第7章 离子镀和离子束沉积
离子束沉积
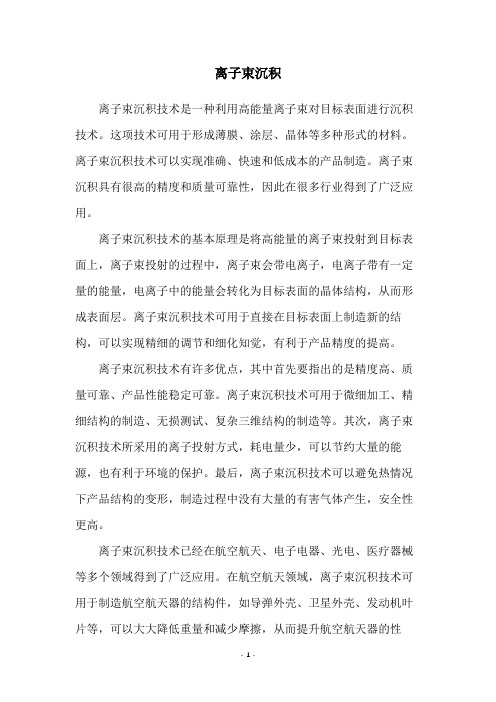
离子束沉积离子束沉积技术是一种利用高能量离子束对目标表面进行沉积技术。
这项技术可用于形成薄膜、涂层、晶体等多种形式的材料。
离子束沉积技术可以实现准确、快速和低成本的产品制造。
离子束沉积具有很高的精度和质量可靠性,因此在很多行业得到了广泛应用。
离子束沉积技术的基本原理是将高能量的离子束投射到目标表面上,离子束投射的过程中,离子束会带电离子,电离子带有一定量的能量,电离子中的能量会转化为目标表面的晶体结构,从而形成表面层。
离子束沉积技术可用于直接在目标表面上制造新的结构,可以实现精细的调节和细化知觉,有利于产品精度的提高。
离子束沉积技术有许多优点,其中首先要指出的是精度高、质量可靠、产品性能稳定可靠。
离子束沉积技术可用于微细加工、精细结构的制造、无损测试、复杂三维结构的制造等。
其次,离子束沉积技术所采用的离子投射方式,耗电量少,可以节约大量的能源,也有利于环境的保护。
最后,离子束沉积技术可以避免热情况下产品结构的变形,制造过程中没有大量的有害气体产生,安全性更高。
离子束沉积技术已经在航空航天、电子电器、光电、医疗器械等多个领域得到了广泛应用。
在航空航天领域,离子束沉积技术可用于制造航空航天器的结构件,如导弹外壳、卫星外壳、发动机叶片等,可以大大降低重量和减少摩擦,从而提升航空航天器的性能。
在电子电器领域,离子束沉积技术可以快速地生产出特殊电子元件,具有高精度、高可靠性以及耐高温和耐冲击等特点,可用于制造汽车、工业控制器、太阳能电池等电子元件。
此外,离子束技术也可用于制造高质量的医疗器械,如胸管、肝管等,可有效改善人类的健康水平。
综上所述,离子束沉积技术在多个行业得到了广泛应用。
离子束沉积技术具有准确、快速和低成本的特性,可以有效改善产品的精度、质量和可靠性。
第七章 电子束和离子束加工

电子束可焊接的材料范围很广,除了适合于普通的碳钢、合金钢、不锈钢外, 更有利于焊接高熔点金属(如钽、钼、钨、钛等及其合金)和活泼金属(如锆、 钛、铌等),还可焊接异种金属材料、半导体材料以及陶瓷和石英材料等,例如 铜和不锈钢的焊接,钢和硬质合金的焊接等。 由于电子束焊接对焊件的热影响小、变形小,可以在工件精加工后进行焊接。 又由于它能够实现不同种类金属的焊接,有可能将复杂的工件分成几个零件。这 些零件可以单独地使用最合适的材料,采用合适的方法来加工制造,最后利用电 子束焊接成一个完整的零部件,从而可以获得理想的使用性能和显著的经济效益。 例如,可变后掠翼飞机的中翼盒长达6.7m,壁厚12.7~57mm,钛合金小零件 可以用电子束焊接制成,共70道焊缝,仅此一项工艺就减轻飞机重量270kg。大 型涡轮风扇发动机的钛合金机匣,壁厚1.8~69.8mm,外径2.4m,是发动机中最 大、加工最复杂、成本最高的部件。采用电子束焊接后,节约了材料和加工工时, 成本降低40%。阿波罗登月仓的铍合金框架和制动引擎中的64个零部件也都采用 了电子束焊接。Fra bibliotek3、热处理
电子束热处理是把电子束作为热源,并适当控制电子束 的功率密度,使金属表面加热而不熔化,达到热处理的目 的。 电子束热处理的加热速度和冷却速度都很高,在相变过 程中,奥氏体化时间很短,只有几分之一秒乃至千分之一 秒,奥氏体晶粒来不及长大,从而能获得一种超细晶粒组 织,可使工件获得用常规热处理不能达到的硬度。
4、电子束曝光
电子束曝光是先利用低功率密度的电子束照射称为电致抗蚀剂的 高分子材料,由入射电子与高分子相碰撞,使分子的链被切断或重新 聚合而引起分子量的变化,这一步骤也称为电子束光刻。通常将它作 为集成电路、微电子器件以及微型机械元器件的刻蚀前置工序。如果 按规定图形进行电子束曝光,就会在电致抗蚀剂中留下潜像。然后将 它浸入适当的溶剂中,则由于分子量不同而溶解度不一样,就会使潜 像显影出来。将光刻与离子束刻蚀或蒸镀工艺结合,就能在金属掩模 或材料表面上制作出图形来。
离子镀原理
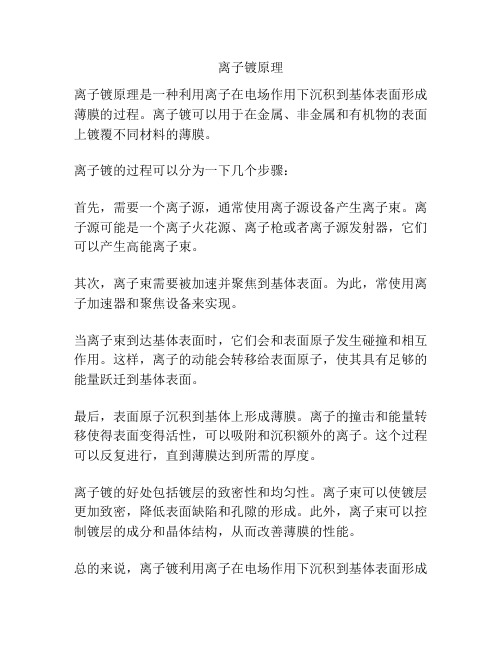
离子镀原理
离子镀原理是一种利用离子在电场作用下沉积到基体表面形成薄膜的过程。
离子镀可以用于在金属、非金属和有机物的表面上镀覆不同材料的薄膜。
离子镀的过程可以分为一下几个步骤:
首先,需要一个离子源,通常使用离子源设备产生离子束。
离子源可能是一个离子火花源、离子枪或者离子源发射器,它们可以产生高能离子束。
其次,离子束需要被加速并聚焦到基体表面。
为此,常使用离子加速器和聚焦设备来实现。
当离子束到达基体表面时,它们会和表面原子发生碰撞和相互作用。
这样,离子的动能会转移给表面原子,使其具有足够的能量跃迁到基体表面。
最后,表面原子沉积到基体上形成薄膜。
离子的撞击和能量转移使得表面变得活性,可以吸附和沉积额外的离子。
这个过程可以反复进行,直到薄膜达到所需的厚度。
离子镀的好处包括镀层的致密性和均匀性。
离子束可以使镀层更加致密,降低表面缺陷和孔隙的形成。
此外,离子束可以控制镀层的成分和晶体结构,从而改善薄膜的性能。
总的来说,离子镀利用离子在电场作用下沉积到基体表面形成
薄膜的原理。
通过控制离子束的能量和聚焦,可以实现高质量、均匀和致密的薄膜镀层。
fib离子束沉积的原理
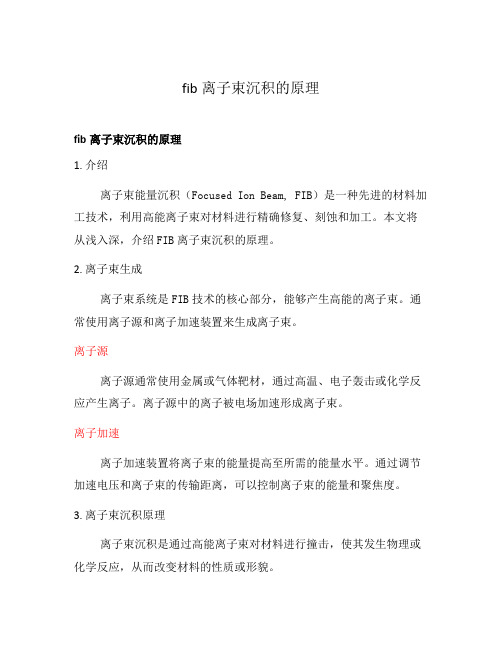
fib离子束沉积的原理fib离子束沉积的原理1. 介绍离子束能量沉积(Focused Ion Beam, FIB)是一种先进的材料加工技术,利用高能离子束对材料进行精确修复、刻蚀和加工。
本文将从浅入深,介绍FIB离子束沉积的原理。
2. 离子束生成离子束系统是FIB技术的核心部分,能够产生高能的离子束。
通常使用离子源和离子加速装置来生成离子束。
离子源离子源通常使用金属或气体靶材,通过高温、电子轰击或化学反应产生离子。
离子源中的离子被电场加速形成离子束。
离子加速离子加速装置将离子束的能量提高至所需的能量水平。
通过调节加速电压和离子束的传输距离,可以控制离子束的能量和聚焦度。
3. 离子束沉积原理离子束沉积是通过高能离子束对材料进行撞击,使其发生物理或化学反应,从而改变材料的性质或形貌。
物理效应离子束撞击材料表面时,会发生以下物理效应: - 离子的动能转化为材料内能,使材料加热,产生热应变和相变现象。
- 离子与材料原子发生碰撞,引起原子的位移、排列和表面重组。
- 离子束的能量沉积在材料中形成能量密集区,导致局部熔化、烧蚀或溶解。
化学效应离子束还可以引起材料的化学反应,例如: - 离子与材料原子发生化学反应,生成新的化合物。
- 离子束激发材料内部原子或分子,使其发生电子激发、离解和电离。
4. 应用领域FIB离子束沉积技术在以下领域有广泛的应用: - 微电子学:用于IC芯片的修复和改造。
- 材料科学:用于微纳加工、表面改性和纳米结构的制备。
- 生命科学:用于细胞操作、组织切片和生物样品制备。
5. 结论FIB离子束沉积技术利用高能离子束的物理和化学效应,对材料进行精确的修复、刻蚀和加工。
它在微电子学、材料科学和生命科学等领域具有广泛的应用前景。
作为资深的创作者,了解和掌握FIB离子束沉积的原理,将能够更好地应用和推动该技术的发展。
6. FIB离子束沉积的优势和挑战优势•高精度:FIB离子束沉积可以实现亚微米级别的加工精度,适用于高精度微纳加工需求。
第七章气相沉积技术

离子镀膜的基本过程
蒸发 材料
蒸发材料 被电离
离子加速
基片 (工件)
气体光辉放电
镀膜材料的蒸发、材料离子化、离子加速、离子轰击 工件表面沉积成膜。
28
离子镀膜的特点
膜层的附着力强,不易脱落,这是离子镀膜的重要特性。
如在不锈钢上镀制2050m厚的银膜,可以达到300MPa的 粘附强度,钢上镀镍,粘附强度也极好。
1
负偏压
靶
plasma
基片
物理 气相沉积
反应性气体 CH4
基片
化学 气相沉积
2
7.1 气相沉积的过程
气相沉积基体过程包括三个步骤: (1)提供气相镀料;
蒸发镀膜: 使镀料加热蒸发; 溅射镀膜: 用具有一定能量的离子轰击,从靶材上击出镀料原子。 (2)镀料向所镀制的工件(或基片)输送 (在真空中进行,这主要是为了避免过多气体碰撞) 高真空度时(真空度为 10-2Pa): 镀料原子很少与残余气体分子碰撞,基本上是从镀源直线前进至基片; 低真空度时(如真空度为 10Pa): 则镀料原子会与残余气体分子发生碰撞而绕射,但只要不过于降低镀膜 速率,还是允许的。 真空度过低,镀料原子频繁碰撞会相互凝聚为微粒,则镀膜过程无法进 行。
22
3)溅射镀膜工艺与应用
溅射薄膜按其不同的功能和应用可大致分为机械功能膜和 物理功能膜两大类。
前者包括耐磨、减摩、耐热、抗蚀等表面强化薄膜材料、 固体润滑薄膜材料;后者包括电、磁、声、光等功能薄膜 材料等。
23
采用Cr、Cr-CrN等合金靶或镶嵌靶,在N2、CH4等气氛 中进行反应溅射镀膜,可以在各种工件上镀Cr、CrC、 CrN等镀层。纯铬膜的显微硬度为425~840HV,CrN膜 为1000~350OHV,不仅硬度高且摩擦系数小,可代替水 溶液电镀铬。
第7章 离子镀和离子束沉积
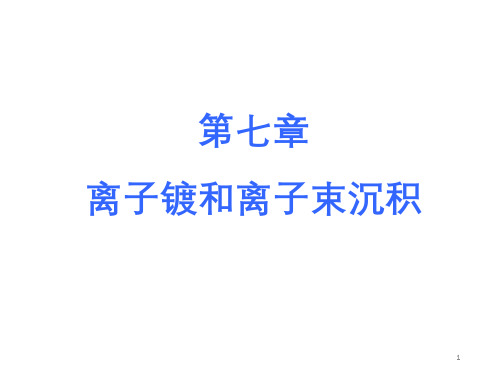
离子轰击在离子镀中的作用
对基片表面的作用(膜层沉积之前)
1)溅射清洗。高能粒子轰击基片表面,引起表面原子射出,产生溅射。 清除吸附气体、溅射掉表面物质、发生化学反应。 2)产生缺陷和位错网。轰击粒子的能量传递给表面的晶格原子。 3)破坏表面结晶结构。稳定的缺陷造成表面晶体结构的破坏变成非晶态 结构。同时,气体的掺入也会破坏表面的结晶结构。 4)气体掺入。低能离子轰击会造成气体掺入表面和淀积膜之中,掺入气 体量可高达百分之几。 5)表面成分变化。由于系统内各成分的溅射率不同,会造成表面成分与 基体成分的不同。
• 从阴极直接产生等离子体 • 入射粒子能量高、离化率60-80% • 蒸镀速度快,绕镀性好
14
离子束沉积
离子束沉积法是利用离化的粒子作为蒸镀物质,在较低的 基片温度下形成薄膜。
金属离子入射固体表面的效应:
沉积;溅射;注入
E 500 eV
E 50 eV
E 500 eV
在Si (111) 基片表面 沉积Ge+
a. 电子束蒸镀离子束辅助沉积(IBAD) b. 离子束溅射辅助沉积(IBSAD),又叫双离子束溅射沉积
19
习题
1. 离子镀中采用的蒸发源和离化方式各有哪几种? 2. 简述离子轰击对基片的作用。 3. 简述离子束辅助沉积的概念及常见的两种工艺。
20
6)表面形貌变化。表面经离子轰击后,无论晶体和非晶体基片的表面形 貌,将会发生很大的变化,使表面粗糙度增大,并改变溅射率。
7)温度升高。因为轰击离子的绝大部分能量都变成热能。
8
离子轰击在离子镀中的作用
对薄膜生长的影响
• 在离子镀时,一方面有镀材粒子沉积到基片上,另一方面有高能 离子轰击表面,使一些沉积粒子溅射出来。当前者的速率大于后 者,薄膜就会增厚。这一特殊的淀积与溅射的综合过程使膜基界 面和薄膜生长具有许多特点。
第7章特种加工

第 7章
特种加工
7.6.2电子束加工的特点 (1)由于电子束能够极其微细地聚焦,甚至能聚焦到0.1μm,所以 加工面积可以很小,是一种精密微细的加工方法。 ( 2)电子束能量密度很高,在极微小束斑上能达到106~109W /cm2,使照射部分的温度超过材料的熔化和气化温度,去除材料 主要靠瞬时蒸发,是一种非接触式加工。 (3)由于电子束的能量密度高,而且能量利用率可达90%以上,因 而加工生产率很高。 ( 4)可以通过磁场或电场对电子束的强度、位置、聚焦等进行直接 控制,所以整个加工过程便于实现自动化。 (5)由于电子束加工在真空中进行,因而污染少,加工表面不氧化, 特别适用于加工易氧化的金属及合金材料,以及纯度要求极高的半导 体材料。 ( 6)电子束加工需要一套专用设备和真空系统,价格较贵,因而生 产应用有一定局限性。
第 7章
特种加工
7.1.2特种加工的特点 (1)不是主要依靠机械能,而是主要依靠其他能量(如电 、化学、光、声、热等)去除金属材料。 (2)加工过程中工具和工件之间不存在显著的机械切削力 ,故加工的难易与工件硬度无关。 (3)各种加工方法可以任意复合、扬长避短,形成新的工 艺方法,更突出其优越性,便于扩大应用范围。 7.1.3特种加工的分类 特种加工按能量来源和作用形式的不同可分为: 1)电火花加工 2)电化学加工 3)高能束加工 4)物料切蚀加工 5)化学加工 6)复合加工
第 7章
特种加工
3)电火花加工的应用 电火花加工由于具有其它加工方法无法替代的加工能 力和独特仿形效果,加上电火花加工工艺技术水平的不断 提高、数控电火花加工机床的普及,其应用领域日益扩大 ,已在模具制造、机械、宇航、航空、电子、仪器、轻工 业等部用来解决各种难加工的材料和复杂形状零件的加 工问题。 加工各种形状复杂的型腔和型孔。如冲模的型孔、锻 模的型槽和注射模、吹塑模、压铸模等的型腔。 电火花加工除了用来加工模具工作件的型面外,还可 以用来加工模具中其它零件的型孔。这对保证模具制造质 量,缩短模具制造周期十分有利。 电火花加工与成形磨削配合使用时,其效果更加显著 。
现代加工技术第7章 电子束离子束加工

2024/10/7
7.1.电子束加工
3 电子束加工的应用
II 加工型孔或特殊外表
切割复杂型面,切口宽度6~3 μm ,边 缘粗糙度可控制在±0.5μm ;
不仅可以加工直孔也可以加工弯孔和 立体曲面;
Page 9
2024/10/7
7.1.电子束加工
3 电子束加工的应用
III 刻蚀
在微电子器件生产中,为了制造多层固体组件,利用电 子束对陶瓷或半导体材料可出许多微细沟槽和孔 ; 制版;
ii 蚀刻加工时,对离子入射能量、束流大小、离子 入射到工件上的角度以及工作室气压等分别控制;
iii 氩气离子蚀刻效率取决于离子能量和入射角度;
入射能量增大蚀刻效率增加;
入射角度增加蚀刻效率增加,但角度过大使有效束流减 小,40º~60º效率最高;
Page 21
2024/10/7
7.2.离子束加工
Page 10
2024/10/7
7.1.电子束加工
3 电子束加工的应用
IV 焊接
当高能量密度的电子束轰击焊件外表时,使焊件接头处 的金属熔融,在电子束不断轰击下,形成一个被熔融金 属环绕的毛细管状的蒸气管,如果焊件按一定速度沿接 缝与电子束作相对运动,那么接缝上的蒸气管由于电子 束的离开而重新凝固,形成焊缝 ; 焊接速度快,焊缝窄、强度好,热影响区小,变形小; 可以焊接难熔金属和化学活性高的金属; 可以焊接不同材料;
Pag.离子束加工
2 离子束加工装置
I 离子源
i 考夫曼型离子源;
Page 19
2024/10/7
7.2.离子束加工
2 离子束加工装置
I 离子源
ii 双等离子体型离子源;
- 1、下载文档前请自行甄别文档内容的完整性,平台不提供额外的编辑、内容补充、找答案等附加服务。
- 2、"仅部分预览"的文档,不可在线预览部分如存在完整性等问题,可反馈申请退款(可完整预览的文档不适用该条件!)。
- 3、如文档侵犯您的权益,请联系客服反馈,我们会尽快为您处理(人工客服工作时间:9:00-18:30)。
11
典型的离子镀方式
活性反应离子镀ARE ARE 特点
• 电离增加了反应物的活性,基片温度低。 • 可在任何母材上制备薄膜,如金属、玻璃、陶瓷、 塑料等,并可获得多钟化合物膜。 • 沉积速率高,最高可达75 m/min。 • 化合物的生成反应和沉积物的生长是分开的,可 分别独立控制。
12
典型的离子镀方式
6)表面形貌变化。表面经离子轰击后,无论晶体和非晶体基片的表面形 貌,将会发生很大的变化,使表面粗糙度增大,并改变溅射率。
7)温度升高。因为轰击离子的绝大部分能量都变成热能。
8
离子轰击在离子镀中的作用
对薄膜生长的影响
• 在离子镀时,一方面有镀材粒子沉积到基片上,另一方面有高能 离子轰击表面,使一些沉积粒子溅射出来。当前者的速率大于后 者,薄膜就会增厚。这一特殊的淀积与溅射的综合过程使膜基界 面和薄膜生长具有许多特点。
a. 电子束蒸镀离子束辅助沉积(IBAD) b. 离子束溅射辅助沉积(IBSAD),又叫双离子束溅射沉积
19
习题
1. 离子镀中采用的蒸发源和离化方式各有哪几种? 2. 简述离子轰击对基片的作用。 3. 简述离子束辅助沉积的概念及常见的两种工艺。
20
1)首先是在溅射与淀积混杂的基础上,由于蒸发粒子不断增加,在 膜基界面形成“伪扩散层”。这是一种膜基界面存在基片元素和 蒸发膜材元素的物理混合现象。即在基片与薄膜的界面处形成一 定厚度的组分过渡层,缓和了基片和膜材料的不匹配性,可提高 膜基界面的附着强度。
9
离子轰击在离子镀中的作用
对薄膜生长的影响
2
离子镀概述
过程:
• 真空度抽至10-4Pa的髙真空后,通入 惰性气体(如Ar),使真空度达到1~101Pa。 • 接通高压电源,在蒸发源与基片之间 建立了一个低压气体的等离子体区。
• 使镀材蒸发,蒸发粒子进入Plasma区, 与其中的正离子和被激活的惰性气体 原子及电子发生碰撞,其中一部分蒸 发粒子被电离成正离子,正离子在负 高压电场加速的作用下,到达并沉积 在基片表面成膜;其中一部分获得了 能量的原子,也沉积成膜。
空心阴极放电离子镀HCD
HCD是利用空心热阴极放电产生等离子体的镀膜技术。
• 热阴极离子电子束 数十eV,数百A • 离化率22-40%+大 量高速中性粒子 • 工作压力宽,沉积 压力范围 10-1-104Torr
13
典型的离子镀方式
多弧离子镀
把金属蒸发源(靶源)作为阴极,通过它与阳极壳体之间的弧 光放电,使靶材蒸发并离化,形成空间等离子体,对基体进行 沉积镀膜。
10
典型的离子镀方式
活性反应离子镀ARE
• 在离子镀过程中,在真 空室中导入能和金属蒸 气反应的活性气体,如 O2, N2, C2H2, CH4 等代 替Ar 或将其掺入 Ar 气中, 并用各种放电方式使金 属蒸气和反应气体的分 子、原子激活离化,促 进其间的化学反应,在 基片表面上就可获得化 合物镀层。
• 从阴极直接产生等离子体 • 入射粒子能量高、离化率60-80% • 蒸镀速度快,绕镀性好
14
离子束沉积
离子束沉积法是利用离化的粒子作为蒸镀物质,在较低的 基片温度下形成薄膜。
金属离子入射固体表面的效应:
沉积;溅射;注入
E 500 eV
E 50 eV
E 500 eV
在Si (111) 基片表面 沉积Ge+
17
离子束沉积
离化团束沉积
• 膜层致密,附着力 强,结晶性好 • 对基板及薄膜损伤 小,可用于制备半 导体膜和磁性膜等 功能薄膜
• 可大量输运蒸镀原 子,沉积速率高
• 可独立调节各个实 验参数,镀膜过程 及薄膜性能可控
18
离子束沉积
离子束辅助沉积
离子束辅助沉积是指在气相沉积镀膜的同时,用具有一定能量 的离子束进行轰击,以提高薄膜质量。
3
离子镀概述
成膜条件:
淀积作用 n 溅射剥离效应 nj
> >
N n
A
60M
10
4
nj=0.63×1016 j/cm2•s
入射离子数/单位时间Fra bibliotek淀积原子、离子数/单位时间
j:离子电流密度 , 假设轰击基片的为一价的正离子 (Ar+)
µ :淀积速率
NA:常数
ρ:膜层密度
M:膜材料质量
15
离子束沉积
离子束沉积方法分类: • • • • • 直接引出式 质量分离式 部分离化式(离子镀) 离化团束沉积 离子束辅助沉积 可调参数 • 离子种类 • 离子能量 • 离子电流大小 • 入射角 • 束斑大小 • 离子比例 • 基片温度 • 真空度
16
离子束沉积
直接引出式和质量分离式
从离子源引出离子束后,再进行质量 分离,选择其中的某种离子照射基片
第七章
离子镀和离子束沉积
1
离子镀概述
定义:离子镀是在真空条件下,利用气体放电使气体 或被蒸发物质部分离化,在气体离子或被蒸发物质离 子轰击作用的同时把蒸发物或者反应物沉积在基片上。 特点:
1. 把气体的辉光放电、等离于体技术与真空蒸发镀膜结合 在一起; 2. 附着性好-表面清洗;沉积+溅射 3. 密度高-离子轰击,形成致密结构 4. 绕射性-离化后的正离子沿电力线方向运动 5. 材料范围宽-金属、非金属、合成材料、敏感材料 6. 易于化合物膜层的形成-活性增加 7. 沉积速率高,成膜速度快
离子轰击在离子镀中的作用
对基片表面的作用(膜层沉积之前)
1)溅射清洗。高能粒子轰击基片表面,引起表面原子射出,产生溅射。 清除吸附气体、溅射掉表面物质、发生化学反应。 2)产生缺陷和位错网。轰击粒子的能量传递给表面的晶格原子。 3)破坏表面结晶结构。稳定的缺陷造成表面晶体结构的破坏变成非晶态 结构。同时,气体的掺入也会破坏表面的结晶结构。 4)气体掺入。低能离子轰击会造成气体掺入表面和淀积膜之中,掺入气 体量可高达百分之几。 5)表面成分变化。由于系统内各成分的溅射率不同,会造成表面成分与 基体成分的不同。
4
离子镀方式
镀料的气化方式
– 电阻加热 – 电子束加热 – 空心阴极放电 – 高频感应 – 弧光放电
5
离子镀方式
气化分子或原子的离化/激活方式
– 辉光放电 – 电子束 – 热电子 – 离子源 – 弧光放电
6
离子轰击在离子镀中的作用
离子镀膜区别于真空蒸发镀膜的许多特性均与离子、高速中 性粒子参与镀膜过程有关。在离子镀的整个过程中都存在着 离子轰击。
离化率是指被电离的原子数占全部蒸发原子数的百分比例。 • 离化率是衡量离子镀特性的一个重要指标。特别在反应离 子镀中更为重要,因为它是衡量活化程度的主要参量,对 镀层薄膜的各种性质产生直接影响。
• 离子能量:在电子束蒸发镀膜中,若蒸发温度为 2000 K, 则蒸发原子的平均能量为 0.2 eV。在离子镀中,轰击离子 的能量与基片加速电压有关,典型的离子能量值为 50~5000 eV。 7