国内外先进热轧技术综述b
热轧工艺的介绍范文

热轧工艺的介绍范文热轧工艺是金属材料加工中最常用的一种工艺,通过高温下对金属材料的压力加工,使其形成所需的形状和尺寸。
热轧工艺在钢铁制造、有色金属加工等行业中广泛应用,具有高效、节能、易实施等优点。
首先是原料准备。
热轧的原料通常是钢坯或铜坯等金属坯料,这些坯料通常由铸造、锻造等工艺制造而成。
在热轧前,需要对坯料进行验收、分类、堆放等操作,确保坯料的质量和工艺要求。
接下来是预处理。
预处理包括切割、切断、修边、除尘等操作,目的是将坯料修整为所需的形状和尺寸,便于后续的加工操作。
然后是加热。
热轧工艺需要将金属坯料加热到一定的温度,通常是在屈服点以上。
加热的方式可以采用盐浴炉、电炉、气焰加热等方法。
加热的目的是提高金属材料的塑性,便于后续的变形加工。
接下来是热轧。
热轧是热轧工艺的核心步骤,其过程是将加热后的金属坯料送入轧机,通过一系列辊轧的作用,使金属坯料逐渐变形成所需的形状和尺寸。
热轧的辊轧方式可分为两种:板轧和型轧,板轧适用于制造板材,型轧适用于制造型材。
辊轧时,金属坯料会经历塑性变形、终轧等工序,形成所需的材料。
然后是冷却。
热轧后的金属材料需要经过适当的冷却措施,以冷却和固定其内部组织,使金属材料具有所需的力学性能。
冷却的方式可以采用水冷、风冷等方法,具体根据材料和工艺要求来选择。
冷却的过程中,还需进行拉伸、弯曲等操作,以确保金属材料的尺寸和形状满足要求。
最后是整理。
整理是对热轧后的金属材料进行精整的一道工序,包括锯切、修磨、清洗等操作,以获得光洁的表面和精确的尺寸。
总之,热轧工艺通过高温下的压力加工,使金属材料逐渐变形成所需的形状和尺寸,广泛应用于钢铁制造、有色金属加工等行业。
热轧工艺具有高效、节能、易实施等优点,但也存在着能耗较大、设备投资高等缺点。
随着科技的发展,热轧工艺也在不断创新和改进,以满足不同材料和工艺要求。
我国热轧带钢生产的新技术

我国热轧带钢生产的新技术作者:胡彬彬来源:《中国科技博览》2012年第32期[摘要]:近年来,我国热轧宽带钢产量迅猛增长,随着前期投产的生产线产量的陆续释放,以及即将投产产能的增加,后期国内热轧板卷产量增幅将继续保持在较高水平。
而近几年来我国集中建设了一大批宽带钢热轧机,数量之多,建设速度之快,不仅在我国,在全世界也是空前的。
[关键词]:热轧新技术连铸中图分类号:TG333.7+1 文献标识码:文章编号:1009-914X(2012)32- 0339-01近年来我国新建传统宽带钢热连轧机组除个别采用二手设备外有两种情况,一是引进国外技术装备的、具有当代世界最先进水平的轧机,二是由我国自主集式或国产的具有先进水平的轧机;热轧宽带钢连轧机组在工艺设备技术上的新发展,包括如下的新技术:板坯定宽压力机、带坯边部加热器、热卷箱及带钢无头轧制、精轧机组前设置立辊(FE)轧机、精轧机板型控制(凸度和平直度控制)、精轧机架数选择、全液压卷取机等。
1、连铸坯热送热装技术连铸坯热送热装是指连铸坯在600℃以上高温时直接装炉或先放入保温装置,以协调连铸与轧钢生产节奏,待机装入加热炉加热,然后再把经过加热1050℃以上的高温连铸坯直接送往轧机轧制。
该项技术具有节能、缩短生产周期、减少板坯存放仓库面积等效果,集成了几工序间的系统工程技术,需要多项技术的支撑,包括炼钢、连铸和热轧三者统一的生产计划管理,计算机进行实时控制;生产线设备具有较高的作业率;无缺陷高温连铸坯的生产;连铸和热轧均具有在线调宽的手段;热轧实施“自由轧制计划”;连铸和热轧厂布置紧凑或采取保温快速运输;加热炉采用多段快速步进梁,长行程装入机及热惰性小的陶瓷纤维耐火炉衬等,以适应热装的需要;在线补热和保温措施,如连铸和粗轧机间以及精轧机前设边部加热器,中间辊道设保温罩等。
2、直接轧制技术直接轧制是把1050℃以上的高温连铸坯,经边部加热后直接送往轧机轧制。
该技术要求炼钢、连铸能稳定生产无缺陷板坯,连铸机出料辊道和轧钢加热炉后装料辊道以辊道直接相连,输送辊道上加设保温罩等保温热坯设施,加热炉设有长行程装料机,以便于冷、热坯交叉装料时可将高温坯装入炉内深入。
《热轧钢板超快速冷却工艺的研究》范文

《热轧钢板超快速冷却工艺的研究》篇一一、引言热轧钢板作为重要的金属材料,在汽车制造、机械制造、桥梁建筑等多个领域都有着广泛的应用。
为了满足工业发展的需求,热轧钢板的性能提升变得尤为重要。
超快速冷却工艺作为一项先进的钢铁制造技术,能显著改善热轧钢板的性能,因而成为了近年来的研究热点。
本文将对热轧钢板超快速冷却工艺进行研究,以期为工业生产提供理论支持。
二、热轧钢板超快速冷却工艺概述热轧钢板超快速冷却工艺,即通过高效率的冷却设备和方法,将高温状态下的热轧钢板在极短时间内降低到常温,以改善钢板的组织结构,从而提高其机械性能、抗腐蚀性能等。
这种工艺在保证钢板质量的同时,还能提高生产效率,降低能耗。
三、热轧钢板超快速冷却工艺的研究内容1. 冷却速率对热轧钢板性能的影响本研究首先关注了冷却速率对热轧钢板性能的影响。
通过对比不同冷却速率下的钢板性能,我们发现,适当的超快速冷却可以显著提高钢板的强度和韧性,同时也能提高其抗腐蚀性能。
这主要是因为超快速冷却可以使得钢板的组织结构更加均匀、致密。
2. 冷却过程中组织结构的变化本研究还关注了超快速冷却过程中钢板组织结构的变化。
通过金相显微镜和电子显微镜观察发现,超快速冷却能够使得钢板的组织结构变得更加致密、晶粒更加细小。
这种组织结构的改变,使得钢板的机械性能和抗腐蚀性能得到了显著提升。
3. 工艺参数的优化为了进一步提高超快速冷却工艺的效果,我们还对工艺参数进行了优化。
通过调整冷却设备的参数、优化冷却介质的选择等措施,我们成功提高了冷却效率,同时保证了钢板的性能和质量。
四、研究方法本研究采用了理论分析、实验研究和数值模拟相结合的方法。
首先,我们通过查阅文献和资料,对超快速冷却工艺的原理和影响因素进行了理论分析。
然后,我们设计了实验方案,通过实验研究了不同条件下超快速冷却对热轧钢板性能的影响。
最后,我们还采用了数值模拟的方法,对实验结果进行了验证和预测。
五、结论通过对热轧钢板超快速冷却工艺的研究,我们得出以下结论:1. 超快速冷却工艺可以显著提高热轧钢板的性能,包括强度、韧性以及抗腐蚀性能等。
《2024年热轧钢板超快速冷却工艺的研究》范文
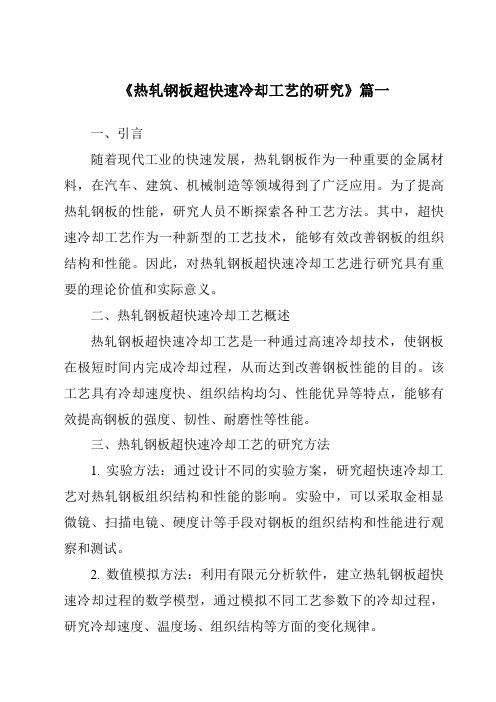
《热轧钢板超快速冷却工艺的研究》篇一一、引言随着现代工业的快速发展,热轧钢板作为一种重要的金属材料,在汽车、建筑、机械制造等领域得到了广泛应用。
为了提高热轧钢板的性能,研究人员不断探索各种工艺方法。
其中,超快速冷却工艺作为一种新型的工艺技术,能够有效改善钢板的组织结构和性能。
因此,对热轧钢板超快速冷却工艺进行研究具有重要的理论价值和实际意义。
二、热轧钢板超快速冷却工艺概述热轧钢板超快速冷却工艺是一种通过高速冷却技术,使钢板在极短时间内完成冷却过程,从而达到改善钢板性能的目的。
该工艺具有冷却速度快、组织结构均匀、性能优异等特点,能够有效提高钢板的强度、韧性、耐磨性等性能。
三、热轧钢板超快速冷却工艺的研究方法1. 实验方法:通过设计不同的实验方案,研究超快速冷却工艺对热轧钢板组织结构和性能的影响。
实验中,可以采取金相显微镜、扫描电镜、硬度计等手段对钢板的组织结构和性能进行观察和测试。
2. 数值模拟方法:利用有限元分析软件,建立热轧钢板超快速冷却过程的数学模型,通过模拟不同工艺参数下的冷却过程,研究冷却速度、温度场、组织结构等方面的变化规律。
3. 理论分析方法:结合金属学、材料科学等相关理论,分析超快速冷却工艺对热轧钢板组织结构和性能的影响机制,为优化工艺参数提供理论依据。
四、热轧钢板超快速冷却工艺的实验研究通过实验研究,我们发现超快速冷却工艺能够有效改善热轧钢板的组织结构和性能。
在实验中,我们采用了不同的冷却速度和温度制度,观察了钢板组织结构的变化规律。
结果表明,适当的超快速冷却工艺能够使钢板获得均匀细小的组织结构,提高钢板的强度和韧性。
此外,我们还研究了超快速冷却工艺对钢板耐磨性的影响,发现经过超快速冷却处理的钢板具有更好的耐磨性能。
五、热轧钢板超快速冷却工艺的优化与展望针对热轧钢板超快速冷却工艺,我们还需要进一步优化工艺参数,提高工艺的稳定性和可靠性。
未来,我们可以从以下几个方面进行研究和探索:1. 深入研究超快速冷却工艺对热轧钢板组织结构和性能的影响机制,为优化工艺参数提供更加准确的依据。
国内外先进热轧技术综述b
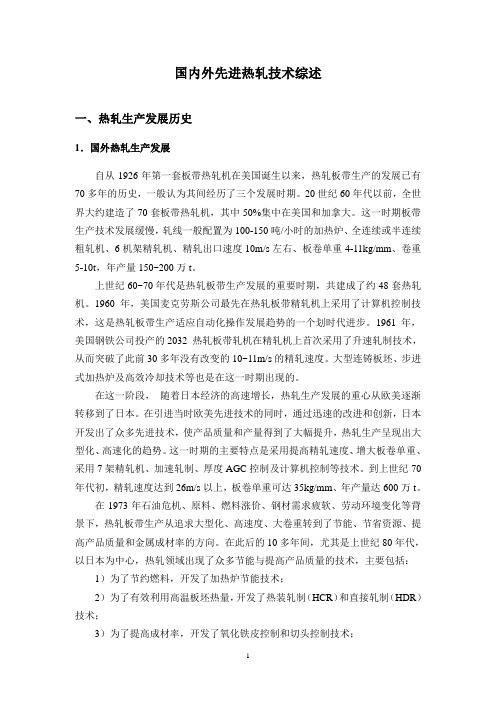
国内外先进热轧技术综述一、热轧生产发展历史1.国外热轧生产发展自从1926年第一套板带热轧机在美国诞生以来,热轧板带生产的发展已有70多年的历史,一般认为其间经历了三个发展时期。
20世纪60年代以前,全世界大约建造了70套板带热轧机,其中50%集中在美国和加拿大。
这一时期板带生产技术发展缓慢,轧线一般配置为100-150吨/小时的加热炉、全连续或半连续粗轧机、6机架精轧机、精轧出口速度10m/s左右、板卷单重4-11kg/mm、卷重5-10t,年产量150~200万t。
上世纪60~70年代是热轧板带生产发展的重要时期,共建成了约48套热轧机。
1960年,美国麦克劳斯公司最先在热轧板带精轧机上采用了计算机控制技术,这是热轧板带生产适应自动化操作发展趋势的一个划时代进步。
1961年,美国钢铁公司投产的2032 热轧板带轧机在精轧机上首次采用了升速轧制技术,从而突破了此前30多年没有改变的10~11m/s的精轧速度。
大型连铸板坯、步进式加热炉及高效冷却技术等也是在这一时期出现的。
在这一阶段,随着日本经济的高速增长,热轧生产发展的重心从欧美逐渐转移到了日本。
在引进当时欧美先进技术的同时,通过迅速的改进和创新,日本开发出了众多先进技术,使产品质量和产量得到了大幅提升,热轧生产呈现出大型化、高速化的趋势。
这一时期的主要特点是采用提高精轧速度、增大板卷单重、采用7架精轧机、加速轧制、厚度AGC控制及计算机控制等技术。
到上世纪70年代初,精轧速度达到26m/s以上,板卷单重可达35kg/mm、年产量达600万t。
在1973年石油危机、原料、燃料涨价、钢材需求疲软、劳动环境变化等背景下,热轧板带生产从追求大型化、高速度、大卷重转到了节能、节省资源、提高产品质量和金属成材率的方向。
在此后的10多年间,尤其是上世纪80年代,以日本为中心,热轧领域出现了众多节能与提高产品质量的技术,主要包括:1)为了节约燃料,开发了加热炉节能技术;2)为了有效利用高温板坯热量,开发了热装轧制(HCR)和直接轧制(HDR)技术;3)为了提高成材率,开发了氧化铁皮控制和切头控制技术;4)为了提高产品质量,开发了板厚、板宽、板凸度高精度控制技术。
《热轧钢板超快速冷却工艺的研究》范文

《热轧钢板超快速冷却工艺的研究》篇一一、引言随着现代工业的快速发展,热轧钢板因其良好的力学性能和较高的生产效率,在汽车、建筑、机械制造等领域得到了广泛应用。
然而,传统的热轧钢板生产工艺中,冷却环节往往存在冷却速度慢、效率低下等问题,这在一定程度上限制了产品的性能和应用范围。
因此,研究热轧钢板超快速冷却工艺,对于提高产品质量、生产效率和降低成本具有重要意义。
二、热轧钢板超快速冷却工艺的必要性超快速冷却工艺是指通过采用先进的冷却技术和设备,使热轧钢板在极短的时间内完成冷却过程。
这种工艺的必要性主要体现在以下几个方面:1. 提高产品性能:超快速冷却可以显著提高钢板的强度、硬度和耐磨性,同时改善其韧性和抗疲劳性能。
2. 扩大应用范围:超快速冷却工艺可以生产出满足不同领域需求的高性能钢板,如汽车制造、航空航天等。
3. 降低成本:通过提高生产效率和降低能耗,超快速冷却工艺可以降低企业的生产成本。
三、热轧钢板超快速冷却工艺的研究内容1. 冷却设备的研发:研究开发高效、可靠的超快速冷却设备,如喷水式、喷气式等设备,以满足不同钢种和工艺需求。
2. 冷却速度的优化:通过调整冷却设备的参数和工艺流程,研究不同钢种的最佳冷却速度,以达到最佳的力学性能和微观组织结构。
3. 微观组织结构的研究:通过金相显微镜、电子显微镜等手段,研究超快速冷却过程中钢板的微观组织结构变化,为优化工艺提供理论依据。
4. 力学性能的测试与分析:对超快速冷却后的钢板进行拉伸、冲击、硬度等力学性能测试,分析其性能变化规律,为实际应用提供参考。
四、热轧钢板超快速冷却工艺的应用及前景1. 应用领域:热轧钢板超快速冷却工艺已广泛应用于汽车制造、建筑、机械制造等领域,取得了显著的成果。
2. 技术进步:随着科技的不断发展,超快速冷却技术将进一步改进和完善,提高冷却效率和效果,拓宽应用范围。
3. 发展趋势:未来,热轧钢板超快速冷却工艺将与智能化、自动化技术相结合,实现生产过程的智能化控制和优化,提高生产效率和产品质量。
热轧宽带钢生产新技术及其特点
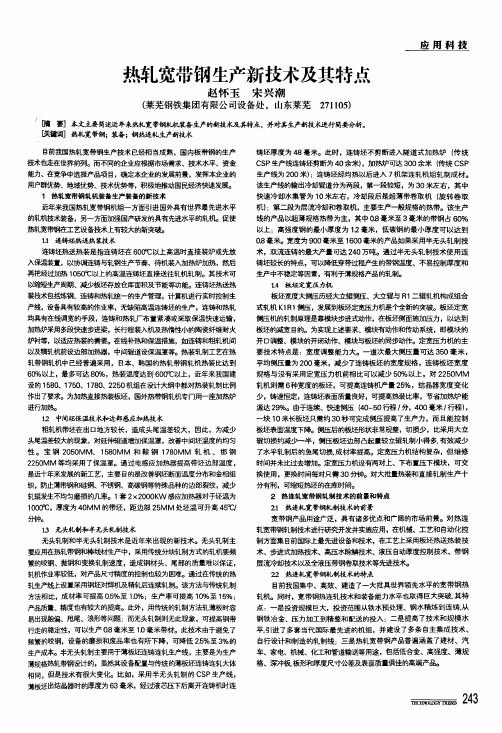
瓣L宽带钢生产新技术及其特点赵怀玉宋兴潮(莱芜钢铁集团有限公司设备处,山东莱芜271105)脯耍】本文主要简述近年来热轧宽带钢轧机裴备生产的新技术缓其特点,并对其生产新技术进行简要分析。
陕键词】热轧宽带钢;装备;钢热连轧生产声讨支书目前我国热轧宽带钢生产技术已经相当成熟,国内板带钢的生产技术也走在世界前列。
而不同的企业应根据市场需求、技术水平、资金能力、在竞争中选择产品项目,确定本企业的发展前景,发挥本企业的用户群洗势、地域优势、技术优势等,积极地推动国民经济快速发展。
1热轧宽带钢轧机装备生产装备的新技术近年来我国热轧宽带钢机组一方面引进国外具有世界最先进水平的轧机技术装备,另一方面加强国产研发的具有先进水平的轧机。
促使热轧宽带钢在工艺设备技术上有较大的新突破。
1.1连铸坯热送热装技术连铸坯热送热装是指连铸坯在60a℃以上高温时直接装炉或先放入保温装置,以协调连铸与轧钢生产节奏,待机装入加热炉加热,然后再把经过加热105a℃以上的高温连铸坯直接送往轧机轧制。
其技术可以缩短生产周期、减少板坯存放仓库面积及节能等功能。
连铸坯热送热装技术包括炼钢、连铸和热轧统一的生产管理,计算机进行实时控制生产线,设备具有较高的作业率,无缺陷高温连铸坯的生产,连铸和热轧均具有在线调宽的手段,连铸和热轧厂布置紧凑或采取保温快速运输,加热炉采用多段快速步进梁,长行程装^机及热睁陛小的陶瓷纤维耐火炉衬等,以适应热装的需要。
在线补热和保温措施,如连铸和粗轧机间以及情轧机前设边部加热器,中间辊道设保温罩等。
热装轧制工艺在热轧带钢轧机中已经普遍采用,日本、韩国的热轧带钢轧机热装比达到600/0以上,最多可达80%,热装温度达到60a℃以上,近年来我国建设的1580、1750、1780、2250机组在设计大纲中都对热装轧制比例作出了要求。
为加热.直接热装板坯,国外热带钢轧机专门用一座加热炉进行加热。
12中间坯保温技术和边部感应加热技术粗轧机带坯在出口地方较长,造成头尾温差较大,因此,为减少头尾温差较大的现象,对延伸辊道增加保温罩,改善中间坯温度的均匀性。
国内外高精度轧制技术
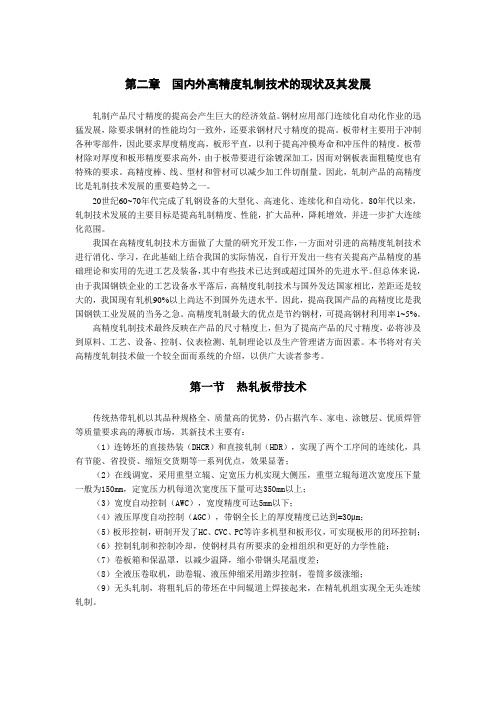
第二章国内外高精度轧制技术的现状及其发展轧制产品尺寸精度的提高会产生巨大的经济效益。
钢材应用部门连续化自动化作业的迅猛发展,除要求钢材的性能均匀一致外,还要求钢材尺寸精度的提高。
板带材主要用于冲制各种零部件,因此要求厚度精度高,板形平直,以利于提高冲模寿命和冲压件的精度。
板带材除对厚度和板形精度要求高外,由于板带要进行涂镀深加工,因而对钢板表面粗糙度也有特殊的要求。
高精度棒、线、型材和管材可以减少加工件切削量。
因此,轧制产品的高精度比是轧制技术发展的重要趋势之一。
20世纪60~70年代完成了轧钢设备的大型化、高速化、连续化和自动化。
80年代以来,轧制技术发展的主要目标是提高轧制精度、性能,扩大品种,降耗增效,并进一步扩大连续化范围。
我国在高精度轧制技术方面做了大量的研究开发工作,一方面对引进的高精度轧制技术进行消化、学习,在此基础上结合我国的实际情况,自行开发出一些有关提高产品精度的基础理论和实用的先进工艺及装备,其中有些技术已达到或超过国外的先进水平。
但总体来说,由于我国钢铁企业的工艺设备水平落后,高精度轧制技术与国外发达国家相比,差距还是较大的,我国现有轧机90%以上尚达不到国外先进水平。
因此,提高我国产品的高精度比是我国钢铁工业发展的当务之急。
高精度轧制最大的优点是节约钢材,可提高钢材利用率1~5%。
高精度轧制技术最终反映在产品的尺寸精度上,但为了提高产品的尺寸精度,必将涉及到原料、工艺、设备、控制、仪表检测、轧制理论以及生产管理诸方面因素。
本书将对有关高精度轧制技术做一个较全面而系统的介绍,以供广大读者参考。
第一节热轧板带技术传统热带轧机以其品种规格全、质量高的优势,仍占据汽车、家电、涂镀层、优质焊管等质量要求高的薄板市场,其新技术主要有:(1)连铸坯的直接热装(DHCR)和直接轧制(HDR),实现了两个工序间的连续化,具有节能、省投资、缩短交货期等一系列优点,效果显著;(2)在线调宽,采用重型立辊、定宽压力机实现大侧压,重型立辊每道次宽度压下量一般为150mm,定宽压力机每道次宽度压下量可达350mm以上;(3)宽度自动控制(AWC),宽度精度可达5mm以下;(4)液压厚度自动控制(AGC),带钢全长上的厚度精度已达到±30μm;(5)板形控制,研制开发了HC、CVC、PC等许多机型和板形仪,可实现板形的闭环控制;(6)控制轧制和控制冷却,使钢材具有所要求的金相组织和更好的力学性能;(7)卷板箱和保温罩,以减少温降,缩小带钢头尾温度差;(8)全液压卷取机,助卷辊、液压伸缩采用踏步控制,卷筒多级涨缩;(9)无头轧制,将粗轧后的带坯在中间辊道上焊接起来,在精轧机组实现全无头连续轧制。
- 1、下载文档前请自行甄别文档内容的完整性,平台不提供额外的编辑、内容补充、找答案等附加服务。
- 2、"仅部分预览"的文档,不可在线预览部分如存在完整性等问题,可反馈申请退款(可完整预览的文档不适用该条件!)。
- 3、如文档侵犯您的权益,请联系客服反馈,我们会尽快为您处理(人工客服工作时间:9:00-18:30)。
国内外先进热轧技术综述一、热轧生产发展历史1.国外热轧生产发展自从1926年第一套板带热轧机在美国诞生以来,热轧板带生产的发展已有70多年的历史,一般认为其间经历了三个发展时期。
20世纪60年代以前,全世界大约建造了70套板带热轧机,其中50%集中在美国和加拿大。
这一时期板带生产技术发展缓慢,轧线一般配置为100-150吨/小时的加热炉、全连续或半连续粗轧机、6机架精轧机、精轧出口速度10m/s左右、板卷单重4-11kg/mm、卷重5-10t,年产量150~200万t。
上世纪60~70年代是热轧板带生产发展的重要时期,共建成了约48套热轧机。
1960年,美国麦克劳斯公司最先在热轧板带精轧机上采用了计算机控制技术,这是热轧板带生产适应自动化操作发展趋势的一个划时代进步。
1961年,美国钢铁公司投产的2032 热轧板带轧机在精轧机上首次采用了升速轧制技术,从而突破了此前30多年没有改变的10~11m/s的精轧速度。
大型连铸板坯、步进式加热炉及高效冷却技术等也是在这一时期出现的。
在这一阶段,随着日本经济的高速增长,热轧生产发展的重心从欧美逐渐转移到了日本。
在引进当时欧美先进技术的同时,通过迅速的改进和创新,日本开发出了众多先进技术,使产品质量和产量得到了大幅提升,热轧生产呈现出大型化、高速化的趋势。
这一时期的主要特点是采用提高精轧速度、增大板卷单重、采用7架精轧机、加速轧制、厚度AGC控制及计算机控制等技术。
到上世纪70年代初,精轧速度达到26m/s以上,板卷单重可达35kg/mm、年产量达600万t。
在1973年石油危机、原料、燃料涨价、钢材需求疲软、劳动环境变化等背景下,热轧板带生产从追求大型化、高速度、大卷重转到了节能、节省资源、提高产品质量和金属成材率的方向。
在此后的10多年间,尤其是上世纪80年代,以日本为中心,热轧领域出现了众多节能与提高产品质量的技术,主要包括:1)为了节约燃料,开发了加热炉节能技术;2)为了有效利用高温板坯热量,开发了热装轧制(HCR)和直接轧制(HDR)技术;3)为了提高成材率,开发了氧化铁皮控制和切头控制技术;4)为了提高产品质量,开发了板厚、板宽、板凸度高精度控制技术。
5)为了提高产品性能,开发了以高强钢为中心的控制轧制、控制冷却等热处理技术(TMCP)。
6)为了提高劳动生产率,生产自动化和无人化操作进一步得到发展。
在此基础上,热轧板带生产又经过近30年的不断发展和完善,目前已经达到了很高的水平,具有大型化、高精度、全自动、高效率的显著特点,并出现了薄板坯连铸连轧、无头轧制等更为先进的生产技术。
当代热轧板带生产和现代制造技术、计算机技术及信息技术有机结合,正向着系统连续化、自动化、柔性化、高速高精度的方向发展。
2.我国热轧生产发展我国热轧带钢生产技术在建国以后很长时期内相对落后。
1958年鞍钢建成第一套1700mm带钢半连轧机组。
1978年武钢建成第二套1700mm带钢连轧机组。
而随后1989年宝钢2050mm带钢热轧机的建立,标志着我国带钢热轧生产进入快速发展的时期。
大致可分为以下三个阶段:(1)初期发展阶段这个时期热轧线建设基本靠国家投入。
由于资金、技术等多方面限制,水平参差不齐。
1989年投产的宝钢2050热轧采用了L1、L2级计算机控制,其自动宽度、自动厚度控制、CVC板形控制、强力弯辊、控制轧制和控制冷却等代表了当时最先进的热轧生产技术。
1994年投产的太钢1549热轧和梅钢1422热轧是引进了日本的二手设备。
虽然整体技术水平相对落后,但在安装过程中进行了设备和生产技术方面的改造,技术水平有所提高。
在同一时期,我国还有自行建设了两套国产热轧线,即1980年投产的本钢1700热轧和1992年投产的攀钢1450热轧。
由于当时国内的设计和制造水平有限,这两套轧机的整体水平不高。
(2)全面引进世界新技术,提高技术水平阶段20世纪90年代中期以后,各大企业均以引进国外最先进技术为主。
如1996年投产的宝钢1580热轧和1999年投产的鞍钢1780热轧等,都是世界传统热轧线最先进水平的代表。
以1580热轧为例,除现代化热轧线通常采用的一系列先进技术以外,还包括:轧线与连铸机紧凑布置形式,从而可实现直接热装,并有实现直接轧制的可能;●板坯定宽压力机,大大减少了板坯宽度规格;●精轧机全液压压下机AGC技术;●PC板形控制系统,与强力弯辊系统一起使板形调控能力大大增加;●在线磨辊装置;●中间辊道保温技术和带坯边部感应加热技术;●轧机全部采用交流同步电机和GTO电源变换器及4级计算机控制;(3)以满足市场需要和提高竞争力为目的的发展阶段由于近年国家经济快速发展,对钢材需求不断增加,因此除国营大中型企业外,中小型企业,甚至民营企业都把热轧板带作为发展的重点,建设了大量先进热轧生产线(见附表1)。
尤其是2000年后,热轧线建设数量之多,速度之快,不仅在我国,在全世界也是空前的。
其中既有以武钢2250mm为代表的当代最先进的热轧线,也有以唐钢、马钢和涟钢为代表的薄板坯连铸连轧线,还有一些炉卷轧机。
与此同时,我国带钢热轧技术和装备能力水平也取得巨大发展,不仅引进了多套当代国际最先进的机组,而且建设了多条自主集成、自行设计和制造的热轧线。
同时,这个阶段对引进的二手轧机和原技术较落后的国产轧机进行了全面技术改造,使其达到了现代化水平。
目前我国热轧技术装备已完全摆脱落后状态,并已处于世界先进水平之列。
我国热轧带钢生产所采用的一些先进技术包括:●铸坯的热装轧制(HCR)和直接轧制(HDR)技术;●步进式加热炉;●板坯定宽压力机;●宽度自动控制(AWC);●精轧机全液压厚度自动控制系统(AGC);●完善的板形控制技术;●热卷箱、保温罩和边部加热装置;●控制轧制和控制冷却;●全液压卷取机;●交流传动技术;●3级或4级计算机控制;●紧凑化布置,增大粗轧机组能力,减少粗轧机组机架数;●薄板坯连铸连轧技术;二、先进热轧技术1、热装轧制与直接轧制技术热装轧制(HCR)是将连铸板坯在高温下直接装入加热炉,有效利用板坯余热,可以大幅度节约能源。
热装轧制技术1970年前后开始在日本应用,到上世纪80年代,日本的平均热装率已达到50%,最高达80%。
装炉温度平均为500°C,最高达800°C左右。
热装轧制节能效果明显,若热轧温度为400°C-500°C,可节约燃料4.187×108J/t。
热装轧制是将炼钢、连铸和热轧几个各自独立的工序连续化,集成了多项工序间的系统工程技术。
因此,热装轧制需要解决工序间的温度、产量、工艺参数匹配和质量控制等一系列技术问题,具体的支撑技术包括:●炼钢、连铸和热轧三者统一的生产计划管理,计算机实时控制;●生产线设备具有较高的作业率;●无缺陷高温连铸坯的生产;●连铸和热轧均具有在线调宽的手段;●连铸和热轧布置紧凑或采取保温快速运输;●加热炉采用多段快速步进梁,长行程装入机及热惰性小的陶瓷纤维耐火炉衬等,以适应热装的需要;●热轧在线补热和保温措施,如设置中间辊道保温罩和精轧机前设边部加热器等;●热轧能实现自由轧制。
在热装轧制的基础上,进一步出现了连铸坯不经过加热炉的直接轧制(HDR)工艺,该项技术1981年开始应用。
直接轧制是把1050℃以上的高温连铸坯,经边部加热后直接送往轧机轧制。
根据日本的生产经验,除取向硅钢、高牌号非取向硅钢、不锈钢以及高牌号镀锡板之外,其余钢种都能直接轧制。
直接轧制工艺节能效果更为显著,可以节能50%左右。
而且缩短了生产周期,使连铸机和热轧机更紧密地联系在一起,是热装轧制技术的高水平阶段。
为实现直接轧制工艺,热装轧制所采用的技术措施同样对实现直接轧制是必需的,如无缺陷高温板坯、热送坯的保温设备、板坯边角加热炉、生产管理计算机以及区域管理计算机等硬件条件。
此外,高水平的连铸和热轧操作、生产计划和各工序的协调是实现直接轧制的关键。
由于直接轧制对软、硬件要求很高,投产后的一段时间难于实现直接轧制,国外新建热轧带钢轧机一般优先考虑热装炉工艺和直接热装炉工艺的实现,预留采用直接轧制工艺余地。
热装轧制和直接轧制技术是当代热轧带钢生产技术的发展方向,具有节能、缩短生产周期、减少板坯存放仓库面积等优点。
热装轧制工艺已有多年的生产经验,目前,热装轧制技术在热轧带钢生产中已经普遍采用,而直接轧制技术则处于发展和完善中。
在日本和韩国,连铸坯热装比例在60%以上,热装温度达600°C 以上。
如日本JFE福山厂1780热轧热装率为65%,直接轧制率为30%,热装温度达1000°C。
我国目前平均热装率为40%,平均热装温度为500°C-600°C。
2、自由轧制技术自从1973年石油危机以后,以热装轧制和直接轧制为代表的节能技术、市场需求的多样化和小批量化,促进了自由轧制技术的发展。
为满足热装轧制和直接轧制工艺要求,减少连铸板坯规格并提高连铸机产量,需要打破以往精轧机按轧制单元安排轧制计划的限制。
这就要求精轧机可以由宽到窄,也可以由窄到宽逆转轧制,同时要求同一宽度轧制批量增大,轧制的厚度也可以一定程度上跳越。
自由程度轧制是一个换辊单元内,钢质、厚度、宽度几乎可以不受限制地自由过渡的轧制技术,宽度可以逆转而不受宽度过渡的制约。
实施自由轧制技术受到多个条件的限制,主要包括:●轧制里程(总轧里程、同宽轧制里程);●为保证带钢板形所需的辊缝形状;●为保证表面质量的“棺”型轧制计划;●为保证板厚精度和穿带稳定,需避免大幅度厚度跳跃。
为了克服传统轧制计划中的这些限制条件,保证带钢的厚度精度、板形、凸度、边部减薄、表面质量,以及轧制稳定性,需要多项相关技术的支撑,如下表1所示。
表1 自由轧制支撑技术序号限制全宽润滑边部润滑在线磨辊轧辊横移板形控制高精度精轧设定跑偏控制1 轧制里程○○○2 同宽里程○○○3 由窄变宽○○○4 辊缝形状○5 厚度变换○○采用自由轧制技术可获较高的热装和直送轧制率,取得显著的实际节能效果;同时也可减少连铸坯的规格,提高连铸机产量,实现稳定操作。
自由轧制是热轧中实现柔性生产组织、提高生产效率和了降低生产成本的一个重要算途径。
随着工艺润滑技术、PC、CVC轧机和板形控制技术、工作辊横移技术、在线磨辊技术和高速钢轧辊的开发应用、液压AGC、高精度设定模型及AGC系统的发展,热轧自由轧制的自由度也在不断扩大。
3、无头轧制和半无头轧制技术(1)无头轧制无头轧制和半无头轧制技术是近年来发展的新技术。
无头轧制主要应用在热轧带钢和棒线材生产中。
采用传统分块轧制方式的轧机要频繁的咬钢、抛钢和变换轧制速度,造成钢材头、尾部的质量难以保证,轧机作业率较低,对产品尺寸精度的控制也较为困难。