常减压装置工艺流程简述
常减压装置工艺流程

常减压装置工艺流程常减压装置是一种用于能量和压力的降低的设备,常用于化工、石油和天然气等行业。
下面是一个常减压装置的工艺流程的简要描述。
1. 原料准备:首先需要将原料输入到常减压装置中。
原料可以是能量和压力相对较高的物质,例如高压气体或液体。
2. 进料系统:原料通过一个进料系统进入到常减压装置中。
进料系统包括进料管道、阀门和调节装置,用于控制原料的流动和压力。
3. 减压系统:常减压装置的核心部分是减压系统。
减压系统包括减压阀和减压过程控制装置。
减压阀通过控制进料压力和出料压力的差异,实现压力的降低。
减压过程控制装置可以根据需要调整减压速度和压力水平。
4. 分离系统:在减压过程中,原料中可能会存在一些杂质或不需要的物质。
分离系统用于将这些杂质或不需要的物质与主要产物进行分离。
分离系统可以包括分离柱、分离塔等设备。
5. 冷却系统:减压后的物质往往具有较高的温度。
冷却系统用于降低物质的温度,以防止进一步的反应或损坏设备。
6. 收集和处理系统:常减压装置产生的产物需要进行收集和处理。
收集系统用于收集产物,处理系统用于对产物进行进一步的处理和利用。
7. 控制系统:常减压装置需要一个控制系统来控制各个过程的顺序和参数。
控制系统可以包括传感器、计算机和控制阀。
8. 安全系统:常减压装置属于高风险设备,需要具备一套完善的安全系统。
安全系统可以包括温度、压力和流量的监测和报警装置,以及紧急停机装置。
9. 能源系统:常减压装置需要能源来提供动力和支持运行。
能源系统可以包括电力供应、燃料供应和冷却水供应等。
10. 维护和保养:常减压装置需要定期进行维护和保养,以确保设备的正常运行和延长使用寿命。
以上是一个常减压装置的工艺流程的简要描述。
实际的工艺流程可能会根据具体的设备和生产要求有所差异。
对于常减压装置的设计和操作,还需要根据具体的项目需求和技术要求进行详细的分析和评估。
常减压蒸馏装置工艺流程图

可再生能源
利用太阳能、风能等可再生能源,减少 化石燃料的使用,降低碳排放,促进能源 可持续利用。
能源监测
建立能源管理信息系统,实时监测能源 使用情况,及时发现异常情况并采取措 施,提高能源利用效率。
产品质量控制
严格检测
对所有生产的产品进行全面、 细致的理化检测,确保产品指 标符合质量标准。
抽样分析
离方法,提高分离效率和纯 度。
3 提高能源利用率
采用节能技术,如废热回收 利用,降低整体能耗。
4 降低生产成本
优化原料、催化剂、工艺参 数等,减少原材料消耗和废 弃物产生。
设备检修
定期检查
定期检查装置内各设备的运行状态,及 时发现并修复故障,确保设备安全可靠 运行。
及时维修
发现问题后立即采取维修措施,防止故 障扩散,最大限度减少对生产的影响。
产品包装
合适的包装材料
1
选用安全环保的包装材料,如玻璃瓶、塑料容器或金属罐
,以确保产品的密封性和防渗漏性。
2
适当的包装尺寸
根据产品特性和客户需求,设计不同容量的包装规格,满
醒目的标签设计
3
足不同消费场景。
在包装上印刷产品名称、成分、生产日期等关键信息,同
时兼顾美观大方的视觉效果。
废气处理
尾气洁净
1
确保废气排放达到环保标准
液态回收 2
从废气中回收可用液体成分
热量回收 3
利用废气热量进行能源回收
常减压蒸馏装置会产生各种废气,包括含有有机物的尾气、酸性气体和含热量较高的气体。通过设置多级废气处理系统,可以实现 尾气洁净、液态成分回收以及热量回收,最大限度地提高资源利用率,降低环境影响。
冷却水系统
常减压流程

常减压工艺流程简述一、加工方案根据原油性质和产品要求,常减压装置可以分为三种类型:1.燃料型除生产重整原料、汽油组分、煤油、柴油和燃料油外,减压馏分油和减压渣油进行二次加工,如通过催化裂化或加氢裂化转化为各种轻质燃料,在此方案中,减压塔是燃料型的,不生产润滑油组分原料。
2.燃料-润滑油型(我厂三套常减压全为此类型)除生产重整原料、汽油组分、煤油、柴油和燃料油外,部分或大部分减压馏分油和减压渣油还被用于生产各种润滑油产品。
其中减压塔是润滑油型减压塔。
3.燃料-化工型除生产重整原料、汽油组分、煤油、柴油和燃料油外,还生产化工原料和化工产品。
塔顶石脑油作为重整原料制取芳烃,轻质油一部分作燃料,一部分裂解制烯烃,重馏分油作为催化裂化原料生产制取轻质燃料。
在此方案中,减压塔也是燃料型的。
二、常减压工艺流程在原油蒸馏过程中,精馏塔是最重要的设备,除此之外,还有电脱盐罐、加热炉、冷换热设备以及机泵、管线自控仪表等。
40℃左右的原油由罐区进入装置,经换热器热至130℃左右,进入电脱盐罐,在电场和破乳剂的作用下进行脱盐、脱水,要求脱后含盐小于3mg/L,含水小于0.5%;脱后原油再经过换热器换热至200-240℃进入初馏塔,从初馏塔顶馏出汽油组分或重整原料,初馏塔底油由泵抽出经换热后送至常压炉加热到360℃左右进入常压塔。
原油在常压塔中进行分馏,塔顶生产汽油组分或重整原料,侧线生产煤油、喷气燃料、轻重柴油等。
常压塔一般设置2个中段回流。
常压塔底油是高于350℃的组分,称为常压重油。
常压重油用泵送至减压炉加热至380-400℃进入减压塔。
通过真空系统,使之在减压条件下进行蒸馏。
塔顶一般馏出的是裂解气、蒸汽和少量的油气。
减压蜡油由侧线抽出,可作为催化裂化、加氢裂化的原料,也可作为润滑油原料。
减压渣油一般作为燃料油、焦化原料、催化裂化原料。
三、工艺过程1.一脱三注包括原油电脱盐、分馏塔顶注氨、注水、注缓蚀剂(我厂常减压蒸馏在塔顶只注水和缓蚀剂),目的是为了脱除原油中的盐和减轻塔顶腐蚀。
常减压规程 (2)
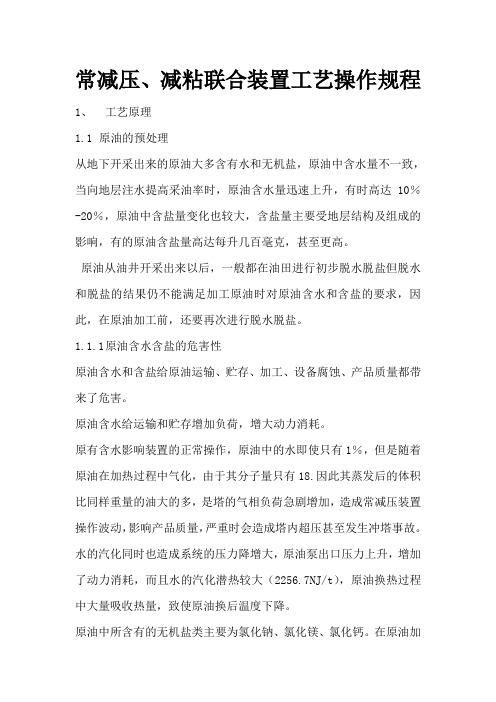
常减压、减粘联合装置工艺操作规程1、工艺原理1.1原油的预处理从地下开采出来的原油大多含有水和无机盐,原油中含水量不一致,当向地层注水提高采油率时,原油含水量迅速上升,有时高达10%-20%,原油中含盐量变化也较大,含盐量主要受地层结构及组成的影响,有的原油含盐量高达每升几百毫克,甚至更高。
原油从油井开采出来以后,一般都在油田进行初步脱水脱盐但脱水和脱盐的结果仍不能满足加工原油时对原油含水和含盐的要求,因此,在原油加工前,还要再次进行脱水脱盐。
1.1.1原油含水含盐的危害性原油含水和含盐给原油运输、贮存、加工、设备腐蚀、产品质量都带来了危害。
原油含水给运输和贮存增加负荷,增大动力消耗。
原有含水影响装置的正常操作,原油中的水即使只有1%,但是随着原油在加热过程中气化,由于其分子量只有18.因此其蒸发后的体积比同样重量的油大的多,是塔的气相负荷急剧增加,造成常减压装置操作波动,影响产品质量,严重时会造成塔内超压甚至发生冲塔事故。
水的汽化同时也造成系统的压力降增大,原油泵出口压力上升,增加了动力消耗,而且水的汽化潜热较大(2256.7NJ/t),原油换热过程中大量吸收热量,致使原油换后温度下降。
原油中所含有的无机盐类主要为氯化钠、氯化镁、氯化钙。
在原油加工过程中由于氯化镁、氯化钙水解产生强腐蚀性的氯化氢,尤其在溶于水形成盐酸后富腐蚀就更加严重,这种腐蚀常发生在塔顶冷凝冷却系统。
另外,在加热炉管及换热设备中,由于水份蒸发使盐沉积下来而结垢,影响传热,同时使炉管寿命缩短,压力降增大,严重时可使炉管或换热器堵塞,造成装置停工。
原油加工后,无机盐类进入重油渣油中,将影响燃料油、沥青的产品质量并造成重油加工的催化剂中毒。
为了消除原油含水含盐对加工过程的危害,一般要求原油在加工前进行脱水脱盐,本装置采用二级电脱盐设备,脱后原油含水量要求小于0.1%,含盐量要求在3㎎/1-5㎎/1.1.1.2脱水脱盐原理由于原油中的盐类,大部分是溶于所含水中的。
常减压装置工艺流程说明

常减压装置工艺流程说明一、原油换热及初馏部分原油经原油泵P1001 A-C升压进入装置后分为两路,一路与原油—初顶油气换热器E1001AB换热,然后经过原油—常顶循(II)换热器E1003、原油—减一及减一中换热器E1004、原油—常一中(II)换热器E1005AB、原油—常三线(II)换热器E1006AB,换热后温度升至134℃,与另一路换后原油合并进电脱盐罐V1001;另外一路与原油—常顶油气换热器E1002AB换热后,依次经过原油—常顶循(I)换热器E1007、原油—常一线换热器E1008、原油—常二线(II)换热器E1009、原油—减渣(V)换热器E1010A-C,温度升至138℃,与另一路合并。
合并后温度为136℃的原油至电脱盐。
脱盐后的原油分为两路,一路脱后原油分别经过E1011AB、E1012AB、E1013AB、E1014A-C、E1015AB,分别与减三线(II)、常二线(I)、常二中(II)、减渣(IV)、减二及减二中换热,温度升至240℃。
另一路脱后原油分别经过E1016、E1018、E1019AB、E1020A-C,分别与减二线、常一中(I)、减三线(I)、减三及减三中(II)换热,温度升至236℃,然后与从E1015AB来的脱后原油合为一路进入初馏塔T1001。
初馏塔顶油气经过E1001AB,与原油换热后再经初顶油气空冷器Ec1001AB、后冷器E1041AB,冷凝冷却到40℃后,进入初馏塔顶回流罐V1002进行气液分离,V1002顶不凝气进入低压瓦斯罐,然后引至加热炉F1001燃烧。
初顶油进入初顶油泵P1002AB,升压后一路作为初馏塔顶回流返回到T1001顶部,另一路作为汽油馏分送至罐区(汽油)。
初馏塔底油经初底泵P1003AB抽出升压后分为两路,一路经初底油—减渣(III)换热器E1021A-D、初底油—常三线(I)换热器E1022、初底油—减三及减三中(I)换热器E1026A-C,换热至297℃;另一路经过初底油—常二中(I)换热器E1025A-C、初底油—减渣(II)换热器E1026A-D换热后温度升至291℃,二路混合后温度为294℃,进入初底油—减渣(I)换热器,温度升至311℃进常压炉F1001,经加热炉加热至369℃后,进入常压塔T1002进行分离。
常减压装置概述(实习报告)

常减压装置主要工艺流程路线及重要工艺条件1 主要工艺路线1.1 初馏系统原油自装置外原油罐区来,经原油泵后分两路送入脱前原油换热系统。
脱前原油分别与初定循环油、常顶循环油、常一线油、常二线油、常三线油、减一线油、常一中油和常二中油进行换热,脱后原油分别与常一线油、常二线油、常三线油、常一中油、常二中油、减一线油、减二线油、减三线油、减一中油、减二中油和减渣油进行换热。
两路脱盐原油换热后合并进入初馏塔,混合后的脱盐原油温度为253℃。
初馏塔共26层塔板,合并后的脱盐原油从初馏塔第四层塔板送入塔内蒸馏。
初馏塔定的油气与原油换热到87℃,进入初顶空冷器冷凝冷却到60℃,再进过初顶水冷器冷凝冷却到40℃后进入初顶回流以及产品罐进行气液分离。
初顶不凝气从产品管顶部送至初顶气分液罐作为常压加热炉的燃料,初顶气也可进入压缩机入口分液罐经压缩机升压后去焦化装置脱硫;初顶油用初顶回流及产品泵从产品罐中抽出,一部分打回初馏塔顶做回流,另一部分送至轻烃回收部分回收其中的轻烃;产品罐中的水相与常顶回流及常压产品罐的水相一起作为含硫污水由常顶含硫污水泵送出装置。
初侧线油从初馏塔的第十六层或第十二层塔板送出,由初侧泵送至常压塔与常一中返塔线合并送入常压塔。
初底油从初馏塔顶抽出,经初低泵送入初底油换热系统换热。
初底油在换热前分成两路,与常二中油、常三线油、减二中油和渣油进行换热,温度达到295℃,再分八路送入常压炉加热,升温至358℃,进入常压塔第六层塔盘。
1.2 常压系统常压塔共50层塔盘,加热后初底油作为进料从第六层塔盘进入,气提蒸汽由塔底通入。
常压塔顶油气经常顶空冷器冷却冷凝至60℃,再经常顶水冷器冷凝冷却至40℃后送入常顶回流及产品罐,在此进行气液分离。
常顶不凝气从常顶回流及产品罐顶部送出,与自减顶分水罐来的减顶气混合后一起经压缩机入口分凝罐分液并经常顶气压缩机升压后送出装置,至焦化装置做进一步处理。
需要时常顶气课由压缩机入口分液罐直接去常减顶燃料气分液罐,作为常压炉的燃料;常顶回流及产品泵将常顶油从常顶回流及产品罐中抽出,送出装置。
常减压装置加工方案和工艺流程
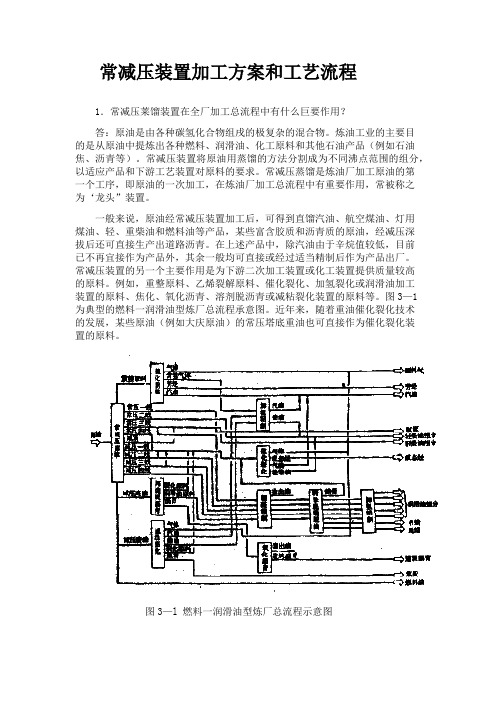
常减压装置加工方案和工艺流程1.常减压莱馏装置在全厂加工总流程中有什么巨要作用?答:原油是由各种碳氢化合物组戌的极复杂的混合物。
炼油工业的主要目的是从原油中提炼出各种燃料、润滑油、化工原料和其他石油产品(例如石油焦、沥青等)。
常减压装置将原油用蒸馏的方法分割成为不同沸点范围的组分,以适应产品和下游工艺装置对原料的要求。
常减压蒸馏是炼油厂加工原油的第一个工序,即原油的一次加工,在炼油厂加工总流程中有重要作用,常被称之为‘龙头”装置。
一般来说,原油经常减压装置加工后,可得到直馏汽油、航空煤油、灯用煤油、轻、重柴油和燃料油等产品,某些富含胶质和沥青质的原油,经减压深拔后还可直接生产出道路沥青。
在上述产品中,除汽油由于辛烷值较低,目前已不再宜接作为产品外,其余一般均可直接或经过适当精制后作为产品出厂。
常减压装置的另一个主要作用是为下游二次加工装置或化工装置提供质量较高的原料。
例如,重整原料、乙烯裂解原料、催化裂化、加氢裂化或润滑油加工装置的原料、焦化、氧化沥青、溶剂脱沥青或减粘裂化装置的原料等。
图3—1为典型的燃料一润滑油型炼厂总流程承意图。
近年来,随着重油催化裂化技术的发展,某些原油(例如大庆原油)的常压塔底重油也可直接作为催化裂化装置的原料。
图3—l 燃料一润滑油型炼厂总流程示意图因此,常减压蒸馏装置的操作,直接影响着下游二次加工装置和全厂的生产状况。
2.根据原油的不同特点和不同的产品要求,有什么不同的加工流程?答:我国石油资源丰富,分布地域辽阔。
因此,各地所产原油其性质差异极大,即使是同一油田的不同油井所产原油,由于其生成条件不同,也存在着较大差异,如果再考虑到国外原油,那么差别就更大。
所以,根据不同的原油和不同的产品要求,应考虑不同的加工方案和工艺流程,以达到合理利用石油资源和最佳的经济效益。
目前,国内各炼油厂的常减压蒸馏装置有近百套之多,分布在全国各地。
主要加工大庆、胜利、任丘、辽河、中原、大港、南阳、玉门、新疆等原油,其加工流程根据原油性质和产品要求的不同可归纳为:l)燃料一润滑油。
aspen常减压系统流程模拟计算
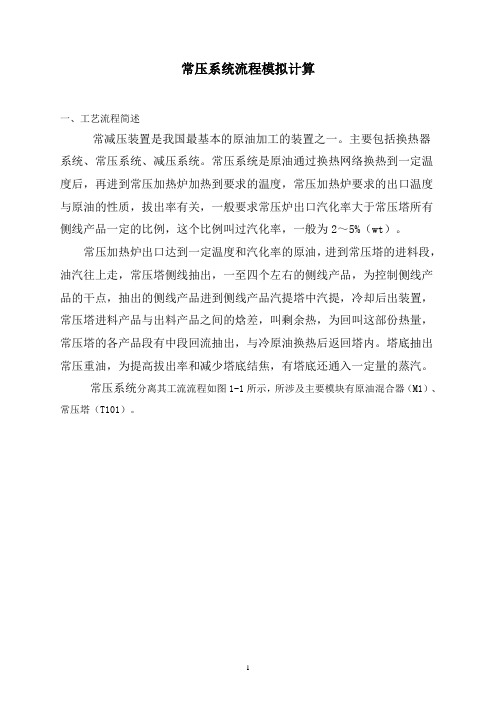
常压系统流程模拟计算一、工艺流程简述常减压装置是我国最基本的原油加工的装置之一。
主要包括换热器系统、常压系统、减压系统。
常压系统是原油通过换热网络换热到一定温度后,再进到常压加热炉加热到要求的温度,常压加热炉要求的出口温度与原油的性质,拔出率有关,一般要求常压炉出口汽化率大于常压塔所有侧线产品一定的比例,这个比例叫过汽化率,一般为2~5%(wt)。
常压加热炉出口达到一定温度和汽化率的原油,进到常压塔的进料段,油汽往上走,常压塔侧线抽出,一至四个左右的侧线产品,为控制侧线产品的干点,抽出的侧线产品进到侧线产品汽提塔中汽提,冷却后出装置,常压塔进料产品与出料产品之间的焓差,叫剩余热,为回叫这部份热量,常压塔的各产品段有中段回流抽出,与冷原油换热后返回塔内。
塔底抽出常压重油,为提高拔出率和减少塔底结焦,有塔底还通入一定量的蒸汽。
常压系统分离其工流流程如图1-1所示,所涉及主要模块有原油混合器(M1)、常压塔(T101)。
图1 常压系统模拟计算流程图CGAS原油中瓦斯,OIL原油;W塔顶切水,GAS-常顶气,GN常顶油;CP1常一线;S1常一线汽提蒸汽CP2常二线;S2常二线汽提蒸汽;CP3常三线;S3常三线汽提蒸汽;C4常四线产品;SS常底汽提蒸汽;CB常底油2二、需要输入的主要参数1、装置进料数据32、单元操作参数3、设计规定及模拟技巧3.1原油蒸馏数据的重要性3.2过汽化率3.3热平衡与产品分布的密切关系三、软件版本ASPEN PLUS软件12.1版本减压系统流程模拟计算一、工艺流程简述常减压装置是我国最基本的原油加工的装置之一,其中主要包括原油换热系统、常压系统、减压系统。
常压塔底出来的常压渣油,进到减压加热炉达到一定温度和汽化率的原油,进到减压塔的进料段,油汽往上走,减压塔侧线抽出,一至三个左右的侧线产品,有的还抽出过汽化油,抽出的侧线产品与原油换热后,冷却后出装置,减压塔进料产品与出料产品之间的焓差,叫剩余热,为回收这部份热量,减压塔的各产品段有中段回流抽出,与冷原油换热后返回塔内,为减少结焦,还有一部份不经过换热的循环冲洗油。
- 1、下载文档前请自行甄别文档内容的完整性,平台不提供额外的编辑、内容补充、找答案等附加服务。
- 2、"仅部分预览"的文档,不可在线预览部分如存在完整性等问题,可反馈申请退款(可完整预览的文档不适用该条件!)。
- 3、如文档侵犯您的权益,请联系客服反馈,我们会尽快为您处理(人工客服工作时间:9:00-18:30)。
常减压装置工艺流程简述
一、概述
常减压装置是一种用于石油化工生产中的重要设备,主要用于对原油、天然气等物质进行分离和提纯。
其工艺流程包括以下几个步骤:加热、蒸发、分馏、冷凝等。
二、加热
在常减压装置中,首先需要将原料进行加热,以使其达到蒸发的温度。
加热的方式有多种,包括外部加热和内部加热。
外部加热通常采用蒸
汽或电加热器等方式,而内部加热则是通过在设备内设置换热器来实现。
三、蒸发
当原料达到一定温度后,开始进入蒸发阶段。
在这个过程中,原料会
逐渐转化为气态,并且随着温度的升高而不断增多。
同时,在设备内
设置的分离板也会起到重要作用,帮助将不同成分的气体进行分离。
四、分馏
经过蒸发后,原料已经被分解成了多种组分。
在分馏阶段,需要根据
这些组分的物理性质进行进一步处理,并将它们分离出来。
这个过程中,常减压装置内设置的分馏塔会起到关键作用。
在分馏塔内,不同
组分的气体会根据其密度和沸点等特性进行分离,最终得到纯净的产品。
五、冷凝
在分馏结束后,需要将气态产物重新转化为液态。
这个过程称为冷凝。
常减压装置中通常采用水冷或空气冷却等方式进行冷凝。
通过这个过程,可以将产物从气态转化为液态,并且去除其中的杂质和不纯物质。
六、总结
以上就是常减压装置的工艺流程简述。
需要注意的是,在实际生产中,还需要考虑多种因素,如温度、压力、流量等参数的控制和调整。
只
有合理地控制这些因素,并根据实际情况进行灵活调整,才能获得高效、可靠的生产效果。