抽油机的设计与优化初步报告08656228
油田抽油机设计范文
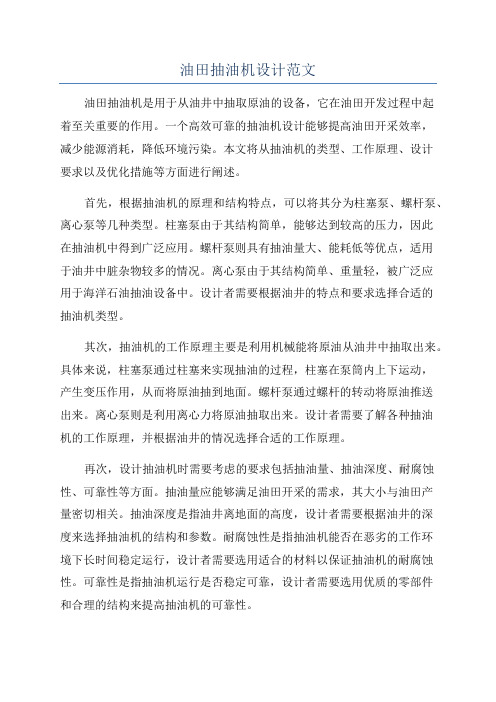
油田抽油机设计范文油田抽油机是用于从油井中抽取原油的设备,它在油田开发过程中起着至关重要的作用。
一个高效可靠的抽油机设计能够提高油田开采效率,减少能源消耗,降低环境污染。
本文将从抽油机的类型、工作原理、设计要求以及优化措施等方面进行阐述。
首先,根据抽油机的原理和结构特点,可以将其分为柱塞泵、螺杆泵、离心泵等几种类型。
柱塞泵由于其结构简单,能够达到较高的压力,因此在抽油机中得到广泛应用。
螺杆泵则具有抽油量大、能耗低等优点,适用于油井中脏杂物较多的情况。
离心泵由于其结构简单、重量轻,被广泛应用于海洋石油抽油设备中。
设计者需要根据油井的特点和要求选择合适的抽油机类型。
其次,抽油机的工作原理主要是利用机械能将原油从油井中抽取出来。
具体来说,柱塞泵通过柱塞来实现抽油的过程,柱塞在泵筒内上下运动,产生变压作用,从而将原油抽到地面。
螺杆泵通过螺杆的转动将原油推送出来。
离心泵则是利用离心力将原油抽取出来。
设计者需要了解各种抽油机的工作原理,并根据油井的情况选择合适的工作原理。
再次,设计抽油机时需要考虑的要求包括抽油量、抽油深度、耐腐蚀性、可靠性等方面。
抽油量应能够满足油田开采的需求,其大小与油田产量密切相关。
抽油深度是指油井离地面的高度,设计者需要根据油井的深度来选择抽油机的结构和参数。
耐腐蚀性是指抽油机能否在恶劣的工作环境下长时间稳定运行,设计者需要选用适合的材料以保证抽油机的耐腐蚀性。
可靠性是指抽油机运行是否稳定可靠,设计者需要选用优质的零部件和合理的结构来提高抽油机的可靠性。
最后,为了进一步提高抽油机的工作效率和节能效果,设计者可以采取一些优化措施。
例如,可以采用变频器来控制抽油机的转速,以适应不同抽油量的需求。
同时,设计者还可以采用高效能的电机和传动装置,来降低抽油机的能源消耗。
此外,还可以对抽油机的泵筒、柱塞等关键部件进行优化设计,以提高其耐磨性和耐腐蚀性。
综上所述,油田抽油机设计是一个综合性的工程项目,需要设计者充分考虑抽油机的类型、工作原理、设计要求以及优化措施等各个方面。
常规游梁式抽油机主要结构参数的优化设计

常规游梁式抽油机主要结构参数的优化设计常规游梁式抽油机是一种常用的输油装置,其主要结构参数的优化设计可以对其性能进行改进,提高其运行效率和可靠性。
本文将对常规游梁式抽油机主要结构参数进行优化设计,包括游梁长度、游梁截面形状和抽油杆直径等。
首先,游梁长度是常规游梁式抽油机中一个重要的结构参数。
游梁长度直接影响到抽油杆的行程和往复运动次数,在保证充分抽油的同时,要尽量减少杆件的磨损和能耗。
根据实际工况和抽油需求,可以通过模型计算和实验测试,得到最优的游梁长度。
一般而言,游梁长度应尽量适当,既能确保抽油杆的行程充分,又能减少抽油过程中的能耗和磨损。
其次,游梁截面形状也是常规游梁式抽油机的一个关键参数。
游梁截面形状直接影响到游梁的刚度和强度,进而影响到整个抽油机的运行性能。
对于游梁截面形状的优化设计,一方面可以通过有限元分析和疲劳试验来确定合适的截面形状,避免应力集中和疲劳破坏;另一方面,可以通过几何优化设计和材料选择,来改善结构的刚度和强度,提高抽油机的运行效率和寿命。
最后,抽油杆直径也是常规游梁式抽油机中一个重要的结构参数。
抽油杆直径直接影响到抽油杆的刚度和强度,进而影响到整个抽油机的运行效率和可靠性。
抽油杆直径的优化设计需要综合考虑抽油机的工作负荷、抽油深度和运行速度等因素。
一般而言,抽油杆直径应尽量适当,既能满足抽油机的工作需求,又能保证抽油杆的强度和刚度,避免因直径过大或过小而导致的过度磨损或破坏。
综上所述,常规游梁式抽油机的主要结构参数优化设计包括游梁长度、游梁截面形状和抽油杆直径等方面。
通过合理的优化设计,可以提高抽油机的运行效率和可靠性,减少能耗和材料磨损,延长抽油机的使用寿命。
优化设计要综合考虑抽油机的工作条件、工作负荷和运行速度等因素,采用合适的分析方法和试验手段,确保设计参数的准确性和可靠性。
抽油机系统动力性能分析与优化设计

抽油机系统动力性能分析与优化设计摘要:近年来,油田再用的抽油机总数高达数十万台,并且每年的抽油机需求量在6000台左右,对抽油机的质量要求也越来越高。
目前对抽油机机构尺寸的优化设计主要是最大扭矩因素和悬点最大加速度,这核心都是为了优化抽油机的动力性能,因此,通过对抽油机动力性能主要影响因素分析,选择最优的目标函数,正确优化设计计算抽油机,对提高抽油机采油效果和抽油设备技术经济指标有重要意义。
关键词:抽油机;动力性能;扭矩因素;平衡装置;曲柄旋转速度抽油机作为当前油田的主要采油设备,其动力性能的优劣性直接影响到石油的开采效果,对动力性能的研究分析,进而选择最优的目标函数,从而提高抽油机开采效率。
通过对抽油机系统动力性能影响的主要因素包扩有悬点加速度、扭矩因素、平衡方式、均方根扭矩等进行分析阐述,比较不同目标函数的优化结果进行分析对比,为抽油机机构优化设计方面起到参考作用1悬点加速度抽油机在正常工作时,因为它的悬点的最大加速度大小变动将会直接使抽油机的悬点最大载荷大小发生改变,所是衡量整体游梁式抽油机动力性能优越性的最常用指标之一。
如果悬点加速度一旦过大,便会加剧悬点载荷在上、下冲程中的载荷差,即抽油机在上冲程时它的载荷峰值会很高,而在下冲程时它的的载荷谷值又很小,因此就造成抽油机的悬点载荷曲线是比较难被平衡。
所以就这一方面来说,抽油机的悬点加速度的大小不但影响着悬点载荷扭矩的大小,而且还直接影响到抽油机平衡后的减速器净扭矩的曲线形态变化。
因此,在对抽油机的机构进行优化设计时,为了满足抽油机的“慢提快放”的工况需求,需要使上冲程的悬点加速度应用有两个必要的特点,一个是随着四连杆机构的曲柄转动时悬点加速度曲线的变化要缓慢,第二是需要在抽油机进行向上冲程时它的悬点最大加速度够小。
在抽油机运行的上冲程阶段,悬点加速度曲线如果兼有缓慢和小的特性,可以减少抽油杆柱和油液的摩擦以及油液与管壁的摩擦,降低悬点静载荷,同时悬点加速度的峰值降低,在其他条件不变的情况下直接减少了抽油机的动载荷。
抽油机井生产参数设计方法与优化调整对策

抽油机井生产参数设计方法与优化调整对策1. 引言1.1 研究背景石油是世界上最重要的能源资源之一,而抽油机是石油开采过程中最常用的工具之一。
抽油机井作为石油开采的重要环节,其生产参数设计与优化调整对石油生产效率和成本控制具有非常重要的意义。
研究表明,合理的抽油机井生产参数设计可以有效提高油田的采收率和产量稳定性,同时降低开采难度和成本。
由于石油地质条件、油层性质和井筒结构等因素的多样性,抽油机井的生产参数设计方法需要根据具体情况进行综合考虑和优化。
针对抽油机井生产参数设计方法与优化调整对策的研究具有非常重要的现实意义和实践价值。
通过深入研究和分析抽油机井生产参数的设计原理和优化调整方法,可以进一步提高油田的开采效率,降低生产成本,从而为石油行业的可持续发展做出贡献。
1.2 研究意义抽油机井是油田开发中常见的生产设备,其生产参数设计方法与优化调整对策对于提高油田生产效率具有重要意义。
研究抽油机井生产参数设计方法和优化调整对策,可以有效提高油井的生产效率和产量,减少生产成本,提高油田开发利润。
通过研究抽油机井生产参数设计方法和优化调整对策,可以更好地掌握油井的生产情况,及时发现问题并提出解决方案,保障油田生产正常稳定运行。
研究抽油机井生产参数设计方法和优化调整对策,也有助于提高油田开发的技术水平,推动油田产业的发展,对于国家能源安全和经济发展具有重要意义。
我们有必要对抽油机井生产参数设计方法与优化调整对策进行深入研究,以推动油田开发行业的发展与进步。
2. 正文2.1 抽油机井生产参数设计方法抽油机井生产参数设计方法是指在生产过程中对井口压力、产量、动态液面等参数进行合理设计和调整,以确保井的正常运行和高效生产。
在抽油机井生产参数设计中,需要考虑以下几个方面:1. 井口压力设计:井口压力是影响井内产量和油气流动的重要参数,合理设计井口压力可以提高生产效率。
在设计井口压力时,需要考虑地层特性、产能需求和设备性能等因素,采用合适的调节方式来实现压力控制。
游梁式抽油机连杆机构尺度优化及结构设计
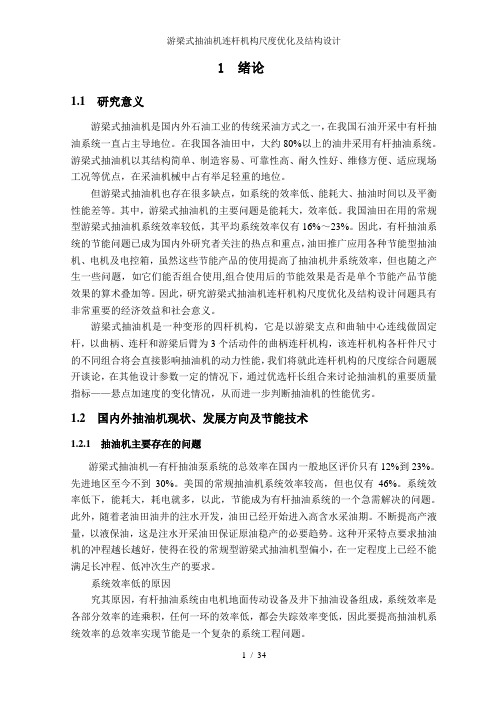
1绪论1.1 研究意义游梁式抽油机是国内外石油工业的传统采油方式之一,在我国石油开采中有杆抽油系统一直占主导地位。
在我国各油田中,大约80%以上的油井采用有杆抽油系统。
游梁式抽油机以其结构简单、制造容易、可靠性高、耐久性好、维修方便、适应现场工况等优点,在采油机械中占有举足轻重的地位。
但游梁式抽油机也存在很多缺点,如系统的效率低、能耗大、抽油时间以及平衡性能差等。
其中,游梁式抽油机的主要问题是能耗大,效率低。
我国油田在用的常规型游梁式抽油机系统效率较低,其平均系统效率仅有16%~23%。
因此,有杆抽油系统的节能问题已成为国内外研究者关注的热点和重点,油田推广应用各种节能型抽油机、电机及电控箱,虽然这些节能产品的使用提高了抽油机井系统效率,但也随之产生一些问题,如它们能否组合使用,组合使用后的节能效果是否是单个节能产品节能效果的算术叠加等。
因此,研究游梁式抽油机连杆机构尺度优化及结构设计问题具有非常重要的经济效益和社会意义。
游梁式抽油机是一种变形的四杆机构,它是以游梁支点和曲轴中心连线做固定杆,以曲柄、连杆和游梁后臂为3个活动件的曲柄连杆机构,该连杆机构各杆件尺寸的不同组合将会直接影响抽油机的动力性能,我们将就此连杆机构的尺度综合问题展开谈论,在其他设计参数一定的情况下,通过优选杆长组合来讨论抽油机的重要质量指标——悬点加速度的变化情况,从而进一步判断抽油机的性能优劣。
1.2 国内外抽油机现状、发展方向及节能技术1.2.1 抽油机主要存在的问题游梁式抽油机—有杆抽油泵系统的总效率在国内一般地区评价只有12%到23%。
先进地区至今不到30%。
美国的常规抽油机系统效率较高,但也仅有46%。
系统效率低下,能耗大,耗电就多,以此,节能成为有杆抽油系统的一个急需解决的问题。
此外,随着老油田油井的注水开发,油田已经开始进入高含水采油期。
不断提高产液量,以液保油,这是注水开采油田保证原油稳产的必要趋势。
这种开采特点要求抽油机的冲程越长越好,使得在役的常规型游梁式抽油机型偏小,在一定程度上已经不能满足长冲程、低冲次生产的要求。
抽油机井生产参数设计方法与优化调整对策
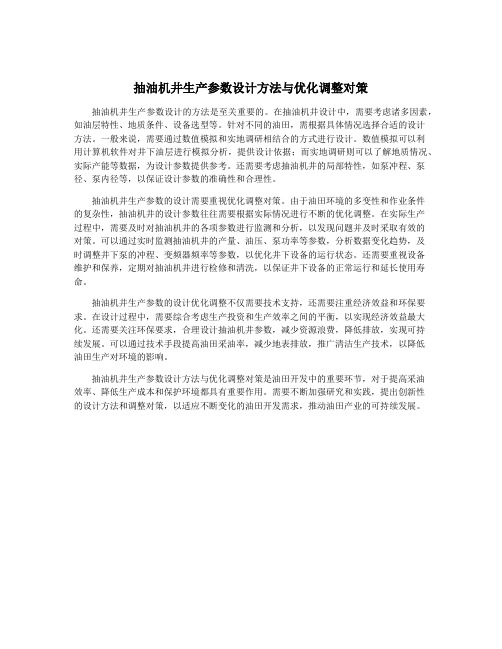
抽油机井生产参数设计方法与优化调整对策抽油机井生产参数设计的方法是至关重要的。
在抽油机井设计中,需要考虑诸多因素,如油层特性、地质条件、设备选型等。
针对不同的油田,需根据具体情况选择合适的设计方法。
一般来说,需要通过数值模拟和实地调研相结合的方式进行设计。
数值模拟可以利用计算机软件对井下油层进行模拟分析,提供设计依据;而实地调研则可以了解地质情况、实际产能等数据,为设计参数提供参考。
还需要考虑抽油机井的局部特性,如泵冲程、泵径、泵内径等,以保证设计参数的准确性和合理性。
抽油机井生产参数的设计需要重视优化调整对策。
由于油田环境的多变性和作业条件的复杂性,抽油机井的设计参数往往需要根据实际情况进行不断的优化调整。
在实际生产过程中,需要及时对抽油机井的各项参数进行监测和分析,以发现问题并及时采取有效的对策。
可以通过实时监测抽油机井的产量、油压、泵功率等参数,分析数据变化趋势,及时调整井下泵的冲程、变频器频率等参数,以优化井下设备的运行状态。
还需要重视设备维护和保养,定期对抽油机井进行检修和清洗,以保证井下设备的正常运行和延长使用寿命。
抽油机井生产参数的设计优化调整不仅需要技术支持,还需要注重经济效益和环保要求。
在设计过程中,需要综合考虑生产投资和生产效率之间的平衡,以实现经济效益最大化。
还需要关注环保要求,合理设计抽油机井参数,减少资源浪费,降低排放,实现可持续发展。
可以通过技术手段提高油田采油率,减少地表排放,推广清洁生产技术,以降低油田生产对环境的影响。
抽油机井生产参数设计方法与优化调整对策是油田开发中的重要环节,对于提高采油效率、降低生产成本和保护环境都具有重要作用。
需要不断加强研究和实践,提出创新性的设计方法和调整对策,以适应不断变化的油田开发需求,推动油田产业的可持续发展。
抽油机井生产参数设计方法与优化调整对策

抽油机井生产参数设计方法与优化调整对策随着石油资源的逐渐枯竭和全球能源需求的不断增长,抽油机井的生产参数设计和优化调整对策成为了石油行业中的重要课题。
抽油机井的生产参数设计直接影响着井底油藏压力、产油率、油井寿命等关键技术指标,科学合理地设计和优化调整抽油机井的生产参数对于提高油田开发效率、降低生产成本至关重要。
本文将从抽油机井生产参数设计方法和优化调整对策两个方面进行探讨。
一、抽油机井生产参数设计方法1. 根据油井地质条件进行评价在设计抽油机井的生产参数时,首先需要对油井所处的地质条件进行充分评价。
包括油井的地质构造、井底油藏压力、产层渗透率、岩石物性等方面的信息。
只有了解了这些地质条件,才能够进行合理的设计。
2. 选择合适的抽油机类型根据油井地质条件和产能需求,选择合适的抽油机类型是至关重要的。
不同类型的抽油机适用于不同的地质条件和产能需求,有的适合高产量的油井,有的适合稳产的油井。
3. 确定抽油机井生产参数在确定抽油机井生产参数时,需要考虑到井底油藏压力、井筒动液面、产层流动梯度、液面高度等因素。
通过合理的计算和分析,确定出最佳的生产参数。
4. 确定井下设备型号和数量根据井口条件和产能需求,确定适合的泵体型号和数量。
同时要考虑到抽油机井的石油工程投资和生产成本,选择适当的设备型号和数量。
5. 建立合理的生产参数调整机制在设计抽油机井生产参数时,要建立合理的调整机制,包括压裂井眼液面调整机制、泵装置改造机制、固井控制机制等。
这些机制的建立可以保证抽油机井生产参数的灵活调整,以适应油井实际生产情况。
二、抽油机井优化调整对策1. 根据抽油机井实际生产情况进行调整在抽油机井的优化调整中,需要根据油井实际的生产情况进行调整。
包括井底油藏压力、产油率、动液面位置等数据的监测和分析,及时调整生产参数。
2. 加强抽油机井维护管理加强对抽油机井的维护管理,包括定期对井下设备进行检修和更换,保持抽油机井的正常运行状态。
抽油机井生产参数设计方法与优化调整对策

抽油机井生产参数设计方法与优化调整对策随着石油开采的不断深入,油田的开发难度也越来越大,尤其是对于采用抽油机井的油田来说,如何合理设计生产参数、优化调整对策成为了当前油田开发中亟待解决的问题。
抽油机井是一种采油工艺设备,通过抽油机将油井中的原油提升到地面,为油田生产提供了便利条件。
本文将针对抽油机井生产参数设计方法与优化调整对策进行探讨分析。
一、抽油机井生产参数设计方法1. 确定生产井的产量目标生产井的产量目标是在设计抽油机井生产参数时的首要考虑因素。
根据油田的地质条件和储量情况,以及生产井的类型和特点,确定合理的产量目标对于设计生产参数至关重要。
产量目标的设定应综合考虑油层压力、产能条件、油田开发计划等因素,以达到最大限度地提高油田的生产效益。
2. 分析地质条件及产能数据在确定了生产井的产量目标后,需要对油田的地质条件和产能数据进行详细分析。
地质条件的分析包括油层压力、油层岩性、渗透率、孔隙度等方面的信息。
产能数据的分析包括油井的有效产能、油井的产液量、抽油机的实际扬程等方面的信息。
通过对地质条件和产能数据的分析,可以为设计生产参数提供科学的依据。
3. 确定抽油机类型和参数根据地质条件和产能数据的分析结果,选择合适的抽油机类型和参数。
抽油机的选择应考虑到油井的产量目标、油层压力、油井产液量等因素,而抽油机的参数设计应兼顾抽油机的功率、扬程、效率等方面的要求。
通过合理选择抽油机类型和参数,可以提高抽油机井的生产效率和节约生产成本。
4. 设计抽油机井的工作制度在确定了抽油机类型和参数后,需要设计抽油机井的工作制度,包括抽油机的启停时间、工作负荷、运行方式等方面的内容。
工作制度的设计应充分考虑到油田地质条件和抽油机要求,既能保证抽油机的正常运行,又能提高抽油机井的生产效率。
1. 不断精细调整生产参数抽油机井的生产参数不是一成不变的,需要根据油田的实际情况进行不断的精细调整。
在实际生产中,通过对抽油机井的工作制度、抽油机参数等方面的优化调整,可以提高抽油机井的生产效率和油田的产量水平。
- 1、下载文档前请自行甄别文档内容的完整性,平台不提供额外的编辑、内容补充、找答案等附加服务。
- 2、"仅部分预览"的文档,不可在线预览部分如存在完整性等问题,可反馈申请退款(可完整预览的文档不适用该条件!)。
- 3、如文档侵犯您的权益,请联系客服反馈,我们会尽快为您处理(人工客服工作时间:9:00-18:30)。
抽油机的设计与优化初步报告08656228抽油机的设计与优化初步报告第1章概述1.1抽油机的类型、特点和应用采油设备分公司的产品有:干扰平衡游梁抽油机,偏轮游梁式抽油机,塔式节能抽油机。
干扰平衡游梁抽油机:是一种新型的节能抽油机。
不仅保持了常规游梁抽油机结构简单、可靠耐用的优点,而且具有附加动载小,能耗低,综合效率高,比常规抽油机节电30-50%以上,能延长整机使用寿命的特点。
如14干扰平衡机只需要配37千瓦电机及53KN减速箱。
如图1.1-1:图 1.1-1 干扰平衡游梁抽油机图1.1-2 塔式节能抽油机塔式节能抽油机:高效、节能、冲程、冲次在额定范围内无级调节,并可内设无线集中监控接口,通过配套设施实现遥控。
该机调参简易、维护方便、安全可靠、维护费用低,与常规抽油机相比节能50%以上,是一种智能型的节能抽油机,如图1.1-2。
偏轮游梁式抽油机:该抽油机是在常规游梁抽油机的基础上,在游梁尾部配置一偏轮,以偏轮为中心形成一六连杆机构,能很好的改善抽油机的运动性能。
在相同情况下,与常规抽油机相比:1.悬点动负荷减小,最大线速度小;2.减速箱输出扭矩减小30%-50%;3.节能37%以上;4.所配电网容量减少30%以上,如图1.1-3。
常规游梁式抽油机:该机型在设计中严格执行API标准,其特点是结构简单、可靠性好、适用型强如图1.1-4。
图 1.1-3 偏轮游梁式抽油机图1.1-4 常规游梁式抽油机1.2 抽油机的现状及发展方向随着石油机械匍造水平的不断提高,各种新型抽油机的开发和推广应用也取得了新的进展。
据有关资料统计,我国目前抽油机井约占机械采油井总数的92.2%,主要是采用游粱式抽油机。
这种抽油机具有结构简单、管理方便、操作和维修容易等特点,在今后很长一段时期内,仍将在我国机械采油中占主导地位。
为了节能增产,首先要改造现有常规游粱式抽油机,同时加速开发各种新型节能游粱式抽油机和各类长冲程无游梁抽油机,并继续研制液压抽油机,这对发展我国石油工业,具有十分重要的意义,本文试图对我国抽油机的现状及与国际先进水砰的差距做一概述,并对我国抽油机的发展方向提出几点建议。
1.2.1我国抽油机的现状目前,我国抽油机主要制造厂有十几家,产品主要以游梁式抽油机为主,约占抽油机总数的98%~99%,有30多种规格,并已形成了系列,基本上满足了陆地油田开采的需要各种新型节能游粱式抽油机,如前置式抽油机、异相曲柄平衡抽油机、前置式气平衡抽油机、配有CJT型节能拖动装置的常规抽油机和用窄V 形带传动的常规抽油机等均已在全国各个油羽推广应用,井取得了显著的经济效益。
长冲程、低冲次的无游梁式抽油机的研制也取得了一些进展,如由胜利油用设计并与有关厂家协作生产的链条式长冲程抽油机,已有近千台在各油田投入使用,在低冲次抽油和抽稠油方面已初见成效。
此外,桁架结构的滑轮组增距式抽油机、滚筒式长冲程抽油机进入了试用阶段;齿轮增距式长冲程抽油机的研制工作也取得了新的进展.重量轻、成本低、便于调速和调整冲程的液压抽油机,经过几年的研制和工业性试采油,也积累了一定的经验。
其它型式新颖的抽油机,如带传动游梁式抽油机、新型摇轷抽油机、大轮式游粱抽油机,六连杆游粱式抽油机和斜并抽油机也正处于开发和研制过程中。
然而,游粱式抽油机的缺点是不容易实现长冲程低冲次的要求,因而不能满足稠油井、深抽井和吉气井采油作业的需要。
同时,长冲程低冲次的无游梁式抽油机的性能尚有待完善度不足容易变形等问题),而且品种规格还很少,不能适应当前石油工业的发展。
液压抽油机至今仍处在研制阶段。
1.2.2我国抽油机与国际先进水平的差距1.新型节能抽油机发展缓慢目前,我国各油田使用的如前所述5种节能型抽油机,有些是刚从试制阶段过渡到使用阶段,仅就前3种抽油机来看,品种规格还不全,批量生产量还很少,因此全面推广应用受到一定限制。
如我国目前生产的前置式抽油机只有12型和16型两种规格,迄今仅有500多台在油田使用.而美国Lu in公司1959年就取得专利的马克Ⅱ型抽油机(即前置式抽油机),目前有8个档次46种规格。
罗马尼亚的前置式抽油机也有35种规格。
我国的第一批异相曲柄平衡抽油机是1986年6月通过部级鉴定的,现在只有为数不多的厂家生产.而早在60年代美国CMI公司就采用计算机模拟动态分析辅助设计研制出了异相曲牺平衡抽油机;。
由于这种抽油机具有许多优点,其经济指标已达到了目前在用抽油机的最好水平,因而在世界范围内获得了广泛的应用.我国生产的前置式气平衡抽油机目前仅有6种规格,悬点载荷为50~ 140kN,冲程为1.8~ 5mH。
53 o 而美国勒夫金公司生产的前置式气平衡抽油机删有26种规格,悬点载荷为48,47~ 213.19kN,冲程为1.37~ 6.10 .1。
国外上述几种节能型抽油机还广泛地采用了先进的数控系统,从而能保证采油作业始终处于最佳状态。
与此同时,有些国家还先后研制了许多型式新颖的节能抽油机。
如美国Jo—Way工具公司研制的一种前置式全胶带传动无齿轮减速器抽油机,称为大圈抽油机,是采用一个装在曲柄上直径为3.05m 的胶带轮来传动的,具有运行平稳、扭矩均衡和良好的节能效果。
美国D.L M 钢铁公司研制的一种特殊结构型式的轮式抽油机,只需一台2.2~ 7.4kW 的电动机就可以驱动,现场使用情况表观,可节电80%。
另外,还有其它型式的如齿形胶带传动抽油机、天然气发动机驱动抽油机、智能抽油机和玻璃钢抽油杆抽油机等节能型抽油机.这些抽油机应用于世界各个地区、各种工况条件下的抽油作业,均取得了良好的节能效果。
2.长冲程抽油机的发展速度不能适应采油业的需要目前,我国常用的长冲程抽油机的冲程一般不超过5m(宝鸡石油机攘厂生产的目前国内最大型号的CYJQ16⋯6 105B前置式抽油机,其最大冲程为6m),故我国大多数把冲程超过4.5m的称为长冲程抽油机.目前我国油田在用的绝大部分长冲程抽油机的冲程均在5m以下,且种类不多,规格不全,发展速度缓慢.如我国的链条式长冲程抽油机,早在60年代就开始研制,由于多方面原因,直到最近几年才初步在各油田推广应用而冲程超过6m 的国产长冲程抽油机如KCJ16— 8—53Hz抽油机和LzCJ12— 7.2— 73HB抽油机,仍处在试用阶段。
但在国外,自70年代Ll来,长冲程抽油机(国外系指冲程超过6m 的抽油机为长冲程抽油机)的开发和推广应用则得到了很大的发展,有些抽油机的冲程已达到20m 以上,并已发展到多品种、系列化.如美国国民供应公司生产的链条斌长冲程抽油机,冲程为9.14m,冲数为3min’,同时还采用微机监控井下泵的工作情况“。
该公司研制的世界上第一台智油机,总高仅2,44m,其最大冲程却已经达到12.19m,冲程长度可以进行调节.而WesternGear公司生产的液压驱动、重锤平衡(重锤置于一事先挖好的鼠洞内)的长冲程抽油机,能抽冲程可达24.38m,悬点载荷为l55.6kN0。
3.液压抽油机仍处于研制阶段我国液压抽油机的起步较晚,加之我匣液压技术水平与国际先进水平存在着差距,从而阻碍了液压抽油机的发展。
山吉林工业大学研制的第一台国产液压抽油机1987年底通过工厂台架试验,经试乐运行,发现存在不少问题,如漏油、发热、可靠性差,连续运行间远远低于游梁式抽油机,关键液压元件的质量较差等。
加之液压抽油机的维护保养比游粱式抽油机复杂得多,从而阻碍了其推广应用。
早在40年代,美、苏就已先后研制出液压抽油机(美国Lufkin公司曾经生产出4种型号、最大悬点载荷1 58kN、冲程为6.1~ 12.2 m 的液压抽油机。
苏联全苏石油机械研究院和阿塞拜疆石油机械研究所也先后试制成3种型号、悬点载荷30~ 1 50kN,冲程3~ 10 rn的液压抽油机) 。
随着液压技术的发展,国外液压抽油机的研制和推广应用近年来又有了新的发展。
如加拿大热能发展有限公司研制的液缸式无游梁抽油机,特别适于用来开采稠油。
这种抽油机悬点载荷为57.57~106.75kN,冲程为2.79~ 4.88m,并配有电了控制监测系统,用控制抽油机冲程及冲程位置、冲程参数,监控抽油杆足否过载,确保抽油系统安全运行。
美国Mape公司生产的液压驱动塔架式长冲程抽油机,有6种规格,其冲程可以从2.5m 调到10m,并可在0~ 5min 范围内任意调节冲程次数。
这些液压抽油机已广泛地应用于油田采油作业中。
1.2.3有关我国抽油机发展方向的几点建议1.改造现有常规游粱式抽油机,加速开发新型节能抽油机。
2.加速开发各类长冲程无游粱式抽油机。
3.继续加紧研制液压抽油机。
第2章常规游梁式抽油机传动方案设计2.1简述系统的组成工作原理2.1.1系统的组成系统的结构图见图2.1-1图2.1-1 常规游梁式抽油机的组成(1)刹车装置:刹车也叫制动器,它是由手刹车中间座、拉杆、锁死弹簧、刹车轮、刹车片等部件组成。
刹车片与车轮接触时发生摩擦起到制动作用。
(2)电动机:电机是动力的来源,一般采用感应式三相交流电动机。
(3)曲柄:它是由铸铁铸就的一个部件,装在减速器输出轴上。
曲柄上开有大小冲程的孔眼叫冲程孔,专门为调节冲程所用。
(4)平衡块:是由铸铁铸就的一个部件,上有吊孔,它是由螺丝固定在曲柄上的能产生旋转惯性,起着驴头上下运动负荷平衡的作用,可在曲柄上前后调整达到抽油机前后平衡。
(5)连杆:特的作用是曲柄与横梁之间的连接杆件。
(6)尾轴承:它起着横梁和游梁相连的作用,减小摩擦使游梁上下运动较轻便。
(7)减速箱:它是把高速的电动机转变成低速运动的减速装置,现场多采用三轴两级减速。
(8)支架:支架支撑着游梁全部重量和它所承担的重量,而且是游梁的可靠支柱。
(9)游梁:它安装在支架轴承上,绕支架轴承上下摆动,尾端通过为轴承与横梁连接在一起,前端装有驴头,游梁可前后移动调节,以便使驴头始终对准井口。
(10)驴头:它装在游梁最前端,驴头为弧面,它的弧线是以支架轴承为圆心,以游梁前臂长为半径画弧而得到的。
它保证了抽油时光杆始终对正井口中心。
驴头担负着井内抽油杆、泵摩擦阻力及液体的重量。
(11)悬绳器:也叫绳辫子,它是悬挂抽油杆的,为了使光杆在抽油过程中处于周定油井中心位置,因此它本身是柔性结构,在运动中使光杆始终对正井口中心。
驴头担负着井内抽油杆、泵摩擦阻力及液柱的重量。
(12)底座:它是担负起抽油机全部重量的唯一基础。
下部与水泥混凝土的基础由螺栓连接成一体,上部与支架、减速器有螺栓连接成一体。
2.1.2系统的工作原理电动机将其高速的旋转运动通过皮带传动传递给减速箱的输入轴,经减速箱减速后变为曲柄的低速旋转运动。
同时曲柄通过连杆装置经横梁拉着游梁后壁摆动。
游梁前端装有驴头,活塞以上液柱及抽油杆柱等载荷均通过光杆与悬绳器连接悬挂在驴头上。