塑料制品产生气纹的分析及消除措施
塑胶产品的常见缺陷及分析

塑胶产品的常见缺陷及分析塑料制品是现代生活中不可或缺的一部分。
然而,塑料制品仍然存在一些常见的缺陷,这些缺陷可能导致产品质量下降,甚至无法使用。
下面是一些常见的塑料制品缺陷及其分析。
1.气泡和气孔:塑料制品中的气泡和气孔是由于在制造过程中塑料内部的空气没有完全排除或者在冷却期间塑料表面形成的。
这些气泡和气孔会导致产品表面不光滑,并在应力作用下引起断裂。
减少气泡和气孔的方法包括将塑料完全熔化,并控制良好的冷却过程。
2.毛边和厚度不均:由于模具设计和制造不当,塑料制品的边缘可能会有毛边。
毛边的存在会影响产品的外观和使用寿命。
此外,塑料制品的厚度分布不均匀可能导致产品一些部分容易破裂。
为了解决这些问题,需要优化模具设计,并确保模具制造过程的准确性。
3.烧伤和变色:在注塑过程中,如果温度控制不当,塑料可能会被过热,导致烧伤和变色。
这些问题会影响产品的外观和性能。
要解决这些问题,需要正确控制注塑机的温度和压力,并使用合适的冷却设备。
4.变形和翘曲:塑料制品可能在使用过程中变形或翘曲,这主要是由于应力超过材料的强度限制引起的。
为了避免变形和翘曲,可以通过增加产品的结构设计,加固材料强度或者改变制造过程来提高产品的稳定性。
5.色差:塑料制品可能存在色差,这是由于原料、配方和加工条件的变化引起的。
色差会影响产品的外观一致性。
要解决这个问题,需要优化原料和配方的选择,严格控制加工过程的温度和压力,以确保产品色差的控制在可接受的范围内。
综上所述,塑料制品的常见缺陷包括气泡和气孔、毛边和厚度不均、烧伤和变色、变形和翘曲以及色差。
这些缺陷可能导致产品质量下降,影响外观和性能。
为了解决这些问题,需要优化模具设计、加强原料和配方的控制,严格控制加工过程中的温度和压力。
只有通过严格的质量控制,才能生产出高质量的塑料制品。
PC制品出现银纹解决办法

PC制品出现银纹、气泡、真空泡的原因及解决办法PC制品出现银纹、气泡、真空泡,是PC料常见的制品缺陷之一,引起这些缺陷的原因较多且复杂,故较难判断和排除。
银纹(或气纹)是指塑料在充模过程中受到气体干扰而出现在制品表面熔料方向上的缺陷。
气体的成分主要包括水汽、空气、分解气及溶剂气,其中以水汽、分解气和空气为多见。
当这些气体超过一定的限度时,在注射成型后模腔失压,接近制品表面的气体就会冒出来,沿料流方向刻蚀成一连串在光照下闪闪烁烁的大大小小的泡点,称之为银纹或气纹。
实际上,在注塑过程中气体的存在是不可避免的,而且有相当一部分还残留在塑料内部。
当模内压力足够大,而气体含量又不超过一定的限度时,气体以分散的状态溶解到塑料里面去;但当模内压力不够大,而气体含量又超过一定的限度时,这些气体便从熔融塑料中纷纷释放出来,到达制品表面而形成银纹,困闭在厚的壁体内而成为气泡。
无论是制品表面的银纹,还是制品壁内的气泡,都可能是由4种气体中某一种气体为主的作用结果或几种气体共同作用的结果,它与原料、模具、塑化系统、工艺参数的调节、甚至天气的变化(尤其是湿度的变化)等因素有很大的关系。
所以这个问题比较复杂。
但不管怎样,问题的重点及解决对策应该集中在气体上,也就是说应如何控制气体的含量。
PC原料(1)水汽一般说来,如果气泡不规则地分散在制品表面,大都是由水汽所引起的。
PC的热熔料对水分非常敏感,要求含水量在0.02%以下。
所以要控制水分的含量,就要对料进行充分的干燥。
一般PC料的干燥温度在120℃左右,干燥时间4h左右,时间不能太长,如超过l0h,物料易变质,特别是加入了阻燃剂的料更不宜干燥时间过长;而干燥方式则以除湿干燥机的效果为最好,对料也没有影响。
检查干燥效果是否良好,可用对空注射法,看射出的料是否连续、光洁且不冒白气。
(2)空气如果气泡粒极为细微而密集,主要分布在制品浇口周围,形成光芒状纹或扇形纹,这多半是空气引起的。
PC件的入水口气纹成为注塑难题的原因分析

PC件的入水口气紋成为注塑难题的原因分析在众多透明料当中,比如GPPS、K料、透明ABS和PC料, PC件是最容易在入水位置产生气纹的,而且还是最难消除的。
因为PC料的流动性,在这些料当中相对最差,注塑时必須使用快速的射胶,否则就容易走料不齐或者产生震紋。
而快速射胶后果,就是在入水口位置造成因熔胶快速射至型腔表面后反弹而形成的輕微困气,而且注塑件越厚,困气面积就越大。
由于料溫较高,致使困气位置的熔胶表面被氧化,並在此形成气膜,將熔胶与模具表面隔离,从而令注塑件表面形成亚色气紋,影响注塑件的透明度。
而其他透明料的流动性相对就好得多,因而比较容易充型,且不易产生震紋,因此射胶速度可以相对较低,入水口位置的困气即使存在也非常轻微,所以不易形成亚色气紋。
即使产生了气紋,也比胶容易清除,我們只需降低一点射胶速度和压力就可以將它解決,震紋或缺料問題也不会产生,而PC料要降低速度就不行了,不是震纹就是缺料。
因此,PC料的入水口气紋問題,可以说是常用透明料中最难消除的,称得上是个注塑难題,必須采取一些措施和调机技巧才有可能將它解決。
后面将会介绍解决这一难题的注塑技术技巧供大家参考。
PC件变脆和起白雾的原因及其工艺问题几年前,我们很少见到PC料注塑件有变脆的问题。
那是因为当时使用的PC料牌子比较少,通常只有日本产的PC7025A和1250Y两种牌号。
如今生产PC料的厂家越来越多,牌子和牌号自然也不少。
问题跟着也就来了。
因各种牌号的PC料注塑技术工艺不尽相同,而且对工艺要求的严格程度也不同,因而再使用一贯注塑PC7025A和1250Y的注塑工艺去生产其他牌号的PC 料,难免就出问题了,经常可以看到PC注塑件有时会经不起冲击的脆性问题。
经过仔细的研究我們发现,由于各种牌号的PC料的耐热程度和物理特性的不同,熔胶温度,甚至连烘料温度度和烘料时间都会对注塑件的抗冲击性能产生重大影响。
通常在生产PC7025A和1250Y料时,熔胶温度一般都可调至290到310度,而生产某些牌号的PC料時,再使用这段温度来注塑,注塑件就会变得很脆了。
塑料制品产生气纹的分析及消除措施

塑料制品产生气纹的分析及消除措施塑料制品是现代工业生产中广泛使用的材料之一,它们的优点包括坚固、轻便、易加工等。
然而,塑料制品在生产过程中有时会出现气纹现象,这给产品的外观质量带来了一定的影响。
本文将对塑料制品产生气纹的原因进行分析,并提出消除气纹的措施。
1.塑料原料:选择不合适的塑料原料或添加剂,比如使用含有挥发性成分较高的原料,或原料配比不合理,会增加塑料内部的气泡产生,从而导致气纹的产生。
2.注塑工艺:注塑过程中的温度、压力、冷却等工艺参数的设定不合理,会影响塑料的熔融和流动性能,进而造成气纹。
3.模具设计:模具设计中存在问题,比如模具排气口设计不合理或位置不当,会导致注射过程中无法及时排除气体,从而产生气纹。
针对以上原因,可以采取以下措施来消除塑料制品产生气纹:1.塑料原料的选择:选用低挥发性成分的塑料原料,并严格控制添加剂的比例,尽量减少塑料内部气泡的产生。
2.注塑工艺优化:优化注塑过程中的温度、压力和冷却参数,确保塑料熔融均匀、流动性能良好,从而减少气泡的产生。
3.模具设计改进:合理设计模具的排气系统,包括合理设置排气口和通道,确保在注射过程中气体能够及时排除。
4.控制注射速度:控制注射速度不宜过快,过快的注射速度容易产生气纹。
5.熔融温度控制:控制熔融温度在适当的范围内,避免过高的熔融温度造成气纹。
6.增加压力保持时间:在注射结束后,适当延长保压时间,使塑料内部气泡能够更好地排除。
除了以上措施外,还可以通过使用辅助排气设备,比如真空排气装置或真空注射设备,来增加排气效果,减少气纹的发生。
在消除塑料制品产生气纹的过程中,需要综合考虑原料、工艺和模具等多个因素,并进行适当的实验和改进。
通过不断优化和改进生产过程,可以有效地减少塑料制品的气纹现象,提升产品的质量和外观。
注塑工程改善方案(3篇)
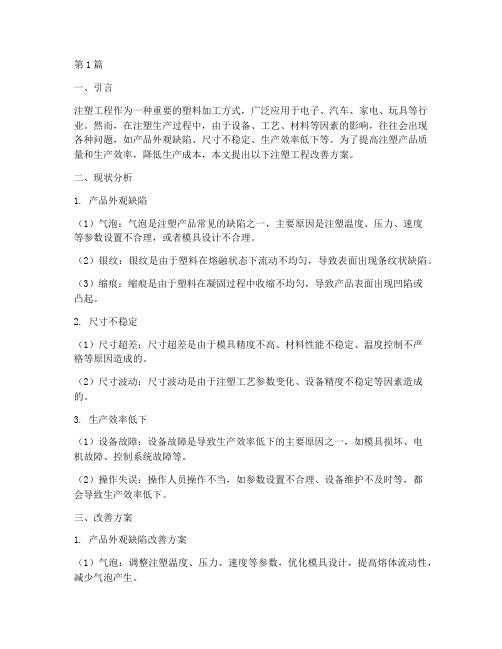
第1篇一、引言注塑工程作为一种重要的塑料加工方式,广泛应用于电子、汽车、家电、玩具等行业。
然而,在注塑生产过程中,由于设备、工艺、材料等因素的影响,往往会出现各种问题,如产品外观缺陷、尺寸不稳定、生产效率低下等。
为了提高注塑产品质量和生产效率,降低生产成本,本文提出以下注塑工程改善方案。
二、现状分析1. 产品外观缺陷(1)气泡:气泡是注塑产品常见的缺陷之一,主要原因是注塑温度、压力、速度等参数设置不合理,或者模具设计不合理。
(2)银纹:银纹是由于塑料在熔融状态下流动不均匀,导致表面出现条纹状缺陷。
(3)缩痕:缩痕是由于塑料在凝固过程中收缩不均匀,导致产品表面出现凹陷或凸起。
2. 尺寸不稳定(1)尺寸超差:尺寸超差是由于模具精度不高、材料性能不稳定、温度控制不严格等原因造成的。
(2)尺寸波动:尺寸波动是由于注塑工艺参数变化、设备精度不稳定等因素造成的。
3. 生产效率低下(1)设备故障:设备故障是导致生产效率低下的主要原因之一,如模具损坏、电机故障、控制系统故障等。
(2)操作失误:操作人员操作不当,如参数设置不合理、设备维护不及时等,都会导致生产效率低下。
三、改善方案1. 产品外观缺陷改善方案(1)气泡:调整注塑温度、压力、速度等参数,优化模具设计,提高熔体流动性,减少气泡产生。
(2)银纹:优化熔体流动路径,减少流动阻力,提高熔体流动性,降低银纹产生。
(3)缩痕:优化模具冷却系统,提高冷却效果,减少塑料收缩,降低缩痕产生。
2. 尺寸不稳定改善方案(1)尺寸超差:提高模具精度,严格控制材料性能,优化温度控制,确保产品尺寸稳定。
(2)尺寸波动:优化注塑工艺参数,提高设备精度,减少操作误差,降低尺寸波动。
3. 生产效率低下改善方案(1)设备故障:加强设备维护保养,定期检查设备状态,提高设备可靠性。
(2)操作失误:加强操作人员培训,提高操作技能,规范操作流程,减少操作失误。
四、具体实施措施1. 优化注塑工艺参数(1)根据塑料材料性能和产品要求,合理设置注塑温度、压力、速度等参数。
塑胶件气纹原因对策

塑胶件气纹原因对策内部因素:1.塑料材料的选择:一些塑料材料更容易产生气纹,例如硬度较高的材料。
因此,在选择塑料材料时,需要考虑材料的特性,避免选择易产生气纹的材料。
2.注塑工艺参数:注塑工艺参数的设置对于塑胶件的质量有很大的影响。
例如,注射速度、压力和温度等参数的不合理设定可能会导致气体陷入熔融塑料中,从而产生气纹。
3.模具设计:模具的设计也会影响塑胶件的质量。
例如,模具的冷却系统是否合理、气道的设置是否恰当等,都会对气纹的形成产生影响。
外部因素:1.环境因素:环境温度和湿度等因素对塑胶件的形成也有一定的影响。
例如,在高温和潮湿的环境下进行注塑成型,可能会使熔融塑料中的气体无法充分排除,从而产生气纹。
2.模具表面处理:模具的表面处理也会影响塑胶件的质量。
如果模具表面存在凹凸不平的情况,容易在注塑过程中产生气阱,导致气体陷入塑料中,从而产生气纹。
针对以上原因,可以提出以下对策来减少或消除塑胶件的气纹:1.材料选择:选择与具体产品要求相匹配的塑料材料,避免选择易产生气纹的材料。
2.优化注塑工艺参数:合理设置注射速度、压力和温度等参数,确保气体能够顺利排除。
3.模具设计优化:合理设计模具的冷却系统和气道,确保冷却和排气效果良好。
4.环境控制:控制注塑过程的环境温度和湿度,避免在高温和潮湿的环境下进行注塑成型。
5.模具表面处理:进行表面处理,确保模具表面光滑平整,避免产生气阱。
总的来说,塑胶件气纹是一个常见的缺陷,但可以通过合理的材料选择、注塑工艺参数优化、模具设计优化、环境控制和模具表面处理等对策来减少或消除气纹的发生。
制造商应该认真对待这个问题,并根据具体情况采取相应的措施来提高产品的质量和外观。
塑胶件气纹原因对策
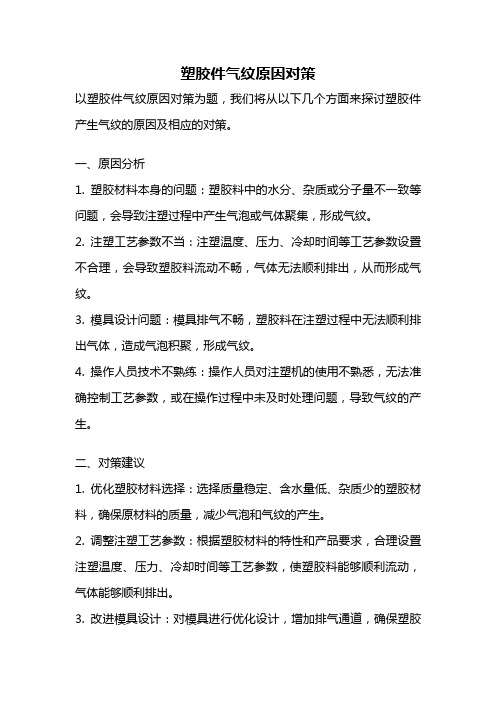
塑胶件气纹原因对策以塑胶件气纹原因对策为题,我们将从以下几个方面来探讨塑胶件产生气纹的原因及相应的对策。
一、原因分析1. 塑胶材料本身的问题:塑胶料中的水分、杂质或分子量不一致等问题,会导致注塑过程中产生气泡或气体聚集,形成气纹。
2. 注塑工艺参数不当:注塑温度、压力、冷却时间等工艺参数设置不合理,会导致塑胶料流动不畅,气体无法顺利排出,从而形成气纹。
3. 模具设计问题:模具排气不畅,塑胶料在注塑过程中无法顺利排出气体,造成气泡积聚,形成气纹。
4. 操作人员技术不熟练:操作人员对注塑机的使用不熟悉,无法准确控制工艺参数,或在操作过程中未及时处理问题,导致气纹的产生。
二、对策建议1. 优化塑胶材料选择:选择质量稳定、含水量低、杂质少的塑胶材料,确保原材料的质量,减少气泡和气纹的产生。
2. 调整注塑工艺参数:根据塑胶材料的特性和产品要求,合理设置注塑温度、压力、冷却时间等工艺参数,使塑胶料能够顺利流动,气体能够顺利排出。
3. 改进模具设计:对模具进行优化设计,增加排气通道,确保塑胶料在注塑过程中能够顺利排出气体,减少气泡的产生。
4. 提高操作人员技术水平:加强对操作人员的培训,使其熟练掌握注塑机的使用方法和工艺参数的调整,提高操作技术水平,及时处理问题,减少气纹的发生。
三、其他注意事项1. 定期维护设备:定期对注塑机进行检查和维护,确保设备的正常运行,减少因设备问题导致的气纹产生。
2. 加强质量检验:建立完善的质量检验体系,对产品进行全面的检测,及时发现并处理存在气纹的产品,确保产品质量。
3. 优化生产流程:优化生产流程,减少工艺环节,缩短注塑周期,降低气纹产生的机会。
塑胶件产生气纹是一个复杂的问题,需要从材料、工艺、模具和操作人员等多个方面进行综合分析和解决。
通过优化选择材料、调整工艺参数、改进模具设计、提高操作人员技术水平等对策,可以有效减少塑胶件气纹的产生,提高产品质量。
同时,加强设备维护、质量检验和优化生产流程等也是减少气纹产生的重要措施。
巧用原料,轻松改善注塑件气痕问题

巧用原料,轻松改善注塑件气痕问题
?今天,小编给大家6个巧用原料的小妙招,轻松改善令人深恶痛绝的塑料件表面气痕问题。
妙招1:控制含水率【一般原料含水率
妙招2:强化阻燃型材料的干燥水平【强化阻燃型材料的干燥水平,且料筒温度不能超过阻燃剂最适宜加工温度】,轻松改善因含阻燃剂高温易分解大量气体和吸潮,产生的表面气痕问题。
妙招3:降低小分子挥发物【降低料筒温度,加强干燥及加强模具排气来减少小分子挥发量】,轻松因塑料中含有易挥发的添加剂、着色剂、分解残余物等,在高温下或强剪切下会发热气化产生大量气体,产生的表面气痕问题。
妙招4:排除颗粒间空气【采用合适的溶胶温度计速度,再配以合适的背压设定,排除颗粒间空气】,轻松因塑料颗粒之间含有空气,产生的表面气痕问题。
妙招5:减少聚合物大分子链降解【降低加工温度、高温停留时间及剪切发热,减少聚合物大分子链降解】,轻松改善因原料本身分子链耐热不足或易水解,高温下降解产生气
体,产生的表面气痕问题。
妙招6:控制回料比例【控制回料比例?。
- 1、下载文档前请自行甄别文档内容的完整性,平台不提供额外的编辑、内容补充、找答案等附加服务。
- 2、"仅部分预览"的文档,不可在线预览部分如存在完整性等问题,可反馈申请退款(可完整预览的文档不适用该条件!)。
- 3、如文档侵犯您的权益,请联系客服反馈,我们会尽快为您处理(人工客服工作时间:9:00-18:30)。
塑料制品产生气纹的分析及消除措施
摘要:针对塑料制品产生气纹的缺陷,对注塑设备,模具,材料性能,工艺参数及周围环境等因素进行研究,分析了产生气纹的原因,又根据不同气纹的特点,采取了相应的消除措施,能够有效地解决此类缺陷。
关键词:气纹;排气;流动性
一、引言
气纹是容易产生且很难消除的质量缺陷。
气纹不仅仅会影响产品的外观,还会影响产品的强度。
国内有关技术资料对产生气纹的机理过程涉及的不多,造成操作人员遇到具体问题时,不能快速找到问题产生的原因,不知该采取哪些工艺措施,问题得不到及时的解决,导致资源大量浪费,会对企业造成巨大的损失。
针对塑料制品产生气纹这一缺陷,本文对其产生因素进行了分析和研究,详细的阐述了气纹的产生机理及现象,又根据不同气纹的特点,制定了相应的应对措施。
在生产过程中,根据观察到的现象做出准确的判断,就可以推断出气纹产生的原因,继而制定出相对应的消除措施方案进行解决。
二、气纹产生的原理
气纹是塑料在充模过程受到气体的干扰而出现在制品表面熔料流动方向上的缺陷。
气体的成份包括水汽、分解气、空气,可见,气纹存在的根本原因是有气体存在,如果高温熔融态塑料流体在填满模具之前,不能将气体顺畅排出,气体就会与塑料熔体混合流动,冷却成型后,内部气体形成气孔,外部气体产生流动痕迹,即气纹[1]。
事实上,在注塑过程中气体的存在是不可避免的,而且有相当一部分残留在塑料内部。
当模内压力足够大,气体含量没有超过一定的限度时,气体以分散的状况溶解到塑料里面去;但当模内压力不够大,而气体含量又超过一定的限度时,这些气体便从熔融塑料中纷纷释放出来,到达制品表面而形成气纹。
造成气纹缺陷的主要原因有六点:1 注塑设备与注塑产品不相配;2 模具排气槽设计太少或太小;3 生产工艺的影响;4塑料熔体自身不断地产生气体;5 注塑设备所处的环境湿度大;6 塑料熔体流动性差。
1.注塑设备的影响
设备的选择要合理,如果制品与浇口凝料料重之和小于最大注射量的20%,则剩下的原料会因螺杆的旋转产生的剪切力,机筒的加热而分解产生气体。
如果大于最大注射量的80%,则会出现熔料受热不均的现象,很难以成型精密制品。
螺杆设计如果合理, 与所加工的塑料种类匹配, 成型工艺范围就会相对较宽; 否则成型工艺范围可能很窄甚至不能成型制品。
不同型号、大小的注塑机其射嘴的孔也是各有差异的,有2.5MM、3.5MM、5MM等等,机器越大其射嘴孔相应也就越大。
喷嘴孔太小、物料在喷嘴处流涎或拉丝、机筒或喷嘴有障碍物或毛刺,高速料流经过时产生摩擦热使料分解产生气体,气体来不及排出会产生气纹现象。
2.模具排气不畅的影响
在高温高压下,低黏度熔融塑料突然穿越狭窄的浇口,熔融原料注射进入模具型腔的时间很短,进入具有较大自由空间的型腔,形成高压喷射状态,夹带了流道和型腔内存在的空气。
原料在模具中的填充过程又是气体被排出的过程,模具分型面缺乏必要的排气孔道或排气孔道不足、堵塞、位置不好,又没有嵌件、顶针之类加工缝隙排气,使流道和型腔中的空气不能在塑料进入的同时离去,极易造成气体被裹入高温熔体中,随着熔体的流动,气体逸出熔体表面,形成流动痕迹[2]。
3.生产工艺的影响
如果注射压力过高、注射速度过快,模具中的气体来不及排出,就会受到急剧压缩,骤然积聚大量机械能,从排气槽释放的气体又急剧膨胀将机械能转化成热能迅速释放出来,极易造成排气槽部位零件表面过烧,产生焦斑。
除此之外,还会产生物料摩擦热过高,容易造成熔料因温度偏高而降解或变色;同时,过快的注射熔料流速会让模腔内空气被急剧加压而升温,也会使熔料汇合处因降解而出现焦黄色。
但如果注射速度过慢,注塑成型制品用时间增加,熔料受降温的影响充满模腔的时间加长,流动所受到的阻力加大,这样会造成成型制品出现冷合料缝痕,还会造成原料的温度大幅度下降,随温度降低,原料的粘度升高,流动性变差,
一方面使气体不能及时从熔融原料中分离出来反而产生流纹,另一方面就是熔体前沿温度的急速冷却形成了高粘度流动体,阻碍了气体向前流动排出,在通过模腔狭窄区域(如零件薄壁区域)时,受到很大阻力,使熔体内部压力升高,容易形成高温灼热气体,产生零件表面过烧现象。
4.塑料熔体自身产生气体的影响
如果注塑设备适合生产某种产品,塑料模具设计合理,排气顺畅,但塑料自身不断产生气体,那么塑料熔体在射胶过程和冷却成型过程中依然会产生气纹。
自身产生气体主要有两种类型:
(1)水蒸汽的影响
水蒸汽来源主要是原材料受潮时吸收的水分,熔胶过程中,原材料受热,水分被不断蒸发逸出,射入模具后,塑料熔体表面水蒸汽遇冷迅速冷凝,在零件表面形成蒸汽纹。
如果模具排气不良,灼热的水蒸汽就会造成零件表面过烧现象。
(2)分解气体的影响
一些质量差的塑料熔胶过程中,由于受高温或高剪切力(螺杆转速过快、背压过高)影响,一些易挥发相直接从熔体中逸出;特别是当含有微量杂质或微量水分时,可能发生催化裂化反应。
造成塑料产生分解气的原因:熔体温度过高,造成分解;料筒温度过高,或料筒的发热圈控制失调。
小制品用大机,或缓冲垫量过大,或料筒内的呆料、死角处因长期受热而分解,或成型周期太长,使熔体在料筒里的停留时间过长而造成分解;熔体在料筒里的剪切过大,螺杆的压缩比过大,螺槽太浅等,再加上螺杆转速过大,背压过大等。
5.注塑设备所处的环境影响
当注塑机处于潮湿的环境中,空气湿度过大空气湿度过大,遇到冷的模具而凝聚成水的水珠(如模温低于露点),造成模具的模穴内带有微量的水分,这些水分被熔料汽化后成水蒸气,气体来不及排出便会产生气纹现象。
6.熔体流动性差的影响
许多塑料具有熔体流动性差的性质,它对气纹产生的影响有两种类型,一种是塑料在熔胶阶段产生的气体不能及时逸出并从料筒后段排出,导致其最终被带
入模具中;另一种是在模具中使裹入塑料熔体中的气体不及时逸出。
三、典型实例分析
仪表罩塑件图
气纹
具有气纹的仪表罩图
该仪表罩是在800T注塑机中生产的,产品图号53A-05171,毛重801g,净重792g,材料牌号ABS/VK125,成型周期65s。
1.仪表罩出现气纹的原因
经分析造成气纹的原因主要有:⑴熔料温度或模具温度过低;⑵注射速度、
压力过高;⑶背压偏低;⑷模具排气不良;⑸原料干燥不充分或过热分解;⑹模
具浇注系统有缺陷。
2.可行的改进方案
⑴适当提高料筒温度,使气体容易逸出,但PC/ABS塑料温度不能超过270℃,防止高温分解,影响PC/ABS塑料性能。
⑵适当降低注射压力、注射速度,使气体有充分时间排出。
应当注意的是,注射压力和注射速度是相互关联的,调整时不能采取同时改变两者的方式,因为进行调整时并不能确定造成气纹的原因究竟是注塑压力过大还是注射速度过大。
正确的方法是先选择其中一个参数进行调整,然后看其产生的效果,再决定下一步的操作。
⑶增加背压,提高熔料速度,可以使裹入原料中的空气以及原料自身易挥发相产生的气体从料筒后段充分排出。
⑷改善模具的排气。
保证注塑过程中物料填充到模具内时所产生的各种气体顺利的排出模具。
⑸原材料应该充分干燥,建议70℃~80℃,烘料时间不少于4h,并做好防潮措施(特别在阴雨天),防止水蒸汽的影响[3]。
合格的仪表罩图
四、结语
注塑制品上的气纹会降低制品的强度,影响外观, 因此气纹是注塑制品失效的一个重要原因。
气纹区域材料的形态结构是影响制品性能的直接原因, 要消除或减小气纹对制品性能的影响, 以提高制品的性能, 应充分考虑不同材料形成的气纹的形态结构。
只有通过正确地认识气纹区域材料的形态结构与制品性能的关系, 才能在工业生产中合理地选择模塑材料。
这对于提高注塑制品的质量, 延
长注塑制品的使用寿命具有重要意义。
参考文献
[1] 刘西文:注射成型技术疑难问题解答.北京:印刷工业出版社,2011.
[2] 李海梅:注塑成型及模具设计实用技术.北京:化学工业出版社,2002.
[3] 崔继耀:注塑生产疑难问题与对策.北京:国防工业出版社,2008.。