陶瓷生产技术及设备
陶瓷生产工艺技术概况

陶瓷生产工艺技术概况第一节陶瓷生产及原料概况陶瓷是指用粘土、石英等天然硅酸盐原料经过粉碎、成型、煅烧等过程而得到的具有一定形状和强度的制品。
主要指日常生活中常见的日用陶瓷和建筑陶瓷、电瓷等。
陶瓷的生产发展经历了漫长的过程,从传统的日用陶瓷、建筑陶瓷、电瓷发展到今天的氧化物陶瓷、压电陶瓷、金属陶瓷等特种陶瓷,虽然所采用的原料不同,但其基本生产过程都遵循着“原料处理一成型一煅烧”这种传统方式,因此,陶瓷可以认为是用传统的陶瓷生产方法制成的无机多晶产品。
陶瓷制品的品种繁多,它们之间的化学成分、矿物组成、物理性质、以及制造方法,常常互相接近交错,无明显的界限,而在应用上却有很大的区别。
因此很难硬性地归纳为几个系统,详细的分类法各家说法不一,到现在国际上还没有一个统一的分类方法。
整理汇编如下:一、根据陶瓷原料杂质的含量、和结构紧密程度把陶瓷制品分为陶质、瓷质和炻质三类1、陶质制品为多孔结构,吸水率大(低的为9%—12%,高的可达18% —22%)、表面粗糙。
根据其原料杂质含量的不同及施釉状况,可将陶质制品分为粗陶和细陶,又可分为有釉和无釉。
粗陶一般不施釉,建筑上常用的烧结粘土砖、瓦均为粗陶制品。
细陶一般要经素烧、施釉和釉烧工艺,根据施釉状况呈白、乳白、浅绿等颜色。
建筑上所用的釉面砖(内墙砖)即为此类。
2、炻质制品介于瓷质制品和陶质制品之间,结构较陶质制品紧密,吸水率较小。
炻器按其坯体的结构紧密程度,又可分为粗炻器和细炻器两种,粗炻器吸水率一般为4~/ 0—8%,细炻器吸水率小于2%,建筑饰面用的外墙面砖、地砖和陶瓷锦砖(马赛克)等均属粗炻器。
3、瓷质制品煅烧温度较高、结构紧密,基本上不吸水,其表面均施有釉层。
瓷质制品多为日用制品、美术用品等。
瓷器是陶瓷器发展的更高阶段。
它的特征是坯体已完全烧结,完全玻化,因此很致密,对液体和气体都无渗透性,胎薄处星半透明,断面呈贝壳状,以舌头去舔,感到光滑而不被粘住。
二、陶瓷可简单分为硬质瓷,软质瓷、特种瓷三大类1、硬质瓷(hard porcetain)具有陶瓷器中最好的性能。
高性能陶瓷的制造技术开发与生产方案(一)
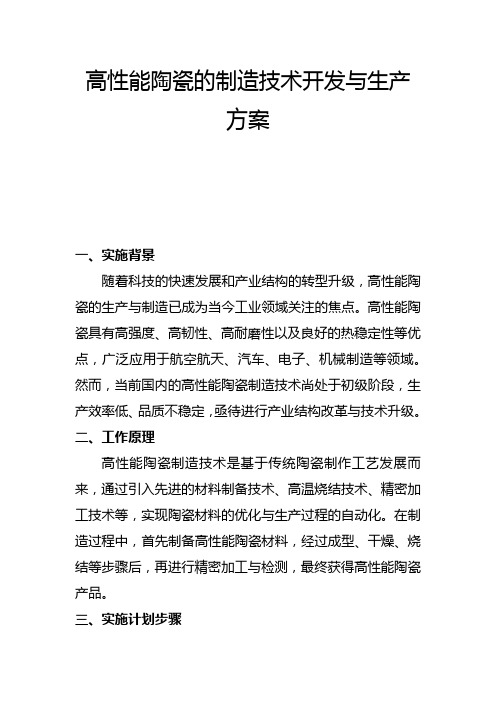
高性能陶瓷的制造技术开发与生产方案一、实施背景随着科技的快速发展和产业结构的转型升级,高性能陶瓷的生产与制造已成为当今工业领域关注的焦点。
高性能陶瓷具有高强度、高韧性、高耐磨性以及良好的热稳定性等优点,广泛应用于航空航天、汽车、电子、机械制造等领域。
然而,当前国内的高性能陶瓷制造技术尚处于初级阶段,生产效率低、品质不稳定,亟待进行产业结构改革与技术升级。
二、工作原理高性能陶瓷制造技术是基于传统陶瓷制作工艺发展而来,通过引入先进的材料制备技术、高温烧结技术、精密加工技术等,实现陶瓷材料的优化与生产过程的自动化。
在制造过程中,首先制备高性能陶瓷材料,经过成型、干燥、烧结等步骤后,再进行精密加工与检测,最终获得高性能陶瓷产品。
三、实施计划步骤1.技术研发:组织技术团队进行高性能陶瓷材料的基础研究,探索材料的组成与性能关系,研究制备工艺对材料性能的影响。
同时,对生产设备进行升级改造,提高生产效率与产品质量。
2.设备采购:根据技术研发需求,采购先进的陶瓷材料制备设备、烧结设备、精密加工设备等。
确保设备性能稳定、精度高、可靠性好。
3.生产线建设:依据采购的设备,设计并建设高性能陶瓷生产线。
优化生产流程,提高生产效率。
4.试生产与调试:进行试生产,对生产过程进行监控与调试。
对出现的问题及时进行调整和改进,确保生产线正常运行。
5.产品质量检测:对生产的高性能陶瓷产品进行质量检测,确保产品性能符合预期要求。
同时,建立完善的质量控制体系,确保产品质量的稳定性和可靠性。
6.投产与市场推广:在确保产品质量稳定后,正式投产并开展市场推广工作。
加强与客户的沟通与合作,提供定制化服务,满足不同市场需求。
四、适用范围本方案适用于高性能陶瓷的制造与生产领域。
具体包括以下方面:1.高性能陶瓷材料制备:采用先进的材料制备技术,实现高性能陶瓷材料的批量生产。
2.高性能陶瓷零部件制造:通过精密加工技术,生产高性能陶瓷零部件,满足航空航天、汽车、电子等领域的需求。
陶瓷生产技术及设备-3

成 型
3.1 器形的合理设计
陶瓷制品的器形设计讲究 “实用、美观、可加工、高生产效率” 的原则。
3.2 成型方法的分类与选择
一、成型方法的分类
半干压法:坯料含水率 8~15%
1. 压制法成型
普通压制法成型
等静压法成型
干压法:坯料含水率 3~7%
2. 可塑法成型:雕塑、拉坯、印坯、盘筑、旋坯、滚压、车坯、 挤出、注塑、轧膜法等。坯料含水率 18~26 %。 常压注浆(石膏模) 3. 注浆法成型 中高压注浆(多孔树脂模) 坯料含水率 28~35% 流延法成型(金属模) 热压铸法注浆(金属模)
● 轧膜成型适于轧制 1mm以下 的坯片,通常是 0.15mm左右, 最薄可达 0.05mm。
3.3 可塑成型
八、其他手工可塑成型方法
1. 雕塑
一般雕塑
雕塑
镂空雕塑 堆贴雕塑
● 镂空雕塑
3.3 可塑成型
八、其他手工可塑成型方法
1. 雕塑
● 堆贴雕塑
3.3 可塑成型
八、其他手工可塑成型方法
2. 盘筑(围筑)塑形
3.3 可塑成型
三、挤压(出)成型
挤出成型主要适用于管状、棒状、截面和中孔一致的制品的成型。 坯体外形由挤出机机嘴的内表面形状确定,坯体长度则根据尺寸 要求进行切割。
3.3 可塑成型
四、车坯成型
● 主要设备:立式或卧式车坯机;模具:金属车刀 车坯成型适合用来成型外形复杂的圆柱状制品,如各种瓷质绝 缘件。所采用的坯料为经真空练泥机挤出的塑性泥段。有湿式 车坯和干式车坯二种。 湿式车坯:坯料含水率16~18%,成型坯体精度较差且易 变形,但刀具磨损小,无粉尘产生。 干式车坯:坯料含水率 6~11%,成型坯体精度高,但刀 具磨损大,粉尘大。
陶瓷行业自动化
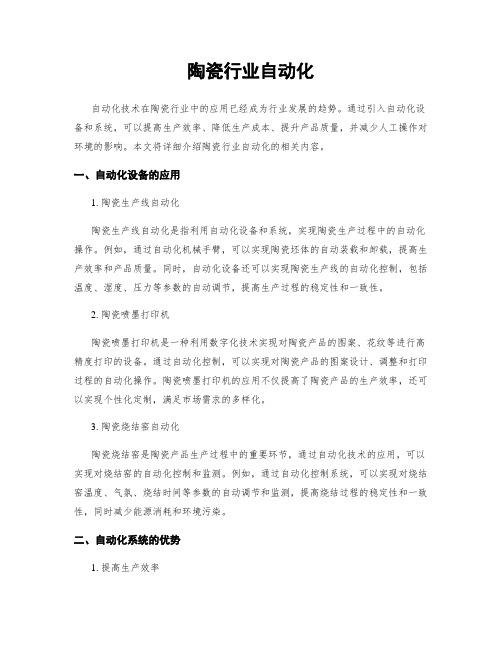
陶瓷行业自动化自动化技术在陶瓷行业中的应用已经成为行业发展的趋势。
通过引入自动化设备和系统,可以提高生产效率、降低生产成本、提升产品质量,并减少人工操作对环境的影响。
本文将详细介绍陶瓷行业自动化的相关内容。
一、自动化设备的应用1. 陶瓷生产线自动化陶瓷生产线自动化是指利用自动化设备和系统,实现陶瓷生产过程中的自动化操作。
例如,通过自动化机械手臂,可以实现陶瓷坯体的自动装载和卸载,提高生产效率和产品质量。
同时,自动化设备还可以实现陶瓷生产线的自动化控制,包括温度、湿度、压力等参数的自动调节,提高生产过程的稳定性和一致性。
2. 陶瓷喷墨打印机陶瓷喷墨打印机是一种利用数字化技术实现对陶瓷产品的图案、花纹等进行高精度打印的设备。
通过自动化控制,可以实现对陶瓷产品的图案设计、调整和打印过程的自动化操作。
陶瓷喷墨打印机的应用不仅提高了陶瓷产品的生产效率,还可以实现个性化定制,满足市场需求的多样化。
3. 陶瓷烧结窑自动化陶瓷烧结窑是陶瓷产品生产过程中的重要环节,通过自动化技术的应用,可以实现对烧结窑的自动化控制和监测。
例如,通过自动化控制系统,可以实现对烧结窑温度、气氛、烧结时间等参数的自动调节和监测,提高烧结过程的稳定性和一致性,同时减少能源消耗和环境污染。
二、自动化系统的优势1. 提高生产效率通过引入自动化设备和系统,可以实现陶瓷生产过程中的自动化操作,减少人工操作的时间和成本,提高生产效率。
例如,自动化机械手臂可以实现陶瓷坯体的自动装载和卸载,大大提高了生产线的运行效率。
2. 降低生产成本自动化设备和系统的应用可以减少人工操作的需求,降低人工成本。
同时,自动化设备还可以实现对生产过程的自动化控制和监测,减少生产中的误差和废品率,降低生产成本。
3. 提升产品质量自动化设备和系统的应用可以实现对生产过程的自动化控制和监测,提高产品质量的稳定性和一致性。
例如,通过自动化控制系统,可以实时监测陶瓷产品的温度、湿度、压力等参数,及时调整生产过程,保证产品质量的稳定性。
陶瓷生产工艺技术
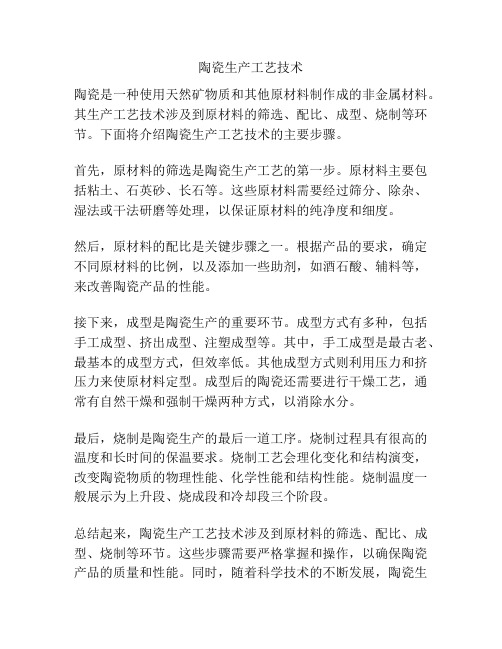
陶瓷生产工艺技术
陶瓷是一种使用天然矿物质和其他原材料制作成的非金属材料。
其生产工艺技术涉及到原材料的筛选、配比、成型、烧制等环节。
下面将介绍陶瓷生产工艺技术的主要步骤。
首先,原材料的筛选是陶瓷生产工艺的第一步。
原材料主要包括粘土、石英砂、长石等。
这些原材料需要经过筛分、除杂、湿法或干法研磨等处理,以保证原材料的纯净度和细度。
然后,原材料的配比是关键步骤之一。
根据产品的要求,确定不同原材料的比例,以及添加一些助剂,如酒石酸、辅料等,来改善陶瓷产品的性能。
接下来,成型是陶瓷生产的重要环节。
成型方式有多种,包括手工成型、挤出成型、注塑成型等。
其中,手工成型是最古老、最基本的成型方式,但效率低。
其他成型方式则利用压力和挤压力来使原材料定型。
成型后的陶瓷还需要进行干燥工艺,通常有自然干燥和强制干燥两种方式,以消除水分。
最后,烧制是陶瓷生产的最后一道工序。
烧制过程具有很高的温度和长时间的保温要求。
烧制工艺会理化变化和结构演变,改变陶瓷物质的物理性能、化学性能和结构性能。
烧制温度一般展示为上升段、烧成段和冷却段三个阶段。
总结起来,陶瓷生产工艺技术涉及到原材料的筛选、配比、成型、烧制等环节。
这些步骤需要严格掌握和操作,以确保陶瓷产品的质量和性能。
同时,随着科学技术的不断发展,陶瓷生
产工艺技术也在不断创新和提升,以满足市场需求和陶瓷产品的多样化。
陶瓷制品的数字化创作与生产技术

陶瓷制品的数字化创作与生产技术随着科技的不断进步和数字化方案的流行,各行各业都在不断探索数字化创作与生产技术。
陶瓷制品作为传统的工艺品,在数字化时代也开始尝试应用数字化创作与生产技术,以满足市场需求和提高生产效率。
本文将介绍陶瓷制品数字化创作与生产技术的相关内容。
首先,陶瓷制品数字化创作与设计方面采用了多种技术手段。
传统的手工绘画和雕刻技术可以通过数字化工具进行模拟和重现,实现了更高效、更精确的设计过程。
例如,利用计算机辅助设计(CAD)软件,设计师可以轻松绘制图案和雕刻图案,实现复杂程度较高的陶瓷制品设计。
同时,数字化技术还使得设计师能够通过虚拟现实技术(VR)实时观察和调整作品的效果,更好地满足消费者的需求。
其次,陶瓷制品数字化生产技术在生产工艺上带来了革命性的变革。
传统的陶瓷工艺通常需要多个环节进行手工操作,生产周期较长且工艺复杂。
而数字化生产技术的应用,可以实现生产过程的自动化和智能化。
例如,数控机床和机械臂等智能设备可以代替工人进行精确的陶瓷零件的切割和拼接,提高生产效率和产品质量。
此外,3D打印技术的应用也为陶瓷制品生产带来了许多创新。
与传统工艺相比,3D打印技术可以实现复杂形状的制作,并且减少了原材料的浪费。
这种技术的应用使得陶瓷制品的生产过程更加灵活、高效。
此外,陶瓷制品数字化创作与生产技术还促进了个性化定制的发展。
传统的陶瓷制品通常是批量生产的,缺乏个性化和定制的特点。
而数字化技术的应用使得定制化生产成为可能。
消费者可以通过在线平台或者APP进行定制需求的提交,利用数字化的工艺技术,制造出满足消费者个性化需求的陶瓷制品。
这不仅在一定程度上满足了消费者个性化需求,也为陶瓷行业带来了更多的商机和市场潜力。
然而,陶瓷制品数字化创作与生产技术也面临一些挑战和问题。
首先,数字化技术的应用需要专业的人才和技术支持。
陶瓷制品行业传统工艺的技术人才通常缺乏数字化的技术理解和专业知识,因此需要加强人才培养和技术转型。
陶瓷自动化生产线
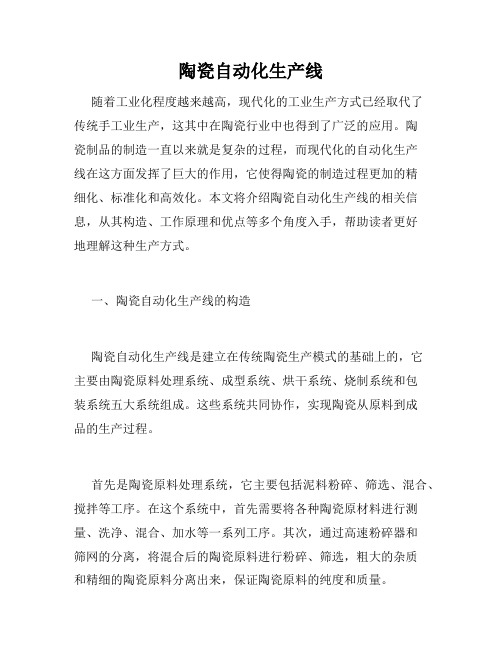
陶瓷自动化生产线随着工业化程度越来越高,现代化的工业生产方式已经取代了传统手工业生产,这其中在陶瓷行业中也得到了广泛的应用。
陶瓷制品的制造一直以来就是复杂的过程,而现代化的自动化生产线在这方面发挥了巨大的作用,它使得陶瓷的制造过程更加的精细化、标准化和高效化。
本文将介绍陶瓷自动化生产线的相关信息,从其构造、工作原理和优点等多个角度入手,帮助读者更好地理解这种生产方式。
一、陶瓷自动化生产线的构造陶瓷自动化生产线是建立在传统陶瓷生产模式的基础上的,它主要由陶瓷原料处理系统、成型系统、烘干系统、烧制系统和包装系统五大系统组成。
这些系统共同协作,实现陶瓷从原料到成品的生产过程。
首先是陶瓷原料处理系统,它主要包括泥料粉碎、筛选、混合、搅拌等工序。
在这个系统中,首先需要将各种陶瓷原材料进行测量、洗净、混合、加水等一系列工序。
其次,通过高速粉碎器和筛网的分离,将混合后的陶瓷原料进行粉碎、筛选,粗大的杂质和精细的陶瓷原料分离出来,保证陶瓷原料的纯度和质量。
其次是成型系统,它是陶瓷自动化生产线中非常重要的环节。
成型是将制作好的陶瓷原料通过数控成型设备进行成型制品的工序。
数控成型设备可以根据模型的尺寸和要求来自动调整成型机的动作,从而实现陶瓷制品的快速、高效、精确的生产。
设备机器的钢架和模具、电器都是高品质制造的。
在制品的质量方面,能保持稳定性并长期稳定运行。
接下来是烘干系统,烘干是指陶瓷成型后进行水分蒸发和晾干,这个环节是陶瓷生产线中不可或缺的环节。
通过高温加热,可以将陶瓷中的水分蒸发掉,让瓷体更加坚固,稳定,然后就可以进入到下一个制品生产环节。
烘干系统主要包括压克力深型烘箱和气流循环热风烘箱,可以对陶瓷制品进行高效、快速的烘干,并且保证瓷的品质。
最后是烧制系统,烧制是陶瓷制作的最后一步。
烧成的速度和温度会根据陶瓷制品不同的材质和尺寸而有所改变。
烧制是一个温度变化复杂、时间长的过程,主要包括进行观察、测温、燃烧控制等一系列工作。
陶瓷生产工艺技术概况
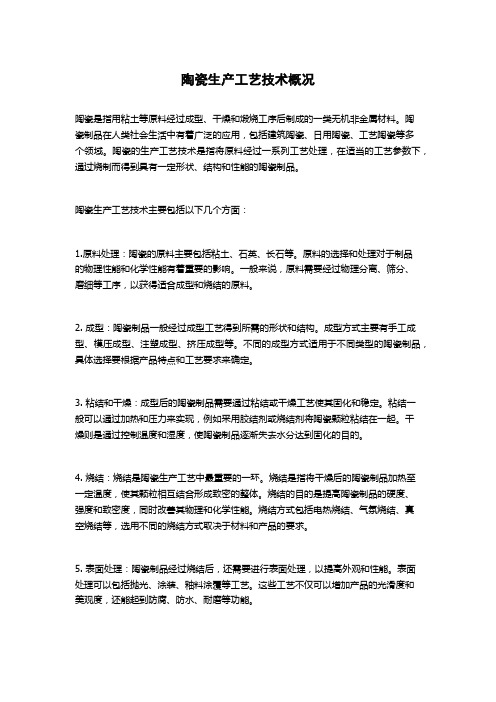
陶瓷生产工艺技术概况陶瓷是指用粘土等原料经过成型、干燥和煅烧工序后制成的一类无机非金属材料。
陶瓷制品在人类社会生活中有着广泛的应用,包括建筑陶瓷、日用陶瓷、工艺陶瓷等多个领域。
陶瓷的生产工艺技术是指将原料经过一系列工艺处理,在适当的工艺参数下,通过烧制而得到具有一定形状、结构和性能的陶瓷制品。
陶瓷生产工艺技术主要包括以下几个方面:1.原料处理:陶瓷的原料主要包括粘土、石英、长石等。
原料的选择和处理对于制品的物理性能和化学性能有着重要的影响。
一般来说,原料需要经过物理分离、筛分、磨细等工序,以获得适合成型和烧结的原料。
2. 成型:陶瓷制品一般经过成型工艺得到所需的形状和结构。
成型方式主要有手工成型、模压成型、注塑成型、挤压成型等。
不同的成型方式适用于不同类型的陶瓷制品,具体选择要根据产品特点和工艺要求来确定。
3. 粘结和干燥:成型后的陶瓷制品需要通过粘结或干燥工艺使其固化和稳定。
粘结一般可以通过加热和压力来实现,例如采用胶结剂或烧结剂将陶瓷颗粒粘结在一起。
干燥则是通过控制温度和湿度,使陶瓷制品逐渐失去水分达到固化的目的。
4. 烧结:烧结是陶瓷生产工艺中最重要的一环。
烧结是指将干燥后的陶瓷制品加热至一定温度,使其颗粒相互结合形成致密的整体。
烧结的目的是提高陶瓷制品的硬度、强度和致密度,同时改善其物理和化学性能。
烧结方式包括电热烧结、气氛烧结、真空烧结等,选用不同的烧结方式取决于材料和产品的要求。
5. 表面处理:陶瓷制品经过烧结后,还需要进行表面处理,以提高外观和性能。
表面处理可以包括抛光、涂装、釉料涂覆等工艺。
这些工艺不仅可以增加产品的光滑度和美观度,还能起到防腐、防水、耐磨等功能。
6. 检测和质量控制:陶瓷生产过程中需要进行检测和质量控制,以确保产品的质量符合标准和要求。
常见的检测项目包括外观检验、尺寸测量、物理性能测试、化学成分分析等。
合格的产品需要进行标识和包装,以便于销售和交付给客户。
陶瓷生产工艺技术是一门综合性的工艺学科,需要掌握熟练的操作技能和丰富的经验。
- 1、下载文档前请自行甄别文档内容的完整性,平台不提供额外的编辑、内容补充、找答案等附加服务。
- 2、"仅部分预览"的文档,不可在线预览部分如存在完整性等问题,可反馈申请退款(可完整预览的文档不适用该条件!)。
- 3、如文档侵犯您的权益,请联系客服反馈,我们会尽快为您处理(人工客服工作时间:9:00-18:30)。
体 积 密 度
一种
压电
陶瓷
的烧
成温
介
度与
电
其压
常 数
电性
能组
织结
构之
间的
关系
介 电 损 耗
最佳烧成范围:1240~1260℃
一、烧成制度与产品性能的关系
(二)保温时间对产品性能的影响
在适宜的烧成温度下,适当保温有利于使坯釉的物理化学反应 更趋完全,形成均匀的内部结构。但若保温时间过长,也会导 致大量小晶粒溶解、晶粒平均尺寸增大、晶相总量减少。无论 普通陶瓷还是特种陶瓷都是如此。
日用瓷坯在不同烧成气氛下的最大烧结线收缩变化的比较
(四)烧成气氛对产品性能的影响 1. 普通陶瓷的烧成情况
(3)气氛对坯体过烧膨胀的影响
日用瓷坯在不同烧成气氛下过烧40℃产生的线膨胀比较
(四)烧成气氛对产品性能的影响 1. 普通陶瓷的烧成情况
(4)气氛对坯体线收缩速率的影响
日用瓷坯在不同烧成气氛下的最大线收缩速率的比较
另外,采取还原气氛烧成时,在制品进入还原气氛烧成之前,往往要进 行一段时间的氧化保温焙烧,即:使制品在950~1050℃附近,于强氧 化气氛下保温一定时间。其作用是使坯体的氧化分解反应在釉层玻化之 前能充分反应完全,沉碳得以烧尽,为烧还原气氛做好准备。
(四)烧成气氛对产品性能的影响 1. 普通陶瓷的烧成情况
烧成温度 (℃)
玻璃相
物 相 组 成(%) 莫来石 (方)石英 气孔(Vol.%)
1210
56
9
32
3
1270
58
13
28
2
1310
61
15
23
1
1350
62
10
10
1
一、烧成制度与产品性能的关系
(一)烧成温度对产品性能的影响
在不过烧的情况下,随着烧 成温度的提高,制品的体积 密度增大,吸水率和气孔率 逐渐减小,则其机械强度将 增大,釉面光泽度及显微硬 度也会提高。
CaSO4 1250~1370℃ CaO + SO3
MgSO4 > 900℃ MgO + CO2 Na2SO4 1200~1370℃ Na2O + SO3
还原气氛下
1080~1100℃
2Fe2O3 1250~1370℃ 4 FeO + O2
Fe2O3 + CO 1000~1100℃ 2 FeO + O2
● 各项烧成制度的内容: 温度制度:升温速度、(最高)烧成温度、保温 时间、冷却速度 气氛制度:气氛性质、气氛浓度、气氛转换温度
压力制度:压力性质、压力大小、零压位位置
6.1 烧成制度
● 各项烧成制度都可以用一个曲线图表示:
油(气)烧隧道窑的温度制度曲线
6.1 烧成制度
油(气)烧隧道窑的压力制度曲线
● 烧成温度或烧成范围的确 定,主要决定于配方组成、 坯料的加工细度,以及产品 的质量性能要求。同时还要 考虑烧成时间的长短。
抗介 折电 强强 度度
抗折强度 介电强度
1200
1280
1360
烧成温度(℃)
烧成温度对电瓷机电性能的影响
一、烧成制度与产品性能的关系
(一)烧成温度对产品性能的影响
过高的烧成温度对特种陶瓷制品来说也是有害的。会导致制品中的 晶粒平均尺寸过大或少数晶粒猛增,甚至将一些气孔包裹进去,从 而破坏显微组织结构的均匀性,使产品的机电性能变差。
介抗 电张 强强 度度
1
1:抗张强度
2
2:介电强度
保温时间
电瓷的机电强度随保温时间的变化
一、烧成制度与产品性能的关系
(二)保温时间对产品性能的影响
2 3 1
保温时间 (h)
高铝瓷保温时间与其部分性能的关系
1— 抗折强度
2— 玻璃相含量 3— 介电损耗角
Hale Waihona Puke 一、烧成制度与产品性能的关系
(二)保温时间对产品性能的影响
升温速度的快慢对制品烧成过程中所产生的体积收缩、残存的气孔 率有明显影响,从而影响制品的机械性能和光学性能。
(×10-4) MPa
抗
折
强 度
300
(
) 200
抗折强度 介质损耗角正切
介 质 损 耗 5角 正 4切 3
温度范围:900~1200℃
2
100
500 400 300 200 100 升温速度 (℃/h) 75氧化铝瓷的升温速率对部分性能的影响
一、烧成制度与产品性能的关系
(四)烧成气氛对产品性能的影响
烧成气氛对坯釉中有关组分在高温下的反应温度及反应速度、体积效 应均有影响,从而将直接影响着制品的矿物组成、晶粒的尺寸及数量、 玻璃相的组成及含量、气孔的数量及形态等,并进而严重影响产品的 质量性能。
通常,还原气氛都能在一定程度上降低化学反应的开始温度,例如:
一、烧成制度与产品性能的关系
(三)升、降温速度对产品性能的影响
● 普通陶瓷烧成后,缓冷可导致较大的体积收缩、较小的 气孔率。生产实践证明,对于含玻璃相多的致密烧结坯体, 应采取高温快冷、低温缓冷的冷却制度。高温快冷不但可以防
止粗晶形成,还可防止低价铁的重新氧化及釉面析晶,提高釉面 光泽度。但是,对于膨胀系数大、或含有大量SiO2 、ZrO2的坯体, 由于晶型转变伴随较大的体积效应,故在转变温度附近冷却速度 也不能太快。此外,对于厚且大的坯件,也要注意适当缓冷,否 则会因内外温差太大,造成太大的内应力而引起开裂。
一、烧成制度与产品性能的关系
(四)烧成气氛对产品性能的影响
1. 关于气氛的有关概念
非中性气氛还存在一个 “浓度”的问题,即根据窑内烟气中的游离 氧或CO浓度的大小,氧化气氛和还原气氛有强弱之分:
性实 质际 及生 其产 强中 弱, 程对 度窑 的内 界气 定氛
氧化气氛
强氧化气氛:游离氧浓度为8~10% 普通氧化气氛:游离氧浓度为4~5%
3
: 18h 内 由 常 温
2
升至1300℃
1
某种卫生瓷的升温速率对其部分性质的影响
一、烧成制度与产品性能的关系
(三)升、降温速度对产品性能的影响
冷却速度的快慢对制品结构中的晶粒大小、体积收缩有明显影响, 从而影响制品的性能。对于某些特种陶瓷制品,也包括含玻璃相多 的普陶制品高温段的冷却,急冷可以防止粗晶的形成,因此可显著 改善其机电性能。
中性气氛: 游离氧浓度为1~1.5%
还原气氛
强还原气氛:CO浓度为6~9% 弱还原气氛:CO浓度为2~4%
CO浓度2~9%, 游离氧<1%
(四)烧成气氛对产品性能的影响
1. 关于气氛的有关概念
普通陶瓷制品的烧成只有两种情况:氧化气氛烧成或还原气氛烧成。
氧化气氛烧成时,坯体始终处于氧化气氛中加热升温。而还原气氛
二次烧成:工序较多、生产周期长、能耗高;坯体活性低、不易 形成良好的坯釉中间层;但对烧成工艺控制难度小、釉面效果易 保证、釉料损失少。
二次烧成又有两种情况:(1)高温素烧、低温釉烧;(2)低温素 烧、高温釉烧
6.1 烧成制度
为了保证既定的烧成过程的顺利进行,即为了实现上述目标, 必须制定一整套合理的烧成制度。一套完整的烧成制度包括: 温度制度、气氛制度、压力制度。
● 总之,在实际生产中,适当地降低烧成温度,而通过保温一 定时间来完成烧结过程,常能保证产品质量和降低烧成废品率。 生产实践证明,对于同一种陶瓷或耐火材料制品,在稍高的烧 成温度下、适当缩短保温时间,或者在稍低的烧成温度下、适当
延长保温时间,都能得到质量合格的产品。
一、烧成制度与产品性能的关系
(三)升、降温速度对产品性能的影响
一、烧成制度与产品性能的关系
(三)升、降温速度对产品性能的影响
如果保温时间相同,普陶制品的坯体在快速升温的情况下,产 生的体积收缩要比慢速升温的情况小,因而通常残存的气孔率 要大,则强度较小,透光率也低。
(%) MPa
抗
折
强 度
200
(
150
) 100
50
气 孔 率
4
: 24~48h 内 由
常温升至1300℃
另外,Fe2O3 含量较高时,若采取氧化焰烧成,不但会使坯体泛黄, 还易导致釉面气泡或针孔:
Fe2O3 + SiO2
2 FeO·SiO2 +
1 2
O2
对于含 TiO2量较高的坯体,应采取氧化焰烧成。否则,部分TiO2会变 成蓝到紫色的 Ti2O3,有时还会形成黑色的FeO·Ti2O3尖晶石及其他铁 钛混合晶体,并加深呈色。
第六章 烧成与窑具
6.1 烧成制度
烧成是对陶瓷、耐火材料生坯进行高温焙烧,使之发生质 变成为陶瓷或耐火材料成品的过程。其间,坯体及釉料将 发生一系列物理化学变化,从而最终形成一定的矿物组成 和显微结构,并获得所要求的性能。
陶瓷制品的烧成方式通常有一次烧成和二次烧成两种情况。 一次烧成:工序较简单、生产周期短、能耗小;生坯活性大、 易形成良好的坯釉中间层、烧后产品的坯釉结合牢固;但对 生坯强度要求较高、烧成工艺控制难度较大。
一、烧成制度与产品性能的关系
(四)烧成气氛对产品性能的影响
一般来讲,对含铁量高、有机物含量少、吸附性弱的坯体应采取还 原气氛烧成。反之宜在氧化气氛中烧成。
窑 头 室温
氧化分解阶段
高温阶段
300℃
T1 T2
950℃
氧化气氛
强弱 还还
原原
止火 温度
冷却阶段
窑 尾 常温
还原气氛
采取还原气氛烧成时的窑内气氛制度示意图
(一)烧成温度对产品性能的影响 在各项烧成工艺参数中,温度无疑是影响坯釉在高温下的物理 化学变化的最主要因素。