离子镀和离子束沉积
表面离子注入与沉积
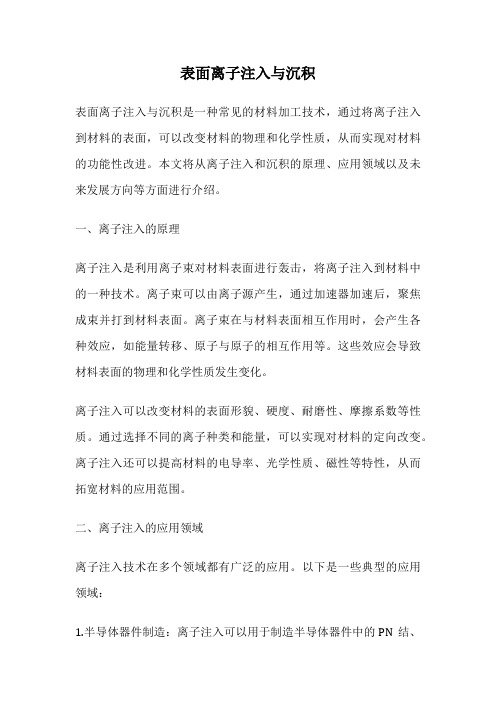
表面离子注入与沉积表面离子注入与沉积是一种常见的材料加工技术,通过将离子注入到材料的表面,可以改变材料的物理和化学性质,从而实现对材料的功能性改进。
本文将从离子注入和沉积的原理、应用领域以及未来发展方向等方面进行介绍。
一、离子注入的原理离子注入是利用离子束对材料表面进行轰击,将离子注入到材料中的一种技术。
离子束可以由离子源产生,通过加速器加速后,聚焦成束并打到材料表面。
离子束在与材料表面相互作用时,会产生各种效应,如能量转移、原子与原子的相互作用等。
这些效应会导致材料表面的物理和化学性质发生变化。
离子注入可以改变材料的表面形貌、硬度、耐磨性、摩擦系数等性质。
通过选择不同的离子种类和能量,可以实现对材料的定向改变。
离子注入还可以提高材料的电导率、光学性质、磁性等特性,从而拓宽材料的应用范围。
二、离子注入的应用领域离子注入技术在多个领域都有广泛的应用。
以下是一些典型的应用领域:1.半导体器件制造:离子注入可以用于制造半导体器件中的PN结、电阻等区域。
通过控制离子注入的能量和剂量,可以实现对半导体材料的掺杂和局部改变。
2.光学薄膜制备:离子注入可以用于制备光学薄膜材料,如反射膜、透明导电膜等。
通过离子注入,可以提高薄膜的透明性和耐磨性,从而提高光学器件的性能。
3.材料改性:离子注入可以用于改变材料的表面性质,如硬度、摩擦系数等。
通过离子注入,可以使材料具有更好的耐磨性和耐腐蚀性,提高材料的使用寿命。
4.医疗器械:离子注入可以用于改善医疗器械的表面性能,如减少摩擦、改善耐磨性等。
通过离子注入,可以使医疗器械具有更好的生物相容性和抗菌性。
5.能源材料:离子注入可以用于改善能源材料的性能,如提高锂离子电池的电导率、延长电池寿命等。
通过离子注入,可以提高能源材料的储能密度和循环稳定性。
三、离子注入与沉积的发展方向离子注入与沉积技术在材料科学和工程领域有着广泛的应用前景。
随着材料科学的不断发展和需求的不断增加,离子注入与沉积技术也在不断更新和完善。
离子束沉积
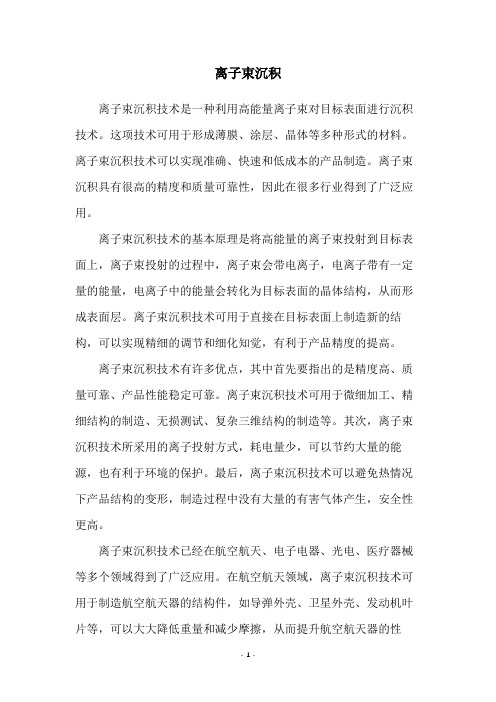
离子束沉积离子束沉积技术是一种利用高能量离子束对目标表面进行沉积技术。
这项技术可用于形成薄膜、涂层、晶体等多种形式的材料。
离子束沉积技术可以实现准确、快速和低成本的产品制造。
离子束沉积具有很高的精度和质量可靠性,因此在很多行业得到了广泛应用。
离子束沉积技术的基本原理是将高能量的离子束投射到目标表面上,离子束投射的过程中,离子束会带电离子,电离子带有一定量的能量,电离子中的能量会转化为目标表面的晶体结构,从而形成表面层。
离子束沉积技术可用于直接在目标表面上制造新的结构,可以实现精细的调节和细化知觉,有利于产品精度的提高。
离子束沉积技术有许多优点,其中首先要指出的是精度高、质量可靠、产品性能稳定可靠。
离子束沉积技术可用于微细加工、精细结构的制造、无损测试、复杂三维结构的制造等。
其次,离子束沉积技术所采用的离子投射方式,耗电量少,可以节约大量的能源,也有利于环境的保护。
最后,离子束沉积技术可以避免热情况下产品结构的变形,制造过程中没有大量的有害气体产生,安全性更高。
离子束沉积技术已经在航空航天、电子电器、光电、医疗器械等多个领域得到了广泛应用。
在航空航天领域,离子束沉积技术可用于制造航空航天器的结构件,如导弹外壳、卫星外壳、发动机叶片等,可以大大降低重量和减少摩擦,从而提升航空航天器的性能。
在电子电器领域,离子束沉积技术可以快速地生产出特殊电子元件,具有高精度、高可靠性以及耐高温和耐冲击等特点,可用于制造汽车、工业控制器、太阳能电池等电子元件。
此外,离子束技术也可用于制造高质量的医疗器械,如胸管、肝管等,可有效改善人类的健康水平。
综上所述,离子束沉积技术在多个行业得到了广泛应用。
离子束沉积技术具有准确、快速和低成本的特性,可以有效改善产品的精度、质量和可靠性。
多弧离子镀磁控溅射复合沉积

多弧离子镀磁控溅射复合沉积
多弧离子镀磁控溅射复合沉积是一种先进的表面处理技术,常用于制备功能性薄膜材料。
其工艺过程包括离子镀、磁控溅射和复合沉积三个步骤。
在离子镀步骤中,将基片作为阴极放置在离子源中,通过电弧放电或射频加热使金属阳极材料释放离子。
离子在离子源内被加速并排列成束,然后通过减速器进入装置的真空室。
离子束在进入真空室后会被聚焦并沉积在基片表面,形成均匀的金属薄膜。
这一步骤可以提高基片表面的粗糙度和增加表面活性位点数量。
在磁控溅射步骤中,将基片作为靶材放置在溅射室中,真空室内注入惰性气体(如氩气)。
通过电弧放电或射频放电,使靶材表面产生高温等离子体,使靶材表面的原子或分子离开靶材并冲击基片表面。
这个过程可以形成一层均匀致密的薄膜,增加基片表面的硬度和抗腐蚀性能。
复合沉积步骤是将离子镀和磁控溅射两个步骤结合起来,以更好地改善薄膜的性能。
通常先进行离子镀步骤,增加基片表面的活性位点数量,然后再进行磁控溅射步骤,形成一层均匀的薄膜。
这种复合沉积可以延长薄膜的使用寿命,提高其机械强度和耐磨性。
多弧离子镀磁控溅射复合沉积技术具有较高的沉积速率、良好的薄膜质量和复杂化学成分的调控能力。
它广泛应用于光学薄
膜、电子薄膜、功能性涂层等领域,如太阳能电池、显示器件和传感器等。
电磁场控制的电弧离子镀弧源设计及沉积工艺的研究
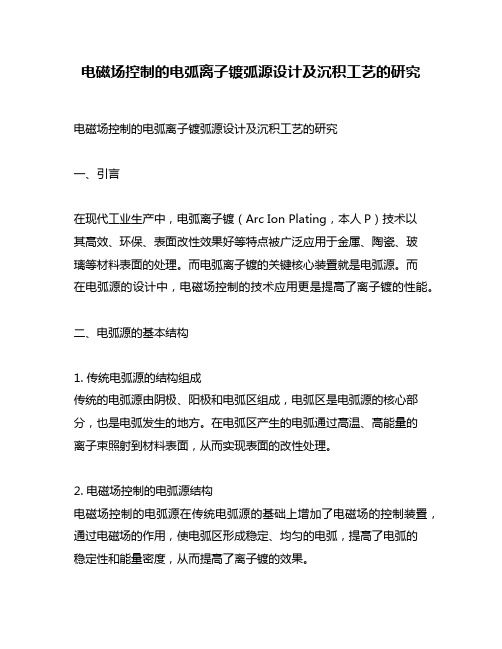
电磁场控制的电弧离子镀弧源设计及沉积工艺的研究电磁场控制的电弧离子镀弧源设计及沉积工艺的研究一、引言在现代工业生产中,电弧离子镀(Arc Ion Plating,本人P)技术以其高效、环保、表面改性效果好等特点被广泛应用于金属、陶瓷、玻璃等材料表面的处理。
而电弧离子镀的关键核心装置就是电弧源。
而在电弧源的设计中,电磁场控制的技术应用更是提高了离子镀的性能。
二、电弧源的基本结构1. 传统电弧源的结构组成传统的电弧源由阴极、阳极和电弧区组成,电弧区是电弧源的核心部分,也是电弧发生的地方。
在电弧区产生的电弧通过高温、高能量的离子束照射到材料表面,从而实现表面的改性处理。
2. 电磁场控制的电弧源结构电磁场控制的电弧源在传统电弧源的基础上增加了电磁场的控制装置,通过电磁场的作用,使电弧区形成稳定、均匀的电弧,提高了电弧的稳定性和能量密度,从而提高了离子镀的效果。
三、电弧源的电磁场控制原理1. 磁场控制电弧的作用通过在电弧源周围加上磁场,可以控制电弧的弧焰形状和大小,提高电弧的稳定性和均匀性,使得电弧能够更集中地照射到材料表面,从而提高了离子镀的效率和质量。
2. 磁场控制的影响因素磁场控制电弧的效果受到多个因素的影响,包括磁场的强度、方向、形状等因素,以及电弧源的工作状态等。
通过合理调节这些因素,可以实现最佳的电弧控制效果。
3. 电弧源与磁场控制的结合在电弧源的设计中,合理地加入磁场控制装置,并通过精密的电磁场控制系统,可以实现对电弧的准确控制和精细调节,从而提高离子镀的效果和稳定性。
四、电弧离子镀工艺的研究1. 电弧离子镀的基本原理电弧离子镀是一种表面处理技术,通过离子束对材料表面进行改性处理。
在电弧离子镀中,离子束的能量和流密度是影响镀层质量的重要因素。
2. 电弧离子镀的沉积工艺在电弧离子镀的实际工艺中,除了电弧源的设计外,气氛控制、工艺参数的选择和控制、基材的预处理等都对镀层的形成和性能有重要影响。
通过合理的工艺设计和控制,可以获得具有良好性能的表面镀层。
离子束和离子助

Your company slogan
离子束沉积
定义 在离子束沉积过程中,所希望的膜材 料被离化,具有高能量的膜材料离子 被引入到高真空区,在达到基片之前 被减速,以实现低能直接沉积。
Your company slogan
离子束沉积
原理
Your company slogan
离子束沉积
实例 Appleton等人 在Si,Ge基片上,高质量外延 生长了Si,Ge。
LOGO
离子束和离子助
普通真空镀膜
普通真空镀膜时,工件夹固在真空罩内,当高温蒸发源通 电加热后,促使待镀材料蒸发。由于升温,蒸发料粒子获 得一定动能,则沿着视线方向徐徐上升,最后附着于工件 表面上堆积成膜。
真空镀膜
离子束和离子助
Your company slogan
目录
1
离子束沉积
2
离子辅助沉积
Your company slogan
离子辅助沉积——2、阴极电弧等离子体沉积
Your company slogan
离子辅助沉积——3、热空阴极枪蒸发
Your company slogan
离子辅助沉积——4、非平衡磁控离子轰击
Your company slogan
离子辅助沉积——5、共离子轰击沉积
实验条件:沉积温度为400oC 离子束能量35Kev 真空室气压10-9Torr 在真空中安装了减速透镜和样品架 实验结果: 沉积率为1-5nm/min 对样品进行测试和分析,得基片上获 得均匀、连续且各向同性的高纯薄膜。 Your company slogan
目录
1
离子束沉积
2
离子辅助沉积
Your company slogan
镀膜玻璃的技术原理

镀膜玻璃的技术原理
镀膜玻璃是在玻璃表面涂覆一层薄膜,这层薄膜可以具有不同的功能,如防反射、隔热、隔音等。
其技术原理主要有以下几点:
1. 蒸镀法:通过在真空环境下,将金属或化合物材料加热至升华或熔化状态,然后以极高速度沉积在玻璃表面。
该方法主要适用于金属膜的制备。
2. 离子镀法:利用离子束照射的方式,将金属或化合物材料加热至气化状态,然后在玻璃表面形成薄膜。
离子束的照射可以提高薄膜的致密性和附着力,使其具有较好的耐磨性和耐腐蚀性。
3. 化学镀法:通过化学反应在玻璃表面生成薄膜。
具体的方法有浸渍法、溶胶凝胶法、离子交换法等。
这些方法在制备过程中可以控制膜层的成分和结构,从而获得具有特定功能的薄膜。
薄膜的功能性质主要取决于薄膜的成分和结构。
例如,利用特定材料可以使薄膜具有高反射或低反射的特性,提高光学透光性;通过控制薄膜厚度和组成,可以实现隔热、隔音的效果。
半导体工艺 离子注入 沉积
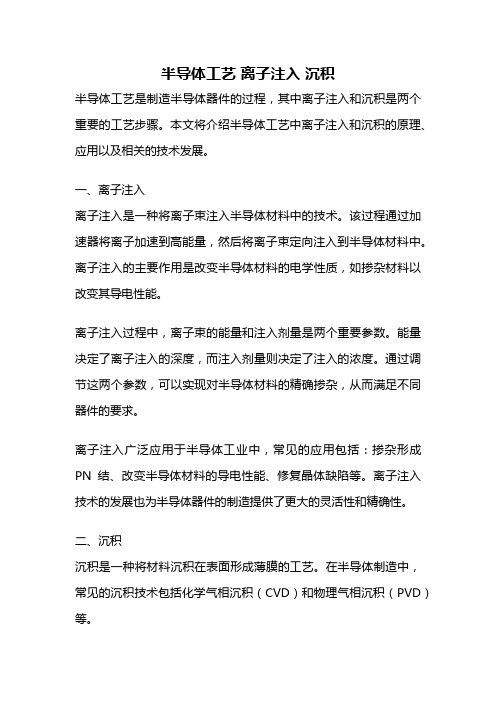
半导体工艺离子注入沉积半导体工艺是制造半导体器件的过程,其中离子注入和沉积是两个重要的工艺步骤。
本文将介绍半导体工艺中离子注入和沉积的原理、应用以及相关的技术发展。
一、离子注入离子注入是一种将离子束注入半导体材料中的技术。
该过程通过加速器将离子加速到高能量,然后将离子束定向注入到半导体材料中。
离子注入的主要作用是改变半导体材料的电学性质,如掺杂材料以改变其导电性能。
离子注入过程中,离子束的能量和注入剂量是两个重要参数。
能量决定了离子注入的深度,而注入剂量则决定了注入的浓度。
通过调节这两个参数,可以实现对半导体材料的精确掺杂,从而满足不同器件的要求。
离子注入广泛应用于半导体工业中,常见的应用包括:掺杂形成PN结、改变半导体材料的导电性能、修复晶体缺陷等。
离子注入技术的发展也为半导体器件的制造提供了更大的灵活性和精确性。
二、沉积沉积是一种将材料沉积在表面形成薄膜的工艺。
在半导体制造中,常见的沉积技术包括化学气相沉积(CVD)和物理气相沉积(PVD)等。
化学气相沉积是利用气相反应使气体中的原子或分子在表面沉积形成薄膜的过程。
该技术可以实现对薄膜的组成、厚度和均匀性的精确控制。
化学气相沉积广泛应用于制备硅氧化物、多晶硅、氮化硅等薄膜,是半导体器件制造中不可或缺的工艺步骤。
物理气相沉积是通过物理方法使固态材料蒸发或溅射,并在表面形成薄膜。
这种技术常用于制备金属薄膜,如铝、铜、钨等。
物理气相沉积具有高沉积速率和良好的薄膜质量,适用于制备金属导线、电极等器件结构。
沉积技术在半导体工艺中扮演着重要的角色。
薄膜的质量和均匀性对器件的性能有重要影响,因此沉积工艺的优化和控制非常关键。
三、技术发展随着半导体工艺的不断发展,离子注入和沉积技术也在不断改进和创新。
目前,离子注入技术趋向于高能量和低剂量注入,以减小材料的损伤和提高器件性能。
而沉积技术则在实现高均匀性、高速率和低温沉积方面取得了重要进展。
随着半导体器件不断向微纳米尺寸发展,离子注入和沉积技术也面临着新的挑战。
离子镀技术制备薄膜
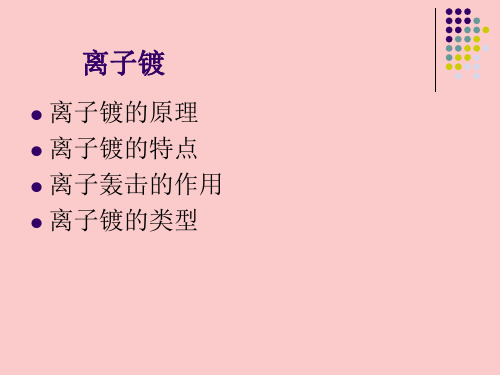
离子镀的原理 离子镀的特点 离子轰击的作用 离子镀的类型
3.1 离化 PVD 技术
一、概念:通过将成膜材料高度电离化形成膜材料离子,从而其增加 沉积动能,并使之高化学活性状态下沉积薄膜的技术。 二、出发点: 以其它手段激发沉积物质粒子,然后使之与高度电离的等离子体交 互作用 (类似 PECVD),促使沉积粒子离化,使之既可被电场加速而获 得更高动能,同时在低温状态下具有高化学活性。 三、基本特点: 大多数是蒸发/溅射 (气相物质激发) 与 等离子体离化过程 (赋能、 激活) 的交叉结合! 蒸发:速度快、结合力较低、薄膜致密性差、厚度均匀性差 溅射:速度慢、结合力较高、薄膜较致密、厚度均匀
离子镀膜技术——离子轰击的作用
破坏表面晶格 离子轰击产生的缺陷很稳定的话,表面的晶体结构 就会被破坏而成为非晶态 气体掺入 不溶性气体的掺入能力决定于迁移率、捕获位置、 基片温度及淀积粒子的能量大小 非晶材料 表面形貌变化 表面粗糙度增大,溅射率改变 温度升高
如图所示 ≈ 电阻蒸发 + 三 极溅射 引入热阴极(第三 极)的作用: 发射更多 电子,气体离化率、等 离子体荷电密度
离子镀膜技术——离子镀膜的类型
特点:
( 1 )二阴极法中放电开始的气压为 10-2Torr 左右,而
多阴极法为10-3Torr左右,可实现低气压下的离子镀膜。真 空度比二级型离子镀的真空度大约高一个数量级。所以, 镀膜质量好,光泽致密 (2) 二极型离子镀膜技术中,随着阴极电压降低,放 电起始气压变得更高;而在多阴极方式中,阴极电压在 200V就能在10-3 Torr左右开始放电。
离子镀膜技术——离子镀膜的类型
直流二极型离子镀
直流二极型离子镀的 特征是利用二极间的辉光 放电产生离子、并由基板
- 1、下载文档前请自行甄别文档内容的完整性,平台不提供额外的编辑、内容补充、找答案等附加服务。
- 2、"仅部分预览"的文档,不可在线预览部分如存在完整性等问题,可反馈申请退款(可完整预览的文档不适用该条件!)。
- 3、如文档侵犯您的权益,请联系客服反馈,我们会尽快为您处理(人工客服工作时间:9:00-18:30)。
基体成分的不同。 6)表面形貌变化。表面经离子轰击后,无论晶体和非晶体基片的表面形
貌,将会发生很大的变化,使表面粗糙度增大,并改变溅射率。 7)温度升高。因为轰击离子的绝大部分能量都变成热能。8来自离子轰击在离子镀中的作用
➢ 对薄膜生长的影响
• 在离子镀时,一方面有镀材粒子沉积到基片上,另一方面有高能 离子轰击表面,使一些沉积粒子溅射出来。当前者的速率大于后 者,薄膜就会增厚。这一特殊的淀积与溅射的综合过程使膜基界 面和薄膜生长具有许多特点。
1)首先是在溅射与淀积混杂的基础上,由于蒸发粒子不断增加,在 膜基界面形成“伪扩散层”。这是一种膜基界面存在基片元素和 蒸发膜材元素的物理混合现象。即在基片与薄膜的界面处形成一 定厚度的组分过渡层,缓和了基片和膜材料的不匹配性,可提高 膜基界面的附着强度。
15
离子束沉积
离子束沉积方法分类: • 直接引出式 • 质量分离式 • 部分离化式(离子镀) • 离化团束沉积 • 离子束辅助沉积
– 电阻加热 – 电子束加热 – 空心阴极放电 – 高频感应 – 弧光放电
5
离子镀方式
➢ 气化分子或原子的离化/激活方式
– 辉光放电 – 电子束 – 热电子 – 离子源 – 弧光放电
6
离子轰击在离子镀中的作用
离子镀膜区别于真空蒸发镀膜的许多特性均与离子、高速中 性粒子参与镀膜过程有关。在离子镀的整个过程中都存在着 离子轰击。
➢ 离化率是指被电离的原子数占全部蒸发原子数的百分比例。
• 离化率是衡量离子镀特性的一个重要指标。特别在反应离 子镀中更为重要,因为它是衡量活化程度的主要参量,对 镀层薄膜的各种性质产生直接影响。
• 离子能量:在电子束蒸发镀膜中,若蒸发温度为 2000 K, 则蒸发原子的平均能量为 0.2 eV。在离子镀中,轰击离子 的能量与基片加速电压有关,典型的离子能量值为 50~5000 eV。
• 从阴极直接产生等离子体 • 入射粒子能量高、离化率60-80% • 蒸镀速度快,绕镀性好
14
离子束沉积
离子束沉积法是利用离化的粒子作为蒸镀物质,在较低的 基片温度下形成薄膜。
金属离子入射固体表面的效应:
沉积;溅射;注入
E 500 eV E 50 eV
E 500 eV
在Si (111) 基片表面 沉积Ge+
11
典型的离子镀方式
➢ 活性反应离子镀ARE
ARE 特点
• 电离增加了反应物的活性,基片温度低。 • 可在任何母材上制备薄膜,如金属、玻璃、陶瓷、
塑料等,并可获得多钟化合物膜。 • 沉积速率高,最高可达75 m/min。 • 化合物的生成反应和沉积物的生长是分开的,可
分别独立控制。
12
典型的离子镀方式
4)对膜层内应力的影响也很明显。内应力是由尚未处于最低能量 状态的原子所产生的。通常,蒸发薄膜具有拉应力,离子镀薄 膜具有压应力。
10
典型的离子镀方式
➢ 活性反应离子镀ARE
• 在离子镀过程中,在真 空室中导入能和金属蒸 气反应的活性气体,如 O2, N2, C2H2, CH4等代 替Ar或将其掺入Ar气中, 并用各种放电方式使金 属蒸气和反应气体的分 子、原子激活离化,促 进其间的化学反应,在 基片表面上就可获得化 合物镀层。
第七章 离子镀和离子束沉积
1
离子镀概述
➢ 定义:离子镀是在真空条件下,利用气体放电使气体 或被蒸发物质部分离化,在气体离子或被蒸发物质离 子轰击作用的同时把蒸发物或者反应物沉积在基片上。
➢ 特点:
1. 把气体的辉光放电、等离于体技术与真空蒸发镀膜结合 在一起;
2. 附着性好-表面清洗;沉积+溅射 3. 密度高-离子轰击,形成致密结构 4. 绕射性-离化后的正离子沿电力线方向运动 5. 材料范围宽-金属、非金属、合成材料、敏感材料 6. 易于化合物膜层的形成-活性增加 7. 沉积速率高,成膜速度快
9
离子轰击在离子镀中的作用
➢ 对薄膜生长的影响
2)经离子轰击的表面形貌受到破坏,可能比未破坏的表面提供更 多的成核位置,即使在非反应系统中成核密度也较高。可减少 基片与膜层界面的空隙,使得离子镀具有良好附着力。
3)离子对膜层的轰击作用,对膜的形态和结晶组分也有影响。离 子镀膜时,由于离子的轰击作用,可消除柱状结晶,减轻阴影 效应,形成均匀的颗粒状结晶。
➢ 空心阴极放电离子镀HCD
HCD是利用空心热阴极放电产生等离子体的镀膜技术。
• 热阴极离子电子束 数十eV,数百A
• 离化率22-40%+大 量高速中性粒子
• 工作压力宽,沉积 压力范围 10-1-104Torr
13
典型的离子镀方式
➢ 多弧离子镀
把金属蒸发源(靶源)作为阴极,通过它与阳极壳体之间的弧 光放电,使靶材蒸发并离化,形成空间等离子体,对基体进行 沉积镀膜。
7
离子轰击在离子镀中的作用
➢ 对基片表面的作用(膜层沉积之前)
1)溅射清洗。高能粒子轰击基片表面,引起表面原子射出,产生溅射。 清除吸附气体、溅射掉表面物质、发生化学反应。
2)产生缺陷和位错网。轰击粒子的能量传递给表面的晶格原子。 3)破坏表面结晶结构。稳定的缺陷造成表面晶体结构的破坏变成非晶态
结构。同时,气体的掺入也会破坏表面的结晶结构。 4)气体掺入。低能离子轰击会造成气体掺入表面和淀积膜之中,掺入气
3
离子镀概述
➢ 成膜条件:
淀积作用
>
溅射剥离效应
n
n
NA
60M
10 4
>
nj
nj=0.63×1016 j/cm2•s
淀积原子、离子数/单位时间
入射离子数/单位时间
j:离子电流密度 , 假设轰击基片的为一价的正离子 (Ar+)
µ:淀积速率 ρ:膜层密度
NA:常数
M:膜材料质量
4
离子镀方式
➢ 镀料的气化方式
2
离子镀概述
➢ 过程:
• 真空度抽至10-4Pa的髙真空后,通入 惰性气体(如Ar),使真空度达到1~101Pa。
• 接通高压电源,在蒸发源与基片之间 建立了一个低压气体的等离子体区。
• 使镀材蒸发,蒸发粒子进入Plasma区, 与其中的正离子和被激活的惰性气体 原子及电子发生碰撞,其中一部分蒸 发粒子被电离成正离子,正离子在负 高压电场加速的作用下,到达并沉积 在基片表面成膜;其中一部分获得了 能量的原子,也沉积成膜。