6063铝合金常见缺陷
6063铝合金铸锭_中心裂纹_的成因及对策

6063铝合金铸锭“中心裂纹”的成因及对策苏亚军(焦作市万方集团有限责任公司,河南 焦作 454003)摘要:阐述了6063铝合金“中心裂纹”铸锭对铝型材表面质量的不良影响,其次,分析了裂纹的形成机理及其影响因素,提出了具体的解决方案。
关键词:中心裂纹;热裂纹;铸造应力;氧化物条痕;组织条痕Causes and Coun ter m ea sures of Chevron Crackfor 6063A lloy lngotSU Ya -Jun(Jaozuowanfang (group )co .,ltd J i a ozuo 45403)Abstract :T he article elabo rates on the negative influence of the chevron crack of 6063alum in ium all oy ingo t on the sur 2face quality of 6063alum in ium all oy p rofile ,analyses the fom nati on m echan is m and effects of the chevron crack and the p ropo ses coun ter m easuresKeywords :Chevron crack ;ho t tear ;casting stress ;ox ide streak ;structural streak前言在6063铝合金型材的生产过程中,有时会出现被称为“氧化物条痕”的挤压材表面缺陷。
这种缺陷是因铸锭内部的非金属夹杂物,在平行于挤压方向上流入挤压件表面而造成的。
客观存在于挤压过程中只表现挤压件光泽不佳,呈现白色浑浊的表面。
腐蚀后,表面粗糙、发灰,阳极氧化处理后,因为有缺陷的部位不形成氧化膜,所以可借助涡流测厚仪检测出来。
有资料[1]认为:“氧化物条痕”的产生主要是由于铸锭表面及挤压筒内残留金属中的非金属夹杂物流入挤压件而造成的。
6063铝合金型材氧化缺陷原因分析及解决

6063铝合金型材氧化缺陷原因分析及解决1问题的提出在实际生产中,加工率大(ε>95%),壁厚较薄(δ≤1.5mm)的T5状态的6063铝合金挤压型材在经硫酸阳极氧化处理后,其表面会呈现有规律(而有时无规律)分布的白色斑点(或无光斑痕);严重时呈现深色斑痕——“白斑”。
“白斑”的分布规律及特征是:它是在平行于挤压方向的平面上大致等间距的、呈线状或扁四边形状或不规则星点(片)状的、相对于基体表面有微小深度而呈凹槽形的一种表面缺陷。
白斑通常分布于型材的一个或几个表面,有时会分布在型材的所有表面(对薄壁空心型材,则是分布于某一平面或曲面的内外两侧)。
2原因分析在现场见到,“白斑”形成于“碱蚀”工序,在经随后的稀硝酸(或硫酸)“中和”之后,并未消失;经硫酸阳极氧化处理后,又更加清晰地呈现出来。
笔者专门截取了两段“白斑”点面积较大(F=30~40mm2)的碱蚀洗(槽液中,ω(Zn2+)≥5×106)型材试样。
然后,采用DV-5型原子发射火花直读光谱仪分别对上述两段试样的“白斑”区的成分做了定量分析,其结果如下(表中数据均为质量分数):由表1的分析结果可见:“白斑”处Si、Mg、Zn元素的含量明显增加:而表2的结果表明:“白斑”处Si、Zn元素的含量明显增加,而Mg元素的含量却有所下降。
从金属材料腐蚀的观点看来,Mg2Si这种表面缺陷实质上是6063铝合金材料发生“剥落腐蚀”的结果。
剥落腐蚀是一种浅表面的选择腐蚀,腐蚀是沿着金属表面发展的,其产物的体积往往比发生腐蚀的金属大得多,因而膨胀。
一般而言,当铝与呈阴极性的异种金属相邻接时,“剥落腐蚀”程度上升。
在电子显微镜下观察发现:“剥落腐蚀”通常沿不溶组成物(如Si,Mg2Si等),或沿晶界进行。
2.1铸锭质量的影响6063铝合金的主要相组成是:α(Al)固溶体、游离Si(阳极相)和F eAl3(阳极相);当铁含量大于时,有β(F e Si Al)(阳极相);而当铁含量小于时,有α(F e Si Al)(阴极相);其他可能的杂质相是:MgZn2、CuAl2等。
6063挤压型材条纹缺陷产生原因分析及解决措施
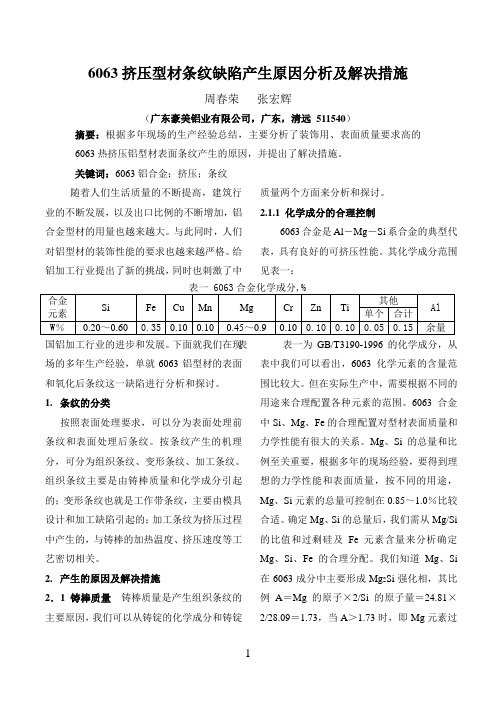
6063挤压型材条纹缺陷产生原因分析及解决措施周春荣张宏辉(广东豪美铝业有限公司,广东,清远511540)摘要:根据多年现场的生产经验总结,主要分析了装饰用、表面质量要求高的6063热挤压铝型材表面条纹产生的原因,并提出了解决措施。
关键词:6063铝合金;挤压;条纹随着人们生活质量的不断提高,建筑行业的不断发展,以及出口比例的不断增加,铝合金型材的用量也越来越大。
与此同时,人们对铝型材的装饰性能的要求也越来越严格。
给铝加工行业提出了新的挑战,同时也刺激了中国铝加工行业的进步和发展。
下面就我们在现场的多年生产经验,单就6063铝型材的表面和氧化后条纹这一缺陷进行分析和探讨。
1.条纹的分类按照表面处理要求,可以分为表面处理前条纹和表面处理后条纹。
按条纹产生的机理分,可分为组织条纹、变形条纹、加工条纹。
组织条纹主要是由铸棒质量和化学成分引起的;变形条纹也就是工作带条纹,主要由模具设计和加工缺陷引起的;加工条纹为挤压过程中产生的,与铸棒的加热温度、挤压速度等工艺密切相关。
2.产生的原因及解决措施2.1 铸棒质量铸棒质量是产生组织条纹的主要原因,我们可以从铸锭的化学成分和铸锭质量两个方面来分析和探讨。
2.1.1 化学成分的合理控制6063合金是Al-Mg-Si系合金的典型代表,具有良好的可挤压性能。
其化学成分范围见表一:表表一为GB/T3190-1996的化学成分,从表中我们可以看出,6063化学元素的含量范围比较大。
但在实际生产中,需要根据不同的用途来合理配置各种元素的范围。
6063合金中Si、Mg、Fe的合理配置对型材表面质量和力学性能有很大的关系。
Mg、Si的总量和比例至关重要,根据多年的现场经验,要得到理想的力学性能和表面质量,按不同的用途,Mg、Si元素的总量可控制在0.85~1.0%比较合适。
确定Mg、Si的总量后,我们需从Mg/Si的比值和过剩硅及Fe元素含量来分析确定Mg、Si、Fe的合理分配。
6063铝型材阳极氧化表面斑点腐蚀缺陷的原因分析

6063铝型材阳极氧化表面斑点腐蚀缺陷的原因分析6063铝型材经阳极氧化后,具有具有良好的耐蚀性能和装饰性能,近年来,随着国民经济的发展及人们生活水平的提高,铝合金门窗、铝合金幕墙的使用越来越普及,然而不少的铝合金在使用一段时间以后,表面出现形态各异的腐蚀缺陷,其中斑点腐蚀较为常见,严重影响铝型材的使用性能及装饰效果。
为了合理改善铝型材的表面质量,达到控制表面斑点腐蚀的目的,很有必要对斑点缺陷做深入细致的分析。
下面就6063铝型材经阳极氧化后表面出现的斑点腐蚀的问题,分析斑点腐蚀的本质、成因及生成机理,探讨产生斑点腐蚀的关键因素。
1 斑点腐蚀的本质分析由所使用的6063铝型材成分可知,为了确保Mg元素充分形成强化相Mg2Si,一般在配制合金成分时人为的使Si元素适量过剩。
因为随着Si含量的增加,合金的晶粒变细,热处理效果较好。
但另一方面,Si的过剩也有负面作用,使合金的塑性降低,耐蚀性变坏。
研究表明:过剩Si不仅能形成游离态的Si相,还会与基体形成α相(Al12Fe2Si)和β相(Al9Fe3Si2),这样在铝合金中存在游离态的Si相、α相(Al12Fe2Si)、β相(Al9Fe3Si2)等阴极相粒子和阳极相Mg2Si粒子。
α相和β相对合金的腐蚀性能影响很大,尤其是β相能显着降低合金的腐蚀性能。
斑点处残留物的成分主要是游离Si相和AlFeSi相,同时发现氯元素在残留物处也发生了吸附,这说明Cl-参与了腐蚀过程。
腐蚀区中锌元素含量较基体高得多,说明合金中的杂质元素锌也参与了腐蚀过程。
阳极氧化工序中,阳极相Mg2Si是合金的点蚀源。
在阳极氧化碱洗时,Mg2Si 粒子优先溶解而形成蚀坑,其中镁溶解在溶液中而硅在铝合金上残留下来,当蚀坑聚集在晶粒上就会使该晶粒颜色发暗。
在硫酸中和工序中硅不易除去,故斑点腐蚀蚀坑底部硅含量较其他区域高。
2 斑点腐蚀的成因分析影响斑点腐蚀的主要因素有预处理过程中的碱洗温度、碱洗时间以及合金成分中的Zn、Fe、Si元素含量与合金的挤压状态等。
6063铝合金型材雪花斑产生机理及对策

6063铝合金型材雪花斑产生机理及对策齐少山(曲阜远东铝业有限公司 山东 曲阜 273100)摘要:对6063铝合金型材产生的“雪花斑”缺陷进行了研究。
并通过大量的试验证明,雪花斑产生的主要原因是铝棒中的含有H,阳极氧化前处理时,H与Al发生原电池反应,产生坑点腐蚀所致。
关键词:雪花斑;介稳定相;坑点腐蚀;中和中图分类号:TG115121+313,TG115121+513 文献标识码:B 文章编号:1005-4898(2004)04-0027-03C ausing Mechanism and Countermeasurefor“Snow2Shape Spot”for6063Aluminum Alloy ProfilesQI Shao2shan(Q u fu F ar2E ast Aluminum Co Ltd,Q u fu,Shandong273100,China)Abstract:The defect“snow2shape spot”existed in6063aluminum alloy profiles is analyzed1The main cause of“snow2shape spot”is that H2existed in aluminum rod,and primary battery reaction was occurred between H and Al prior to anodizing,thus caused the pit spot1K eyw ords:snow shape spot;metastable phase;pitting corrosion;neutralization 6063铝合金因其良好的可挤压成形、易氧化、着色、具有稳定的物理性能,并作为现代建筑门窗幕墙工程中的主要构架而被广泛采用。
但在6063铝合金型材的氧化生产过程中,经常会有不同厂家铝棒所挤型材在氧化前处理过程中产生一种类似“雪花”状缺陷的不合格品(行业界简称雪花斑),给铝型材生产的稳定性和成品率造成很大的影响。
6063铝合金挤压型材觉缺陷及其解决方法

6063铝合金挤压型材觉缺陷及其解决方法
1.毛刺:毛刺是挤压型材表面的突出物,会影响外观和触感。
毛刺的
主要原因是金属挤压时的不均匀变形和模具壁口的磨损。
解决方法包括增
加材料的充填比例,优化挤压工艺参数,增加模具壁口的滑移润滑剂等。
2.断裂:断裂是挤压型材在生产和使用过程中出现的一个严重问题。
断裂的原因可以是材料本身的强度不足、挤压工艺参数设置不当、模具设
计不合理等。
解决方法包括选择合适的6063铝合金型材,优化挤压工艺
参数,加强模具的冷却和加热控制等。
3.冷裂纹:冷裂纹是在挤压型材的表面或内部出现的长而细的裂纹。
冷裂纹的出现与材料的热处理过程和冷却速度不当有关。
解决方法包括优
化挤压工艺参数,控制冷却速度,合理设计材料的热处理过程等。
4.物理性能不稳定:6063铝合金挤压型材的物理性能,如硬度、抗
拉强度、延展性等,可能存在不稳定的情况。
这可能是由于挤压工艺中的
应力集中和不均匀变形导致的。
解决方法包括优化挤压工艺参数,增加冷
却控制,合理设计模具结构等。
5.起皮:起皮是指挤压型材表面出现的局部脱层现象,降低了型材的
使用寿命。
起皮的原因主要是模具的磨损和使用不当。
解决方法包括定期
检查和维护模具,增加模具的使用寿命,减少起皮现象的发生。
总之,6063铝合金挤压型材的觉缺陷可能会影响其质量和使用寿命。
通过合理选择材料、优化挤压工艺参数、改进模具设计和加强质量控制等
措施,可以有效地解决这些问题,提高挤压型材的质量和性能。
铝合金圆铸锭质量缺陷分析
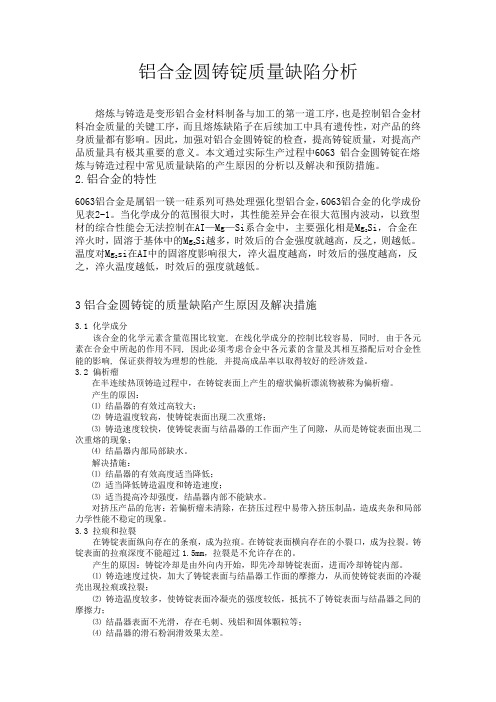
铝合金圆铸锭质量缺陷分析熔炼与铸造是变形铝合金材料制备与加工的第一道工序,也是控制铝合金材料冶金质量的关键工序,而且熔炼缺陷子在后续加工中具有遗传性,对产品的终身质量都有影响。
因此,加强对铝合金圆铸锭的检查,提高铸锭质量,对提高产品质量具有极其重要的意义。
本文通过实际生产过程中6063 铝合金圆铸锭在熔炼与铸造过程中常见质量缺陷的产生原因的分析以及解决和预防措施。
2.铝合金的特性6063铝合金是属铝一镁一硅系列可热处理强化型铝合金,6063铝合金的化学成份见表2-1。
当化学成分的范围很大时,其性能差异会在很大范围内波动,以致型Si,合金在材的综合性能会无法控制在AI—Mg—Si系合金中,主要强化相是Mg2淬火时,固溶于基体中的MgSi越多,时效后的合金强度就越高,反之,则越低。
2si在AI中的固溶度影响很大,淬火温度越高,时效后的强度越高,反温度对Mg2之,淬火温度越低,时效后的强度就越低。
3铝合金圆铸锭的质量缺陷产生原因及解决措施3.1 化学成分该合金的化学元素含量范围比较宽, 在线化学成分的控制比较容易, 同时, 由于各元素在合金中所起的作用不同, 因此必须考虑合金中各元素的含量及其相互搭配后对合金性能的影响, 保证获得较为理想的性能, 并提高成品率以取得较好的经济效益。
3.2 偏析瘤在半连续热顶铸造过程中,在铸锭表面上产生的瘤状偏析漂流物被称为偏析瘤。
产生的原因:⑴结晶器的有效过高较大;⑵铸造温度较高,使铸锭表面出现二次重熔;⑶铸造速度较快,使铸锭表面与结晶器的工作面产生了间隙,从而是铸锭表面出现二次重熔的现象;⑷结晶器内部局部缺水。
解决措施:⑴结晶器的有效高度适当降低;⑵适当降低铸造温度和铸造速度;⑶适当提高冷却强度,结晶器内部不能缺水。
对挤压产品的危害:若偏析瘤未清除,在挤压过程中易带入挤压制品,造成夹杂和局部力学性能不稳定的现象。
3.3 拉痕和拉裂在铸锭表面纵向存在的条痕,成为拉痕。
6063铝合金型材表面麻点的成因及解决方法

收稿日期:2006-08-03 作者简介:杜新宇(1968-),男,河南南阳人,工程师。
6063铝合金型材表面麻点的成因及解决方法杜新宇(南阳市康远机器总厂,河南南阳473125)摘要:通过生产实践与试验分析,找出6063铝合金型材产生麻点缺陷的各种原因,提出了避免和减轻这一缺陷的方法。
关键词:6063铝合金;型材;麻点;挤压工艺;铸锭;挤压工具中图分类号:TG 379 文献标识码:A 文章编号:1007-7235(2006)12-0032-03Countermeasures and causes of point defects on 6063aluminiumalloy profile surfacesDU X in 2yu(N anyang K angyu an Machine Work ,N anyang 473125,China)Abstract :Through practice and test analysis ,the author of the paper has found out the various reas ons for the formation of the vice of rough points in the production of 6063aluminum alloy.Then he has suggested methods for av oiding or abating such a vice.K ey w ords :6063aluminum alloy ;profile ;rough point ;extrusion process ;ing ot ;extrusion implement 在6063合金挤压生产中,型材表面常出现麻点现象。
麻点的形状像彗星轨迹,好像缝衣针的针尖在型材表面剜挑的犁痕。
麻点头部小、尾部大,严重时用手摸可感觉麻点尾部有硬质点。
- 1、下载文档前请自行甄别文档内容的完整性,平台不提供额外的编辑、内容补充、找答案等附加服务。
- 2、"仅部分预览"的文档,不可在线预览部分如存在完整性等问题,可反馈申请退款(可完整预览的文档不适用该条件!)。
- 3、如文档侵犯您的权益,请联系客服反馈,我们会尽快为您处理(人工客服工作时间:9:00-18:30)。
6063铝合金常见缺陷6063铝合金>铝合金型材以其良好的塑性、适中的热处理强度、良好的焊接性能以及阳极氧化处理后表面华丽的色泽等诸多优点而被广泛应用。
但在生产过程中经常会出现一些缺陷而致使产品质量低下,成品率降低,生产成本增加,效益下降,最终导致企业的市场竞争能力下降。
因此,从根源上着手解决6063铝合金挤压型材的缺陷问题是企业提高自身竞争力的一个重要方面。
笔者根据多年的铝型材生产实践,在此对6063铝合金挤压型材常见缺陷及其解决办法作一总结,和众多同行交流,以期相互促进。
1.碰伤划伤、擦伤、碰伤是当型材从模孔流出以及在随后工序中与工具、设备等相接触时导致的表面损伤。
1.1主要原因:1.1.1铸锭表面附着有杂物或铸锭成分偏析。
铸锭表面存在大量偏析浮出物而铸锭又未进行均匀化处理或均匀化处理效果不好时,铸锭内存在一定数量的坚硬的金属颗粒,在挤压过程中金属流经工作带时,这些偏析浮出物或坚硬的金属颗粒附着在工作带表面或对工作带造成损伤,最终对型材表面造成划伤;1.1.2模具型腔或工作带上有杂物,模具工作带硬度较低,使工作带表面在挤压时受伤而划伤型材;1.1.3出料轨道或摆床上有裸露的金属或石墨条内有较硬的夹杂物,当其与型材接触时对型材表面造成划伤;1.1.4在叉料杆将型材从出料轨道上送到摆床上时,由于速度过快造成型材碰伤;1.1.5在摆床上人为拖动型材造成擦伤;1.1.6在运输过程中型材之间相互摩擦或挤压造成损伤。
1.2解决办法1.2.1加强对铸锭质量的控制;1.2.2提高修模质量,模具定期氮化并严格执行氮化工艺;1.2.3用软质毛毡将型材与辅具隔离,尽量减少型材与辅具的接触损伤;1.2.4生产中要轻拿轻放,尽量避免随意拖动或翻动型材;1.2.5在料框中合理摆放型材,尽量避免相互摩擦。
2.机械性能不合格2.1主要原因2.1.1挤压时温度过低,挤压速度太慢,型材在挤压机的出口温度达不到固溶温度,起不到固溶强化作用;2.1.2型材出口处风机少,风量不够,导致冷却速度慢,不能使型材在最短的时间内降到200℃以下,使粗大的Mg2Si过早析出,从而使固溶相减少,影响了型材热处理后的机械性能;2.1.3铸锭成分不合格,铸锭中的Mg、Si含量达不到标准要求;2.1.4铸锭未均匀化处理,使铸锭组织中析出的Mg2Si相无法在挤压的较短时间内重新固溶,造成固溶不充分而影响了产品性能;2.1.5时效工艺不当、热风循环不畅或热电偶安装位置不正确,导致时效不充分或过时效。
2.1.6挤压系数过低。
2.2解决办法2.2.1合理控制挤压温度和挤压速度,使型材在挤压机的出口温度保持在最低固溶温度以上;2.2.2强化风冷条件,有条件的工厂可安装雾化冷却装置,以期达到6063合金冷却梯度的最低要求;2.2.3加强铸锭的质量管理;2.2.4对铸锭进行均匀化处理;2.2.5合理确定时效工艺,正确安装热电偶,正确摆放型材以保证热风循环通畅。
2.2.6选择合理的挤压系数,棒材的挤压系数控制在(25)以上。
3.几何尺寸超差3.1主要原因3.1.1由于模具设计不合理或制造有误、挤压工艺不当、模具与挤压筒不对中、不合理润滑等,导致金属流动中各点流速相差过大,从而产生内应力致使型材变形;3.1.2由于牵引力过大或拉伸矫直量过大导致型材尺寸超差。
3.2解决办法3.2.1合理设计模具,保证模具精度;3.2.2正确执行挤压工艺,合理设定挤压温度和挤压速度;3.2.3保证设备的对中性;3.2.4采用适中的牵引力,严格控制型材的拉伸矫直量。
4.挤压波纹:挤压波纹是指在挤压型材表面出现的类似于水波纹的情况,一般无手感,在光的作用下表现明显。
4.1主要原因4.1.1牵引机发生周期性上下跳动使型材表面发生局部弯折;4.1.2模具设计不合理,工作带在挤压力作用下发生颤动导致型材出现波纹。
4.2解决办法4.2.1保证牵引机运行平稳;4.2.2合理设计模具结构。
5.麻面:麻面是指在型材表面出现的密度不等、带有拖尾、非常细小的瘤状物,手感明显,有尖刺的感觉。
5.1主要原因:由于铸锭中的夹杂物或模具工作带上粘有金属或杂物,在挤压时被高温高压的铝夹带着脱落,在型材表面形成麻面。
5.2解决办法5.2.1适当降低挤压速度,采用合理的挤压温度和模具温度;5.2.2严格控制铸锭质量,降低铸锭中的夹杂物含量,将铸锭进行均匀化处理;5.2.3加强修模质量管理。
6.黑斑:型材阳极氧化后局部出现近似圆形的黑灰色斑点,在型材纵向贴摆床的面上等距离分布,大小不一。
6.1主要原因:由于挤压机出口处风冷量不够,导致铝材在较高温度下接触摆床,接触部位的冷却速度于其它位置不同,有粗大的Mg2Si相析出,在阳极氧化处理后该部位变为黑灰色。
6.2解决办法6.2.1加强风冷强度,避免摆床上型材的间隔过小,保证风冷的温度梯度;6.2.2有条件的工厂应采用雾化水冷与风冷相结合的方法,可完全消除黑斑。
7.条纹:挤压型材的条纹缺陷种类比较多,形成因素也较复杂,这里仅就一些常见条纹的产生原因及解决方法加以论述。
7.1摩擦纹:模具每次光模上机挤压后,纹路都不能一一对应,有轻有重。
7.1.1主要原因:在挤压过程中,型材流出模孔的瞬间与工作带紧紧地靠在一起,构成一对热状态下的干摩擦副,且将工作带分成两个区——粘着区和滑动区。
在粘着区内,金属质点受到至少来自两个方面的力的作用:摩擦力和剪切力。
当粘着区内金属质点所受摩擦力大于剪切力时,金属质点就会粘附在粘着区工作带表面上,并将型材表面擦伤而形成摩擦纹。
7.1.2解决办法7.1.2.1调整模具工作带出口角α,使其在-1°~-3°范围内,这样可降低工作带粘着区高度,减小该区的摩擦力,增大滑动区;7.1.2.2进行高效的模具氮化处理,使模具表面硬度保持在HV900以上;工作带表面渗硫可降低粘着区摩擦力,减少摩擦纹。
7.2组织条纹7.2.1主要原因:铸锭铸造组织不均匀,成分偏析,铸锭表皮下存在较严重的缺陷,铸锭的均匀比处理不充分等,在随后的挤压过程中导致型材表面成分不均匀,从而使型材氧化后的着色能力不相同,形成组织条纹。
7.2.2解决办法:7.2.2.1合理执行铸造工艺,消除或减轻组织偏析;7.2.2.2铸锭表面车皮;7.2.2.3认真进行铸锭均匀化处理。
7.3金属亮纹:在氧化白料中表现发亮,大多数情况下为笔直条状且宽度不定,在氧化着色料中该条纹呈浅色条状。
7.3.1主要原因由于金属流动出现摩擦或变形极其剧烈时,金属局部温度会上升很高,另外金属流动不均匀也会导致晶粒发生剧烈破碎,然后发生再结晶,致使该处组织发生变化,在随后的氧化处理中导致型材表面出现纵向的亮条纹,着色处理中致使型材着不上色或呈现浅色条纹。
7.3.2解决办法:7.3.2.1合理设计模具结构;7.3.2.2模具加工要注意工作带的过渡,防止出现工作带落差;7.3.2.3保证模桥呈水滴形,消除棱角。
7.4焊合条纹:焊合条纹又称焊缝,笔直通长,在氧化白料中多呈现浅灰色,着色料中多显浅色。
7.4.1主要原因7.4.1.1模具分流孔设计过小;7.4.1.2焊合室深度不够,不能保证有足够的压力;7.4.1.3挤压时模具焊合室内铝料供应不足;7.4.1.4挤压工艺不合理,润滑不当。
7.4.2解决办法7.4.2.1合理设计模具结构;7.4.2.2注意挤压温度和挤压速度的协调;7.4.2.3尽量减少润滑或不润滑。
8.裂纹:挤压时型材受到拉应力作用而在表面形成程度不同的金属横向撕裂现象。
8.1主要原因8.1.1由于摩擦力的原因使金属表层受到附加拉应力的作用,当附加拉应力大于表层金属抗拉强度时就会产生裂纹;8.1.2挤压温度过高,金属表层抗拉强度下降,在摩擦力作用下产生裂纹;8.1.3挤压速度过快时,金属表层所受的附加拉应力增加使型材产生裂纹。
8.2解决办法:严格控制挤压工艺参数以保证合理的出口速度和出口温度。
9.波浪、扭拧、弯曲波浪、扭拧、弯曲是由于金属流动不均匀造成的型材外形缺陷。
9.1主要原因9.1.1模具工作带设计不合理导致金属流动不均匀;9.1.2挤压速度过快或挤压温度过高导致金属流动不均匀;9.1.3模具型孔布局不合理造成金属流动不均匀;9.1.4导路不合适或未安装导路;9.1.5润滑不合适。
9.2解决办法9.2.1修整模具工作带使金属流动均匀;9.2.2采用合理的挤压工艺,在保证出口温度的前提下尽量采用低温挤压;9.2.3合理设计模具结构;9.2.4配置合适的导路;9.2.5合理润滑;9.2.6采用牵引机牵引挤压。
10.气泡:型材表层金属与基体金属出现局部连续或断续的分离,表现为圆形或局部连续凸起。
10.1主要原因10.1.1由于挤压筒经长期使用后尺寸超差,挤压时筒内气体未排除,变形金属表层沿前端弹性区流出而造成气泡;10.1.2铸锭表面有沟槽或铸锭组织中有气孔,铸锭在墩粗时包进了气体,挤压时气体进入金属表层;10.1.3挤压时,铸锭或模具中带有水分和油污,由于水和油污受热挥发成气体,在高温高压的金属流动中被卷入型材表面形成气体;10.1.4设备排气装置工作不正常;10.1.5金属填充过快,造成挤压排气不好。
10.2解决办法10.2.1合理选择和配备挤压工具,及时检查和更换;10.2.2加强铸锭的质量管理,严格控制铸锭的表面质量和含气量;10.2.3保证设备的排气系统正常工作;10.2.4剪刀、挤压筒和模具应尽量少涂油或不涂油;10.2.5合理控制挤压速度,按要求进行排气。
11.石墨压入沿型材纵向浅表层呈条状半露的孔隙,短的几毫米,长则几厘米或更长。
孔隙中主要成分为石墨。
11.1主要原因:11.1.1由于石墨润滑剂中石墨比例过高或石墨没有完全搅拌均匀,有颗粒或块状石墨存在;11.1.2石墨润滑剂的涂抹过于接近分流或型孔,挤压时这些石墨没有进入压余,而是被高温高压的金属流卷入制品的浅表层形成石墨压入。
11.2解决办法:11.2.1使用优质的润滑剂;11.2.2润滑剂涂抹时要离分流孔或型孔远一些,尽量少使用或不使用润滑剂。