2000m3高炉炉型设计
2000m3高炉开炉方案

2000m3⾼炉开炉⽅案2000m3⾼炉开炉⽅案根据⾼炉⼯程进度和公司安排,定于#年#⽉#⽇点⽕开炉,为实现安全顺利开炉和迅速达产,特制定开炉⽅案如下:⼀、成⽴开炉领导⼩组开炉前的准备⼯作⼆、开炉前的准备⼯作1、对上料系统、炉顶设备、送风系统、煤⽓系统、煤粉喷吹系统和炉前设备等进⾏全⾯、认真的检查,并进⾏12⼩时以上的联动试车,运转正常,确保⽆误后⽅可开炉。
2、蒸汽和通重⼒除尘器氮⽓管路试汽(⽓),炉前⽤压缩空⽓、氧⽓和烘烤⽤途的焦炉煤⽓管道正常要求管路畅通⽆泄漏,汽(⽓)压>0.4MPa。
3、⾼炉各种计算机监控系统、仪表、仪器安装校对完毕,运转正常。
4、上料电⼦秤安装校对完毕,准确可靠。
5、制作临时炭包,铺好并烤⼲所有渣铁沟。
6、准备好备⽤的风⼝⼩套、吹管各⼀套(风⼝∮120mm×450mm 20个,∮110mm×450mm 8个),风⼝⼆套6个。
备件科准备,7#⾼炉领取。
提前烧好热风炉,要求风温⼤于900℃,为⾼炉点⽕做好准备。
7、准备烧铁⼝氧⽓40瓶,氧⽓管1000kg,氧⽓瓶周转使⽤,氧⽓带和卡⼦2套,同时联系管道氧⽓正常供⽓。
8、准备好⽑渣罐(⼤罐)4个和铁罐6个第⼀次铁使⽤。
准备加长钻杆20根。
9、准备好开炉需要的⽆⽔炮泥和有⽔泡泥,⾼炉提供⽤量和规格。
10、准备⽊柴350m3,∮200~300mm,L=500~800mm左右,不能使⽤带油的腐烂⽊柴。
开炉前3天供应科负责送到炉台。
11、准备好开炉料,料仓上料前认真检查每个料仓,把杂物彻底清理⼲净。
(1)烧结矿⽤400m2直过料,保证所有烧结矿仓满仓(装料前24⼩时以内⼊仓,不能提前)(2)使⽤5#、6#焦炉⽣产的焦炭,提前1~2天⼊仓装满。
(3)硅⽯满仓,灰⽯ 100t,萤⽯80t。
(灰⽯不能多上,另上临时通知)开炉料要有分析并报给技术科。
12、风⼝⾯积确定开炉⽤20个∮120×450mm和8个∮110×450mm的风⼝,前期⽤西铁⼝出铁,均匀堵8个风⼝(3#、6#、10#、13#、15#、19#、23#、27#),开20个风⼝送风。
2000m3高炉本体设计
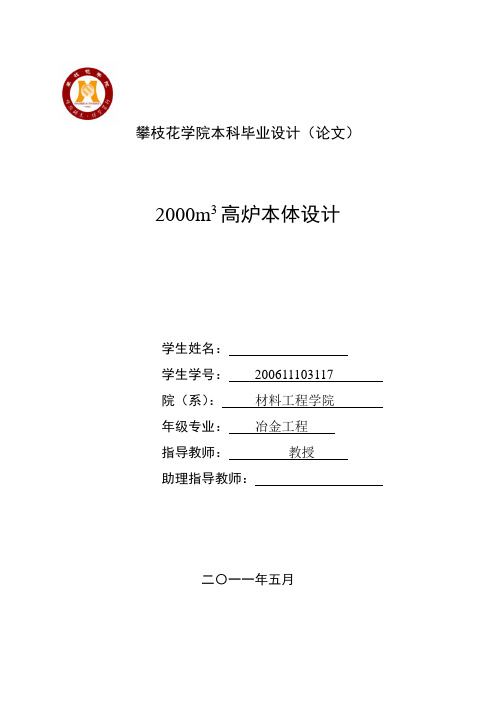
攀枝花学院本科毕业设计(论文)2000m3高炉本体设计学生姓名:学生学号:200611103117院(系):材料工程学院年级专业:冶金工程指导教师:教授助理指导教师:二〇一一年五月摘要高炉炼铁的历史悠久,炼铁技术日臻成熟,是当今主要的炼铁方式。
高炉作为炼铁工艺的主体设备,其结构的合理性对炼铁的工艺操作、生产技术指标以及自身的寿命都有十分重要的影响。
根据攀枝花钒钛磁铁矿的高炉冶炼特点,通过进行配料计算和物料平衡计算,设计了2000m3高炉本体。
设计过程除考虑通常的高炉设计方案外,还考虑了攀枝花钒钛磁铁矿多年高炉冶炼的一些生产实践经验。
所设计完成的高炉本体炉缸直径为9.88m、炉腰直径为10.97m、高径比为2.55、有效高度为27.97m;高炉基础的基墩高1.9m、直径13.53m、基座高2m;采用碳砖加高铝砖综合炉底、全碳砖炉缸;冷却设备的设计为水冷炉底、炉缸和炉底采用三段光面冷却壁、炉身采用镶砖冷却壁;高炉钢结构采用炉体框架式结构,最后采用CAD绘制出高炉本体图。
关键词高炉,高炉本体,炉型,钒钛磁铁矿ABSTRACTThe blast furnace iron-making has a long history which has become the main way of iron manufacture. As the main equipment of ironmaking, the blast furnace plays the most important role. The rationality of the blast furnace’s structural design has great influence on the process operations and technique level of ironmaking and it will decide the useful life of the blast furnace itself. According to the characteristics of the vanadic titanomagnetite smelted in BF in Panzhihua, the 2000m3blast furnace body was designed in this subject based on the calculations of the burden control and the material balance. Besides common design plans of the blast furnace, some practical experiences of the vanadic titanomagnetite smelted in BF was considered in this subject. The basic information of the blast furnace which has been designed is as following: the diameter hearth is 9.88m, the belly diameter is 10.97m, the aspect ratio of the furnace is 2.55, the effective height is 27.97m. As to the blast furnace foundation, the height of under hearth is 1.9m, the diameter of the under hearth is 13.53m, the furnace pad or foundation is 2 m. The hearth bottom adopts carbon bricks and high alumina bricks synthesize technic, the hearth just builds up with carbon bricks. The cooling device is designed to water-cooled hearth bottom, three segments mill finish stave is used for the hearth and hearth bottom, the stack uses inlaid brick stave to make it cool down. The steel structure of the BF adopts frame-type for the furnace body. Finally, the diagram of BF body was gained by using the CAD drawing tools.Key words blast furnace,BF body,furnace type,V-Ti magnetite目录摘要 (I)ABSTRACT (II)1 绪论 (1)1.1 课题背景 (1)1.2 攀枝花钒钛磁铁矿特点 (2)1.3 课题设计的内容及意义 (2)2 高炉设计原始数据 (4)2.1 矿石原料成分 (4)2.2 配矿比 (4)2.3 焦炭成分 (4)2.4 喷吹煤粉成分 (4)2.5 生铁成分 (4)2.6 元素分配比 (5)2.7 炉渣碱度 (5)2.8 工艺技术指标 (5)3 高炉设计工艺计算 (6)3.1 配料计算 (6)3.1.1 根据铁平衡求铁矿石需求量 (6)3.1.2 根据碱度平衡计算石灰石用量 (6)3.1.3 终渣成分 (6)3.1.4 生铁成分校核 (7)3.2 物料平衡计算 (8)3.2.1 需要补充的原始条件 (8)3.2.2 根据碳平衡计算风量 (8)3.2.3 计算煤气成分及数量 (9)3.2.4 编制物料平衡表 (11)4 高炉内型设计计算 (12)4.1 高炉炉型 (12)4.2 高炉炉型设计原则 (13)4.3 高炉内型尺寸确定 (13)4.3.1 炉缸直径 (14)4.3.2 炉腰直径 (14)4.3.3 炉喉直径 (15)4.3.4 铁口中心线到炉底砌砖之间的距离 (15)4.3.5 炉缸高度 (15)4.3.6 炉腹角与炉腹高度 (15)4.3.7 炉身角与炉身高度 (16)4.3.8 有效高度、炉喉高度、炉腰高度 (16)4.3.9 风口、渣口、铁口数 (17)4.3.10 炉容校核 (17)5 高炉本体及主要设备选择 (19)5.1 高炉基础 (19)5.1.1 高炉基础设计条件 (20)5.1.2 基墩设计计算 (20)5.1.3 基座设计 (20)5.2 高炉内衬结构 (21)5.2.1 炉底 (21)5.2.2 炉缸 (22)5.2.3 炉腹 (22)5.2.4 炉腰 (23)5.2.5 炉身 (23)5.2.6 炉喉 (23)5.3 高炉冷却设备设计 (24)5.3.1 冷却设备的作用 (24)5.3.2 冷却介质 (24)5.3.3 高炉各部位冷却设备设计 (24)6 高炉钢结构设计 (26)6.1 炉壳 (26)6.1.1 炉壳厚度的计算 (26)6.1.2 炉壳折点的确定 (27)6.2 炉体平台及走梯 (27)6.3 高炉本体钢结构类型 (28)6.4 高炉主要热工检测仪表 (29)结论 (30)参考文献 (32)致谢 (34)1 绪论1.1课题背景尽管21世纪是一个信息的时代。
高炉本体尺寸设计
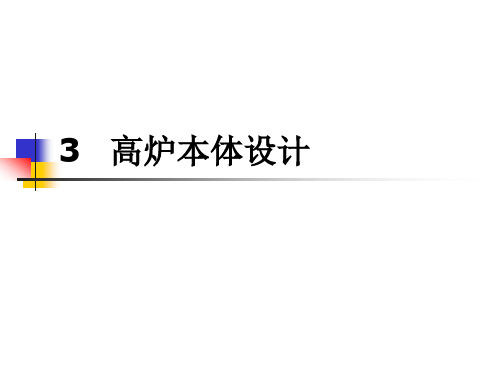
1. 比较法:
由给定的产量确定炉容,根据建厂的冶炼 条件,寻找条件相似,炉容相近,各项生产技 术指标较好的合理炉型作为设计的基础。经过 几次修订参数和计算,确定较为合理的炉型。 目前,设计高炉多采用这种方法。
风口中心线与铁口中心线间距离称 为风口高度(hf)。
风口高度可参照下式计算:
hf
hZ k
式中:
k ——渣口高度与风口高度之比,一般
取0.5~ 0.6,渣量大取低值。
(4)风口数目(n): 主要取决于炉容大小,与炉缸直径
成正比,还与冶炼强度有关。 风口数目可以按下式计算:
中小型高炉:
n 2(d 1)
2. 计算法:
计算法即经验数据的统计法。 计算时可选定某一关系式,算出某一主
要尺寸,再根据炉型中各部位尺寸间的关系 式作炉型计算,最后校核炉容,修定后确定 设计炉型。
经验公式 :
大型高炉:
Hu 6.44Vu0.2
d 0.32Vu 0.45
适应于我国50~70年代1000~2000m3高 炉的基本情况,炉型为瘦长型。
炉腹高度由下式计算 :
h2
D 2
d
tg
炉腹角一般为79º~83º,过大不利于煤气
分布并破坏稳定的渣皮保护层,过小则增
大对炉料下降的阻力,不利于高炉顺行。
4. 炉身: 炉身呈正截圆锥形。
作用:
(1)适应炉料受热后体积的膨胀,有利于 减小炉料下降的摩擦阻力,避免形成料拱。
(2)适应煤气流冷却后体积的收缩,保证 一定的煤气流速。
D
d1 2
tg
设计2000立方米热风炉的炼铁课程设计解析

附件一湖南工业大学课程设计资料袋冶金工程学院(系、部)2010 ~ 2011 学年第 2 学期课程名称炼铁课程设计指导教师刘竹林职称教授学生姓名夏雨专业班级冶金091 学号01234567题目设计向2000立方米高炉提供热风的热风炉成绩起止日期2011 年5月16 日~2011 年5 月29 日目录清单附件二湖南工业大学课程设计任务书2010 —2011 学年第 2学期冶金工程学院(系、部)冶金技术专业冶金091 班级课程名称:炼铁课程设计设计题目:设计向2000立方米高炉提供热风的热风炉完成期限:自2011 年 5 月16 日至2011 年 5 月29 日共 2 周指导教师(签字):年月日系(教研室)主任(签字):年月日(课程设计名称)设计说明书向2000立方米高炉提供热风的热风炉起止日期:2011 年 5 月16 日至2011 年5 月29 日学生姓名夏雨班级冶金091学号01234567成绩指导教师(签字)冶金工程学院(部)2011年月日湖南工业大学冶金工程学院课程设计答辩评价表湖南工业大学冶金工程学院课程设计评阅表前言从冶炼角度看,风是高炉冶炼的重要原料之一。
高炉发展史充分说明改进鼓风对高炉的发展有着极其重要的作用。
风也是强化高炉冶炼的最积极因素,就现在已采用的新技术来看,风的含义不仅与鼓风机有关,还和热风温度、喷吹、富氧、脱湿等技术的应用即风的质量有关。
热风炉为主的热风系统是综合鼓风系统的重要内容。
1828年美国开始使用热风。
实践和理论均证明:热风不仅是降焦、增产和提高生铁质量的重要措施之一,也为提高所喷吹燃料的燃烧率,为改善喷吹效果和加大喷吹量提供有利条件。
因此国内外高炉均致力于提高风温。
热风炉系统的重要作用就是加热冷风,降低焦比,提高生产效益。
现代高炉普遍采用蓄热式热风炉,由于热烧(即加热格子砖)和送风(即冷却格子砖)是交替工作的,为保证向高炉连续供风,故每座高炉至少配置两座热风炉,一般配置三座,大型高炉配置四座为宜。
毕业设计—高炉炉型设计

目录中文摘要 (Ⅰ)英文摘要 (Ⅱ)1 绪论 (4)1.1砖壁合一薄壁高炉炉型的发展和现状 (4)1.2砖壁合一薄壁高炉炉型的应用 (4)2 高炉能量利用计算 (6)2.1高炉能量利用指标与分析方法 (6)2.2直接还原度选择 (7)2.3配料计算 (8)2.4物料平衡 (13)2.5 热平衡 (17)3 高炉炉型设计 (23)3.1 炉型设计要求 (23)3.2 炉型设计方法 (24)3.3炉型设计与计算 (24)4 高炉炉体结构 (28)4.1 高炉炉衬结构 (28)4.2高炉内型结构 (29)4.3 炉体冷却 (30)4.4 炉体钢结构 (31)4.5风口、渣口及铁口设计 (31)5砖壁合一的薄壁炉衬设计 (33)5.1砖壁合一的薄壁炉衬结构的布置形式 (33)5.2砖壁合一的薄壁炉衬高炉的内型 (33)5.3砖壁合一的薄壁炉衬高炉的内衬 (34)5.4薄壁高炉的炉衬结构和冷却形式 (34)6结束语 (36)参考文献 (37)摘要近年来, 炼铁技术迅猛发展, 总的发展趋势是建立精料基础, 扩大高炉容积, 减少高炉数目, 延长高炉寿命, 提高生产效率,控制环境污染, 持续稳定地生产廉价优质生铁, 增加钢铁工业的竞争力。
现代高炉的冶炼特征是, 低渣量, 大喷煤, 低焦比, 高利用系数;高炉结构的特征是,采用软水冷却、全冷却壁、薄壁炉衬、操作炉型的薄壁高炉。
高炉采用大喷煤、高利用系数冶炼, 要求改善高炉的料柱透气性和延长高炉寿命高炉精料、布料、耐火材料、冷却等技术的进步,不断促进长寿的薄壁高炉发展。
高炉的炉型随着高炉精料性能、冶炼工艺、高炉容积、炉衬结构、冷却形式的发展而演变, 高炉设计的理念也随着科学技术的进步和生产实践的进展而更新。
薄壁高炉的设计炉型就是高炉的操作炉型, 在生产中几乎始终保持稳定, 消除了畸形炉型。
长期稳定而平滑的炉型, 有利于高炉生产的稳定和高效长寿。
高炉操作炉型的显著特征是, 炉腰直径扩大, 高径比减小, 炉腹有、炉身角缩小。
1号2000m3高炉球式热风炉设计特点及应用

1 'O0 古炉球式热风炉设计特点及应用 -2 0m3  ̄
闭立钢 摘 张海峰 要 :介 绍柳 钢 1 0 m  ̄ 号20 0 3 _ , E高炉 配套 的球 式热风 炉 的设 计 与改进 、应 用效果 ,以及 相应 的干
法 除尘、 热风 炉操作优 化 措施 。
关 键词 :球 式 热风 炉 ;20 0 0 m 高炉 ;干 法除尘 ;球 床 ;操 作制度
耐火 球 直径 :7 m 5 m,6 m 0 m,5 m 0 m; 球床 全 高度 :95 .m; 耐火 球重 量 :117 ; 7t 总蓄热 面 积 :4 6 m ; 35 4
大容积高炉 。本文 阐述了柳钢 l 0 m高炉球 号2O0 3
式 热 风炉 的设 计 特 点 ,通 过 实 施优 化 操 作 制度 , 采 用PD I 控制 自动烧 炉 ,使 高炉 风 温 长 期稳 定 在 I10 8 ℃左右 ,为 高炉 强化 冶炼 提供 了有 力保 证 。
De e o v l pm e nd Ap i a i n o . nta plc H tSt v
BILi a g -g n ZHANG i・e Ha—fng
Ab t a t T e d s n a d i r v me t a d t e a p i ai n e f c f l g n ' No 1 0 m B . sr c : h e i n mp o e n n h p l t f t o i a g s g c o e u . 2 0 0 F P b l o tv a n r d c d t e c re p n ig d y d s n o t v p r t n o t z t n me s r s e b e h tso e w s i to u e . h o r s o d n r u ta d h tso e o e ai p i ai a u e o mi o wa n r d c d si t u e o Ke yW o d : P b l Ho S o e 2 0 m。 r s e b e t tv ; O 0 BE; Dr Du t o lc in P b l B d O e a i g S se y s C l t ; e b e e ; p r t y t m e o n
毕业设计2000立方米高炉设计

第一章绪论 (4)1概述 (4)1.2 高炉生产主要经济技术指标 (4)1.3高炉冶炼现状及其发展 (5)1.4本设计采用的新技术。
(5)第二章高炉车间设计 (5)2.1厂址的选择 (5)2.2 高炉炼铁车间平面布置应遵循的原则 (6)2.3 车间布置形式 (6)第三章高炉本体设计 (7)3.1高炉数目及总容积的确定 (7)3.2 炉型设计 (7)3.3参数 (9)3.4炉衬设计 (9)3.4.1炉底炉缸的炉衬设计 (9)3.4.2炉腹,炉腰和炉身下部的炉衬设计 (10)3.4.3炉身上部和炉喉砌筑 (10)3.5高炉冷却 (10)3.5.1高炉冷却设备的作用及冷却介质 (10)3.5.2高炉冷却设备设计 (11)3.5.3冷却设备工作制度 (11)3.6高炉钢结构及高炉基础 (11)3.6.1高炉钢结构 (11)3.6.2高炉基础 (12)第4章高炉车间原料系统 (12)4.1贮矿槽及贮焦槽的设计 (13)4.1.1贮矿槽的设计 (13)4.1.2副矿槽 (13)4.1.3贮焦槽设计 (13)4.1.4矿槽的结构形式 (13)4.2给料器,槽下筛分与称量设计 (14)4.2.1给料器 (14)4.2.2槽下筛分 (14)4.2.3槽下称量 (14)4.3胶带机的设计 (15)4.4炉顶装料设备 (15)4.5探料装置 (16)第5章高炉送风系统 (16)5.1高炉鼓风机 (16)5.1.1高炉冶炼对鼓风机的要求: (16)15.1.2鼓风机出口风量的计算 (17)5.1.3鼓风机出口风压的计算 (17)5.1.4鼓风机的选择 (17)5.2高炉热风炉设计 (18)5.2.1热风炉基本结构形式 (18)5.3燃烧器及阀门 (20)5.3.1燃烧器 (20)5.3.2热风炉阀门 (20)5.4提高风温途径 (20)5.5余热回收装置 (20)第6章高炉喷煤系统 (20)6.1煤粉的制备 (21)6.1.1原煤的贮存 (21)6.1.2煤的干燥 (21)6.1.3磨煤机 (21)6.1.4粗粉分离器 (22)6.1.5旋风分离器 (22)6.1.6锁气器 (22)6.1.7布袋收集器 (22)6.2煤粉喷吹系统 (22)6.2.1喷吹设备的确定 (23)6.3安全措施 (23)6.3.1煤粉爆炸条件 (24)6.3.2采取的安全措施 (24)第7章高炉煤气除尘系统 (24)7.1概述 (24)7.1.1高炉煤气除尘的目的 (24)7.1.2评价煤气除尘装置的主要指标 (24)7.2高炉煤气除尘设备 (25)7.2.1荒煤气管道 (25)7.3重力除尘器 (26)7.3.1重力除尘器原理: (26)7.3.2主要尺寸—圆筒部分直径和高度 (26)7.4文氏管 (26)7.4.1文氏管除尘原理: (26)7.4.2半精细除尘设计 (26)7.4.3精细除尘设计 (27)7.5布袋除尘 (27)7.6煤气除尘系统附属设备 (27)7.6.1煤气遮断阀 (27)7.6.2煤气放散阀 (27)7.6.3煤气切断阀 (27)7.6.4调压阀组 (28)7.7炉顶余压发电 (28)2第8章渣铁处理系统 (28)8.1 概述 (28)8.2 风口平台和出铁场 (28)8.2.1 风口平台 (28)8.2.2 出铁场 (29)8.3 渣铁沟和撇渣器 (29)8.3.1 主铁沟 (29)8.3.2 撇渣器 (29)8.3.3 支铁沟和支沟 (29)8.3.4 摆动流嘴 (30)8.4 炉前主要设备 (30)8.4.1 开铁口机 (30)8.4.2 堵铁口泥炮 (30)8.4.4 堵渣口机 (30)8.5 铁水处理设备 (30)8.5.1 铁水罐车 (31)8.5.2 铸铁机 (31)8.6 炉渣处理 (31)3第一章绪论1概述高炉冶炼是获得生铁的主要手段,它以铁矿石(天然富矿,烧结矿,球团矿)为原料,焦碳,煤粉,重油,天然气等为燃料和还原剂,以石灰石等为溶剂,在高炉内通过燃料燃烧,氧化物中铁元素的还原以及非氧化物造渣等一系列复杂的物理化学过程,获得生铁。
2000高炉工艺参数

南京钢铁联合有限公司炼铁新厂作业文件高炉工艺参数控制标准文件编码:管理部门:技术质量部版本:试行控制状态:发放编号:拟制:审核:批准:2005年 3月31日发布 2005年 4月1日实施本基准适用于炼铁新厂2000M3操业管理。
1、原燃料管理1)焦炭质量要求焦炭质量控制基准:M40:≥82%;M10:≤7.0%;Ad≤12.85%;CRI≤30%,CSR ≥60%;焦炭水分:3-7%;焦末≤5%。
2)喷吹煤要求喷吹无烟煤灰分Ad%≤13.00%3)烧结矿要求高炉入炉烧结矿5-10mm粒级组成≤22%4)槽位管理A 总在库量小于50%,高炉减风10~30%,并调整用料结构。
B 总在库量小于30%,高炉减风50%,并做好休风准备。
2、炉温管理基准(1)铁水温度目标值:PT=1480±20℃增热情况下:风温→湿度→喷煤量→O/C→风量(见风量管理)减热情况下:喷煤量→O/C →湿度→风温→风量及料制3、煤气分布管理基准**W=十字测温边缘温度平均值/炉顶平均温度Z=中心5点温度之和/炉顶平均温度CCT--十字测温中心温度4、装料管理5、炉渣成分管理基准6、风量管理(1)风压波动管理风压波动上下限规定:±3δP=Po、δ-表示波动后风压,正常时风压,正常时风压偏差。
P、Po(3)下列情况要求减风A)风压超限或炉况失常时;B)炉温向凉,不减风不能防止炉凉时;C)低料线作业时;a)低于正常料线1米以上,估计1小时无法赶上正常料线或炉顶温度超限(>280℃),打水也不能制止时;应将风量控制在正常风量的80~90%;b)料线已经达到3米,且造成空料的原因仍然未排除时,应将风量控制在正常风量的40%以下,并立即组织出铁,准备休风;c)料线深达4米,且仍然无明确恢复正常时间,应迅速请示厂调,经批准后按正常程序休风;d)料线深达6米应迅速按正常程序休风;D) 动力故障(水、电、气)或渣铁排放故障危及管理安全生产时;E) 因上次铁未出尽(或铁口难开),铁水贮存量达到120吨(或者渣量40吨)而又不具备重叠出铁条件时,减风10%以上。
- 1、下载文档前请自行甄别文档内容的完整性,平台不提供额外的编辑、内容补充、找答案等附加服务。
- 2、"仅部分预览"的文档,不可在线预览部分如存在完整性等问题,可反馈申请退款(可完整预览的文档不适用该条件!)。
- 3、如文档侵犯您的权益,请联系客服反馈,我们会尽快为您处理(人工客服工作时间:9:00-18:30)。
2000m3 高炉炉型设计说明书
摘要:本设计要求建 2000m3 炼铁高炉。设计主要内容包括高炉炉型设计计算及高炉本体立 剖图,同时对所设计高炉的特点进行简述。设计高炉有效容积为 2000m3,高径比取 2.3,高 炉利用系数取值为 2.0,据此设计高炉炉型。设计本着优质、高产、低耗和对环境污染小的 宗旨,为日产生铁 4000t 的高炉提供高炉内型设计。设计说明书对 2000m3 高炉内型进行了 的详细的计算,并结合国内外相同炉容高炉的先进生产操作经验及相关的数据,力求设计的 高炉达到高度机械化、自动化和大型化,达到最佳的生产效益。 关键词:高炉发展;高炉炉型;炉型计算;
3
②炉缸 高炉炉型下部的圆筒部分为炉缸,炉缸的上、中、下部位分别没有 风口、渣口与铁口,现代大型高炉多不设渣口。炉缸下部容积盛装液态渣铁,上 部空间为风口的燃烧带。
(1)炉缸直径 炉缸直径过大和过小都直接影响高炉生产。直径过大将导 致炉腹角过大,边缘气流过分发展,中心气流不活跃而引起炉缸堆积,同时加速 对炉衬的侵蚀;炉缸直径过小限制焦炭的燃烧.影响产员的提高。炉缸截面积应 保证一定数量的焦炭和喷吹燃料的燃烧,炉缸截面燃烧强度是高炉冶炼的一个重 要指标,它是指每 1h 每 1m3 炉缸截面积所烧侥的焦炭的数量,一般为 1.00~ 1.25t/(m 2·h)。炉缸截面燃烧强度的选择,应与风机能力和原燃料条件相适应, 风机能力大、原料透气性好、燃料可燃性好的燃烧强度可选大些,否则选低值。
(1)无型阶段-又称生吹法。在土坡挖洞,四周砌行块,以木炭冶炼,这 是原始的方法。
(2)大腰阶段-炉腰尺寸过大的炉型。出于当工业不发达,高炉冶炼以人 力、蓄力、风力、水力鼓风,鼓风能力很弱,为了保证整个炉缸截面获得高温, 炉缸直径很小,冶炼以木炭或无烟煤为燃料,机械强度很低,为了避免高炉下部 燃料被压碎,从而影响料柱透气性,故有效高度很低;为了人工装料方便并能够 将炉料装到炉喉中心.炉喉直径也很小,而大的炉腰直径减小了烟气流速度,延 长了烟气在炉内停留时间,起到焖住炉内热量的作用。因此,炉缸和炉喉直径小, 有效高度低,而炉腰直径很大。这类高炉生产率很低,一座 28m3 高炉日产量只 有 1.5 t 左右。
(3)近代高炉-由于鼓风机能力进一步提高.原燃料处理更加精细, 高炉 炉型向着“大型横向”发展。 高炉内型合理与否对高炉冶炼过程有很大影响。 炉型设计合理是获得良好技术经济指标,保证高炉操作顺行的基础。 1.2 五段式高炉
①高炉有效客积和有效高度 高炉大钟下降位置的下沿到铁口中心线间的距 离称为高炉有效高度,对于无钟炉顶为旋转溜槽最低位置的下缘到铁口中心线之 间的趴离。在有效高度范围内,炉型所包括的容积称为高炉有效容积。高炉的有 效高度,对高炉内煤气与炉料之间传热传质过程行很大影响。在相同炉窖和冶炼 强度条件下,增大有效高度,炉料与煤气流接触机会增多,有利于改善传热传质 过程、降低燃料消耗;仅过分增加有效高度,料校对煤气的阻力增大.容易形成 料供,对炉科下降不利。高炉有效高度应适应原燃料条件,如原燃料强度、粒度 及均匀性等。生产实践证明,高炉有效高度与有效容积有一定关系,但不是直线 关系,当有效容积增加到—定值后,有效高度的增加则不显著。
高冶炼强度、高富氧喷煤比和长寿命化作为大型高炉操作的主要优势受到大 家越来越高的关注和青睐,但是高炉大型化作为一项系统工程,它在立足自身条 件的基础上仍须匹配的炼钢、烧结和炼焦能力。我国近年推出的《钢铁产业发展 政策》中规定高炉炉容在 300m3 以下归并为淘汰落后产能项目,且仍存在扩大小 高炉容积的淘汰范围的趋势。同时国内钢铁产业的快速发展均加速了世界和我国 高炉大型化的发展进程。由于大型化高炉具备的单位投资省、效能高和成本低等 特点,从而有效地增强了其竞争力。
绪论
最近二十年来,日本和欧盟区的在役高炉座数由 1990 年的 65 座和 92 座下降 到 28 座和 58 座,下降幅度分别为 56.9%和 37%,但是高炉的平均容积却分别由 1558m3 和 1690m3 上升到 4157m3 和 2063m3,上升幅度为 166.8%和 22%,这基本代 表了国外高炉大型化的发展状况。
(2)炉缸高度 炉缸高度的确定,包括渣口高度、风口高度以及风口安 装尺寸的确定。 铁口位于炉缸下水平面,铁口数目根据高炉炉容或高炉产量而 定,一般 1000m3 以下高炉设一个铁口,1500~3000m3 高炉设 2~3 个铁口,3000m3 以上高炉设 3~4 个铁口,或以每个铁口日出铁量 1500—3000t 设铁口数目。原 则上出铁口数目取上限,有利于强化高炉冶炼。 渣口中心线与铁口中心线间距 离称为渣口高度,它取决于原料条件,即渣量的大小。渣口过高,下渣量增加, 对铁口的维护不利;渣口过低,易出现渣中带铁事故,从而损坏渣口,大、中型 高炉渣口高度多为 1.5~1.7m。
我国高炉大型化的发展模式与国外基本相近,主要是采取新建大型高炉、以 多座旧小高炉合并成大型高炉和高炉大修扩容等形式来推动着高炉的大型化发 展。据不完全统计,我国自 2004 年以来相继建成投产的 3200m3 级 15 座,4000m3 级 8 座,5000m3 级 3 座,且有越来越大的趋势。目前,河北迁钢和山东济钢等 企业也正在建设 4000m3 级高炉,近来宝钢湛江和武钢防城港项目也在规划筹建
目录
摘 要 ..............................................................................................................................1 绪 论 ..............................................................................................................................2 第一章 高炉炉型 ...................................................................................................... .....3 1.1 炉型的发展过程......................................................................................................3 1.2 五段式高炉...............................................................................................................4 第二章 高炉炉型设计计算 .........................................................................................3
2.1 定容积 .............................................................................................................5 2.2 确定年工作日和日产量 ..............................................................................5 2.3 炉缸尺寸 .........................................................................................................5 2.4 死铁层厚度 .....................................................................................................5 2.5 炉腰直径、炉腰角、炉腹高度 .................................................................6 2.6 炉喉直径、炉喉高度 ...................................................................................6 2.7 炉身角、炉身高度、炉腰高 .....................................................................7 2.8 有效容积校核 ............................................................................................... 7 第三章 结论 .....................................................................................................................8 附录 ...................................................................................................................................8 参考文献 ..........................................................................................................................11 致谢 ...................................................................................................................... 我国高炉大型化的标准主要是依据高炉容积的大小来划分的,且衡量标准也