160吨顶底复吹转炉设计
顶底复吹转炉整体倒置拼装翻转就位施工工法
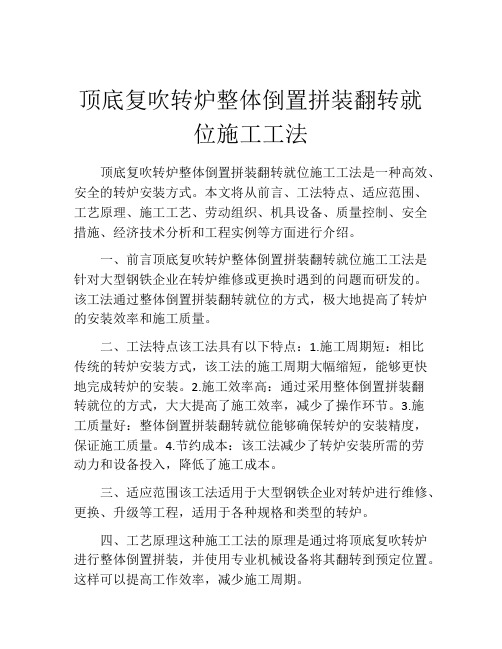
顶底复吹转炉整体倒置拼装翻转就位施工工法顶底复吹转炉整体倒置拼装翻转就位施工工法是一种高效、安全的转炉安装方式。
本文将从前言、工法特点、适应范围、工艺原理、施工工艺、劳动组织、机具设备、质量控制、安全措施、经济技术分析和工程实例等方面进行介绍。
一、前言顶底复吹转炉整体倒置拼装翻转就位施工工法是针对大型钢铁企业在转炉维修或更换时遇到的问题而研发的。
该工法通过整体倒置拼装翻转就位的方式,极大地提高了转炉的安装效率和施工质量。
二、工法特点该工法具有以下特点:1.施工周期短:相比传统的转炉安装方式,该工法的施工周期大幅缩短,能够更快地完成转炉的安装。
2.施工效率高:通过采用整体倒置拼装翻转就位的方式,大大提高了施工效率,减少了操作环节。
3.施工质量好:整体倒置拼装翻转就位能够确保转炉的安装精度,保证施工质量。
4.节约成本:该工法减少了转炉安装所需的劳动力和设备投入,降低了施工成本。
三、适应范围该工法适用于大型钢铁企业对转炉进行维修、更换、升级等工程,适用于各种规格和类型的转炉。
四、工艺原理这种施工工法的原理是通过将顶底复吹转炉进行整体倒置拼装,并使用专业机械设备将其翻转到预定位置。
这样可以提高工作效率,减少施工周期。
五、施工工艺该工法的施工工艺主要包括以下几个阶段:转炉准备、转炉分解、转炉倒置拼装、转炉翻转就位等。
在每个阶段中,都需要按照严格的操作规程进行施工。
六、劳动组织为确保施工的顺利进行,需要合理组织劳动力,包括安排具备相关技能和经验的工人,以及需要的管理人员和监督人员。
七、机具设备该工法所需的机具设备主要包括吊装机械、翻转机械、焊接设备、工具等。
这些设备在施工过程中起到重要的作用。
八、质量控制为确保施工质量,需要采取一系列的质量控制措施,包括对施工工艺每个阶段进行检查和验收,确保施工过程达到设计要求。
九、安全措施施工中需要注意一些安全事项,如使用合适的安全防护设备,确保工人的人身安全;合理规划作业流程,减少工人受伤的风险等。
转炉顶底复吹技术
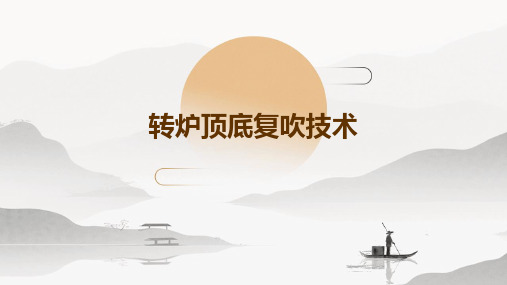
通过精确控制气体流量和吹炼参数,可以生产出 高质量的钢种。
强化冶金反应
通过顶底复吹技术,可以更有效地促进钢液中的 冶金反应,提高钢液纯净度。
节能减排
该技术能够降低炼钢过程中的能耗和减少污染物 排放。
技术发展历程
起源
转炉顶底复吹技术起源于20世纪 70年代,最初是为了解决传统转 炉炼钢技术中存在的冶金反应不
这种相互作用不仅有助于加速熔池的熔炼过程,还有助于提高钢水的纯净度和均 匀性,降低杂质含量。
顶底复吹对熔池搅拌的影响
顶底复吹技术通过向熔池底部吹入氧气或其他气体,产生强 烈的搅拌作用,使熔池内的钢水充分混合。这种搅拌作用有 助于加速钢水的传热和传质过程,提高熔炼效率。
顶底复吹的搅拌作用还能减少钢水中的夹杂物和气泡,提高 钢水的纯净度和致密性。
副枪测量准确
定期检查副枪测量准确性,确保钢水温度和 成分控制准确。
控制顶吹氧气流量
根据钢水氧化反应需求,调整顶吹氧气流量, 控制钢水温度和成分。
设备维护保养
定期对顶底复吹设备进行维护保养,确保设 备正常运行。
04
转炉顶底复吹技术的效果与 优化
转炉顶底复吹技术的效果
提高氧气利用率
通过底吹和顶吹的结合,使氧气更加 均匀地分布在熔池中,提高了氧气的 利用率,降低了能耗。
的远程监控和智能控制。
03
案例三
某欧洲大型钢厂采用先进的顶底复吹技术,提高了转炉的生产效率和产
品质量。该技术通过优化气体流量和吹炼工艺参数,降低了能耗和生产
成本,提高了企业的经济效益。
感谢您的观看
THANKS
减少氮气消耗
采用顶吹技术,可以减少氮气的消耗 量,降低生产成本。
5__转炉顶底复吹技术

图5 -2为双层套管构造
Ⅱ
BSC-BAP LD-OB LD-HC
85~ 95 80~ 90 92~ 95 90~ 92 60~ 80 20~ 40 0
5~ 15 10~ 20 5~ 8
块 块 块 或 粉 粉
STB 或STB-P Ⅲ Ⅳ K-BOP OBM-S (K-OBM ) KS KHS
日本住友 金属 日本川崎
德国 MaxhutteKlockner
底吹O2 流量 m3/min
使用其它种 类气体及流 量m3/min
加入石灰 底吹方式 顶 部 块 块 块 块 块 块 单孔喷嘴或多孔塞 炉底喷嘴 炉底喷嘴或沟槽砖, 大部分时间吹N2,最 后阶段吹Ar/ CO2 炉底喷嘴吹O2或空气, 用N2遮盖 OBM型喷嘴、天然 气遮盖 炉底喷嘴 底 部 透气砖 小口径喷嘴
( 2 )吹炼后期强化熔池搅拌,使钢——渣反应 接近平衡,降低了吹炼终点钢液中的氧含量, 冶炼低碳钢( C=0.01 ~ 0.02% ),可避免钢渣 的过氧化,还可减少脱氧时的合金消耗。 ( 3 )化渣快,有利于渣——钢间反应的进行, 进一步提高了炉渣脱磷、脱硫的能力。一般, 顶吹转炉吹炼时,磷在渣——钢间的分配比 (P)/ [P]≈70,硫的分配比(S)/ [S]=5~7; 而在复吹转炉中,( P) / [P] = 80 ~ 120 ,( S) / [S] =8~10 。 ( 4 )反应速度快,热效率高,可实现炉内二次 燃烧。 (5)熔池富余热量减少。
8~ 10 20~ 40 60~ 80 100
内喷嘴:O2/ CO2;外喷嘴: CO2/ N2/ Ar0.03~0.07
炉底喷嘴吹入氧化性 气体,STB-P为顶枪 喷石灰粉 OBM型喷嘴,氧气 底喷石灰粉、
经侧面喷嘴、从顶部吹O2, 有时用油/氧预热废钢。每 吨钢多用5m3 O2,增加废钢 50kg/t钢水。
4顶底复合吹炼转炉
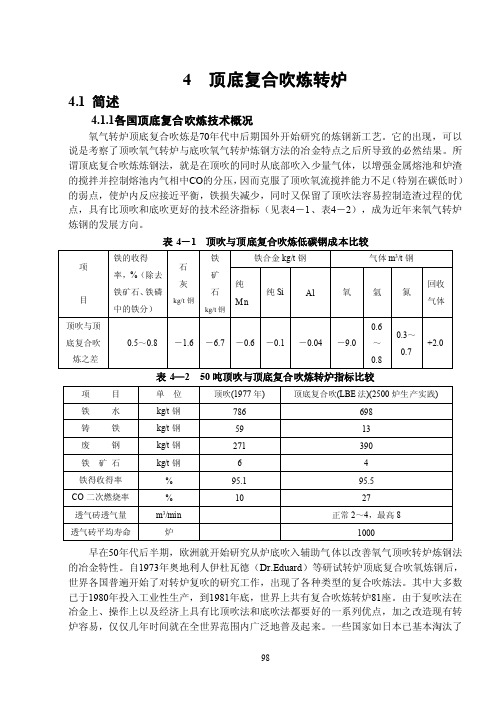
4 顶底复合吹炼转炉4.1 简述4.1.1各国顶底复合吹炼技术概况氧气转炉顶底复合吹炼是70年代中后期国外开始研究的炼钢新工艺。
它的出现,可以说是考察了顶吹氧气转炉与底吹氧气转炉炼钢方法的冶金特点之后所导致的必然结果。
所谓顶底复合吹炼炼钢法,就是在顶吹的同时从底部吹入少量气体,以增强金属熔池和炉渣的搅拌并控制熔池内气相中CO的分压,因而克服了顶吹氧流搅拌能力不足(特别在碳低时)的弱点,使炉内反应接近平衡,铁损失减少,同时又保留了顶吹法容易控制造渣过程的优点,具有比顶吹和底吹更好的技术经济指标(见表4-1、表4-2),成为近年来氧气转炉炼钢的发展方向。
表4-1 顶吹与顶底复合吹炼低碳钢成本比较表4—2 50吨顶吹与顶底复合吹炼转炉指标比较早在50年代后半期,欧洲就开始研究从炉底吹入辅助气体以改善氧气顶吹转炉炼钢法的冶金特性。
自1973年奥地利人伊杜瓦德(ard)等研试转炉顶底复合吹氧炼钢后,世界各国普遍开始了对转炉复吹的研究工作,出现了各种类型的复合吹炼法。
其中大多数已于1980年投入工业性生产,到1981年底,世界上共有复合吹炼转炉81座。
由于复吹法在冶金上、操作上以及经济上具有比顶吹法和底吹法都要好的一系列优点,加之改造现有转炉容易,仅仅几年时间就在全世界范围内广泛地普及起来。
一些国家如日本已基本淘汰了98单纯顶吹法。
4.1.2我国顶底复合吹炼技术的发展概况我国首钢及鞍钢钢铁研究所,分别于1980年和1981年开始进行复吹的试验研究,并于1983年分别在首钢30吨转炉和鞍钢150吨转炉推广使用。
到目前为止全国大部分转炉钢厂都不同程度的采用了复合吹炼技术,设备不断完善,工艺不断改进,复合吹炼钢种已有200多个,技术经济效果不断提高。
表4—3是90年代初我国已有的复吹工艺及其主要特征。
表4—3 我国已有的复合吹炼法及主要特征1)底部供气元件。
底部供气元件是复合吹炼技术的关键之一。
我国最初采用的是管式结构喷嘴,1982年采用双层套管,1983年改为环缝,虽然双层套管与环缝比,除了使用N2、CO2、Ar外,还可以吹入粉料等,但是从结构上看还是环缝最简单。
转炉设计

180t 顶底复吹转炉设计一、转炉炉型设计原始条件: 炉子平均出钢量180t 。
金属收得率取92%,最大废钢比取20%,采用废钢矿石冷却,铁水采用P08低磷生铁{w (si )≤0.85%,w (p )≤0.2%,w (s )≤0.05%}1、熔池形状确定转炉炉型有筒球型、锥球型、截锥型,熔池形状选用截锥型。
为了满 足顶底复吹的要求,炉型趋于矮胖型,由于在炉底上要设置底吹喷嘴,炉底为平底,所以熔池为截锥形。
2、炉容比确定炉容比系指转炉有效容积t V 与公称容量T 之比值。
t V 系炉帽体积帽V 、炉身体积身V 、和容池体积c V 三个内腔容积之和。
由于顶底复吹转炉吹炼过程比较平稳,产生泡沫渣的量比顶吹转炉要少得多,喷溅较少,因此其炉容比比顶吹转炉小,但比底吹转炉要大。
根据冶炼条件取炉容比为0.95m 3/t 。
3、熔池尺寸的确定熔池是容纳金属并进行一系列复杂物理化学反应的过程,其主要尺寸有熔池 直径和熔池深度。
设计时,应根据装入量、供氧强度、喷嘴类型、冶金动力学条件以及炉衬蚀损的影响综合考虑。
截锥型熔池尺寸如图(1)所示:则其体积为: )(12h2112d Dd D V ++=π熔(1) 熔池直径D :熔池直径通常指熔池处于平静状态时金属液面的直径。
D=Kt G =1.63×15180=5.646m 式中G ——炉子公称容量,180t ;t ——平均每炉钢纯吹氧时间,取15分钟; K ——比例系数,根据炉子容量取1.63; (2)熔池深度h :根据经验,取D d 7.01== 3.952m其中熔池体积38.268.6180m GV c ===ρ故熔池深度: 20.574c V h D == 2646.5574.08.26⨯=1.465m校核26.0646.5465.1/==D h 符合要求 4、炉帽尺寸的确定(1)炉帽倾角θ:本计算中取θ=65度(2)炉口直径d :炉口直径为熔池直径的43~53%,本计算中取48%则 d=48%D=0.48×5.646=2.710m(3)炉帽高度H 帽:炉帽高度是截椎体高度与炉口直线段高度值和。
最新版本氧气顶底复吹转炉设计
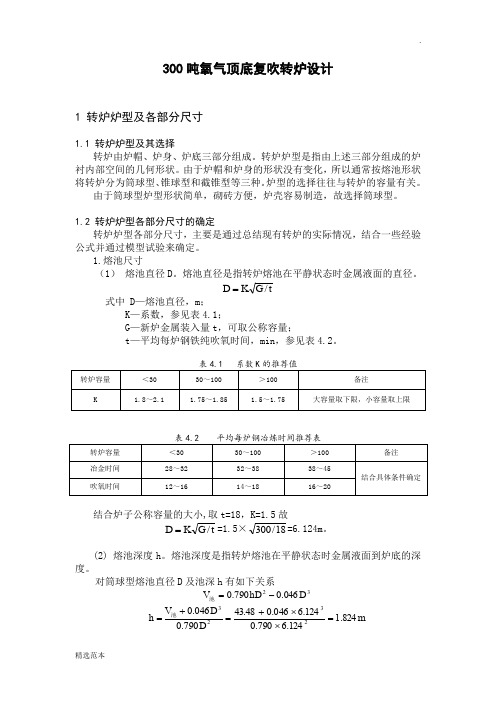
300吨氧气顶底复吹转炉设计1 转炉炉型及各部分尺寸1.1 转炉炉型及其选择转炉由炉帽、炉身、炉底三部分组成。
转炉炉型是指由上述三部分组成的炉衬内部空间的几何形状。
由于炉帽和炉身的形状没有变化,所以通常按熔池形状将转炉分为筒球型、锥球型和截锥型等三种。
炉型的选择往往与转炉的容量有关。
由于筒球型炉型形状简单,砌砖方便,炉壳容易制造,故选择筒球型。
1.2 转炉炉型各部分尺寸的确定转炉炉型各部分尺寸,主要是通过总结现有转炉的实际情况,结合一些经验公式并通过模型试验来确定。
1.熔池尺寸(1) 熔池直径D 。
熔池直径是指转炉熔池在平静状态时金属液面的直径。
t G K D /=式中 D —熔池直径,m ; K —系数,参见表4.1;G —新炉金属装入量t ,可取公称容量;t —平均每炉钢铁纯吹氧时间,min ,参见表4.2。
表4.1 系数K 的推荐值转炉容量<30 30~100 >100 备注K1.8~2.11.75~1.851.5~1.75大容量取下限,小容量取上限表4.2 平均每炉钢冶炼时间推荐表转炉容量 <30 30~100 >100 备注冶金时间 28~32 32~38 38~45结合具体条件确定吹氧时间12~1614~1816~20结合炉子公称容量的大小,取t=18,K=1.5故t G K D /==1.5×18/300=6.124m 。
(2) 熔池深度h 。
熔池深度是指转炉熔池在平静状态时金属液面到炉底的深度。
对筒球型熔池直径D 及池深h 有如下关系32046.090.70D hD V -=池m D D V h .8241.124690.70.124646.0043.4890.7046.002323=⨯⨯+=+=池这里 43.489.6300====铁铁池ρGV V m ³。
2.炉帽尺寸的确定(1) 转炉一般都用正口炉帽,其主要尺寸有炉帽倾角,炉口直径和炉帽高度。
取炉帽倾角θ=60°。
转炉顶底复吹工艺总结

转炉顶底复吹工艺总结我厂于2006年3月29日与钢铁研究总院合作完成了对3#转炉底吹工艺改造,并获得初步成功。
在8月3日完成了对1#转炉的改造,8月23日完成了对2#转炉的改造。
至此,我厂的3座转炉已经全部实现了顶底复吹。
现对顶底复吹工艺在我厂的使用情况做一总结。
1、冶炼过程1.1过程枪位控制的调整复吹转炉由于底吹的影响,熔池物化反应强度发生改变,冶炼操作方式也与顶吹有所不同。
经过技术人员与操作工的摸索,复吹总体枪位比顶吹高200mm,特别是吹炼进行到4分钟左右[C]-[O]反应初起,枪位必须提高到距钢液面1600~1700mm,以避免金属喷溅。
并将最低枪位由顶吹时的距液面800mm改为距液面1000mm,过程枪位的波动控制在1000mm~1700mm,减少了过程的喷溅和返干,并有效地减少了烧枪。
1.2渣料的调整由于复吹转炉反应速度加快,熔池搅拌均匀,渣中TFe较顶吹转炉低,石灰加入量有所减少,萤石的加入量较大。
1.3终点控制的差异复吹与顶吹转炉相比,终点控制存在一定的差异:复吹转炉由于熔池的搅拌比顶吹有所加强,拉碳时火焰收缩没有顶吹明显,终点碳容易拉低;复吹转炉成渣速度快,要求对过程温度、化渣情况的变化应及时做出反应;复吹终点成分、温度更加均匀,出钢温度可适当降低5℃左右,配[C]时要按成分的中上限控制。
2、复吹转炉冶金效果评价(部分)2.1钢水终点[C][O]浓度积采用“长寿复吹转炉冶炼技术(LCB)”后,增强了吹炼末期熔池搅拌强度,使钢液中的[C]-[O]反应更加接近平衡,降低了钢水的氧化性,提高了钢水的质量。
经检测表明,在[C]×[ O]积方面,比顶吹转炉降低0.000006。
我们取样分析,3#转炉[C]×[ O]积平均为0.002841, 2#转炉平均为0.002847,降低0.000006。
([C][O]浓度积只有3#炉数据))2.2复吹工艺对终渣氧化性的影响采用复吹工艺之后,由于熔池搅拌加强,使渣-钢间的反应更加趋于平衡,从而使渣中的TFe含量有所降低。
顶底复吹转炉炉底新型砌筑方式实践
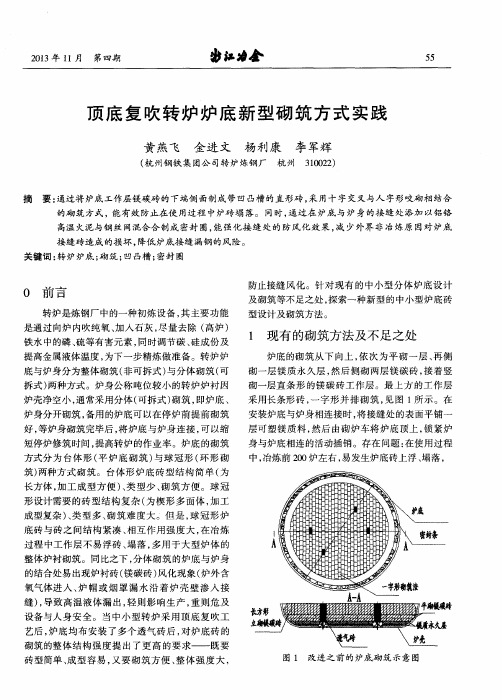
经分析认 为 : 在 炉役 初 期 , 砖 与砖 之 间没 有 烧
结成 一整 体 。 由于 含 碳 耐火 制 品 中鳞 片状 石 墨 的
层 面趋 向于垂直 受压方 向, 鳞片状 石 墨 的 晶体 结 构
特征 使其 热膨胀 性能各 向异性 , 层与 层 之 间的热 膨 胀率 比同一 层 内的膨 胀 率 大 得 多 。含 碳 耐火 制 品 中鳞 片石 墨定 向分 布 , 从 而使 含碳 耐 火 材 料 在 平 行 于受压 方 向上 的热 膨 胀 率大 于 垂 直 于 受 压方 向 的热 膨率 。 同一 块 砖 的成 型过 程 中加 压 方 向 的膨 胀 系数 比垂直成 型方 向大 得 多 。在 受 热时 , 对 于砌 筑 台体 的 直 条 形 砖 , 横 向与 纵 向 的 膨 胀 受 力 不 一 致, 砖发 生扭 曲 , 产生 膨 胀 缝 隙 。 由于镁 碳 砖 表 面 存 在石 墨 , 其表 面 光滑 , 摩 擦 系数小 , 在 砖 与砖 之 间 的刚性作 用 下 , 相互 挤压 缺乏 有效 的 变形 弹性 作 用
高温 火泥 与钢 丝 网混合合 制成 密 封 圈 , 能 强化 接 缝 处 的 防风 化 效 果 , 减 少外界 非 冶 炼 原 因对 炉 底
接缝 砖造 成 的损坏 , 降低 炉底接 缝 漏钢 的风 险 。
关 键词 : 转 炉 炉底 ; 砌筑; 凹 凸槽 ; 密封 圈 防止接 缝 风 化 。针 对 现 有 的 中小 型分 体 炉 底 设 计 及砌 筑等 不足之 处 , 探索一 种 新 型 的中小 型 炉底 砖
2 0 1 3 年1 1 月 第 四 期
全
5 5
顶 底 复 吹 转 炉 炉 底 新 型 砌 筑 方 式 实 践
黄 燕飞 金进文 杨利康 李军辉
- 1、下载文档前请自行甄别文档内容的完整性,平台不提供额外的编辑、内容补充、找答案等附加服务。
- 2、"仅部分预览"的文档,不可在线预览部分如存在完整性等问题,可反馈申请退款(可完整预览的文档不适用该条件!)。
- 3、如文档侵犯您的权益,请联系客服反馈,我们会尽快为您处理(人工客服工作时间:9:00-18:30)。
160t 顶底复吹转炉设计
一、转炉炉型设计
原始条件: 炉子平均出钢量160t 。
金属收得率取90%,最大废钢比取20%,采用废钢矿石冷却,铁水采用P08低磷生铁{w (si )≤0.85%,w (p )≤0.2%,w (s )≤0.05%}
1、熔池形状确定
转炉炉型有筒球型、锥球型、截锥型,熔池形状选用截锥型。
为了满 足顶底复吹的要求,炉型趋于矮胖型,由于在炉底上要设置底吹喷嘴,炉底为平底,所以熔池为截锥形。
2、炉容比确定
炉容比系指转炉有效容积t V 与公称容量T 之比值。
t V 系炉帽体积帽V 、炉身体积身V 、和容池体积c V 三个内腔容积之和。
由于顶底复吹转炉吹炼过程比较平稳,产生泡沫渣的量比顶吹转炉要少得多,喷溅较少,因此其炉容比比顶吹转炉小,但比底吹转炉要大。
根据冶炼条件取炉容比为0.95m 3/t 。
3、熔池尺寸的确定
熔池是容纳金属并进行一系列复杂物理化学反应的过程,其主要尺寸有熔池 直径和熔池深度。
设计时,应根据装入量、供氧强度、喷嘴类型、冶金动力学条件以及炉衬蚀损的影响综合考虑。
截锥型熔池尺寸如图(1)所示:
则其体积为: )(12h 2
112d Dd D V ++=
π熔 (1) 熔池直径D : 熔池直径通常指熔池处于平静状态时金属液面的直径。
D=K
t G =1.70×18160=5.068 式中G ——炉子公称容量,160t ;
t ——平均每炉钢纯吹氧时间,取18分钟;
K ——比例系数,根据炉子容量取1.70;
(2)熔池深度h :
根据经验,取D d 7.01== 3.548 其中熔池体积35.238.6160m G V c ==
=ρ 故熔池深度: 20.574c V h D == 2068.5574.05.23⨯=1.594 m 校核315.0068
.51.594/==
D h 符合要求 4、炉帽尺寸的确定 (1)炉帽倾角θ:本计算中取θ=60度
(2)炉口直径d :炉口直径为熔池直径的43~53%,本计算中取45%
则 d=45%D=0.45×5.068=2.281m
(3)炉帽高度H 帽:炉帽高度是截椎体高度与炉口直线段高度值和。
H 锥()θtg d D -=21=()m tg H 414.260281.25.0682
10=⨯-=帽 直线段高度H 口一般为300~400mm ,本计算中取H 口=400mm 。
则有 m H H H 814.24.0414.2=+=+=口锥帽 炉帽总容积为:3222m 46.824d d 12=+++=d H D D H V 直锥帽)(ππ
5、炉身尺寸确定
(1) 炉膛直径D 膛=D (无加厚段)
(2)根据选定的炉容比0.95m 3/t ,可求出炉子总容积为总V =0.95⨯160=152m 3 身V =总V -c V -帽V =152-23.5-28.46=100.04m 3
(3)炉身高度H 身
m 959.44/2
==D V H )(身身π 则炉型内高内H =h+帽H +身H =1.594+2.814+959.4=9.367m
6、出钢口尺寸确定
(1).位置
出钢时出钢口应处于钢液最深处,因此出钢口应设在炉帽和炉身内衬的交界处,以便当转炉处于水平位置出钢时其位置最低,这样钢水容易出净,又不容易下渣。
(2)出钢口中心线水平倾角θ:
出钢口角度是指出钢口中心线与水平显得夹角,,其大小应考虑缩短出钢口长度,有利维修、减少钢水二次氧气及热损失,大型转炉的出钢口角度趋向减小。
国外不少采用0°,但0°倾角使钢流对钢包内金属的冲力变小。
本设计取θ=18°
(3).出钢口直径T d :出钢口直径决定着出钢时间,因此随炉子容量而异。
出钢时间通常为2-8min 。
通常T d 可按下面经验公式确定:
0.19m 18.52cm 16075.16375G .163≈=⨯+=+=T d
式中:G —转炉公称容量,本计算中取160t
(4).出钢口衬砖外径:
ST d =6d T =6⨯0.19=1.14m
(5).出钢口长度:
L T =7d T =7⨯0.19=1.33m
二、 转炉炉衬设计
1、炉衬厚度:
炉身工作层选700mm,永久层115mm,填充层100mm,总厚度为700+115+100=915 mm
则炉衬外径即炉壳内径为D
=5.068+0.915×2=6.898m
壳内
炉帽和炉底工作层均选600mm,炉帽永久层为150mm,炉底永久层用标准镁砖立砌一层230mm,粘土砖平砌三层65×3=195mm;
则炉底砖衬总厚度为600+230+195=1025mm
故炉壳内型高度为
H=9.367+1.025=10.392m
1
工作层材质全采用镁碳砖。
2、材质:
选用沥青或树脂结合的镁碳转,含碳量为14%。
镁碳砖具有耐高温、耐渣侵和耐剥落等优良的使用性能。
与其他镁砖相比,在使用过程中变质层变薄,不至于引起砖体结构的剥落,加入相当的数量的石墨改善了砖的导热性能,具有良好的抗震性。
用镁碳砖砌筑炉衬,大幅度的提高了炉衬的使用寿命,再配合溅渣护炉等护炉技术,炉衬寿命可达1万次以上。
但由于镁碳砖成本较高,因此根据在冶炼过程中,工作层不同部位受损情况的不同,采用不同档次的镁碳砖,这样整个炉衬的受损情况较为均匀,就是综合砌炉。
(1).炉口部位。
该部位温度变化剧烈,熔渣和高温废气的冲刷较严重,在加料和清理残钢、残渣时。
炉口受到撞击,因此用于炉口的耐火砖必须具有抗热震性和抗渣性,耐熔渣和高温废气的冲刷,且不易粘钢的易于清理的镁碳砖。
(2). 炉帽部位。
该部位是受熔渣侵蚀最严重的部位,同时还受温度急变的影响和含尘废气的冲刷,故使用抗渣性强和抗热震性好的镁碳砖。
(3). 炉衬装料侧。
该部位除受吹炼过程熔渣和钢水时的直接撞击与冲刷、化学侵蚀外,还要受到装入料废钢和兑铁水时的冲蚀,给炉衬带来严重的机械性
损伤,因此应砌筑具有较高抗渣性、高强度、高抗热震性的镁碳砖。
(4).炉衬出钢侧。
此部位主要是受出钢时钢水的热冲击和冲刷作用,损坏速度低于装料侧,所以可砌筑档次低一些的镁碳砖,并且砌筑厚度可薄一些。
出钢口除受高温钢水的冲刷外,还经受温度急变的影响,蚀损严重,需要经常更换,影响冶炼时间,而出钢口则采用等静压成型的整体镁碳砖出钢口,整体结构方便更换。
(5).渣线部位。
此部位在吹炼过程中,炉衬与熔渣长期接触受到严重侵蚀而形成。
在出钢侧渣线位置的变化并不明显,但在排渣侧受到熔渣的强烈侵蚀,再加上吹炼过程中其他作用的共同影响,衬砖损毁较为严重,应砌筑抗渣性良好的镁碳砖。
(6). 两侧耳轴部位。
该部位出受吹炼过程的蚀损外,其表面又无保护渣层覆盖,砖体中的碳素极易被氧化,并难于修补,因而损坏严重。
故此部位应砌筑抗渣性好、抗氧化性能强的高级镁碳砖。
(7).熔池和炉底部位。
此部位炉衬在吹炼过程中受钢水强烈冲蚀,并且采用顶底复吹工艺,炉底中心部位容易损毁,可与装料侧砌筑相同材质的镁砖。
炉衬由永久层、填充层和工作层组成。
无绝热层时,永久层紧贴炉壳,修炉时一般不予拆除,作用是保护炉壳,常用镁砖砌筑。
填充层介于永久层与工作层之间,一般用焦油镁砂捣打而成,厚度约80~100 mm。
工作层与金属、熔渣和炉气接触的内层炉衬,工作条件相当恶劣,用高、中、低不同档次的镁碳砖砌筑。
炉帽可用二步煅烧镁砖。
三、转炉炉壳设计:
1、炉壳厚度确定:
查表选择:炉帽:65mm厚钢板
炉身:75mm 厚钢板
炉底:65mm 厚钢板
2、炉壳转角半径:
SR 1=SR 2=900mm
SR 3=0.5δ底=0.5×1025=510mm
3、验算高宽比:
由以上数据可计算得:H 总=10392+65=10457mm
D 壳=6898+2×75=7019mm
则: 壳总D H =7019
10457=1.49 由此可知,壳
总D H ≥1.3,符合高宽比的推荐值,因此所设计的炉子尺寸基本上是合适的,能够保证转炉的正常冶炼。