球团工艺简介及生产流程图
球团矿工艺流程

球团矿生产工艺流程在球团矿的生产流程中,一般包括原料准备、配料、混合、造球、烘干和焙烧、冷却、成品和返矿处理等工序,如下图所示配料:原料配比采用酸性精粉+膨润土,配料按照1.05配比(料重/成品)。
其中包含水份挥发、返粉等烧损。
烘干机:经过配料后精粉通过烘干机脱去精粉矿水份,从而为润磨机进一步提高精粉细度创造条件。
润磨机:精粉经过润磨机钢球研磨,提高精粉细度8-10%(出料粒度要求小于250目的达到70%以上),同时将混合料进行较好的混合,为下一步的造球提供条件。
圆盘造球机:将皂土、红泥、铁精矿粉混合后,输入圆盘造球机上部的混合料仓内,均匀地向造球机布料,同时由水管供给雾状喷淋水,倾斜(倾角一般为40一50°)布置的圆盘造球机,由机械传动旋转,混合料加喷淋水在圆盘内滚动成球,球大小约10-25mm。
干燥和焙烧:在竖炉顶部烘干床(小水梁上的蓖板中部位置)对造好生球进行烘干,以脱去球内水份,使生球达到有效的强度,然后进入焙烧带进行培烧,温度约1100℃左右(一厂热电偶显示在850左右),生成成品球团矿。
冷却成品:成品球团矿在竖炉底部经过高压风机强制通风(高压风冷却热球后变为热空气,然后通过大水梁上的导风墙上升到烘干床对冷球进行烘干),达到球团矿有效冷却,减少对下道工序的烧损。
卸料:齿辊(内通水冷却)卸料到炉下料仓(仓壁装有冷却壁),再通过电磁振动给料机对料车给料,由卷扬卸料给运输车辆到高炉。
导风墙:竖炉炉膛内的导风墙是由耐火材料(盖板砖)构筑成的纵贯竖炉炉膛的中空墙,导风墙内有竖直风道,把与炉膛下部的热矿球进行热交换后的冷却风引导到炉口烘床下面以对生球进行有效烘干。
导风墙由其下部的大水梁进行支撑。
大水梁通水冷却。
水系统:水泵房(造球盘东)供水给造球盘、大小水梁、齿辊卸料器、料仓冷却壁。
小水梁、齿辊卸料器、料仓冷却壁的冷却水经凉水塔后,回水泵房进行循环。
大水梁采用汽水冷却,蒸汽到炉顶汽包,经凝汽器后上凉水塔回水泵房。
球团生产工艺(1)

混匀设备 轮式混合机 卧式混合机 立式混合机
球团生产工艺(1)
• 立式混合机
1、传动装置2、润滑装置3、筒体4、检修口5、下料门6、下料推杆7பைடு நூலகம்耙齿
球团生产工艺(1)
4、造球设备 圆锥造球机 圆筒造球机 圆盘造球机
球团生产工艺(1)
圆锥造球机
球团生产工艺(1)
4、造球设备 圆锥造球机 圆筒造球机 圆盘造球机
年份
2004
工序能耗 (kg/t)
40.24
2005 35.80
历年工序能耗
2006
2007
36.16
33.86
2008 32.03
2009
2010 (1-11月)
26.67 25.58
球团生产工艺(1)
(3)降低膨润土配比提高球团矿质量攻关
1、膨润土大型工业试验取得突破性成果。钙基膨润土优化试验、 汽巴粘结剂配加试验、钙钠混合膨润土试验、复合膨润土配加试验等 选择出性能更优的膨润土做为粘结剂,使新粘结剂配比降低至1%左 右;
14.5
环冷Ⅳ段
<100
-
28
9
球团生产工艺(1)
(六)生产实践
1、生产实践中遇到的问题
回转窑长期结圈; 生产过程中能耗大; 膨润土用量大,球团矿铁低硅高。
球团生产工艺(1)
2、采取的措施
(1)回转窑结圈问题攻关
低熔点物
煤灰分熔点低 球团中含硅高
结圈
煤灰分高 粉末多
预热球强度差 生球爆裂 铁原料粒度粗
2、现场设备智能化。 3、集现场设备的远程控制、参数化及故障诊断 为一体。 4、现场总线是计算机网络通信向现场级的延伸。 5、系统可靠性高,可维护性好。 6、节省成本。
首钢球团厂生产工艺流程简介

二系列球团矿冷却系统配置简图
首钢球团厂球团工艺流程
3.4.7 主体设备技术参数
①一、二系列链篦机主要技术参数
项 宽度 有效长度 功率 电压 目 单 位 m m kw V 一系列 4 21.5 18.5 380 二系列 4.5 56 11 380
首钢球团厂球团工艺流程
②一、二系列回转窑本体主要技术参数
首钢球团厂球团工艺流程
首钢球团厂 生产工艺流程简介
首钢球团厂球团工艺流程
1 2
前言
生产线基本概况
3
工序配置
简 介 目 录
4
高炉酸性炉料的对比分析
首钢球团厂球团工艺流程
1
前言
首钢球团厂始建于1985年,于1986年6月建 成投产,开始金属化球团生产;1989年 3月转产 氧化球团;2000年进行了以优化回转窑长径比和 改进冷却方式为主的工艺改造,率先形成链篦机回转窑-环冷机氧化球团生产新工艺,年产设计能 力100万吨,开创了国内氧化球团生产技术的新纪 元;
各段分别配置5个、2个、7个。
3.4.2 二系列生球干燥和预热系统主要由“链篦机本体、3台耐 热风机(1#、2#、3#)、1台主引风机、干返放灰部分”等组成 。链篦机工艺分布为五段三室,由鼓风干燥段、抽风干燥Ⅰ段 、抽风干燥Ⅱ段、预热Ⅰ段、预热Ⅱ段构成;风箱共计配置19 个,各段分别配置3个、2个、3个、4个、7个。
首钢球团厂球团工艺流程
2003年 4月份,第二条年产200万吨链篦 机-回转窑-环冷机氧化球团生产线竣工投产, 促进了国内大型回转窑的发展。
也正式随着首钢球团厂对氧化球团工艺和 技术的优化,引领了国内球团工业的发展,尤 其是二十一世纪,链篦机-回转窑-环冷机氧化 球团技术的迅猛发展,促进了与国际先进生产 工艺的接轨。
球团工艺
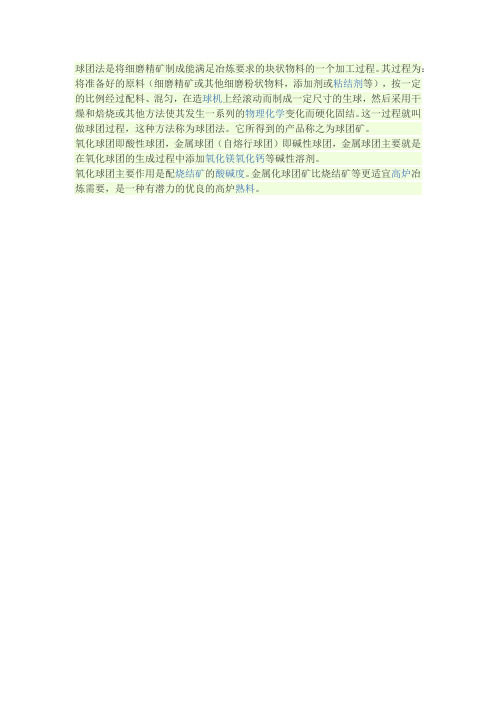
球团法是将细磨精矿制成能满足冶炼要求的块状物料的一个加工过程。
其过程为:将准备好的原料(细磨精矿或其他细磨粉状物料,添加剂或粘结剂等),按一定的比例经过配料、混匀,在造球机上经滚动而制成一定尺寸的生球,然后采用干燥和焙烧或其他方法使其发生一系列的物理化学变化而硬化固结。
这一过程就叫做球团过程,这种方法称为球团法。
它所得到的产品称之为球团矿。
氧化球团即酸性球团,金属球团(自熔行球团)即碱性球团,金属球团主要就是在氧化球团的生成过程中添加氧化镁氧化钙等碱性溶剂。
氧化球团主要作用是配烧结矿的酸碱度。
金属化球团矿比烧结矿等更适宜高炉冶炼需要,是一种有潜力的优良的高炉熟料。
球团工艺、设备情况介绍.
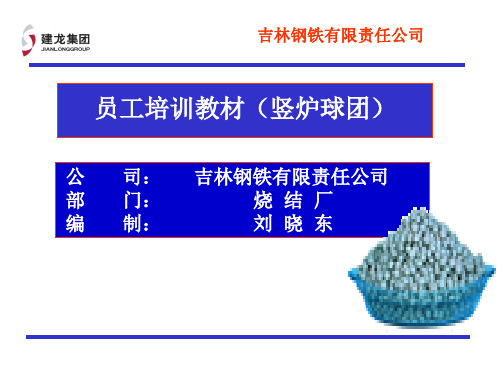
球团工艺、设备情况简介
成品系统岗位主要设备有: ⑴、带冷机岗位:50m2轻型鼓风带冷机两台,每台最大处理能力 100t/h,冷却温度600度降至80度。 ⑵、成品筛分岗位:振动筛,能力250t/h,筛孔尺寸5mm。
员工培训教材(竖炉球团)
第二章:球团工艺对原料的要求
第一节:球团工艺对铁精矿的要求
TFe% 铁精粉 66 FeO% 25 SiO2% 5 陪烧后损失% -2
膨润土(干基)
1.6
0
65
7
配料配比:按100Kg干料计算 铁精粉:98.2Kg,占98.8%,膨润土1.2 Kg,占1.2%(生产经验确定) 确定条件(实际经验):铁精粉陪烧后残留FeO≤0.6%,其余全部氧化成 Fe2O3 计算各种原料进入球团矿部分(以100Kg干料为标准) 铁精粉:Q精=98.8×[1-(-2%)]=100.78(kg) 膨润土:Q土 =1.2×(1-7%)=1.12(kg)
膨润土配比小或膨润土实际下料量偏 小 膨润土配比大或膨润土实际下料量偏 大
高品位铁精粉配比适当提高;检查低品位铁精粉 流量误差;检查膨润土实际配比
适当增加膨润土配比和检查膨润土下料量 适当减少膨润土配比或调整膨润土下料量
配料操作
2、配料的计算和调整: 目前我们使用的计算方法为:根据本厂的原料和化学成分,事先确定配比, 再进行配料计算。 单一精矿粉计算实例 已知条件:原料化学成分
球团工艺、设备情况简介
第三节:吉林钢铁烧结厂球团工序设备简介:
球团工艺、设备情况简介
吉林钢铁公司烧结厂现生产运行的2x10m2竖炉其主要系统包括:原料 系统、主体、辅助、成品系统。 原料系统岗位主要设备有: ⑴、配料岗位:配料矿槽8个,每个矿槽容积:162m3;直径为2.0m 圆 盘给料机6台;给料能力为20~200吨/h; 皮带称量秤六台,能力:15~150t/h; 失重称2台,小时配料量:0.7~2.1t。 ⑵、烘干岗:Φ3.6m×20m圆筒烘干机一台;处理量:220t/h(湿重)。 ⑶、润磨岗位:Φ3.5m× 6.2m润磨机二台,生产能力:80t/h。 ⑷、造球岗位:直径为1. 6m 圆盘给料机6台;每台圆盘给料能力为: 10~100吨/h ;Φ6.0m 造球机六台,每台造球机生产能力为:60 t/h—70 t/h;混合矿槽6个,每个矿槽容积:28m3。 ⑸、58辊双层箱式筛分机岗位:生产能力为:110t/h,上层筛辊间距为 18mm,下辊筛间距为6mm。
球团工艺介绍
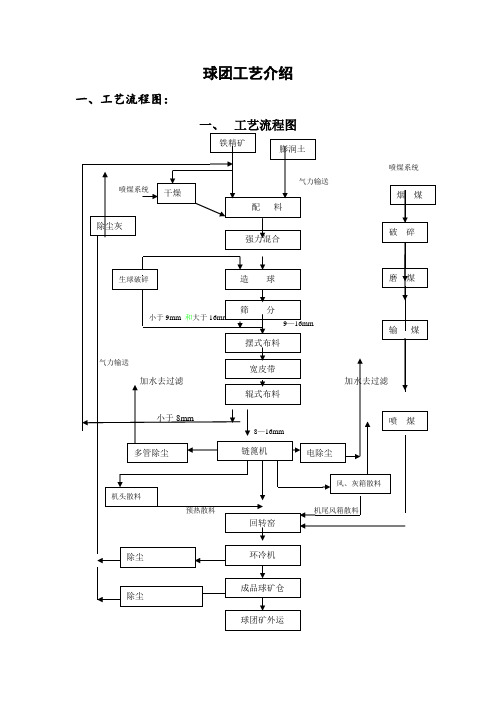
球团工艺介绍一、工艺流程图:二、工艺系统介绍:1、精矿过滤系统:主要承担选矿和精选来矿浆的脱水、精矿粉的储存、精矿向球团系统输送、部分精矿粉的装车任务,每小时向球团系统供料380-420吨。
工艺流程:来自选矿和精选的矿浆(浓度50-60%)先经过过滤厂房外的三管分矿器,然后分配到各台过滤机,共配置7台过滤机,正常运行4-5台,型号ZPG-72,盘式外滤,过滤面积72m2,利用系数0.7-1 t/m2.h,每台过滤机都配置真空泵及气水分离器。
过滤后的精矿粉水分在10%以下,精矿粉落在排料皮带上,排料皮带可以移动,可以将料给到取球团的GL-1皮带(去球团生产系统),也可以给到精矿料仓。
精矿仓面积102m×30m,可以储存矿粉2.5万吨,配置两台20吨抓斗(跨距28.5m),既可以装火车发运,也可以将精矿粉输送到球团生产流程。
矿浆中的水分在过滤后和部分精矿粉形成滤液(浓度5-8%),各台过滤机的滤液合并到滤液泵池(共配置4台砂泵,型号100ZJ—1-A36,流量200 m3/h,扬程60 m),由砂泵输送到滤液浓缩大井(直径50m),经过浓缩以后的矿浆(浓度35%)经过大井底部排出,由砂泵(2台,型号100ZJ—1-A36,流量200 m3/h,扬程60 m )输送到选矿来精矿管道上,经过旋流器浓缩(旋流器型号FX300-GK,)底流进入选矿矿浆中,溢流又返回浓缩大井。
大井分离后的水,悬浮物含量在0.3%以下,由大井周边排出,汇集后由水泵输送到过滤和精选循环使用。
2、干燥系统:主要承担过滤后精矿的进一步脱水任务,使精矿水分在9.2±0.2%,适于造球,处理量380-420吨/h。
工艺流程:来自过滤机或精矿仓的湿精矿粉和链蓖机前辊式布料器的湿返料由皮带转运进入圆筒干燥机(型号φ3.6×29,转速3.45r/min,斜度5%),干燥机前配置煤粉燃烧炉,(燃煤能力 3 t/h,炉膛温度低于1200℃,火道温度低于800℃) ,燃烧后的高温烟气和湿精矿粉顺流进入干燥机,对流干燥.干燥后的含水废气经过冲击式除尘器净化,排入大气. 干燥后的精矿粉由皮带转运到配料室。
球团生产工艺流程
选择适当的预热温度 300℃-900 ℃ 左右;焙烧带:温度控制1150
℃—1200 ℃,热量来自磁铁矿氧化放热、燃烧室供热和鼓风带来的 热量,在该带球团主要发生化学反应,球团的强度会急剧提高;均热 带起固结充分的作用,烧结反应完成要在高温下持续一段时间,所以 均热带对球团质量至关重要;冷却带是竖炉过程的最后一个阶段,球 团到了冷却带和鼓入炉的冷空气对流进行热交换。
• 二、配料:
• 配料是球团工艺的基础,生产球团的原料主要包括精矿粉,添加剂: 膨润土,要求,膨润土的配比不高于1.8%,混合料要求具有均匀性和 稳定性。配料系统控制:主要通过电子皮带秤和人工跑盘计算配料量, 跑盘时矿粉允许的波动范围:≤±0.5kg/m,膨润土允许的波动范围: ≤±0.02kg/m。
含量%
49.83 26.80 5.79 13.33 2.98 2.76 0.095 0.164
•
• • • •
• 附:流程图:
ቤተ መጻሕፍቲ ባይዱ
氧化铁皮
膨 润 土 配料系统
自然脱水湿泥 烘干系统 加热炉
斗式提升机
强力混合机
中间仓
斗式提升机
高压压球机
高压压球机 助燃、冷风机
引风机 (4座)
污泥球焙烧炉(4 座) 成品球
膨润土
造 球 生球筛分
16毫米以上
煤气、空气
竖炉焙烧 成品矿仓
冷却风
污泥球新线工艺流程
• • 污泥球生产情况简介: 一、污泥球生产线的主要作用:是将炼钢收尘系统产生的的含铁尘泥 (简称 污泥)加入适量的膨润土和氧化铁皮,冷压成型,通过烘干和简单的焙烧成 成品污泥球。 二、生产设备及产能:目前公司本部污泥球生产系统由一套配料系统、一套 烘干系统、两台高压压球机、4座污泥球焙烧炉组成,生产系统的产能可达 400—450吨/日,目前日产300吨左右(6月30日后),现价段炼钢日产污泥 270吨(干基)左右。 三、污泥球生产配料:膨润土2%,炼钢污泥98%,正常情况下可配比一定量 的氧化铁皮。 四、成品球团指标情况: 质量指标:污泥球平均强度2400N, 950N合格率65%, 化学成份: TFe FeO SiO2 CaO MgO Al2O3 S P 成份
简述球团生产工艺流程
简述球团生产工艺流程
球团生产工艺是一种将铁矿石粉通过高温固结制成球团的工艺流程。
以下是一般球团生产工艺的简要流程:
1. 配料:将铁矿石粉、添加剂(如膨润土、石灰石等)和燃料
(如煤粉、天然气等)按照一定比例混合。
2. 造球:将混合好的原料通过造球机进行造球,制成直径约 10-
15 毫米的球体。
3. 干燥:将造好的球团进行干燥,去除水分,以便进行后续的处理。
4. 预热:将干燥后的球团送入预热器中进行预热,使其温度升高
到一定程度。
5. 焙烧:将预热后的球团送入回转窑或竖炉中进行焙烧,使其在
高温下固结。
6. 冷却:将焙烧后的球团进行冷却,使其温度降低到适宜的程度。
7. 筛分:将冷却后的球团进行筛分,去除不合格的球团。
8. 成品:将合格的球团包装成成品,准备运输和销售。
球团生产工艺的优点包括:铁矿石利用率高、产品质量好、生产效率高、环保等。
球团矿生产原理及工艺(PPT65页)
摆动
索状
毛细
泥浆
生球生成过程
母球生成:
点状水粘结粉矿颗粒形成含水很高的母球。
母球长大:
母球在滚动过程中,在毛细水的作用下,矿粉颗粒被 拉紧,毛细管变细,将毛细水挤出到球表面,粘结更 多的矿粉,使母球长大。这时在母球表面喷洒水分时 会加快母球的成长。
生球的密实:
生球长大到一定尺寸后,停止加水,此时球团在滚动 和毛细水作用下,颗粒进一步靠近,颗粒内部的空隙 变小,毛细力作用增大,生球进一步密实,毛细水进 一步被挤到球表面,粘上矿粉直至内部毛细水被全部 挤出,达到最大的生球强度。
粒度对爆裂温度的影响
生球爆裂的试验结果
皂土、生球水分对爆裂的影响
结晶水与爆裂温度的关系
原料底 水含量 与落下 强度及 爆裂温 度的关
系
球团矿固结机理
磁铁矿氧化固结机理
赤铁矿氧化微晶的生成 赤铁矿微晶的再结晶 赤铁矿晶体的长大
赤铁矿氧化固结机理
赤铁矿的再结晶 晶体长大
球团矿的液相粘结
铁酸钙粘结相 硅酸盐粘结
薄膜水:
在结合水外部由于残余的颗粒表面能形成的水膜,能够在不同颗粒表 面迁移。
结合水和薄膜水是维持生球强度的要素之一。 毛细水:
• 存在与矿石颗粒缝隙中的水,通过毛细力拉紧矿粉颗粒,是粉矿成球 的主要动力。
重力水:
• 超过结合水、薄膜水和矿石颗粒空隙能够容许的最大毛细水的总量后 的水,破坏生球。
生球生成机理1
历史:
球团矿工的始于1919年,由瑞典开发。 1946年在美国实现了球团矿的竖炉的工业性生产。
产生原因:
美国为了利用含铁只有35%的低品位铁燧岩,将其粉碎到-44μm达 到90%以上进行磁选,获得了高品位精矿。但这种精矿不能烧结, 所以采用了球团工艺。
球团工艺、设备情况介绍.
球团工艺对原料的要求
第二节:球团工艺对其他含铁原料的要求
球团工艺对原料的要求
1、 炼钢污泥
为了提高铁精粉的粒度组成,我们在球团 矿生产当中往往在原料使用上加入2%的炼 钢污泥调整其铁精粉的粒度组成使其满足造 球机理的要求。 ⑴、炼钢污泥的品位 提高球团含铁原料的品位能改善球团焙烧 性能。国内球团多用60%以上品位的炼钢污 泥来调节精矿粉的粒级组成,此外还要求成 分稳定。 ⑵、炼钢污泥的粒度 炼钢污泥的粒度及其组成对生球的强度和造球产量以及球团的焙烧固结过程都有 很大影响。球团生产要求炼钢污泥的粒度细,而且有合适的粒度组成。一般为— 325目的占85%以上。 ⑶、炼钢污泥的水分 含铁原料的水分对配料、润磨、造球影响很大。所以炼钢污泥的水分我们要求 不大于15%,从而防止生球水份过大会恶化炉内料柱透气性,使竖炉难以正常生产。
开始动工筹建,一期工程于2011年9月18日竣工投
产;二期预计投产时间为2011年10月20日;其年
设计能力为:110万吨。
球团工艺、设备情况简介
第三节:吉林钢铁烧结厂球团工序设备简介:
球团工艺、设备情况简介
吉林钢铁公司烧结厂现生产运行的2x10m2竖炉其主要系统包括:原料 系统、主体、辅助、成品系统。 原料系统岗位主要设备有: ⑴、配料岗位:配料矿槽8个,每个矿槽容积:162m3;直径为2.0m 圆 盘给料机6台;给料能力为20~200吨/h; 皮带称量秤六台,能力:15~150t/h; 失重称2台,小时配料量:0.7~2.1t。 ⑵、烘干岗:Φ3.6m×20m圆筒烘干机一台;处理量:220t/h(湿重)。 ⑶、润磨岗位:Φ3.5m× 6.2m润磨机二台,生产能力:80t/h。 ⑷、造球岗位:直径为1. 6m 圆盘给料机6台;每台圆盘给料能力为: 10~100吨/h ;Φ6.0m 造球机六台,每台造球机生产能力为:60 t/h—70 t/h;混合矿槽6个,每个矿槽容积:28m3。 ⑸、58辊双层箱式筛分机岗位:生产能力为:110t/h,上层筛辊间距为 18mm,下辊筛间距为6mm。
- 1、下载文档前请自行甄别文档内容的完整性,平台不提供额外的编辑、内容补充、找答案等附加服务。
- 2、"仅部分预览"的文档,不可在线预览部分如存在完整性等问题,可反馈申请退款(可完整预览的文档不适用该条件!)。
- 3、如文档侵犯您的权益,请联系客服反馈,我们会尽快为您处理(人工客服工作时间:9:00-18:30)。
烧结厂球团工艺简介及生产流程图
德晟金属制品有限公司烧结厂建设1座12m 2竖炉,利用系数
6.3t/m 2•h ,年产酸性球团矿60万t 。
车间组成及工艺流程
1.1 车间组成
车间组成:配料室、烘干机室、润磨室、造球室、生筛室、转运站、焙烧室、带冷机通廊、成品缓冲仓、风机房、煤气加压站、软水站、高低压配电室等。
1.2 工艺流程
工艺流程图见付图
1.2.1 精矿接受与贮存
竖炉生产主要原料为磁铁矿精粉,对铁精粉化学成分要求是
精矿进料采用汽车输送,汽车将精矿粉卸到下沉式精矿堆场,经抓斗吊运至配料仓。
进厂铁精粉化学成分 名称
TFe(
%)
Feo (%) SiO2(%) S(%) 粒度(-200mm )
磁铁矿
份 ≥65
≤23 ≤7 ≤0.2 ≥85
1.2.2膨润土接受与贮存
竖炉对膨润土化学成分要求是:
进厂膨润土化学指标
名称
吸水率(2h)
∕%
吸蓝量
(100g膨润土∕g)
膨胀容(2g
膨润土∕ml)
粒度
(-200mm)
水分
(%)
钠基膨
润土
≥400 ≥30 15 ≥95 ≤10 袋装膨润土用汽车运入,储存在膨润土库,由库内设的电葫芦将袋装
膨润土运至膨润土配料仓平台,由人工抖袋将膨润土卸到膨润土配料仓。
1.2.3配料系统
配料矿槽采用单列配置,4个精矿配料仓,容积100m3,储量8.8h,三用一备;2个膨润土仓,膨润土仓为一用一备。
配料室为地
下结构。
采用自动重量配料,根据设定的给料量和铁精粉与膨润土的
配比,自动调节给料量。
铁精粉通过仓下2m圆盘给料机和配料皮带
秤配料。
膨润土通过螺旋给料机和螺旋秤配入皮带。
圆盘给料机和螺
旋给料机采用变频控制。
并且尽量做到铁精矿与膨润土两料流首尾重合。
在配料室膨润土落料点处和膨润土设抽风除尘,采用布袋除尘器,
布袋除尘器采用反吹清灰方式。
设置铁精粉仓库和膨润土库。
铁精粉仓库能容纳约9天的用量,
下沉式结构,铁精粉采用抓斗吊上料,设置2台10t抓斗吊。
膨润土
库用来堆放袋装膨润土,膨润土设电葫芦环形轨道由电葫芦将袋装膨
润土吊运至膨润土配料仓顶平台,人工抖袋卸料至膨润土配料仓。
1.2.4原料干燥系统
精矿进厂水分为10.5%左右,不能满足造球对精矿水分要求,因此设计中采用了干燥工艺,将精矿中水分部分脱除,以保证铁精矿水份满足造球工序的要求。
需干燥的湿精矿粉经配料胶带机运至干燥窑,物料干燥后经胶带机运至造球前料仓。
干燥选用Φ2.4×18m圆筒干燥机,采用顺流式,脱去4%的水分,干燥后料的水分控制在6~7%左右。
精矿干燥热风炉以焦炉煤气为燃料,配置助燃风机,窑进口烟气温度700~900℃,出口废气温度120℃,从干燥机排出的废气经烟囱排放。
按年60万吨计算,干燥窑需焦炉煤气910m3/h,压力9kPa,助燃风量14000m3/h,全压力5kPa。
1.2.5润磨
来自干燥系统的混合料经皮带运输机运入润磨室,在周边排料的润湿球磨机中进行磨矿。
润磨机的主要作用是将铁精矿粉进一步细磨,提高精矿的活性度,增加造球原料的比表面积,改善成球性能,同时降低膨润土用量,提高生球强度,使球团矿的品位得以提高。
考虑润磨机产量及需要100%润磨,选用3870润磨机1台。
经润磨后的造球混合料运往造球室中间仓。
润磨室设旁路,特殊情况下铁精粉不经润磨直接进入造球系统。
润磨机上料采用移动式皮带机给料。
1.2.6造球系统
经混料后的造球混合料经皮带机运至造球室中间矿仓。
中间矿仓为单列布置,每台造球机配设一个中间矿仓,仓容40m3,混合料通过犁式卸料器和头轮卸入中间矿仓,经仓下圆盘给料机及上造球皮带机稳定向造球机供料,在造球过程中添加约~1.0%的水,以使混合料水分控制在造球最佳值。
实践证明造球过程中加适量的水利于成球。
在机械力和毛细水的作用下,造球盘内形成清晰的母球区、生球长大区和成球区。
造好的生球直接上竖炉。
为进一步提高造球质量,造球系统配置3台6m圆盘造球机,造球机转速可调,倾角可调。
造球机单列布置,二用一备,配置一条皮带将生球运往筛分室。
生球各落料点落差高度尽可能小,以免生球破碎。
造球室去筛分室皮带带速控制为0.8m/s。
1.2.7生球筛分
来自造球室的生球经带式输送机运进生球筛分室进行生球筛分,产品为9~18mm的生球,经带式输送机运往竖炉焙烧室;筛除返球为<9mm和大于18mm的返料,经返料皮带机、转运站送往返料皮带上,再运往润磨机进行润磨。
生球筛分室设44辊圆辊筛1台,倾角10-13度,选用陶瓷辊。
分组集中传动。
竖炉开炉或调整炉况时需补充熟球。
熟球补球仓位于筛分室外侧地面上,熟球用铲车运至补球仓,经由皮带机送至筛分室上竖炉皮带。
1.2.8竖炉焙烧室
竖炉焙烧系统的主要工艺设备是12m2竖炉一座。
竖炉采用自立式结构。
本竖炉主体采用钢筋混凝土框架结构,屋顶采用现浇混凝土屋面。
一层设置两台排料电振给料机(GZ6型);
二层设置辊式卸料器和液压泵站;
三层为燃烧室平台,设置卧式燃烧室2个,每室配2只环缝涡流式焦炉煤气烧嘴;
四层炉顶布料平台,布料采用往复式布料小车,布料小车的皮带宽度B=650mm、L=12m。
通过梭式布料器布到竖炉烘干床上的合格生球,在炉内下降过程中与上升的热气体进行逆流热交换,生球从炉顶开始,经历干燥、预热、焙烧、均热和冷却共五个阶段,最后成品球从炉底排出。
12m2竖炉的烘干床水梁、大水梁、下部水套等部位采用循环水强化冷却,循环冷却水由相邻烧结厂泵房提供;导风墙水梁采用汽化冷却,补充水来自相邻竖炉软水站。
炉框架上部设有汽化冷却汽包和事故水箱。
汽包容积8m3。
在竖炉焙烧带的供热是焦炉煤气通过烧咀在圆形卧式燃烧室燃烧后经过喷火口打入焙烧带。
燃烧室的助燃风机选用二台离心式助燃风机,一使一备;风量48000 m3 / h,升压25kPa。
竖炉冷却带的冷却风,选用二台离心式冷却风机,一使一备;风
量60000m3/h,升压29 kPa。
1.2.9成品冷却输送系统
成品冷却输送系统配置6台50m2轻型鼓风带冷机对竖炉排出的热球团矿进行冷却,冷却后球团矿温度小于120℃。
冷却后的成品球团落入成品缓冲仓,经成品皮带机运往成品仓储存或经由成品皮带机不经成品仓直接转运至高炉矿槽。
从带冷机中掉下细颗粒落入带冷机下面的收尘斗中,由带冷机下安置的刮板运输机随同成品球一同运送到成品缓冲仓中。
成品仓下可直接装车将成品球运至成品堆场。
成品仓容积为3x220m3,三个储仓储量460吨,可以储存成品球团6个小时。
竖炉生产工艺流程图
精矿粉
配料仓 膨润土 烘干混合室 润磨机室
造球室 生筛室
焙烧室
带冷机
成品料仓
成品转运站 送至高炉
电除尘 尘
除
尘灰 煤气 水 助燃风
冷却风 助燃风 煤气
Welcome To Download !!!
欢迎您的下载,资料仅供参考!。