2.1-2.2铸件缺陷分析与质量控制
铸造铸件常见缺陷原因与解决方法分析

铸造铸件常见缺陷原因与解决方法分析前言铸造工艺过程复杂,影响铸件质量的因素很多,往往由于原材料控制不严,工艺方案不合理,生产操作不当,管理制度不完善等原因,会使铸件产生各种铸造缺陷。
常见的铸件缺陷名称、特征和产生的原因,详见下表。
★ 常见铸件缺陷及产生原因★缺陷名称特征产生的主要原因气孔在铸件内部或表面有大小不等的光滑孔洞①炉料不干或含氧化物、杂质多;②浇注工具或炉前添加剂未烘干;③型砂含水过多或起模和修型时刷水过多;④型芯烘干不充分或型芯通气孔被堵塞;⑤春砂过紧,型砂透气性差;⑥浇注温度过低或浇注速度太快等缩孔与缩松缩孔多分布在铸件厚断面处,形状不规则,孔内粗糙①铸件结构设计不合理,如壁厚相差过大,厚壁处未放冒口或冷铁;②浇注系统和冒口的位置不对;③浇注温度太高;④合金化学成分不合格,收缩率过大,冒口太小或太少砂眼在铸件内部或表面有型砂充塞的孔眼①型砂强度太低或砂型和型芯的紧实度不够,故型砂被金属液冲入型腔;②合箱时砂型局部损坏;③浇注系统不合理,内浇口方向不对,金属液冲坏了砂型;④合箱时型腔或浇口内散砂未清理干净粘砂铸件表面粗糙,粘有一层砂粒①原砂耐火度低或颗粒度太大;②型砂含泥量过高,耐火度下降;③浇注温度太高;④湿型铸造时型砂中煤粉含量太少;⑤干型铸造时铸型未刷涂斜或涂料太薄夹砂铸件表面产生的金属片状突起物,在金属片状突起物与铸件之间夹有一层型砂①型砂热湿拉强度低,型腔表面受热烘烤而膨胀开裂;②砂型局部紧实度过高,水分过多,水分烘干后型腔表面开裂;③浇注位置选择不当,型腔表面长时间受高温铁水烘烤而膨胀开裂;④浇注温度过高,浇注速度太慢铸件沿分型面有相对位置错移①模样的上半模和下半模未对准;②合箱时,上下砂箱错位;③上下砂箱错型未夹紧或上箱未加足够压铁,浇注时产生错箱冷隔铸件上有未完全融合的缝隙或洼坑,其交接处是圆滑的①浇注温度太低,合金流动性差;②浇注速度太慢或浇注中有断流;③浇注系统位置开设不当或内浇道横截面积太小;④铸件壁太薄;⑤直浇道(含浇口杯)高度不够;⑥浇注时金属量不够,型腔未充满浇不足铸件未被浇满裂纹铸件开裂,开裂处金属表面有氧化膜①铸件结构设计不合理,壁厚相差太大,冷却不均匀;②砂型和型芯的退让性差,或春砂过紧;③落砂过早;④浇口位置不当,致使铸件各部分收缩不均匀★ 常见铸件缺陷及预防措施★序缺陷名称缺陷特征预防措施1 气孔在铸件内部、表面或近于表面处,有大小不等的光滑孔眼,形状有圆的、长的及不规则的,有单个的,也有聚集成片的。
铸造工艺流程中的铸件缺陷分析与改进策略

铸造工艺流程中的铸件缺陷分析与改进策略铸造工艺是一种重要的金属加工方法,用于制造各种形状的金属件。
然而,在铸造过程中,铸件缺陷是一个常见的问题,它会影响到铸件的质量和性能。
因此,对于铸造工艺流程中的铸件缺陷进行深入分析,并提出改进策略,对于提高铸件质量和工艺效率具有重要意义。
一、铸件缺陷的分类与原因分析在铸造工艺中,铸件缺陷可以分为表面缺陷和内部缺陷两类。
常见的表面缺陷包括气孔、砂眼、砂洞等;内部缺陷主要有夹杂物、孔洞、收缩系数不均匀等。
1.1 气孔气孔是铸造工艺中最常见的表面缺陷之一。
其形成的原因通常有两个方面,一是液态金属中溶解气体含量过高,二是在金属凝固过程中,气体生成而未能有效排除。
造成气孔的常见因素包括砂芯质量不佳、浇注温度过高、浇注速度过快等。
1.2 砂眼和砂洞砂眼是指铸件表面局部凹陷的缺陷,而砂洞是指铸件内部或边缘凹陷的缺陷。
主要原因包括模具缺陷、浇注系统设计不合理、浇注金属温度过低等。
1.3 夹杂物夹杂物是指铸件中存在的杂质,如炉渣、油污等。
其主要原因包括铁水净化不彻底、砂芯质量不佳等。
1.4 孔洞孔洞是指铸件内部存在的封闭空腔。
常见的孔洞形式包括气孔和收缩孔。
造成孔洞的原因主要有铁水中含气量高、铸型泥浆含水量高等。
1.5 收缩系数不均匀收缩系数不均匀是指铸件不同部位的收缩量不一致。
这可能会引起铸件的内部应力集中,从而导致开裂和变形。
收缩系数不均匀的原因包括铸造合金的特性、浇注温度的控制等。
二、改进策略为了减少铸件缺陷,提高铸件质量和工艺效率,以下是一些改进策略的具体措施:2.1 优化模具设计模具设计是影响铸件质量的关键因素之一。
通过优化模具结构、提高模具材料质量和表面光洁度,可以减少砂眼、砂洞等表面缺陷的产生。
2.2 控制浇注温度和速度浇注温度和速度对铸件质量有着直接的影响。
合理控制浇注温度和速度,可以降低气孔和夹杂物等缺陷的产生。
2.3 改进铸型材料和工艺选择合适的铸型材料,对铸件质量和工艺效率的提高至关重要。
压铸件缺陷与质量控制

压铸件缺陷与质量控制一.压铸件缺陷与消除措施压铸件缺陷按产生部位和性质分类可分为:•表面缺陷•内部缺陷•形状和尺寸缺陷•成分和性能缺陷•基体不连贯缺陷1.1 表面缺陷定义:压铸件表面上存在的瑕疵分类:表面流痕和花纹、网状毛刺及印痕、飞边、缩陷(凹陷)、粘模拉伤、划(碰)伤1.1.1 表面缺陷及消除措施(1)表面流痕及花纹特征:压铸件表面上有与金属液流动方向一致的条纹或与金属基体颜色不一样的无方向的纹路。
危害性:不影响产品的使用,打磨和喷丸可以消除原因:首先进入压铸模具型腔内的金属液形成极薄而又不完全的金属层后,被后来的金属液弥补而留下的痕迹。
消除措施:1)提高压铸模具温度2)适当降低压射速度3)调整脱模剂或减少用量4)调整内浇口截面面积或减少用量2)网状毛刺及印痕特征:在压铸件表面呈现网状发丝凸起或凹陷的痕迹(日常生产中的龟裂)危害性:不影响产品使用,但增加清理工作量原因:金属液流入模具型腔后,在压力作用下窜进模具龟裂纹中,凝固后形成网状毛刺。
消除措施:1)消除压铸模具表面龟裂纹2)适当降低浇注温度或压铸模具温度3)调整顶杆长度或型腔相关零件的配合间隙(3)飞边特征:分型面位置出现层状金属薄片,由压铸件向外延伸危害性:增加清理量、影响产品致密性、产品尺寸精度原因:1)压铸机锁模力不够,造成涨形2)压铸模具或滑块闭合不严3)压铸模具和合金液温度高、压射速度过快、压射比压过大消除措施:1)清理压铸模具分型面2)降低压射速度、压射比压、浇注温度、模具温度3)检查压铸机合模机构和合模力4)修整压铸模具4)缩陷(凹陷)特征:在压铸件厚、大部位的表面上有平滑的凹陷区危害性:减小产品有效壁厚,承载力低,影响使用和外观原因:局部过热,比周围金属液凝固慢,体积减小下凹,局部困气造成消除措施:1)改善模具的热分布,加大脱模剂喷涂量,设置冷却装置2)提高压射比压3)改善型腔排气条件4)消除压铸件厚大断面(5)气泡特征:压铸件表皮下有气体聚集,在表面鼓泡危害性:一般不影响产品使用,不可用于需要电镀和热处理的产品原因:1)压射过程中卷入的气体和脱模剂产生的气体2)合金液本身包含的气体滞留在压铸件表皮下消除措施:1)提高压室充满度,减少压室中的气体2)降低第一阶段压射速度,调整低速/高速压射转换位置,减少卷气3)降低压铸模具温度或延长开模时间4)更换脱模剂或减少用量5)对合金液精炼除气,降低含气量6)改善内浇口、溢流槽、排气道的排气条件(6)冲蚀特征:压铸件局部位置、浇口附近有麻点或凸纹危害性:可以打磨和喷丸去除,但对电镀和表面粗糙度低的产品要求严格原因:浇注系统设计不当,造成金属液对压铸模具局部冲刷和模具局部温度过高消除措施:1)降低压铸模具温度和压射速度2)修复压铸模具冲蚀部位并加强冷却3)改变浇注系统7)机械拉伤特征:压铸件表面延出模方向留有擦伤的痕迹危害性:导致压铸件表面破坏,对受力件循环应力产生不利影响原因:脱模斜度不足、压铸件顶出时偏斜,模具型腔有损伤消除措施:1)增加压铸模具脱模斜度,修复型腔内表面损伤2)降低模具表面粗糙度,增加脱模剂用量3)调整顶出机构,使顶出平衡4)缩短开模时间(8)粘模拉伤特征:压铸件与型壁发生焊合粘连,脱出时压铸件被撕破拉伤危害性:导致压铸件表面破坏,对受力件循环应力产生不利影响原因:由于高温、高压或金属液过渡冲击模具型腔导致两者发生焊合消除措施:1)降低浇注温度和模具温度2)减低冲型速度和压射压力3)增加脱模剂用量,加强隔离作用4)改进浇注系统,在过热处增加冷却管道5)检查模具型腔表面硬度和修复受损表面6)检查合金中的Fe 含量是否低,低会导致金属液与型腔亲和力增加,导致粘模拉伤9)划(碰)伤特征:压铸件表面的擦痕和碰伤危害性:损害压铸件表面,影响应用原因:主要在取出、清理、搬运、装卸、运转过程中造成消除措施:各个工序环节小心作业1.2 内部缺陷定义:压铸件内部孔洞类缺陷分类:气孔、缩孔和缩松、夹渣及氧化皮1.2.1 内部缺陷及消除措施(1)气孔特征: 压铸件内部存在的气体形成的孔洞(具有光滑的表面,形状呈椭圆形或圆形危害性: 对压铸件的密闭性和整体性影响较大原因:压射过程中卷入的气体、脱模剂产生的气体、金属液本身包含的气体消除措施:1)提高压室充满度、减少压室气体2)降低压射速度,减小喷溅使气体排出充分3)提高增压压力,缩小气泡体积4)更换脱模剂,减小用量5)对合金液除气,控制熔化和浇注温度6)增大内浇口截面面积,修改溢流槽、排气道,改善排气条件2)缩孔和缩松特征:压铸件内部收缩形成的孔洞,形状不规则,表面不光滑的叫缩孔。
压铸产品质量缺陷分析及解决对策.ppt
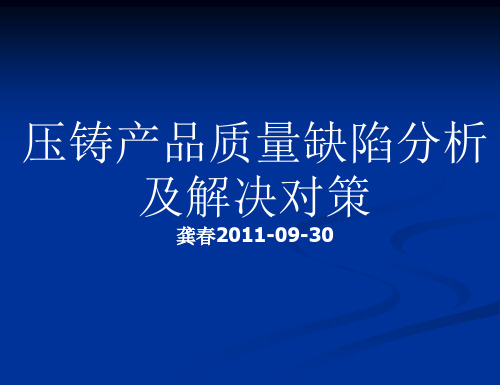
龚春2011-09-30
压铸件缺陷的控制措施 1 成形类缺陷 成形类缺陷主要发生在压铸件表面,大多可以目测看出。
欠铸和边角不清等缺陷与充填速度有关;流痕多出现在浇口附 近,除了与层流效应有关外,还和压铸模的温度有关;麻面、 冷隔等缺陷主要是由合金液温度过低而造成的,易出现在远离 浇口的涡流区和两股合金液流的交汇处,当改变浇口或提高合 金液的温度后就会消除。控制这类缺陷,除了要注意浇注系统 的设计外,更重要的是要选择合适的压铸工艺方法。目前常用 的压铸工艺方法有低温高速压铸法、高温低速压铸法和低温低 速压铸法等。低温浇注可减少合金液的烧损和炉具烧蚀,高速 压射可获得高质量的铸件表面,因此低温高速压铸法在铜合金、 铝合金的薄壁件生产中优点明显;高温低速压铸法主要用于壁 厚中等、易冲击型芯而又充填不良的压铸件上,较高的温度可 满足成形要求,较低的充型速度可降低合金液流对型芯的冲击 趋势;厚壁件的主要矛盾是气孔和保压补缩,常选用低温低速 压铸法。
1、 修理模具表面损伤处,修正斜度,600细油石顺磨提高光洁度0.4 2、 调整或更换顶杆,使顶出力平衡 3、 更换离型剂或加浓,改变喷涂角度特别是浇口直冲部位,比如Y43油底 壳、0627机盒、130右箱体等。 4、 调整合金含铁量,适当增加 5、 控制合适的浇注温度,控制模具温度,因为水基涂料成膜在170-350℃ 6、 修改内浇口,避免直冲型芯型壁或对型芯表面进行特殊处理 7、调整工艺参数:降低快压流量、降低压射力,能压好件的前提下,压力温 度越低越好
为了控制这类缺陷,除了要确保推出机构的推出 力分布均匀外,在进行浇口设计时还要特别注意合金 液流进入型腔时的导向,尽量避免合金液流正面冲击 型面和型芯,同时要选用适当的压铸工艺参数和稍长 的铸件留模时间。
铸件缺陷分析
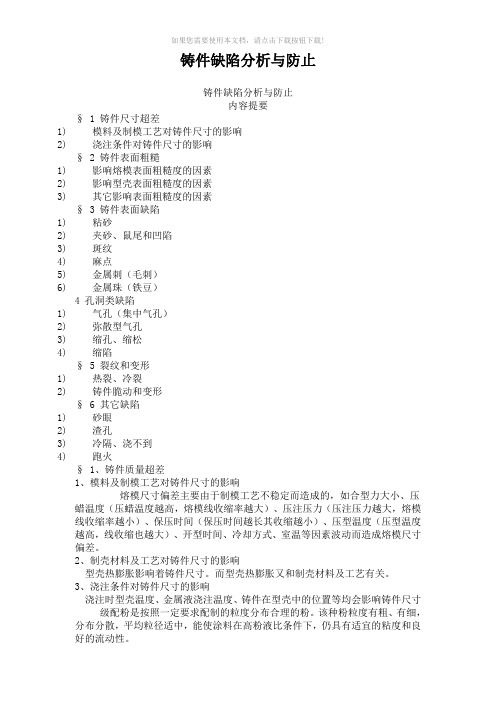
铸件缺陷分析与防止铸件缺陷分析与防止内容提要§ 1 铸件尺寸超差1) 模料及制模工艺对铸件尺寸的影响2) 浇注条件对铸件尺寸的影响§ 2 铸件表面粗糙1) 影响熔模表面粗糙度的因素2) 影响型壳表面粗糙度的因素3) 其它影响表面粗糙度的因素§ 3 铸件表面缺陷1) 粘砂2) 夹砂、鼠尾和凹陷3) 斑纹4) 麻点5) 金属刺(毛刺)6) 金属珠(铁豆)4 孔洞类缺陷1) 气孔(集中气孔)2) 弥散型气孔3) 缩孔、缩松4) 缩陷§ 5 裂纹和变形1) 热裂、冷裂2) 铸件脆动和变形§ 6 其它缺陷1) 砂眼2) 渣孔3) 冷隔、浇不到4) 跑火§ 1、铸件质量超差1、模料及制模工艺对铸件尺寸的影响熔模尺寸偏差主要由于制模工艺不稳定而造成的,如合型力大小、压蜡温度(压蜡温度越高,熔模线收缩率越大)、压注压力(压注压力越大,熔模线收缩率越小)、保压时间(保压时间越长其收缩越小)、压型温度(压型温度越高,线收缩也越大)、开型时间、冷却方式、室温等因素波动而造成熔模尺寸偏差。
2、制壳材料及工艺对铸件尺寸的影响型壳热膨胀影响着铸件尺寸。
而型壳热膨胀又和制壳材料及工艺有关。
3、浇注条件对铸件尺寸的影响浇注时型壳温度、金属液浇注温度、铸件在型壳中的位置等均会影响铸件尺寸级配粉是按照一定要求配制的粒度分布合理的粉。
该种粉粒度有粗、有细,分布分散,平均粒径适中,能使涂料在高粉液比条件下,仍具有适宜的粘度和良好的流动性。
3、影响金属液精确复型的因素(1)型壳温度对金属液复型的因素(2)浇注温度对金属液复型的因素金属液复印型壳工作表面细节的能力,即充型能力;在此简称为“复型”能力。
为使金属液能精确复型,就必须有足够高的型壳温度和金属液浇注温度,并保证金属液有足够的压力头。
提高型壳温度对改善金属液流动能力、复型能力均有良好效果,故型壳温度是应当予以重视的因素。
熔模铸造铸钢件用硅溶胶型壳,其焙烧温度达1150-1175℃,型壳出炉后迅速浇注,使铸件轮廓清晰,表面粗糙度低。
铸件缺陷分析与铸件质量检测_2
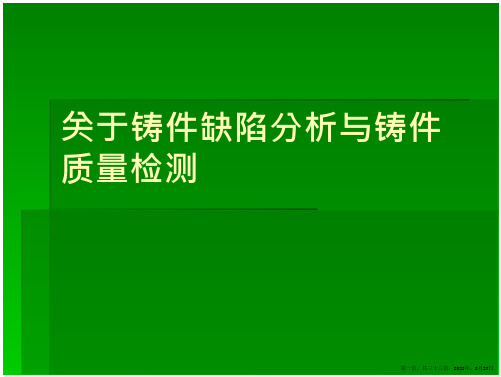
· 掉砂
1. 合箱后,上型面的砂粒,或砂块掉落,掉落的砂粒或砂
块落在下箱,浇注出来的铸件便会在上箱处有凸起的疤结 或多肉,下箱则会有密集砂眼或缺肉,而上多下缺的形状 基本相同。
2. 造型时,砂型紧实率不实处在起模时粘到模具上,假如合箱后, 会产生多肉,虽不至于废,但会给后续修磨带来很大麻烦,有 的必须用机加才能去除,得不偿失。此种情况在造型后,合箱 前,造型人员能够看得见,并且不能够合箱浇注,一定要重新 造型
(是较大的砂眼,对于此图也可以说是砂胎掉落,严重影响外观质量)
良品
不良品
典型的砂眼
第五页,共三十三页,2022年,8月28日
二、多肉类缺陷
· 抬型、抬箱
由于金属液的浮力使上型抬起,从而增加了铸件的厚度 解决办法:增加压箱铁重量,提高型砂强度,适 当降低浇 注温度,浇注时稳流浇注
· 披缝、飞边、毛翅
④金属成分(针对铸铁)
· 硅含量过高,铝量超标 · 球铁球化处理时,镁残留超标 · 金属液中硫、锰含量超标 · 添加废钢时卷入的氮气过多,易形成氮气孔
氮气孔与缩孔很难甄别,因为它的孔壁不是圆滑的, 并且也在铸件内部
第二十一页,共三十三页,2022年,8月28日
⑤熔化
· 炉料潮湿、锈蚀、油污严重
· 出炉口,浇包未完全烘干
· 球化不良
球墨铸铁在球化检验时呈现非球化状态。 · 球化衰退
球化检验时不同部位的石墨形态不一,有少量 球化,还有团絮状的,甚至出现与灰铁石墨类 似的形态(俗称:灰了)
产生球化不良和球化衰退的主要原因是,球化处 理不当,或浇注时间过长,如不是以上原因还 需查找原材料、球化剂等方面原因
第二十九页,共三十三页,2022年,8月28日
铸件质量评定与失效分析
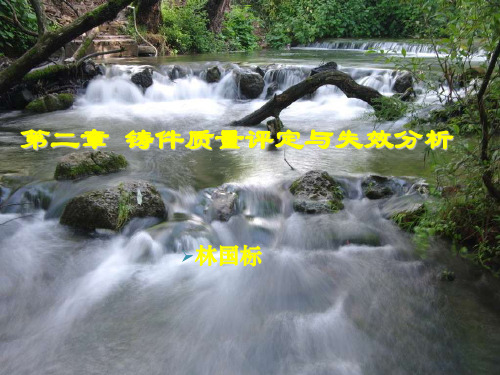
2.2 用“标准”评定铸件质量 是否合格
标准时由国家承认的标准制订单位批 准的对各种产品(铸件)规格、材料、试 验方法、术语定义或工艺方法的规定。 国家标准作为最基本要求,有时并不 能满足客户需求,企业就需要制订其自身 的标准,以对产品提出更高要求。
表2-1 铸件力学性能、化学成分、金相组织 标准
表2-2 铸件尺寸公差分等 (JB/JQ 82001-1992)
表2-3 铸件重量公差等级(JB/JQ 82001-1990)
表2-4 铸件浇冒口切割残余量分等 (JB/JQ82001-1990)
表2-5 铸件硫、磷含量分等(JB/JQ820011990)
2.3 用综合法评定铸件质量等级
对一个铸造工厂的铸件质量评定,不能 只看铸件的实物质量,还要注意铸件质量的 稳定性和可靠性。
我国铸造行业制定有《铸件质量评定方 法》标准(JB/T 7258),包括抽样的规定,检 测的项目、条件和方法。
铸件实物质量、技术管理和售后服务三 个方面综合评定铸件质量等级。
其中一质、品种不同而增减。 二级指标加权值之和等于1。 (1)有分等(分级)指标的质量项目,如 尺寸公差、表面粗糙度、重量公差、含硫量、 铝合金针孔、浇冒口残余量,评定标准表2-6所 示;
(2)对失效铸件在现场进行初步观察和分析
①观察其变形和表面情况,初步判断其受力 方向和应力状态; ②观察表面有无冷加工和热加工缺陷; ③观察是否有腐蚀和磨损造成的缺陷; ④观察断裂部位是否在铸件结构的应力集 中部位; ⑤观察失效铸件的断口和裂纹分布情况。
(3)对失效铸件进行检测试验,查清原因
(4)对失效铸件写出分析报告
第二章 铸件质量评定与失效分析
林国标
主要内容
2.1 铸件质量分类分等 2.2 用“标准”评定铸件质量
浅析铸钢件消失模铸造常见缺陷与防治措施
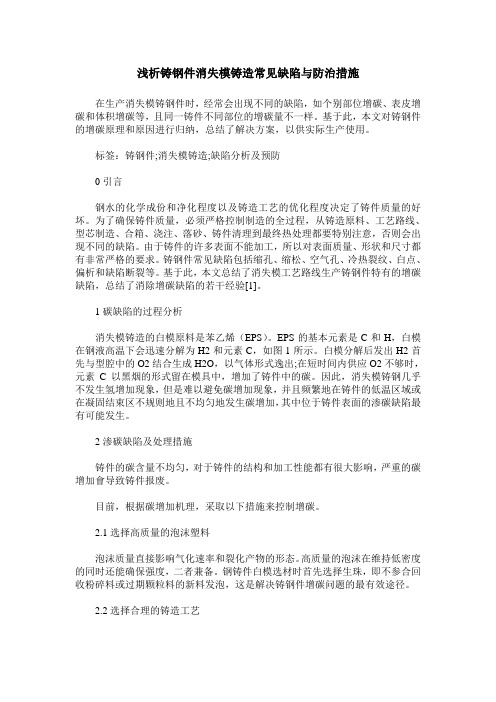
浅析铸钢件消失模铸造常见缺陷与防治措施在生产消失模铸钢件时,经常会出现不同的缺陷,如个别部位增碳、表皮增碳和体积增碳等,且同一铸件不同部位的增碳量不一样。
基于此,本文对铸钢件的增碳原理和原因进行归纳,总结了解决方案,以供实际生产使用。
标签:铸钢件;消失模铸造;缺陷分析及预防0引言钢水的化学成份和净化程度以及铸造工艺的优化程度决定了铸件质量的好坏。
为了确保铸件质量,必须严格控制制造的全过程,从铸造原料、工艺路线、型芯制造、合箱、浇注、落砂、铸件清理到最终热处理都要特别注意,否则会出现不同的缺陷。
由于铸件的许多表面不能加工,所以对表面质量、形状和尺寸都有非常严格的要求。
铸钢件常见缺陷包括缩孔、缩松、空气孔、冷热裂纹、白点、偏析和缺陷断裂等。
基于此,本文总结了消失模工艺路线生产铸钢件特有的增碳缺陷,总结了消除增碳缺陷的若干经验[1]。
1碳缺陷的过程分析消失模铸造的白模原料是苯乙烯(EPS)。
EPS的基本元素是C和H,白模在钢液高温下会迅速分解为H2和元素C,如图1所示。
白模分解后发出H2首先与型腔中的O2结合生成H2O,以气体形式逸出;在短时间内供应O2不够时,元素C以黑烟的形式留在模具中,增加了铸件中的碳。
因此,消失模铸钢几乎不发生氢增加现象,但是难以避免碳增加现象,并且频繁地在铸件的低温区域或在凝固结束区不规则地且不均匀地发生碳增加,其中位于铸件表面的渗碳缺陷最有可能发生。
2渗碳缺陷及处理措施铸件的碳含量不均匀,对于铸件的结构和加工性能都有很大影响,严重的碳增加會导致铸件报废。
目前,根据碳增加机理,采取以下措施来控制增碳。
2.1选择高质量的泡沫塑料泡沫质量直接影响气化速率和裂化产物的形态。
高质量的泡沫在维持低密度的同时还能确保强度,二者兼备。
钢铸件白模选材时首先选择生珠,即不参合回收粉碎料或过期颗粒料的新料发泡,这是解决铸钢件增碳问题的最有效途径。
2.2选择合理的铸造工艺为了防止白模气化和燃烧速度过快,模型装箱采取“能站不要躺”的原则,确保白模不会太快燃烧发气。
- 1、下载文档前请自行甄别文档内容的完整性,平台不提供额外的编辑、内容补充、找答案等附加服务。
- 2、"仅部分预览"的文档,不可在线预览部分如存在完整性等问题,可反馈申请退款(可完整预览的文档不适用该条件!)。
- 3、如文档侵犯您的权益,请联系客服反馈,我们会尽快为您处理(人工客服工作时间:9:00-18:30)。
合金在凝固过程中发生的化 学成分不均匀现象称为偏析 偏析主要是由于合金在凝固 过程中溶质再分配和扩散不 充分引起的. 偏析对合金的力学性能、抗裂性 及耐腐蚀性等有程度不同的损害。 但利用偏析现象可以净化或提纯 金属等。
• 为什么会出现偏析?
•
• 偏析的利弊?
第二章 铸件缺陷的形成因素
第一节 铸造合金因素 3、铸造合金的偏析与铸件缺陷
第二章 铸件缺陷的形成因素
第一节 铸造合金因素 1、铸造合金的液态特性与铸件缺陷 铸造合金在熔炼时,温度通常在液相线以上 100-400度。在这样的过热度状态下,金属液内部 形态与固态晶体类似,但晶格常数更大些。 处于高温的原子集团,不停地运动,此起彼伏 ,瞬息万变。宏观看,金属液是由原子集团和空穴 组成。从液态转变为固态时,原子集团联系紧密, 原来的空穴消失,加之晶体中晶格常数减小,导致 体积减小。从而在铸件内形成孔洞,使铸件产生缩 孔、缩松等缺陷。
由于密度的差异,
收缩孔 正偏析 逆V偏析 V偏析
负偏析
第8章 凝固缺陷与控制
图11-5 铸锭产生V形和逆V形 偏析部位示意图
15
第二章 铸件缺陷的形成因素
第一节 铸造合金因素 4、铸造合金的收缩过程与铸件缺陷
液态收缩阶段
三个阶段
凝固收缩阶段 固态收缩阶段
温 度 /℃
T浇
温 度 /℃
m
温 度 /℃
第二章 铸件缺陷的形成因素
第二节 冶金因素 金属液态温度与铸件缺陷 金属液态温度对铸件质量的影响,分为熔炼温度 与浇注温度两方面的影响。 1.熔炼温度 铸铁的熔炼温度是指出铁时的合适温度。 铁液的实用最低熔炼温度与牌号有关。低于这一 温度铁液会严重氧化。对于氧化严重的铁液,加人 孕育剂,则先起脱氧作用,结果铁液形核作用不足 ,孕育衰退过快;而且铁液夹杂物增加,使铸件的 力学性能下降;气孔、针孔的缺陷易于形成。
•
使用冒口、补贴和冷铁
温 度
纵向温度分布曲线
冒口
浇口
距离
顺序凝固方式示意图
21
温度
纵向温度分布曲线
I 内浇道
II
III
冷铁
距离
同时凝固方式示意图
22
第二章 铸件缺陷的形成因素
第二节 冶金因素 原材料品质与铸件缺陷 原材料特别是铁锭对铸件质量的影响,一直受 到关注。采用优质生铁生产的铸件,其性能容易 达标且缺陷少。 从铸铁遗传性的角度观察,三方面值得重视:一 是组织结构特征的保留;二是合金元素和微量元素 遗传效应;三是熔液的性质与铸锭缺陷的保存。 当然,铸铁的遗传性与生铁锭中所含的气体种 类与含量,夹杂物的种类与数量等,也是有相当 密切的关系。
第二章 铸件缺陷的形成因素
第一节 铸造合金因素 2、金属的凝固方式与铸件质量的关系
1)窄结晶温度范围的合金
这类合金包括纯金属、共晶成分合金 和其它窄结晶温度范围的合金 金属浇入铸型后,首先 在型壁处过冷,形成激冷 层,然后按柱状晶的形势 紧密生长,固相界面前沿 为平面推进的方式.
2 金属的凝固方式与铸件质量的关系
2、晶界偏析
• 在合金凝固过程中,溶质元素和非金属 夹杂物常富集于晶界,使晶界与晶内的化 学成分出现差异,这种成分不均匀现象称为 晶界偏析。
• 晶界偏析比晶内偏析的危害更大,既能降 低合金的塑性与高温性能,又增加热裂纹倾 向。
2、晶界偏析 • 晶粒并排生长, 晶界平行于晶体 生长方向,晶界 与液相的接触处 存在凹槽,溶质 原子在此处富集, 凝固后就形成了 晶界偏析。
n
液态收缩
凝固收缩
凝固收缩
固相收缩
III
I
II
III
I
II
A
n 成分/% a)
m
B
a)合金相图
体收缩率/% 体收缩率/% ) c) V凝=V ( Lb ( % S )+V(LS ) TL-TS ) 100 图11-14 二元合金收缩过程示意图 V固=V固 (TSc)恒温凝固的合金 T0 ) 100 % b)有一定结晶温度范围的合金
εV总=εV液+εV凝+εV固
其中,液态收缩和凝固收缩是铸件产
生缩孔和缩松的基本原因 。而固相收缩对
应力、变形与裂纹影响较大。
(二)防止铸件产生缩孔和缩松的途径
•
顺序凝固
铸件各部位由远及近,朝着帽口方向顺序凝固。 用于凝固收缩大、结晶间隔窄的金属。
•
同时凝固
凝固时产生热裂纹、变形倾向小。
用于凝固收缩小、对气密性要求不高的铸件。
第二章 铸件缺陷的形成因素
第二节 冶金因素 不同铸铁牌号的适宜温度
第二章 铸件缺陷的形成因素
第二节 冶金因素 金属液态温度与铸件缺陷 2.浇注温度的影响 浇注温度过高,则容易产生缩孔、缩松的缺陷。 浇注温度过低,容易产生气孔的缺陷。铸铁件浇注 温度一般在1395一1420℃之间。 在一定的生产条件下,对于不同的产品,应有 不同的最佳浇注温度范围。铸件产生气孔、夹杂物 缺陷和缩孔、缩松缺陷最少时,其浇注温度就是合 适的。
(弱)
冷却条件
(快)
二、宏观偏析
宏观偏析是指宏观尺寸上的偏析,包括: • • • 正常偏析 逆偏析 V形偏析和逆V形偏析
•
•
带状偏析与层状偏析
重力偏析
当铸锭中央部 分在凝固下沉 先凝固部分结晶沉 时,侧面向斜 淀,在铸锭的下半 下方产生拉应 部形成低于平均成 力,在其上部 形成逆V形裂缝, 分的负偏析区,上 并被富含溶质 部则形成高于平均 的液相所填充, 成分的正偏析区。 最终形成逆V形 00 %
(一)影响缩孔与缩松的因素 •
• • • 金属的性质 (收缩系数α大)
铸型的冷却能力 (蓄热系数b小) 浇注温度与浇注速度 铸件尺寸 (大) (高,快)
•
补缩能力 (弱)
• 例:铸铁的缩孔、缩松倾向
• 金属从浇注温度冷却到室温所产生的体收缩为液
态收缩、凝固收缩和固态收缩之和,即:
2、晶界偏析
• 晶粒相对生长,在对合 处彼此相遇。晶粒结晶 时所排出的溶质(k0< 1 )和其他杂质元素在 固 - 液界面前沿富积, 在最后凝固的晶界对合 部位将含有较多的溶质 和其他低熔点物质,造 成晶界偏析。
微观偏析的影响因素与消除措施
合金液、固相线间隔
(宽)
偏析程度 的影响因素
偏析元素的扩散能力
采用普通冒口消除缩松是很困难 的,往往采用其它措施,如增加 冒口的补缩压力,加速冷却等.
2 金属的凝固方式与铸件质量的关系
2)宽结晶温度范围的合金
(2)由于粗大的等轴晶较早成晶体骨 架,而粗大的等轴晶的高温强度低,当 晶间因收缩出现裂纹时,又得不到液态 金属的及时填充使之愈合,故铸件产生 热裂的倾向大; (3)若这类合金在充填过程中发生凝固, 其充型能力也很差。
2 金属的凝固方式与铸件质量的关系
2)宽结晶温度范围的合金 这类合金凝固区域 宽,过冷很小,容易 发展为树枝发达的粗 大等轴晶组织。
铝、镁合金 铝铜合金 铝镁合金 镁合金 铜合金 锡青铜 铝青铜 结晶温度范围 大黄铜 铁碳合金 高碳钢 球墨铸铁
(1)当粗大的等轴晶互相连 接以后,便将尚未凝固的液 态金属分割成一个个互不沟 通的溶池,最后在铸件中形 成分散性的缩松。
偏析的分类:微观偏析、宏观偏析 一、微观偏析
• 微观偏析是指微小范围(约一个晶粒范围)内的化学 成分不均匀现象,按位置不同可分为:
• •
晶内偏析(枝晶偏析) 晶界偏析
8
1、晶内偏析
• 晶内偏析是在一个晶粒内出现的成分不均 匀现象,常产生于具有结晶温度范围、能 够形成固溶体的合金中。 • 固溶体合金按树枝晶方式生长时,先结晶 的枝干与后结晶的分枝也存在着成分差异, 又称为枝晶偏析。
2.金属的凝固方式与铸件质量的关系
3)中等结晶温度范围的合金 这类合金常用的有中碳钢、高锰钢、白口铸铁等。凝 固区域为中等宽度,它们的补缩特性、热裂倾向性和充型 性能介于窄结晶温度范围合金和宽结晶温度范围合金之间。
第二章 铸件缺陷的形成因素
第一节 铸造合金因素 3、铸造合金的偏析与铸件缺陷
•
什么叫偏析?
1)窄结晶温度范围的合金
由于凝固前沿直接与液态金属接 触,当液态凝固成为固态而发生 体积收缩时,可以不断地得到液 体的补充,所以 ( 1)产生分散缩松的倾向小,而 是在铸件最后凝固部位留下集中 缩孔,设置冒口易消除。 ( 2)这类合金铸件在凝固过程中 当收缩受阻而产生晶间裂纹时, 也容易得到金属液的充填,使裂 纹愈合,所以铸件的热裂倾向小
第二章 铸件缺陷的形成因素
第二节 冶金因素 金属熔炼方式与铸件缺陷 铸铁的熔炼通常采用冲天炉、工频、中频感应电 炉和冲天炉—电炉双联熔炼。 1)工频炉熔炼的铁液温度可调节范围大,最高温 度可达1500C。且化学成分波动范围较小, 化学成 分易于控制;这对于熔炼高合金铸铁如高镍球墨铸 铁等,是必要的条件。 2)冲天炉熔炼的铁液容易增硫。 3)工频炉熔炼的铁液比较“硬”,主要表现在试 样的白口宽度较大,缩凹深度较深。布氏硬度值较 高;相应抗拉强度值也较高。