线圈制造工艺流程及工艺要求
铁芯卷绕工艺
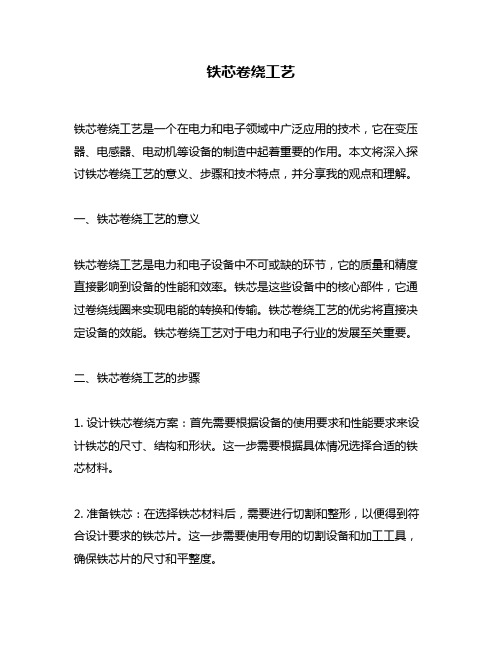
铁芯卷绕工艺铁芯卷绕工艺是一个在电力和电子领域中广泛应用的技术,它在变压器、电感器、电动机等设备的制造中起着重要的作用。
本文将深入探讨铁芯卷绕工艺的意义、步骤和技术特点,并分享我的观点和理解。
一、铁芯卷绕工艺的意义铁芯卷绕工艺是电力和电子设备中不可或缺的环节,它的质量和精度直接影响到设备的性能和效率。
铁芯是这些设备中的核心部件,它通过卷绕线圈来实现电能的转换和传输。
铁芯卷绕工艺的优劣将直接决定设备的效能。
铁芯卷绕工艺对于电力和电子行业的发展至关重要。
二、铁芯卷绕工艺的步骤1. 设计铁芯卷绕方案:首先需要根据设备的使用要求和性能要求来设计铁芯的尺寸、结构和形状。
这一步需要根据具体情况选择合适的铁芯材料。
2. 准备铁芯:在选择铁芯材料后,需要进行切割和整形,以便得到符合设计要求的铁芯片。
这一步需要使用专用的切割设备和加工工具,确保铁芯片的尺寸和平整度。
3. 将线圈绕制在铁芯上:通过将导线按照设计要求绕制在铁芯上,形成线圈。
这一步需要严格控制线圈的层数、匝数和绕制质量,以确保线圈的性能和稳定性。
4. 确保绕制质量:对于高精度设备,还需要进行绕制质量的检测和控制。
这一步需要使用相关的测试设备和检测方法,以确保绕制的线圈质量符合要求。
5. 绝缘处理:绕制完线圈后,还需要对线圈进行绝缘处理,以防止电流和电场的干扰。
这一步可以采用绝缘漆或其他绝缘材料进行处理。
6. 性能测试和调试:还需要对卷绕完成的铁芯进行性能测试和调试。
这一步主要是验证设备的工作性能和效果,确保铁芯卷绕工艺的质量和稳定性。
三、铁芯卷绕工艺的技术特点1. 深度定制:铁芯卷绕工艺需要根据具体设备的使用要求和性能要求进行定制,以满足不同设备的需求。
2. 精密加工:铁芯的加工过程需要严格的尺寸控制和表面处理,以确保铁芯的质量和精度。
3. 高效绕制:铁芯卷绕工艺需要高效地绕制线圈,以提高生产效率和降低成本。
4. 技术创新:随着科技的不断进步,铁芯卷绕工艺也在不断创新和发展,以适应新型设备和新的技术需求。
点火线圈生产工艺

点火线圈生产工艺
点火线圈是一种用于汽车点火系统的关键部件,主要用于提供高压电能以产生火花点燃汽油混合气体。
以下是点火线圈的生产工艺的一般步骤:
1. 材料准备:点火线圈的主要材料是铜线、绝缘材料和磁性材料。
首先需要准备好这些材料,根据设计要求进行切割和清洁处理。
2. 线圈绕制:将铜线按照设计要求制成线圈。
这是点火线圈生产工艺的关键步骤之一。
可以使用手工或自动化设备进行绕制,确保线圈的尺寸和导线间的间隙符合要求。
3. 绝缘处理:将绕制好的线圈进行绝缘处理,以防止电流泄漏和短路发生。
常用的绝缘材料有绝缘漆、绝缘胶和绝缘纸。
将线圈浸泡在绝缘液体中或通过喷涂的方式进行绝缘处理。
4. 组装:组装点火线圈的各个部件,包括磁铁、高压插头和线圈。
确保各个部件的正确安装和固定,同时要进行质量检测,以确保组装的点火线圈符合要求和标准。
5. 测试:将组装好的点火线圈进行测试,以确保其正常工作和性能稳定。
测试项目包括线圈的电阻、绝缘电阻和耐压等。
可以使用专业的测试设备进行测试,并根据测试结果进行调整和修复。
6. 包装和出厂:将测试合格的点火线圈进行包装,以保护其在
运输过程中不受损坏。
在包装过程中,可以附带说明书和认证文件。
最后将成品点火线圈出厂交付给客户或销售商。
点火线圈生产工艺需要严格控制每个步骤的质量和工艺参数,以确保生产出的点火线圈质量符合要求,并具备稳定可靠的性能。
包扎电机线圈绝缘的工艺流程及质量要求

包扎电机线圈绝缘的工艺流程及质量要求To begin with, I would like to introduce the process of insulation for motor coil winding and the quality requirements associated with it.Insulation is a crucial step in safeguarding the motor coil winding against electrical shorts, moisture, and mechanical damage. The insulation process involves several steps, including material selection, preparation, application, and testing.First and foremost, material selection plays a vital rolein ensuring proper insulation. There are various types of insulating materials available, such as varnish, tapes, resins, and sleeves. The choice of material depends on factors like operating temperature range, voltage level, environmental conditions, and desired electrical performance.After selecting the appropriate insulation material, the next step is preparation. This involves cleaning thesurface of the motor coil to remove dirt, oil residue or any other contaminants that might affect adhesion or insulation performance. Cleaning can be achieved using solvents or special cleaning agents specifically designed for electrical components.Once clean, the insulation material is applied to the motor coil winding. Different techniques can be used for applying insulation materials such as dipping or impregnation methods. Dipping involves immersing the coil into a bath of insulating liquid or varnish to ensure uniform coverage. Alternatively, impregnation entails injecting insulating resin into the gaps between individual turns of wire to enhance overall integrity.Finally comes the testing phase. Quality control measures are implemented to verify that proper insulation has been achieved. Various electrical tests are conducted to assess factors such as dielectric strength and resistance to thermal stress. These tests ensure that the motor winding will perform reliably under normal operating conditions.The quality requirements for motor coil winding insulation are stringent due to safety concerns and operational reliability considerations. Some essential aspects include:1. Adequate thickness: The insulation layer must have sufficient thickness to withstand voltage stresses without breakdown.2. Uniformity: Insulation should be applied evenly across all parts of the motor coil winding to prevent weak spots.3. Adhesion: The insulation material should adhere firmly to the coil surface, preventing any air gaps or delamination.4. Thermal resistance: The insulation must possess good thermal conductivity and resist the degradation caused by high temperatures generated during motor operation.5. Chemical resistance: Motor coil insulation should be resistant to various chemicals encountered in different operational environments.6. Mechanical protection: Insulation should provide mechanical protection against abrasion, vibration, and external physical damage.In conclusion, the process of insulating motor coilwindings involves careful material selection, preparation, application, and testing. Compliance with rigorous quality requirements is necessary to ensure optimal performance and safety. By adhering to these processes and standards, manufacturers can produce reliable electric motors thatmeet industry demands effectively.翻译:我想介绍包扎电机线圈绝缘的工艺流程及相关的质量要求。
电感工艺技术流程

电感工艺技术流程电感工艺技术流程是指在电感产品制造过程中,按照一定的标准和要求,通过一系列的工艺流程对原料进行加工、组装和测试等操作,最终生产出符合质量要求的电感产品。
电感工艺技术流程一般包括原料准备、线圈制作、组装和测试等环节。
首先是原料准备环节。
在电感工艺技术流程中,原料准备是非常重要的一环。
最常见的电感材料有铁芯、线圈、绝缘材料等。
在原料准备环节,要根据产品的规格和要求,准备好所需要的各种原材料,并进行材料质量的检验和测试。
接下来是线圈制作环节。
线圈是电感的重要组成部分,线圈的制作对电感的性能影响非常大。
在线圈制作环节,首先要根据产品设计要求,选择合适的线径和线圈匝数。
然后,使用相应的机械设备将线圈制作出来。
制作过程需要注意线圈的匝数和匝间的间距,以及线圈的绝缘性能。
然后是组装环节。
组装环节是将各个零部件进行装配的过程。
在组装过程中,要根据产品的结构和要求,选择合适的组装方式和工具。
将线圈、铁芯、绝缘材料等按照设计要求进行组装,同时保证组装的精度和质量。
在组装过程中,还需要进行质量检验,检查是否存在组装错误和不合格现象。
最后是测试环节。
测试环节是对电感产品的性能进行检验和测试的过程。
常见的测试项目有直流电阻、电感值、磁感应强度等。
通过测试环节,可以对产品的质量进行评估和判断。
对于不合格品要进行修改、调试或重新制作。
总之,电感工艺技术流程是电感产品制造过程中,按照一系列的工艺流程对原料进行加工、组装和测试的过程。
通过严格的流程控制和质量检验,可以生产出符合要求的电感产品。
这不仅关乎着电感产品的质量,也对电子电气设备的性能和可靠性起着重要的影响。
放电线圈生产工艺规程

放电线圈生产工艺规程一、设备及工艺装备1、真空浇注罐:真空度-0.1MPa温度110℃2、混料罐:真空度–0.1MPa温度60℃3、电动搅拌装置:转速80-120转/分4、电热鼓风干燥箱:0-300℃自动控温循环风。
5、真空泵:真空度-0.1 MPa速度40升/秒6、浇注模具(根据生产规模而定)夹件、漏斗、标件各类工具等。
7、绕线机MKRⅢ一台,手动两台,台灯两台。
8、电烙铁100W。
9、玻璃胶枪。
二、材料1、环氧树脂(E39D)2、固化剂(甲基四氢苯酐)3、增韧剂4、硅微粉5、促进剂6、色浆7、真空泵油8、酒精9、脱模剂10、聚脂薄膜11、电磁线φ0.17、φ0.71、φ1.2512、绝缘纸板δ=1、δ=0.513、铜皮δ=0.2014、腊管φ815、紫铜管φ5*116、电工无纬带17、玻璃胶18、透明胶布19、焊锡丝20、绝缘漆21、绝缘树脂黑漆22、硅钢片δ=0..3523、导热油24、半导体漆25、石膏粉26、δ=5 钢板27、δ=2.5钢板28、各种标件等三、测试检验设备1、三倍频2、模拟测试仪3、万用表两只4、耐压机5、兆欧表四、浇注工艺流程:1.新模具或停用2月以上模具,用软布擦净油污后,进烘箱280℃烘2小时,除去残存油膜后涂上脱膜剂,再进烘箱280℃恒温2小时,在高温下,第二次涂脱膜剂,再加热到150℃停止加热,随烘箱冷却待用。
2.装模:把二次绕组和辅助绕组装在模芯体上,再把一次绕组装在二次绕组外面,放在下模的体内,固定好接线柱,按图纸和绝缘尺寸要求,调整好绝缘距离,合上上模,用4根系好的电工无纬带再次调整绝缘距离,盖上底盖,锁紧螺丝待浇。
3.调整时应注意①严禁用铜铁物质敲击绕组体。
②装模时如发现金属物质或影响绝缘的物质进入模内或粘在绕组线圈上,要及时清理。
③装模使用的固定螺纹都要涂上硅油。
④合模和装盖时,要在模的分箱面涂上玻璃胶,以防漏模。
4.预装好的模具安好浇注漏斗,用自动小车送入浇注罐内,加热100 ℃持续3小时。
线圈绕制组装工艺规程

Q/XX 016-20XX代替 Q/XX 493-20XX1目的为了规范线圈绕制组装工艺符合产品设计要求特制订本企业标准。
2范围本标准规定了线圈绕制组装的材料、设备及工具、准备工作、工艺流程、检查、注意事 项。
本标准适用于我公司有线圈骨架的单段及多段电磁线圈的绕制及后续处理,线径从 Φ0. 03~ 6 2. 0 (mm)o3材料3.1 绕制用导线常用电磁线的主要性能见表lo表1常用电磁线的主要性能注:1)电磁线应提供以下五项检验报告:①耐压性能;②耐刮性能;③针孔试验;④伸长率试验; ⑤耐溶剂试验2)具体性能指标见GB/T6109. 13.2 引出导线3.2.1 2.1铜特软绞线TTJR :沪Q/JB1847-79适用于作电磁线线径小于①0. 2mm 的线圈弓I 接线。
3.2.2丁睛聚氯乙烯复合物绝缘引接线JBF : JB1138-76适用于交流500V 以下线圈的引接 线。
允许工作温度130℃。
3.2.3橡皮绝缘丁睛护套引接线JBQ :适用于交流1140V 以下电磁线圈的引接线。
允许工 作温度130℃。
3.2.4镀锡铜芯聚四氟乙烯绝缘安装线AF-200:适用于耐热要求较高的电磁线圈的引接 线。
允许工作温度200℃。
3.3 绝缘带 XXX 有限公司企业标准 线圈绕制组装工艺规程3.3.1 醇酸玻璃漆布带2432:适用于作线圈包扎。
允许工作温度130'C。
3.3.2 环氧玻璃漆布带2433:适用于包扎环氧树脂绕注的特种电气线圈。
允许工作温度130℃ o3.3.3 有机硅玻璃漆布带2450:适用于高温线圈的包扎绝缘。
允许工作温度180℃。
3.3.4 醋酸绝缘粘胶带:适用于作线圈的内缓冲层,外包扎材料和固定线圈标牌用。
3.3.5 聚脂薄膜粘带:适用于作线圈的内缓冲层,外包扎材料和固定线圈标牌用。
3.4 绝缘丝无碱玻璃纤维丝:适用于作包扎固定线圈引接线。
3.5 焊料、焊剂1 .5.1焊料3 . 5.1.1焊锡丝:工业级3. 5.1.2焊料:锡铅比为63: 37,直径为0. 8mm的管状焊锡丝。
线圈工艺流程

线圈工艺流程
线圈工艺流程:
线圈制作是电子产品制造过程中非常重要的环节之一,它用于稳定电流、产生电磁场或储存能量。
线圈工艺流程包括准备材料、绕线、固定定位、焊接和测试等环节。
首先,准备线圈所需的材料和工具。
材料包括铜线、铁芯、绝缘材料等。
工具包括绕线机、焊接设备、剪刀、胶带等。
根据设计要求选择合适的材料和工具。
接下来是绕线环节。
将铜线从线盘拉出,用绕线机将铜线绕成所需的形状和层数。
绕线时要控制绕线的速度和紧密度,以保证线圈的质量和性能。
绕线完成后,需要固定定位线圈,防止线圈松动或移位。
可以使用胶带、胶水等固定定位材料,确保线圈的稳定性。
固定定位完成后,进行焊接。
将线圈两端的铜线焊接到电子产品的相应位置,确保电流的正常传导。
焊接完成后,需要进行测试。
测试内容包括电阻测量、电感测量、短路测试等,以确保线圈的质量和性能符合设计要求。
对于不合格的线圈,需要进行后续处理或更换。
最后,对线圈进行清洁和包装。
清洁可以使用清洁剂擦拭线圈表面,去除灰尘和污渍。
包装可以使用泡沫箱、塑料袋等包装
材料,防止线圈在运输过程中受到损坏。
总结起来,线圈工艺流程包括准备材料、绕线、固定定位、焊接和测试等环节。
每个环节都非常重要,都需要保证施工过程中的质量控制。
只有通过严格的工艺流程,才能生产出符合设计要求的线圈产品。
电机线圈制造工艺流程介绍
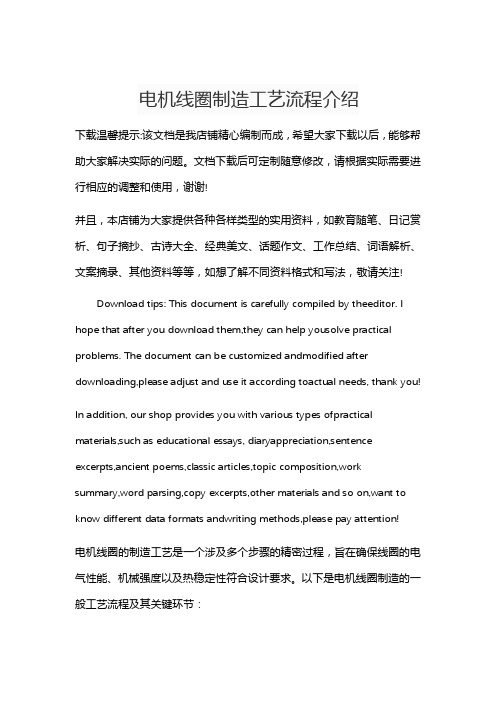
电机线圈制造工艺流程介绍下载温馨提示:该文档是我店铺精心编制而成,希望大家下载以后,能够帮助大家解决实际的问题。
文档下载后可定制随意修改,请根据实际需要进行相应的调整和使用,谢谢!并且,本店铺为大家提供各种各样类型的实用资料,如教育随笔、日记赏析、句子摘抄、古诗大全、经典美文、话题作文、工作总结、词语解析、文案摘录、其他资料等等,如想了解不同资料格式和写法,敬请关注!Download tips: This document is carefully compiled by theeditor. I hope that after you download them,they can help yousolve practical problems. The document can be customized andmodified after downloading,please adjust and use it according toactual needs, thank you! In addition, our shop provides you with various types ofpractical materials,such as educational essays, diaryappreciation,sentence excerpts,ancient poems,classic articles,topic composition,work summary,word parsing,copy excerpts,other materials and so on,want to know different data formats andwriting methods,please pay attention!电机线圈的制造工艺是一个涉及多个步骤的精密过程,旨在确保线圈的电气性能、机械强度以及热稳定性符合设计要求。
- 1、下载文档前请自行甄别文档内容的完整性,平台不提供额外的编辑、内容补充、找答案等附加服务。
- 2、"仅部分预览"的文档,不可在线预览部分如存在完整性等问题,可反馈申请退款(可完整预览的文档不适用该条件!)。
- 3、如文档侵犯您的权益,请联系客服反馈,我们会尽快为您处理(人工客服工作时间:9:00-18:30)。
线圈制造工艺流程及工艺要求
绕线——包梭型——拉型——整型——压导线——包绝缘——热压成型——外屏处理(防电晕)
1、绕线:a) 根据图纸校对绕线模尺寸、测量线规;
b) 匝数准确;
c) 松紧一致;
d) 绕线过程中出现导线外绝缘损伤要及时修复;
2、包梭型:a) 梭型包扎紧凑、平直;
b) 刮净引线头;
3、拉型:a) 根据(图纸)制作角度板,校对拉型机的角度、节距符合图
纸要求(直线部分长3-5mm,鼻高符合图纸少10-15mm);
b) 拉型过程应用力一致,尽量保证线圈的几何尺寸(直线和端
部长度、端部弧度、跨距等);
c) 弯引线,引线距离近量符合图纸;
4、整型:a) 对整型胎,直线部分短3-5mm;
b) 敲打线圈,使线圈附和整型胎,不可敲打端部和换位处;
c) 不允许打成死弯;
5、压导线:a) 利用角度板调整压型机;
b) 做鼻高标尺;
c) 按热压工艺进行(附表1);
d)扒除白布带,不允许用剪刀等利器;
e) 检查线圈外表有无损伤,如存在问题,及时反映;
6、包绝缘:a) 校直线圈引线;
b)包引线绝缘从距离鼻端25mm起始至斜边1/2处止;
c)包扎对地绝缘要求紧、均匀,压缩量控制在15-20%,注意包扎层数和绝缘厚度;
d)包端部要求紧、均匀,不能用过大的力,以防云母带被拉松;
7、热压成型:a)利用角度板调整压型机;
b) 按热压工艺进行(附表1);
c) 清除余胶及飞边;
d) 调整升高;
e) 检查线圈各尺寸,如出现异常需查清原因后方可投入批量生
产;
8、防晕处理:a)图纸有防电晕要求的,才进行此项工作;
b)防电晕漆必须搅拌均匀后方可使用;
c)防电晕漆使用时只能采用高阻压低阻;
d) 按防电晕处理工艺要求进行生产。
表1
表2:高压电机线圈匝间耐压试验规范(适用于3至13.8KV):
表3:线圈电晕试验值(厂内试验):
表4:整机定子线圈电晕试验值(厂内试验):
表5:线圈各工艺过程交流耐压试验:。