汽车发动机零部件的柔性化生产
机器人视觉在汽车零部件生产线的应用

机器人视觉在汽车零部件生产线的应用摘要:汽车发动机周边零部件生产线基本要周期性换不同模具生产不同的工件,通过机器人视觉解决机器人生产线上料单一的难点。
用程序与模具切换,实现不同工件的生产。
关键词:汽车;机器人视觉;零部件生产线;柔性化生产汽车发动机周边零部件生产企业为了适应多样化、准时化的市场需求,基本要在一年中周期性更换不同模具生产不同的工件。
所以,对于机器人生产线要具有柔性化生产能力。
但如何解决机器人生产线柔性化生产的难点是整个汽车发动机周边零部件生产企业的痛点。
柔性化生产的最大难点在于上料方式,解决上料方式等于实现柔性化生产的基本条件。
本文通过具体项目的设计方案来描述如何让汽车零部件柔性化机器人生产线成功落地。
1、工艺简介1.1产品信息:2SV1.5T节温器,型号19320-59B-0002,材质铝合金。
1.2柔性化机器人生产线工艺过程人工摆料(上料输送装置)→视觉检测寻位→机器人抓料→机器人在OP10夹具上料→OP10机加工→机器人取OP10的料→OP10夹具清渣吹渣→机器人放置毛坯料→机器人持10序工件清洗→工件换面→机器人取20序工件→OP20夹具清渣吹渣→机器人放置10序工件→OP20机加工→OP20工件清洗/吹气→机器人下料(下料输送装置)→人工装框。
2、柔性化机器人生产线2.1柔性化机器人生产线结构组成:上料输送线、视觉定位检测系统、FANUC机器人、机器人双夹爪、机器人行走轴、4台加工中心、系统控制柜、液压夹具控制柜、液晶显示屏、换面台、清洗装置、网格板、安全防护装置、下料输送线、模具、刀具。
2.2机器人动作顺序表3、机器人视觉应用用普通的输送带做上料输送线,让操作工无论工具歪斜、反向,均能自动识别,并精密抓取。
输送线前端装配检测开关,检测输送线横向方向是否有料,以便给输送线信号使输送线继续输送。
输送线配合视觉1进行粗定位,反馈信号给机器人抓取,机器人抓取工件后,移动到视觉2检测,通过视觉检测使机器人调整后序放置工件角度,进行精定位。
工业工程方案改善实例
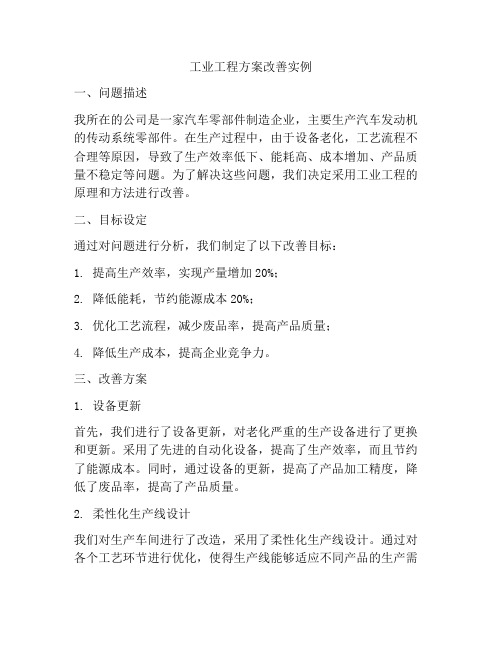
工业工程方案改善实例一、问题描述我所在的公司是一家汽车零部件制造企业,主要生产汽车发动机的传动系统零部件。
在生产过程中,由于设备老化,工艺流程不合理等原因,导致了生产效率低下、能耗高、成本增加、产品质量不稳定等问题。
为了解决这些问题,我们决定采用工业工程的原理和方法进行改善。
二、目标设定通过对问题进行分析,我们制定了以下改善目标:1. 提高生产效率,实现产量增加20%;2. 降低能耗,节约能源成本20%;3. 优化工艺流程,减少废品率,提高产品质量;4. 降低生产成本,提高企业竞争力。
三、改善方案1. 设备更新首先,我们进行了设备更新,对老化严重的生产设备进行了更换和更新。
采用了先进的自动化设备,提高了生产效率,而且节约了能源成本。
同时,通过设备的更新,提高了产品加工精度,降低了废品率,提高了产品质量。
2. 柔性化生产线设计我们对生产车间进行了改造,采用了柔性化生产线设计。
通过对各个工艺环节进行优化,使得生产线能够适应不同产品的生产需求,大大提高了生产线的灵活性和适应性。
这样一来,就可以有效降低产品的更换时间,提高了生产效率。
3. 作业分析与改进我们开展了对生产作业的分析,优化了作业流程。
合理安排工人的作业任务,减少了非生产性动作和浪费,提高了作业效率。
同时,我们还引入了一些辅助工具和工艺改进措施,进一步提高了生产效率和产品质量。
4. 绩效管理体系建立为了更好地监控生产过程和效果,我们建立了绩效管理体系。
制定了生产目标和绩效考核指标,对生产过程进行全面监控和评估。
通过绩效管理体系的建立,我们可以及时发现和解决生产中的问题,及时调整生产计划,保障生产效率和产品质量。
四、改善效果经过改善方案的实施,我们取得了以下改善效果:1. 生产效率提高了30%,产量增加了20%;2. 能源成本减少了25%,节约了大量能源费用;3. 产品质量稳定性得到了提高,废品率降低了15%;4. 生产成本降低了20%,企业利润大幅提升。
发动机智能装配线的柔性化设计及应用探究

发动机智能装配线的柔性化设计及应用探究摘要:发动机是汽车的心脏,属于汽车不可缺少的构成部分,其质量会对汽车寿命、行驶安全产生直接影响。
发动机会应用到装配线进行装配生产,随着汽车需求量不断增加,发动机装配线生产压力逐渐提升,如何提升发动机装配线生产质量与效率,是需要重点关注的话题。
基于此,本文重点对发动机智能装配线的柔性化设计及应用进行分析,从发动机装配线生产特点入手,进行了发动机智能装配线的柔性化设计,提出发动机装配生产线的智能化应用,希望为相关人员提供参考借鉴。
关键词:发动机;智能装配线;柔性化设计引言我国社会经济不断发展下,为制造业发展带来了良好契机,智能制造已经成为制造业未来发展的主要趋势。
汽车发动机直接决定着汽车的性能,因此,汽车发动机生产线应不断优化改进,通过先进技术的不断应用,形成智能装配线,基于智能化技术下,提升发动机装配线生产效率,进一步提升发动机生产质量。
本文就发动机智能装配线的柔性化设计及应用相关内容进行分析,具体如下。
一、发动机装配线生产特点发动机制造过程中会涉及到较为复杂的制造工艺,装配环节尤为重要,若想保证发动机装配工作的良好开展,提升装配生产效率,应通过发动机装配线加以实现。
对于发动机总装环节而言,是一种离散型流水线制造模式,实际生产装配环节,缸体会从第一道工序按照一定顺序进行加工,经历过全部工序后,最终形成发动机产品。
装配环节较为复杂,经历工序较多,并且生产环节还应对所有数据信息进行详细记录。
发动机装配线生产特点主要体现在以下几方面:第一,对质量及标准要求高[1]。
若想保证发动机质量,装配线需要有高质量的控制能力,并且,当存在不合格发动机时,还能对其进行返修,这种情况下,会使整线控制程序更加负责。
第二,多机型混线以及柔性化生产。
发动机装配线应具备机型识别功能,可以获取不同机型的工作参数,针对性的进行设备控制,并且,对操作工做出指导,更好的开展装配工作。
此外,柔性化的好坏,会对装配线后续拓展、改造产生直接影响,可通过科学配置软件实现柔性化生产。
发挥技术制造优势 研发汽车关键零部件柔性生产线及关键加工设备

m
产
嫁
商 。企业研 发 的大型多工位 压力机 首先 出 口到美 国市场 ,并引领 国 内汽 车逐步推 广应用 ,在引导
四 、结束 语
“ 十二五 ”期 间 ,企 业将遵 循 “ 以市场 为导
高端 冲压设备 市场方面 发挥 了重 要作用 。今年 以 来 ,先后 拿到 了国际两 大汽车 巨头的快 速冲压线
z 轴全 闭环控 制 ( 栅尺 ),提 高机床 的 光
加工 精度 ;高速立 式 、卧式加工 中心应 满足 的主
( 2)自动 动平 衡技 术 。为了 使 主轴运 转 平
要技 术指 标 :定位精 度 ≤00 O .l mm;重复定 位精
度 ≤OO 5 m;主轴最 高转 速 ≥10 0/ i; 三轴 . m 0 8 0r n a r
00 rm 。 .6 a
是共 和 国建 国初期 全 国机床 行业 十八 罗汉之 一 。
从 2 世 纪 9 年 代 末 至 已经 过 去 的 “ 一五 ”期 0 0 十 间 ,集 团公 司走 出了一条具有 自身特 点 的集成 创 新之 路 ,企业 规模 、技术水平 、制造 能力取 得 了 突飞猛进 的发展 ,经济实 现了跨越 式增长 ,成为
度更稳定 。
配备A C /轴转 台 ,通过试制五轴加工 单元 ,开 展 了以下技术 的研究 : 高速 加工 中心 的特点就 是主轴 旋转 的高速 和
驱动 部件移 动 的高 速 ,这 就要求运 动部件 的质 量
在保 证足够 刚度 的情况下 应该最 轻 ,这样 才能 使
运 动 部 件 实现 高 的加 速 度 和快 速 移 动 速 度 。 目 前 ,高速加 工 中心 的结构有 许 多种 ,我们 选定 的
发动机曲轴制造工艺进展及敏捷柔性生产线

20 . 世纪 7 ~8 年代 2 0 0
这一时期 ,曲轴粗加工采用 C C车削、C C外铣加工, N N 加工状况有所 改善。精加工仍多以普通磨床磨削工艺为主。
30 . 世纪 8 年代中期 2 0
到2 世纪 8 年代中期,又出现了C C内铣工艺, N 0 0 N C C内铣加工性能 指标要高于C C外铣加工, N 尤其是对于锻钢曲轴 , 内铣更有利于断屑。 精 加工工艺多采用半 自 曲轴磨床,头架和尾座同步杠传动,加工精度有一 动
41 8 ~19 年 .9 5 9 0
1 8 ~19 9 5 9 0年开发出了曲轴车
拉 一 车 车拉工艺 ( 为双刀 图l 盘车 一
颈。采用这种方式加工精度较低,柔性很差, 工序质量稳定性低, 且容易产 生较大的内部应力, 难以达到合理的加工余量。 在粗加工后一般需要进行去
应力 回火处理 , 释放应力。因此粗加 工需要给后续精加 工工序 留较 大的加 工 余量 ,以去除弯 曲变形量 。曲轴精加工采 用的是普通磨 削工艺 ,一般采用
采用直线光栅尺或圆度光栅尺检测, 可实现闭环控制。 该加工中心备有4 ~ 8 9 工位刀库可实现自动换刀, 6 一次装夹可进行车、 铣、钻、 镗、 攻螺纹等的 加工。曲轴精加工方面, 也出现了工序集成的C N数控磨床, B 即一次装夹磨
削全部曲轴主轴颈和连杆轴颈 ( 摆动跟踪 磨削 ) 。 由以上演变可以看出 ,曲轴的加工工艺正 向着高速 、高效 、 复合化 方向 发展 。 目前较 为流行的粗加工工 艺是主轴颈采 用车 一车拉工艺和高速外铣 , 连杆轴颈采用高速随动外铣 , 全部采用干式切削; 精加工 采用数控磨 床加工 , 具 有 自动进给 、自 动修正砂轮 、 寸和 圆度 自 补偿 、自动分度和两端电子 尺 动
机械制造中的柔性制造系统

机械制造中的柔性制造系统在当今高度竞争的制造业环境中,企业需要不断提高生产效率、降低成本、提高产品质量,并快速响应市场的变化。
为了实现这些目标,柔性制造系统(Flexible Manufacturing System,简称FMS)应运而生。
柔性制造系统是一种先进的制造技术,它将计算机技术、自动化技术和制造技术有机地结合起来,为机械制造企业提供了高度灵活和高效的生产解决方案。
一、柔性制造系统的定义和组成柔性制造系统是由数控加工设备、物料储运系统和计算机控制系统等组成的自动化制造系统。
它能够在不停机的情况下,根据生产任务的变化,自动调整加工工艺和生产流程,实现多品种、中小批量生产的高效化和自动化。
数控加工设备是柔性制造系统的核心,包括数控机床、加工中心等。
这些设备具有高精度、高效率和高自动化程度的特点,能够完成各种复杂零件的加工。
物料储运系统负责原材料、在制品和成品的存储和运输。
它通常包括自动化仓库、输送装置、搬运机器人等,能够实现物料的快速准确配送,保证生产的连续性。
计算机控制系统是柔性制造系统的大脑,它负责对整个生产过程进行监控、调度和管理。
通过计算机控制系统,操作人员可以实时掌握生产进度、设备状态和质量情况,并及时做出调整和决策。
二、柔性制造系统的特点1、高度灵活性柔性制造系统能够快速适应产品品种和生产批量的变化,无需对设备进行大规模的调整和改造。
它可以在同一生产线上同时生产多种不同的产品,大大提高了企业的市场响应能力。
2、高效率通过自动化的物料储运和加工过程,柔性制造系统能够减少生产中的等待时间和运输时间,提高设备的利用率和生产效率。
3、高质量由于采用了先进的数控加工设备和严格的质量控制手段,柔性制造系统能够保证产品的高精度和高质量,降低废品率和次品率。
4、可扩展性柔性制造系统可以根据企业的发展需求进行扩展和升级,增加新的设备和功能,以满足不断增长的生产需求。
三、柔性制造系统的工作原理在柔性制造系统中,计算机控制系统首先接收生产任务,并根据产品的工艺要求和设备的可用性,制定生产计划和调度方案。
汽车发动机缸体柔性生产线的研制

O 引 言
随着 世 界 经 济 的 复苏 和 国 内经 济 的快 速 增 长 , 汽
等 行 业 中还 保 持 着 一 定 的 份 额 。 然 而 , 的 刚 性 化 这 它
一
特 点 , 它 在 经 济 大 潮 中 难 以适 应 产 品 多 品 种 、 新 使 更
( eh ooyC ne , a inMahn o l ru o , a a i nn 10 2 C ia T cn l etr D Fa c i T o G o pC . D l nLa ig1 2 , hn ) g e i o 6
Absr t:Thi r il e e t h e lpme t a d a tac s a tceprs n st e d veo n n ppl a i n n c i d r fe i e ma ufc u ig l e i to s o yl e xbl n a t rn i .Ap・ c n l n pl a ins o i i r t i to fsm l ype o o u t wi e i to u e c a fpr d c l b r d c d.Ac o dig t h pe i c rq r me t l n c r n o t e s cf e uie n ,ma e g nea i k e rl d sg f f xbe i ns l e in o e i l l l ne f'ty.Th e in a d d v lp ni of fe be ma ufc u ig s t m o e h th n e d g s n e eo u t x l n a t rn yse t g t e wi li r Clmps a ,Nu rc lCon r lS t ,Tr n po tto v c d o h c e s ra e ie .Th st e d- meia to yse m a s ra in De ie a t e a c o ild c s n r s v e po ii fe ve ba k fo c t me s s ws t e a v t g d r l bit ft s ype o le b ema ufc u ig l e I s sg c r m us o r ho h d a a e a ei l y o hi t n n a i ff x l n a t rn n . tha i- i i ni c te e t o e b ema ufc u ig s t i a in f a f c n f x l n a t rn ys e i Ch . li m n n Ke r s:fe bl n a t rn ys e ;u i offe b e ma ufcu i yse ;ca y wo d l x e ma ufc u ig s t i m n t x l n a t rng s t li m lmps n me c lc n r l ; u r a o to i
汽车发动机缸盖柔性生产线综合应用技术

缸盖是 内燃机 的 重 要部 件 , 为 发 动机 较 难 加 工 部 件 之 一 。其通 常材 质 有 铸 铁件 和 铝 合 金 , 铸 铁 件 一 般
缸 盖作 为 发 动 机 进 排 气 通 道 以及 燃 烧 室 组 成 部 分, 其功 能部 位相 关 尺寸要 求 即为关键 尺寸 ( 表2 ) 。
表 1 缸 盖 各 面 主 要 内容 分 布 描 述
序 号 平 面 内 容 描 述 备 注
用 于 传统 的小 汽车 或 卡 车 发 动机 , 铝合 金 一 般 用 于 现 代 新 颖 的小 汽车发 动机 和赛 车发 动机 。随着 汽车新 品
开发 周期 大大 缩短 , 日益发展 的多样性 需 求 , 使 车 型数 量急 剧增 加 。为 了满 足变 品种 、 变批 量 的需要 , 汽 车发 动机 生产 线 多采用 更 为灵活 的加 工 中心组 线 。宁 夏小 Fra bibliotek应用 情况 。
2
罩 盖结合 面, 主要孔 系为气 门挺 杆柱孑 L 、 火 顶 面 花塞孔 、 凸轮 轴孔 、 出砂孔 、 螺栓 安装孔 面 、 定位销孔 、 螺纹孑 L 等
进 气 面 进 气 歧 管 安 装 面 , 主 要喷油 嘴孔 、 凸 轮 轴 感 知器 孑 L 、 螺 纹 孔 系 排气 面 排 气歧 管 安 装 面 , 主 要 螺 纹 孔 系
摘
要: 阐述 了缸 盖 柔性 生产线 综 合应用 技 术。 柔性 生产 线 加 工 工艺 工 艺设 备 高速加 工
文 献标 识码 : A
关键 词 : 缸盖
中图分 类号 : U 4 6 4
Te c h a p p l i c a t i o n o n a u t o e n g i n e c y l i n d e r h e a d f l e x i b l e p r o d u c t i o n l i n e
- 1、下载文档前请自行甄别文档内容的完整性,平台不提供额外的编辑、内容补充、找答案等附加服务。
- 2、"仅部分预览"的文档,不可在线预览部分如存在完整性等问题,可反馈申请退款(可完整预览的文档不适用该条件!)。
- 3、如文档侵犯您的权益,请联系客服反馈,我们会尽快为您处理(人工客服工作时间:9:00-18:30)。
汽车发动机零部件的柔性化生产作者:李如松在十多年前,要用加工中心来替代自动线还是难于办到的事,然而在今天,这种替代已成了现实。
在上世纪80年代末和90年代初,像轿车发动机这样的大批量生产领域,采用的加工设备主要还是自动线和组合机床。
例如德国大众汽车厂在Salzgitter的发动机生产厂里,生产包括样机在内的(1~)升排量的四缸、五缸和六缸发动机,采用的加工设备,自动线就占了60%,组合机床和加工中心各占了20%。
然而就在这几年中,众多机床厂充分利用在刀具技术和驱动技术等方面取得的巨大进步,在90年代初兴起高速加工和开发出高速加工中心,显着提高了加工中心的生产效率。
与此同时,由于经济的全球化和需求的个性化,促使产品品种日益增多,设备的柔性成了决择加工设备的重要因素。
在这样的技术和市场情况下,于是高速加工中心在90年代中期就开始进入大批量生产领域,打破了自动线和组合机床在这些领域里的垄断地位。
目前,在汽车发动机的缸盖、缸体、变速箱体和离合器壳等箱体件的加工中,由高速加工中心组成的柔性生产线已大部分替代了自动线、高速加工中心已成为汽车发动机箱体件加工的主要设备。
加工中心和自动线是两种不同类型的机床,最初,它们有着不同的应用领域,它们之间并不存在着竞争。
技术的进步和市场的变化,推动了自动线的柔性化和加工中心的高速化发展。
致使这两种不同类型机床的应用领域彼此接近和相互重叠,生产率和柔性这两个特征参数之间的矛盾渐渐在消失。
目前,在中、大批量生产领域有些工件的加工完全可以采用高速加工中心来实现。
而对于一些需采用复杂刀具又需机床配合的工件加工,则愈来愈多地转向采用模块化的生产系统,在这样的生产系统中,可以根据具体的加工任务来集成加工中心和自动线及组合机床,以便充分地利用自动线和加工中心各自的优点。
自动线的柔性化及其特点为适应不断增加的变型品种的生产,在70年代末和80年代初,众多组合机床制造厂家相继利用NC技术开发出了柔性自动线用的各种不同类型的数控加工模块。
这些加工模块按其运动坐标数,有单坐标、双坐标和三坐标模块;按其主轴数,有单主轴和多主轴模块(转塔式多轴加工模块)。
由于这些模块是数控的,因此,当柔性自动线由加工变型品种中的一种工件转向加工另一种工件时,可通过改变数控程序来实现自动换刀、自动更换多轴箱和自动改变加工行程以及自动改变工作循环、切削用量和加工位置等,以适应变型多品种加工。
图1所示是一条加工载重卡车八种变速箱体的柔性自动线。
该线采用了四台双坐标数控铣削模块,六台数控转塔式多轴加工模块和六台立柱移动式三坐标加工模块,辅助工位有清洗工位和采用机器人进行操作的装夹工作站。
当由一种工件的加工转换为另一种工件的加工时,只须通过夹具上的编码来调用所要加工工件的数控程序、所需的刀具和加工参数,而无需进行机械等方面的手动调整。
图1:加工变速箱体的柔性自动线(德国Chemnitz机械研究所)柔性自动线与刚性自动线一样,也是一种刚性连接的多工位自动化加工设备,柔性自动线所加工的变型品种在工件的几何形状和加工工艺上必须高度相似,并且这些工件在自动线设计时应该是确定了的,因此,柔性自动线的柔性还是有限的。
由于柔性自动线上所有的加工工位之间是互补关系,所以当自动线上某一台机床发生故障时,就会造成全线停顿,致使设备利用率下降,即使在最好情况下,自动线的利用率也仅为70%。
目前,例如在汽车工业中,像发动机的缸体、缸盖和变速箱体不仅品种多,而且在6年左右的时间里,往往会被新的产品所替代,这就要求加工设备不仅要适应已确定的变型品种的加工,而且还要求能适应尚未确定,而今后有待发展的工件的加工。
显然,柔性自动线由于其结构上的特点,就难于满足这样的要求了。
加工中心的高速化在80年代初,加工中心主轴的最高转速还仅为4000r/min,最高轴移动速度约为20 m/min。
但在随后的(7~8)年中,由于驱动、主轴轴承和控制等技术的长足进步,促使高速加工中心问世。
目前,高速加工中心的主轴转速已普遍达到(15000 ~24000)r/min,轴加速度达(1~2)g,轴移动速度达到(80~120)m/min,两次切削间的间隔时间(切屑到切屑的时间)达(~)秒。
这样,使得这类加工中心可以采用高效刀具以很高的切削速度和进给速度进行高效加工,大大缩短了基本时间。
如粗镗直径为86mm、深度135mm的灰铸铁缸体的缸孔,加工时间仅秒(进给速度达4500mm/min);钻铣铝合金离合器壳上M16 ×深22mm的螺纹孔也只需秒。
由于高速加工中心轴加速度和移动速度的提高,同样也缩短了辅助时间,然而,目前对于大多数加工任务来说,辅助时间占加工流程时间的份额可达(50~70)%,这样高份额的辅助时间主要是由换刀过程(刀具退出加工部位——主轴停在规定的角度位置——主轴移到换刀位置——换刀(或许进行刀具的自动检验)——刀库移动(直接换刀)或机械手进行换刀运动——吹净刀柄——拉紧刀柄——主轴启动到工作转速——主轴刀具重新进行切削加工)产生的,由此可见,减少换刀次数是缩短辅助时间的重要途径。
特别是在中、大批量的生产中,高速加工中心通常可以采用多工件夹具(在多面体夹具上装夹多个相同的工件)、复合刀具(将多个不同的加工工序集中在一把刀具上)和多功能刀具(用一把刀具实现多种工序的加工)来减少换刀次数,从而缩短辅助时间。
基本时间和辅助时间的显着缩短使高速加工中心在生产效率方面达到了组合机床和自动线那样的高水平,为高速加工中心进入大批量生产领域创造了条件。
柔性生产线和混合生产系统目前,汽车发动机的缸体、缸盖和离合器壳的加工已普遍采用柔性生产线(由高速加工中心组成)和混合生产系统(由高速加工中心和自动线组成),按目前的技术水平,采用混合生产系统加工缸盖年最佳加工件数可达(30~35)万件,采用柔性生产线加工离合器壳的年最佳加工件数达(35~40)万件(图2和图3)。
图2:用柔性生产线(XHC241高速加工中心)和自动线加工离合器壳的单件费用比较。
(绿色区表示采用高速加工中心是合适的;红色区表示采用自动线是合适的)图3:加工离合器壳的高速加工中心和自动线在投资费用方面的比较柔性生产线是由若干台高速加工中心通过按一定方向传递工件的输送系统连接而成,输送系统往往采用滚动输送带实现工件的连续输送,输送带同时起到工件的中间贮存作用,这有利于提高机床的利用率。
在生产线上高速加工中心按预定的生产工艺流程依次进行排列,在每个加工单元上至少安排两台可实现互替的同一规格和型号的高速加工中心进行平行加工,这样,当某一台加工中心出现故障而停机时,另一台加工中心仍可继续进行加工,由此避免造成整个生产线的停顿。
因此,这种柔性生产线的利用率可高达(90~95)%。
柔性生产线的模块化结构和成倍的加工设备配置,使生产线可实现分阶段投建。
因为对新产品年销售量的预测往往不一定正确,因此对于首次投产的系统用户可以不急于进行大量设备投资,今后还可以根据市场对产品需求的增加而相应扩充生产线的规模,这无疑有利于提高投资的经济效益。
然而,自动线则与此相反,在项目确定时,其设备的规模和其总投资就确定了。
工件的加工,无疑要选择最合适的机床型式,根据具体的加工任务,通过柔性生产线和自动线的组合就能充分发挥高速加工中心和组合机床各自的优点,以最合理的加工工艺确保工件的加工精度和加工效率。
这种由高速加工中心和自动线组成的混合生产系统主要用于加工发动机的缸体(曲轴箱)和缸盖。
缸体上的主轴承孔、缸盖上的气门阀座和导管孔以及凸轮轴孔不仅孔本身的精度要求很高(H6),而且相邻孔的位置精度要求也很高(如凸轮轴孔相临孔同轴度<,气门阀座和导管孔的同轴度,汽油发动机<,柴油发动机<),所以加工主轴孔和凸轮轴孔,通常要采用具有导向的专用长镗杆,而气门阀座和导管孔则要采用致动受控刀具进行加工。
很显然,组合机床要比高速加工中心更适合于采用这样的工艺和刀具来进行加工。
加工气门阀座和导管孔以及凸轮轴孔均采用了自动线进行加工,而加工中心用来加工缸盖的其它部位。
加工中心的数量可根据市场对产品的需求量的增加而进行扩充,采用的高速加工中心都是一种型号和规格的XHC241。
这样做,有利于提高使用的经济性,因为,这些加工中心具有类似的操作、保养和修理,减少了备件,从而简化了组织管理。
前些年,我国一汽集团(FAW)无锡柴油机厂从德国Grob机床制造厂引进的缸体和缸盖(载重汽厂发动机)两条生产线,就是属于加工中心和组合机床混合配置的生产系统,从这里可以看出,在载重汽车的柴油机行业,过去传统由组合机床承担的一些加工任务,也愈来愈多地由加工中心来完成了。
高速加工中心有很好的应用前景对于汽车的中、大批量生产,在生产技术的目标和任务方面主要体现在高的生产率、高的柔性、高的质量和低的单件费用四个基本要求上。
在目前,在满足这几项要求方面,自动线和高速加工中心的主要差异是在柔性上,而在生产中对于柔性的要求主要基于下列不同的理由:◆适应产量(如产量提高某一数量级)◆对已知工件变型品种的适应能力◆对将来未知的而今后要加工的工件变型品种的适应能力显然,高速加工中心和由它组成的柔性生产线能很好满足这些方面的要求。
在目前,组合机床在实现某些加工工艺方面还具有优势,但是,在工件的综合加工上由高速加工中心完全来替代组合机床的发展趋向仍将继续下去。
例如,像德国Makino机床制造厂在其最近开发的配备有提升换刀系统和专用刀库的J4M高速加工中心上,通过采用静压导向的镗杆加工主轴孔和凸轮轴孔和通过采用CNC-U轴控制的专用刀具加工气门座圈和导管孔,取得了良好效果。
从而用加工中心替代组合机床对缸体和缸盖的加工无疑是一个良好的开端。
由此可以预测,随着刀具和加工工艺的进一步开发以及加工中心结构的完善,用高速加工中心在更大范围内替代自动线还将有进一步的发展。