精益生产中七大浪费
精益生产七大浪费

精益生产七大浪费在当今竞争激烈的市场环境中,企业都在努力追求高效、高质量和低成本的生产模式。
精益生产作为一种先进的生产理念和方法,旨在消除各种浪费,提高生产效率和质量,增强企业的竞争力。
精益生产中,识别和消除七大浪费是关键的环节。
一、过度生产的浪费过度生产是指生产出超出客户需求或比需求时间更早的产品。
这种浪费不仅占用了大量的资金、库存空间和生产资源,还可能导致产品过时、质量下降以及增加管理成本。
例如,一家服装厂预计某个款式的衣服会畅销,于是大量生产,结果市场需求发生变化,导致大量库存积压,这些积压的服装不仅占用了仓库空间,还可能因为长时间存放而出现质量问题,最终只能低价处理或者报废,造成了巨大的经济损失。
造成过度生产的原因往往是企业对市场需求的预测不准确,或者为了追求设备的高利用率而盲目生产。
要避免过度生产的浪费,企业需要建立以客户需求为导向的生产计划,加强市场调研和预测,采用灵活的生产方式,如拉动式生产,根据客户的实际订单来安排生产。
二、库存的浪费库存包括原材料、在制品和成品的库存。
过多的库存会掩盖生产过程中的问题,如质量缺陷、设备故障、生产不均衡等。
库存还会占用大量的资金,增加仓储成本和管理成本,同时也增加了产品损坏、过期和变质的风险。
比如,一家电子厂为了防止原材料供应中断,大量囤积电子元件,结果市场上出现了新的技术和产品,导致这些囤积的元件无法使用,变成了废品。
此外,大量的在制品库存也会导致生产周期延长,降低生产效率。
要减少库存的浪费,企业需要优化供应链管理,与供应商建立紧密的合作关系,确保原材料的及时供应。
同时,通过优化生产流程,实现生产的均衡化和准时化,减少在制品库存。
三、搬运的浪费搬运是指在生产过程中对物料、产品的不必要的移动和运输。
不合理的工厂布局、过长的生产线、过多的中间存储环节等都会导致搬运的浪费。
搬运不仅增加了人力和物力的消耗,还可能导致产品的损坏和质量问题。
例如,一家汽车制造企业,零部件需要经过多次搬运才能到达装配线,在搬运过程中,不仅耗费了大量的时间和人力,还容易造成零部件的磕碰和划伤。
精益生产之七大浪费

精益生产之七大浪费精益生产是一种以最小化浪费为目标,通过优化流程和提高效率来提高产品质量和客户满意度的管理方法。
在精益生产中,有七大浪费被认为是造成资源浪费和低效率的主要原因,它们是:过产、等待、运输、不合格、运动、库存和过程错误。
1. 过产(Overproduction):过产是指在没有实际需求的情况下进行生产活动,导致产品过度积压和资源浪费。
这不仅会给企业带来高成本,还会增加库存量和缩短产品寿命。
2. 等待(Waiting):等待是指生产过程中出现的不必要的停顿和延迟。
这可能是由于设备故障、物料不足、工人缺席等原因导致的。
等待会降低生产效率,增加生产周期,延迟产品交付。
3. 运输(Transportation):运输是指不必要的材料和产品的长距离运输。
这使得运输成为了一个独立的过程,需要额外的时间和资源。
这些额外的步骤可能会导致物料的损坏、遗失和延迟,进一步增加了生产成本。
4. 不合格(Defects):不合格是指生产中出现的错误、缺陷和质量问题。
不合格的产品需要进行修正、重新制造或报废,这增加了不必要的时间和资源。
这不仅会导致生产延误,还会降低产品质量和客户满意度。
5. 运动(Motion):运动是指工人在生产过程中进行不必要的移动和动作。
这可能是由于生产线布局不合理、工具和设备摆放不当等原因导致的。
这增加了工人的体力消耗,降低了生产效率,也增加了人为错误的可能性。
6. 库存(Inventory):库存是指未经加工的原材料和半成品的储存量。
过多的库存可能会导致资金占用、过期损失、储存空间浪费等问题。
此外,库存过多也会隐藏潜在的问题,如质量问题和需求变化的风险。
7. 过程错误(Processing):过程错误是指生产过程中出现的不必要的重复、增补和调整。
这可能是由于不合理的工艺流程、工具和设备的不良设计等原因导致的。
这会增加生产成本和时间,降低生产效率和产品质量。
有效管理和消除以上七大浪费是精益生产的关键。
精益生产的七大浪费概述

精益生产的七大浪费概述精益生产是一种管理哲学和方法论,旨在通过消除浪费来提高生产效率和质量。
在精益生产中,有七大浪费被广泛认可,包括:1. 运动:指的是任何不必要的移动或行动,例如工人需要频繁移动到不同的工作区域以完成任务。
精益生产鼓励将工作站布置得合理,以减少不必要的运动,从而提高效率。
2. 待料:指的是生产过程中等待原材料、工具或设备供应的时间。
这种等待会导致生产线停滞,降低生产效率。
精益生产鼓励将供应链优化,以减少待料时间。
3. 过产量:指的是生产超过需求的产品,或者在产品的某个阶段生产过多的零件。
过产量会导致库存积压、成本上升,甚至可能导致产品过期。
精益生产鼓励按需生产,以避免过产量的浪费。
4. 等待:指的是生产过程中因为等待其他任务完成而导致的停滞时间。
这种等待会导致生产线的延迟和低效。
精益生产鼓励优化工艺流程,减少等待时间。
5. 过度加工:指的是对产品进行超出需求或规格要求的加工步骤。
过度加工会增加生产成本和时间。
精益生产鼓励消除不必要的加工步骤,以提高效率和降低成本。
6. 错误:指的是在生产过程中出现的错误或瑕疵,例如产品缺陷或错误装配。
这些错误会导致废品产生和重工成本增加。
精益生产鼓励通过质量控制和错误预防来减少错误的发生。
7. 运输:指的是产品或物料在生产过程中频繁移动或运输的浪费。
这种浪费会增加时间和成本,同时也增加了损坏产品的风险。
精益生产鼓励优化布局和流程,减少不必要的运输。
通过有效地识别和消除这七大浪费,精益生产能够提高生产效率、降低成本,并提供更高质量的产品。
精益生产鼓励组织和管理层始终关注价值流,并持续改进以实现更高的效率和竞争力。
精益生产是一种以消除浪费为核心的管理哲学和方法论,旨在提高生产效率和质量。
在精益生产中,有七大浪费被广泛认可,并成为了改善生产流程的重要依据。
这七大浪费是运动、待料、过产量、等待、过度加工、错误和运输。
首先,运动是指不必要的移动或行动。
在生产过程中,员工频繁移动到不同的工作区域以完成任务会增加生产时间和劳动成本。
精益生产七大浪费
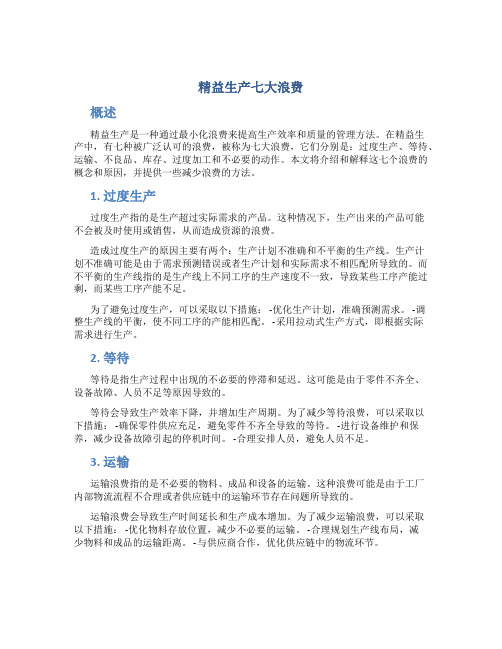
精益生产七大浪费概述精益生产是一种通过最小化浪费来提高生产效率和质量的管理方法。
在精益生产中,有七种被广泛认可的浪费,被称为七大浪费,它们分别是:过度生产、等待、运输、不良品、库存、过度加工和不必要的动作。
本文将介绍和解释这七个浪费的概念和原因,并提供一些减少浪费的方法。
1. 过度生产过度生产指的是生产超过实际需求的产品。
这种情况下,生产出来的产品可能不会被及时使用或销售,从而造成资源的浪费。
造成过度生产的原因主要有两个:生产计划不准确和不平衡的生产线。
生产计划不准确可能是由于需求预测错误或者生产计划和实际需求不相匹配所导致的。
而不平衡的生产线指的是生产线上不同工序的生产速度不一致,导致某些工序产能过剩,而某些工序产能不足。
为了避免过度生产,可以采取以下措施: -优化生产计划,准确预测需求。
-调整生产线的平衡,使不同工序的产能相匹配。
-采用拉动式生产方式,即根据实际需求进行生产。
2. 等待等待是指生产过程中出现的不必要的停滞和延迟。
这可能是由于零件不齐全、设备故障、人员不足等原因导致的。
等待会导致生产效率下降,并增加生产周期。
为了减少等待浪费,可以采取以下措施: -确保零件供应充足,避免零件不齐全导致的等待。
-进行设备维护和保养,减少设备故障引起的停机时间。
-合理安排人员,避免人员不足。
3. 运输运输浪费指的是不必要的物料、成品和设备的运输。
这种浪费可能是由于工厂内部物流流程不合理或者供应链中的运输环节存在问题所导致的。
运输浪费会导致生产时间延长和生产成本增加。
为了减少运输浪费,可以采取以下措施: -优化物料存放位置,减少不必要的运输。
-合理规划生产线布局,减少物料和成品的运输距离。
-与供应商合作,优化供应链中的物流环节。
4. 不良品不良品是指在生产过程中产生的不合格产品。
不良品可能是由于工艺问题、材料质量不合格、操作失误等原因导致的。
不良品会增加返工和废品处理的成本,并降低生产效率。
精益生产之七大浪费
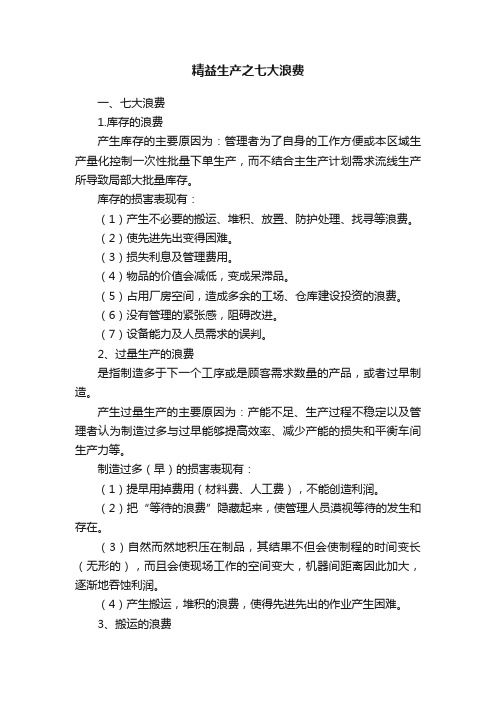
精益生产之七大浪费一、七大浪费1.库存的浪费产生库存的主要原因为:管理者为了自身的工作方便或本区域生产量化控制一次性批量下单生产,而不结合主生产计划需求流线生产所导致局部大批量库存。
库存的损害表现有:(1)产生不必要的搬运、堆积、放置、防护处理、找寻等浪费。
(2)使先进先出变得困难。
(3)损失利息及管理费用。
(4)物品的价值会减低,变成呆滞品。
(5)占用厂房空间,造成多余的工场、仓库建设投资的浪费。
(6)没有管理的紧张感,阻碍改进。
(7)设备能力及人员需求的误判。
2、过量生产的浪费是指制造多于下一个工序或是顾客需求数量的产品,或者过早制造。
产生过量生产的主要原因为:产能不足、生产过程不稳定以及管理者认为制造过多与过早能够提高效率、减少产能的损失和平衡车间生产力等。
制造过多(早)的损害表现有:(1)提早用掉费用(材料费、人工费),不能创造利润。
(2)把“等待的浪费”隐藏起来,使管理人员漠视等待的发生和存在。
(3)自然而然地积压在制品,其结果不但会使制程的时间变长(无形的),而且会使现场工作的空间变大,机器间距离因此加大,逐渐地吞蚀利润。
(4)产生搬运,堆积的浪费,使得先进先出的作业产生困难。
3、搬运的浪费不必要的搬运零件和产品,例如两个连续的生产工序,将产品在完成一个工序后,先运到仓库,然后再运到下一个工序。
较理想的情况是让两个工序的位置相邻,以便使产品能够从一个工序立即转到下一个工序。
产生搬运的主要原因为:车间布置采用批量生产,依工作站为区别的集中的水平式布置(也就是分工艺流程批量生产),无连续流生产的观念。
4、等待的浪费在生产过程中,操作员或者设备空闲。
产生等待的主要原因为:作业不平衡,安排作业不当、待料、品质不良等。
5、多余动作的浪费操作员所作的没有增值的动作,例如找零件,找工具、文件等。
产生多余动作的主要原因为:生产场地规划不好,生产模式设计不周全,生产动作不规范统一。
6、缺陷的浪费不良品和废品。
精益生产概述之七大浪费

精益生产概述之七大浪费精益生产是一种旨在消除浪费、提高效率和质量的管理方法。
在这个方法中,七大浪费被认为是导致资源浪费和低效率的主要原因。
因此,精益生产的目标是通过识别和消除这些浪费来实现生产过程的优化。
以下是精益生产中七大浪费的概述:1. 运输浪费(Transportation):指在生产过程中不必要的物料、产品或信息的运输。
这种浪费可能是由于生产线布局不合理、物料存放位置不当等导致的。
2. 库存浪费(Inventory):指在生产过程中过多的存储物料、产品或信息。
高库存不仅占用了宝贵的空间,还导致资金被束缚,增加了物料管理的复杂性。
3. 过程浪费(Process):指生产过程中的任何不必要的任务、步骤或动作。
这些浪费可能是由于不必要的检查、重复的手动操作或不必要的文件处理等原因造成的。
4. 动作浪费(Motion):指工人在生产过程中做出的不必要的动作或移动。
这些浪费可能包括在工作站之间来回移动、长时间等待或不必要的物料搬运等。
5. 等待浪费(Waiting):指在生产过程中由于等待而导致的停滞或不必要的停机时间。
这种浪费可能是由于生产过程中的停机、设备故障或不平衡的任务分配等原因造成的。
6. 蒙眬浪费(Over-processing):指在生产过程中对产品进行过度加工或处理,超出了产品要求或客户需求的范围。
这种过度加工不仅浪费资源,还可能导致产品成本增加。
7. 缺陷浪费(Defects):指生产过程中产生的不合格产品或错误。
这些缺陷可能导致产品退货、修复或重新制造,增加了成本和时间。
通过识别和消除这七大浪费,精益生产能够提高生产效率和质量,减少资源浪费和成本。
这种方法不仅适用于制造业,也可应用于服务业和其他组织。
通过优化流程,改进布局和减少浪费,组织可以实现更高的生产效率和更满意的客户。
精益生产是一个追求效率和质量的管理方法,它的目标是通过消除七大浪费来优化生产过程。
该方法最初由日本丰田汽车公司引入,并且已被广泛应用于不同的行业和组织。
精益生产中的七大浪费及改善方法
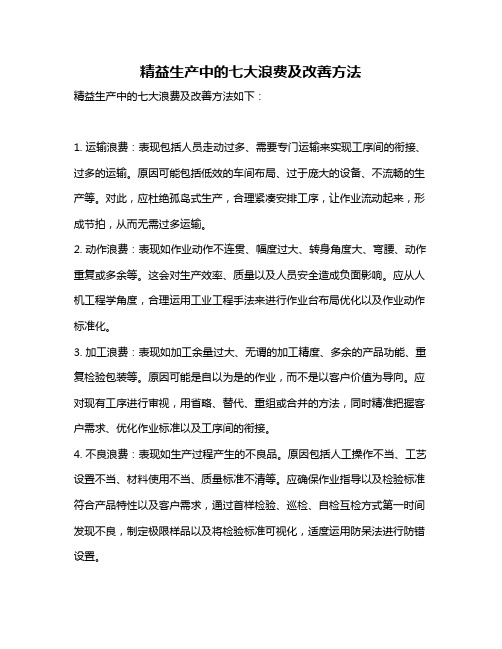
精益生产中的七大浪费及改善方法精益生产中的七大浪费及改善方法如下:1. 运输浪费:表现包括人员走动过多、需要专门运输来实现工序间的衔接、过多的运输。
原因可能包括低效的车间布局、过于庞大的设备、不流畅的生产等。
对此,应杜绝孤岛式生产,合理紧凑安排工序,让作业流动起来,形成节拍,从而无需过多运输。
2. 动作浪费:表现如作业动作不连贯、幅度过大、转身角度大、弯腰、动作重复或多余等。
这会对生产效率、质量以及人员安全造成负面影响。
应从人机工程学角度,合理运用工业工程手法来进行作业台布局优化以及作业动作标准化。
3. 加工浪费:表现如加工余量过大、无谓的加工精度、多余的产品功能、重复检验包装等。
原因可能是自以为是的作业,而不是以客户价值为导向。
应对现有工序进行审视,用省略、替代、重组或合并的方法,同时精准把握客户需求、优化作业标准以及工序间的衔接。
4. 不良浪费:表现如生产过程产生的不良品。
原因包括人工操作不当、工艺设置不当、材料使用不当、质量标准不清等。
应确保作业指导以及检验标准符合产品特性以及客户需求,通过首样检验、巡检、自检互检方式第一时间发现不良,制定极限样品以及将检验标准可视化,适度运用防呆法进行防错设置。
5. 等待浪费:表现如人员(以及设备)在等待,或者有时忙、有时闲的不均衡现象。
原因如生产线品种切换、工作量少、时常缺料、设备闲置等。
应实施生产均衡化,快速换模技术的运用,全员生产性防护,多技能工,消除不良浪费,提升供应商水准。
6. 过量生产:这是常被视为最大的浪费。
其结果导致库存、资金的占用以及潜在的报废风险。
应形成一个流、节拍化生产。
“一个流生产”是指从毛坯投入成品产出的整个制造加工过程,零件始终处于不停滞、不堆积、不超越的状态。
每道工序加工完一个制件后立即流到下一工序;工序间的在制品数量不超过前工序的装夹数量。
零件的运动不间断、不超越、不落地。
只有合格的产品才允许往下一道工序流。
节拍化生产要求是需求节拍与生产节拍平衡。
精益生产七大浪费

精益生产七大浪费精益生产是一种管理哲学和方法论,旨在通过消除浪费、提高效率和优化价值流程来提升生产效能。
而精益生产中的七大浪费是指那些没有为产品或服务的生产和提供增加价值的活动或过程。
本文将围绕这七大浪费展开,分别进行详细解析和说明。
1. 运输浪费运输浪费是指物资、产品或信息在生产过程中的多余传递和搬运。
例如,在生产线上,如果没有优化工作站的布局,会导致物料的来回搬运、多余的运输过程,加大了时间和成本的浪费。
解决运输浪费的方法包括优化生产线布局,减少物料的运输距离和传递次数;采取合理的物流管理措施,确保物料的及时供应和准确投放;建立合理的生产计划,避免产生过多的中间库存。
2. 库存浪费库存浪费是指过多的原材料、在制品或成品存放在生产过程中所产生的时间、资金和空间的浪费。
为了解决库存浪费,可以采取以下措施:建立精确的需求预测和生产计划,避免过多的生产;与供应商建立稳定的合作关系,减少库存的积压;优化生产流程,避免产生过多的在制品。
3. 过程浪费过程浪费是指在生产过程中,因为制造步骤没有得到充分合理地优化,导致时间、资源和能量的浪费。
为了减少过程浪费,可以采取以下方法:优化生产流程,减少不必要的工序和步骤;引入先进的生产技术和设备,提高生产效率;提供员工培训和改善活动,增强员工的工作技能和问题解决能力。
4. 动作浪费动作浪费是指在生产过程中,工人或操作人员因为工作站布局不合理、工具不合适等原因,需要进行过多的移动、等待和修复等动作,从而造成时间和能量的浪费。
解决动作浪费的方法包括:对工作站进行优化布局,让操作人员能够更便捷地完成工作;提供适合的工具和设备,减少不必要的动作和劳动强度;建立高效的沟通和协作机制,减少信息传递和等待的时间。
5. 过度加工浪费过度加工浪费是指产品或服务的加工、处理或处理过程中,因为超出必要的要求或标准,而导致时间、资源和能量的浪费。
为了解决过度加工浪费,可以采取以下措施:确立明确的产品标准和质量要求,避免过度加工和处理;加强质量管理和监督,提高产品或服务的质量稳定性;进行产品优化和工艺改进,减少不必要的加工环节。
- 1、下载文档前请自行甄别文档内容的完整性,平台不提供额外的编辑、内容补充、找答案等附加服务。
- 2、"仅部分预览"的文档,不可在线预览部分如存在完整性等问题,可反馈申请退款(可完整预览的文档不适用该条件!)。
- 3、如文档侵犯您的权益,请联系客服反馈,我们会尽快为您处理(人工客服工作时间:9:00-18:30)。
現場 浪費 七要素之 四 動作的浪費: 兩手空閑,單手空閑,作業動作突然停止, 作業動作過大,左右手交換,步行過多,轉 身的角度太大,移動中變換”狀態”,不明 技巧,伸背動作,變腰動作以及重復動作和 不必要的動作等,這些動作的浪費造成了 時間和體力上的不必要消耗.
現場 浪費 七要素之 五 加工的浪費: 加工的浪費也叫過分加工的浪費,主要包 含兩層含義:第一是多余的加工和過分精 確的加工,例如實際加工精度過高造成資 源浪費,第二是需要多余的作業時間和輔 助設備,還要增加生產用電,氯壓,油等能 源的浪費,另外還增加了管理的工時.
現場 浪費 七要素之 六 庫存的浪費: 有些企業由于生產能力比較強大,為了不 浪費生產能力而不中斷生產,增加了制品, 使得制品周期變短,空間變大,還增加了搬 運,堆積的浪費,此外,制造過多或過早,會 帶來龐大的庫存量,利息負擔增加,不可避 免地增加了貶值的風險.
現場 浪費 七要素之 七 管理的浪費 管理浪費指的是問題發生以后,管理人員 才采取相應的對策來進行補救而產生的 額外浪費,管理浪費是由于事先管理不到 位而造成的問題,科學的管理應該是具有 相當的預見性,有合理的規划,并在事情的 推進過程中加強管理,控制和反饋,這樣就 可以在很大程度上減少管理浪費現象的 發生.
制作:馮蕭輝
現場浪費七要素 現場 浪費 七要素 1.等待的浪費 2.搬運的浪費 3.不良品的浪費 4.動作的浪費 5.加工的浪費 6.在庫的浪費 7.制造過多(早)的浪費
現場 浪費 七要素之 一 等待的浪費: (閑視的浪費) 閑著沒事,等著下一動作的來臨.作業 平衡,安排作業不當.缺料,等料,待料,品質 不良所造成.
現場 浪費 七要素之 二 搬運的浪費: 水線化生產觀念.
現場 浪費 七要素之 三 不良修理的浪費: 所謂不良,修理的浪費,指的是由于工廠 內出殃不良品,需要進行處置的時間,人力, 物力上的浪費,以及由此造成的相關損失. 這類浪費具體包括:材料的損失,不良品變 成廢品;設備,人員和工時的損失,額外的 修復,鑒別,追加檢查的損失;有時需要降 低處理產品,或者由于耽誤出貨而導致工 廠信譽的下降.