金属工艺学课件
合集下载
金属工艺学课件(PPT45页).pptx
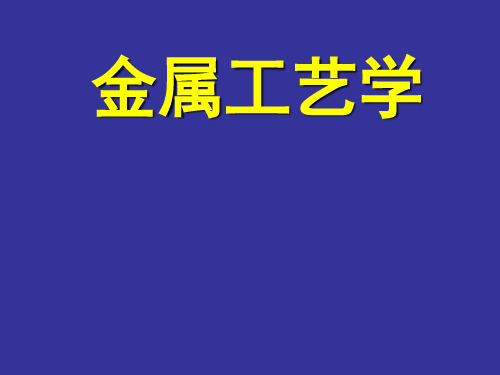
。2020年11月27日星期五下午3时1分51秒15:01:5120.11.27
• 15、会当凌绝顶,一览众山小。2020年11月下午3时1分20.11.2715:01November 27, 2020
• 16、如果一个人不知道他要驶向哪头,那么任何风都不是顺风。2020年11月27日星期五3时1分51秒15:01:5127 November 2020
(三)型材 型材主要有板材、棒材、线材 等。常用截面形状有圆形、方形、六角形和 特殊截面形状。就其制造方法,又可分为热 轧和冷拉两大类。热轧型材尺寸较大,精度 较低,用于一般的机械零件。冷拉型材尺寸 较小,精度较高,主要用于毛坯精度要求较 高的中小型零件。
• (四)焊接件 焊接件主要用于单件小批 生产和大型零件及样机试制。其优点是制 造简单、生产周期短、节省材料、减轻重 量。但其抗振性较差,变形大,需经时效 处理后才能进行机械加工。
《金属工艺学》上、下册 《材料成型工艺基础》
《机械制造学》 《工程材料与热加工工艺》 《机械加工工艺》 《机械加工工艺基础》
《材料成形学》
高等教育出版社
邓文英
华中理工大学出版社 沈其文
机械工业出版社
王贵成
西北工业大学出版社 裴崇斌
西北工业大学出版社 裴崇斌
清华大学出版社
金问楷
机械工业出版社
李新城
网络资源
课程的特点
• 课程是机类专业应掌握的一门重要的专业
基础课,具有很强的综合性和实践性,是
在掌握了工程制图和金工实习课之后开设 的专业基础课。通过本课程的教学,培养 学生把理论与实践结合起来学习的理念, 提高工程实践的意识,并能用所学的基本 原理和方法分析实际生产技术问题,为学 习后续课程并为以后从事机械设计和制造 方面的工作奠定必要的基础。
金属工艺学全套精品课件
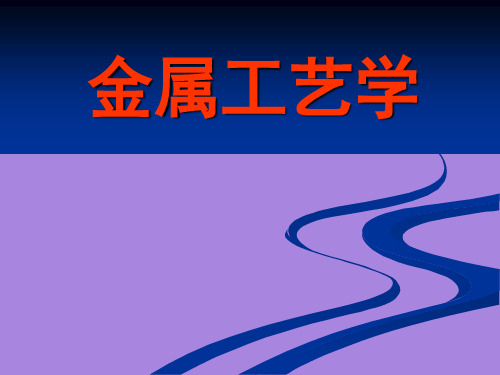
屈服强度与抗拉强度的比值称为屈强比(小于 1)。
l
二、塑性(塑性变形)
金属材料在外力作用下产生不可逆转的永久
变形而不发生断裂的能力称为塑性。常用的塑性 指标有断后伸长率δ和断面收缩率ψ,均通过试验 测定。
1、断后伸长率δ:又称延伸率,是指试件被拉 断后,其标距长度的最大伸长量Δl与原始标距l0
的百分比。
5、金属的塑性变形会导致其 提高, 下降,这种现象称为加工硬化。
二、单项选择题:
1、金属材料表现出力学性能的是
()
A. 导电性 B. 抗氧化性 C. 导热性 D. 硬度
2、试件拉断前承受的最大标称拉应力称为
一、强度:
金属材料在外力作用下抵抗永久变形或 断裂的能力称为强度。
按外力性质不同划分,强度有抗拉强度、 抗压强度、抗剪强度、抗扭强度和抗弯强 度等。工程指标一般为屈服强度和抗拉强 度。
F S
金属材料的屈服强度、抗拉强度以及塑性指标是 在万能材料试验机上通过对金属材料进行拉伸试验 测定的。
构件在力的作用下,抵抗永久变形或断裂的能力 (强度),既取决于承受的内力大小,又取决于构 件的横截面的大小和形状,因而用应力值来衡量构 件的强度。一般,把单位面积上的抵抗破坏的内力 称为应力,即:
工艺性能是指金属材料在各种加工工艺 过程中所表现出来的性能,包括铸造、锻 造、焊接、热处理性能及切削加工性能等。
金属材料的力学性能又称机械性能,是 指金属材料在外力(即载荷)作用下所表 现出的抵抗变形和破坏的能力。包括强度、 塑性、硬度、冲击韧性和疲劳强度等,是 机械零件和构件设计、选材的主要依据。
冲击韧性,简称韧性。导致冲击的因素主要有载荷或速 度突然变化(惯性)。
2、金属疲劳: 金属材料在指定循环基数的交变载荷作用下,不产
l
二、塑性(塑性变形)
金属材料在外力作用下产生不可逆转的永久
变形而不发生断裂的能力称为塑性。常用的塑性 指标有断后伸长率δ和断面收缩率ψ,均通过试验 测定。
1、断后伸长率δ:又称延伸率,是指试件被拉 断后,其标距长度的最大伸长量Δl与原始标距l0
的百分比。
5、金属的塑性变形会导致其 提高, 下降,这种现象称为加工硬化。
二、单项选择题:
1、金属材料表现出力学性能的是
()
A. 导电性 B. 抗氧化性 C. 导热性 D. 硬度
2、试件拉断前承受的最大标称拉应力称为
一、强度:
金属材料在外力作用下抵抗永久变形或 断裂的能力称为强度。
按外力性质不同划分,强度有抗拉强度、 抗压强度、抗剪强度、抗扭强度和抗弯强 度等。工程指标一般为屈服强度和抗拉强 度。
F S
金属材料的屈服强度、抗拉强度以及塑性指标是 在万能材料试验机上通过对金属材料进行拉伸试验 测定的。
构件在力的作用下,抵抗永久变形或断裂的能力 (强度),既取决于承受的内力大小,又取决于构 件的横截面的大小和形状,因而用应力值来衡量构 件的强度。一般,把单位面积上的抵抗破坏的内力 称为应力,即:
工艺性能是指金属材料在各种加工工艺 过程中所表现出来的性能,包括铸造、锻 造、焊接、热处理性能及切削加工性能等。
金属材料的力学性能又称机械性能,是 指金属材料在外力(即载荷)作用下所表 现出的抵抗变形和破坏的能力。包括强度、 塑性、硬度、冲击韧性和疲劳强度等,是 机械零件和构件设计、选材的主要依据。
冲击韧性,简称韧性。导致冲击的因素主要有载荷或速 度突然变化(惯性)。
2、金属疲劳: 金属材料在指定循环基数的交变载荷作用下,不产
《金属工艺学》课件
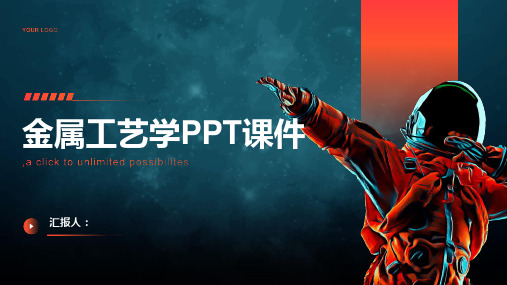
金属的加工工艺
金属的铸造工艺
铸造工艺简介:将熔融的金属倒入模具中,冷却后形成所需形状的工艺 铸造方法:砂型铸造、金属型铸造、离心铸造等 铸造材料:铁、钢、铝、铜、锌等 铸造工艺特点:可生产复杂形状的零件,成本低,生产效率高
金属的锻造工艺
锻造方法:自由锻造、模锻、 冲压、挤压等
锻造工艺:将金属加热到一 定温度,通过锤打、挤压等 方式改变其形状和性能
切削工具:包括车刀、铣刀、钻头、 锯片等
切削方法:包括车削、铣削、钻削、 锯削等
切削参数:包括切削速度、进给量、 切削深度等
切削质量:包括表面粗糙度、尺寸精 度、形位精度等
切削效率:包括生产效率、能耗、刀 具寿命等
金属的热处理工艺
热处理的原理和分类
热处理的原理:通过改变金属的微观结构, 提高其力学性能和耐腐蚀性
金属的表面处理技术
表面涂装技术
目的:保护金 属表面,提高 耐腐蚀性、耐
磨性等性能
主要方法:电 镀、喷涂、热
浸镀等
电镀:利用电 解原理,在金 属表面形成一 层金属或合金
镀层
喷涂:利用高 压气流将涂料 喷涂到金属表 面,形成一层
保护层
热浸镀:将金 属加热到一定 温度,使其表 面形成一层金 属或合金镀层
智能化:利用人工智能技术, 实现金属加工的自动化、智 能化
数字化:利用数字化技术, 实现金属加工的精确控制和
优化
绿色化:采用环保技术和材 料,实现金属加工的绿色化
和可持续发展
绿色环保和可持续发展要求
减少能源消耗:提高能源利用效率, 降低生产过程中的能源消耗
循环利用:提高金属材料的回收利 用率,实现资源的循环利用
添加标题
添加标题
金属工艺学第17章课件.ppt

17.2.3 常用机床
2)车床的主要组成部件
1—主轴箱; 2—卡盘; 3—滑板; 4—刀架; 5—冷却管; 6—尾座; 7—丝杠; 8—光杠; 9—床身; 10—操纵杆; 11—溜板箱; 12—盛液箱; 13—进给箱; 14—挂轮箱 CA6140型卧式车床的外形
27
17.2 金属切削机床的基础知识
16M1432B万能外圆磨床 1—床身; 2—头架; 3—工作台; 4—内圆磨装置; 5—砂轮架;
6—尾座; 7—脚踏操纵板
42
17.2 金属切削机床的基础知识
17.2.3 常用机床
1)刨床
牛头刨床 1—工作台; 2—滑枕; 3—刀架; 4—横梁; 5—床身; 6—底座
43
17.2 金属切削机床的基础知识
17.2.3 常用机床
1)车床的工艺范围
卧式车床适用于:加工各种轴类、套类 和盘类零件上的回转表面。其工艺范围非常 广泛,适用性很强。在车床上可进行:钻中 心孔、车外圆、车端面、车锥体、钻孔、铰 孔、车内孔、车成形面、车螺纹、滚花、绕 弹簧、攻螺纹和套螺纹等加工。
26
17.2 金属切削机床的基础知识
1)机床的 组、系代号
每类机床分成若干组、型,其代号用两位阿 拉伯数字组成(第一位数字代表组别,第二位数 字代表型别),位于类代号或特性代号之后。
23
17.2 金属切削机床的基础知识
17.2.2 机床的型号
2)机床的 主要参数
机床的主参数代号用阿拉伯数字表示(其数 值为主参数的本身 1/10或1/100),位于组、 型代号之后。
刀具在进给运动方向相对于工件的位移 量,称为进给量。车削加工的刀具进给量常 用工件每转一周刀具的位移量来表述和度量, 用 f 表示,单位为 mm/r。
金属工艺学教学PPT
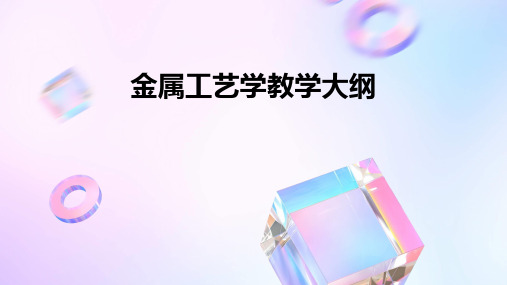
03
金属加工工艺
铸造工艺
铸造工艺基础
介绍铸造工艺的基本原理、铸 造材料、铸造设备及工装模具
等。
铸造工艺设计
学习铸造工艺方案制定、浇注 系统设计、冒口和冷铁设计等 。
铸造合金材料
了解常用铸造合金材料的性能 特点、应用范围及熔炼技术。
铸造缺陷与质量控制
分析铸造过程中常见的缺陷及 质量控制方法,提高铸造件质
金属工艺学的重要性
金属工艺学在现代工业制造中扮演着至关重要的角色,它涉 及到航空航天、汽车、船舶、能源、建筑、医疗器械等多个 领域,是实现从原材料到最终产品的关键环节。
金属工艺学的历史与发展
金属工艺学的起源
金属工艺学可以追溯到古代,人类最 早使用石头和骨头制作工具和武器, 后来逐渐掌握了炼铁和铜等金属的加 工技术。
VS
安全要求
实验室应配备必要的安全设施和防护用品 ,确保学生的人身安全和健康。学生在实 践过程中应按照指导教师的要求进行操作 ,如遇紧急情况应及时报告并采取相应措 施。
感谢您的观看
THANKS
金属工艺的创新与发展趋势
总结词
金属工艺的创新与发展趋势
创新点1
3D打印技术在金属工艺中的应用。
描述1
通过3D打印技术,可以实现金属零件的快速原型 制造,提高设计效率和生产灵活性。
金属工艺的创新与发展趋势
创新点2
01
金属表面处理技术的改进。
描述2
02
采用新型表面处理技术,如电镀、喷涂等,提高金属表面的美
观性和耐久性。
发展趋势1
03
数字化技术在金属工艺中的应用。
金属工艺的创新与发展趋势
01
描述3
利用数字化技术进行金属工艺设 计和优化,实现智能化制造和个 性化定制。
金属工艺学课件
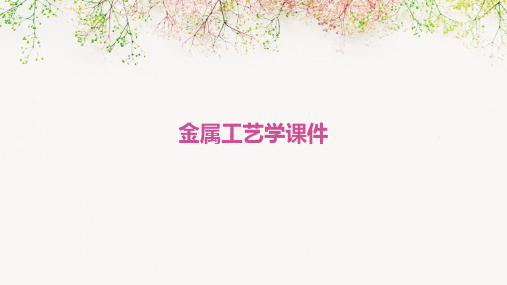
分类
热处理技术可以分为退火、淬火、回火等多种方式。
应用
热处理技术广泛应用于钢铁、有色金属等领域,是提高金属性能和 延长使用寿命的重要手段。
05
金属工艺学的未来发展
新材料的应用
轻质金属材料
随着航空航天、汽车等行业的快速发展,轻质金属材料如 钛合金、铝合金等在金属工艺领域的应用将更加广泛。
高性能金属材料
80%
医疗器械
金属工艺学在医疗器械领域的应 用也十分重要,如人工关节、心 脏起搏器等医疗器械的制造。
02
金属材料的性质
金属材料的物理性质
01
02
03
04
导热性
金属材料具有良好的导热性, 可以用于制造各种散热器、加 热器等。
导电性
金属材料是电的良导体,广泛 用于电线、电缆等电气产品的 制造。
密度
金属材料的密度较大,质地较 重,具有较高的质量感和稳定 性。
智能制造技术
将信息技术与制造技术深度融合,实现生产过程 的智能化和柔性化,提高生产效率和产品质量。
3
精密加工技术
利用高精度机床和加工工具,实现金属零件的高 精度加工,提高产品的稳定性和可靠性。
环保与可持续发展
01
绿色制造技术
通过采用清洁能源、减少废弃物 排放等方式,实现生产过程的环 保和可持续发展。
金属工艺学的重要性
金属工艺学在工业生产、航空航天、交通运输、医疗器械等领域 具有广泛应用,对于推动科技进步和社会发展具有重要意义。
金属工艺学的历史与发展
古代金属工艺
早在公元前,人类就开始使用金属,如铜、铁等, 用于制造工具和武器。
工业革命时期的金属工艺
随着工业革命的兴起,金属工艺得到了迅速发展, 各种新的加工技术不断涌现。
热处理技术可以分为退火、淬火、回火等多种方式。
应用
热处理技术广泛应用于钢铁、有色金属等领域,是提高金属性能和 延长使用寿命的重要手段。
05
金属工艺学的未来发展
新材料的应用
轻质金属材料
随着航空航天、汽车等行业的快速发展,轻质金属材料如 钛合金、铝合金等在金属工艺领域的应用将更加广泛。
高性能金属材料
80%
医疗器械
金属工艺学在医疗器械领域的应 用也十分重要,如人工关节、心 脏起搏器等医疗器械的制造。
02
金属材料的性质
金属材料的物理性质
01
02
03
04
导热性
金属材料具有良好的导热性, 可以用于制造各种散热器、加 热器等。
导电性
金属材料是电的良导体,广泛 用于电线、电缆等电气产品的 制造。
密度
金属材料的密度较大,质地较 重,具有较高的质量感和稳定 性。
智能制造技术
将信息技术与制造技术深度融合,实现生产过程 的智能化和柔性化,提高生产效率和产品质量。
3
精密加工技术
利用高精度机床和加工工具,实现金属零件的高 精度加工,提高产品的稳定性和可靠性。
环保与可持续发展
01
绿色制造技术
通过采用清洁能源、减少废弃物 排放等方式,实现生产过程的环 保和可持续发展。
金属工艺学的重要性
金属工艺学在工业生产、航空航天、交通运输、医疗器械等领域 具有广泛应用,对于推动科技进步和社会发展具有重要意义。
金属工艺学的历史与发展
古代金属工艺
早在公元前,人类就开始使用金属,如铜、铁等, 用于制造工具和武器。
工业革命时期的金属工艺
随着工业革命的兴起,金属工艺得到了迅速发展, 各种新的加工技术不断涌现。
金属工艺学第九章课件.pptx
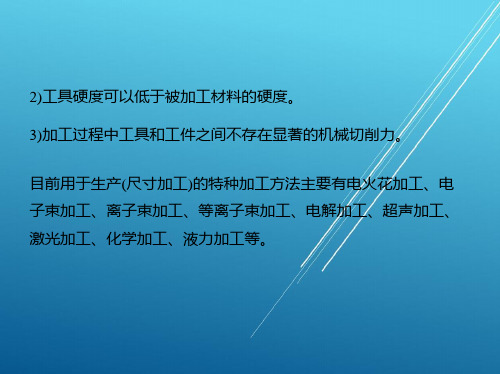
二、数控加工技术的特点 数控加工技术的主要特点如下:
1)零件的加工精度高,尺寸一致性好 由于数控机床本身的精密度 高,特别是有的数控机床具有加工过程自动检测和误差补偿等功 能,因而能可靠地保证加工精度和尺寸的稳定性。
2)生产效率高。数控加工过程是一种自动加工过程,不需要工人直 接操作机床。加工中零件的装夹次数少。一次装夹可加工出很多 表面,可省去划线找正和检测等许多中间工序。加工复杂零件时, 效率可提高5~10倍,劳动强度也低。
3)特别适合加工形状复杂的轮廓表面。可加工如叶片、叶轮及成 形模具等具有复杂空间曲面的零件。
4)有利于实现计算机辅助制造。目前在机械制造业中,CAD/CAM 的应用日趋广泛,而数控机床及其加工技术正是计算机辅助制造 系统的基础。
5)对操作者(不含编程人员)技术水平的要求相对较低。
6)初始投资大,加工成本高。数控机床的价格一般比同规格的普通 机床高出许多,机床备件的价格也很高,加上零件加工进行编程、
图9-7 激光加工的工作原理示意图 1—激光器 2—光阑 3—反射镜 4—聚焦
镜 5—工件 6—工作台 7—电源
3.激光加工的特点及应用 1)不需要直接接触的加工工具,所以不存在工具损耗问题,适宜自 动化生产系统。
2)由于激光的功率密度高,几乎能加工所有的材料,如各种金属材 料、陶瓷、石英、金刚石及半导体等。
超声加工除用于工件的成形加工外还可以用于清洗、焊接和探伤 等。
四、激光加工
1.激光的特性
普通光源(如白炽灯、日光灯、氙灯、氪灯等)的发光是以自发辐 射为主。
1)强度高,红宝石脉冲激光器的亮度比高压脉冲氙灯高370亿倍,比 太阳表面的亮度也要高200多亿倍。
2)单色性好,激光的波长(或者频率)是某一确定的数值,或严格地讲 是波长的范围(谱线宽度)非常小。
1)零件的加工精度高,尺寸一致性好 由于数控机床本身的精密度 高,特别是有的数控机床具有加工过程自动检测和误差补偿等功 能,因而能可靠地保证加工精度和尺寸的稳定性。
2)生产效率高。数控加工过程是一种自动加工过程,不需要工人直 接操作机床。加工中零件的装夹次数少。一次装夹可加工出很多 表面,可省去划线找正和检测等许多中间工序。加工复杂零件时, 效率可提高5~10倍,劳动强度也低。
3)特别适合加工形状复杂的轮廓表面。可加工如叶片、叶轮及成 形模具等具有复杂空间曲面的零件。
4)有利于实现计算机辅助制造。目前在机械制造业中,CAD/CAM 的应用日趋广泛,而数控机床及其加工技术正是计算机辅助制造 系统的基础。
5)对操作者(不含编程人员)技术水平的要求相对较低。
6)初始投资大,加工成本高。数控机床的价格一般比同规格的普通 机床高出许多,机床备件的价格也很高,加上零件加工进行编程、
图9-7 激光加工的工作原理示意图 1—激光器 2—光阑 3—反射镜 4—聚焦
镜 5—工件 6—工作台 7—电源
3.激光加工的特点及应用 1)不需要直接接触的加工工具,所以不存在工具损耗问题,适宜自 动化生产系统。
2)由于激光的功率密度高,几乎能加工所有的材料,如各种金属材 料、陶瓷、石英、金刚石及半导体等。
超声加工除用于工件的成形加工外还可以用于清洗、焊接和探伤 等。
四、激光加工
1.激光的特性
普通光源(如白炽灯、日光灯、氙灯、氪灯等)的发光是以自发辐 射为主。
1)强度高,红宝石脉冲激光器的亮度比高压脉冲氙灯高370亿倍,比 太阳表面的亮度也要高200多亿倍。
2)单色性好,激光的波长(或者频率)是某一确定的数值,或严格地讲 是波长的范围(谱线宽度)非常小。
《金属工艺学》课件
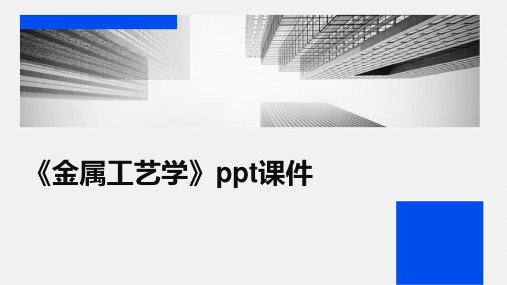
金属工艺学分类
金属工艺学可以根据加工对象和应用 领域分为多种分支,如铸造、锻造、 焊接、切削加工、热处理等。
金属工艺学的应用领域
机械制造业
航空航天业
金属工艺学在机械制造业中应用广泛,涉 及各种零件的加工、装配和维修。
航空航天器制造需要高精度和高性能的金 属材料和加工技术,金属工艺学在航空航 天业中发挥着重要作用。
汽车制造业
电子工业
汽车制造业需要大量金属材料和加工技术 ,包括车身、底盘、发动机等部件的制造 和装配。
电子工业中,金属材料广泛应用于电路板 、连接器、散热器等部件的制造。
金属工艺学的历史与发展
01
古代金属工艺
早在公元前,人类就开始使用金属材料,如青铜、铁等,用于制造工具
、武器和饰品。
02
工业革命时期的金属工艺
退火与正火工艺
退火工艺
退火是一种将金属加热到适当温度,保温一段时间,然后缓慢冷却至室温的热 处理工艺。其主要目的是消除金属内部的应力,提高其塑性和韧性,以便于进 一步加工。
正火工艺
正火是将金属加热到适当温度,保持一定时间后,在静止空气中冷却的热处理 工艺。其主要目的是细化金属的晶粒,提高其机械性能,如强度和韧性。
。
焊接缺陷及防止
03
焊接过程中可能出现气孔、夹渣、裂纹等缺陷,需采取相应措
施进行防止。
金属的切削加工工艺
切削加工原理
通过刀具对金属工件进行切削,以去除多余的金属材料,实现工 件形状和尺寸的加工。
切削加工方法分类
根据切削加工的特点和应用,可分为车削、铣削、钻削、磨削等 。
切削加工技术要求
切削加工过程中需要考虑刀具材料、切削液、切削参数等因素, 以确保加工质量和效率。
金属工艺学可以根据加工对象和应用 领域分为多种分支,如铸造、锻造、 焊接、切削加工、热处理等。
金属工艺学的应用领域
机械制造业
航空航天业
金属工艺学在机械制造业中应用广泛,涉 及各种零件的加工、装配和维修。
航空航天器制造需要高精度和高性能的金 属材料和加工技术,金属工艺学在航空航 天业中发挥着重要作用。
汽车制造业
电子工业
汽车制造业需要大量金属材料和加工技术 ,包括车身、底盘、发动机等部件的制造 和装配。
电子工业中,金属材料广泛应用于电路板 、连接器、散热器等部件的制造。
金属工艺学的历史与发展
01
古代金属工艺
早在公元前,人类就开始使用金属材料,如青铜、铁等,用于制造工具
、武器和饰品。
02
工业革命时期的金属工艺
退火与正火工艺
退火工艺
退火是一种将金属加热到适当温度,保温一段时间,然后缓慢冷却至室温的热 处理工艺。其主要目的是消除金属内部的应力,提高其塑性和韧性,以便于进 一步加工。
正火工艺
正火是将金属加热到适当温度,保持一定时间后,在静止空气中冷却的热处理 工艺。其主要目的是细化金属的晶粒,提高其机械性能,如强度和韧性。
。
焊接缺陷及防止
03
焊接过程中可能出现气孔、夹渣、裂纹等缺陷,需采取相应措
施进行防止。
金属的切削加工工艺
切削加工原理
通过刀具对金属工件进行切削,以去除多余的金属材料,实现工 件形状和尺寸的加工。
切削加工方法分类
根据切削加工的特点和应用,可分为车削、铣削、钻削、磨削等 。
切削加工技术要求
切削加工过程中需要考虑刀具材料、切削液、切削参数等因素, 以确保加工质量和效率。
- 1、下载文档前请自行甄别文档内容的完整性,平台不提供额外的编辑、内容补充、找答案等附加服务。
- 2、"仅部分预览"的文档,不可在线预览部分如存在完整性等问题,可反馈申请退款(可完整预览的文档不适用该条件!)。
- 3、如文档侵犯您的权益,请联系客服反馈,我们会尽快为您处理(人工客服工作时间:9:00-18:30)。
硬度测定方法有压入法、划痕法、回 弹高度法等。
金属材料的硬度可用专门仪器来测试, 常用的有布氏硬度机、洛氏硬度机等。
15 2020/12/8
布氏硬度
HBS(HBW ) 0.102
2F
N mm2
D(D D 2 d 2 )
式中:F—试验力,N D—压头的直径,mm
布氏硬度试验原理图
单位面积所受的 力值即为硬度
2020/12/8
缩孔
缩松
38 2020/12/8
⑵偏析:合金中各部分化 学成分不均匀的现象称为 偏析。铸锭(件)在结晶时, 由于各部位结晶先后顺序 不同,合金中的低熔点元 素偏聚于最终结晶区,造 成宏观上的成分不均匀, 称宏观偏析。适当控制浇 注温度和结晶速度可减轻 宏观偏析。
硫在钢锭中偏析的模拟结果
以得到补缩所致。
逐层凝固合金易产生缩孔(如纯金属、共晶合金),糊状
凝固合金易产生缩松,(如锡青铜)。
36 2020/12/8
2、缩孔和缩松的防止: 1)、适当地降低浇注温度和浇注速度。 2)、采用顺序凝固、冒口补缩(顺序凝固原则)。 3)、按冷铁、采用金属型。 缩孔部位的确定:常用“凝固等温线法”、“内切圆法”37。
布氏硬度与洛氏硬度的特点比较
布氏硬度的特点:
布氏硬度因压痕面积较大,HB值的 代表性较全面,而且实验数据的重复性 也好,但由于淬火钢球本身的变形问题 ,不能试验太硬的材料,一般在HB450 以上的就不能使用。
由于压痕较大,成品检验也有困难 。
通常用于测定铸铁、有色金属、低 合金结构钢等材料的硬度。
HBS表示用淬火钢球作为压头 测出的硬度值。
HBW表示用硬质合金球作为 压头测出的硬度值。
16 2020/12/8
洛氏硬度
洛氏硬度试验原理图
试验时,先加初试验 力,然后加主试验力, 压入试样表面之后, 去除主试验力,在保 留初试验力的情况下, 根据试样残余压痕深 度增量来衡量试样的 硬度大小。
17 2020/12/8
金属熔化
液态金属浇入铸型
落砂清理后成为铸件
29
2020/12/8
二、铸造的特点:
1、能制成形状复杂,特别是具 有复杂内腔的毛坯;
2、铸件重量及所用合金几乎不 受限制;
3、铸件的切削加工余量较小、 成本低。因此,得到了广泛的 应用。
但是:
1、抗拉强度和冲击韧性不如锻、 焊件。
2、工艺复杂,故废品率高。
➢有些机件在工作时要受到高速作用的载荷 冲击,如锻压机的锤杆、冲床的冲头、汽车 变速齿轮、飞机的起落架等。 ➢瞬时冲击引起的应力和应变要比静载荷引 起的应力和应变大得多,因此在选择制造该 类机件的材料时,必须考虑材料的抗冲击能 力,即冲击韧度。
20 2020/12/8
金属材料抵抗冲击载荷作用而不破坏的能力叫 做冲击韧度。常用一次摆锤冲击试验来测定金 属材料的冲击韧度(大能量、一次冲断)。
退火低碳钢力-伸长曲线
oe——弹性变形阶段;es——屈服阶段; sb——强化阶段;bk——缩颈阶段
s-屈服点 b-开始发生缩颈现象
8 2020/12/8
强度极限B
颈缩阶段
屈服极限S 屈服阶段 弹性极限P 弹性阶段
强化阶段
9 2020/12/8
强度指标
1.屈服点
在拉伸试验过程中,外力不增加(保持恒定),但试样
螺旋形试样
31 2020/12/8
1)、合金流动性的测定:用“螺旋形
试样”的长度来衡量。在相同浇注
条件下,试样愈长,流动性愈好。
2)、影响合金流动性的因素:主要是
合金的化学成分。液相线与固相线
间的距离(T液-T固)称为结晶间隔。
Fe-C合金流动性与含碳量关系
结晶间隔越大流动性越差,反之越好,因此共晶成分合金流动性
仍然能继续伸长(变形),这种现象称屈服。S点称屈服点,
S点对应的应力称屈服点应力。用符号σs表示。屈服点应力 σs可按下式计算:
σs = Fs / A0
(MPa)
式中:Fs—试样屈服时的载荷,N
A0—试样原始横截面积,mm2。
10 2020/12/8
2.
抗拉强度是指试样拉断前承受的最大应力
值,用符号σb表示,单位为Mpa,
试验表明,在冲击载荷不太大的情况下,金属 材料承受多次重复冲击的能力,主要取决于强 度。
冲击值对组织缺陷很敏感,因此冲击试验是生 产上用来检验冶炼、热加工、热处理等工艺质 量的有效方法。
21 2020/12/8
夏比冲击试验 试验原理
冲击韧度:
ak = AK/A (J·cm-2)
式中:Ak—折断试样所消耗的冲击功(J) A—试样断口处的原始截面积(mm2)
18 2020/12/8
洛氏硬度的特点: 洛氏硬度HR可以用于硬度很高的材料
,而且压痕很小,几乎不损伤工件表面, 故在钢件热处理质量检查中应用最多。
但洛氏硬度由于压痕较小,硬度代表 性就差些,如果材料中有偏析或组织不均 的情况,则所测硬度值的重复性也差。
19 2020/12/8
三、冲击韧度(ak)
2 2020/12/8
课程的性质、任务和要求
性质:
➢ 研究常用工程材料及其成形方法的综合性课程 ➢ 体现理论教学与实践环节密切结合的技术基础课程
任务和要求:
➢了解产品的制造过程 ➢掌握常用工程材料的种类与性能,能初步选用 ➢掌握材料成形的基本原理和工艺特点,能初步运用
3 2020/12/8
第一篇 金属材料的基础知识
一、铸件的凝固 逐层凝固(充型能力好,便于补缩)
1、凝固方式 糊状凝固(易形成缩孔、难以获得结晶紧实的铸件) 中间凝固(介于上两者间)
铸件的凝固方式
33 2020/12/8
合金的结晶温度范围
2、影响凝固方式的主要因素
合金性质
铸件的温度梯度 铸型的蓄热能力
浇注温度
二、铸造合金的收缩
铸造合金在浇注、凝固、直至冷却到室温的过程中,其体积或尺寸
39 2020/12/8
⑶气孔: 是指液态金属中溶解的气体或反应生成的 气体在结晶时未逸出而存留于铸锭(件)中的气泡.铸 锭中的封闭的气孔可在热加工时焊合,张开的气 孔需要切除。铸件中出现气 孔则只能报废。
铸件中的气孔
40 2020/12/8
第三节 铸造内应力 变形和裂纹
内力:构件内部相互作用并达平衡的力。 与内应力、变形、裂纹相关的是固态收缩。 一、内应力的形成:因固态收缩受阻。 按内应力产生的原因分为:机械应力、热应力。 1、机械应力(受机械阻碍而形成的) 原因:铸件固态收缩时,受到铸型或型芯等的机械阻碍
式中:A0—试样的原始截面积(mm2)
A1—试样断面处的最小截面积(mm2)
δ和φ愈大,则塑性愈好。良好的塑性是金
属材料进行塑性加工的必要条件。
14 2020/12/8
二、硬度
固体材料抵抗塑性变形、压入或压痕 的能力。
硬度是衡量金属材料软硬程度的一种 性能指标。它直接影响到材料的耐磨 性及切削加工性。
4 2020/12/8
第一节 金属材料的力学性能
力学性能是指金属材料在受外力作用时所 反映出来的固有性能。
金属材料的力学性能主要有:强度、塑性、 硬度、冲击韧度和疲劳强度等。
力学性能指标,是选择、使用金属材料的 重要依据。
5 2020/12/8
一、强度与塑性
强度:材料抵抗由外力载荷所引起的应变或 断裂的能力。
34 2020/12/8
三、铸件中的缩孔与缩松: 1、缩孔和缩松的形成: 液态合金在冷凝过程中,若其液态收缩和凝固收缩所缩减的容积得 不到补足,则在铸件最后凝固部位形成一些孔洞,按孔洞的大小和 分布,分为缩孔和缩松。 1)、缩孔:集中在铸件上部或最后凝固的部位容积较大的孔洞。 特征:多呈倒圆锥形,内表面粗糙,通常隐藏在铸件内层,有时暴 露于表面。
最好.(图2-3)。
2、浇注条件(浇注温度和充型压力):浇注温度越高,充型压力
越大则充型能力越好。
3、铸型填充条件(铸型的蓄热能力,铸型温度和铸型中的气
体):铸型的蓄热能力低,铸型温度较高,铸型排气能力较好时
则充型能力较好。
由于充型能力低而引起的缺陷有:冷隔、浇不足。
32 2020/12/8
第二节 铸件的凝固与收缩
σb= Fb / A0
(Mpa )
式中:Fb—试样承受的最大载荷,N
A0—试样原始横截面积,mm2。
11 2020/12/8
屈服点应力(屈服强度)和抗拉强度在设 计机械和选择、评定金属材料时有重要意 义 。 机械零件多以σs作为强度设计的依 据。
对于脆性材料,在强度计算时,则以σb为 依据。
25 2020/12/8
疲劳曲线
在循环载荷作用下, 材料承受一定的循环 应力σ和断裂时相应的 循环次数N之间的关 系可以用曲线来描述 ,即σ-N之间的关系 曲线,称疲劳曲线
σ-N 曲线
▪ 当零件所受的应力按正弦曲线对称循环时,疲劳强
度以符号σ-1表示,即当应力低于σ-1值,既使循环周 次无穷多也不发生断裂 。
26 2020/12/8
σ-N 曲线
无数次应力循环: • 对于钢材为107, • 有色金属和某些超高强度钢常取108。
27 2020/12/8
第二篇 铸造
铸件
GM-KD5025数控龙门磨床床身 (41T)
28 2020/12/8
第一章 铸造的工艺基础 一、铸造:将液态合金浇注 到与零件的形状、尺寸相适 应的铸型空腔中,待其冷却 凝固,以获得毛坯或零件的 生产方法,叫做铸造。
22 2020/12/8
标准冲击试样有两种,一种是夏比U形缺口试样, 另一种是夏比V形缺口试样
同一条件下同一材料制作的两种试样,其U形试样 的a k值明显大于V形试样的a k,所以这两种试样的 值a k不能相互比较。对于脆性材料试样一般不开缺口。
金属材料的硬度可用专门仪器来测试, 常用的有布氏硬度机、洛氏硬度机等。
15 2020/12/8
布氏硬度
HBS(HBW ) 0.102
2F
N mm2
D(D D 2 d 2 )
式中:F—试验力,N D—压头的直径,mm
布氏硬度试验原理图
单位面积所受的 力值即为硬度
2020/12/8
缩孔
缩松
38 2020/12/8
⑵偏析:合金中各部分化 学成分不均匀的现象称为 偏析。铸锭(件)在结晶时, 由于各部位结晶先后顺序 不同,合金中的低熔点元 素偏聚于最终结晶区,造 成宏观上的成分不均匀, 称宏观偏析。适当控制浇 注温度和结晶速度可减轻 宏观偏析。
硫在钢锭中偏析的模拟结果
以得到补缩所致。
逐层凝固合金易产生缩孔(如纯金属、共晶合金),糊状
凝固合金易产生缩松,(如锡青铜)。
36 2020/12/8
2、缩孔和缩松的防止: 1)、适当地降低浇注温度和浇注速度。 2)、采用顺序凝固、冒口补缩(顺序凝固原则)。 3)、按冷铁、采用金属型。 缩孔部位的确定:常用“凝固等温线法”、“内切圆法”37。
布氏硬度与洛氏硬度的特点比较
布氏硬度的特点:
布氏硬度因压痕面积较大,HB值的 代表性较全面,而且实验数据的重复性 也好,但由于淬火钢球本身的变形问题 ,不能试验太硬的材料,一般在HB450 以上的就不能使用。
由于压痕较大,成品检验也有困难 。
通常用于测定铸铁、有色金属、低 合金结构钢等材料的硬度。
HBS表示用淬火钢球作为压头 测出的硬度值。
HBW表示用硬质合金球作为 压头测出的硬度值。
16 2020/12/8
洛氏硬度
洛氏硬度试验原理图
试验时,先加初试验 力,然后加主试验力, 压入试样表面之后, 去除主试验力,在保 留初试验力的情况下, 根据试样残余压痕深 度增量来衡量试样的 硬度大小。
17 2020/12/8
金属熔化
液态金属浇入铸型
落砂清理后成为铸件
29
2020/12/8
二、铸造的特点:
1、能制成形状复杂,特别是具 有复杂内腔的毛坯;
2、铸件重量及所用合金几乎不 受限制;
3、铸件的切削加工余量较小、 成本低。因此,得到了广泛的 应用。
但是:
1、抗拉强度和冲击韧性不如锻、 焊件。
2、工艺复杂,故废品率高。
➢有些机件在工作时要受到高速作用的载荷 冲击,如锻压机的锤杆、冲床的冲头、汽车 变速齿轮、飞机的起落架等。 ➢瞬时冲击引起的应力和应变要比静载荷引 起的应力和应变大得多,因此在选择制造该 类机件的材料时,必须考虑材料的抗冲击能 力,即冲击韧度。
20 2020/12/8
金属材料抵抗冲击载荷作用而不破坏的能力叫 做冲击韧度。常用一次摆锤冲击试验来测定金 属材料的冲击韧度(大能量、一次冲断)。
退火低碳钢力-伸长曲线
oe——弹性变形阶段;es——屈服阶段; sb——强化阶段;bk——缩颈阶段
s-屈服点 b-开始发生缩颈现象
8 2020/12/8
强度极限B
颈缩阶段
屈服极限S 屈服阶段 弹性极限P 弹性阶段
强化阶段
9 2020/12/8
强度指标
1.屈服点
在拉伸试验过程中,外力不增加(保持恒定),但试样
螺旋形试样
31 2020/12/8
1)、合金流动性的测定:用“螺旋形
试样”的长度来衡量。在相同浇注
条件下,试样愈长,流动性愈好。
2)、影响合金流动性的因素:主要是
合金的化学成分。液相线与固相线
间的距离(T液-T固)称为结晶间隔。
Fe-C合金流动性与含碳量关系
结晶间隔越大流动性越差,反之越好,因此共晶成分合金流动性
仍然能继续伸长(变形),这种现象称屈服。S点称屈服点,
S点对应的应力称屈服点应力。用符号σs表示。屈服点应力 σs可按下式计算:
σs = Fs / A0
(MPa)
式中:Fs—试样屈服时的载荷,N
A0—试样原始横截面积,mm2。
10 2020/12/8
2.
抗拉强度是指试样拉断前承受的最大应力
值,用符号σb表示,单位为Mpa,
试验表明,在冲击载荷不太大的情况下,金属 材料承受多次重复冲击的能力,主要取决于强 度。
冲击值对组织缺陷很敏感,因此冲击试验是生 产上用来检验冶炼、热加工、热处理等工艺质 量的有效方法。
21 2020/12/8
夏比冲击试验 试验原理
冲击韧度:
ak = AK/A (J·cm-2)
式中:Ak—折断试样所消耗的冲击功(J) A—试样断口处的原始截面积(mm2)
18 2020/12/8
洛氏硬度的特点: 洛氏硬度HR可以用于硬度很高的材料
,而且压痕很小,几乎不损伤工件表面, 故在钢件热处理质量检查中应用最多。
但洛氏硬度由于压痕较小,硬度代表 性就差些,如果材料中有偏析或组织不均 的情况,则所测硬度值的重复性也差。
19 2020/12/8
三、冲击韧度(ak)
2 2020/12/8
课程的性质、任务和要求
性质:
➢ 研究常用工程材料及其成形方法的综合性课程 ➢ 体现理论教学与实践环节密切结合的技术基础课程
任务和要求:
➢了解产品的制造过程 ➢掌握常用工程材料的种类与性能,能初步选用 ➢掌握材料成形的基本原理和工艺特点,能初步运用
3 2020/12/8
第一篇 金属材料的基础知识
一、铸件的凝固 逐层凝固(充型能力好,便于补缩)
1、凝固方式 糊状凝固(易形成缩孔、难以获得结晶紧实的铸件) 中间凝固(介于上两者间)
铸件的凝固方式
33 2020/12/8
合金的结晶温度范围
2、影响凝固方式的主要因素
合金性质
铸件的温度梯度 铸型的蓄热能力
浇注温度
二、铸造合金的收缩
铸造合金在浇注、凝固、直至冷却到室温的过程中,其体积或尺寸
39 2020/12/8
⑶气孔: 是指液态金属中溶解的气体或反应生成的 气体在结晶时未逸出而存留于铸锭(件)中的气泡.铸 锭中的封闭的气孔可在热加工时焊合,张开的气 孔需要切除。铸件中出现气 孔则只能报废。
铸件中的气孔
40 2020/12/8
第三节 铸造内应力 变形和裂纹
内力:构件内部相互作用并达平衡的力。 与内应力、变形、裂纹相关的是固态收缩。 一、内应力的形成:因固态收缩受阻。 按内应力产生的原因分为:机械应力、热应力。 1、机械应力(受机械阻碍而形成的) 原因:铸件固态收缩时,受到铸型或型芯等的机械阻碍
式中:A0—试样的原始截面积(mm2)
A1—试样断面处的最小截面积(mm2)
δ和φ愈大,则塑性愈好。良好的塑性是金
属材料进行塑性加工的必要条件。
14 2020/12/8
二、硬度
固体材料抵抗塑性变形、压入或压痕 的能力。
硬度是衡量金属材料软硬程度的一种 性能指标。它直接影响到材料的耐磨 性及切削加工性。
4 2020/12/8
第一节 金属材料的力学性能
力学性能是指金属材料在受外力作用时所 反映出来的固有性能。
金属材料的力学性能主要有:强度、塑性、 硬度、冲击韧度和疲劳强度等。
力学性能指标,是选择、使用金属材料的 重要依据。
5 2020/12/8
一、强度与塑性
强度:材料抵抗由外力载荷所引起的应变或 断裂的能力。
34 2020/12/8
三、铸件中的缩孔与缩松: 1、缩孔和缩松的形成: 液态合金在冷凝过程中,若其液态收缩和凝固收缩所缩减的容积得 不到补足,则在铸件最后凝固部位形成一些孔洞,按孔洞的大小和 分布,分为缩孔和缩松。 1)、缩孔:集中在铸件上部或最后凝固的部位容积较大的孔洞。 特征:多呈倒圆锥形,内表面粗糙,通常隐藏在铸件内层,有时暴 露于表面。
最好.(图2-3)。
2、浇注条件(浇注温度和充型压力):浇注温度越高,充型压力
越大则充型能力越好。
3、铸型填充条件(铸型的蓄热能力,铸型温度和铸型中的气
体):铸型的蓄热能力低,铸型温度较高,铸型排气能力较好时
则充型能力较好。
由于充型能力低而引起的缺陷有:冷隔、浇不足。
32 2020/12/8
第二节 铸件的凝固与收缩
σb= Fb / A0
(Mpa )
式中:Fb—试样承受的最大载荷,N
A0—试样原始横截面积,mm2。
11 2020/12/8
屈服点应力(屈服强度)和抗拉强度在设 计机械和选择、评定金属材料时有重要意 义 。 机械零件多以σs作为强度设计的依 据。
对于脆性材料,在强度计算时,则以σb为 依据。
25 2020/12/8
疲劳曲线
在循环载荷作用下, 材料承受一定的循环 应力σ和断裂时相应的 循环次数N之间的关 系可以用曲线来描述 ,即σ-N之间的关系 曲线,称疲劳曲线
σ-N 曲线
▪ 当零件所受的应力按正弦曲线对称循环时,疲劳强
度以符号σ-1表示,即当应力低于σ-1值,既使循环周 次无穷多也不发生断裂 。
26 2020/12/8
σ-N 曲线
无数次应力循环: • 对于钢材为107, • 有色金属和某些超高强度钢常取108。
27 2020/12/8
第二篇 铸造
铸件
GM-KD5025数控龙门磨床床身 (41T)
28 2020/12/8
第一章 铸造的工艺基础 一、铸造:将液态合金浇注 到与零件的形状、尺寸相适 应的铸型空腔中,待其冷却 凝固,以获得毛坯或零件的 生产方法,叫做铸造。
22 2020/12/8
标准冲击试样有两种,一种是夏比U形缺口试样, 另一种是夏比V形缺口试样
同一条件下同一材料制作的两种试样,其U形试样 的a k值明显大于V形试样的a k,所以这两种试样的 值a k不能相互比较。对于脆性材料试样一般不开缺口。