杂而又精密的技术,它为微型机械系统的制造提供了重要的技术支持,也为微型传感器和执行器的集成提供了关键的工艺手段。
随着技术的不断进步,相信MEMS硅微加工技术将会在更多领域展现出其巨大的潜力和价值。
mems工艺
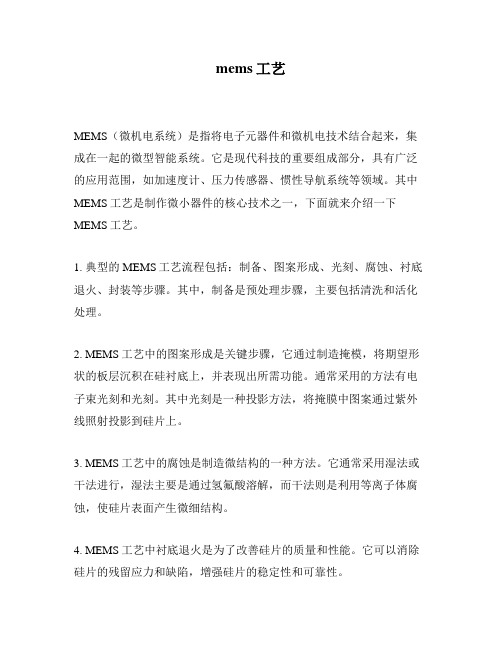
mems工艺
MEMS(微机电系统)是指将电子元器件和微机电技术结合起来,集成在一起的微型智能系统。
它是现代科技的重要组成部分,具有广泛的应用范围,如加速度计、压力传感器、惯性导航系统等领域。
其中MEMS工艺是制作微小器件的核心技术之一,下面就来介绍一下MEMS工艺。
1. 典型的MEMS工艺流程包括:制备、图案形成、光刻、腐蚀、衬底退火、封装等步骤。
其中,制备是预处理步骤,主要包括清洗和活化处理。
2. MEMS工艺中的图案形成是关键步骤,它通过制造掩模,将期望形状的板层沉积在硅衬底上,并表现出所需功能。
通常采用的方法有电子束光刻和光刻。
其中光刻是一种投影方法,将掩膜中图案通过紫外线照射投影到硅片上。
3. MEMS工艺中的腐蚀是制造微结构的一种方法。
它通常采用湿法或干法进行,湿法主要是通过氢氟酸溶解,而干法则是利用等离子体腐蚀,使硅片表面产生微细结构。
4. MEMS工艺中衬底退火是为了改善硅片的质量和性能。
它可以消除硅片的残留应力和缺陷,增强硅片的稳定性和可靠性。
5. MEMS工艺中的封装是保护微结构,避免其与环境接触。
它通常包括两种方法:微机械制造的封装和传统的封装。
综上所述,MEMS工艺是一种复杂的工艺流程,需要应用多种技术手段,在制造微小器件时具有重要的应用价值。
而且随着科技的不断进步,MEMS技术在未来将有更广阔的应用前景。
MEMS湿法腐蚀释放工艺研究的开题报告

MEMS湿法腐蚀释放工艺研究的开题报告
题目:MEMS湿法腐蚀释放工艺研究
摘要:MEMS (Micro-Electro-Mechanical Systems) 是微电子机械系统的缩写,指的是把微型机械制造技术和微电子制造技术相结合,制造出能够感知、处理、存储、输出信息的微型机械系统。
湿法腐蚀释放是MEMS 制造过程中的重要技术之一,本文将对 MEMS 湿法腐蚀释放工艺进行研究。
内容:
1. MEMS 制造技术简介
2. MEMS 湿法腐蚀释放工艺原理与分类
3. MEMS 湿法腐蚀释放工艺的关键技术及其应用
4. 湿法腐蚀释放工艺参数优化研究
5. 实验结果与分析
6. 讨论与结论
研究意义:MEMS 技术在生产制造、生命科学、环境检测、军事领域等多个行业有广泛的应用,其中湿法腐蚀释放作为 MEMS 技术中的核心制造技术之一,对 MEMS 的可制造性和出货率有着重要的影响。
通过对 MEMS 湿法腐蚀释放工艺进行研究,可优化 MEMS 制造流程,提高MEMS 制造效率和产品质量,具有重要的实际应用价值。
关键词:MEMS,湿法腐蚀释放,制造技术,参数优化。
MEMS工艺(9腐蚀技术)

腐蚀技术是MEMS工艺中的关键步骤之一,通过控制材料的去除过程, 可以实现微纳结构的高精度制造。
03
强调本次汇报的重点
本次汇报将重点介绍MEMS工艺中的9种腐蚀技术,包括其原理、特点、
应用及发展趋势。
汇报范围
01
02
03
04
腐蚀技术种类
本次汇报将涵盖湿法腐蚀、干 法腐蚀、电化学腐蚀、光化学 腐蚀、等离子体腐蚀、反应离 子腐蚀、深反应离子腐蚀、激 光腐蚀和微细电火花腐蚀等9 种腐蚀技术。
mems工艺定义
MEMS工艺
MEMS(Micro-Electro-Mechanical Systems)工艺是一种微机电 系统技术,它结合了微电子技术和机械工程技术,通过微米级甚至 纳米级的制造精度,制造出具有特定功能的微型器件和系统。
9腐蚀技术
9腐蚀技术是MEMS工艺中的一种重要技术,它利用特定的腐蚀液 对材料进行选择性腐蚀,从而实现对微型结构的精确加工和制造 。
结合纳米压印、纳米光刻等技术, 实现纳米级别的微结构加工,应用 于生物芯片、光学器件等领域。
05
9腐蚀技术优势与不足
优势分析
01
02
03
高精度制造
9腐蚀技术能够实现高精 度的MEMS器件制造,满 足复杂结构和微小尺寸的 需求。
批量化生产
该技术适用于批量化生产, 能够提高生产效率,降低 成本。
兼容性强
在未来发展中,9腐蚀技术需要不断改 进和完善,提高生产效率、降低成本、 拓展应用领域,以适应MEMS市场的不 断变化和发展需求。同时,也需要与其 他MEMS制造技术相互补充和融合,形 成更加完善的MEMS制造体系。
06
9腐蚀技术改进方向及前景展望
- 1、下载文档前请自行甄别文档内容的完整性,平台不提供额外的编辑、内容补充、找答案等附加服务。
- 2、"仅部分预览"的文档,不可在线预览部分如存在完整性等问题,可反馈申请退款(可完整预览的文档不适用该条件!)。
- 3、如文档侵犯您的权益,请联系客服反馈,我们会尽快为您处理(人工客服工作时间:9:00-18:30)。
1.KOH system
KOH是目前在微机电领域中最常使用的非等 向蚀刻液,为一碱金属之强碱蚀刻液,其金 属杂质会破坏CMOS的氧化层电性,所以不 兼容于IC制程; 但因其价格低廉、溶液配制简单、对硅(100) 蚀刻速率也较其它的蚀刻液为快,更重要的 是操作时稳定、无毒性、又无色,可以观察 蚀刻反应的情况,是目前最常使用的蚀刻液 之一。
在物理腐蚀方法中,利用放电时所产生的高能 惰性气体离子对材料进行轰击,腐蚀速率与轰 击粒子的能量、通量密度以及入射角有关; 在化学腐蚀中,惰性气体(如四氟化碳)在高 频或直流电场中受到激发并分解(如形成氟离 子),然后与被腐蚀材料起反应形成挥发性物 质; 在物理化学结合的方法中,既有粒子与被腐蚀 材料的碰撞,又有惰性气体与被腐蚀材料的反 应。
Ethylenedamine 为有机淡黄色溶液,加入 pyrocatochol后颜色会变成暗褐色,随着反应的进 行,颜色会加深,故不易观察蚀刻表面的反应过程, 蚀刻速率也会改变,这是因为蚀刻液接触到空气中 的氧氧化所引起,此一氧化过程会使得化合物 pyrazine (C4H4N2)增加而改变其蚀刻速率; EDP不具碱金属离子,可与IC制程相容,且对蚀刻 停止所需的硼掺杂浓度较低,大约为7 x 1019 离子 /cm-3,但是EDP具有毒性,蚀刻操作温度须在摄 氏一百多度,危险性较高,操作及废液处理的困难 度亦较高,故在一般微机电制程中不常使用。
5、 P-N 结自停止腐蚀
(1)电钝化腐蚀: 各向异性腐蚀液
(2)PN结自停止:
N-Si
P-Si
腐蚀保护技术
如果硅晶片表面已经形成一些图案,其中 部分薄膜会被腐蚀液所影响,所以必须利 用腐蚀保护技术来保护已完成的结构。 目前常用的保护技术有两种:
一是制作夹具或用胶将整个面保护住;
另一种是淀积氮化硅将正面包住,待背后腐蚀 完后再将氮化硅去除
硅刻蚀的技术是将被腐蚀材料先氧化,然 后由化学反应使其生成一种或多种氧化物 再溶解。
在同一腐蚀液中,由于混有各种试剂,所 以上述两个过程是同时进行的。
体硅各向异性腐蚀 是利用腐蚀液对单晶硅不同晶向腐蚀速 率不同的特性,使用抗蚀材料作掩膜, 用光刻、干法腐蚀和湿法腐蚀等手段制 作掩膜图形后进行的较大深度的腐蚀。 机理:腐蚀液发射空穴给硅,形成氧化 态Si+,而羟基OH-与Si+形成可溶解的 硅氢氧化物的过程。
氮气出口 冷凝水出口
腐蚀设备
冷凝洄流管道 冷凝水 温控温度计 冷凝水入口
氮气
气体 流量 控制 计
磨沙密封口
氮气入口
硅片 腐蚀液 甘油池 石英提篮 石英支架 搅拌器转子 加热电炉
继电器 电源
硅和硅氧化物典型的腐蚀速率
材料 硅在<100>晶向 腐蚀剂 KOH 腐蚀速率 0.25-1.4m/min
硅在<100>晶向 二氧化硅 二氧化硅
(1) 重掺杂自停止腐蚀(KOH 和EDP:51013/cm3, RE/RD~100) (2)(111)面停止 (3) 时间控制 (4)P-N结自停止腐蚀 (5)电化学自停止腐蚀
自停止腐蚀典型工艺流程
工艺路线(1)
硅 光刻胶 扩散层 二氧化硅
工艺路线(2)
1、薄膜自停止腐蚀
薄膜自停止腐蚀是指晶片刻蚀到最后,终止于其它不 会被刻蚀所影响的薄膜,这层薄膜可以是氧化硅、氮 化硅、富硅氮化硅、聚亚酰胺,甚至是金属。 利用薄膜自停止腐蚀必须考虑刻蚀选择性,以及薄膜 应力问题,因为应力太大将使薄膜发生破裂。
薄膜残余应力问题
薄膜应力引起结构破裂的问题,主要分为两 大类:
第一类是制造过程的残留热应力、高温淀积后回 归常温,由于热膨胀系数不同所产生的残留热应 力;这种残留热应力可由高温退火的方式达到一 定消除;
第二类是薄膜间因膨胀系数不同造成的残余应力
凸角腐蚀补偿
凸角腐蚀是指在硅岛或硅梁的腐蚀成型过 程中,凸角部分被腐蚀掉的现象,体硅各 向异性腐蚀时经常出现,这是因为对(100) 晶面的硅片体硅腐蚀时,凸角的边缘与[110] 方向平行,而腐蚀液对此方向的腐蚀速度 较快。若要腐蚀出带凸角的整齐的台面结 构,必须采取凸角补偿。
腐蚀技术概述
因为缺乏对工件形状的控制手段,各向同性腐蚀 在微加工生产中总是很难达到技术要求
体硅腐蚀包括:各向异性腐蚀和 各向同性腐蚀
各向异性腐蚀的不足:
腐蚀速率比各项同性腐蚀慢,速率仅能 达到1um/min 腐蚀速率受温度影响 在腐蚀过程中需要将温度升高到100℃左 右,从而影响到许多光刻胶的使用
2 、重掺杂自停止腐蚀技术
KOH对硅的腐蚀在掺杂浓度超过阈值浓 N0(约为5×1019CM-3)时,腐蚀速率很小, 轻掺杂与重掺杂硅的腐蚀速率之比高达数 百倍,可以认为KOH溶液对重掺杂硅基本 上不腐蚀。
高掺杂硼有两个缺点:
与标准的CMOS工艺不兼容
导致高应力,使得材料易碎或弯曲
重掺杂硼的硅腐蚀自停止效应比重掺杂磷的 硅明显,所以工艺中常采用重掺杂硅作为硅 腐蚀的自停止材料。
湿法腐蚀
简介 各向异性腐蚀 各向同性腐蚀 自停止腐蚀技术
简介
材料刻蚀是微纳技术的最重要手段之一, 在进行新工艺设计时,了解各种材料的 刻蚀速率和腐蚀特性是极为重要的前提。 微技术的出现,加快了各种腐蚀技术特 别是硅腐蚀技术的研究步伐。
硅腐蚀方法主要有两种:干法和湿法 腐蚀特性主要有:各向同性和各向异性 腐蚀的控制: 选择性刻蚀或非选择性 刻蚀 选择方法:晶向和掩模 多种腐蚀技术的应用:体硅工艺(三维 技术),表面硅工艺(准三维技术)
MEMS工艺—— 体硅加工工艺(腐蚀)
石云波
3920397(O) shiyunbo@
主要内容
湿法腐蚀
各向异性 各向同性 自停止腐蚀技术 凸角补偿技术
干法刻蚀
深槽技术
一、体硅微制造
体硅微制造广泛应用于微型传感器和 加速计的制造上 通过基底材料的去除(通常是硅晶 片),来形成想要的三维立体的微结 构。
A:乙酸(CH3COOH)
W: Water
Etching Bulk Silicon
三、自停止腐蚀技术 机理:
EPW和KOH对硅的腐蚀在掺杂浓度小 于11019cm-3时基本为常数,超过该浓 度时,腐蚀速率与掺杂硼浓度的4次方 成反比,达到一定的浓度时,腐蚀速率 很小,甚至可以认为腐蚀“停止”。
四、干法腐蚀
湿法腐蚀的缺点:图形受晶向限制,深宽比较差, 倾斜侧壁,小结构粘附。
侠义的干法刻蚀主要是指利用等离子体放 电产生的化学过程对材料表面的加工 广义上的干法刻蚀则还包括除等离子体刻 蚀外的其它物理和化学加工方法,例如激 光加工、火花放电加工、化学蒸汽加工以 及喷粉加工等。
干法刻蚀的优点:
氮化硅 氮化硅
EDP KOH EDP
KOH EDP
பைடு நூலகம்
0.75m/min 40-80nm/h 12nm/h
5nm/h 6nm/h
影响腐蚀质量因素
反应机制
反应物扩散到腐蚀液表面 反应物与腐蚀表面发生化学反应 反应物的生成物扩散到溶液中去
影响腐蚀质量因素
晶格方向
腐蚀溶液的选择
腐蚀溶液的浓度
腐蚀时间
表面流速A
操作温度温度
转子
硅片 深度A
表面流速B
搅拌方式
低速区 深度B 高速区 腐蚀液 容器
100方向硅片的腐蚀特点
111面凹角停止
110方向硅片的腐蚀特点
影响各向异性腐蚀的主要因素
(1) 溶液及配比
(2) 温度
各向同性腐蚀
硅的各向同性腐蚀在半导体工艺中以及在微 机械加工技术中有着极为广泛的应用。常用的 腐蚀液为HF-HNO3加水或者乙酸系统。腐蚀机 理为:
重掺杂自停止腐蚀工艺流程
3、(111)面自停止腐蚀
KOH溶液对(100)和(111)面硅的 腐蚀速率差别很大,可高达100~400 倍,因此可利用(111)面作为停止腐 蚀的晶面。
(111)面自停止腐蚀工艺流程
4、电化学自停止腐蚀
电化学自停止腐蚀技术不需要重掺杂层,由于 用了外延技术,因此腐蚀自停止层可以做的很 厚。
具有分辨率高、各向异性腐蚀能力强、 腐蚀的选择比大、能进行自动化操作等
干法刻蚀的过程:
腐蚀性气体离子的产生 离子向衬底的传输 衬底表面的腐蚀 腐蚀反应物的排除
干法腐蚀的主要形式:
*纯化学过程:(等离子体腐蚀 ) *纯物理过程: (离子刻蚀、离子束腐蚀) *物理化学过程:反应离子腐蚀RIE ,离子 束辅助自由基腐蚀ICP.
4、TMAH
氢氧化四钾铵为有机、无色之水溶液,原本为半导体制程中 正胶的显影液,但目前亦应用于蚀刻制程中。 TMAH的毒性低为其最大优点,对于SiO及SiN等介电材料蚀 刻率低;对于Ti和Al有明显的蚀刻,在蚀刻组件前需加入适 当的硅粉末,降低对铝的蚀刻率,亦可加入酸来降低蚀刻液 的pH值,如酸与铝会发生化学反应生成硅铝酸盐,硅铝酸盐 对蚀刻液有较好的抵抗能力,可以保护铝材的电路。 TMAH的蚀刻反应过程会因操作参数不同而有极大的差异, 且长时间蚀刻蚀刻液亦不稳定。此外,适用于硅微加工的高 浓度TMAH(>15%)价格高昂,都是无法广泛应用的原因。
2.EDP system
EPW[NH2(CH2)2NH2乙二胺,C6H4(OH2)2 (邻 苯二酚),H2O] EDP[ Ethylen Diamine, Procatechol, H2O] 特点:蒸 气有毒,时效较差, P+选择性好
2 NH 2 (CH 2 ) 2 NH 2 Si 3C6 H 4 (CH 2 ) 2 NH 2 (CH 2 ) 2 NH Si(C6 H 4 O2 ) 3 2 H
1.KOH system