常减压装置工艺流程说明
常减压装置工艺流程

常减压装置工艺流程常减压装置是一种用于能量和压力的降低的设备,常用于化工、石油和天然气等行业。
下面是一个常减压装置的工艺流程的简要描述。
1. 原料准备:首先需要将原料输入到常减压装置中。
原料可以是能量和压力相对较高的物质,例如高压气体或液体。
2. 进料系统:原料通过一个进料系统进入到常减压装置中。
进料系统包括进料管道、阀门和调节装置,用于控制原料的流动和压力。
3. 减压系统:常减压装置的核心部分是减压系统。
减压系统包括减压阀和减压过程控制装置。
减压阀通过控制进料压力和出料压力的差异,实现压力的降低。
减压过程控制装置可以根据需要调整减压速度和压力水平。
4. 分离系统:在减压过程中,原料中可能会存在一些杂质或不需要的物质。
分离系统用于将这些杂质或不需要的物质与主要产物进行分离。
分离系统可以包括分离柱、分离塔等设备。
5. 冷却系统:减压后的物质往往具有较高的温度。
冷却系统用于降低物质的温度,以防止进一步的反应或损坏设备。
6. 收集和处理系统:常减压装置产生的产物需要进行收集和处理。
收集系统用于收集产物,处理系统用于对产物进行进一步的处理和利用。
7. 控制系统:常减压装置需要一个控制系统来控制各个过程的顺序和参数。
控制系统可以包括传感器、计算机和控制阀。
8. 安全系统:常减压装置属于高风险设备,需要具备一套完善的安全系统。
安全系统可以包括温度、压力和流量的监测和报警装置,以及紧急停机装置。
9. 能源系统:常减压装置需要能源来提供动力和支持运行。
能源系统可以包括电力供应、燃料供应和冷却水供应等。
10. 维护和保养:常减压装置需要定期进行维护和保养,以确保设备的正常运行和延长使用寿命。
以上是一个常减压装置的工艺流程的简要描述。
实际的工艺流程可能会根据具体的设备和生产要求有所差异。
对于常减压装置的设计和操作,还需要根据具体的项目需求和技术要求进行详细的分析和评估。
常减压装置工艺流程简述

常减压装置工艺流程简述
一、概述
常减压装置是一种用于石油化工生产中的重要设备,主要用于对原油、天然气等物质进行分离和提纯。
其工艺流程包括以下几个步骤:加热、蒸发、分馏、冷凝等。
二、加热
在常减压装置中,首先需要将原料进行加热,以使其达到蒸发的温度。
加热的方式有多种,包括外部加热和内部加热。
外部加热通常采用蒸
汽或电加热器等方式,而内部加热则是通过在设备内设置换热器来实现。
三、蒸发
当原料达到一定温度后,开始进入蒸发阶段。
在这个过程中,原料会
逐渐转化为气态,并且随着温度的升高而不断增多。
同时,在设备内
设置的分离板也会起到重要作用,帮助将不同成分的气体进行分离。
四、分馏
经过蒸发后,原料已经被分解成了多种组分。
在分馏阶段,需要根据
这些组分的物理性质进行进一步处理,并将它们分离出来。
这个过程中,常减压装置内设置的分馏塔会起到关键作用。
在分馏塔内,不同
组分的气体会根据其密度和沸点等特性进行分离,最终得到纯净的产品。
五、冷凝
在分馏结束后,需要将气态产物重新转化为液态。
这个过程称为冷凝。
常减压装置中通常采用水冷或空气冷却等方式进行冷凝。
通过这个过程,可以将产物从气态转化为液态,并且去除其中的杂质和不纯物质。
六、总结
以上就是常减压装置的工艺流程简述。
需要注意的是,在实际生产中,还需要考虑多种因素,如温度、压力、流量等参数的控制和调整。
只
有合理地控制这些因素,并根据实际情况进行灵活调整,才能获得高效、可靠的生产效果。
常减压操作步骤

1、设备和管线的水冲洗、单机试运、水联运1.1 水冲洗的目的(1)将施工中遗留在设备、管线内的铁锈、焊渣等杂物冲洗干净,防止在运转时卡坏阀门、法兰、孔板,堵塞管线、设备和机泵。
(2)检查在管线、设备、阀门、法兰、焊缝有无泄漏,保证管线、设备畅通。
(3)进一步考验机泵安装质量、性能及其他设备施工质量。
(4)通过对装置的水冲洗、水联运,急躁发现处理问题,同时进行技术练兵,使操作人员进一步熟悉工艺流程及仪表控制方案,为装置首次开车一次成功打下坚实基础。
1.2 水冲洗前的准备工作(1)管线做好标记,注明介质名称和走向,阀门写上介质走向和用途。
(2)机泵出口安装好合适的压力表,机泵进口安装好过滤网,对机泵进行开泵前的有关检查。
(3)关所有塔壁阀门。
联系仪表对各塔的液位进行调试。
(4)加热炉管进料均加过滤网,避免杂物冲入炉管。
(5)所有系统管线控制阀均已拆下,仪表流量孔板亦要拆开加上垫片,关闭仪表引线手阀和安全阀,冲洗时先走副线,然后冲洗短管,待完全冲洗干净后照原样装上。
(6)打开常压塔、减压塔顶人孔,以备装水时应用,避免损坏设备。
(7)联系调度将新鲜水送至装之前,并协商好外管道的水冲洗方案。
1.3 水冲洗的原则和注意事项1.3.1 原则:(1)水冲洗时,要求动力车间协调配合,保证新鲜水出口压力0.5MPa以上,流量100m3/h才能冲洗管线中的泥沙、焊渣等杂质。
(2)冲洗时原则上水不进容器、换热器、塔器,确实必须进设备的要等管线冲洗干净后才能进设备。
(3)冲洗时设备开口要加保护挡板,开口法兰间隙至少要有1cm以上距离,满足冲洗要求。
(4)冲洗顺序一般要求从上往下冲洗,流量不足的可以启泵打水从下往上冲洗。
(5)机泵入口管线冲洗干净后加恢复入口过滤器后才能启运。
1.3.2 注意事项:(1)系统进行冲洗时,严禁不合格的介质进入机泵、换热器、塔、容器等设备,管道上的孔板、流量计、调节阀、测温元件等在冲洗或吹扫时应予拆除,焊接的阀门要拆掉阀芯或全开。
常减压装置说明书

一、工艺流程1.1装置概况本装置为石油常减压蒸馏装置,原油经原油泵(P-1/1.2)送入装置,到装置内经两路换热器,换热至120℃,加入一定量的破乳剂和洗涤水,充分混合后进入电脱盐罐(V1)进行脱盐。
脱后原油经过两路换热器,换热至235℃进入初馏塔(T1)闪蒸。
闪蒸后的拔头原油经两路换热器,换热至310℃,分四股进入常压塔加热炉(F1)升至368℃进入常压塔(T2)。
常压塔塔底重组分经泵送到减压塔加热炉(F2)升温至395℃进入减压塔(T4)。
减压塔塔底渣油经两路换热器,送出装置。
1.2工艺原理1.2.1原油换热罐区原油(45℃)经原油泵P-1/1.2进入装置,分两路进行换热。
一路原油与E-1(常顶气)、E-2(常二线)、E-3(减一线)、E-4(减三线)、E-5(常一线)、E-6(减渣油)换热到120℃;二路原油与E-14(常顶气)、E-16(常二线)、E-17(减二线)换热到127.3℃。
两路原油混合换热后温度为120℃,注入冷凝水,经混合阀(PDIC-306)充分混合后,进入电脱盐罐(V-1)进行脱盐脱水。
脱后原油分成两路进行换热,一路脱后原油与E-7(常二线)、E-8(减二线)、E-9/1.2(减三线)、E-10/1~4(渣油)换热到239.8℃;二路脱后原油与E-11/1.2(减一中)、E-12/1.2(常二线)、E--13/1.2(减渣)换热到239.7℃。
两路脱后原油换热升温到230℃合为一路进入初馏塔(T-1)汽化段。
初馏塔塔顶油气经空冷气(KN-5/1~5)冷凝到77℃,进入初顶回流罐(V-2)。
油气经分离后,液相用初顶回流泵(P-4/1.2)打回初馏塔顶作回流,其余油气继续由初顶空冷器(KN-1/1~3)、初顶后冷器(N-1)冷却到40℃,进入初顶产品罐(V-3)。
初馏塔侧线油从初馏塔第10层用泵(P-6/1.2)抽出与常一中返塔线合并送到常压塔第33层塔盘上。
初馏塔底拔头油,经初底泵(P-2/1.2)抽出分两路换热。
【常减压工艺流程】常减压工艺流程的原理
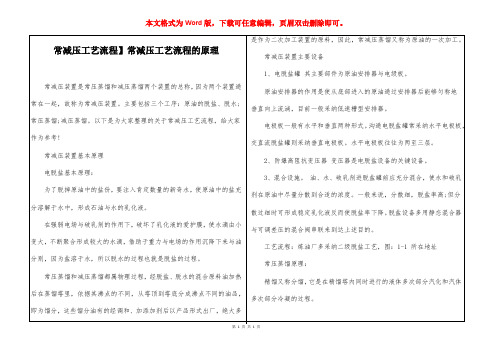
五括钢结构、炉管、炉墙、燃烧器、孔类配件等。
它分为自然通风和强制通风两种方式。前者依靠烟囱本身的抽力,后
第1页共1页
者使用风机。
本文格式为 Word 版,下载可任意编辑,页眉双击删除即可。
过去,绝大多数炉子都采纳自然通风方式,烟囱安装在炉顶。
随着炉子的结构冗杂化,炉内烟气侧阻力增大,加之提高加热炉的热
蒸塔、常压塔、减压塔。
的是管孔式液体分布器和喷淋型液体分布器。
、蒸馏塔的结构:
气体分布器:气体分布器一般应用在汽提蒸汽入塔处,目的是使蒸汽
塔体:塔体是由直圆柱型桶体,高度在 35~40 米左右,材质一般为 匀称分布。
第1页共1页
本文格式为 Word 版,下载可任意编辑,页眉双击删除即可。
破沫 XX:在减压塔进料上方,一般都装有破沫 XX,破沫 XX 由丝 XX
以靠预热燃烧空气来回收,使回收的热量再次返回到炉中
烧时产生的高温火焰与烟气作为热源,加热炉中高速流淌的物料,使其到
是采纳另外的系统回收热量。前者称为空气预热方式,后者通用水回
达后续工艺过程所要求的温度。
收称为废热锅炉方式。
管式加热炉一般由辐射室、对流室、余热回收系统、燃烧及通风系统
燃烧及通风系统:通风系统的作用是把燃烧用空气导入燃烧器,将废
散过细时可形成稳定乳化液反而使脱盐率下降。脱盐设备多用静态混合器
在强弱电场与破乳剂的作用下,破坏了乳化液的爱护膜,使水滴由小 与可调差压的混合阀串联来到达上述目的。
变大,不断聚合形成较大的水滴,借助于重力与电场的作用沉降下来与油
工艺流程:炼油厂多采纳二级脱盐工艺,图:1-1 所在地址
分别,因为盐溶于水,所以脱水的过程也就是脱盐的过程。
常在一起,故称为常减压装置。主要包括三个工序:原油的脱盐、脱水; 垂直向上流淌,目前一般采纳低速槽型安排器。
常减压蒸馏装置工艺流程图

可再生能源
利用太阳能、风能等可再生能源,减少 化石燃料的使用,降低碳排放,促进能源 可持续利用。
能源监测
建立能源管理信息系统,实时监测能源 使用情况,及时发现异常情况并采取措 施,提高能源利用效率。
产品质量控制
严格检测
对所有生产的产品进行全面、 细致的理化检测,确保产品指 标符合质量标准。
抽样分析
离方法,提高分离效率和纯 度。
3 提高能源利用率
采用节能技术,如废热回收 利用,降低整体能耗。
4 降低生产成本
优化原料、催化剂、工艺参 数等,减少原材料消耗和废 弃物产生。
设备检修
定期检查
定期检查装置内各设备的运行状态,及 时发现并修复故障,确保设备安全可靠 运行。
及时维修
发现问题后立即采取维修措施,防止故 障扩散,最大限度减少对生产的影响。
产品包装
合适的包装材料
1
选用安全环保的包装材料,如玻璃瓶、塑料容器或金属罐
,以确保产品的密封性和防渗漏性。
2
适当的包装尺寸
根据产品特性和客户需求,设计不同容量的包装规格,满
醒目的标签设计
3
足不同消费场景。
在包装上印刷产品名称、成分、生产日期等关键信息,同
时兼顾美观大方的视觉效果。
废气处理
尾气洁净
1
确保废气排放达到环保标准
液态回收 2
从废气中回收可用液体成分
热量回收 3
利用废气热量进行能源回收
常减压蒸馏装置会产生各种废气,包括含有有机物的尾气、酸性气体和含热量较高的气体。通过设置多级废气处理系统,可以实现 尾气洁净、液态成分回收以及热量回收,最大限度地提高资源利用率,降低环境影响。
冷却水系统
常减压蒸馏装置的工艺流程01
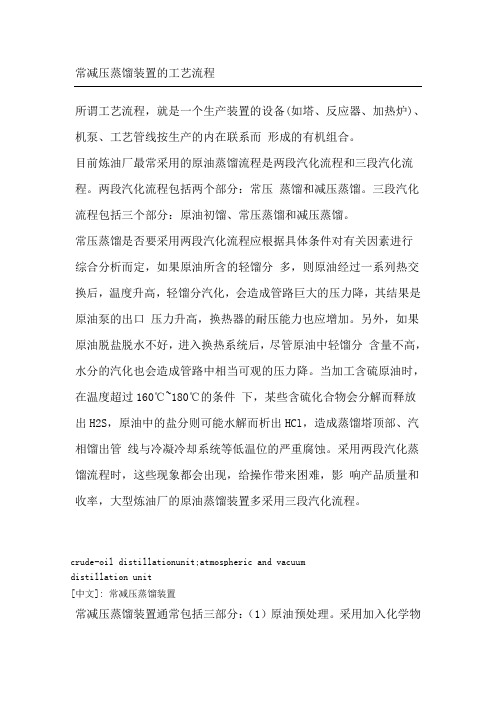
常减压蒸馏装置的工艺流程所谓工艺流程,就是一个生产装置的设备(如塔、反应器、加热炉)、机泵、工艺管线按生产的内在联系而形成的有机组合。
目前炼油厂最常采用的原油蒸馏流程是两段汽化流程和三段汽化流程。
两段汽化流程包括两个部分:常压蒸馏和减压蒸馏。
三段汽化流程包括三个部分:原油初馏、常压蒸馏和减压蒸馏。
常压蒸馏是否要采用两段汽化流程应根据具体条件对有关因素进行综合分析而定,如果原油所含的轻馏分多,则原油经过一系列热交换后,温度升高,轻馏分汽化,会造成管路巨大的压力降,其结果是原油泵的出口压力升高,换热器的耐压能力也应增加。
另外,如果原油脱盐脱水不好,进入换热系统后,尽管原油中轻馏分含量不高,水分的汽化也会造成管路中相当可观的压力降。
当加工含硫原油时,在温度超过160℃~180℃的条件下,某些含硫化合物会分解而释放出H2S,原油中的盐分则可能水解而析出HCl,造成蒸馏塔顶部、汽相馏出管线与冷凝冷却系统等低温位的严重腐蚀。
采用两段汽化蒸馏流程时,这些现象都会出现,给操作带来困难,影响产品质量和收率,大型炼油厂的原油蒸馏装置多采用三段汽化流程。
crude-oil distillationunit;atmospheric and vacuumdistillation unit[中文]: 常减压蒸馏装置常减压蒸馏装置通常包括三部分:(1)原油预处理。
采用加入化学物质和高压电场联合作用下的电化学法除去原油中混杂的水和盐类。
(2)常压蒸馏。
原油在加热炉内被加热至370℃左右,送入常压蒸馏塔在常压(1大气压)下蒸馏出沸点较低的汽油和柴油馏分,残油是常压重油。
(3)减压蒸馏。
常压重油再经加热炉被加热至410℃左右,进入减压蒸馏塔在约8.799千帕(60毫米汞柱)绝压下蒸馏,馏出裂化原料的润滑油原料,残油为减压渣油。
参见原油蒸馏。
仅供个人用于学习、研究;不得用于商业用途。
For personal use only in study and research; not for commercial use.Nur für den persönlichen für Studien, Forschung, zu kommerziellen Zwecken verwendet werden.Pour l 'étude et la recherche uniquement à des fins personnelles; pas à des fins commerciales.толькодля людей, которые используются для обучения, исследований и не должны использоваться в коммерческих целях.以下无正文仅供个人用于学习、研究;不得用于商业用途。
石油炼制常压减压蒸馏装置

第十四章石油炼制常压减压蒸馏装置一、常减压蒸馏装置概述及工艺流程说明1、装置概述装置主要设备有30台, 各类设备参数如下。
(1) 加热炉2台常压炉1 台, 138,160,000 kJ/h减压炉1台, 75,360,000 kJ/h(2) 蒸馏塔4座初馏塔(塔-1):φ 3000×26033 mm常压塔(塔-2):φ3800×34962 mm汽提塔(塔-3):φ1200×24585 mm减压塔(塔-4):φ6400/φ3200×38245 mm(3) 冷换设备116台(不包括空气预热器)换热器76台,总换热面积11455 m2,其中用于发生蒸汽有1140 m2,用于加热电脱盐注水175 m2;冷凝冷却器40 台,总冷却面积10180 m2。
(4) 泵55台电动离心泵42台,蒸汽往复泵1台,计量泵10台,刮板泵2台。
(5) 风机1台。
(6) 容器 33个(7) 吹灰器26台其中伸缩式4台,固定式22台。
2、工艺流程说明(1)原油换热系统①原油从油罐靠静位能压送到原油泵(1#、2#)进口,在原油泵进口注入利于保证电脱盐效果的破乳剂和新鲜水,经泵后再注入热水,然后分三环路与热油品换热到110~120℃,进入电脱盐罐进行脱盐脱水。
②原油在电脱盐罐内经20000V高压交流电所产生的电场力作用,微小的水滴聚集成大水滴,依靠密度差沉降下来,从而与原油分离。
因原油中的盐分绝大部分溶于水中,故脱水其中也包括脱盐。
③原油从电脱盐罐出来后注入NaOH,目的是把原油残留的容易水解的MgCl、CaCl2转2化为不易水解的NaCl,同时中和原油中的环烷酸、H2S等,降低设备腐蚀速率,延长开工周期。
然后经接力泵(01#,02#)后分三路,其中二路继续与热油品换热到220~230℃后进初馏塔,另一路则先后经过炉-2、炉-1对流室冷进料管加热到210~220℃后进初馏塔。
(2)初馏系统被加热至220~230℃的原油进入初馏塔(塔-1)第6层(汽化段)后,分为汽液两相,汽相进入精馏段(第6层上至塔顶),液相进入提馏段(第6层下至塔底)。
- 1、下载文档前请自行甄别文档内容的完整性,平台不提供额外的编辑、内容补充、找答案等附加服务。
- 2、"仅部分预览"的文档,不可在线预览部分如存在完整性等问题,可反馈申请退款(可完整预览的文档不适用该条件!)。
- 3、如文档侵犯您的权益,请联系客服反馈,我们会尽快为您处理(人工客服工作时间:9:00-18:30)。
常减压装置工艺流程说明
一、原油换热及初馏部分
原油经原油泵P1001 A-C升压进入装置后分为两路,一路与原油—初顶油气换热器E1001AB换热,然后经过原油—常顶循(II)换热器E1003、原油—减一及减一中换热器E1004、原油—常一中(II)换热器E1005AB、原油—常三线(II)换热器E1006AB,换热后温度升至134℃,与另一路换后原油合并进电脱盐罐V1001;另外一路与原油—常顶油气换热器E1002AB换热后,依次经过原油—常顶循(I)换热器E1007、原油—常一线换热器E1008、原油—常二线(II)换热器E1009、原油—减渣(V)换热器E1010A-C,温度升至138℃,与另一路合并。
合并后温度为136℃的原油至电脱盐。
脱盐后的原油分为两路,一路脱后原油分别经过E1011AB、E1012AB、E1013AB、E1014A-C、E1015AB,分别与减三线(II)、常二线(I)、常二中(II)、减渣(IV)、减二及减二中换热,温度升至240℃。
另一路脱后原油分别
经过E1016、E1018、E1019AB、E1020A-C,分别与减二线、常一中(I)、减三线(I)、减三及减三中(II)换热,温度升至236℃,然后与从E1015AB来的脱后原油合为一路进入初馏塔T1001。
初馏塔顶油气经过E1001AB,与原油换热后再经初顶油气空冷器Ec1001AB、后冷器E1041AB,冷凝冷却到40℃后,进入初馏塔顶回流罐V1002进行气液分离,V1002顶不凝气进入低压瓦斯罐,然后引至加热炉F1001燃烧。
初顶油进入初顶油泵P1002AB,升压后一路作为初馏塔顶回流返回到T1001顶部,另一路作为汽油馏分送至罐区(汽油)。
初馏塔底油经初底泵P1003AB抽出升压后分为两路,一路经初底油—减渣(III)换热器E1021A-D、初底油—常三线(I)换热器E1022、初底油—减三及减三中(I)换热器E1026A-C,换热至297℃;另一路经过初底油—常二中(I)换热器E1025A-C、初底油—减渣(II)换热器E1026A-D换热后温度升至291℃,二路混合后温度为294℃,进入初底油—减渣(I)换热器,温度升至311℃进常压炉F1001,经
加热炉加热至369℃后,进入常压塔T1002进行分离。
二、常压蒸馏部分
常顶油气106℃经原油—常顶油气换热器E1002AB换热至101℃,经常顶油气空冷器Ec1002A-F、常顶油气后冷器E1042AB换热至40℃后,进入常顶回流罐V1003,不凝气经低压瓦斯罐引至加热炉F1001,液相经常顶回流泵P1004AB升压后,一部分作为塔顶回流返回常压塔顶,另一部分作为汽油馏分送至罐区(汽油)。
常一线油自常压塔T1002第15层塔板自流入常一线油汽提塔,用过热蒸汽进行汽提,汽提后的气相返回常压塔T1002第13层板,液相由泵P1005AB抽出,经原油—常一线换热器E1108换热器E1008换热至126℃,经常一线油—瓦斯换热器E1044、常一线油—热水换热器E1031AB、常一线水冷器E1043AB,冷至40℃后,送至罐区(轻柴)。
常二线自常压塔T1002第29层塔板自流入汽提塔T1003中段,用过热蒸汽气提,汽提后的气相返回常压塔T1002第27层塔板,液相由泵P1006AB抽出,经原油—常二线换热
器(I)E1012、原油—常二线换热器E1032AB、常二线油空冷器Ec1003AB,冷至50℃后,送至罐区(轻柴)。
常三线自常压塔T1002第41层塔板自流入汽提塔T1003下段,用过热蒸汽气提,汽提后的气相返回常压塔T1002第39层塔板,液相由泵P1007AB抽出,经初底油—常三线换热器(I)E1022、原油—常三线换热器(II)E1006AB 换热至153℃后,再经常三线油—热水换热器E1033AB换热和常三线空冷器Ec1004AB冷至60℃后,送至罐区(蜡油)。
常顶循油自常压塔T1002第5层塔板由泵P1009AB抽出,经原油—常顶循换热器(I)E1007、原油—常顶循(II)E1003AB,换热至89℃后,返回常压塔顶。
常一中油自常压塔T1002第19层塔板由泵P1010AB抽出,经脱后原油—常一中换热器(I)E1018、原油—常一中换热器(II)E1005AB,换热至150℃后,返回常压塔第16层塔盘。
常二中油自常压塔T1002第33层塔板由泵P1012AB抽出,经初底油—常二中换热器(I)E1025A-C、脱后原油—
常二中换热器(II)E1013AB,换热至202℃后,返回常压塔第30层塔盘。
常压渣油由泵P1012AB抽出,升压后分为两路,一路送至减压炉F1002加热至339℃后,送至减压塔进行分离;另一路经脱后原油—常渣换热器E1014 C、原油—常渣换热器E1010 C 换热后,再分为两路,一路去蜡油罐,一路经常渣—热水换热器E1037后送至燃料油罐。
三、减压部分
减压塔为全填料干式减压塔。
减顶温度为75℃,残压为15mmHg。
减顶油气从减压塔顶出来后,经过增压器后进入减顶增压器EJ1001AB、空冷器Ec1008A-F冷凝冷却至38℃,凝缩油经大气腿流入减顶分水罐V1004;未凝气体经减顶一级抽空器EJ1002AB后,再经减顶一级空冷器Ec1007AB冷凝冷却至40℃,液相经大气腿流入减顶分水罐V1004,气相被减顶二级抽空器EJ1003AB抽出至减顶分水罐V1004,减顶分水罐内的减顶油经减顶油泵P1014AB升压后合并到减一线油出装置,气相至减顶瓦斯罐V1020,分液后引至减压
炉F1002烧掉。
减一线油由减一及减一中油泵P1015AB自T1004第I 段填料下集油箱抽出升压,经原油—减一及一中换热器E1004、减一及一中—热水换热器E1034AB换热后至减一线及一中空冷器EC1005冷却至50℃分为两路:一路作为回流打回T1004顶部,一路作为蜡油出装置。
减二线油由减二及减二中油泵P1016AB自T1004第III段填料下集油箱抽出升压,经脱后原油—减二及二中换热器E1015AB、减二及二中蒸汽发生器ER-1001,温度降为203℃分为两路:一路作为中段回流打回T1004,另一路经脱后原油—减二线换热器E1016后再分为两路,一路作为热进料至催化裂化装置,另一路经减二线—热水器换热器E1035AB冷至90℃后出装置。
减三线油由减三及减三中油泵P1017AB自T1004第IV 段填料下集油箱抽出升压,经初底油—减三及三中(I)换热器E1023A-D、脱后原油—减三及减三中(II)换热器E1020A-C,换热至246℃分为两路:一路作为中段回流打回T1004,另。