液压支架强度可靠性优化设计方法研究论文
支架液压系统的优化设计

支架液压系统的优化设计支架液压系统的优化设计摘要:液压支架是我国目前煤矿开采过程中经常会使用到的一项设备。
但是,在实际应用的过程中,还是或多或少的存在着一定的问题,对我们工作实际效果产生了一定的影响。
在本文中,将就支架液压系统的优化设计进行一定的分析与探讨。
关键词:支架液压系统;优化设计引言液压支架是我国煤矿开采过程中经常会使用到的一项设备。
目前,我国对于液压支架主要以手动操作为主,且液压支架中的元件也常常具有着稳定性差、可靠性低、元件寿命低等问题,对于支架的良好应用产生了较为负面的影响。
对此,就需要我们能够通过对原有液压支架系统进行优化的方式来获得更好的应用效果。
1.支架液压系统的优化设计1.1 首先,我们可以通过集成式的方式对支架液压系统进行设计,并尽可能的多使用叠加式以及板式的方式进行设计,以此使管路中所具有的接头数量能够得到减少。
通过管路的减少,不但能够有效的减小管路在压力方面所存在的损失,还能够使失效的环节能够得到减少,以此使系统能够具有更高的运行效率以及更为灵敏的反响。
同时,通过这种方式所获得的管路情况也具有着更为整齐与简洁的特征。
1.2 在支架实际应用中,其所具有的速度对操作质量具有着较大的作用,尤其是对于支架所具有的移架时间来说更是如此。
而在缸径保持稳定的前提下,支架液压系统所具有的流量值就会对支架工作中所具有的运动速度产生影响。
对此,就需要我们在对支架液压系统进行设计时应当尽可能的加大系统流量。
另外,在工作面方面,我们也可以设置为双回、双供的供液系统,并将一路放置在电缆槽中,另一路放置在架间。
1.3 在实际工作中,当煤矿采高逐渐增大时,采高支架所具有的阻力也会随之增大。
同时,在我们对支架应用的过程中,如果顶板出现了来压情况,那么需要立柱能够在一时间实施泄液操作,以此保障支架能够更为平安,而要想保证该项操作能够得到良好的实现,就需要增大平安阀所具有的流量,以此帮助我们缩短泄液时间。
煤矿井下液压支架的优化与改进

煤矿井下液压支架的优化与改进煤矿井下液压支架是煤矿生产中不可或缺的设备之一,其作用是在煤矿开采过程中支撑和保护煤矿巷道的稳定。
然而,在实际运用中,液压支架也存在一些问题,例如承载能力不足、安全性能不高、操作复杂等。
为了解决这些问题,液压支架的优化与改进显得尤为重要。
本文将探讨煤矿井下液压支架的优化与改进问题,并提出一些切实可行的解决方案。
一、承载能力提升目前,煤矿井下液压支架的承载能力相对较低,无法满足大规模煤矿的高产能需求。
为了提升承载能力,可以采取以下措施:1. 优化结构设计:通过改进液压缸数量和位置、增加支撑面积等方式,优化液压支架的结构设计,提高承载能力。
2. 使用高强度材料:选择高强度、高韧性的材料来制造液压支架的关键部件,如液压缸、连杆等,增强其承载能力。
3. 引入智能控制技术:通过引入智能控制技术,实现对液压支架的自动调节,减少负荷不均匀的情况,提高承载能力。
二、安全性能提升煤矿井下液压支架的安全性能对于煤矿生产的稳定和工人的安全至关重要。
为了提升安全性能,可以采取以下措施:1. 强化质量控制:严格按照国家标准进行液压支架的制造和安装,确保其符合质量要求,减少因设备质量问题导致的事故风险。
2. 加强液压系统的监测与维护:定期进行液压系统的巡检与维护,确保液压支架的液压系统处于良好状态,减少故障发生的可能性。
3. 提高安全操作培训:加强对液压支架操作人员的培训,提高其对设备操作的熟练度和安全意识,减少人为操作引起的事故风险。
三、操作便捷性提升煤矿井下液压支架的操作复杂性是使用过程中常见的问题之一。
为了提升操作便捷性,可以采取以下措施:1. 尽量自动化:引入自动化控制技术,降低人为操作的需求,减少操作的复杂性,提高操作便捷性。
2. 优化人机界面:设计直观、易懂的人机界面,简化操作过程,减少操作人员的负担,提高操作便捷性。
3. 减轻设备重量:通过采用轻量化材料、减少不必要的结构部件等方式,减轻液压支架的整体重量,提高其搬运和操作的便捷性。
液压支架生产安全可靠性论文
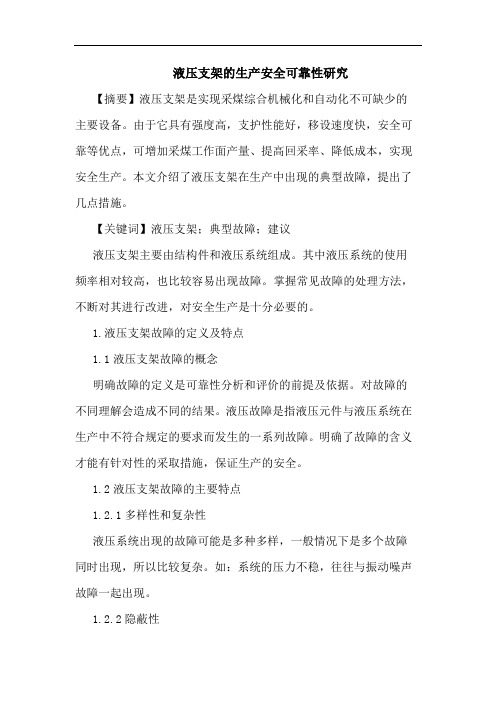
液压支架的生产安全可靠性研究【摘要】液压支架是实现采煤综合机械化和自动化不可缺少的主要设备。
由于它具有强度高,支护性能好,移设速度快,安全可靠等优点,可增加采煤工作面产量、提高回采率、降低成本,实现安全生产。
本文介绍了液压支架在生产中出现的典型故障,提出了几点措施。
【关键词】液压支架;典型故障;建议液压支架主要由结构件和液压系统组成。
其中液压系统的使用频率相对较高,也比较容易出现故障。
掌握常见故障的处理方法,不断对其进行改进,对安全生产是十分必要的。
1.液压支架故障的定义及特点1.1液压支架故障的概念明确故障的定义是可靠性分析和评价的前提及依据。
对故障的不同理解会造成不同的结果。
液压故障是指液压元件与液压系统在生产中不符合规定的要求而发生的一系列故障。
明确了故障的含义才能有针对性的采取措施,保证生产的安全。
1.2液压支架故障的主要特点1.2.1多样性和复杂性液压系统出现的故障可能是多种多样,一般情况下是多个故障同时出现,所以比较复杂。
如:系统的压力不稳,往往与振动噪声故障一起出现。
1.2.2隐蔽性液压系统是通过高压油液来传递动力,液压系统中的元件数量较多,元件和油液都处于密封的壳体和管道内,不能从外部直接观察,因故障具有隐蔽性,不易判断和检测。
2.液压支架生产中常见的故障2.1构件常见的故障底座是支架结构件中的一个关键部件。
也是结构件中出现问题较多的一个部件。
(1)底座开裂一般出现在后柱窝处内外主筋板上。
由于此处是主筋板高差过渡处。
应力集中,如果没有很好设计过渡角并采取加强措施将发生大量主筋板开裂现象。
可以采取两个主要措施:其一是打开两柱窝间的箱体结构,在断裂处加焊一定厚度的金属板;其二是加大内主筋板过渡弧角,以减小应力集中。
(2)底座扭曲此问题主要是由于在底座设计中没有加过桥板,底座在使用中左右两部分易出现错位扭曲。
2.2液压系统常见故障分析2.2.1立柱胀缸支架立柱由于出现串液而失去支撑能力这一状况不断出现在生产中。
充填综采液压支架底座强度分析及其结构优化
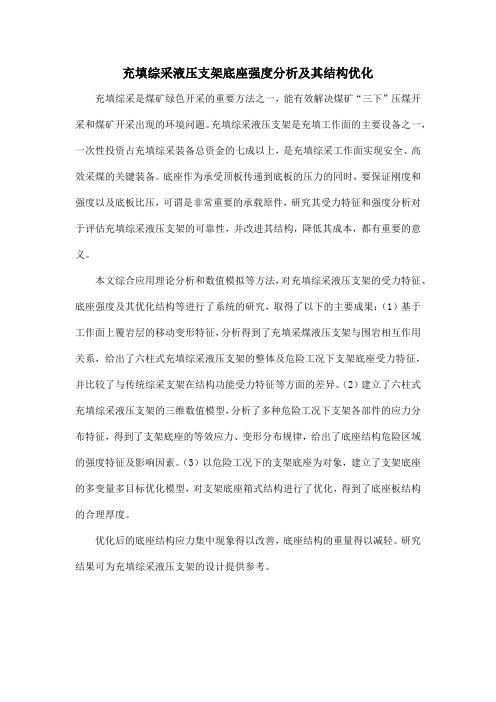
充填综采液压支架底座强度分析及其结构优化充填综采是煤矿绿色开采的重要方法之一,能有效解决煤矿“三下”压煤开采和煤矿开采出现的环境问题。
充填综采液压支架是充填工作面的主要设备之一,一次性投资占充填综采装备总资金的七成以上,是充填综采工作面实现安全、高效采煤的关键装备。
底座作为承受顶板传递到底板的压力的同时,要保证刚度和强度以及底板比压,可谓是非常重要的承载原件,研究其受力特征和强度分析对于评估充填综采液压支架的可靠性,并改进其结构,降低其成本,都有重要的意义。
本文综合应用理论分析和数值模拟等方法,对充填综采液压支架的受力特征、底座强度及其优化结构等进行了系统的研究,取得了以下的主要成果:(1)基于工作面上覆岩层的移动变形特征,分析得到了充填采煤液压支架与围岩相互作用关系,给出了六柱式充填综采液压支架的整体及危险工况下支架底座受力特征,并比较了与传统综采支架在结构功能受力特征等方面的差异。
(2)建立了六柱式充填综采液压支架的三维数值模型,分析了多种危险工况下支架各部件的应力分布特征,得到了支架底座的等效应力、变形分布规律,给出了底座结构危险区域的强度特征及影响因素。
(3)以危险工况下的支架底座为对象,建立了支架底座的多变量多目标优化模型,对支架底座箱式结构进行了优化,得到了底座板结构的合理厚度。
优化后的底座结构应力集中现象得以改善,底座结构的重量得以减轻。
研究结果可为充填综采液压支架的设计提供参考。
液压系统可靠性分析与优化研究

液压系统可靠性分析与优化研究第一章绪论液压系统作为工业领域最重要的动力传输方式之一,在机床、建筑、冶金、石油、化工等重要领域有着广泛的应用。
然而,液压系统可靠性不足是工业生产中经常遇到的一个问题。
发生的问题可能会导致生产中断、产品质量下降,甚至严重的事件可能会影响人员安全。
如何提高液压系统的可靠性是液压系统研究中的重要课题。
第二章液压系统可靠性分析液压系统是一种复杂的机电系统,在其工作过程中可能会遇到不同的故障。
针对不同的故障,可以采用不同的方法进行可靠性分析。
下面,我们简单介绍一些常用的可靠性分析方法。
1. 事故树分析事故树分析是一种利用树形结构进行系统故障分析的方法。
这种方法利用事件和门等逻辑符号进行系统可靠性分析。
将系统的起始事件作为根节点,将潜在的故障条件和组合作为故障事件进行分析。
在事故树分析中,我们可以通过改变故障条件的数量和组合方式,来确定故障发生的概率。
2. 故障模式和影响分析故障模式和影响分析是一种本质上是一种监测和预测故障的方式。
其基本原理是在实验室或野外测试中,测试员可以记录系统的每一个参数,当出现异常时,可以在记录中找到原因并分析其根源。
通过对系统的监测,我们可以及时预测可能出现的故障,采取必要的措施以降低故障的发生概率。
第三章液压系统可靠性优化研究液压系统的可靠性优化涉及到多个方面,例如设计、原材料选择、制造工艺等。
下面,我们将详细介绍一些常用的液压系统可靠性优化方法。
1. 规范化设计规范化设计是一种将制造过程中包含的设计要求和工艺规范全部提取出来并规范化的方式。
这种设计方法可以有效的降低制造成本、加速生产过程以及优化产品性能。
2. 成本效益分析成本效益分析是可靠性优化研究中常用的一种分析方法。
其主要目的是对各种可能导致成本单元的因素进行分析,从而确定解决问题的最佳路径。
例如,利用保养和维护等方式来降低成本单元的出现率,或者通过优化设计来减少成本单元的数量等。
3. 故障模式效应和危险性分析故障模式效应和危险性分析是液压系统可靠性研究中另一个重要的分析方法。
液压支架设计与应用毕业论文

液压支架毕业论文1 绪论回采面中,为了确保工作面机器和人员的安全生产,要对顶板进行支撑和管理,以防止工作面空间的顶板冒落。
液压支架是以高压液体为动力,由金属构件和若干液压元件组成。
它使顶板的支撑、切顶、移架和输送机等工序全部实现了机械化。
因而大大地改善了回采工作面的工作条件、降低了人们的劳动强度,有效地增加了劳动安全性,使工作面的产量和效率得到了很大的提高,并为工作面的自动化创造了条件。
但液压支架对煤层的地质条件要求较高。
液压支架动作原理可概括如下:液压支架在工作过程中,必须具备升、降、推、移四个基本功作,这些动作是利用泵站供给的高压乳化液通过工作性质不同的几个液压缸来完成的。
(1) 升柱当需要支架上升支护顶板时,乳化液进入立柱的活塞腔,另一回腔液,推动活塞上升,使与活塞杆相连接的顶梁紧紧接触到顶板。
(2) 降柱当需要降柱时,高压液进入立柱的活塞杆腔,另一回腔液迫使活塞杆下降,于是顶梁脱离顶板。
(3) 支架和输送机前移支架和输送机的前移,都是由底座上的推移千斤顶来完成的。
当需要支架前移时,先降柱卸载,然后高压液进入推移千斤顶的活塞杆腔,另一腔回液,以输送机为支点,缸体前移,把整个支架拉向煤壁;当需要推输送机时,支架支撑顶板后,高压液进入推移千斤顶的活塞腔,另一腔回液,以支架为支点,使活塞杆伸出,把输送机推向煤壁。
支架的支撑力与时间的曲线,称为支架的工作特性曲线,如下图所示:图1—1 支架工作特性曲线支架立柱工作时,其支撑力随时间的变化过程可分为三个阶段。
支架在升柱时,高压液进入立柱下腔,立柱升起使顶梁接触顶板,立柱下腔压力增加,当增加到泵站工作压力时,泵站自动卸载,支架的液控单向阀关闭,立柱下腔压力达到初撑力,此阶段为初撑阶段;支架初撑后,随顶板下沉,立柱下腔压力增加,直至增加到支架的安全阀调定压力,立柱下腔压力达到工作阻力。
此阶段为增阻阶段,随着顶板压力继续增加,使立柱下腔压力超过支架的安全阀压力调定值时,安全阀打开而溢流,立柱下缩,使顶梁压力减小,立柱下腔压力降低,当低于安全阀压力调整值后,安全阀停止溢流,这样在安全阀调整压力的限制下,压力曲线随时间呈波浪形变化,此阶段为恒阻阶段。
液压支架强度优化设计方法

FORUM 论坛工艺68 /矿业装备 MINING EQUIPMENT液压支架强度优化设计方法□ 牛海军 山西焦煤西山煤电东曲矿国内液压支架的发展液压支架作为综采工作面的核心设备,通常和采煤机一起配套使用,当采煤达到综合机械化的情况下,发挥安全防护、顶板支护等价值。
对于三机一架,液压支架的应用规模最大,当下市场需求已经超过200亿元。
和工程机械进行比较,液压支架的小时利用数与社会存量都是工程机械减速器的新需求。
在经济活动与市场的双重影响下,工程机械没有新增需求。
对于井下工作,液压支架具有良好的支护价值,该煤田未开采完,绝不会被应用到其他煤田,所以为了达到新增煤炭产能的目的,必须做好液压支架投资工作。
从另一个角度来看,国内煤炭机械化有着很好的发展空间,煤矿产量只要超过30万吨都能使用综采,当前国内中小煤矿机械化约55%,综采机械化有很好的发展空间。
只要综采机械化提高,液压支架的需要也会增加。
液压支架作为开采煤矿长壁的核心设备,它的技术展现了国家煤机装备水平。
当前,液压支架产品主要涉及大采高液压支架、中厚煤层、薄煤层、综采放顶、大倾斜角、端头支架与超前支护的液压支架。
我国研发的大倾角长壁综采技术在世界一直处在领先状态。
以最大应力约束为出发点的可靠性设计针对液压支架掩护梁强度设计,可以把掩护梁最大受力始终低于屈服极限水平作为约束条件,为方便分析,做好掩护梁最大应力采样工作,然后作为对比分析的条件,通过分析,不断优化改良。
增强变量设定优化液压支架掩护梁结构,主要从空间尺寸、重要参数出发进行设计,然后再作为恒定状态,所以变量设计最好选用和部件吻合的钢板厚度,在优化有限元的同时,明确初始值。
假设液压支架掩护梁的3个板厚分别是T1、T2、T3,都属于设计变量,T1是25mm,是掩护梁竖筋板厚;T2为25mm,是掩护梁的上顶板厚;T3也是25mm,是掩护梁是下腹板厚。
在这种状态之下,掩护梁的整体质量达到3345g。
液压支架的生产安全可靠性研究及应用

S HANG Huiln ・i g f 平 能 化 集 团 设 各 相 赁 分 公 司 .河 南 平 顶 山 中 47 2 ) 6 0 1
摘
要 :旨在 改善 、 强液压 支 架的生产 安全 可 靠性 , 增 营造本 质 人机 ・ 全 生产 环境 , 进 实现 综 采 面 安 促
以某 矿 己 1 — 10 O综 采 工 作 面为 例 , 面装 用 5 76 该
Z 60 Y 4 0型液压支 架 1 3架 , 续生 产 1 7 连 8个月 , 产过 生
[ = [ ]
求得 安全 系数 :
+ /3 2・ ( a 2 p2 =22 M )( ・ 66 P )
n
: :
当立 柱 内部 压力 P≥10 M a 缸 体 即将 变 形 时 , 未 3 P 、 也 能将其 击穿 。 铁谱 分析结 果表明 : 污染物污染是造成 安全 阀失效 的直接原 因 , 而安全 阀本身 的抗 污染 能力亦不容忽视 。
5 液压 系统 中的污 染物
是 4 P , 5M a 相应 拉力为 4 7k 3 N。计 算得 出平衡 连接座 产 生变形损 坏 的临 界 载荷 是 10 N, 应 的工 作 压 40k 相
式 中: —— 缸体 壁厚 , =2 8 m . 5e
P—— 立柱工作 压 力 , :3 . a P 9 8MP
就立柱 缸体胀 缸 而言 , 于 设计 和产 品 制造 质 量 对 方 面的影响 因素 , 主要验算 立柱 缸体 的壁厚 。
n
收稿 日期 :0 01-6 2 1 —2 0
≥ [] n
() 6
式 中 :r o —— 耳 座铰 接孔危 险截 面上 的拉 应力 , a MP
- 1、下载文档前请自行甄别文档内容的完整性,平台不提供额外的编辑、内容补充、找答案等附加服务。
- 2、"仅部分预览"的文档,不可在线预览部分如存在完整性等问题,可反馈申请退款(可完整预览的文档不适用该条件!)。
- 3、如文档侵犯您的权益,请联系客服反馈,我们会尽快为您处理(人工客服工作时间:9:00-18:30)。
液压支架强度可靠性优化设计方法研究论文
1基于最大应力约束的强度可靠性优化设计
1.1优化变量设定
在对液压支架掩护梁结构进行优化的阶段中,液压支架中的主要参数以及空间尺寸已
经基本完成设计,为恒定状态。
因此,设计变量可以选取支架主要部件所对应的钢板厚度,同时可在有限元优化中对其初始值进行定义。
假定对于液压支架掩护梁而言,3个板厚分
别定义为T1,T2,T3,均为设计变量,T1取值为25.0mm,为掩护梁竖筋板板厚,T2取值
为25.0mm,为掩护梁上顶板板厚,T3取值为25.0mm,为掩护梁下腹板板厚。
该状态下掩
护梁整体质量为3345.0g。
1.2有限元优化分析
在有限元分析过程当中,选择掩护梁受力条件最为恶劣的偏载工况作为加载方式。
在
此工况下,整个液压支架的实验高度取值为2400.0mm。
应力极限值在460.0MPa范围内,
因此可设定掩护梁重量最小作为强度可靠性优化设计的基本目标。
同时,遵循现行国家标准,将设计变量的增长步长设置为5.0mm。
同时,对于液压支架而言,厚度在15.0mm以下的板材较为单薄,与液压支架其他组件结构无法相互配合,因此缺乏实际意义,故而在可
靠性优化设计分析中,按照下表方式选择板厚,计算相应的组合方案。
1.3有限元优化结果分析
根据在不同组合方案下得到的数据分析来看,按照表1所取值IDE各种板厚组合方案
均能够满足液压支架掩护梁结构强度可靠性优化设计中“掩护梁最大受力不超过屈服极限
水平”的要求。
在此状态下,在液压支架重量取最小值时,板材厚度T1,T2,T3均取值
为20.0mm,与之相对应的探测点1应力水平为398.9MPa,探测点2应力水平为413.7MPa,可以满足应力标准要求,对应的液压支架掩护梁质量水平为2992.29kg。
2基于疲劳寿命约束的强度可靠性优化设计
由于在现行国家标准《煤矿用液压支架第一部分(通用技术条件)》中,已经针对液
压支架疲劳强度实验方法与结果提出了严格要求,因此在液压支架实验中仅需要满足要求
即可,无需过分追求较大的疲劳寿命水平。
从这一角度上来说,在对液压支架强度可靠性
进行优化分析的`过程中,不需要单独将液压支架疲劳寿命作为优化目标,将其满足循环
寿命作为可靠性优化中的约束条件之一。
从这一角度上来说,对于液压支架掩护梁而言,
基于疲劳寿命约束的强度可靠性优化设计可以从如下角度进行分析
2.1设定负载水平
在现行国家标准《煤矿用液压支架第一部分(通用技术条件)》中,耐久性试验规范中要求采取内加载方式进行循环加载,加载压力交替设置为1.05*额定工作压力以及
0.25*额定工作压力。
加载周期按照规范标准,设定为20000次。
2.2有限元优化分析
有限元分析过程当中,结构材料为Q460,弹性模量取值为210000.0MPa,密度标准值为7.85kg/m3,泊松比取值为0.3,结构屈服强度取值为460.0MPa。
根据结构优化分析数据表,可在满足所设定疲劳寿命(即加载周期20000次)的条件下,最优方案为板材厚度T1,T2,T3分别取值为20.0mm,20.0mm,以及25.0mm,与之相对应的探测点1寿命水平为3.2*104,探测点2寿命水平为2.6*104。
3可靠性优化设计结果分析
根据以上分析数据,在最终确定可靠性优化设计方案的过程中,可以首先考虑适当减小T1板材厚度,然后可对T2板材厚度进行调整,最后是对T3板材厚度的控制。
根据有限元分析结果,在满足液压支架掩护梁疲劳寿命以及应力水平基本要求的前提下,可先选几组性能较好的数据作为优选方案,展开进一步分析。
备选数据方案如下表所示。
4结束语
对以上各个方案的可靠性优化结果进行对比分析:其中,对于A方案而言,在该组合下,液压支架掩护梁质量减小比例最大,虽然疲劳寿命有一定程度上的下降,但仍然能够满足所设定疲劳寿命(即加载周期20000次)的基本要求,同时应力变化较小。
对于B方案以及C方案而言,虽然疲劳寿命取值有一定程度上的提高趋势,但同时应力值也对应下降,液压支架掩护梁质量减小状态不理想。
对比A方案,D方案虽然能够使液压支架掩护梁的整体重量得到控制,但液压支架掩护梁的应力水平以及疲劳寿命改善效果均不理想。
E方案虽然能够增大疲劳寿命,但也同时降低了最大应力水平,导致液压支架掩护梁质量与优化前差异不明显。
故而,最终选择A方案作为可靠性优化方案。
感谢您的阅读,祝您生活愉快。