超微粉末的制备技术
粉体制备技术

表2-1普氏硬度岩石分级表
8
应该指出的是: 微裂缝理论:脆性断裂的主要理论基础。 1920年,Griffith认为材料的理论强度和实际强度 之所以有较大的差异主要是由于:实际材料中总是存在 许多细小的裂纹和缺限,在外力作用下,这些裂纹和缺 限附近产生应力集中现象。当应力达到一定程度时,裂 纹开始扩展而导致断裂。
气体蒸发法 活化氢熔融金属反应法 构 筑 法 溅射法 真空沉积法 加热蒸发法
制 备 方 法
混合等离子体法 沉 淀 法 共沉淀法 化合物沉淀法 喷雾干燥法 喷 雾 法 喷雾水解法 喷雾焙烧法 水解法
化 学 方 法
氧化还原法 冻结干燥法 激光合成法 火花放电法
4
2.2 粉碎法制备超细粉体常用方法及设备分类
1
超细粉体的的制备方法很多 : 按产品粒径大小:微米粉体制备法、亚微米粉体制备法; 纳米粉体制备法。工艺条件控制不同----容易引起混乱。 按制备方法的性质:物理方法与化学方法。
(1)物理法又分为粉碎法和构筑法 粉碎法是借用各种外力,如机械力、流能力、化学能、声能、热能 等使现有的块状物料粉碎成超细粉体。由大至小(微米级)。 构筑法通过物质的物理状态变化来生成粉体。由小至大(纳米级) (2)化学法:包括溶液反应法(沉淀法)、水解法、气相反应法及喷 雾法等,其中,溶液反应法(沉淀法)、气相反应法及喷雾法目前在 工业上已大规模用来制备微米、亚微米及纳米材料。 目前,工业中用得最多的是通过粉碎法,应用最多的粉体是通过粉 碎法、化学法产生的微米级和亚微米级粉体,纳米粉体的生产及使用 量相对较少。
转子在电机带动下绕主轴高速旋转,产生较大的离心力场,在 粉碎腔内中心形成一很强的负压区,借助负压被粉碎物料从转子 和定子中心吸入,在离心力作用下,物料由中心向四周扩散,在 向四周的扩散过程中,物料首先受到内圈转齿及定齿的撞击、剪 切、摩擦、以及物料与物料之间的相互碰撞和摩擦作用而被粉碎 。随着转齿的线速度由内圈向外圈逐步提高,物料在向外圈的运 动过程中受到越来越强烈的冲击、剪切、摩擦、碰撞等作用而被 粉碎的越来越细。最后在外圈与撞击环的冲击与冲击作用下得到 进一步粉碎而被超细粉碎。
一种超细粉体的制备方法

一种超细粉体的制备方法
一种常用的超细粉体制备方法是湿法粉碎。
首先,将原料加入到适量的溶剂中,形成一个悬浮液。
溶剂的选择取决于原料的性质和所需的最终产品。
然后,悬浮液会被放入一个湿法研磨装置中,如球磨机或珠磨机。
这些设备通常由旋转的容器和固定的磨球或磨珠组成。
在研磨过程中,悬浮液中的颗粒受到了两个力的作用:剪切力和冲击力。
剪切力使颗粒相互摩擦和碰撞,从而导致颗粒的破碎和细化。
冲击力则通过撞击颗粒表面来实现破碎。
经过一段时间的研磨,颗粒逐渐变得更小和更均匀。
当颗粒达到所需的尺寸范围后,研磨过程停止,悬浮液经过过滤或离心分离,得到超细粉体。
这种湿法粉碎方法可以生产出高质量的超细粉体,其粒径可控制在几纳米到几微米的范围内。
此外,湿法研磨还可以实现对原料的均质混合和化学反应,提高产品的质量和性能。
超细粉体的制备方法

超细粉体的制备方法
超细粉体的制备方法有很多种,常见的包括以下几种:
1. 气相法:将化学反应产生的气体混合等离子体中,通过物理和化学反应使气态物质转变为粉末。
2. 溶剂法:将所需材料溶于有机溶剂或水中,在适当条件下,将溶液慢慢蒸发干燥,得到超细粉末。
3. 机械法:通过机械剪切、碾磨和冲击等机械力量作用,将粗粉末不断细化。
4. 化学沉淀法:将水溶性物质溶解于水中,在控制pH值的情况下加入化学试剂,产生沉淀物,然后进行干燥和烘烤,得到超细粉末。
5. 等离子体法:将所需材料在大气压下暴露于等离子体中,利用等离子体的热、光、化学反应以及激波力等效应制备超细粉末。
6. 真空喷雾法:将所需材料通过喷雾喷入真空环境中,利用强大的气相冷却作用,使溶液迅速凝固成超细粉末。
7. 物理气相法:通过高功率激光或电弧等方式将金属材料蒸发,形成高温高压等离子体,利用等离子体的力和能量将其制备成超细粉末。
超微茶粉工艺技术
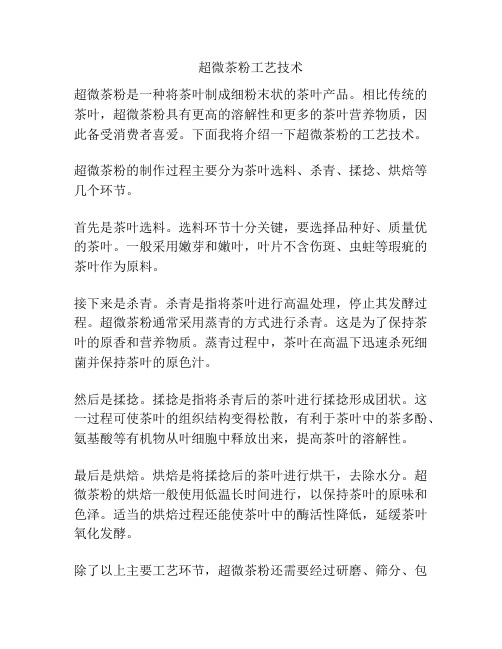
超微茶粉工艺技术超微茶粉是一种将茶叶制成细粉末状的茶叶产品。
相比传统的茶叶,超微茶粉具有更高的溶解性和更多的茶叶营养物质,因此备受消费者喜爱。
下面我将介绍一下超微茶粉的工艺技术。
超微茶粉的制作过程主要分为茶叶选料、杀青、揉捻、烘焙等几个环节。
首先是茶叶选料。
选料环节十分关键,要选择品种好、质量优的茶叶。
一般采用嫩芽和嫩叶,叶片不含伤斑、虫蛀等瑕疵的茶叶作为原料。
接下来是杀青。
杀青是指将茶叶进行高温处理,停止其发酵过程。
超微茶粉通常采用蒸青的方式进行杀青。
这是为了保持茶叶的原香和营养物质。
蒸青过程中,茶叶在高温下迅速杀死细菌并保持茶叶的原色汁。
然后是揉捻。
揉捻是指将杀青后的茶叶进行揉捻形成团状。
这一过程可使茶叶的组织结构变得松散,有利于茶叶中的茶多酚、氨基酸等有机物从叶细胞中释放出来,提高茶叶的溶解性。
最后是烘焙。
烘焙是将揉捻后的茶叶进行烘干,去除水分。
超微茶粉的烘焙一般使用低温长时间进行,以保持茶叶的原味和色泽。
适当的烘焙过程还能使茶叶中的酶活性降低,延缓茶叶氧化发酵。
除了以上主要工艺环节,超微茶粉还需要经过研磨、筛分、包装等环节才能最终成为出售的茶叶产品。
其中,研磨环节十分关键,目的是将揉捻后的茶叶制成细粉末状。
这是由于超微茶粉使用时,无需沸水浸泡即可溶解,需要更细的茶叶颗粒。
当然,在整个工艺技术过程中,还需要严格控制时间、温度和湿度等因素。
不同的茶叶品种在加工过程中的时间和温度要求是不同的,需要根据具体茶叶品种来进行调整。
另外,工艺环节中的湿度也需要注意,以避免茶叶吸湿变质。
通过严格把控超微茶粉制作过程中的每个环节,能够保证超微茶粉的品质和安全。
同时,也能够最大限度地保留茶叶中的香气和营养物质,使消费者能够享受到更美味、更健康的超微茶粉。
植物提取物超微粉体制备技术研究进展

植物提取物超微粉体制备技术研究进展摘要:植物提取物大都是脂溶性成分,因其水溶性差、生物利用度低,故其在临床上的推广应用受到了一定程度的限制。
文章综述了有关能增强植物提取物水溶性的超临界流体技术、高压均质技术、液相可控沉淀技术、喷雾干燥技术、乳化溶剂扩散技术、机械研磨技术等超微粉体制备技术的研究进展。
关键词:植物提取物;水溶性;生物利用度;超微粉体技术;综述中图分类号:S609.9;TQ460 文献标志码:A 文章编号:1003—8981(2015)02—0167—05我国拥有丰富的药用植物资源,已经从植物提取物中发现了大量具有显著生理或药理活性的有效成分。
如姜黄素具有抗肿瘤[1-2]、抗炎[3]、抗氧化[4] 多种生物活性;甘草酸抗炎[5]、保肝解毒[6] 等方面有较好的疗效;紫杉醇对多种肿瘤细胞具有明显的抑制作用[7-8];水飞蓟宾在诱导肿瘤细胞凋亡[9]、抗炎症[10] 和抗氧化[11] 等方面有显著疗效。
但是,很多植物提取物中的有效成分往往存在水溶性差、生物利用度低、体内组织代谢转化迅速等问题[12],这在一定程度上限制了植物提取物在临床上的推广应用[13]。
随着药学科学的不断进步及各种超微粉体在药物制剂学方面的成功应用,超微粉体制备技术已成为人们关注的重点[14]。
有关研究结果表明,超微粉体因为粒径小,比表面积大大增加,与大颗粒相比,药物颗粒具有更好的水溶性和更高的饱和溶解度[15]。
目前国内外学者对如何解决植物提取物水溶性差等问题进行了一些卓有成效的研究,文中综述了植物提取物超微粉体制备技术的研究进展,以期为其深入研究与推广应用提供参考。
1 植物提取物超微粉体制备技术的研究进展1.1 植物提取物超微粉体的超临界流体制备技术超微粉体的超临界流体制备技术原理是利用超临界流体与药物溶液混合后从喷嘴喷出,在喷出的瞬间形成超微粒子[16]。
目前,用于制备超微粉体的超临界流体技术主要有超临界流体快速膨胀技术(SAS)和超临界流体抗溶剂结晶技术(RESS)及以这两种技术为基础而衍生出的气体抗溶剂结晶技术(GAS)、超临界流体干燥技术(SFD)、超临界反向结晶技术(RCM)、气体饱和溶液技术(PGSS)等技术。
超微粉原理

超微粉原理超微粉原理的定义和基本概念超微粉原理是一种通过材料高速旋转及高温制备加工等方法将母材料加工为微米级别的细粉末。
超微粉技术是在微观尺度下制备细粉末的先进技术。
在超微粉的制备过程中,减少了晶界、位错等缺陷,从而使粉末具有与块材料不同的材料性质。
超微粉材料的制备方法超微粉制备的方法有多种,其中最常用的方法是机械铣削、热喷涂、光化学还原、溅射、电子束消融、等离子体喷射等。
机械铣削法是在机床上,通过刀具切削母材制成超微粉,同时需要对切削速度,进给速度、加工量等进行控制。
该方法产生的超微粉的粒径一般在几微米到十几微米之间。
热喷涂法是一种通过高能喷射将母材击碎制成超微粉的方法。
通过热喷涂,材料制成的超微粉粒径可达到纳米级别。
热喷涂法制备的超微粉材料具有非常高的比表面积和活性。
光化学还原法是使用光敏化学药品,通过光化学反应将母材制成超微粉的方法。
该方法制备的粉末具有非常高的纯度和结晶度,并且具有非常好的结构性能。
在溅射法中,使用高能电子束或离子束将母材熔化溅射在基片上,从而形成超微粉;在等离子喷射法中,使用气体生成等离子体,并通过等离子体喷射形成超微粉。
这两种方法制造的超微粉也在实际应用中保持广泛的通用性。
通过超微粉化,材料的表面积和内部空腔明显增加,因此比表面积增加,异常活性也相应提高,晶界面的碰撞和位错相互迫近及堆积等现象增加,是母材料性质发生改变。
超微粉对材料力学性能,热学性能,物理性质等都会产生重要影响。
在材料科学和制造领域中,超微粉材料可以用于制备高强度、高导热性、高抗腐蚀性的材料,并应用于特殊领域,如生物医学、能源存储、电子器件等。
特别是在石墨、碳材料、高温结构材料、耐腐蚀材料、金属粉末冶金等领域中,超微粉技术发挥了重要作用。
超微粉使用注意事项超微粉具有活性强,易氧化的特点,因此在制备和使用过程中,必须注意避免超微粉受到空气和水分的污染,同时应采取防静电措施,以避免超微粉的粉尘可能会对人员造成不良影响。
化学法制备超微粉体

气相法
气相制粉法有两种:一种是系统中不发生化学反应的蒸发-凝聚法(PVD);另 一种是气相化学反应法(CVD)。
一、 蒸发-凝聚法
蒸发-凝聚法是将原料加热至高温(用电弧或等离子流等加热),使之气化, 接着在具有很大温度梯度的环境中急冷,凝聚成微粒状物料的方法。这 一过程不伴随化学反应。 采用这种方法能制得颗粒直径在5nm~100nm范围的微粉, 适于制备单一氧化物、复合氧化物、碳化物或金属的微粉。 使金属在惰性气体中蒸发-凝聚,通过调节气压,就能控制生成的金属 颗粒的大小。液体的蒸汽压低,如果颗粒是按照蒸发-液体-固体那样经过 液相中间体后生成的,那么颗粒成为球形或接近球状。
6/4/2019
气相法
二、 气相化学反应法
气相化学反应法是将挥发性金属化合物的蒸气通过化学反应合成所 需物质的方法。气相化学反应可分为两类:一类为单一化合物的热分 解(A(g)→B(s) +C(g));另一类为两种以上化学物质之间的反应(A(g) + B(g) →C(s)+ D(g))。 气相反应法除适用于制备氧化物外,还适用于制备液相法难于直接 合成的金属、氮化物、碳化物、硼化物等非氧化物。制备容易、蒸气 压高、反应性较强的金属氯化物常用作气相化学反应的原料。
液相法
(3)共沉淀法
共沉淀法是在混合的金属盐溶液(含有两种或两种以上的金属离子)中加 入合适的沉淀剂,反应生成组成均匀的沉淀,沉淀热分解得到高纯超微 粉体材料。
共沉淀法的关键在于保证沉淀物在原子或分子尺度上均匀混合。
例:四方氧化锆或全稳定立方氧化锆的共沉淀制备。以ZrOCl2·8H2O和 Y2O3(化学纯)为原料来制备ZrO2-Y2O3的纳米粉体的过程如下:Y2O3用盐 酸溶解得到YCl3,然后将ZrOCl2·8H2O和YCl3配制成—定浓度的混合溶 液,在其中加NH4OH后便有Zr(OH)4和Y(OH)3的沉淀粒子缓慢形成。反 应式如下:
超细粉末的制备及其性能研究

超细粉末的制备及其性能研究超细粉末是指晶体材料的粒子尺寸小于100纳米的粉末,具有高比表面积、低热稳定性、高亲表面活性等特征。
目前,随着科学技术的发展和应用需求的增加,对超细粉末的研究和应用也越来越重要。
本文将主要从超细粉末制备的方法和超细粉末的性能研究两个方面进行探讨。
一、超细粉末的制备方法目前,超细粉末的制备方法主要有物理法、化学法、生物法和机械法等四种。
以下对这四种方法进行简要介绍。
1.物理法物理法制备超细粉末主要有气相法和水相法两种。
气相法是指通过物理气相沉积、惰性气体剥离离解等方式制备超细粉末的方法。
其中惰性气体剥离离解可分为惰性气体剥离法和惰性气体离解法两种。
物理气相沉积法就是把物质加热至高温,在惰性气体环境下,使其蒸发并与惰性气体反应制成粉末。
物理气相法制备的超细粉末具有尺寸均一、制备过程简单等优点。
水相法是指通过化学合成方法在水相中合成超细粉末的方法。
其中常用的水相合成方法有溶胶-凝胶法和共沉淀法两种。
溶胶-凝胶法制备超细粉末的步骤包括制备胶体和胶体凝胶两个步骤。
共沉淀法是指通过酸碱中和、沉淀分离等方式制备超细粉末的方法。
水相法制备的超细粉末粒径分布均匀、受到污染少、制备过程要求严格等特点。
2.化学法化学法制备超细粉末主要有溶胶-凝胶法和共沉淀法两种。
溶胶-凝胶法是指通过化学合成在有机胶体中制备超细粉末的方法。
其中,超细粉末的粒径能够通过浸渍次数、胶体凝胶时间、热处理等方式来控制。
共沉淀法就是通过反应沉淀的方式在水中制备超细粉末。
这种方法的重要性在于可以直接得到纳米级别的粉末。
3.生物法生物法制备超细粉末主要有微生物法和植物法两种。
微生物法是指通过微生物代谢合成超细粉末。
例如,菌丝处理剂可以将废矿物化合物转化为超细粉末。
植物法是指通过植物药物提取物制备超细粉末的方法。
4.机械法机械法制备超细粉末主要有球磨法、高能强化法和电化学法等。
球磨法是一种通过高能机进行粉末制备的方法。
其中,球磨法制备超细粉末的步骤包括入料、打球、卸粉、筛选等步骤。
- 1、下载文档前请自行甄别文档内容的完整性,平台不提供额外的编辑、内容补充、找答案等附加服务。
- 2、"仅部分预览"的文档,不可在线预览部分如存在完整性等问题,可反馈申请退款(可完整预览的文档不适用该条件!)。
- 3、如文档侵犯您的权益,请联系客服反馈,我们会尽快为您处理(人工客服工作时间:9:00-18:30)。
1.1.2 超微粉末研究的发展历史
➢ 1984年,德国学者Gleiter等人首次采用惰性气体中蒸发凝聚法制备了 具有清洁表面的纳米粉末,然后在真空室中压制成了块状纳米材料, 并首次提出了纳米材料的概念。从此,人们将粒径在100nm以下的粒 子集合体称之为纳米粉末。
➢ 随后Siegel等人制备出了TiO2和CaF2纳米陶瓷材料,并发现其在室温 下具有良好的韧性。
➢ 1962年,日本物理学家Kubo在量子统计力学的基础上分析了金属超 微粒子的特性及粒子中电子间的相互作用,提出了著名的“久保效 应”,开创了近代超微粒子研究的新阶段。
➢ 20世纪60年代,透射电子显微镜开发成功后,超微粒子的研究工作主 要集中在晶体学和形貌特点方面。
➢ 1963年Ryozi Uyeda等人发展了气相蒸发法制备金属超微粉末的方法。
➢ 1985年,Kroto与Richard E. Smalley,采用激光轰击石墨靶,获得了 碳的团簇,采用质谱仪分析团簇结构时发现了C60。
➢ 1991年日本电镜专家Iijima发现了纳米碳管。
➢ 日本学者在观察2nm大小的Au粒子的晶体结构和形貌时,意外地发现 粒子的形状自发变化的反常现象,进而提出了“准固态”的概念。
E处的密度分布函数(E)为:
(E)
3NE1/ 2 4EF 3/ 4
(1-2)
Байду номын сангаас
➢ 根据自由电子模型,粒子中电子的平均能级间隔δ可以近似表示为:
4EF
3N
(1-3)
式中的N为体系的自由电子数,EF为自由电子的费米能。
1.2.1.1电子状态
➢ 根据公式(1-3)可知,当体系的自由电子数在1024数量级时,自由电 子的能级间隔非常窄,基本上可以看成是连续分布的;但当体系的自 由电子数目为104数量级时,能级间隔就只有10-4eV左右;如果超微 粒子的尺寸进一步减小,则值将更大,这种情况下电子能级的不连 续性就不能忽略了。
空气中利用放电电弧,制备出氧化物的空气凝胶。
➢ 1945年Beek在研究金属薄膜的制备技术时指出,在低压惰性气体中 蒸发金属能够产生超微粉末。
➢ 第二次世界大战期间,日本学者上田良二等人采用气相蒸发法制备了 具有红外吸收能力的氧化锌超微粉末,粉末的粒径小于10nm。
1.1.2 超微粉末研究的发展历史
➢ 久保认为,当δ>kBT时,满足能级离散条件,费米统计分布规律失效, 不能再用经典公式来计算体系的总能量、比热和自旋磁化率等。考虑 温度影响,能级离散条件在比较低的温度下才能够成立。
布
1.2.1.1电子状态
(1)金属超微粒子具有强烈的保持电中性的倾向
从一个半径为r的超微粒子中取去或注
入一个电子时发生的静电能变化为
W e2 2r
(1-1)
当r=0.053nm时,W≈13.6eV; 当r=5.3nm时,W≈0.136eV; 当r=53nm时,W≈0.0136eV。
单个电子在300K 时的热能kBT约 为0.025eV,
1.2 超微粒子的基本特性
1.2.1 超微粒子的电子状态和晶格振动 1.2.1.1电子状态
日本学者久保亮五(Kubo)在量子统计力学的基础上分析了超微 粒子这种微小系统中的电子间相互作用规律,得出如下一些重要 结论:
(1) 金属超微粒子具有强烈的保持电中性的倾向 (2) 金属超微粒子中的自由电子能级分布离散,不再遵守费米统计分
r<10nm时,W(静电能)>>kBT(温度T时的热能)
因此,尽管r<10nm的微粒中自由电子总数可达104~106个,但很难从 中取出一个电子或粒子中注入一个电子,即金属超微粒子具有强烈的
保持电中性的倾向。
1.2.1.1电子状态
(2) 金属超微粒子中的自由电子能级分布离散,不再遵守费米统计分布
➢ 体系尺寸减小时,其自由电子数也很少。一个粒径为数nm的金属超 微粒子中含有的自由电子数在104量级。假定单个粒子为一个独立的 自由电子系统,电子在势阱内运动,考虑不同的边界条件,则在能量
1.1.2 超微粉末研究的发展历史 ➢ 19世纪90年代,随着胶体化学的建立,人们就开始研究直径在
1~100nm间的粒子系统,即所谓的胶体; ➢ Graham等人对胶体系统中的微粒子特性进行了研究,目的是获得具
有实际应用价值的颜料、粘合剂、添加剂和触媒等化学工业原料。
➢ 1900年初有人利用多种方法制备出了白黑催化剂。 ➢ 1921年Kohlschutter等人以Al、Bi、Cu、Fe、Ni等金属作为电极,在
现代粉末冶金技术
第一章 超微粉末的制备技术
1.1.1 超微粒子的定义
1.1概述
关于超微粒子的概念一直没有严格的定义。
20世纪80年代以前,日本学者通常把粒径在1m以下的粉末颗粒称为 超微粒子,将超微粒子的集合体称为超微粉末。
20世纪80年代以后,纳米材料的概念提出后,人们又把粒径小于 100nm的粉末颗粒称之为纳米粒子,将这种粒子的集合体称之为纳米 粉末。
1.1.2 超微粉末研究的发展历史 ➢ 70年代开始,日本开始重视超微粉末制备技术的研究,并确立了金属
超微粉末工业化生产规划,生产的磁性超微粉末被用于磁记录材料。
➢ 从20世纪70年代末到80年代初,关于超微粒子的结构、形貌和物性 的研究比较系统,在采用尺寸效应解释超微粒子特性方面获得了很大 成功。
➢ 而后,发现了超微粒子熔点下降现象;熔化过热现象;解释了超微粒 子的相变现象;研究了超微粒子的热力学特性;开发了超微粒子的应 用新领域。
1.1.2 超微粉末研究的发展历史
➢ 随着现代分析测试技术的迅速发展,特别是新型检测技术及设 备不断涌现,如拉曼光谱、高分辨电子显微镜、核磁共振、精 细XRD等分析手段的发展,使得对超微粒子的研究进入到了表 面原子结构、内部电子结构等微观层次。超微粉末的应用范围 涉及到粉末冶金、材料电子、化工、生物、医药和光学等众多 领域。
超微粒子(或纳米粒子)具有显著的体积效应、表面效应、量子尺寸效 应和宏观量子隧道效应,而且粒子尺寸越小,材料的物性变化就越显 著。
从广义上来说,凡是出现尺寸效应的粉末体系均可以纳入超微粒子的 范畴。
本文仍选择超微粒子为基本概念来介绍粒径在0.1m以下的微小粒子 的特性及制备方面的理论和技术问题。