印染废水的膜法回用技术
印染废水深度处理回用及零排放技术

国家规定
有关印染废水的相关规定和存在的问题
水资源缺乏
降低成本
《印染行业准入条件(2010年修订版)》规定,印染企业要“实行生产排水清浊分流、分质处理、分质回用,水重复利用率要达到35%以上。”
水资源紧张,七大水系遭受不同程度污染,目前在全国640多个城市中,缺水城市已达300多个,其中严重缺水城市达108个。
印染废水深度处理回用零排放的思考
Fig. 4
印染废水经深度处理后可完全实现大部分回用; 臭氧-BAF工艺深度处理印染废水可实现出水COD<40mg/L, 色度<10倍,可实现高标准达标排放或初级回用要求。 膜分离的淡水可有效过滤生化出水有机物、色度、SS和无机盐等组分;它可用于高级回用,可作为锅炉用水,甚至做纯水。 反渗透浓水浓水含盐,有机杂质等,能不能做到既回用浓水的水,又回用浓水中的盐?
排污费成本逐年增加,自来水费用上涨,印染废水处理回用可减少排污费用,降低用水成本。
印染废水处理回用工艺
印染废水
水解酸化
物化混凝
好氧处理
UF+RO
臭氧催化氧化+一体化臭氧-BAF
淡水
浓水
石灰苏打
Fenton/PS氧化
常规处理
达标排放
(COD<40 mg/L,色度<10倍)
深度处理
普通回用水
优质回用水
互太(番禺)纺织印染废水深度处理工程(40000t/d)
规模:40000t/d 工艺:臭氧催化氧化+曝气生物滤池 配套资金:3000万 实施阶段:已完成设计,正在报建
广东溢达纺织印染废水深度处理工程(25000t/d)
规模:25000t/d 工艺:臭氧催化氧化+曝气生物滤池 实施阶段:已经调试运行,处理效果良好
印染废水回用处理工艺

印染废水回用处理工艺纺织印染行业废水具有排放量大、水质变化大、有机物浓度高、色度高等特点,其处理相对复杂.近年来,由于水资源的紧缺,众多环保学者在印染废水回用领域进行了大量研究.为了保证印染废水出水的稳定达标和中水回用,双膜法成为印染废水处理领域深度处理最为常用的处理技术,研究表明,全国75%以上的印染企业利用双膜法作为深度处理技术.双膜法技术包括超滤和反渗透(RO)两种膜处理技术.RO出水包括淡水和浓水,其中,淡水可直接排放或完全回用于印染工序,浓水由于盐度高、含一定浓度的难降解有机物和硬度,不仅不能直接排放,而且处理相当困难.目前,针对印染反渗透浓水(ROC)的主要处理措施有直接排放处理、回流二次处理和膜蒸馏技术.直接排放处理一般是指直接排入海洋,是最为常用的浓水处理技术,但此技术受到地理位置限制,在广大内陆等离海岸较远的地区不宜推广.回流二次处理是指将浓水回流至水处理系统的前处理段,再次进入水处理系统进行二次处理,这样使浓水中的难降解有机物和高盐度物质得不到外排,长期回流会导致生化系统盐分逐渐积累,微生物活性降低并最终导致生物处理系统的崩溃.膜蒸馏技术是一种膜技术与蒸馏技术相结合的膜分离技术,可以实现浓水和盐分的完全回收,但该技术耗能太高,大部分企业很难承受.另外,汪晓军等采用Fenton氧化结合石灰苏打处理印染ROC,实现了印染ROC 的完全回用,但由于Fenton氧化技术处理过程中有可能带入印染需严格限制的Fe2+,因此,需要后续设置絮凝沉淀池以完全去除出水中的Fe2+.鉴于现有各浓水处理工艺的不足,亟需开发一种新的处理工艺解决地理位置受限、处理成本过高及处理工艺复杂等难题.过硫酸盐(PS)氧化作为一种新型的高级氧化技术近年来在环境领域逐渐受到研究人员的关注.在常温条件下,PS是一种较为温和的氧化剂,反应速率较慢.当PS受到外界条件如热、微波、过渡金属离子作用时容易被活化,产生氧化性更强的硫酸根自由基(SO· -4),其标准氧化还原电位E0=2.60 V,高于PS的E0=2.01 V.相应的反应原理如下:pH对PS降解有机物有一定的影响,杨照荣等的研究表明,PS的氧化能力在碱性条件下比酸性和中性条件下较强,因为在碱性条件下硫酸根自由基会生成氧化能力更强的羟基自由基(· OH,E0=2.80 V),反应如下:除pH外,初始PS投加量、反应温度都是影响PS氧化反应的重要影响因素.PS 氧化镇痛药(立痛定)的研究表明,有机物的氧化速率在一定初始PS范围内随初始PS用量的增加而加快.温度的提升大大提高了PS分解垃圾渗滤液中腐殖酸的速率,温度从90 ℃上升到150 ℃时,有机物去除率从63.5%上升到76.0%,温度继续上升到170 ℃,有机物去除率上升到78.8%.石灰苏打软水技术是废水处理领域最为传统的脱硬度技术.印染用水中硬度过高会造成染料在染色织物表面分配的不均匀性,同时降低染色织物的色牢度,是印染回用水严格规定的水质指标.采用石灰软化和微滤工艺处理某热电厂的循环冷却排污水的研究表明,石灰软化可大大降低废水的硬度和碱度,出水完全满足回用要求.本研究结合印染ROC水质特点及印染回用时需补充大量硫酸钠作为印染助剂的要求,将PS氧化和石灰苏打软水技术联合应用于印染ROC处理过程中.首先利用条件实验和正交试验研究PS氧化去除印染ROC难降解有机物的影响因素,包括反应pH、初始PS投加量和反应温度等条件,研究有机物降解的动力学模型;其次分析PS氧化前后无机组分和有机组分;最后确定石灰苏打脱硬度的最佳的石灰和苏打药剂投加量组合.2 材料与方法2.1 印染废水ROC印染ROC取自佛山市西樵镇某纺织有限公司,废水总排放量60000 m3 · d-1,ROC排放量约20000 m3 · d-1.原水水质:CODCr为112.5 mg · L-1,BOD5/CODCr 为0.05,TOC为34.0~35.6 mg · L-1,SO42约9600 mg · L-1,CO32约1500 mg · L-1,Cl-约650 mg · L-1,pH为8.3~8.8.2.2 主要仪器和药品pHs-3c便携式pH计(上海精密科学仪器有限公司);COD快速密闭消解测定仪(广东,韶关);BOD测定仪(美国,HACH);电子天平,恒温振荡器(上海精密科学仪器有限公司);离子色谱仪ICS-1600(美国,戴安);TOC测定分析仪TOC-LCPH/CPN(日本,岛津);PS、磷酸二氢钠、石灰和苏打等药剂均为分析纯(天津科密欧化学试剂有限公司).。
印染废水回用方案
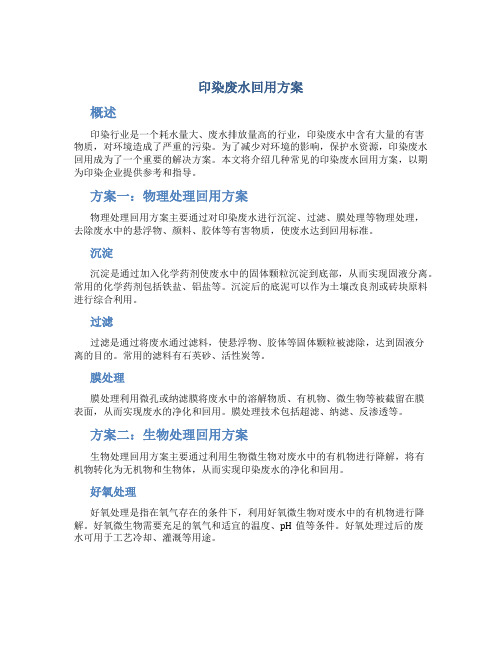
印染废水回用方案概述印染行业是一个耗水量大、废水排放量高的行业,印染废水中含有大量的有害物质,对环境造成了严重的污染。
为了减少对环境的影响,保护水资源,印染废水回用成为了一个重要的解决方案。
本文将介绍几种常见的印染废水回用方案,以期为印染企业提供参考和指导。
方案一:物理处理回用方案物理处理回用方案主要通过对印染废水进行沉淀、过滤、膜处理等物理处理,去除废水中的悬浮物、颜料、胶体等有害物质,使废水达到回用标准。
沉淀沉淀是通过加入化学药剂使废水中的固体颗粒沉淀到底部,从而实现固液分离。
常用的化学药剂包括铁盐、铝盐等。
沉淀后的底泥可以作为土壤改良剂或砖块原料进行综合利用。
过滤过滤是通过将废水通过滤料,使悬浮物、胶体等固体颗粒被滤除,达到固液分离的目的。
常用的滤料有石英砂、活性炭等。
膜处理膜处理利用微孔或纳滤膜将废水中的溶解物质、有机物、微生物等被截留在膜表面,从而实现废水的净化和回用。
膜处理技术包括超滤、纳滤、反渗透等。
方案二:生物处理回用方案生物处理回用方案主要通过利用生物微生物对废水中的有机物进行降解,将有机物转化为无机物和生物体,从而实现印染废水的净化和回用。
好氧处理好氧处理是指在氧气存在的条件下,利用好氧微生物对废水中的有机物进行降解。
好氧微生物需要充足的氧气和适宜的温度、pH值等条件。
好氧处理过后的废水可用于工艺冷却、灌溉等用途。
厌氧处理厌氧处理是指在缺氧或无氧条件下,利用厌氧微生物对废水中的有机物进行降解。
厌氧微生物能够将有机物转化为可再生能源如甲烷等。
并且厌氧处理不需要额外供氧,可以节约能源。
厌氧处理后的废水可用于工艺冷却、灌溉等用途。
方案三:化学处理回用方案化学处理回用方案主要通过加入化学药剂对废水中的有害物质进行沉淀、吸收或中和,达到净化废水的目的。
氧化氧化是指将废水中的有机物转化为无机物的过程。
常用的氧化剂有过氧化氢、高锰酸钾等。
氧化后的废水可以用于工艺冷却、灌溉等用途。
吸附吸附是通过将废水通过吸附剂,使有机物、颜料等物质被吸附到吸附剂表面,达到废水净化的目的。
印染废水的回用

印染废水的回用本文摘自杭州宏阳净水材料有限公司网站。
现有的印染废水回用技术往往是在印染废水达标排放的基础上,对原水(废水处理设施的出水)进行三级处理,由于原水成分复杂,不稳定,很难形成一种规范性、普适性的回用技术路线。
各企业要根据企业回用水质的要求,选择具体的深度处理工艺或者集成工艺。
常用的回用处理工艺有:混凝、过滤、高级氧化、活性炭吸附、膜分离技术、离子交换法等。
单独的回用工艺存在各自缺陷,如臭氧氧化技术处理后的水并不能直接回用于生产,原因是此技术在降低废水中的难降解有机物分子量时,废水COD往除率并不高,脱色效果好,但并不往除溶解性污染物和盐份。
(1)印染废水物化处理(混凝沉淀)生化处理组合(内循环厌氧+HCR/生物活性炭+接触氧化)纤维球过滤回用将各种生物处理单元(包括厌氧、缺氧、好氧、高级好氧等)进行组适用于生化处理是一种发展趋势。
可以采用两种生物处理工艺,即将高效好氧工艺(HCR)法与生物活性炭法(PACT)相结合,进步了反应器中氧的利用率,增强了抗冲击负荷能力,进步了处理效率。
该工艺后处理采用纤维球对原水进行过滤,过滤速度快、效果好,回用水质稳定。
经过生产性试验表明,回用水用于皂洗是可行的,其回用水水洗后的布样色光、深度与自来水洗后的一致。
(2)印染废水二级生化处理化学絮凝离子交换回用用流体床生物膜反应器结合化学絮凝和离子交换法对印染废水进行深度处理。
试验表明,整个集成工艺的CODcr和色度往除率分别达到95.4%和98.5%,该工艺出水可回用到印染所有工序中,但该方案为了降低铁离子浓度和电导率,对离子交换树脂的依靠性较大,这难免会进步离子交换树脂的再生频率。
(3)印染废水二级生化处理二氧化氯氧化(臭氧和其它高级氧化技术)过滤或者吸附回用二级生化出水后采用氧化技术结合活性炭吸附工艺是当前印染废水回用技术经常考虑的工艺。
氧化对废水脱色非常有效,可把复杂的染料大分子转化成了有机小分子,但过程中对CODCr往除非常有限。
印染废水深度处理及回用技术研究

印染废水深度处理及回用技术探究一、引言随着纺织业的迅猛进步,印染工艺成为了纺织企业中不行或缺的环节。
然而,印染工艺所产生的废水污染对环境造成了严峻的影响。
传统的印染废水处理技术虽然能够将有机污染物去除,但却无法有效地处理高浓度的色素和盐类物质。
为了解决这一问题,探究者们不息探究新的深度处理和回用技术,以实现印染废水的经济高效处理和资源化利用。
二、印染废水特性与传统处理技术1. 印染废水特性印染废水的主要特性为高浓度、高COD、高色度以及含有大量的盐类物质。
其中,色素是印染废水中的主要污染物之一,不仅造成水体颜色混浊,还对生态环境造成影响。
另外,印染废水中含有的盐类物质对传统的生物处理工艺具有抑止作用,导致处理效果不佳。
2. 传统处理技术传统的印染废水处理技术主要包括物理、化学和生物处理方法。
物理处理方法包括有机物去除、固体分离和膜技术等,能够有效去除废水中的悬浮物和颜料。
化学处理方法主要是利用化学药剂对废水进行净化,如混凝剂和氧化剂等。
生物处理方法则是利用微生物对有机污染物进行降解和转化。
然而,传统处理技术对高浓度色素和盐类的处理效果有限,且处理成本较高。
三、印染废水深度处理技术为了解决传统处理技术对高浓度色素和盐类的处理问题,探究者们提出了一系列深度处理技术。
1. 高级氧化技术高级氧化技术是利用强氧化剂对废水中的有机污染物进行降解。
常用的高级氧化技术包括臭氧氧化、过氧化氢氧化以及光催化氧化等。
这些技术能够将废水中的有机物转化为二氧化碳和水,达到高效降解的效果。
2. 生物分类技术生物分类技术是在生物处理的基础上,融合了分离与富集技术,通过对微生物的富集分类,实现对印染废水中的有机物的高效降解。
该技术利用了微生物的生理特性,提高了有机物的降解能力。
3. 膜技术膜技术是一种物理处理技术,通过膜的选择性透过性,将废水中的有机物、颜料和盐类物质分离。
常用的膜技术包括微滤、超滤、逆渗透和纳滤等。
膜技术能够高效去除废水中的悬浮物和有机物,同时保留水中的无机盐,实现废水的回用。
印染废水膜法回用中的问题及对策

印染废水膜法回用中的问题及对策所属行业: 水处理关键词:印染废水 MBR 膜法水处理印染废水具有水量大、污染物含量高、色度大、生化性差和水质变化大等诸多特点,处理难度高[1-4]。
GB4287—2012《纺织染整工业水污染物排放标准》的颁布实施,以及产业升级、水价提升和排放总量控制等措施陆续出台,要求印染企业必须对废水进行深度处理及回用。
目前,以MBR (膜生物反应器)、UF(超滤)和RO(反渗透)为深度处理核心路线的膜法水处理技术日益得到推广应用[5-6]。
但由于各种原因,这类膜法水处理系统在使用过程中出现多种问题,很多印染企业甚至对该技术的可靠性和有效性产生怀疑。
其实,绝大多数问题并非出自膜技术本身,而是设计施工方或运行管理方所致,包括对膜法水处理存在很多技术性误解等。
1关键问题及解决方案1.1膜系统处理能力下降膜系统运转一段时间后,有时处理能力明显下降,达不到设计产能。
产生这种现象的原因主要与膜系统工作环境、选型设计、安装施工、运行管理和膜产品性能等有关。
此外,与膜系统(MBR、UF或RO)本身也有一定关系。
(1)工作环境印染废水水温低于设计温度(常见于季节性变化),会导致膜出水性能下降;水质中污染物种类、浓度和水体黏度的变化,也会导致膜的透水性能低于预期值。
解决这些问题,需要在膜系统设计之初,考虑全年最低水温和水质的波动幅度,在选膜面积时留出一定的安全余量。
(2)选型设计由于设计经验不足,过多考虑成本导致选用的膜面积安全余量不足,对膜的产水通量估计过高等,都会使膜达不到设计产能。
无论是MBR膜、UF膜还是RO膜,都必须保证足够的膜面积。
需按照稳定膜通量而非初始通量来进行选型设计。
压力不足、流体分布不均,导致水流或气流偏流,也会影响整体膜性能,对于UF系统和RO系统更是如此。
对于RO系统,膜面流速过低,会导致污染物沉积,引起堵塞。
解决的方法是改善泵、水路和气路设计,使多组膜能均担处理负荷,避免部分膜超负荷产水,而部分膜未发挥作用。
印染废水回用方案

印染废水回用方案
随着环保意识的日益增强,印染废水处理成为了一个重要的问题。
而废水回用则成为了解决废水排放问题的有效途径之一。
以下是一份印染废水回用方案:
1. 废水预处理:将印染废水经过初步处理,如沉淀、过滤等,
去除其中的颜料、悬浮物等大颗粒物质。
2. 生物处理:将经过预处理的印染废水送入生物处理系统中。
通过微生物的代谢作用,去除其中的有机物质和氨氮等有害物质,将其转化为无害的水、气和泥。
3. 色度去除:经过生物处理的印染废水中可能还存在着一定的
色度,需要采用化学方法进行去除。
一般采用氧化剂或还原剂将颜料氧化或还原成无色物质。
4. 活性炭吸附:用活性炭对去色后的印染废水进行进一步处理,吸附其中的有机物和残余颜料等,达到净化的目的。
5. 膜分离:最后将活性炭吸附后的印染废水进行膜分离,去除
其中的微量杂质,以达到回用标准。
6. 回用:将经过膜分离的印染废水用于印染工艺中,实现废水
零排放。
以上是一种较为常见的印染废水回用方案,但不同的行业、企业面临的废水问题不同,因此具体的回用方案需要根据实际情况进行选择和制定。
- 1 -。
纺织染整废水中的染料分离与回用技术

纺织染整废水中的染料分离与回用技术随着全球纺织工业的飞速发展,纺织染整作为产业链中的重要环节,其产生的废水量巨大且含有大量难以降解的染料和其他化学物质,给水环境造成了严重负担。
因此,开发高效的染料分离与回用技术,对于推动纺织行业的可持续发展和保护生态环境具有重要意义。
本文将从六个方面探讨纺织染整废水中的染料分离与回用技术。
一、物理法分离技术物理法是废水处理的初级阶段,主要利用物理原理去除废水中的悬浮物和部分大分子染料颗粒。
常用的物理方法包括沉淀、过滤和浮选等。
沉淀可去除重力作用下沉的较大颗粒;过滤则通过物理屏障截留细小颗粒和部分溶解态染料;而浮选技术,特别是气浮法,通过气泡携带染料颗粒上浮,实现固液分离,特别适用于疏水性染料的去除。
二、化学法处理技术化学处理技术通过化学反应改变废水中的污染物性质,使之易于去除。
混凝法是一种典型的化学处理方式,通过投加混凝剂形成絮状沉淀,吸附废水中的染料分子及其他杂质。
此外,高级氧化工艺如芬顿反应、臭氧氧化和电化学氧化等,能产生强氧化性的自由基,有效分解难降解的有机染料,提高废水的可生化性。
三、生物处理技术生物处理技术利用微生物的代谢作用降解废水中的有机物,包括活性污泥法、生物膜法和厌氧消化等。
针对染整废水的特殊性,常采用组合工艺,如A/O(好氧/厌氧)或SBR(序批式活性污泥法),强化对难降解染料分子的生物降解能力。
通过优化微生物种群和操作条件,可以有效提高处理效率,实现污染物的矿化。
四、膜分离技术膜分离技术是基于选择透过性原理,通过半透膜分离废水中不同分子大小的物质。
纳滤、反渗透和超滤等技术在染整废水处理中得到广泛应用,能有效截留染料分子和其他有机污染物,实现高纯度的水回收。
然而,膜污染问题限制了其长期运行效率,需配合有效的预处理和膜清洗策略。
五、吸附法吸附是一种简单有效的废水处理方法,通过固体吸附剂表面的物理或化学作用力吸附染料分子。
活性炭是最常见的吸附剂,但由于成本和再生问题,研究转向了低成本、易再生的天然材料,如改性黏土、生物质(木屑、果壳)、纳米材料等。
- 1、下载文档前请自行甄别文档内容的完整性,平台不提供额外的编辑、内容补充、找答案等附加服务。
- 2、"仅部分预览"的文档,不可在线预览部分如存在完整性等问题,可反馈申请退款(可完整预览的文档不适用该条件!)。
- 3、如文档侵犯您的权益,请联系客服反馈,我们会尽快为您处理(人工客服工作时间:9:00-18:30)。
印染废水的膜法回用技术
2008年 9月 4日慧聪网
在全国各工业行业中,废水排放量居前5 位的行业为造纸业、化工制造业、电力业、黑色金属冶炼业和纺织印染业,其中纺织印染业废水排放量占全国工业废水统计排放量的7.5%,其废水排放总量居全国工
业行业第五位,总量为14.13 亿吨每年,其中印染废水约为11.3 亿吨(占纺织印染业废水的80%),约占全国工业废水排放量的6%,每天排放量在300-400 万吨。
印染污染物大多是难降解的染料、助剂和有毒有害的重金属、甲醛、卤化物等。
每排放1 吨印染废水,
就能污染20吨水体。
加入WTC后,纺织印染近几年均以两位数增长,但污染物处理设施难以同步,污染物排放总量有增加趋势。
目前全国印染废水处理设施总投资超过百亿元人民币。
在我国工业行业的四大重点COD非放行业中,纺织印染业的COD非放量位居第四位。
造纸、食品行业
的COD非放比重逐年下降,而纺织印染和化工行业的COD非放比重逐年上升,其中纺织印染业的比重从4.7%
上升到5.6%。
可以看出,纺织印染行业的废水存在“水量大、COD非放总量大、废水处理困难”等诸多特点。
2.印染废水进行再利用的必要性
印染废水是以有机污染为主的成分复杂的有机废水,处理的主要对象是BOD5不易生物降解或生物降
解速度缓慢的有机物、碱度、染料色素以及少量有毒物质。
虽然印染废水的可生化性普遍较差,但除个别特殊的印染废水( 如纯化纤织物染色)外,仍属可生物降解的有机废水。
其处理方法以生物处理法为主,同
时需辅以必要的预处理和物理化学深度处理。
预处理工艺主要包括调节、中和、废铬液处理与染料浓脚水预处理等;而生物处理工艺主要为好氧法,目前采用的有活性污泥法、生物接触氧化法、生物转盘和塔式生物滤池等。
为提高废水的可生化性,缺氧、厌氧工艺也已应用于印染废水处理中。
常用的物化处理工艺主要是混凝沉淀法与混凝气浮法。
此外,电解法、生物活性炭法和化学氧化法等有时也用于印染废水处理中。
但通过此类工艺处理的纺织印染废水,最多只能达标排放,不可能达到回用水水质标准作为纺织印染的工艺用水。
而作为回用的工艺用水,对水质指标特别是有机物、色度、硬度等指标有更为严格的要求.
2) 原水硬度在150-325mg/L 之间,大部分可用于生产,但溶解性染料应使用小于或等于17.5mg/L 的软水,皂洗或碱液用水硬度最高为150mg/L;
3) 喷射冷凝器冷却水一般采用总硬度小于或等于17.5mg/L 的软水。
对大部分企业进行实际水质检测的分析结果表明,经处理后达到排放标准的染色废水,由于含有染料、表面活性剂、胶质、软水剂、退浆废水、碱减量废水等的各类无机、有机残余物,水中含盐量往往达到1000mg/L
以上,总硬度也远高于150mg/L,而且硬度组成成分均是用普通的石灰法等难以去除的永久硬度。
因此,即使生化后通过常规加药能将色度去除大部分,该类水如未经脱盐处理,也不可能满足现印染工艺用水的质量要求。
由于工业化发展带来水环境的持续恶化,水资源的日益缺乏使国家对环保节水问题日益重视,目前江浙、广东一带等印染加工业集中地区、北方部分缺水地区,已普遍提高了废水处理排放标准;对印染企业的废水排量也进行严格限制,取水资源费、污水排放费也开始大幅提升。
环保要求的提高已使部分地区印染企业的产能扩张面临着严重的威胁,因此,可以毫不夸张地说,今后对水资源如何进行有效再利用将成为企业发展的生命线。
在此基础上,如何采用水处理新技术不断提升再利用的安全性与经济性已成为目前大部分印染企业都开始重点关注的课题。
3.全膜法工艺介绍
针对目前印染企业已有的废水生化处理工艺及实际工艺用水情况,在保证用水水质安全稳定的前提下,充分考虑投资与运行成本的经济性,我们建议采用先进的膜分离技术,采用膜法工艺对企业的排放废水进行全部或部分处理后再利用,其产水既可以完全达到纯水标准,满足中高档产品的生产工艺需要;同时,在兼顾投资的基础上,建议企业根据实际情况,可以进行分步实施;部分企业如工艺用水硬度及电导率要求不高,可将反渗透纯水与部分预处理超滤膜出水勾兑在一起使用,以最大程度地节约用水成本。
膜法的废水再利用主要包括“超滤膜+反渗透膜”的工艺流程,超滤是以压力为驱动的膜分离过程,它
能够将颗粒物质从流体及溶解组份中分离出来。
超滤膜的典型孔径在0.01〜0.1微米之间,对于细菌和大
多数病菌、胶体、淤泥等具有极高的去除率。
应用在印染废水的再处理流程中,超滤膜除对有机物及色度有一定的去
除作用外,最主要的作用是去除可能污堵反渗透膜的胶体、细菌、病毒等杂质,延长反渗透膜
的清洗周期和寿命,降低总体运行成本;反渗透膜可去除98%勺盐离子,完全去除硬度、同时对COD色度
也具有极高的去除作用,从而确保回用水水质。
采用膜法工艺进行废水再利用最终要达到的目的是:将全部或部分排放废水经过膜技术深度处理后回用,除较经
济地满足企业自身用水的产能要求外,其余废水及回用装置排水合并外排,以控制外排水量,在不影响企业产能的前提下同时达到政府环保部门的要求。
避免企业因为水的问题产能受到限制,或因排放废水超量超标的难控制而引发政府环保部门的强制停产或遭受严厉罚款措施,从而影响企业的正常生产,
给企业带来不必要的损失。
4.膜法工艺处理印染废水回用的实际效果分析
浙江欧美环境工程有限公司利用膜法工艺,处理广州某纺织染整公司印染废水生化处理出水(印染废水中水)作为工艺回用水,两项工程处理水量分别达到1200t/h 和800t/h ,在工程投运之前,浙江欧美环境工程有限公司在该厂做了为期45 天的中试性实验。
4.1超滤对浊度的去除
超滤在膜法处理印染废水中的作用在于去除中水中的绝大部分大颗粒物质和胶体物质,为反渗透的正常稳定运行起保护作用,而作为反渗透预处理,衡量超滤出水的一个很重要的指标就是超滤产水的浊度和产水SDI。
图1显示了
在整个中试运行过程中超滤出水的浊度和原中水的浊度变化对比。
可以看出,超滤的浊度全部控制在0.1NTU 一下,完全满足反渗透进水对浊度的要求。
另外,整个运行过程中,测试超滤的产水SDI,最高为2.06,最低为0.91,也完全满足反渗透进水SDI W5甚至SD K3的要求。
4.2 反渗透对电导率(硬度)的去除超滤在作为反渗透预处理的同时,对中水中的有机物和色度都有一定程度
的去除。
但真正完全去除中
水中残留的有机物和色度、硬度的设备还在于反渗透。
利用反渗透特殊的过滤原理,反渗透产水能够保证五年内含盐量小于80mg/L,硬度小于5mg/L, COD 小于2mg/L 和色度小于1 度的指标。
5.膜法工艺的经济性分析(以实际工程为例)
为准确了解膜法处理印染的经济性,现以我司建设的浙江某地12000T/d 处理水量的纺织印染厂为例进
行计算和比较,范围包括从取水到回用的整个经济性分析。
该地区的政策限制是:凡是该区域内的印染企
业,处理后废水一律不能排河,只能进污水厂管网,进管网的要求是必须处理到COD500以下,排放价2.25 元/ 吨水。
5.1水量平衡
取水; 工艺用水
蒸发量1000T/
; 生化排水12000T/
全膜法处理6000T/
; 回用产水4300T/
排水6000T/
排水1700T/
若不采用回用处理措施,需取水13000T/d ,排水12000T/d ;若采用全膜法回用处理措施,则只需取水
8700T/d ,排水7700T/d 。
5.2膜法工艺的投资和运行成本
如采用膜法处理6000T/d 的印染废水,初期投资为多介质过滤150 万,超滤300 万,反渗透250 万,共计700 万。
6.利用膜法对印染废水进行回用的意义1) 印染废水中水采用膜法处理后回用水基本不含有机物、色度
和硬度,完全满足回用水的要求,技术成熟可靠;2) 以6000T/d 的处理量为例,全膜法系统的直接运行费用仅为1.22 元/ 吨水;投资回收期仅为2.7 年,具有很强的经济性;3) 企业向高档产品发展,工艺用水水质提高,现有工艺的反渗透产水水质达到纯水指标,远远优于现有新鲜水指标;对印染产品品质提升能提供可靠的保障;4) 企业发展生产规模扩大,用水、排水量增加时,回用后可解决排水量受限制的问题;5) 政府对环保要求的提高,将从行政和经济两个方面进一步限制排污,可通过回用解决排放受限的问题;6) 回用项目投运后,大大减少了外排总废水量,社会效益显著。