印染废水深度处理超滤-反渗透双膜法工艺
印染废水回用处理工艺

印染废水回用处理工艺纺织印染行业废水具有排放量大、水质变化大、有机物浓度高、色度高等特点,其处理相对复杂.近年来,由于水资源的紧缺,众多环保学者在印染废水回用领域进行了大量研究.为了保证印染废水出水的稳定达标和中水回用,双膜法成为印染废水处理领域深度处理最为常用的处理技术,研究表明,全国75%以上的印染企业利用双膜法作为深度处理技术.双膜法技术包括超滤和反渗透(RO)两种膜处理技术.RO出水包括淡水和浓水,其中,淡水可直接排放或完全回用于印染工序,浓水由于盐度高、含一定浓度的难降解有机物和硬度,不仅不能直接排放,而且处理相当困难.目前,针对印染反渗透浓水(ROC)的主要处理措施有直接排放处理、回流二次处理和膜蒸馏技术.直接排放处理一般是指直接排入海洋,是最为常用的浓水处理技术,但此技术受到地理位置限制,在广大内陆等离海岸较远的地区不宜推广.回流二次处理是指将浓水回流至水处理系统的前处理段,再次进入水处理系统进行二次处理,这样使浓水中的难降解有机物和高盐度物质得不到外排,长期回流会导致生化系统盐分逐渐积累,微生物活性降低并最终导致生物处理系统的崩溃.膜蒸馏技术是一种膜技术与蒸馏技术相结合的膜分离技术,可以实现浓水和盐分的完全回收,但该技术耗能太高,大部分企业很难承受.另外,汪晓军等采用Fenton氧化结合石灰苏打处理印染ROC,实现了印染ROC 的完全回用,但由于Fenton氧化技术处理过程中有可能带入印染需严格限制的Fe2+,因此,需要后续设置絮凝沉淀池以完全去除出水中的Fe2+.鉴于现有各浓水处理工艺的不足,亟需开发一种新的处理工艺解决地理位置受限、处理成本过高及处理工艺复杂等难题.过硫酸盐(PS)氧化作为一种新型的高级氧化技术近年来在环境领域逐渐受到研究人员的关注.在常温条件下,PS是一种较为温和的氧化剂,反应速率较慢.当PS受到外界条件如热、微波、过渡金属离子作用时容易被活化,产生氧化性更强的硫酸根自由基(SO· -4),其标准氧化还原电位E0=2.60 V,高于PS的E0=2.01 V.相应的反应原理如下:pH对PS降解有机物有一定的影响,杨照荣等的研究表明,PS的氧化能力在碱性条件下比酸性和中性条件下较强,因为在碱性条件下硫酸根自由基会生成氧化能力更强的羟基自由基(· OH,E0=2.80 V),反应如下:除pH外,初始PS投加量、反应温度都是影响PS氧化反应的重要影响因素.PS 氧化镇痛药(立痛定)的研究表明,有机物的氧化速率在一定初始PS范围内随初始PS用量的增加而加快.温度的提升大大提高了PS分解垃圾渗滤液中腐殖酸的速率,温度从90 ℃上升到150 ℃时,有机物去除率从63.5%上升到76.0%,温度继续上升到170 ℃,有机物去除率上升到78.8%.石灰苏打软水技术是废水处理领域最为传统的脱硬度技术.印染用水中硬度过高会造成染料在染色织物表面分配的不均匀性,同时降低染色织物的色牢度,是印染回用水严格规定的水质指标.采用石灰软化和微滤工艺处理某热电厂的循环冷却排污水的研究表明,石灰软化可大大降低废水的硬度和碱度,出水完全满足回用要求.本研究结合印染ROC水质特点及印染回用时需补充大量硫酸钠作为印染助剂的要求,将PS氧化和石灰苏打软水技术联合应用于印染ROC处理过程中.首先利用条件实验和正交试验研究PS氧化去除印染ROC难降解有机物的影响因素,包括反应pH、初始PS投加量和反应温度等条件,研究有机物降解的动力学模型;其次分析PS氧化前后无机组分和有机组分;最后确定石灰苏打脱硬度的最佳的石灰和苏打药剂投加量组合.2 材料与方法2.1 印染废水ROC印染ROC取自佛山市西樵镇某纺织有限公司,废水总排放量60000 m3 · d-1,ROC排放量约20000 m3 · d-1.原水水质:CODCr为112.5 mg · L-1,BOD5/CODCr 为0.05,TOC为34.0~35.6 mg · L-1,SO42约9600 mg · L-1,CO32约1500 mg · L-1,Cl-约650 mg · L-1,pH为8.3~8.8.2.2 主要仪器和药品pHs-3c便携式pH计(上海精密科学仪器有限公司);COD快速密闭消解测定仪(广东,韶关);BOD测定仪(美国,HACH);电子天平,恒温振荡器(上海精密科学仪器有限公司);离子色谱仪ICS-1600(美国,戴安);TOC测定分析仪TOC-LCPH/CPN(日本,岛津);PS、磷酸二氢钠、石灰和苏打等药剂均为分析纯(天津科密欧化学试剂有限公司).。
采用超滤纳滤双膜技术资源化处理印染废水.
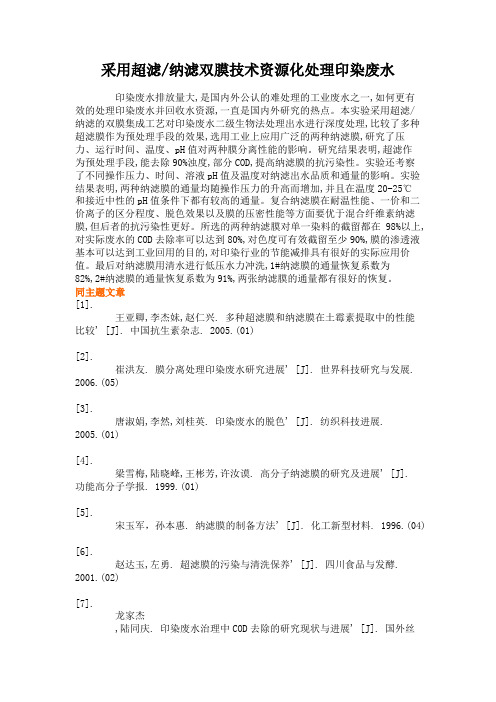
采用超滤/纳滤双膜技术资源化处理印染废水印染废水排放量大,是国内外公认的难处理的工业废水之一,如何更有效的处理印染废水并回收水资源,一直是国内外研究的热点。
本实验采用超滤/纳滤的双膜集成工艺对印染废水二级生物法处理出水进行深度处理,比较了多种超滤膜作为预处理手段的效果,选用工业上应用广泛的两种纳滤膜,研究了压力、运行时间、温度、pH值对两种膜分离性能的影响。
研究结果表明,超滤作为预处理手段,能去除90%浊度,部分COD,提高纳滤膜的抗污染性。
实验还考察了不同操作压力、时间、溶液pH值及温度对纳滤出水品质和通量的影响。
实验结果表明,两种纳滤膜的通量均随操作压力的升高而增加,并且在温度20-25℃和接近中性的pH值条件下都有较高的通量。
复合纳滤膜在耐温性能、一价和二价离子的区分程度、脱色效果以及膜的压密性能等方面要优于混合纤维素纳滤膜,但后者的抗污染性更好。
所选的两种纳滤膜对单一染料的截留都在98%以上,对实际废水的COD去除率可以达到80%,对色度可有效截留至少90%,膜的渗透液基本可以达到工业回用的目的,对印染行业的节能减排具有很好的实际应用价值。
最后对纳滤膜用清水进行低压水力冲洗,1#纳滤膜的通量恢复系数为82%,2#纳滤膜的通量恢复系数为91%,两张纳滤膜的通量都有很好的恢复。
同主题文章[1].王亚卿,李杰妹,赵仁兴. 多种超滤膜和纳滤膜在土霉素提取中的性能比较' [J]. 中国抗生素杂志. 2005.(01)[2].崔洪友. 膜分离处理印染废水研究进展' [J]. 世界科技研究与发展. 2006.(05)[3].唐淑娟,李然,刘桂英. 印染废水的脱色' [J]. 纺织科技进展.2005.(01)[4].梁雪梅,陆晓峰,王彬芳,许汝谟. 高分子纳滤膜的研究及进展' [J].功能高分子学报. 1999.(01)[5].宋玉军,孙本惠. 纳滤膜的制备方法' [J]. 化工新型材料. 1996.(04)[6].赵达玉,左勇. 超滤膜的污染与清洗保养' [J]. 四川食品与发酵. 2001.(02)[7].龙家杰,陆同庆. 印染废水治理中COD去除的研究现状与进展' [J]. 国外丝绸. 2002.(04)[8].宋玉军,孙本惠. 纳滤膜的应用' [J]. 化工新型材料. 1996.(03)[9].印染废水的常用脱色方法' [J]. 纺织信息周刊. 2005.(21)[10].周金盛,陈观文. 纳滤膜技术的研究进展' [J]. 膜科学与技术. 1999.(04)【关键词相关文档搜索】:环境工程; 印染废水; 超滤; 纳滤; 资源化回用【作者相关信息搜索】:浙江工业大学;环境工程;张国亮;丛纬;。
双膜法典型工艺流程
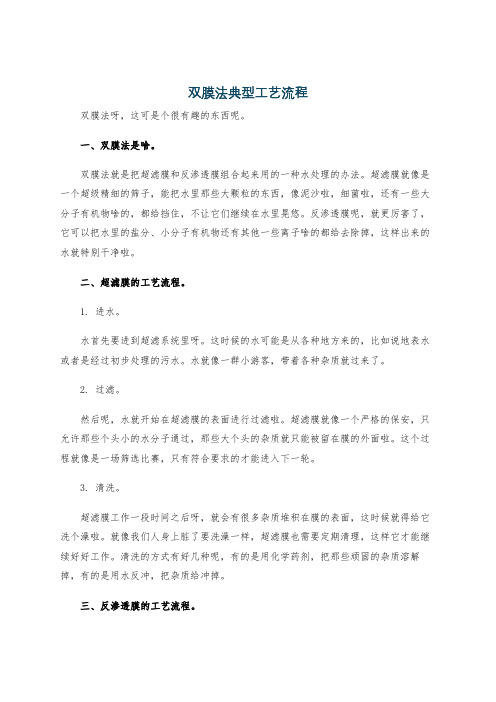
双膜法典型工艺流程双膜法呀,这可是个很有趣的东西呢。
一、双膜法是啥。
双膜法就是把超滤膜和反渗透膜组合起来用的一种水处理的办法。
超滤膜就像是一个超级精细的筛子,能把水里那些大颗粒的东西,像泥沙啦,细菌啦,还有一些大分子有机物啥的,都给挡住,不让它们继续在水里晃悠。
反渗透膜呢,就更厉害了,它可以把水里的盐分、小分子有机物还有其他一些离子啥的都给去除掉,这样出来的水就特别干净啦。
二、超滤膜的工艺流程。
1. 进水。
水首先要进到超滤系统里呀。
这时候的水可能是从各种地方来的,比如说地表水或者是经过初步处理的污水。
水就像一群小游客,带着各种杂质就过来了。
2. 过滤。
然后呢,水就开始在超滤膜的表面进行过滤啦。
超滤膜就像一个严格的保安,只允许那些个头小的水分子通过,那些大个头的杂质就只能被留在膜的外面啦。
这个过程就像是一场筛选比赛,只有符合要求的才能进入下一轮。
3. 清洗。
超滤膜工作一段时间之后呀,就会有很多杂质堆积在膜的表面,这时候就得给它洗个澡啦。
就像我们人身上脏了要洗澡一样,超滤膜也需要定期清理,这样它才能继续好好工作。
清洗的方式有好几种呢,有的是用化学药剂,把那些顽固的杂质溶解掉,有的是用水反冲,把杂质给冲掉。
三、反渗透膜的工艺流程。
1. 超滤水的再处理。
经过超滤膜过滤后的水,虽然已经去掉了很多杂质,但还是不够纯净呢。
这些水就会进入到反渗透膜系统里。
这时候的水就像是一个经过初步训练的小选手,要接受更严格的考验啦。
2. 反渗透过滤。
反渗透膜的过滤原理就更复杂一些啦。
它利用压力,让水从高浓度的一侧向低浓度的一侧流动,在这个过程中,盐分和其他小分子的东西就被截留下来了。
这就好比是在一个很窄的通道里,只有水分子这种身材瘦小的才能挤过去,那些胖胖的盐离子就只能被卡在外面啦。
3. 产品水和浓水。
经过反渗透膜过滤之后呀,就会产生两种水。
一种是产品水,这种水可干净啦,达到了很高的水质标准,可以直接用于很多地方,像工业生产中的一些对水质要求很高的环节,或者是作为生活饮用水。
印染废水深度处理及循环利用技术分析

印染废水深度处理及循环利用技术分析印染废水是指由印染工业过程中产生的废水,其主要污染特征包括高浓度的有机物、酸碱度变化大、色度高和含有大量的悬浮物等。
由于废水组成复杂、难以降解和处理困难,印染废水对环境造成了严重的污染。
为了实现印染废水的深度处理和循环利用,需要应用一系列的技术手段。
一、物理处理技术:1.滤料过滤:将印染废水通过不同孔径的滤网,利用滤重物理效应,去除废水中的悬浮物和颜料颗粒。
2.活性炭吸附:通过将废水与活性炭接触,利用活性炭对有机物的吸附作用,去除废水中的有机物。
3.膜技术:包括微滤、超滤、纳滤和反渗透等多种膜技术,通过膜孔径的选择,实现对废水中各种颗粒和溶解物质的有效分离,达到废水深度处理的目的。
二、化学处理技术:1.氧化法:利用氧化剂如过硫酸盐、高价铁盐等,将废水中的有机物氧化成无机物,从而实现有机物的降解。
2.沉淀法:通过添加适当的沉淀剂如氢氧化钙、聚合氯化铝等,使废水中的悬浮物和颜料颗粒迅速沉淀到废水底部。
3.中和法:通过添加酸碱试剂,调节废水的酸碱度,使废水中的酸碱度达到中性,进而提高废水的生物降解性。
三、生物处理技术:1.好氧生物处理:通过利用好氧菌的代谢能力,将废水中的有机物降解成二氧化碳和水等无害物质。
2.厌氧生物处理:通过利用厌氧菌的代谢能力,将废水中的有机物降解成甲烷等有用产物,实现资源的回收利用。
3.植物处理:利用水生植物如芦苇、菖蒲等,通过其吸收和降解的作用,将废水中的有机物和重金属等污染物去除或转化。
四、循环利用技术:1.膜技术回收:通过膜分离技术,将废水中的水分和溶解物质分离,实现废水的净化并回收水资源。
2.盐类回收:通过蒸发结晶或离子交换等方法,将废水中的盐类回收利用,例如生产工艺中需要的盐类或者是制备其他化学品。
3.余热回收:将废水中的热能通过换热器等设备进行回收,用于加热或供应生产工艺所需的热能。
综上所述,通过物理、化学、生物等多种处理技术的结合运用,可以有效实现印染废水的深度处理和循环利用。
总结双膜法海水淡化技术的技术工艺

总结双膜法海水淡化技术的技术工艺
双膜法海水淡化基本工艺流程为预处理(混凝沉淀+超滤)→反渗透脱盐工艺。
混凝沉淀工艺可以去除海水中大部分悬浮物质。
超滤采用外压式超滤膜,化学性质稳定,耐氯范围广,抗污染性强,易清洗,能将大部分不溶解物质及有机物去除。
反渗透采用聚丙烯酰胺复合膜,脱盐效果极好,单支膜元件脱盐率高达99%以上。
1.超滤工作原理
超滤膜孔径较小,且具有拦截能力,物理截留水中特定大小的杂质,从而实现将溶液中不同成分分离的目的。
2.反渗透工作原理
反渗透是在压力作用下,利用半透膜的选择性将溶质和溶剂分开。
用反渗透技术将海水中的胶体、细菌病毒等有害杂质去除,从而获得高品质淡水。
双膜法海水淡化技术特点
1.超滤膜和反渗透膜产水水质稳定可靠。
2.系统脱盐率高达99%。
3.通过不同等级的反渗透组合设计,能够满足用户不同要求。
4.通过能量回收装置,回收排水压力,降低海水淡化成本。
5.超滤和反渗透系统采用模块化设计,灵活性及可靠性高。
6.自动化程度高,运行维护简单方便。
7.通过开发低热源以及利用热电厂海水取排水设施,有效降低海水淡化成本。
印染废水双膜法(CMF—RO)深度处理及回用研究

印染废水双膜法(CMF—RO)深度处理及回用研究在水资源利用过程中,工业废水回收利用一直是企业技术革新的重要内容。
本文主要从印染废水膜处理技术角度出发,重点对双膜法(CMF-RO)深度处理技术以及相关运行成本进行了剖析,以供同行参考。
标签:废水处理;回用;印染废水双膜法1、引言水在印染行业中作为染料、药剂、助剂等的溶剂,漂洗织物也需要水,行业用水量大,随着水资源的日益短缺和水费不断上涨,该行业对废水的循环使用及回用提出了更高的要求,废水回用技术势必逐步推广。
要实现印染废水的大规模回用,需将废水回用至印染生产过程中,而印染生产用水对水质CODcr、色度、硬度、含盐量等有指标有较为严格的要求。
《纺织染整工业废水治理工程技术规范》(HJ471-2009)中给出指导性的意见:印染废水COD、色度、盐度较高,传统的处理技术难以满足回用的要求。
双膜技术是目前国际上研发和工程化应用的热点,作为一种有效的工程预处理手段,超滤可去除废水中大部分浊度和有机物,从而能减轻反渗透膜的污染,延长膜的使用寿命,减少膜工程的运行成本。
反渗透不仅能有效去除有机物、降低COD,而且具有优秀的脱盐效果。
出水品质能直接回用于印染环节。
2、印染废水膜处理技术2.1 超滤及微滤膜技术印染废水的深度处理一般在生化二级处理之后进行,而作为反渗透的预处理系统,连续膜过滤(CMF)可替代传统絮凝、机械过滤、精滤等RO膜前处理工艺,可有效去除水中的胶体、细菌、微生物、悬浮物等,污染指数(SDI)可小于3,大大减少设备的占地面积,系统产水水质搞并且水质稳定,在处理印染废水时优势十分明显,可以保證反渗透系统的长期连续运行并延长防渗透系统的使用寿命,是新一代的高效水处理系统工艺。
连续膜过滤(CMF)指的是,以微滤亦或超滤膜为中心,配备规格一致的管路与阀门,智能清洗体系,助剂添加体系与智能管控体系,构成一套能够完成连贯操作产水,在线膜清理体系,进而实现持续运行的目标。
MBR+RO双膜技术
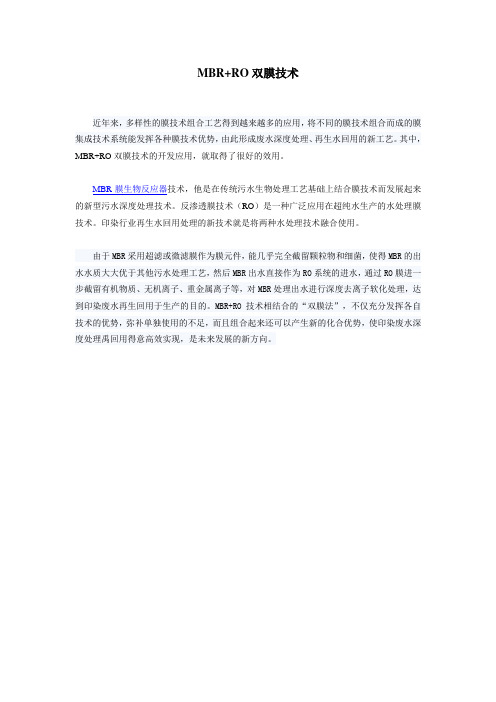
MBR+RO双膜技术
近年来,多样性的膜技术组合工艺得到越来越多的应用,将不同的膜技术组合而成的膜集成技术系统能发挥各种膜技术优势,由此形成废水深度处理、再生水回用的新工艺。
其中,MBR+RO双膜技术的开发应用,就取得了很好的效用。
MBR膜生物反应器技术,他是在传统污水生物处理工艺基础上结合膜技术而发展起来的新型污水深度处理技术。
反渗透膜技术(RO)是一种广泛应用在超纯水生产的水处理膜技术。
印染行业再生水回用处理的新技术就是将两种水处理技术融合使用。
由于MBR采用超滤或微滤膜作为膜元件,能几乎完全截留颗粒物和细菌,使得MBR的出水水质大大优于其他污水处理工艺,然后MBR出水直接作为RO系统的进水,通过RO膜进一步截留有机物质、无机离子、重金属离子等,对MBR处理出水进行深度去离子软化处理,达到印染废水再生回用于生产的目的。
MBR+RO技术相结合的“双膜法”,不仅充分发挥各自技术的优势,弥补单独使用的不足,而且组合起来还可以产生新的化合优势,使印染废水深度处理禹回用得意高效实现,是未来发展的新方向。
印染废水深度处理的主要技术工艺
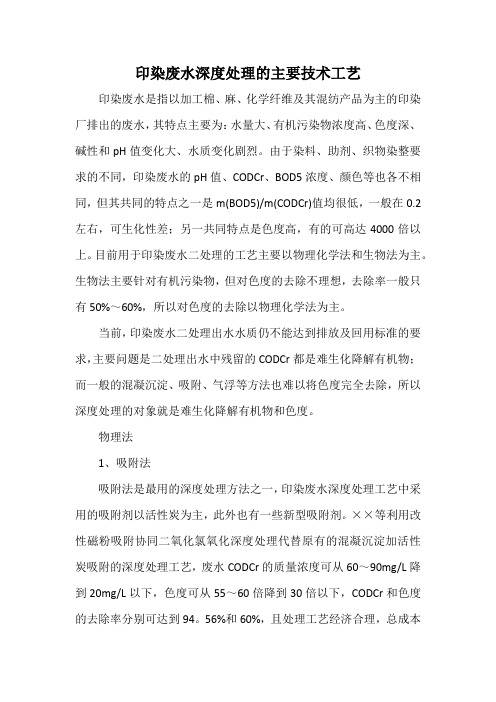
印染废水深度处理的主要技术工艺印染废水是指以加工棉、麻、化学纤维及其混纺产品为主的印染厂排出的废水,其特点主要为:水量大、有机污染物浓度高、色度深、碱性和pH值变化大、水质变化剧烈。
由于染料、助剂、织物染整要求的不同,印染废水的pH值、CODCr、BOD5浓度、颜色等也各不相同,但其共同的特点之一是m(BOD5)/m(CODCr)值均很低,一般在0.2左右,可生化性差;另一共同特点是色度高,有的可高达4000倍以上。
目前用于印染废水二处理的工艺主要以物理化学法和生物法为主。
生物法主要针对有机污染物,但对色度的去除不理想,去除率一般只有50%~60%,所以对色度的去除以物理化学法为主。
当前,印染废水二处理出水水质仍不能达到排放及回用标准的要求,主要问题是二处理出水中残留的CODCr都是难生化降解有机物;而一般的混凝沉淀、吸附、气浮等方法也难以将色度完全去除,所以深度处理的对象就是难生化降解有机物和色度。
物理法1、吸附法吸附法是最用的深度处理方法之一,印染废水深度处理工艺中采用的吸附剂以活性炭为主,此外也有一些新型吸附剂。
××等利用改性磁粉吸附协同二氧化氯氧化深度处理代替原有的混凝沉淀加活性炭吸附的深度处理工艺,废水CODCr的质量浓度可从60~90mg/L降到20mg/L以下,色度可从55~60倍降到30倍以下,CODCr和色度的去除率分别可达到94。
56%和60%,且处理工艺经济合理,总成本为1.053元/t。
××利用超声波-活性炭联合法对印染废水生化出水进行深度处理,CODCr去除率可达89.6%,出水CODCr的质量浓度小于25mg/L。
××等研究并比较了混合炭、原煤炭和果壳炭3种不同材质的活性炭对印染废水生化出水的吸附容量,在活性炭床中,当进水CODCr的质量浓度为75~101mg/L时,出水CODCr浓度可以稳定达到GB4287—92《纺织染整工业水污染物排放标准》一标准的要求。
- 1、下载文档前请自行甄别文档内容的完整性,平台不提供额外的编辑、内容补充、找答案等附加服务。
- 2、"仅部分预览"的文档,不可在线预览部分如存在完整性等问题,可反馈申请退款(可完整预览的文档不适用该条件!)。
- 3、如文档侵犯您的权益,请联系客服反馈,我们会尽快为您处理(人工客服工作时间:9:00-18:30)。
印染废水深度处理超滤/反渗透双膜法工艺
纺织印染业是我国排放废水量较大的工业行业。
印染废水的水质特点为高色度、高化学需氧量、高pH、高盐度、高硬度、低可生化性等,其有机污染负荷大,是一类难处理的工业废水。
在水资源日益匮乏、环保要求日益严格的形势下,提高水回用率、减少新鲜水使用、降低废水排放量势在必行。
常见的印染废水处理方法主要有物理化学法、化学法和生物法。
在实际应用中,由于印染废水水质复杂,使用单一处理方法通常很难获得理想的处理效果,因此,印染废水处理常采用多种技术的组合,以取得最佳净化效果。
尽管如此,目前印染废水的出水水质仍难达到废水排放标准和满足回用要求。
膜技术是新近迅速崛起的一项高新技术。
先进的膜技术产水水质好,能直接回用于印染环节。
近年来,以膜生物反应器(MBR)、超滤(UF)、反渗透(RO)为深度处理核心路线的膜法水处理技术日益得到推广应用。
选择UF/RO双膜法,以印染废水厌氧/好氧(A/O)工艺的二沉池出水为研究对象,进行膜工艺参数优化和污染物去除研究,旨在为膜设备在印染行业的应用与推广提供借鉴与参考。
1、材料与方法
1.1 材料
超滤膜,聚偏氟乙烯(PVDF)材质,1.2m3h-1,BW400-FR反渗透膜,美国陶氏(DOW)。
1.2 印染废水
试验用水系绍兴某染整有限公司A/O工艺的二沉池出水。
水质指标如下:温度23~26℃,pH值6.8~9.5,色度32倍,浊度5.93NTU,全盐量2.53×103mgL-1,悬浮物(SS)含量12mgL-1,化学需氧量(CODCr)219mgL-1,总氮(TN)含量8.14mgL-1,总磷(TP)含量0.383mgL-1,氨氮含量2.79mgL-1。
1.3 膜集成设备
膜系统集成在一个机架当中,分为超滤系统和反渗透系统2个子体系。
各子体系可以单独运行,亦可同时连续运行。
装置处理量为2~5m3d-1。
超滤膜的主要运行参数如下:进水压力,0.02~0.04MPa,产水压力,0~0.02MPa,进水流量,1.2m3h-1,产水流量,1.1m3h-1,反冲压力,0~0.04MPa,反冲流量,1.5m3h-1。
反渗透膜的主要运行参数如下:进水压力,0.99~1.05MPa,浓水压力,0.94~1.01MPa,循环流量,0.85~1.10m3h-1,产水流量,0.012~0.264m3h-1,产水TDS(总溶解性固体物质),6.39mgL-1。
2、结果与分析
2.1 膜集成设备通量变化
为了了解膜集成设备的通量变化,在运行初期监测膜通量随运行压力的变化,结果如图1所示。
可以看出,膜通量随运行压力的增加而变大,但考虑到对膜的损伤,以及对膜污染、膜生产参数、脱盐率等的影响,最终确定运行压力为1MPa,此时膜系统的产水量为4.6m3d-1,可满足试验设计。
2.2 膜集成设备的运行效果
2.2.1 电导率变化
如图2所示,生化水的电导率为 3.60~3.63mScm-1,UF产水的电导率为4.16~4.18mScm-1,RO产水的电导率为0.035~0.037mScm-1。
UF产水的电导率高于生化水电导率。
这可能与超滤膜系统前端利用加药系统投加了NaClO药剂,但超滤膜系统对NaClO 并没有拦截能力有关。
RO系统对生化水电导率的去除率平均达99.0%以上。
2.2.2 色度变化
如图3所示,生化水的颜色为棕色,色度30~34倍,UF产水的色度为13~16倍,RO 产水的色度在46.7%~56.7%,RO工艺对色度的去除率在96.9%~97.7%。
超滤膜的截留分子量在10万u,而色素分子量较小,极易通过超滤膜。
RO系统对色度有比较稳定、明显的去除效果。
这是因为反渗透膜具有致密的结构,化学性质稳定,能够高效截留色素分子。
2.2.3 浊度变化
如图4所示,生化水的浊度为5.86~5.95NTU,UF产水的浊度为0.58~0.60NTU,RO产水的浊度为0.20~0.22NTU。
UF工艺对浊度的去除率为90.1%,RO工艺对浊度的去除率为96.5%。
在双膜法处理过程中引进超滤技术,其关键作用体现在可以截留绝大部分的非溶解性杂质,为反渗透的常规可靠运行打下良好基础。
本设备超滤系统在运行过程中浊度维持在0.60NTU以下,可满足反渗透进水对浊度的要求。
2.2.4 SS含量变化
如图5所示,生化水的SS含量为10~12mgL-1,UF产水的SS含量为1.0~1.2mgL-1,RO产水的SS含量为0.12~0.15mgL-1。
UF工艺对SS的去除率在89.0%~91.7%,超滤主要能截留0.05~0.2μm的颗粒和杂质,有效阻挡胶体、蛋白质、微生物和大分子有机物。
RO 工艺对SS的去除率在98.6%~99.0%。
2.2.5 COD变化
如图6所示,生化水的CODCr为210~230mgL-1,UF产水的CODCr为200~207mgL-1,RO产水的CODCr为18~23mgL-1。
UF工艺对CODCr的去除率在4.8%~10.4%,RO工艺对CODCr的去除率在89.5%~91.4%。
本系统中UF对COD的截留作用不太理想,但反渗透膜可截留纳米级、相对分子质量仅数百的颗粒,去除废水中的小分子溶解性CODCr,从而使得系统对CODCr的总去除率达到90%左右,产水COD始终保持稳定,保证了产水水质。
2.2.6 TN含量变化
如图7所示,生化水的TN含量为7.96~8.05mgL-1,UF产水的TN含量为5.25~5.50mgL-1,RO产水的TN含量为 4.60~4.65mgL-1。
UF工艺对TN的去除率在31.4%~34.5%,RO工艺对TN的去除率在41.9%~43.9%。
2.2.7 氨氮含量变化
如图8所示,生化水的氨氮含量为 2.75~2.80mgL-1,UF产水的氨氮含量为0.61~0.68mgL-1,RO产水的氨氮含量为0.32~0.37mgL-1。
UF工艺对氨氮的去除率在75.5%~78.1%,RO工艺对氨氮的去除率在86.6%~89.2%。
本研究中所用的超滤系统对氨氮这样的小分子在理论上是没有截留效果的,推测氨氮可能是与悬浮物一起被超滤膜去除,具体的机理有待进一步研究。
2.2.8 TP含量变化
如图9所示,生化水的TP含量为0.35~0.38mgL-1,UF产水的TP含量为0.23~0.28mgL-1,RO产水的TP含量为0.11~0.15mgL-1。
UF工艺对TP的去除率在26.3%~39.5%,RO工艺对TP的去除率在63.2%~71.1%。
2.2.9 盐分含量变化
如图10所示,生化水的盐分含量为2.53~2.56gL-1,UF产水的盐分含量为2.97~3.00gL-1,RO产水的盐分含量为0.025~0.028gL-1。
UF产水的盐分含量高于生化水,与电导率的变化趋势基本相同。
这是因为超滤膜系统前端利用加药系统投加了NaClO药剂,但超滤膜系统对NaClO没有拦截能力,氯酸钠发生反应后生成了氯化钠。
在整个运行周期内,RO系统的脱盐率基本维持稳定,平均脱盐率达99.0%。
脱盐率、产水量与跨膜压差是常用的评价RO 工艺运行性能的主要指标。
本试验中,RO膜元件基本完整,未出现破损现象。
脱盐率与RO膜污堵程度不直接相关,这与Tan等的研究结果一致。
2.3 膜设备运行成本
该中试设备在运行过程中每天设备耗电24kWh,按每天处理量 4.6m3、电费0.70元(kWh)-1计,折合处理费用为3.6元m-3。
膜组件杀菌选用NaClO溶液,酸洗选用药剂为柠檬酸,膜组件清洗费为0.2元m-3。
以设备使用年限10a、膜更换周期3~5a计,折合设备成本为0.5元m-3。
总运行成本4.3元m-3。
3、小结
选择UF/RO双膜法集成膜设备,针对印染废水A/O工艺的二沉池出水,进行了膜工艺参数优化和污染物去除研究。
装置处理量为4.6m3d-1,总运行成本为4.3元m-3。
超滤+反渗透系统对电导率的平均去除率为99.0%,对色度的平均去除率为97.2%,对浊度的平均去除率为96.5%,对SS的平均去除率为98.8%,对CODCr的平均去除率为90.3%,对TN的平均去除率为42.6%,对氨氮的平均去除率为87.5%,对TP的平均去除率为65.0%,平均
脱盐率为99.0%。
各项水质分析结果均满足GB4287—2012《纺织染整工业水污染物排放标准》和GB/T19923—2005《城市污水再生利用工业用水水质》的限量要求。
(。