焦化工艺技术发展概述_配煤炼焦篇_一_
焦化工艺的发展史

焦化工艺的发展史
焦化工艺是一种重要的化学工艺,主要是将煤炭或石油等碳质燃料在高温下进行热解,生成焦炭、煤气和其他化学物质。
其发展历史可以追溯到19世纪初,以下是其发展史的主要里程碑:
1. 1794年,英国化学家约瑟夫·普利斯特利发明了焦化炉,首次实现了工业化的焦化生产。
2. 1850年代,美国工业家卡内基开始投资焦化行业,并在1870年代成立了美国首个全国性焦化组织——美国焦化业协会。
3. 20世纪初,美国人W.S.芬克发明了煤气化炉,将固态煤转化为可燃气体,大大提高了能源利用效率。
4. 20世纪20年代至30年代,欧洲和日本国内的焦化技术得到了快速发展,特别是在高炉炼铁方面大放异彩。
5. 20世纪60年代以后,世界各国开始推广新型的焦化技术,如煤气化、溶剂抽提、液化等,以进一步提高能源利用效率、减少污染排放、实现资源循环利用等目标。
6. 近年来,随着环保意识的增强和能源结构的转型,一些发达国家开始放缓焦
化产业的发展,并加强对污染排放的限制和监管。
但是在一些亚洲和非洲地区,仍有不少焦化企业在积极发展,并致力于推进技术创新和环境保护。
焦化厂炼焦工艺介绍分解

焦化厂炼焦工艺介绍分解首先,炼焦过程开始于煤炭的破碎和研磨阶段。
此阶段的目的是将大块煤炭破碎成适合炉料使用的小颗粒。
然后,这些小颗粒被进一步细磨以提高反应速率。
接下来,细磨后的煤炭被送入炼焦炉。
炼焦炉是一个巨大的圆筒形结构,内部设置有多层炼焦炉砖。
炼焦炉通常采用非直接加热方式,即在炉外通过热交换装置将燃烧产生的高温煤气输送到炼焦炉内以加热煤炭。
在炼焦炉的下方放有装料器,用来将细磨后的煤炭均匀地放入炉内。
炉内将煤炭按照时间和温度的不同区域分成干燥预热区、干馏区、焦化区和冷却区。
在干燥预热区,炉内温度逐渐升高,将煤炭中的水分蒸发掉。
同时,在干馏区,高温煤气通过煤炭层,引起煤炭内部的干馏反应。
这个过程将导致煤炭分子内部的结构发生改变,生成焦炭和煤气。
然后,在焦化区,煤炭内部的挥发分子和焦炭分子进一步分解。
这个区域的温度相对较高,可以使煤气中的可燃气体和焦油以及其他挥发分子分离出来。
这些煤气和液态产物被导出到后续处理装置中进行处理和分离。
最后,在冷却区,冷却气体被引入炼焦炉内,将焦炭迅速冷却。
冷却后的焦炭将被输送到焦炭处理装置进行筛分和包装。
总的来说,焦化厂炼焦工艺是一个复杂的过程,需要控制多个参数,如温度、压力和气体流量等。
这些参数的优化会影响煤炭的炼焦效率和焦炭质量。
同时,炼焦过程中产生的煤气也是重要的能源和化学原料,可以用于发电、供热和其他工业生产过程。
因此,焦化厂炼焦工艺的研究和改进对提高能源利用效率和环境保护具有重要意义。
焦化工艺技术发展概述_配煤炼焦篇_一_

括两部分内容 , 一是把该系统用于用煤和来煤计划 的制订和平衡 , 以缩短制订计划的时间和提高计划 的及时性和准确性。二是根据生产数据建立了焦炭 强度预测模型 , 并可以对人为给定的配煤方案进行 焦炭质量的评定。 国内原华东冶金学院 ( 现安徽 工业大学 ) 是 最早从事配煤炼焦研究及应用系统开发的科研院所 之一 , 自 20世纪九十年代以来先后与宝钢、马钢、 济钢、攀钢等企业合作开发了不同层次的配煤炼焦 技术应用及管理系统, 其中宝钢的配煤专家系统最 具代表性 , 其建立的焦炭质量预测系统较为精确, 为宝钢焦炭的长期高质稳定发挥了巨大的作用, 其 炼焦成本也有显著的下降。 近系统, 现已取 得阶段性成果。 2008 年 7 月份 , 本钢历时两年半研究 开发的 适合自身特点的配煤专家系统正式投入使用 , 该系 统解除了人工 计算管理的繁重 劳动, 实现 了在资 源、料场、配煤、炼焦和使用跟踪一体化的全方位 动态实时科 学管 理, 在 优 化焦 煤、肥 煤、 1 /3 焦 煤、瘦煤的配比的同时还提高了焦炭质量预测准确 率和焦炭质量的稳定性 , 是目前国内最完善的配煤 专家系统。
莱钢科技 代以来建设了许多炭化室高度大于 7 m 的大容积焦 炉 , 德国史韦根 ( Schw elgern) 焦化厂拥有当今世 界最大焦炉, 炭化室高达 8 43 m, 该焦炉为两座 70 孔 焦 炉年 产 焦 炭 250 万 , t 相 当 于 我 国普 通 4 3 m焦炉 8座 , 6 m 焦炉 4 5 座。 近年来 , 我国新建顶装焦炉大多数以 6 m 焦炉 为主, 2007 年我国新建投产的焦炉 41 座, 新增产 能 2 163 万 , t 其中炭化室高大于 6 m 大容积焦炉 (含 5 5 米捣固焦炉 ) 23座 , 产能 1435 万 , t 占新 增产能的 66 3 % 。 2008年和 2009 年, 我国每年新 建投产的焦炉都在 50 座以上 , 新增焦炭产能均在 3 000 万 t以上 , 其中顶装焦炉绝大多数为 6 m 以 上的大型焦炉。现我国 6 m 以上大容积机焦年产能 已在 1 亿吨左右 , 已接近当前总产能的 25 %。 2005年 , 鞍山焦耐院开发出 了具有自主知识 产权的 7 m 焦炉 ( 炭化室实际高度 6 98 m ) , 焦炉 炉体﹑焦炉机械﹑焦炉工艺和环保水平等诸多方面 与 6 m 焦炉相比都有了本质的改变, 达到了国际先 进水平且成熟可靠。
炼焦工艺及用煤技术发展

炼焦工艺及用煤技术发展•炼焦工艺概述•炼焦工艺流程与设备•炼焦用煤特性与质量要求•炼焦工艺技术创新与发展趋势•炼焦工艺与下游行业关系目•炼焦工艺及用煤技术发展展望录炼焦工艺是一种将煤进行高温干馏,生产出焦炭和煤气的过程。
炼焦工艺定义炼焦工艺具有高温、隔绝空气、加热缓慢等特点,使得煤在高温下充分热解,得到较多的焦炭和煤气。
炼焦工艺特点炼焦工艺定义与特点炼焦工艺是钢铁、化工等行业的重要能源来源,为这些行业提供热能和化学能。
提供能源提高资源利用率促进经济发展炼焦工艺可以提高煤炭资源的利用率,将原本难以直接利用的煤炭转化为有价值的能源和化工产品。
炼焦工艺的发展对于促进钢铁、化工等行业的经济发展具有重要作用。
03炼焦工艺的重要性0201炼焦工艺起源于19世纪中叶,随着钢铁工业的快速发展,炼焦工艺逐渐得到广泛应用。
起源与发展随着技术的不断进步,炼焦工艺逐渐向高效、环保、节能方向发展,出现了新型炼焦技术和装备。
技术进步未来炼焦工艺将朝着提高能源利用效率、减少环境污染、开发新型炼焦技术和产品等方向发展。
未来发展方向炼焦工艺的历史与发展备煤备煤是指将原煤破碎、筛分和干燥,使其粒度和水分达到炼焦要求的过程。
配煤配煤是将不同品质的煤按一定比例配合炼焦的过程,旨在获得最佳的炼焦效果和经济效益。
备煤与配煤炼焦炼焦是将配合好的煤装入焦炉,在隔绝空气的条件下加热到高温,经过热解、缩聚等反应,得到焦炭的过程。
熄焦熄焦是将刚刚从焦炉取出的红热焦炭用水或湿沙冷却,使其温度降低的过程。
炼焦与熄焦焦炉结构与设备焦炉结构焦炉是一种大型热工窑炉,由炉体、炉门、烟囱等组成,按加热方式可分为蓄热式和热回收式两种。
焦炉设备焦炉设备包括装煤车、推焦车、拦焦车、熄焦车等,用于完成装煤、推焦、拦焦和熄焦等操作。
集约化与智能化发展集约化发展随着技术的发展,炼焦行业正朝着集约化方向发展,通过提高设备效率和生产规模,降低生产成本和提高经济效益。
智能化发展智能化发展是炼焦行业的未来趋势,通过引入人工智能、大数据等先进技术,实现生产过程的自动化和智能化,提高生产效率和产品质量。
炼焦行业工艺技术

炼焦行业工艺技术炼焦行业是将煤炭转化为焦炭的过程,是钢铁工业的重要环节之一。
炼焦工艺技术涉及到多个环节,包括煤炭的预处理、炼焦炉的操作、煤气的处理等。
本文将从以下几个方面介绍炼焦行业的工艺技术。
首先,煤炭的预处理是炼焦过程的第一步。
煤炭的质量和性质会直接影响到焦炭的质量和产量。
在炼焦前,需要对煤炭进行筛分、破碎、干燥等处理,以确保煤炭具有合适的粒度和含水量。
此外,化学分析和物理性质测试也是必要的,以便确定煤炭的品质,并根据需要进行混配。
其次,炼焦炉的操作是关键环节之一。
炼焦炉是将煤炭加热至高温的设备,通过控制不同的工艺参数来实现煤炭的分解和转化。
炼焦炉的主要类型有焦炉、卧式炼焦炉和立式炼焦炉等。
在炼焦过程中,需要精确控制炉内的温度、压力和气体流量,确保煤炭得到充分热解和反应。
此外,炼焦炉内还需要合理布置回收设备,以最大限度地回收和利用产生的煤气和煤焦油。
再次,煤气的处理也是炼焦工艺技术中重要的一环。
炼焦过程中产生的煤气主要包含一氧化碳、氢气和烃类等有价值的成分。
为了提高能源利用效率和减少环境污染,需要对煤气进行处理,主要包括脱硫、脱氨、除尘等步骤。
通过脱硫和脱氨,可以减少煤气中的有害物质含量,提高其燃烧效果;通过除尘处理,可以减少煤气中的颗粒物和粉尘,保护环境。
最后,对于炼焦行业而言,技术创新永远是推动行业进步的动力。
随着科技的不断发展,炼焦行业也在不断探索新的工艺技术。
例如,高炉煤气的再利用、煤炭深度加工等都是当前炼焦行业研究的热点。
同时,智能化技术也逐渐应用于炼焦行业,通过自动控制系统和数据分析,实现工艺参数的精确控制和优化。
总之,炼焦行业是一个涉及到多个环节的工艺过程,需要综合运用多种技术手段。
通过煤炭的预处理、炼焦炉的操作、煤气的处理等环节,可以实现高效、环保的炼焦过程。
随着技术的不断进步,炼焦行业将会不断发展,为钢铁工业的发展做出更大的贡献。
煤炼焦工艺技术
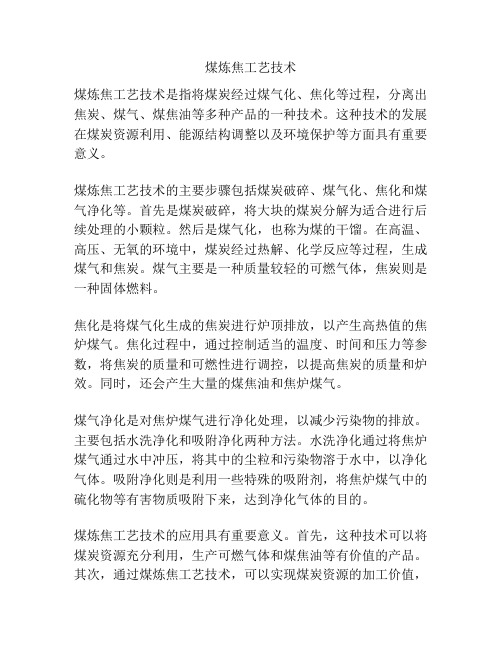
煤炼焦工艺技术煤炼焦工艺技术是指将煤炭经过煤气化、焦化等过程,分离出焦炭、煤气、煤焦油等多种产品的一种技术。
这种技术的发展在煤炭资源利用、能源结构调整以及环境保护等方面具有重要意义。
煤炼焦工艺技术的主要步骤包括煤炭破碎、煤气化、焦化和煤气净化等。
首先是煤炭破碎,将大块的煤炭分解为适合进行后续处理的小颗粒。
然后是煤气化,也称为煤的干馏。
在高温、高压、无氧的环境中,煤炭经过热解、化学反应等过程,生成煤气和焦炭。
煤气主要是一种质量较轻的可燃气体,焦炭则是一种固体燃料。
焦化是将煤气化生成的焦炭进行炉顶排放,以产生高热值的焦炉煤气。
焦化过程中,通过控制适当的温度、时间和压力等参数,将焦炭的质量和可燃性进行调控,以提高焦炭的质量和炉效。
同时,还会产生大量的煤焦油和焦炉煤气。
煤气净化是对焦炉煤气进行净化处理,以减少污染物的排放。
主要包括水洗净化和吸附净化两种方法。
水洗净化通过将焦炉煤气通过水中冲压,将其中的尘粒和污染物溶于水中,以净化气体。
吸附净化则是利用一些特殊的吸附剂,将焦炉煤气中的硫化物等有害物质吸附下来,达到净化气体的目的。
煤炼焦工艺技术的应用具有重要意义。
首先,这种技术可以将煤炭资源充分利用,生产可燃气体和煤焦油等有价值的产品。
其次,通过煤炼焦工艺技术,可以实现煤炭资源的加工价值,提高能源结构的多样性和可持续发展能力。
最后,这种技术有助于减少煤炭的能源排放,改善环境质量。
然而,煤炼焦工艺技术也面临一些挑战和问题。
首先,焦化过程会产生大量的煤焦油和焦炉煤气,对环境造成一定污染。
其次,煤炼焦工艺需要高温高压的条件,对设备和能源的要求较高。
此外,焦化过程中还会产生一定的固体废弃物和废水,对环境和土地资源造成一定影响。
因此,在推广和应用煤炼焦工艺技术的过程中,需要加强对煤炭资源全面利用和环境保护的意识,采取有效的措施减少污染物的排放和废弃物的处理。
此外,还需要进一步完善工艺技术和设备,提高煤炼焦的效率和质量。
焦化工艺流程简述和炼焦操作制度

焦化工艺流程简述和炼焦操作制度•焦化厂主工艺流程和车间配置:备煤:来煤的卸车和倒运至煤场储存,通过皮带将不同煤种的煤送配煤盘按一定配煤比混合,再送粉碎机粉碎后通过皮带送往焦炉煤塔。
炼焦:装煤车从煤塔取煤装入焦炉,生成焦炭和荒煤气,焦炭熄灭后筛除焦粉通过皮带送往炼铁;荒煤气送回收车间。
化产回收:经煤气鼓风机将荒煤气抽入系统,通过除油、脱硫脱氰、脱氨、脱苯等,生成比较洁净的焦炉煤气外送,同时得到不同的化学产品。
精制:对回收分离出的粗焦油进行深加工,得到不同的化工产品。
干熄焦:将焦炉推出的赤热红焦通过冷惰性气体(氮气)冷却至200度以下,转运至筛焦。
焦炭与炼焦用煤的准备•焦炭什么是焦炭:由烟煤、沥青或其他液体碳氢化合物为原料,在隔绝空气的条件下干馏得到的固体产物都可称为焦炭。
根据焦炭的用途分类:(根据原料煤的性质,干馏的条件不同)用于高炉炼铁的称为高炉焦,用于冲天炉熔铁的称为铸造焦;用于铁合金生产的称铁合金用焦,以及气化用焦、电石用焦等。
焦碳的一般性质:焦炭是一种质地坚硬,多孔、呈银灰色并有不同粗细裂纹的碳质固体块状材料,其相对真密度为1.8~1.95,堆积密度为400~520kg/m3焦炭的化学组成及高炉焦质量指标工业分析:水分、灰分、挥发分和固定碳(主要元素:C、H、O、N、P、S)水分:焦炭的水分与炼焦煤料的水分无关,也不取决于炼焦工艺条件,主要受熄焦方式的影响。
灰分:主要成分是SiO2和Al2O3。
挥发分:焦炭的挥发分是焦炭成熟程度的标志,与炼焦煤料和炼焦最终温度有关。
硫分:受炼焦煤料影响,使生铁的主要有害杂质。
磷分:含量较少,主要受炼焦煤料影响。
B、机械强度:我国采用米库姆转鼓实验方法测定焦炭的机械强度。
抗碎强度(俗称M40):焦炭在外力冲击下抵抗碎裂的能力称为焦炭的抗碎强度。
耐磨强度(M10):焦炭抵抗摩擦力破坏的能力,称为焦炭的耐磨强度。
C、筛分组成:焦炭块度>80mm、80~60mm、60~40mm、40~25mm各粒级百分比。
配煤炼焦工艺概述

配煤炼焦工艺概述目前,世界各国生产的焦炭,绝大部分都是在室式炼焦炉内生产的,并且多采用配煤炼焦的方法。
其工艺过程主要包括将炼焦用的几种原料煤按工艺要求进行粉碎、按适宜的比例进行配合、配合煤装炉炼焦和熄焦,其中原料煤的配合对生产符合质量要求的焦炭具有重要意义。
配煤的目的与意义高炉焦和铸造焦等要求灰分低、含硫少、强大、各向民性程度高。
在室式炼焦条件下,单种煤(焦煤除外)炼焦很难满足上述要求,各国煤炭资源也无法满足单种煤炼焦的需求,中国煤炭资源虽然十分丰富,但煤种和储量资源分布不均,因此必采用配煤炼焦。
所谓配煤就是将两种以上的单种煤料,按适当比例均匀配合,以求制得各种用途所要求的焦炭质量。
采用配煤炼焦,既可保证焦炭质量符合要求,又可合理利用煤炭资源,节约优质炼焦煤,同进增加炼焦化学产品产量。
配煤方案的制定是焦化厂生产技术管理的重要组成部分,也是焦化厂规划设计的基础,在确定配煤方案时,应遵循下列原则。
配合煤性质与本厂煤预处理工艺及炼焦条件相适应,焦炭质量按品种要求达到规定指标。
符合本地区煤炭资源条件,有利扩大炼焦煤源。
有利增加炼焦化学产品;防止炭化室中煤料结焦过程产生的侧膨胀压力超过炉墙极限负荷,避免推焦困难。
缩短煤源平均运距,便于调配车皮,避免煤车对流,在特殊情况下有一定调节余地。
来煤数量和质量稳定,最终达到生产满足质量要求的焦炭的同时,使企业取得可观的经济效益。
不同品种焦炭对配合煤的质量指标要求不同用途的焦炭,对配煤的质量指标要求不同,为保证炼出质量合格的焦炭,必须保证配煤的质量。
中国20世纪50年代初的配煤方案是以气煤、肥煤、焦煤和瘦煤四种煤为基础煤按照一定比例配合确定的。
但由于中国炼焦煤资源分布不均衡,不可能在所有地区满足四种煤配合的原则,因而开发了各种配煤技术如用配煤质量指标确定配煤方案。
在进行炼焦配煤操作时,对配合煤的主要质量指标要求包括:化学成分指标即灰分、硫分和磷含量,工艺性质指标即煤化度和黏结性,煤岩组分指标和工艺条件指标即水分、细度、堆密度等。
- 1、下载文档前请自行甄别文档内容的完整性,平台不提供额外的编辑、内容补充、找答案等附加服务。
- 2、"仅部分预览"的文档,不可在线预览部分如存在完整性等问题,可反馈申请退款(可完整预览的文档不适用该条件!)。
- 3、如文档侵犯您的权益,请联系客服反馈,我们会尽快为您处理(人工客服工作时间:9:00-18:30)。
2010 年 2月
是较早使用捣固炼焦工艺的国家之一。原苏联自从 1989 年开始将一个顶装焦炉改造 为捣固炼焦炉以 后, 也开始在其高挥发分煤矿地区采用捣固炼焦工 艺。波兰由于其国内挥发分高的煤源比较多 , 适合 炼焦的煤源不太丰富, 因此也大量采用捣固工艺。 另外印度、法国、捷克、罗马尼亚等国也大量采用 捣固炼焦技术。 6 米的大型捣固焦炉在 20 世纪七 十年代由西德开发并在西德萨尔堡煤矿焦化厂投入 使用。 国内捣固焦炉的 使用已有近 百年的历 史, 20 世纪在很长的一段时期内捣固炼焦技术在国内没有 取得显著的进 展, 只占整个 炼焦能力的很 小一部 分。 21 世纪初鞍山焦耐院、化二 院相继开发成功 了 4米 3 捣固焦炉和 5 米 5捣固焦炉, 2006 年, 鞍 山焦耐院又开发出了当今世界最高的 6 25 米捣固 焦炉 , 它使我国捣固炼焦大型化技术迈向一个新台 阶。 虽然我国煤炭资源比较丰富 , 但炼焦煤资源相 对较少, 强粘结性煤资源更加稀缺。近几年 , 我国 炼焦能力的超常发展, 使主焦煤供应紧上加紧, 国 际市场主焦煤的价格也节节上扬 , 这些均加速了我 国捣固炼焦的普及。 1997 年之前, 我国只在大连、 抚顺和镇江等建有炭化室高 3 2 m 和 3 8 m 小型捣 固焦炉, 总计不到 20 座, 焦炭产能仅有 200 多万 吨, 而到 2009 年我国投产的 捣固焦炉已超过 360 座, 年产能约 1 亿吨 ; 本世纪我国新建的捣固焦炉 大多数为 4 米 3 以上, 自 2000 年我国开发了炭化 室高 4 3 m、宽 500 mm 捣固焦炉, 2002 年 8 月全 国第一座炭化室高 4 3 m 的捣固焦炉在山西省临汾 市同世达实业有限公司投产以来 , 因其技术成熟、 效果好, 在全国很快推广 ; 2005 年 8 月 , 景德镇 焦化煤气总厂将炭化室高 4 3 m、宽 450 mm 的 80 型顶装焦炉改造成捣固焦炉 , 拉开了我国 4 3 m 顶 装焦炉改造成捣固焦炉的序幕。 2006 年底 , 5 5 m 的捣固焦炉在云南曲靖建成投产 , 在全国掀起了建 设 5 5 m 捣固焦炉的热潮 , 目前 11 家企业相继投 产或正在建设 5 5 m 捣固焦炉。 2007 年 6 月, 中 冶焦耐公司总承包了河北唐山市佳华公司的炭化室 高 6 25 m 世界最高的捣固焦炉的建设 , 并于 2009 年 3 月份出焦 , 这标致着我国大型捣固焦炉技术达 到了国际先进水平。目前, 昆钢、莱钢和旭阳也已 决定建设 6 25 m 捣固焦炉。 7
括两部分内容 , 一是把该系统用于用煤和来煤计划 的制订和平衡 , 以缩短制订计划的时间和提高计划 的及时性和准确性。二是根据生产数据建立了焦炭 强度预测模型 , 并可以对人为给定的配煤方案进行 焦炭质量的评定。 国内原华东冶金学院 ( 现安徽 工业大学 ) 是 最早从事配煤炼焦研究及应用系统开发的科研院所 之一 , 自 20世纪九十年代以来先后与宝钢、马钢、 济钢、攀钢等企业合作开发了不同层次的配煤炼焦 技术应用及管理系统, 其中宝钢的配煤专家系统最 具代表性 , 其建立的焦炭质量预测系统较为精确, 为宝钢焦炭的长期高质稳定发挥了巨大的作用, 其 炼焦成本也有显著的下降。 近年来, 鞍山中钢热能研究院与武钢合作开发 以煤岩学为主要理论指导的配煤专家系统, 现已取 得阶段性成果。 2008 年 7 月份 , 本钢历时两年半研究 开发的 适合自身特点的配煤专家系统正式投入使用 , 该系 统解除了人工 计算管理的繁重 劳动, 实现 了在资 源、料场、配煤、炼焦和使用跟踪一体化的全方位 动态实时科 学管 理, 在 优 化焦 煤、肥 煤、 1 /3 焦 煤、瘦煤的配比的同时还提高了焦炭质量预测准确 率和焦炭质量的稳定性 , 是目前国内最完善的配煤 专家系统。
莱钢科技
2010 年 2月
焦化工艺技术发展概述
孙业新
1
配煤炼焦篇 ( 一 )
2
苑
路
邓
群
2
( 1 技术研发中心
摘
2 焦化厂 )
要: 介绍了国内外配煤炼焦技术的发展和应用情况, 并对国外前沿的炼焦新技术的开发 新技术 应用 开发
情况作了介绍 。 关键词: 配煤炼焦
0 前言
焦化是煤化工产业的重要组成部分, 近年来 , 伴随着我国钢铁工业的高速发展, 其工艺技术装备 水平得到了全方位的提高 ; 可以预见 , 高炉炼铁工 艺在未来很长一段时期内 ( 在国内至少 30 年 ) 不 会退出历史舞台的主流, 这将为焦化行业生存发展 提供了强有力的支撑 , 但受日益紧缺的优质炼焦煤 资源以及其它诸多因素的影响 , 其工艺技术的革新 显得越发重要。 现有形式的焦炉大约产生于 100 年多年前。其 间贯穿的工艺技术课题是在煤特性的制约中寻求以 下目的 : 1) 提高生产能力 (如高效操作化, 焦炉大型 化) 2) 提高热效率 ( 如设置蓄热室 ) 3) 回收 副产 物 ( 如煤 化学 及焦 炉煤气 的利 用) 4) 节约资源、环境友好 ( 如科学配煤技术和 新炼焦技术的研究应用 ) 不断追求以上目的的结果致使国内外配煤炼焦 技术经历了一个长期进步发展过程, 现在主要体现 在科学配煤专家系统的开发应用、顶装焦炉的超大 型化、捣固焦炉的推广及大型化、干熄焦技术的推 广及大型化、煤调湿技术的发展及推广等方面 ; 此 外 , 还有一批前沿技术正在研究开发。下面就先进 技术的应用及新技术的研究发展情 况作进一步介 绍。
孙业新, 等: 焦化工艺技术发展概述
莫索 夫方法的基础上 , 美国学 者夏皮洛 1961年进一步 发展和 完善了 这种煤 岩配煤 方法。 该法的特点是以煤岩组成和活性成分反射率为基础 资料, 也把煤岩显微组分分为两大类 : 活性组分 = 镜质组 + 壳质组 + 1 / 3半镜质组; 惰性组分 = 惰质 组 + 2 / 3半镜质组 + 矿物。它的主要发展是把活性 组分 ( 主要是镜质组 ) 以 0 1% 反射率为间隔 , 从 0 3 % ~ 2 1 % 分成 18 类 , 以此标志煤的煤化程度 , 引入强度指数 SI 和组成平衡指数 CB I 两个煤岩参 数作为配煤指标。其中 SI 标志活性组分的平均质 量 , 组成平衡指数 CB I是标志配煤中惰性组分含量 适合与 否的一个 指标, 夏 皮洛以 S I 、 CB I 参数为 纵、横坐标 , 作出一组等强度曲线, 预测值与焦炉 实测值相当吻合 , 其相关系数可达 0 93 , 可较好 的指导配煤。 1 1 3 周师庸煤岩配煤方法 我国周师庸教授于 20 世纪 80 年代初在对新疆 钢铁公司的配煤预测焦炭强度的研究中, 采用镜质 组反射率作为煤化度指标 , 以惰性组分含量作为煤 岩组成指标 , 通过试验选择罗加指数或容惰能力作 为煤的还原程度指标。基于此原理模型, 新疆钢铁 公司和酒泉钢铁公司经过系统的试验 , 建立了预测 方程, 其相关系数 M 40可达 0 86 , M 10可达 0 94 。 1 2 焦炭强度预测及配煤专家系统的开发应用 1 2 1 焦炭强度预测 焦炭强度预测进展大体可分为两个阶段, 第一 阶段是焦炭 的机械强 度的预测。第二阶 段是 CRI 和 CSR 作为焦炭质量指标的预测。 目前, 大多数预测模型所涉及的参数都包括三 个方面 , 1) 用镜质组平均最大反射率作为煤化度 指标反映焦炭的显微结构 ; 2) 用基氏流动度反映 焦炭的气孔结构 ; 3) 用焦炭灰分组成衡量对碳素 溶解反应催化作用。这就把配合煤的粘结性、结焦 性和煤的灰分组成对焦炭反应性和反应后强度的影 响关联起来, 对焦炭的 CR I和 CSR 进行预测。值 得注意的是 , 进一步的预测方法应该把炼焦工艺条 件作为因素加以关联 , 才能使得预测方法更完善 , 预测结果更准确。以准确焦炭质量预测模型为基础 就可以进一步开发出具有实际应用价值的配煤专家 系统。 1 2 2 国内外科学配煤专家系统开发应用情况 日本川崎 钢铁公司开发了以减少焦炭质量波 动、降低成本为主要目的配煤专家系统。该系统包 6
2 顶装焦炉的超大型化
2 1 焦炉大型化的技术优点 1) 劳动生产率提高。由于每班每人处理的煤 量和生产的焦炭多, 劳动生产率高 , 生产成本低, 更具有竞争能力; 2) 减轻了环 境污染。由于密封 面长度减 少, 大大减少了推焦装煤和熄焦时散发的污染物 , 同时 也节约了用于环保设施的投资和操作费用; 3) 有利于改善焦炭质量。大型化后, 由于堆 密度的增大 , 有利于焦炭质 量的提高或多 配弱粘 煤; 4) 热损失少, 热效率高。由于吨煤的散热面 减少 , 热损失降低 , 热效率提高 ; 5) 由于炉组数减少 , 占地面积相应减少; 6) 设计寿命长 , 维修费用低。 2 2 国内外焦炉大型化概况 焦炉大型化炭化室加宽及加高、提高单孔炭化 室产焦量是焦炉的发展方向。国外自 20 世纪 80 年
莱钢科技 代以来建设了许多炭化室高度大于 7 m 的大容积焦 炉 , 德国史韦根 ( Schw elgern) 焦化厂拥有当今世 界最大焦炉, 炭化室高达 8 43 m, 该焦炉为两座 70 孔 焦 炉年 产 焦 炭 250 万 , t 相 当 于 我 国普 通 4 3 m焦炉 8座 , 6 m 焦炉 4 5 座。 近年来 , 我国新建顶装焦炉大多数以 6 m 焦炉 为主, 2007 年我国新建投产的焦炉 41 座, 新增产 能 2 163 万 , t 其中炭化室高大于 6 m 大容积焦炉 (含 5 5 米捣固焦炉 ) 23座 , 产能 1435 万 , t 占新 增产能的 66 3 % 。 2008年和 2009 年, 我国每年新 建投产的焦炉都在 50 座以上 , 新增焦炭产能均在 3 000 万 t以上 , 其中顶装焦炉绝大多数为 6 m 以 上的大型焦炉。现我国 6 m 以上大容积机焦年产能 已在 1 亿吨左右 , 已接近当前总产能的 25 %。 2005年 , 鞍山焦耐院开发出 了具有自主知识 产权的 7 m 焦炉 ( 炭化室实际高度 6 98 m ) , 焦炉 炉体﹑焦炉机械﹑焦炉工艺和环保水平等诸多方面 与 6 m 焦炉相比都有了本质的改变, 达到了国际先 进水平且成熟可靠。