常减压流程
常减压流程图2

压缩机
减压回流过滤器 开工柴油 减二中过滤器 减二中/闪底 减顶污水泵
减顶油泵
减顶轻污油并管 减顶酸性水 并常二线热出料
减二、二中泵 至液位仪表 蒸汽发生器 E115A/D 减三中/闪底 开工柴油
减三中过滤器 减二/原油 减二/电脱盐注水
封油罐 封油罐
蜡油冷却器
至蜡油罐区
至加氢裂化装置 去重污油总管 减三/原油 减三/电脱 减三油产品泵 盐注水 C201 减压塔 减三、三中泵 进料自减压炉 过汽化油泵 至蜡油灌
脱丁烷塔顶后冷器 冷却水
脱丁烷塔进料-塔底 换热器
注缓蚀剂泵 缓蚀剂罐
石脑油分离塔底脱丁烷塔进料换热器 石脑油分离塔底 产品水冷器 冷却水
酸性水至酸性水汽提装置 脱丁烷塔重沸炉
信号加和器
正常无量 信号加和器
石脑油分离塔底 产品后冷器
冷却水
脱丁烷塔顶泵
脱丁烷塔重沸炉泵
脱丁烷塔顶回流泵
燃料 至尾气冷却器 自气封的加氢石脑油罐 连续重整装置来的 来的重石脑油 (脱戊烷工况) 馏分 蜡油加氢裂化装置 分馏塔顶液 石脑油加氢装置 冷高压分离罐底液 连续重整装置 控制信号 重石脑油至气封的加氢 石脑油罐 重石脑油至气封的加氢 石脑油罐 重石脑油至 连续重整装置 至液化气脱硫塔
冷却水 脱乙烷塔底冷却器
正常无量
连续重整装置稳定塔顶液 脱乙烷操作时
至液化气固定床脱硫罐
自胺分液罐来
8
液化气脱硫吸收部分流程图
混合器
液化气碱洗罐
液化气脱硫塔
液化气砂滤塔
胺液分离罐
废碱回收罐 去火炬 水缓冲罐
胺液分离罐底水循环泵
开/停
废碱泵
注碱泵 正常无量 液化气脱硫塔贫胺液泵
常减压蒸馏工艺流程
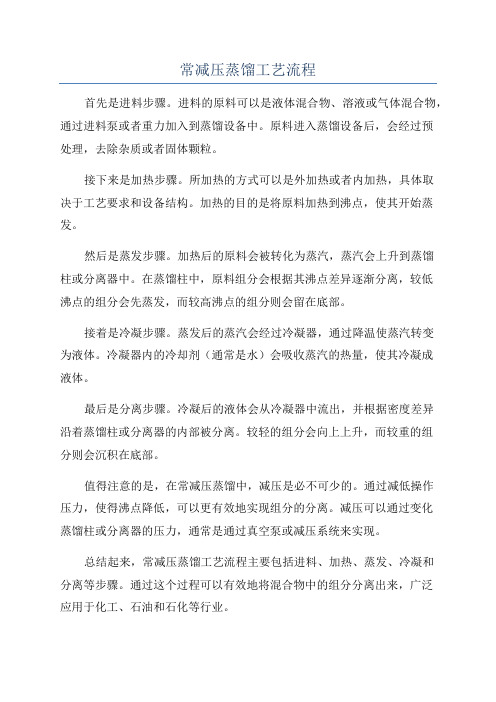
常减压蒸馏工艺流程
首先是进料步骤。
进料的原料可以是液体混合物、溶液或气体混合物,通过进料泵或者重力加入到蒸馏设备中。
原料进入蒸馏设备后,会经过预
处理,去除杂质或者固体颗粒。
接下来是加热步骤。
所加热的方式可以是外加热或者内加热,具体取
决于工艺要求和设备结构。
加热的目的是将原料加热到沸点,使其开始蒸发。
然后是蒸发步骤。
加热后的原料会被转化为蒸汽,蒸汽会上升到蒸馏
柱或分离器中。
在蒸馏柱中,原料组分会根据其沸点差异逐渐分离,较低
沸点的组分会先蒸发,而较高沸点的组分则会留在底部。
接着是冷凝步骤。
蒸发后的蒸汽会经过冷凝器,通过降温使蒸汽转变
为液体。
冷凝器内的冷却剂(通常是水)会吸收蒸汽的热量,使其冷凝成
液体。
最后是分离步骤。
冷凝后的液体会从冷凝器中流出,并根据密度差异
沿着蒸馏柱或分离器的内部被分离。
较轻的组分会向上上升,而较重的组
分则会沉积在底部。
值得注意的是,在常减压蒸馏中,减压是必不可少的。
通过减低操作
压力,使得沸点降低,可以更有效地实现组分的分离。
减压可以通过变化
蒸馏柱或分离器的压力,通常是通过真空泵或减压系统来实现。
总结起来,常减压蒸馏工艺流程主要包括进料、加热、蒸发、冷凝和
分离等步骤。
通过这个过程可以有效地将混合物中的组分分离出来,广泛
应用于化工、石油和石化等行业。
常减压操作步骤

1、设备和管线的水冲洗、单机试运、水联运1.1 水冲洗的目的(1)将施工中遗留在设备、管线内的铁锈、焊渣等杂物冲洗干净,防止在运转时卡坏阀门、法兰、孔板,堵塞管线、设备和机泵。
(2)检查在管线、设备、阀门、法兰、焊缝有无泄漏,保证管线、设备畅通。
(3)进一步考验机泵安装质量、性能及其他设备施工质量。
(4)通过对装置的水冲洗、水联运,急躁发现处理问题,同时进行技术练兵,使操作人员进一步熟悉工艺流程及仪表控制方案,为装置首次开车一次成功打下坚实基础。
1.2 水冲洗前的准备工作(1)管线做好标记,注明介质名称和走向,阀门写上介质走向和用途。
(2)机泵出口安装好合适的压力表,机泵进口安装好过滤网,对机泵进行开泵前的有关检查。
(3)关所有塔壁阀门。
联系仪表对各塔的液位进行调试。
(4)加热炉管进料均加过滤网,避免杂物冲入炉管。
(5)所有系统管线控制阀均已拆下,仪表流量孔板亦要拆开加上垫片,关闭仪表引线手阀和安全阀,冲洗时先走副线,然后冲洗短管,待完全冲洗干净后照原样装上。
(6)打开常压塔、减压塔顶人孔,以备装水时应用,避免损坏设备。
(7)联系调度将新鲜水送至装之前,并协商好外管道的水冲洗方案。
1.3 水冲洗的原则和注意事项1.3.1 原则:(1)水冲洗时,要求动力车间协调配合,保证新鲜水出口压力0.5MPa以上,流量100m3/h才能冲洗管线中的泥沙、焊渣等杂质。
(2)冲洗时原则上水不进容器、换热器、塔器,确实必须进设备的要等管线冲洗干净后才能进设备。
(3)冲洗时设备开口要加保护挡板,开口法兰间隙至少要有1cm以上距离,满足冲洗要求。
(4)冲洗顺序一般要求从上往下冲洗,流量不足的可以启泵打水从下往上冲洗。
(5)机泵入口管线冲洗干净后加恢复入口过滤器后才能启运。
1.3.2 注意事项:(1)系统进行冲洗时,严禁不合格的介质进入机泵、换热器、塔、容器等设备,管道上的孔板、流量计、调节阀、测温元件等在冲洗或吹扫时应予拆除,焊接的阀门要拆掉阀芯或全开。
石油炼化常用工艺流程
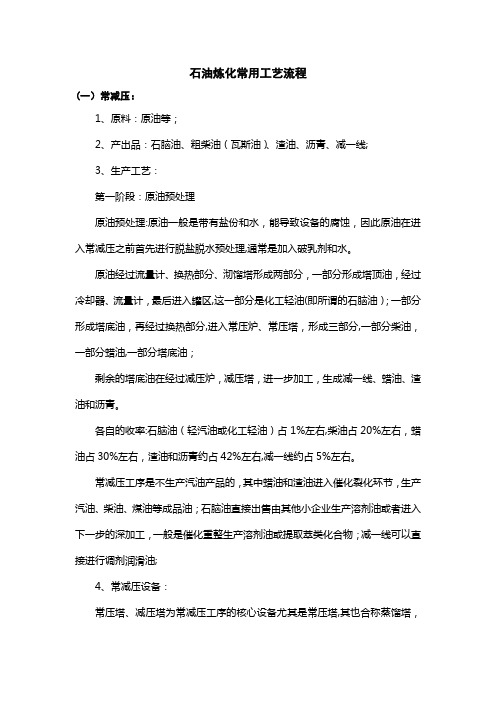
石油炼化常用工艺流程(一)常减压:1、原料:原油等;2、产出品:石脑油、粗柴油(瓦斯油)、渣油、沥青、减一线;3、生产工艺:第一阶段:原油预处理原油预处理:原油一般是带有盐份和水,能导致设备的腐蚀,因此原油在进入常减压之前首先进行脱盐脱水预处理,通常是加入破乳剂和水。
原油经过流量计、换热部分、沏馏塔形成两部分,一部分形成塔顶油,经过冷却器、流量计,最后进入罐区,这一部分是化工轻油(即所谓的石脑油);一部分形成塔底油,再经过换热部分,进入常压炉、常压塔,形成三部分,一部分柴油,一部分蜡油,一部分塔底油;剩余的塔底油在经过减压炉,减压塔,进一步加工,生成减一线、蜡油、渣油和沥青。
各自的收率:石脑油(轻汽油或化工轻油)占1%左右,柴油占20%左右,蜡油占30%左右,渣油和沥青约占42%左右,减一线约占5%左右。
常减压工序是不生产汽油产品的,其中蜡油和渣油进入催化裂化环节,生产汽油、柴油、煤油等成品油;石脑油直接出售由其他小企业生产溶剂油或者进入下一步的深加工,一般是催化重整生产溶剂油或提取萃类化合物;减一线可以直接进行调剂润滑油;4、常减压设备:常压塔、减压塔为常减压工序的核心设备尤其是常压塔,其也合称蒸馏塔,两塔相连而矗,高瘦者为常压塔,矮胖的为减压塔120吨万常减压设备评估价值4600万元。
(二)催化裂化:催化裂化是最常用的生产汽油、柴油生产工序,汽油柴油主要是通过该工艺生产出来.这也是一般石油炼化企业最重要的生产的环节。
1、原料:渣油和蜡油70%左右-—-——-—,催化裂化一般是以减压馏分油和焦化蜡油为原料,但是随着原油日益加重以及对轻质油越来越高的需求,大部分石炼化企业开始在原料中搀加减压渣油,甚至直接以常压渣油作为原料进行炼制。
2、产品:汽油、柴油、油浆(重质馏分油)、液体丙烯、液化气;各自占比汽油占42%,柴油占21.5%,丙烯占5.8%,液化气占8%,油浆占12%。
3、生产工艺:常渣和腊油经过原料油缓冲罐进入提升管、沉降器、再生器形成油气,进入分馏塔,一部分油气进入粗汽油塔、吸收塔、空压机进入凝缩油罐,经过再吸收塔、稳定塔、最后进行汽油精制,生产出汽油.一部分油气经过分馏塔进入柴油汽提塔,然后进行柴油精制,生产出柴油。
常减压装置工艺流程说明

常减压装置工艺流程说明一、原油换热及初馏部分原油经原油泵P1001 A-C升压进入装置后分为两路,一路与原油—初顶油气换热器E1001AB换热,然后经过原油—常顶循(II)换热器E1003、原油—减一及减一中换热器E1004、原油—常一中(II)换热器E1005AB、原油—常三线(II)换热器E1006AB,换热后温度升至134℃,与另一路换后原油合并进电脱盐罐V1001;另外一路与原油—常顶油气换热器E1002AB换热后,依次经过原油—常顶循(I)换热器E1007、原油—常一线换热器E1008、原油—常二线(II)换热器E1009、原油—减渣(V)换热器E1010A-C,温度升至138℃,与另一路合并。
合并后温度为136℃的原油至电脱盐。
脱盐后的原油分为两路,一路脱后原油分别经过E1011AB、E1012AB、E1013AB、E1014A-C、E1015AB,分别与减三线(II)、常二线(I)、常二中(II)、减渣(IV)、减二及减二中换热,温度升至240℃。
另一路脱后原油分别经过E1016、E1018、E1019AB、E1020A-C,分别与减二线、常一中(I)、减三线(I)、减三及减三中(II)换热,温度升至236℃,然后与从E1015AB来的脱后原油合为一路进入初馏塔T1001。
初馏塔顶油气经过E1001AB,与原油换热后再经初顶油气空冷器Ec1001AB、后冷器E1041AB,冷凝冷却到40℃后,进入初馏塔顶回流罐V1002进行气液分离,V1002顶不凝气进入低压瓦斯罐,然后引至加热炉F1001燃烧。
初顶油进入初顶油泵P1002AB,升压后一路作为初馏塔顶回流返回到T1001顶部,另一路作为汽油馏分送至罐区(汽油)。
初馏塔底油经初底泵P1003AB抽出升压后分为两路,一路经初底油—减渣(III)换热器E1021A-D、初底油—常三线(I)换热器E1022、初底油—减三及减三中(I)换热器E1026A-C,换热至297℃;另一路经过初底油—常二中(I)换热器E1025A-C、初底油—减渣(II)换热器E1026A-D换热后温度升至291℃,二路混合后温度为294℃,进入初底油—减渣(I)换热器,温度升至311℃进常压炉F1001,经加热炉加热至369℃后,进入常压塔T1002进行分离。
常减压装置操作规程

常减压装置操作规程常减压装置操作规程1.安全要求1.1 操作人员必须通过相关培训,并具备使用常减压装置的资格和证书。
1.2 操作人员必须严格遵守安全操作规程,并牢记“安全第一”的原则。
1.3 操作人员必须熟悉常减压装置的结构、工作原理和操作步骤,并能够正确使用常减压装置。
1.4 操作人员必须穿戴个人防护装备,如安全帽、安全鞋、防护眼镜、防护手套等。
1.5 在操作过程中,必须保持机器周围的工作环境整洁,并清除可能导致危险的杂物和障碍物。
1.6 在操作过程中,必须注意机器的状态,及时发现并处理设备故障和异常情况。
2.操作流程2.1 准备工作2.1.1 在操作之前,必须检查常减压装置是否处于正常工作状态,包括检查是否有损坏或松动的零件,以及油液是否充足。
2.1.2 在操作之前,必须清理常减压装置及其周围的脏污和杂物,确保机器表面干净。
2.1.3 在操作之前,必须检查紧固部件是否牢固,并清理工作区域,避免杂物和障碍物。
2.2 操作步骤2.2.1 打开常减压装置的电源,确保电源连接正常。
2.2.2 根据需要调节常减压装置的工作压力和流量,确保输出压力和流量符合要求。
2.2.3 在操作之前,必须确认周围人员已远离常减压装置的工作区域,确保操作安全。
2.2.4 打开常减压装置的气源开关,使气体进入装置,同时打开输出阀门。
2.2.5 观察常减压装置的工作状态,确保其正常运行,如有异常情况必须立即停止操作并排除故障。
2.2.6 在操作过程中,必须保持专注,严禁随意触动机器的运动部件和控制部件,以免发生意外。
2.2.7 操作结束后,必须关闭常减压装置的气源开关,并关闭输出阀门。
2.3 维护保养2.3.1 在操作结束后,必须对常减压装置进行日常维护,包括清洁机器表面,清除灰尘和杂物。
2.3.2 定期检查常减压装置的工作状态,包括检查零部件的磨损程度,润滑系统的运行情况等。
2.3.3 如发现设备故障和异常情况,必须及时排除故障,并进行相应的维修和保养。
常减压装置工艺流程说明

常减压装置工艺流程说明一、原油换热及初馏部分原油经原油泵P1001 A-C升压进入装置后分为两路,一路与原油—初顶油气换热器E1001AB换热,然后经过原油—常顶循(II)换热器E1003、原油—减一及减一中换热器E1004、原油—常一中(II)换热器E1005AB、原油—常三线(II)换热器E1006AB,换热后温度升至134℃,与另一路换后原油合并进电脱盐罐V1001;另外一路与原油—常顶油气换热器E1002AB换热后,依次经过原油—常顶循(I)换热器E1007、原油—常一线换热器E1008、原油—常二线(II)换热器E1009、原油—减渣(V)换热器E1010A-C,温度升至138℃,与另一路合并。
合并后温度为136℃的原油至电脱盐。
脱盐后的原油分为两路,一路脱后原油分别经过E1011AB、E1012AB、E1013AB、E1014A-C、E1015AB,分别与减三线(II)、常二线(I)、常二中(II)、减渣(IV)、减二及减二中换热,温度升至240℃。
另一路脱后原油分别经过E1016、E1018、E1019AB、E1020A-C,分别与减二线、常一中(I)、减三线(I)、减三及减三中(II)换热,温度升至236℃,然后与从E1015AB来的脱后原油合为一路进入初馏塔T1001。
初馏塔顶油气经过E1001AB,与原油换热后再经初顶油气空冷器Ec1001AB、后冷器E1041AB,冷凝冷却到40℃后,进入初馏塔顶回流罐V1002进行气液分离,V1002顶不凝气进入低压瓦斯罐,然后引至加热炉F1001燃烧。
初顶油进入初顶油泵P1002AB,升压后一路作为初馏塔顶回流返回到T1001顶部,另一路作为汽油馏分送至罐区(汽油)。
初馏塔底油经初底泵P1003AB抽出升压后分为两路,一路经初底油—减渣(III)换热器E1021A-D、初底油—常三线(I)换热器E1022、初底油—减三及减三中(I)换热器E1026A-C,换热至297℃;另一路经过初底油—常二中(I)换热器E1025A-C、初底油—减渣(II)换热器E1026A-D换热后温度升至291℃,二路混合后温度为294℃,进入初底油—减渣(I)换热器,温度升至311℃进常压炉F1001,经加热炉加热至369℃后,进入常压塔T1002进行分离。
常减压操作规程

常减压装置概述装置概况1.1本装置由换热初馏、常压蒸馏、减压蒸馏、加热炉、电脱盐、三注、电精制部分组成。
原料油以新疆库西外输混合原油为主,主产品主要有:100#、140#、180#道路沥青(减压渣油),副产品为:(汽油)、溶剂油、轻柴油、重柴油、减压蜡油等。
1.2装置布置在厂区的中央地带,西邻辅助区,东靠储油区,南北各预留一装置,全装置占地面积3652㎡。
本装置采用以微计算机技术为基础的具有高灵活性和高可靠性的集散型控制系统(DCS)。
1.2.1该装置采用二级交直流电脱盐、脱水技术,采取在各级电脱盐罐前注破乳剂和注水等技术措施,以满足装置原料含盐、含水的要求,其主要特点有:1.2.1.1电脱盐罐前设混合调节阀,以提高操作的灵活性并达到混合均匀的目的1.2.1.2采用交流全阻抗防爆电脱盐专用变压器,以保证电脱盐设备的安全平稳操作1.2.1.3不停工冲洗,可定期排污1.2.1.4采用组合式电极板1.2.1.5设低液位开关,以保证装置操作安全。
1.2.2装置设置初馏塔,以减少进常压炉的轻组分,从而降低了加热炉负荷,并使原油含水在初馏塔汽化,避免对常压塔操作负荷的冲击。
初馏塔设侧线抽出溶剂油产品,并采用专利技术将常压塔顶油引入初馏塔,增加初顶冷回流量,提高了溶剂油产品的质量和产量。
1.2.3在初馏塔、常压塔、减压塔顶采用注水,注氨气、注缓蚀剂等防腐措施。
1.2.4加热炉设空气预热器和氧含量检测控制仪表,不凝气引入加热炉燃烧以节约能源并减少污染。
1.2.5减压系统采用低速转油线,转油线热膨胀由炉管吸收,降低了转油线压降、温降,以提高拔出率。
1.2.6为了有效利用热能,采用窄点分析技术对换热流程进行了优化设计,以提高换后温度,降低能耗,部分换热器采用了折流杆、螺纹管和内插物等强化传热措施,提高传热强度,减少设备台位,降低设备投资。
1.2.7采用全填料干式减压蒸馏工艺,减压塔采用槽盘式分布器,辐射式进料汽液分布器,规整填料等多项新技术。
- 1、下载文档前请自行甄别文档内容的完整性,平台不提供额外的编辑、内容补充、找答案等附加服务。
- 2、"仅部分预览"的文档,不可在线预览部分如存在完整性等问题,可反馈申请退款(可完整预览的文档不适用该条件!)。
- 3、如文档侵犯您的权益,请联系客服反馈,我们会尽快为您处理(人工客服工作时间:9:00-18:30)。
常减压工艺流程简述
一、加工方案
根据原油性质和产品要求,常减压装置可以分为三种类型:
1.燃料型
除生产重整原料、汽油组分、煤油、柴油和燃料油外,减压馏分油和减压渣油进行二次加工,如通过催化裂化或加氢裂化转化为各种轻质燃料,在此方案中,减压塔是燃料型的,不生产润滑油组分原料。
2.燃料-润滑油型(我厂三套常减压全为此类型)
除生产重整原料、汽油组分、煤油、柴油和燃料油外,部分或大部分减压馏分油和减压渣油还被用于生产各种润滑油产品。
其中减压塔是润滑油型减压塔。
3.燃料-化工型
除生产重整原料、汽油组分、煤油、柴油和燃料油外,还生产化工原料和化工产品。
塔顶石脑油作为重整原料制取芳烃,轻质油一部分作燃料,一部分裂解制烯烃,重馏分油作为催化裂化原料生产制取轻质燃料。
在此方案中,减压塔也是燃料型的。
二、常减压工艺流程
在原油蒸馏过程中,精馏塔是最重要的设备,除此之外,还有电脱盐罐、加热炉、冷换热设备以及机泵、管线自控仪表等。
40℃左右的原油由罐区进入装置,经换热器热至130℃左右,进入电脱盐罐,在电场和破乳剂的作用下进行脱盐、脱水,要求脱后含盐小于3mg/L,含水小于0.5%;脱后原油再经过换热器换热至
200-240℃进入初馏塔,从初馏塔顶馏出汽油组分或重整原料,初馏塔底油由泵抽出经换热后送至常压炉加热到360℃左右进入常压塔。
原油在常压塔中进行分馏,塔顶生产汽油组分或重整原料,侧线生产煤油、喷气燃料、轻重柴油等。
常压塔一般设置2个中段回流。
常压塔底油是高于350℃的组分,称为常压重油。
常压重油用泵送至减压炉加热至380-400℃进入减压塔。
通过真空系统,使之在减压条件下进行蒸馏。
塔顶一般馏出的是裂解气、蒸汽和少量的油气。
减压蜡油由侧线抽出,可作为催化裂化、加氢裂化的原料,也可作为润滑油原料。
减压渣油一般作为燃料油、焦化原料、催化裂化原料。
三、工艺过程
1.一脱三注
包括原油电脱盐、分馏塔顶注氨、注水、注缓蚀剂(我厂常减压蒸馏在塔顶只注水和缓蚀剂),目的是为了脱除原油中的盐和减轻塔顶腐蚀。
2.常减压蒸馏
常减压装置的目的是将原油分割成各种不同沸点范围的组分,以适应产品和下游装置对原料的要求。
其典型流程可分为常减压蒸馏和常压蒸馏。
常减压蒸馏一般包括初馏塔、常压塔和减压塔,为三塔流程,炼厂多采用此方案。
常压蒸馏不设减压塔,为两塔流程,常压重油直接作为催化裂化原料,或进行加氢处理。
3.加热炉
加热炉是常减压蒸馏装置的重要设备,原油分离过程需要大量的
能量,主要通过加热炉提供。
根据生产需要,设置常压和减压加热炉。
常减压蒸馏装置因加热负荷通常较大,多采用立管立式炉。
一般由辐射室、对流室、余热回收系统、燃烧器及通风系统组成。
4.换热流程
常减压蒸馏装置是消耗能量较大地生产装置,其燃料消耗约为原油加工量的2%左右。
换热流程设计采用“窄点技术”进行优化,保证了最高的热回收率和最低的冷热公用工程消耗,采用高效的换热器,优化操作等手段,换热热量的回收率可达86%以上,换热终温可达300℃以上。
5.轻烃回收
原油中轻质油中含有相当数量的饱和烷烃,其中碳3、碳4等液化石油汽组分在1%左右。
采用通常的常减压蒸馏工艺会造成碳3、碳4等液化石油汽组分损失;也会造成石脑油的闪点低,不能作为合格的石脑油产品出厂。
因此,可以设置轻烃回收流程,回收这部分组分。
对于常减压蒸馏装置,最简单的回收方法是适当提高初馏塔或常压塔的操作压力,将初馏塔顶、常压塔顶气体引入催化裂化装置的气压机入口。
或将常压下的初馏塔顶、常压塔顶气体加压送至催化裂化装置。
另一种方法是在蒸馏装置设置轻烃回收系统,现在国内较多采用的是有压缩机和无压缩机回收工艺。
有压缩机回收工艺即将初馏塔顶、常压塔顶的气体经压缩机加压后,与常压塔顶石脑油一起送至轻烃回收部分。
无压缩机回收工艺是通过初馏塔适当提压适当提压操作,使碳-碳4组分几乎全部溶解于初馏塔顶油中没,以液态的形态
通过机泵送至轻烃回收系统。