FMEA讲义.ppt
合集下载
2024年度FMEA培训教材ppt完整版

等级并制定应对措施,可提高系统或产品的可靠性和安全性。
2024/3/23
02 03
改进策略的制定
根据FMEA分析结果,针对高风险和中风险故障模式制定改进策略,包 括设计优化、工艺改进、材料替换等,以降低故障发生的可能性和影响 程度。
改进效果的跟踪
实施改进策略后,需对改进效果进行跟踪和评估,确保改进措施的有效 性。同时,将改进经验反馈到FMEA分析中,不断完善和优化分析过程 。
掌握了FMEA实施的基本技能
通过课程中的案例分析和实践操作,学员们表示已经掌握 了FMEA实施的基本技能,能够独立完成简单的FMEA分析 工作。
增强了团队协作和沟通能力
在课程中,学员们分组进行讨论和案例分析,不仅增强了 团队协作能力,还提高了沟通能力。
34
未来发展趋势预测
2024/3/23
01 02 03
23
05 FMEA在产品设 计阶段应用实践
2024/3/23
24
产品设计阶段FMEA实施流程
流程概述
01 明确FMEA在产品设计阶段的
目标和重要性,以及实施的基 本步骤。
团队组建与培训
02 组建专业的FMEA团队,并进
行必要的培训和技能提升。
功能分析与结构分解
03 对产品的功能进行详细分析,
并进行结构分解,以明确潜在 故障模式。
12
评估方法选择及实施流程
• 方法选择:根据失效模式的性质和影响程度选择合适的评 估方法,如风险矩阵、风险指数等。
2024/3/23
13
评估方法选择及实施流程
实施流程
1. 明确评估目标和范围
2. 收集相关数据和信息
2024/3/23
14
FMEA失效模式及后果分析PPT课件
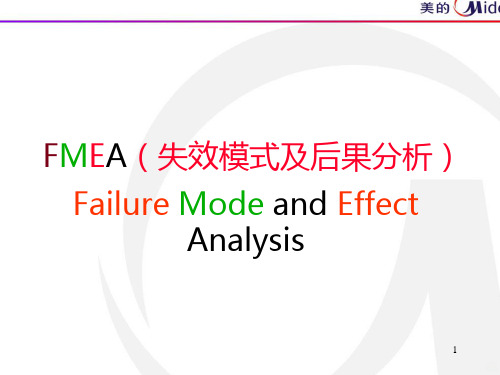
弯曲 断裂 脏污 短路 表面粗糙
毛刺 转运损坏 变形 开路 开孔太深
孔错位 漏开孔 表面太光滑
失效模式应以规范化技术术语描述, 不同于顾客察觉的现象
32
潜在失效的后果
对最终 使用者
噪音 粗糙 费力 工作不正常 异味
渗漏 不能工作 报废 外观不良
对下道 工序
无法紧固 不能配合 不能连接 无法安装 损坏设备 危害操作者
•1960’s-70’s第一次被注意和使用在工程可 靠性 •多方小组准备对产品/过程潜在失效模式和产 品性能影响的文件化体系 •评定产品或过程潜在失效模式的文件,采取 相应措施来消除或降低潜在失效的影响
7
典型的FMEAs
系统
设计
过程
部件 子系统 主系统
部件 子系统 主系统
注意:将系统的 失效模式降为最小
-后果到底有多糟? •O=Likelihood of Occurrence 频 度
-经常发生吗? •D=Likelihood of Detection 探测 度
18
RPN 流程
来自经验和数据
来自预测
DFMEA
项目/功能
潜在 失效模式
潜在 失效后果
严 重级 度别
潜在失效 的起因/机理
频 度
现行 设计控制
10
FMEA 小组
小组 • 为完成同一任务或目标的两个或更多的共同
行动的个体 集体讨论 • 发现许多可能存在和可能发生情况需要小组
的集体讨论
11
成功的FMEA 小组
•控制方向和焦点 •建立自身的统一性 •负责并使用测量方 法 •有全体的支持 •是横向多功能小组
12
FMEA 小组的守则
• 决定前召开小组会议 • 决定谁将参加 • 预先准备议题 • 主张进行会议笔记或记录 • 建立基本准则 • 遵守事先的议程 • 评价会议 • 不允许中断
FMEA精典讲义PPT课件
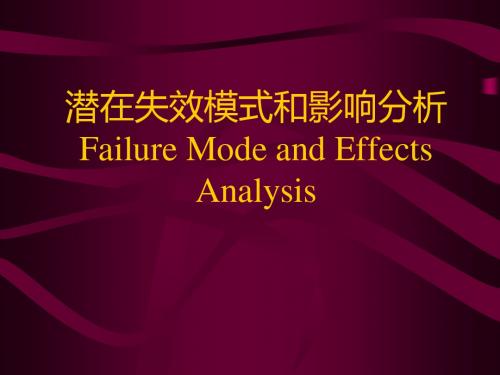
考虑,并揭示设计缺陷; 为设计试验、开发项目的策划提供更多的信息; 确定潜在失效模式、其影响,并按其对“顾客”影响分级, 分析可能的所
有原因, 确定对这些因素的控制,量化严重度、频度和不易探测度。 进行排序, 建议措施,进而建立改进设计和开发试验的优先控制系统降低
失效的风险。确定潜在的产品特殊特性。
响
因
控制
险
措施
现行 控制
原
现行
风
建议
因
控制
险
措施
现行 控制
18
建立设计FMEA
对工程师进行运用设计FMEA的培训, 理解设计控制概念。 了解对于顾客确定关键和特殊特性方法。 设计FMEA是一个创造性的工作,需要采用跨功能的小组。 应考虑包括每个零部件,审查产品的每个特性和功能。 需要调查研究和发挥创造力。
它用于军事项目合约。 • 1970年晚期,汽车工业将FMEA作为在对其零件设计和生产制造的会审项目的一部分。 • 1980年初,产品事故责任的费用突升和不断的法庭起诉事件发生,使FMEA成为降低事
故的不可或缺的重要工具。并由开始的500多家公司扩展到其供应商。 • 1993年包括美国三大汽车公司和美国质量管理协会在内的,美汽车工业行动集团组织采
确定特殊特性, 确定设计验证计划
第 II 阶段
设计验证计划 和报告
生产工艺流程图
开展过程FMEA
确定风险和可行性
把产品特性与生产过程相联系, 明确特殊特性
揭示变差来源, 最后确定特殊特性
第 II 阶段 第III 阶段 第III 阶段
9
设计FMEA
目的 • 设计的分析技术,分析和说明潜在失效模式及其原因和机理; 有助于对设计要求、设计方案进行分析评价; 有助于对制造、装配要求的初始设计确定; 确保潜在失效模式及其影响(对系统/整车运行)在设计和开发过程中得到
有原因, 确定对这些因素的控制,量化严重度、频度和不易探测度。 进行排序, 建议措施,进而建立改进设计和开发试验的优先控制系统降低
失效的风险。确定潜在的产品特殊特性。
响
因
控制
险
措施
现行 控制
原
现行
风
建议
因
控制
险
措施
现行 控制
18
建立设计FMEA
对工程师进行运用设计FMEA的培训, 理解设计控制概念。 了解对于顾客确定关键和特殊特性方法。 设计FMEA是一个创造性的工作,需要采用跨功能的小组。 应考虑包括每个零部件,审查产品的每个特性和功能。 需要调查研究和发挥创造力。
它用于军事项目合约。 • 1970年晚期,汽车工业将FMEA作为在对其零件设计和生产制造的会审项目的一部分。 • 1980年初,产品事故责任的费用突升和不断的法庭起诉事件发生,使FMEA成为降低事
故的不可或缺的重要工具。并由开始的500多家公司扩展到其供应商。 • 1993年包括美国三大汽车公司和美国质量管理协会在内的,美汽车工业行动集团组织采
确定特殊特性, 确定设计验证计划
第 II 阶段
设计验证计划 和报告
生产工艺流程图
开展过程FMEA
确定风险和可行性
把产品特性与生产过程相联系, 明确特殊特性
揭示变差来源, 最后确定特殊特性
第 II 阶段 第III 阶段 第III 阶段
9
设计FMEA
目的 • 设计的分析技术,分析和说明潜在失效模式及其原因和机理; 有助于对设计要求、设计方案进行分析评价; 有助于对制造、装配要求的初始设计确定; 确保潜在失效模式及其影响(对系统/整车运行)在设计和开发过程中得到
FMEA培训教材-PPT精选全文

客户要求 方便调整
舒适 移动顺畅
ቤተ መጻሕፍቲ ባይዱ
产品规格 调节高度 坐垫厚度 旋转角度 椅轮松紧
9
1
3
9
3
1
9
9
重要性 60% 30% 10%
分值
640
330
180
90
FMEA 得原理
客户要求 方便调整
舒适 移动顺畅
分值
产品规格 调节高度 坐垫厚度 旋转角度 椅轮松紧
9
1
3
9
3
1
9
9
640
330
180
90
参数
上升50CM
FMEA 得原理
一、FMEA基本知识
练习:
公司产品:车门 客户要求:
•方便开关 •噪音小 •安全
FMEA 得原理
FMEA 得原理
FMEA 得原理
客户质量要求 Input
客户质量目标
FMEA Output
CTQ 清单 CP 控制计划
FMEA
FMEA 得原理
Output
CTQ 清单
CTQ产出原则:
压 合 状 态
方法
特
样本Sample
殊 特 性 分
产品特 性/过程 参数规 格/公差
评价/ 测量技
术
容 量
频率
类
《
首检
MODULE 检验标
准》
5-20倍 显微镜
6P CS
:6PCS/ 抽检 : 每10PCS
抽1PCS
反应计
控制方法/ 统计技术
责任人
划
《CD-HFM0419701 LCM 镜检 不良明细
措施?
FMEA讲义课件
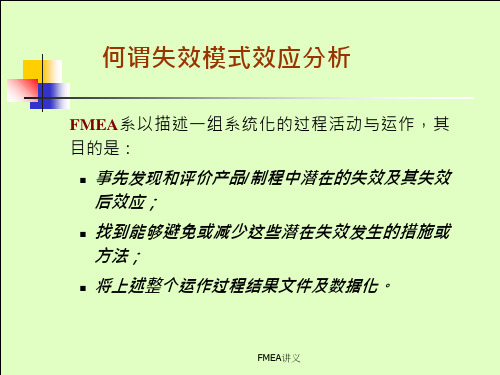
设计FMEA流程图
流 程
说 明
设计工程师应负责确认各项改正行动均经完成或均经通知负责人确实执行。
对RPN之项目应最优先采取必要措施,其目的在降低严重性、发生性及侦测性之分数。若不采有效之改正措施则制程FMEA之成效将受局限。
将风险领先指数做成柏拉图并决定建议之措施
将已采取之改正行动之内容及其完成日期填入记录,重新预估并记录改正后之严重性、发生性及侦测性之结果;计算新的RPN值。如果必要时,采取适当行动以降低RPN值。
9
很高
产品功能不能运作,丧失基本功能
8
高
产品功能能运作,但功能降低,顾客严重不满
7
中等
功能可运作,但舒适性及方便性降低,顾客使用时不满意
6
低
功能能运作,但舒适性及方便性降低,顾客使用时有些不满意
5
很低
如功能性、外观及结构等不合要求,大多数顾客注意到的了缺陷
4
微小
如功能性、外观等不合要求,一般顾客可注意到的缺陷
4
高
设计控制将会侦测出潜在原因/机制和随后的失效模式
3
非常高
设计控制有很高的机会侦测出潜在原因/机制和随后的失效模式
2
几乎肯定
设计控制几乎会侦测出潜在原因/机制和随后的失效模式
1
D-FMEA导入时机与展开
IN PUT
OUT PUT
产品主要功能
.
发生性系指预测该不良模式发生之频
度,不
良之
预防必须加以考虑
.
侦
测性系对该零件或装配件送交生产前,其可
能
存在之设计弱点是否能经设计
验证而查出之能
力
.
设计工程师应负责确认各项改正行动均经完成
FMEA培训教材(ppt)(2024)

2024/1/30
后果分析
针对每种失效模式,分析 其可能对产品功能、安全 性、可靠性等方面造成的 影响和后果。
风险评估
对每种失效模式及其后果 进行风险评估,确定其严 重度、发生度和检测度等 级。
14
评估风险等级并采取预防措施
风险等级评估
综合考虑严重度、发生度 和检测度等级,对每种失 效模式进行风险等级评估 。
2024/1/30
4
FMEA发展历程
起源
FMEA起源于20世纪40年代的军事领域,当 时主要用于评估武器系统的可靠性。
发展
随着工业技术的进步,FMEA逐渐应用于民 用领域,如汽车、航空航天、电子、医疗等 。
标准化
为了规范FMEA的实施,国际标准化组织( ISO)和美国汽车工程师学会(SAE)等制定 了相应的标准和指南。
。
2024/1/30
可靠性增长
在产品设计阶段,通过不断测试和 验证,提高产品的可靠性和稳定性 ,降低失效模式的发生概率。
持续改进
在产品设计和生产过程中,持续关 注失效模式的变化和趋势,及时采 取改进措施,确保产品质量的持续 改进和提升。
16
04
FMEA在生产过程控制中应用
2024/1/30
17
识别生产过程中潜在失效模式及后果
通过引入先进设备、优化工艺流程、提高员工技能等手段 ,提升生产过程的能力和效率,降低潜在失效模式的发生 概率。
风险管理机制完善
建立完善的风险管理机制,包括风险识别、评估、预防、 监控和应对等环节,形成闭环管理,确保生产过程风险的 有效控制和持续改进。
20
05
FMEA在设备维护保养中应用
2024/1/30
21
后果分析
针对每种失效模式,分析 其可能对产品功能、安全 性、可靠性等方面造成的 影响和后果。
风险评估
对每种失效模式及其后果 进行风险评估,确定其严 重度、发生度和检测度等 级。
14
评估风险等级并采取预防措施
风险等级评估
综合考虑严重度、发生度 和检测度等级,对每种失 效模式进行风险等级评估 。
2024/1/30
4
FMEA发展历程
起源
FMEA起源于20世纪40年代的军事领域,当 时主要用于评估武器系统的可靠性。
发展
随着工业技术的进步,FMEA逐渐应用于民 用领域,如汽车、航空航天、电子、医疗等 。
标准化
为了规范FMEA的实施,国际标准化组织( ISO)和美国汽车工程师学会(SAE)等制定 了相应的标准和指南。
。
2024/1/30
可靠性增长
在产品设计阶段,通过不断测试和 验证,提高产品的可靠性和稳定性 ,降低失效模式的发生概率。
持续改进
在产品设计和生产过程中,持续关 注失效模式的变化和趋势,及时采 取改进措施,确保产品质量的持续 改进和提升。
16
04
FMEA在生产过程控制中应用
2024/1/30
17
识别生产过程中潜在失效模式及后果
通过引入先进设备、优化工艺流程、提高员工技能等手段 ,提升生产过程的能力和效率,降低潜在失效模式的发生 概率。
风险管理机制完善
建立完善的风险管理机制,包括风险识别、评估、预防、 监控和应对等环节,形成闭环管理,确保生产过程风险的 有效控制和持续改进。
20
05
FMEA在设备维护保养中应用
2024/1/30
21
FMEA培训教材PPT完整版(2024)

22
产品设计阶段FMEA案例分析
案例一
某型号汽车发动机设计FMEA分 析。针对发动机系统可能出现的 故障模式进行分析,如气缸磨损 、活塞环断裂等,制定相应的改
进措施。
案例二
某型号手机电池设计FMEA分析 。针对电池可能出现的过热、短 路等故障模式进行分析,优化电 池结构和电路设计,提高电池安
全性。
26
过程控制阶段FMEA流程
定义过程范围和功能
01
识别潜在的故障模式
02
评估故障影响的严重度、发生
度和检测度
03
计算风险优先数(RPN)并排 序
04
制定并实施控制措施
2024/1/29
05
跟踪验证控制措施的有效性并
更新FMEA
06
27
过程控制阶段FMEA案例分析
案例一
某汽车制造厂涂装车间过程FMEA分 析
为生产过程FMEA提供支持
产品设计阶段FMEA的输出可以为生产过程 FMEA提供重要的输入和支持。
20
产品设计阶段FMEA流程
组建FMEA团队
由多部门、多学科的专业 人员组成,包括设计、制 造、质量、采购等。
2024/1/29
定义系统和子系统
明确产品的结构和功能, 划分系统和子系统。
识别故障模式
针对每个子系统或部件, 识别所有可能的故障模式 。
9
组建FMEA团队并分配任务
02
01
03
2024/1/29
组建多学科团队
包括设计、制造、质量、采购等相关领域专家。
分配角色与责任
明确团队成员的角色和责任,确保任务有效执行。
提供培训与支持
为团队成员提供FMEA培训,确保掌握相关知识和技 能。
产品设计阶段FMEA案例分析
案例一
某型号汽车发动机设计FMEA分 析。针对发动机系统可能出现的 故障模式进行分析,如气缸磨损 、活塞环断裂等,制定相应的改
进措施。
案例二
某型号手机电池设计FMEA分析 。针对电池可能出现的过热、短 路等故障模式进行分析,优化电 池结构和电路设计,提高电池安
全性。
26
过程控制阶段FMEA流程
定义过程范围和功能
01
识别潜在的故障模式
02
评估故障影响的严重度、发生
度和检测度
03
计算风险优先数(RPN)并排 序
04
制定并实施控制措施
2024/1/29
05
跟踪验证控制措施的有效性并
更新FMEA
06
27
过程控制阶段FMEA案例分析
案例一
某汽车制造厂涂装车间过程FMEA分 析
为生产过程FMEA提供支持
产品设计阶段FMEA的输出可以为生产过程 FMEA提供重要的输入和支持。
20
产品设计阶段FMEA流程
组建FMEA团队
由多部门、多学科的专业 人员组成,包括设计、制 造、质量、采购等。
2024/1/29
定义系统和子系统
明确产品的结构和功能, 划分系统和子系统。
识别故障模式
针对每个子系统或部件, 识别所有可能的故障模式 。
9
组建FMEA团队并分配任务
02
01
03
2024/1/29
组建多学科团队
包括设计、制造、质量、采购等相关领域专家。
分配角色与责任
明确团队成员的角色和责任,确保任务有效执行。
提供培训与支持
为团队成员提供FMEA培训,确保掌握相关知识和技 能。
FMEA培训讲义(PPT 103页)

适时性:在“时间之窗”关闭之
前+
小组的努力:集体的智慧
9
9
天津华诚认证中心
CAQC Certification Inc.
适时性
成功实施FMEA项目的 最重要因素之一
FMEA是预防性的 不是反应性的
应当尽量避免失效 而不是等着顾客提出申诉
10
10
天津华诚认证中心
CAQC Certification Inc.
1
天津华诚认证中心
CAQC Certification Inc.
课程内容
一、FMEA概 述
二、设计 FMEA
三、过程 FMEA
FMEA的定义、起源 FMEA的实施、跟踪 FMEA的分类
设计FMEA简介 设计FMEA的实施
过程FMEA简介 过程FMEA的实施
2
2
天津华诚认证中心
CAQC Certification Inc.
及 回
2、制造开发(1:10)
报
比
3、装配(1:1)
4、服务(1:0.5)
5、顾客抱怨,投诉后处理(1:0.05)
4
4
天津华诚认证中心
CAQC Certification Inc.
FMEA的作用
质
量
意
质量是规划出来的
识
三
质量是生产出来的
层
次
质量是检验出来的
预防作用 经验库
设计\规划部门 生产\制造部门 检验部门
不合格品、顾 客抱怨等
17
17
天津华诚认证中心
CAQC Certification Inc.
3.什么情况下 进 行 F M E A ?
新设计、新技术或新过程。 对现有设计或过程的修改。 将现有的设计或过程用于新的环境、新的场所。
- 1、下载文档前请自行甄别文档内容的完整性,平台不提供额外的编辑、内容补充、找答案等附加服务。
- 2、"仅部分预览"的文档,不可在线预览部分如存在完整性等问题,可反馈申请退款(可完整预览的文档不适用该条件!)。
- 3、如文档侵犯您的权益,请联系客服反馈,我们会尽快为您处理(人工客服工作时间:9:00-18:30)。
FMEA是一种分析方法,是对有关设计、功能和应 用变更的评审,对可能带来的风险进行讨论。
FMEA关注到产品或总成的每一个零件,尤其是关 键和安全件以及设计和制造过程。
FMEA是“事前”的行为,而不是“事后”的操作。
3
FMEA发展历史
FMEA起源于60年代美国的航天航空工业项目; 1970年汽车工业用于对零件的设计和生产制造过
情况3:在一个新的环境、地点、应用或使用形势下 (包括工作循环、法规要求等)使用现有的设计和 过程。该FMEA的范围应着重于新的环境、场所、 应用或使用形式对现有设计和过程的影响。
5
FMEA应用
范围应覆盖公司以及多个层级供应商的FMEA; 适用时,覆盖设计FMEA和过程FMEA; 使FMEA过程成为APQP过程不个缺少的部分; 是工程技术评价的一部分; 是产品和过程设计例行审定和批准的一部分。
潜在的失效模式和后果分析 FMEA
北京标智咨询有限公司 王建平
第一部分
FMEA的概述
2
什么是FMEA?
FMEA是产品设计和过程设计阶段,对构成产品的 子系统、零件及制造过程的各一个工序逐一进行分 析,找出所有潜在的失效模式,并分析其可能的后 果,从而预先采取必要的措施,以提高产品质量和 可靠性的一种系统化的活动;
6
FMEA表格
表
所用表格应覆盖下列方面的内容:
·产品或过程的功能、要求及输出; ·当功能要求不符合时的失效模式; ·失效模式的影响和后果; ·失效模式的潜在原因; ·针对失效模式原因的控制和措施; ·防止失效模式再度发生的措施。
7
FMEA方法—成立小组
FMEA开发主题
·范围 ·职能、要求和期望 ·潜在失效模式-过程和产品可能导致失效的模式 ·失效影响和结果-对内部过程或· 对下游顾客的影响和后果 ·潜在失效的原因 ·潜在失效发生的频率 ·现行预防控制的应用 ·现行探测控制的应用 ·要求的推荐措施
控制,或增加失效条件的探测度; 编制一个潜在失效模式的分级表,为预防/
纠正措施和控制建立一套优选顺序体系; 记录制造或装配过程的结果
注:有时,高的严重度定级可以通过修改设计、使之补偿 或减轻失效的严重度结果来予以减小。例如,“瘪胎”可 以减轻突然爆胎的严重度,“安全带”可以减轻车辆碰撞 的严重程度。
19
设计FMEA—发生度
表
发生频度是指一个特定原因/机制的发生可 能性
发生可能性的评估是相对的,而不是绝对 的,并不绝对反映实际发生的可能性。
16
设计FMEA—步骤和完成时间
在生产设计发布之前,完成DFMEA。
——定义顾客 ——成立小组 ——可制造性、可装配性和可服务性的考虑
表
17
设计FMEA—功能要求
表
用尽可能简明的文字来说明被分析项目满足设计 意图的功能。
——产品的目的和产品整体的设计目标
——安全性
Hale Waihona Puke ——政府法规——可靠性(功能寿命)
15
设计FMEA——简介
表
• 为完整和有效的设计、开发和验证项目的策划提供 信息;
• 根据对“顾客”的影响,建立潜在失效模式等级的 排
序清单,为设计改进、开发和确认试验/分析建立一 个优先系统; • 为推荐和跟踪降低风险的措施提供一个公开的讨论 形式; • 为将来分析研究现场情况,评价设计的更改及开发 更先进的设计提供参考(如获得的教训)。
——外观 ——可装配性设计和制造性设计等
设计严重度.doc表1
18
设计FMEA—严重度
表
严重度是指对一个特定失效模式最严重的影响后果的评价 等级
严重度数值的降低只有通过改变设计才能够实现。
推荐评价准则
小组应对评定准则和分级规则达成一致意见,尽管个别产 品分析可做修改。
注:不推荐修改确定为9和10的严重度数值。严重度数值 定级为1的失效模式不应进行进一步的分析。
注:范围不同,小组的成员也不同。
12
定义顾客
最终用户 OEM组装和制造工厂(汽车制造厂) 供应链制造(供应商和后续制造) 政府法规机构
13
第二部分
设计失效模式和影响分析 DFMEA
14
设计FMEA——简介
表
设计FMEA为设计过程提供支持,能够通过以下方 式降低失效的风险: • 客观地评价设计,包括功能要求和设计选项; • 评价设计是否满足了生产、装配、服务和回收要求 • 提高潜在失效模式及其对系统和车辆运行影响已在 设计和发过程中得到考虑的可能性;
8
FMEA方法—定义范围
建立起FMEA分析的边界,它根据FMEA的类型 (即系统、子系统和零部件)来界定。
·功能模式 · 框(边界)图 · 参数(P)图 · 接口图 · 过程流程图 · 关联矩阵 · 示意图 · 材料清单(BOM)
9
——系统FMEA
一个系统FMEA由多个子系统组成。系统示例包 括:底盘系统、动力系统、内饰系统等等。系统 FMEA主要处理系统、子系统、环境与顾客之间 的所有接口与相互作用。
20
第三部分
制造过程失效模式和影响分析 PFMEA
21
简介
过程FMEA是由负责制造/装配的工程师/小 组主要采用的一种分析技术。
用以最大限度地保证各种潜在的失效模式 及其相关的起因/机理已得到充分的考虑和 论述。
22
过程FMEA
确定过程功能和要求; 确定与产品和过程潜在的失效模式; 评价潜在失效对顾客产生的后果; 确定潜在制造或装配过程起因 确定过程变量,注重降低发生频度的过程
10
——子系统FMEA
子系统FMEA是系统FMEA的子集,示例包括: 前悬挂是底盘系统的子集。子系统FMEA主要处 理子系统内零部件之间所有接口与相互作用。
11
——零部件FMEA
子系统FMEA是子系统FMEA的子集。示例 包括:刹车片是刹车总成的零部件之一, 刹车总成又是底盘系统的一个子系统。
程评审内容的一部分; 1974年美国海军首先将它用于军事项目; 1993年美国汽车行动组织采用、编制FMEA手册。
4
FMEA范围
开展FMEA的三种基本情况:
情况1:新设计、新技术或过程。FMEA的范围是完 整的设计、技术和过程。
情况2:对现有设计和工程的更改。FMEA的范围应 着重于设计和过程的更改,由更改可能引起的相互 作用以及从市场上获得的历史信息,包括法规要求 的变更。
FMEA关注到产品或总成的每一个零件,尤其是关 键和安全件以及设计和制造过程。
FMEA是“事前”的行为,而不是“事后”的操作。
3
FMEA发展历史
FMEA起源于60年代美国的航天航空工业项目; 1970年汽车工业用于对零件的设计和生产制造过
情况3:在一个新的环境、地点、应用或使用形势下 (包括工作循环、法规要求等)使用现有的设计和 过程。该FMEA的范围应着重于新的环境、场所、 应用或使用形式对现有设计和过程的影响。
5
FMEA应用
范围应覆盖公司以及多个层级供应商的FMEA; 适用时,覆盖设计FMEA和过程FMEA; 使FMEA过程成为APQP过程不个缺少的部分; 是工程技术评价的一部分; 是产品和过程设计例行审定和批准的一部分。
潜在的失效模式和后果分析 FMEA
北京标智咨询有限公司 王建平
第一部分
FMEA的概述
2
什么是FMEA?
FMEA是产品设计和过程设计阶段,对构成产品的 子系统、零件及制造过程的各一个工序逐一进行分 析,找出所有潜在的失效模式,并分析其可能的后 果,从而预先采取必要的措施,以提高产品质量和 可靠性的一种系统化的活动;
6
FMEA表格
表
所用表格应覆盖下列方面的内容:
·产品或过程的功能、要求及输出; ·当功能要求不符合时的失效模式; ·失效模式的影响和后果; ·失效模式的潜在原因; ·针对失效模式原因的控制和措施; ·防止失效模式再度发生的措施。
7
FMEA方法—成立小组
FMEA开发主题
·范围 ·职能、要求和期望 ·潜在失效模式-过程和产品可能导致失效的模式 ·失效影响和结果-对内部过程或· 对下游顾客的影响和后果 ·潜在失效的原因 ·潜在失效发生的频率 ·现行预防控制的应用 ·现行探测控制的应用 ·要求的推荐措施
控制,或增加失效条件的探测度; 编制一个潜在失效模式的分级表,为预防/
纠正措施和控制建立一套优选顺序体系; 记录制造或装配过程的结果
注:有时,高的严重度定级可以通过修改设计、使之补偿 或减轻失效的严重度结果来予以减小。例如,“瘪胎”可 以减轻突然爆胎的严重度,“安全带”可以减轻车辆碰撞 的严重程度。
19
设计FMEA—发生度
表
发生频度是指一个特定原因/机制的发生可 能性
发生可能性的评估是相对的,而不是绝对 的,并不绝对反映实际发生的可能性。
16
设计FMEA—步骤和完成时间
在生产设计发布之前,完成DFMEA。
——定义顾客 ——成立小组 ——可制造性、可装配性和可服务性的考虑
表
17
设计FMEA—功能要求
表
用尽可能简明的文字来说明被分析项目满足设计 意图的功能。
——产品的目的和产品整体的设计目标
——安全性
Hale Waihona Puke ——政府法规——可靠性(功能寿命)
15
设计FMEA——简介
表
• 为完整和有效的设计、开发和验证项目的策划提供 信息;
• 根据对“顾客”的影响,建立潜在失效模式等级的 排
序清单,为设计改进、开发和确认试验/分析建立一 个优先系统; • 为推荐和跟踪降低风险的措施提供一个公开的讨论 形式; • 为将来分析研究现场情况,评价设计的更改及开发 更先进的设计提供参考(如获得的教训)。
——外观 ——可装配性设计和制造性设计等
设计严重度.doc表1
18
设计FMEA—严重度
表
严重度是指对一个特定失效模式最严重的影响后果的评价 等级
严重度数值的降低只有通过改变设计才能够实现。
推荐评价准则
小组应对评定准则和分级规则达成一致意见,尽管个别产 品分析可做修改。
注:不推荐修改确定为9和10的严重度数值。严重度数值 定级为1的失效模式不应进行进一步的分析。
注:范围不同,小组的成员也不同。
12
定义顾客
最终用户 OEM组装和制造工厂(汽车制造厂) 供应链制造(供应商和后续制造) 政府法规机构
13
第二部分
设计失效模式和影响分析 DFMEA
14
设计FMEA——简介
表
设计FMEA为设计过程提供支持,能够通过以下方 式降低失效的风险: • 客观地评价设计,包括功能要求和设计选项; • 评价设计是否满足了生产、装配、服务和回收要求 • 提高潜在失效模式及其对系统和车辆运行影响已在 设计和发过程中得到考虑的可能性;
8
FMEA方法—定义范围
建立起FMEA分析的边界,它根据FMEA的类型 (即系统、子系统和零部件)来界定。
·功能模式 · 框(边界)图 · 参数(P)图 · 接口图 · 过程流程图 · 关联矩阵 · 示意图 · 材料清单(BOM)
9
——系统FMEA
一个系统FMEA由多个子系统组成。系统示例包 括:底盘系统、动力系统、内饰系统等等。系统 FMEA主要处理系统、子系统、环境与顾客之间 的所有接口与相互作用。
20
第三部分
制造过程失效模式和影响分析 PFMEA
21
简介
过程FMEA是由负责制造/装配的工程师/小 组主要采用的一种分析技术。
用以最大限度地保证各种潜在的失效模式 及其相关的起因/机理已得到充分的考虑和 论述。
22
过程FMEA
确定过程功能和要求; 确定与产品和过程潜在的失效模式; 评价潜在失效对顾客产生的后果; 确定潜在制造或装配过程起因 确定过程变量,注重降低发生频度的过程
10
——子系统FMEA
子系统FMEA是系统FMEA的子集,示例包括: 前悬挂是底盘系统的子集。子系统FMEA主要处 理子系统内零部件之间所有接口与相互作用。
11
——零部件FMEA
子系统FMEA是子系统FMEA的子集。示例 包括:刹车片是刹车总成的零部件之一, 刹车总成又是底盘系统的一个子系统。
程评审内容的一部分; 1974年美国海军首先将它用于军事项目; 1993年美国汽车行动组织采用、编制FMEA手册。
4
FMEA范围
开展FMEA的三种基本情况:
情况1:新设计、新技术或过程。FMEA的范围是完 整的设计、技术和过程。
情况2:对现有设计和工程的更改。FMEA的范围应 着重于设计和过程的更改,由更改可能引起的相互 作用以及从市场上获得的历史信息,包括法规要求 的变更。