生产工艺流程图及说明
生产工艺流程图
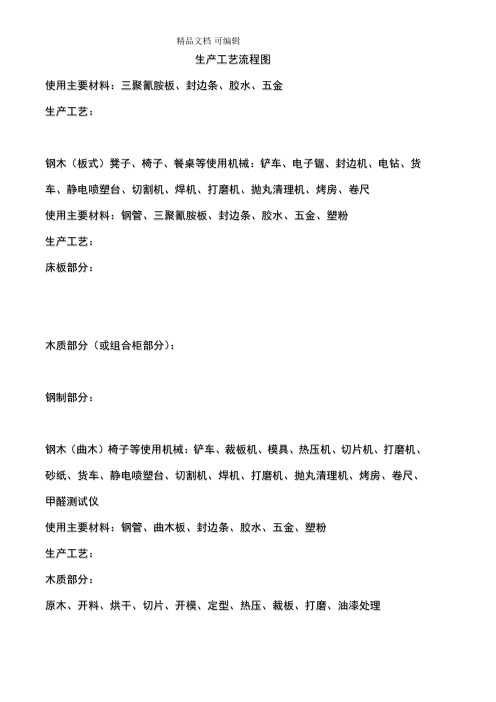
生产工艺流程图使用主要材料:三聚氰胺板、封边条、胶水、五金生产工艺:钢木(板式)凳子、椅子、餐桌等使用机械:铲车、电子锯、封边机、电钻、货车、静电喷塑台、切割机、焊机、打磨机、抛丸清理机、烤房、卷尺使用主要材料:钢管、三聚氰胺板、封边条、胶水、五金、塑粉生产工艺:床板部分:木质部分(或组合柜部分):钢制部分:钢木(曲木)椅子等使用机械:铲车、裁板机、模具、热压机、切片机、打磨机、砂纸、货车、静电喷塑台、切割机、焊机、打磨机、抛丸清理机、烤房、卷尺、甲醛测试仪使用主要材料:钢管、曲木板、封边条、胶水、五金、塑粉生产工艺:木质部分:原木、开料、烘干、切片、开模、定型、热压、裁板、打磨、油漆处理钢制部分:油漆家具(茶几、会议桌、班台、文件柜等油漆家具)使用机械:电子开料锯、裁刀、电熨斗、螺旋机、冷压机、打磨机、电钻、U V设备、码钉枪、砂光机、卷尺、空气压缩机、喷枪、甲醛测试仪使用主要材料:密度板、胶水、胡桃木皮、码钉、五金件生产工艺:油漆家具(纯实木餐桌、床)使用机械:拼板机、铣床、刨木机、电锯、电子开料锯、干燥机、螺旋机、手工刨、四面刨、冷压机、打磨机、电钻、U V设备、码钉枪、砂光机、数控圆盘锯、开榫机、雕刻机、卷尺、排钻、仿形车床、空气压缩机、喷枪、甲醛测试仪使用主要材料:原木、胶水、码钉、五金件生产工艺:油漆家具(带榫头的椅子、床、沙发类型)使用机械:拼板机、铣床、刨木机、电锯、电子开料锯、干燥机、螺旋机、手工刨、四面刨、冷压机、打磨机、电钻、U V设备、码钉枪、砂光机、数控圆盘锯、开榫机、雕刻机、卷尺、排钻、仿形车床、空气压缩机、喷枪、甲醛测试仪使用主要材料:原木、胶水、码钉、五金件生产工艺:床垫使用机械:弹簧机、衍缝机、粘胶机、缝纫机床、打包机床、绣花机使用主要材料:弹簧、椰棕、面料生产工艺:简略说明。
啤酒生产流程图及说明
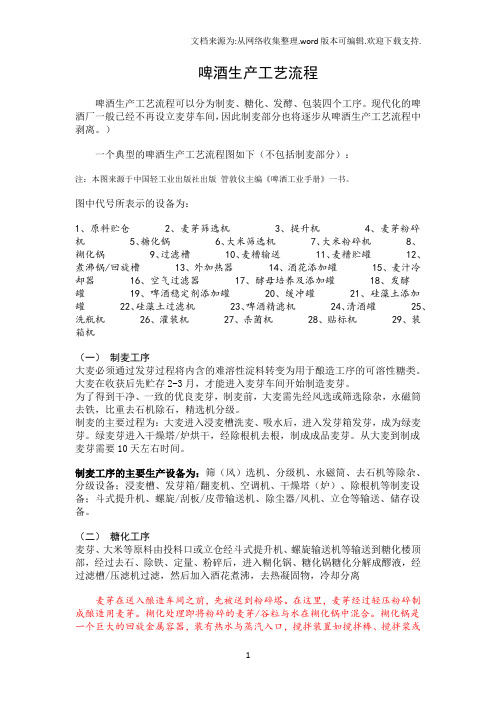
啤酒生产工艺流程啤酒生产工艺流程可以分为制麦、糖化、发酵、包装四个工序。
现代化的啤酒厂一般已经不再设立麦芽车间,因此制麦部分也将逐步从啤酒生产工艺流程中剥离。
)一个典型的啤酒生产工艺流程图如下(不包括制麦部分):注:本图来源于中国轻工业出版社出版管敦仪主编《啤酒工业手册》一书。
图中代号所表示的设备为:1、原料贮仓2、麦芽筛选机3、提升机4、麦芽粉碎机5、糖化锅6、大米筛选机7、大米粉碎机8、糊化锅9、过滤槽 10、麦糟输送 11、麦糟贮罐 12、煮沸锅/回旋槽 13、外加热器 14、酒花添加罐 15、麦汁冷却器 16、空气过滤器 17、酵母培养及添加罐 18、发酵罐 19、啤酒稳定剂添加罐 20、缓冲罐 21、硅藻土添加罐 22、硅藻土过滤机 23、啤酒精滤机 24、清酒罐 25、洗瓶机 26、灌装机 27、杀菌机 28、贴标机 29、装箱机(一)制麦工序大麦必须通过发芽过程将内含的难溶性淀料转变为用于酿造工序的可溶性糖类。
大麦在收获后先贮存2-3月,才能进入麦芽车间开始制造麦芽。
为了得到干净、一致的优良麦芽,制麦前,大麦需先经风选或筛选除杂,永磁筒去铁,比重去石机除石,精选机分级。
制麦的主要过程为:大麦进入浸麦槽洗麦、吸水后,进入发芽箱发芽,成为绿麦芽。
绿麦芽进入干燥塔/炉烘干,经除根机去根,制成成品麦芽。
从大麦到制成麦芽需要10天左右时间。
制麦工序的主要生产设备为:筛(风)选机、分级机、永磁筒、去石机等除杂、分级设备;浸麦槽、发芽箱/翻麦机、空调机、干燥塔(炉)、除根机等制麦设备;斗式提升机、螺旋/刮板/皮带输送机、除尘器/风机、立仓等输送、储存设备。
(二)糖化工序麦芽、大米等原料由投料口或立仓经斗式提升机、螺旋输送机等输送到糖化楼顶部,经过去石、除铁、定量、粉碎后,进入糊化锅、糖化锅糖化分解成醪液,经过滤槽/压滤机过滤,然后加入酒花煮沸,去热凝固物,冷却分离麦芽在送入酿造车间之前,先被送到粉碎塔。
船舶及海洋工程用钢板工艺流程图及说明

船舶及海洋工程用钢板 生产工艺流程图及工艺说明一、工艺流程图加热板坯组批、分切加热质量控制点 除鳞粗轧轧制激光测宽精轧轧制轧制质量控制点 层流冷却激光测厚矫直机矫直冷床冷却上、下表面检验剪切 成品检验、取样、理化检验修磨、复检成品质量控制点 成品标识收集入库板坯验收入库二、工艺说明工艺概述:船舶及海洋工程用连铸板坯经验收入库,根据生产需要对连铸板坯进行分切、组批。
连铸板坯入炉加热后,由辊道送至除鳞机除鳞,除鳞后进入粗轧机,完成粗轧后经激光测宽仪由辊道运送至精轧机。
精轧完成后根据工艺需要进行轧后层流冷却,经激光测厚仪由辊道运送至矫直机,矫直后由检验人员对钢板进行热检,钢板进入冷床自然冷却。
冷却的钢板经上表检验后经翻板机翻身进行下表检验和尺寸检验。
根据检验情况对钢板分断、切边、定尺剪切完成后进行成品检验、修磨、标识,最后由电磁吊收集入库。
1、加热制度1.1炉膛温度控制要求按表1执行(表1)技术参数钢级预热温度℃加热温度℃均热温度℃加热速度mm/min一般强度船体用A、B级钢板≥650 1180~1320 1180~1300 0.7~-0.9 注:使用温度监控系统进行监控,并进行记录。
2.1加热要求①加热速度根据坯料厚度确定,坯料越厚加热速度越慢。
②钢坯加热要烧匀烧透。
③控制炉膛压力处于微正压状态,防止炉头吸冷风。
④生产不正常造成停轧时,加热炉升降温度制度按表2执行。
(表2)停轧时间( h )炉温(℃)提前升温时间(min) 均热段加热段〈0.5 不变不变不变〈1 1200 1200 151-2 1100 1050 302-4 1080 1000 40>4 800 800 802、高压水粗除磷工艺要求2.1加热好的钢坯必须进行除磷,一次除磷不尽,可增加除磷道次。
2.2正常生产时,要保证各喷嘴通畅,高压水泵出口工作压力≥15Mpa。
3、四辊粗轧工艺技术操作要求3.1表面氧化铁皮必须除干净,除不干净不得轧制。
PP-R管件生产工艺流程图及简述
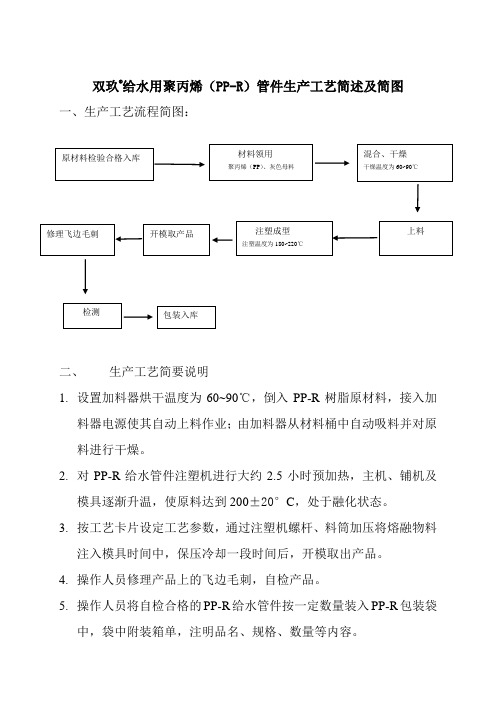
双玖®
给水用聚丙烯(PP-R )管件生产工艺简述及简图 一、生产工艺流程简图:
二、 生产工艺简要说明
1. 设置加料器烘干温度为60~90℃,倒入PP-R 树脂原材料,接入加料器电源使其自动上料作业;由加料器从材料桶中自动吸料并对原料进行干燥。
2. 对PP-R 给水管件注塑机进行大约2.5小时预加热,主机、铺机及模具逐渐升温,使原料达到200±20°C ,处于融化状态。
3. 按工艺卡片设定工艺参数,通过注塑机螺杆、料筒加压将熔融物料注入模具时间中,保压冷却一段时间后,开模取出产品。
4. 操作人员修理产品上的飞边毛刺,自检产品。
5. 操作人员将自检合格的PP-R 给水管件按一定数量装入PP-R 包装袋中,袋中附装箱单,注明品名、规格、数量等内容。
6.对成品PP-R管件进行检验,检验方法参见GB/T18742.3-2002.
7.合格的管件按不同规格装入包装箱中,附上合格证。
8.分别按不同规格的包装进行有序入库存放。
新生产工艺管理流程图及文字说明

新生产工艺管理流程图及文字说明生产工艺管理流程生产技术部接到产品开发需求后,进行产品开发策划并起草设计开发任务书,经公司领导审批后,业务部门根据产品设计开发任务书准备纸张、油墨、印版、烫金等生产材料及生产工艺设备的准备工作,材料、设备准备完成后,安排在印刷车间进行上机打样;打样过程中,由生产技术部组织业务、品质、车间等部门对打样结果进行评审,打样评审通过后,由生产技术部进行送样、签样工作(送中烟技术中心材料部),若签样不合格,需重新进行打样准备;签样完成后,生产技术部根据打样情况形成临时技术标准,品质部形成检验标准,印刷车间根据临时技术标准进生试机生产,生产产品由生产技术部送烟厂进行上机包装测试(若包装测试不通过,生产技术部需重新调整临时技术标准重新试机生产),包装测试通过后,生产技术部根据试机生产时情况形成技术标准。
当月生产需求时,生产技术部按生产组织程序进行组织生产,并同时下达技术标准,印刷车间根据生产技术标准,进行工艺首检,确认各项工艺指标正确无误,进行材料及设备的准备工作,各项工作准备完成后按技术标准要求进行工艺控制,生产技术部对整个生产运行过程进行监督,当工艺运行不符合要求时,通知生产技术部进行工艺调整。
生产结束后,进入剥盒、选盒工序,经过挑选的烟标合格的按成品入库程序进行入库,不合格的产品按不合格程序进行处理。
产品工艺管理流程图业务部生产技术部印刷车间品质部输出记录接到设计更改需求段阶}改更计设{发开吕产不通过不通过通过接到设计开发需求产品开发策划打样准备送样、签样通过不通过形成技术标准(临时)审批不通过上机打样形成检验标准设计开发项目组成立通知产品开发任务书段阶制控艺工产生送客户包装测试■试生产■形成技术标准<接到生产需求组织生产下达工艺标准工艺首检材料准备设备准备工艺监督过程质量监督工艺改进不通过运行判定成品质量监督是合格成品入库结束不合格控制程序过程检验记录工艺检查记录表,匚工艺记录表工艺运行控制剥盒、选盒烟用材料试验评价报告印刷作业指导书生产工作单换版通知单生产操作记录表工艺更改通知单成品检验记录子流程生产工艺更改流程生产技术部接到工艺更改需求时,及时到生产现场进行工艺更改打样,并作好工艺更改记录,工艺更改完成后形成新的技术标准,并以工艺更改通知单的形式通知相关生产部门,相关生产部门接到工艺更改通知后,按新的工艺标准执行生产。
生产工艺及流程图

消毒灭菌舱生产工艺及流程图
一、生产流程图
二、生产工艺说明
1、方管底座:采用8cm*4cm的方钢焊接底架,使用净化铝型版固定底价作为舱底。
2、槽铝和型铝:采用50mm的槽铝和型铝作为底座框架和立柱框架。
3、柱型材:固定四周柱型材作为立板的骨架,起到支撑固定的作用。
4、周边立板:使用外圆柱和内圆柱封边固定,作为立板四周固定槽
板。
5、搭建上框梁:周边立板完成后搭建上框梁,作为顶板的支撑主体。
6、钢质门安装:安装门体和控制开关门电机,安装红外开门感应器。
7、安装顶板:在顶板安装照明灯具和消毒灭菌机,接线,安装顶板。
8、包角铝型材:内弧包角安装,打胶封缝,去除板材包装膜。
9、设备开机测试:接通220V交流电,进行设备开机测试运行。
10、包装封箱:采用泡沫和纸箱对舱体进行封装打包。
生产工艺流程图和工艺说明
1 9 10 12
2 11
13
3 14
4 15
5 16
17
8 7 6
18
至提升机工艺流程设备编号及名称
编号名称
1 永磁筒
2 圆筒初清筛
3 电动三通
4 锤片粉碎机
5 吸尘罩
6 栅筛
7 下料斗
8 斗式提升机
9 风帽
10 组合脉冲除尘器
11 叶轮式闭风机
12 双轴桨叶混合机
13 自动闸门
14 料位器
15 手动闸门
16 螺旋喂料器
17 电子秤
18 刮板输送机
工艺流程图
19 23
20 24
21 25
22 26 工艺流程设备编号及名称编号名称
19 环模制粒机
20 空压机
21 双层冷却器
22 对辊破碎机
23 振动分级筛
24 离心通风机
25 离心集尘器
26 自动打包机
集尘袋
生产流程图工艺说明
一.原料粉碎
需粉碎原料经栅筛除去较大杂质后,投放到下料斗经吸尘罩吸,其目的是降低粉尘浓度。
由提升机送到永磁筒除去磁性铁杂质,再经圆筒初清筛得到合格的原料经粉碎储备仓进入粉碎机粉碎至需要大小粒度的粉料。
生产工艺流程图
服装生产工艺流程图验布│→│裁剪│→│印绣花│→│缝制│→│整烫│→│检验│→│包装│ (一)面辅料进厂检验面料进厂后要进行数量清点以及外观和内在质量的检验,符合生产要求的才能投产使用。
在批量生产前首先要进行技术准备,包括工艺单、样板的制定和样衣制作,样衣经客户确认后方能进入下一道生产流程。
面料经过裁剪、缝制制成半成品,有些梭织物制成半成品后,根据特殊工艺要求,须进行后整理加工,例如成衣水洗、成衣砂洗、扭皱效果加工等等,最后通过锁眼钉扣辅助工序以及整烫工序,再经检验合格后包装入库。
(二)面料检验的目的和要求把好面料质量关是控制成品质量重要的一环。
通过对进厂面料的检验和测定可有效地提高服装的正品率。
面料检验包括外观质量和内在质量两大方面。
外观上主要检验面料是否存在破损、污迹、织造疵点、色差等等问题。
经砂洗的面料还应注意是否存在砂道、死褶印、披裂等砂洗疵点。
影响外观的疵点在检验中均需用标记注出,在剪裁时避开使用。
面料的内在质量主要包括缩水率、色牢度和克重(姆米、盎司)三项内容。
在进行检验取样时,应剪取不同生产厂家生产的、不同品种、不同颜色具有代表性的样品进行测试,以确保数据的准确度。
同时对进厂的辅料也要进行检验,例如松紧带缩水率,粘合衬粘合牢度,拉链顺滑程度等等,对不能符合要求的辅料不予投产使用。
(三)技术准备的主要内容在批量生产前,首先要由技术人员做好大生产前的技术准备工作。
技术准备包括工艺单、样板的制定和样衣的制作三个内容。
技术准备是确保批量生产顺利进行以及最终成品符合客户要求的重要手段。
工艺单是服装加工中的指导性文件,它对服装的规格、缝制、整烫、包装等都提出了详细的要求,对服装辅料搭配、缝迹密度等细节问题也加以明确。
服装加工中的各道工序都应严格参照工艺单的要求进行。
样板制作要求尺寸准确,规格齐全。
相关部位轮廓线准确吻合。
样板上应标明服装款号、部位、规格、丝绺方向及质量要求,并在有关拼接处加盖样板复合章。
工艺流程设计-流程图
CW0401——32x3.5A1A—C H
2023/11/2
(五)管道仪表流程图
管道的公称压力 PG1310-300 A1A-H
管道材质类别 顺序号
代号 A B C
D
管道材质编号
材料名称 铸铁
代号 E
碳钢
F
普通低合金钢
G
合金钢
H
材料名称 不锈钢 有色金属 非金属
衬里及内腐蚀
2023/11/2
2023/11/2
(a)管道相连
(b)管道交叉
(二)工艺流程图的阅读
进
出
表示管道与其他图纸有关,一般在图的左方或右方,在空心 箭头内注明与其相关图纸的图号或序号,在其上方注明来或 去的设备位号或管道号或仪表位号。
2023/11/2
(二)工艺流程图的阅读
• 2.4 工艺流程图中阀门、管件图例
截止阀
管道仪表流程图的标注
2.管道的标注
(1)管道编号对象 所有的管道均要标注管道号。但下列情况除外: ①随设备、机械一起加工和配置的管道。 ②设备管口与设备管口直连,中间不需加短管者。
2023/11/2
(五)管道仪表流程图
③设备管口上直接接阀门、盲板等无管道连接的接管口。 ④管道上的放空管、导淋管。 ⑤设备上、机械上、管道上的伴热管和夹套。 ⑥控制阀的旁路管、切换使用的小型管件或阀组的相同 备用(或旁路)管。 ⑦仪表管线。
闸阀
球阀
直流截止阀
螺纹管帽 管端盲板
管帽
法兰连接 管端法兰(盖) 鹤管
三通截止阀
2023/11/2
三通球阀
四通球阀
四通旋塞阀
(二)工艺流程图的阅读
截止阀
11.生产工艺流程图和工艺说明
生产工艺流程图及工艺说明(一)、原料的接收 1 、散装原料的接收以散装汽车、火车运输的,用自卸汽车经地磅称量后将原料卸到卸料坑。
2 、包装原料的接收:分为人工搬运和机械接收两种。
3 、液体原料的接收:瓶装、捅装可直接由人工搬运入库。
(二)、原料的贮存饲料中原料和物料的状态较多,必须使用各种形式的料仓,饲料厂的料仓有筒仓和房式仓两种。
主原料如玉米、高粮等谷物类原料,流动性好,不易结块,多采用筒仓贮存,而副料如麸皮、豆粕等粉状原料,散落性差,存放一段时间后易结块不易出料,采用房式仓贮存。
(三)、原料的清理饲料原料中的杂质,不仅影响到饲料产品质量而且直接关系到饲料加工设备及人身安全,严重时可致整台设备遭到破坏,影响饲料生产的顺利进行,故应及时清除。
饲料厂的清理设备以筛选和磁选设备为主,筛选设备除去原料中的石块、泥块、麻袋片等大而长的杂物,磁选设备主要去除铁质杂质。
(四)、原料的粉碎饲料粉碎的工艺流程是根据要求的粒度,饲料的品种等条件而定。
按原料粉碎次数,可分为一次粉碎工艺和循环粉碎工艺或二次粉碎工艺。
按与配料工序的组合形式可分为先配料后粉碎工艺与先粉碎后配料工艺。
1 、一次粉碎工艺:是最简单、最常用、最原始的一种粉碎工艺,无论是单一原料、混合原料,均经一次粉碎后即可,按使用粉碎机的台数可分为单机粉碎和并列粉碎,小型饲料加工厂大多采用单机粉碎,中型饲料加工厂有用两台或两台以上粉碎机并列使用,缺点是粒度不均匀,电耗较高。
2 、二次粉碎工艺有三种工艺形式,即单一循环粉碎工艺、阶段粉碎工艺和组织粉碎工艺。
(1 )单一循环二次粉碎工艺用一台粉碎机将物料粉碎后进行筛分,筛上物再回流到原来的粉碎机再次进行粉碎。
( 2 )阶段二次粉碎工艺该工艺的基本设置是采用两台筛片不同的粉碎机,两粉碎机上各设一道分级筛,将物料先经第一道筛筛理,符合粒度要求的筛下物直接进行混合机,筛上物进入第一台粉碎机,粉碎的物料再进入分级筛进行筛理。
- 1、下载文档前请自行甄别文档内容的完整性,平台不提供额外的编辑、内容补充、找答案等附加服务。
- 2、"仅部分预览"的文档,不可在线预览部分如存在完整性等问题,可反馈申请退款(可完整预览的文档不适用该条件!)。
- 3、如文档侵犯您的权益,请联系客服反馈,我们会尽快为您处理(人工客服工作时间:9:00-18:30)。
(1)电解
本项目电解铝生产采用熔盐电解法:其主要生产设备为预焙阳极电解槽,项目设计采用大面六点进电SY350型预焙阳极电解槽。
铝电解生产所需的主要原材料为氧化铝、氟化铝和冰晶石,原料按工艺配料比例加入350KA 预焙阳极电解槽中,通入强大的直流电,在945-955℃温度下,将一定量砂状氧化铝及吸附了电解烟气中氟化物的载氟氧化铝原料溶解于电解质中,通过炭素材料电极导入直流电,使熔融状态的电解质中呈离子状态的冰晶石和氧化铝在两极上发生电化学反应,氧化铝不断分解还原出金属铝——在阴极(电解槽的底部)析出液态的金属铝。
电解槽中发生的电化学反应式如下:
2323497094032CO Al C O Al +⇒-+℃
℃直流电 在阴极(电解槽的底部)析出液态的金属铝定期用真空抬包抽出送往铸造车间经混合炉除渣后由铸造机浇铸成铝锭。
电解过程中析出的O 2同阳极炭素发生反应生成以CO 2为主的阳极气体,这些阳极气体与氟化盐水解产生的含氟废气、粉尘等含氟烟气经电解槽顶部的密闭集气罩收集后送到以Al 2O 3为吸附剂的干法净化系统处理,净化后烟气排入大气。
被消耗的阳极定期进行更换,并将残极运回生产厂家进行回收处置。
吸附了含氟气体的截氟氧化铝返回电解槽进行电解。
电解槽是在高温、强磁场条件下连续生产作业,项目设计采用大面六点进电SY350型预焙阳极电解槽,是目前我国较先进的生产设备。
电解槽为6点下料,交叉工作,整个工艺过程均自动控制。
电解槽阳极作业均由电解多功能机组完成。
多功能机组的主要功能为更换阳极、吊运出铝抬包出铝、定期提升阳极母线、打壳加覆盖料等其它作业。
(2)氧化铝及氟化盐贮运供料系统
氧化铝及氟化盐贮运系统的主要任务是贮存由外购到厂的氧化铝和氟化盐 ,并按需要及时将其送到电解车间的电解槽上料箱内。
本工程采用浓相输送+超浓相的气力输送方案,气力输送具有配置灵活、密闭性好、输送效率高、运行及维护费用低、不干扰其它工序正常作业等优点。
其贮运系统由贮槽、氧化铝仓库及相应的计量配料风动溜糟输送系统等组成,以实现新鲜氧化铝、载氟氧化铝、氟化铝、冰晶石的贮存配送功能,达到向电解槽稳定供料的目的。
本系统主要由新鲜氧化铝、氟化盐贮存输送系统和载氟氧化铝超浓相输送系统组成。
其工艺流程为:氧化铝及氟化盐由汽车运进厂内卸料站,搬运至氧化铝及氟化盐仓库内,氧化铝及氟化盐仓库内的四台电动葫芦桥式起重机协助卸车。
氧化铝拆袋后由液相输送系统送至双层氧化站贮仓。
氟化盐拆袋后槽罐车运送到双层氧化铝贮槽中的氟化盐贮仓内。
综合贮槽的低位槽内的新鲜氧化铝采用风动溜糟送至烟气净化系统,吸氟后的载氟氧化铝经气力提升器送至综合贮槽上部的高位槽。
综合贮槽的高位槽分别存放载氟氧化铝和氟化盐(高位贮槽的氟化盐钢仓),氧化铝超浓相输送系统任务是将载氟氧化铝和氟化盐分别计量、按比例掺配后送入每台电解槽槽上料箱中。
配料计量装置安装在双层贮槽内,这一装置采用静态计量来精确称量氧化铝,采用容积计量按设定的比例掺配氟化盐。
此装置完全解决和克服了系统风和风压对传感器的干扰,可以确保计量和配料的准确性。
两种物料根据要求确定其配比,经给料、计量装置汇入风动溜槽配送系统,送到各个电解槽槽上料箱,供电解用。
(3)铸造工艺
铸造车间的任务是将电解车间生产的液态铝铸造成商品铝锭,本设计产品方案为重熔铝锭,铝锭重20kg/块。
铝液从真空抬包中直接注入铝混合炉内,熔池装满后加入造渣剂,经搅拌后扒去铝液表面浮渣。
扒渣后铝液静置30分钟即可进行浇铸。
铝液在炉内温度宜保持在760~780℃。
铝液从溜槽进入连续式铸造机铸锭,再经自动打印批号、冷却后由堆垛机堆垛、钢带打捆,经质量检验合格、标明产品成份并计量后,运至成品堆场备销。
(4)阳极组装
阳极组装车间的功能是处理来自电解车间的残极和为电解车间提供合格的新阳电极组,处理阳极时,首先将残极上粘附的电解质清理干净,经破碎后送电解车间使用,对用过的铝导杆、钢爪进行校直、修复以备再用,炭块压脱后,残极集中堆放、回收。
磷铁环压脱后,送中频炉熔化。
将钢爪和阳极炭块用熔化的磷生铁浇铸为一体,再进行阳极组装。