传动齿轮磨削裂纹原因分析
磨削裂纹产生的原因及措施
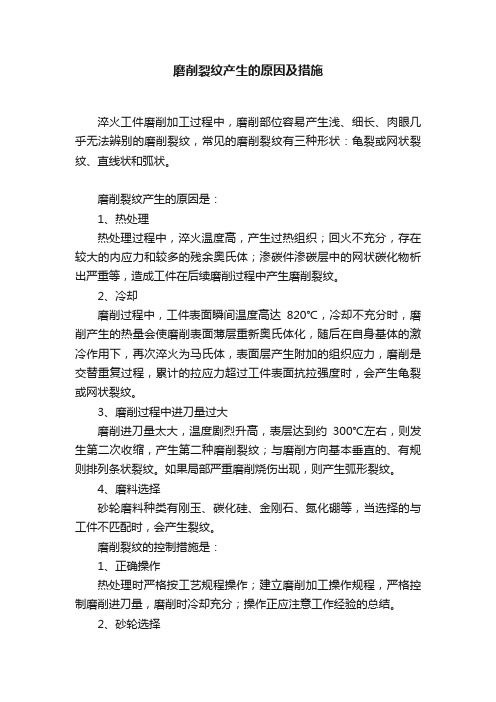
磨削裂纹产生的原因及措施淬火工件磨削加工过程中,磨削部位容易产生浅、细长、肉眼几乎无法辨别的磨削裂纹,常见的磨削裂纹有三种形状:龟裂或网状裂纹、直线状和弧状。
磨削裂纹产生的原因是:1、热处理热处理过程中,淬火温度高,产生过热组织;回火不充分,存在较大的内应力和较多的残余奥氏体;渗碳件渗碳层中的网状碳化物析出严重等,造成工件在后续磨削过程中产生磨削裂纹。
2、冷却磨削过程中,工件表面瞬间温度高达820℃,冷却不充分时,磨削产生的热量会使磨削表面薄层重新奥氏体化,随后在自身基体的激冷作用下,再次淬火为马氏体,表面层产生附加的组织应力,磨削是交替重复过程,累计的拉应力超过工件表面抗拉强度时,会产生龟裂或网状裂纹。
3、磨削过程中进刀量过大磨削进刀量太大,温度剧烈升高,表层达到约300℃左右,则发生第二次收缩,产生第二种磨削裂纹;与磨削方向基本垂直的、有规则排列条状裂纹。
如果局部严重磨削烧伤出现,则产生弧形裂纹。
4、磨料选择砂轮磨料种类有刚玉、碳化硅、金刚石、氮化硼等,当选择的与工件不匹配时,会产生裂纹。
磨削裂纹的控制措施是:1、正确操作热处理时严格按工艺规程操作;建立磨削加工操作规程,严格控制磨削进刀量,磨削时冷却充分;操作正应注意工作经验的总结。
2、砂轮选择1)尽可能选用锋利的砂轮,切削速度快,磨削效率高,磨削表面不易过热。
2)正确选择砂轮结构和硬度级别,以获得自由磨削效应。
3)陶瓷和金属作粘结剂的砂轮,适用于磨削热较高的场合;树脂粘结砂轮,适用磨削热较小的场合。
脆性较大的粘结剂,磨粒容易脱落,有利于使砂轮保持锐利状态。
4)SiC磨料磨削钢和铁基耐热合金时,产生强烈的化学磨损,刚玉类磨料磨削钢时无此反应。
相反,刚玉类磨料磨削玻璃、硅酸盐类陶瓷涂层时,会产生强烈的化学反应,SiC磨料无此反应。
3、如果已产生磨削裂纹,如果未超过加工余量,可进行多次低温回火,去除磨削应力,再按正确的磨削加工方法加工,磨去裂纹深度进行挽救。
机械传动齿轮失效问题分析与应对策略

机械传动齿轮失效问题分析与应对策略简介:机械传动齿轮是机械传动中最常用的部件之一。
它能够将动力从一个部件传递到另一个部件,提供准确、可靠的转速和扭矩转换。
然而,随着运行时间的增长,齿轮会发生磨损、断裂等问题,甚至会导致传动系统失效。
本文将分析机械传动齿轮失效的原因,并提出相应的应对策略。
一、齿轮失效原因(一)磨损在机械传动中,齿轮是直接接触的部件。
长时间使用后,会产生磨损现象,使齿轮失去表面光滑度,从而导致传递扭矩的能力下降,甚至失效。
另外,润滑不良、工作环境恶劣等因素也会加速齿轮磨损的过程。
例如,在没有黄油的情况下,齿轮磨损将更加严重。
(二)齿轮断裂齿轮断裂是指齿轮在运行过程中出现裂纹或破裂,导致传动系统失效。
齿轮断裂的原因可能是材料质量问题、设计问题、制造过程问题等。
如果齿轮的强度和韧性不足,它们容易断裂。
此外,过度负载和振动也会导致齿轮断裂。
(三)腐蚀腐蚀是由介质(如氧气、水、氯化物等)侵蚀导致的齿轮失效。
齿轮被腐蚀后,表面会产生锈斑、氧化层等,从而降低其防锈性能和强度。
对于工作环境中包含腐蚀性介质的传动系统,应采取特殊材料或涂层来保护齿轮。
(四)安装问题齿轮的安装过程非常重要。
如果安装不当,可能导致齿轮错位、偏心、轴与孔的相位差、轴的弯曲或变形等问题。
这些问题会导致齿轮失效或降低传动效率。
因此,正确的安装与对齐是避免齿轮失效的关键因素之一。
二、齿轮失效的应对策略(一)制定维护计划对于机械传动中的齿轮,备份计划是必不可少的。
应定期检查齿轮状态,如磨损、断裂等,及时进行润滑、更换和维修。
制订完善的维护计划能够减少齿轮失效,延长设备使用寿命。
(二)选用合适的材料齿轮的材料和强度与意外磨损和断裂息息相关。
开发并使用高品质和高强度的合金材料,可提高齿轮的寿命以及防止齿轮失效。
(三)加强润滑润滑在防止齿轮失效中发挥重要作用。
正确使用黄油,以保持齿轮表面光滑和防止磨损。
此外,污染和过热的润滑剂也是齿轮失效的根本原因之一。
行星齿轮齿根裂纹渐进故障分析
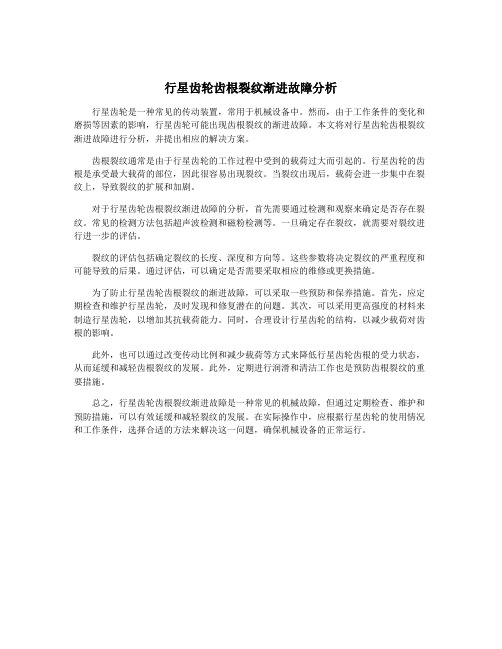
行星齿轮齿根裂纹渐进故障分析
行星齿轮是一种常见的传动装置,常用于机械设备中。
然而,由于工作条件的变化和磨损等因素的影响,行星齿轮可能出现齿根裂纹的渐进故障。
本文将对行星齿轮齿根裂纹渐进故障进行分析,并提出相应的解决方案。
齿根裂纹通常是由于行星齿轮的工作过程中受到的载荷过大而引起的。
行星齿轮的齿根是承受最大载荷的部位,因此很容易出现裂纹。
当裂纹出现后,载荷会进一步集中在裂纹上,导致裂纹的扩展和加剧。
对于行星齿轮齿根裂纹渐进故障的分析,首先需要通过检测和观察来确定是否存在裂纹。
常见的检测方法包括超声波检测和磁粉检测等。
一旦确定存在裂纹,就需要对裂纹进行进一步的评估。
裂纹的评估包括确定裂纹的长度、深度和方向等。
这些参数将决定裂纹的严重程度和可能导致的后果。
通过评估,可以确定是否需要采取相应的维修或更换措施。
为了防止行星齿轮齿根裂纹的渐进故障,可以采取一些预防和保养措施。
首先,应定期检查和维护行星齿轮,及时发现和修复潜在的问题。
其次,可以采用更高强度的材料来制造行星齿轮,以增加其抗载荷能力。
同时,合理设计行星齿轮的结构,以减少载荷对齿根的影响。
此外,也可以通过改变传动比例和减少载荷等方式来降低行星齿轮齿根的受力状态,从而延缓和减轻齿根裂纹的发展。
此外,定期进行润滑和清洁工作也是预防齿根裂纹的重要措施。
总之,行星齿轮齿根裂纹渐进故障是一种常见的机械故障,但通过定期检查、维护和预防措施,可以有效延缓和减轻裂纹的发展。
在实际操作中,应根据行星齿轮的使用情况和工作条件,选择合适的方法来解决这一问题,确保机械设备的正常运行。
机械传动齿轮失效问题分析与应对策略

机械传动齿轮失效问题分析与应对策略机械传动齿轮在使用过程中可能会出现失效问题,这些问题会影响机械传动的正常运转,甚至导致机械设备的故障。
本文将对机械传动齿轮失效问题进行分析,并提出相应的应对策略。
机械传动齿轮的失效问题主要包括齿轮齿面磨损、齿轮齿面断裂、齿轮齿面剥落等。
这些问题的主要原因包括以下几个方面:1. 不合理的齿轮设计。
齿轮的设计应考虑到传动的扭矩、转速等参数,以确保齿轮运转期间不会超过其承受能力。
2. 齿轮制造质量问题。
齿轮的制造质量对其使用寿命至关重要。
如果齿轮制造过程中出现问题,如质量不合格、热处理不足等,都可能导致齿轮失效。
3. 齿轮使用不当。
齿轮在使用过程中需要注重保养和维护,否则会加速齿轮的磨损和失效。
不及时更换润滑油、不定期检查齿轮磨损情况等,都会对齿轮的使用寿命产生负面影响。
针对以上问题,我们可以采取以下应对策略:1. 合理设计齿轮。
在设计齿轮时,应根据传动的扭矩、转速等参数选择合适的材料,并进行适当的强度校核。
还需要确保齿轮的齿面硬度达到要求,以提高其耐磨性和使用寿命。
2. 严格控制齿轮制造质量。
在齿轮制造过程中,应加强质量控制,确保每个工序的合格率。
还应对齿轮进行必要的热处理,以提高其硬度和耐磨性。
3. 加强齿轮的保养和维护。
定期更换齿轮润滑油,并定期检查齿轮的磨损情况,及时进行维修和更换。
还可以采取一些预防措施,如添加润滑剂、减少齿轮负载等,以延长齿轮的使用寿命。
机械传动齿轮的失效问题是影响机械设备正常运转的重要原因。
通过合理设计齿轮、严格控制制造质量以及加强齿轮的保养和维护,可以有效降低齿轮失效的概率,延长机械设备的使用寿命。
对于机械传动齿轮的失效问题应引起重视,并及时采取相应的应对策略。
齿轮传动系统失效原因分析及预测研究

齿轮传动系统失效原因分析及预测研究一、齿轮传动系统的基本结构齿轮传动系统是一种常见的动力传递装置,它利用齿轮之间的啮合来传递动力,实现旋转运动的传递。
齿轮传动系统包括齿轮、轴承、密封装置等组成部分。
其中,齿轮是齿轮传动系统的核心部件,其质量和精度决定着齿轮传动系统的正常运转和寿命。
二、齿轮传动系统失效原因分析齿轮传动系统的失效原因多种多样,常见的有以下几种:1.齿面磨损:齿轮传动系统长时间受重载和高速运转的作用,齿面容易出现磨损。
齿面磨损程度越大,齿轮的噪声和振动就越大,从而导致齿轮传动系统失效。
2.齿面断裂:齿轮传动系统在受到过大的冲击力时,齿面容易出现断裂。
齿面断裂会造成齿轮传动系统的失效,严重的会导致整个机械设备的损坏。
3.齿面损伤:齿轮传动系统在长期使用过程中,齿面会产生小细节损伤,这些小损伤在长时间的使用下,会导致齿轮传动系统的噪声增加,甚至损坏齿轮。
4.轴承过载:齿轮传动系统中轴承的过载会造成轴承的损坏,从而导致整个齿轮传动系统的失效。
轴承过载的原因可能是机械设备的设计问题,或者是在使用过程中对机械设备的错误使用和维护。
五、齿轮传动系统的预测研究为避免齿轮传动系统失效对机械设备的影响,预测研究应成为重点,将其应用到机械设备的日常维护中。
目前,齿轮传动系统预测研究的主要方法有以下几种。
1.振动分析法:通过振动信号采集技术,对振动信号进行分析,从而判断齿轮传动系统的正常或失效状态。
2.声学特性分析法:通过分析齿轮传动系统的噪声谱,可以判断齿轮的状态以及未来的寿命。
3.温度信号分析法:通过采集齿轮传动系统的温度变化,可以对齿轮传动系统的运行状态进行判断。
4.油液分析法:通过对齿轮传动系统中的润滑油进行分析,可以判断齿轮的磨损程度和未来的寿命。
总结:齿轮传动系统是机械设备的核心组成部分,为避免其失效对机械设备的影响,应加强对其预测研究与维护。
通过振动分析法、声学特性分析法、温度信号分析法和油液分析法等技术手段,可以对齿轮传动系统的正常或失效状态进行判断,保障机械设备的正常运行和寿命。
磨削裂纹产生的原因是磨削力过大
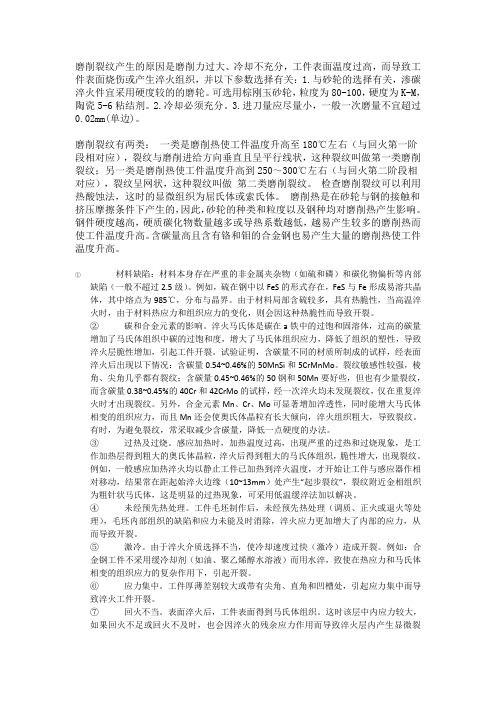
磨削裂纹产生的原因是磨削力过大、冷却不充分,工件表面温度过高,而导致工件表面烧伤或产生淬火组织,并以下参数选择有关:1.与砂轮的选择有关,渗碳淬火件宜采用硬度较的的磨轮。
可选用棕刚玉砂轮,粒度为80-100,硬度为K-M,陶瓷5-6粘结剂。
2.冷却必须充分。
3.进刀量应尽量小,一般一次磨量不宜超过0.02mm(单边)。
磨削裂纹有两类:一类是磨削热使工件温度升高至180℃左右(与回火第一阶段相对应),裂纹与磨削进给方向垂直且呈平行线状,这种裂纹叫做第一类磨削裂纹;另一类是磨削热使工件温度升高到250~300℃左右(与回火第二阶段相对应),裂纹呈网状,这种裂纹叫做第二类磨削裂纹。
检查磨削裂纹可以利用热酸蚀法,这时的显微组织为屈氏体或索氏体。
磨削热是在砂轮与钢的接触和挤压摩擦条件下产生的,因此,砂轮的种类和粒度以及钢种均对磨削热产生影响。
钢件硬度越高,硬质碳化物数量越多或导热系数越低,越易产生较多的磨削热而使工件温度升高。
含碳量高且含有铬和钼的合金钢也易产生大量的磨削热使工件温度升高。
①材料缺陷:材料本身存在严重的非金属夹杂物(如硫和磷)和碳化物偏析等内部缺陷(一般不超过2.5级)。
例如,硫在钢中以FeS的形式存在,FeS与Fe形成易溶共晶体,其中熔点为985℃,分布与晶界。
由于材料局部含硫较多,具有热脆性,当高温淬火时,由于材料热应力和组织应力的变化,则会因这种热脆性而导致开裂。
②碳和合金元素的影响。
淬火马氏体是碳在a铁中的过饱和固溶体,过高的碳量增加了马氏体组织中碳的过饱和度,增大了马氏体组织应力,降低了组织的塑性,导致淬火层脆性增加,引起工件开裂。
试验证明,含碳量不同的材质所制成的试样,经表面淬火后出现以下情况:含碳量0.54~0.46%的50MnSi和5CrMnMo。
裂纹敏感性较强,棱角、尖角几乎都有裂纹;含碳量0.45~0.46%的50钢和50Mn要好些,但也有少量裂纹,而含碳量0.38~0.45%的40Cr和42CrMo的试样,经一次淬火均未发现裂纹,仅在重复淬火时才出现裂纹。
行星齿轮齿根裂纹渐进故障分析

行星齿轮齿根裂纹渐进故障分析
行星齿轮是常用于减速驱动的重要机械元件之一,其具有结构简单、传动平稳、负载
能力强等优点,因此广泛应用于机械设备中。
但是,在使用过程中,行星齿轮也会存在着
一些故障,比如齿根裂纹渐进故障。
下面,我们来具体分析一下这种故障的原因和表现,
以期能更好地解决这一问题。
行星齿轮齿根裂纹是一种比较常见的故障,其主要原因在于长时间的使用过程中会产
生疲劳损伤。
当行星齿轮进行旋转时,由于齿轮上的载荷持续作用,使得齿根处受到重压,从而导致随时间的推移,齿轮齿根处产生裂纹。
如果这些裂纹没有得到及时的修复或更换,行星齿轮齿根裂纹会逐渐扩展,严重影响到齿轮的使用效果和寿命。
1. 行星齿轮的噪声增加:一旦行星齿轮的齿根出现裂纹,其转动时就会发出清晰、
明显的刺耳噪声,如果这种噪声长时间存在,就很可能是行星齿轮齿根裂纹的信号。
2. 行星齿轮的振动增强:行星齿轮转动时,如果发现行星齿轮的振动比以往明显增强,那么就很有可能是因为其齿根处出现了裂纹,使得行星齿轮的整体摆动增大。
3. 行星齿轮的传动效率下降:当行星齿轮受到齿根处裂纹的影响时,会导致行星齿
轮的传动效率急剧下降,因此如果齿轮工作效率下降很明显,那么需要检查齿根是否出现
了裂纹。
通过上述早期信号可以检测到行星齿轮齿根裂纹,一旦发现这些征兆,就需要及时采
取相应的对策和处理,以免行星齿轮的使用寿命受到影响或者出现更严重的故障。
总结来说,行星齿轮齿根裂纹是一种常见的故障,其主要原因在于长期使用中的疲劳
损伤。
早期检测行星齿轮齿根裂纹的征兆可以帮助我们及时采取补救措施,保障齿轮的正
常使用效果与寿命。
磨削裂纹的形成与分析

磨削裂纹的形成:发动机上用的各种轴类零件如驱动轴、凸轮轴、曲轴、摇臂轴等在加工过程中需要热处理,但热处理后淬硬或经过渗碳淬火的轴类零件,在磨削过程中由于表面显微组织发生转变而形成大量的裂纹,即磨削裂纹。
下面就磨削裂纹的形成及特征加以阐述。
一、磨削裂纹的产生:(一)磨削裂纹的生成轴类零件在磨削过程中要产生大量的热量,这些热量只限于表面极薄的区域内,它足以使其表面温度达到800℃以上,而且升温极快。
如果磨削时冷却不够充分,将导致表面层的显微组织重新奥氏体化,并再次淬火成为马氏体。
因而使工件表面层产生极大的附加组织应力,同时由于表面温升极快,造成很大的热应力,当组织应力和热应力叠加超过了材料的强度极限时,被磨削的表面就会出现磨削裂纹。
(二)磨削裂纹形成的影响因素:1、组织结构所谓组织结构方面的影响因素有碳化物的形态与分布,残余奥氏体的数量以及非金属夹杂物。
显微组织中碳化物的形态、分布影响着磨削裂纹的生成,如果碳化物数量较多,颗粒较大,分布不均或集聚存在时,将明显地分割金属的基体,降低其强度。
尤其当以断续网状析出时,则会严重地削弱晶间结合力,明显地影响热传导,从而加剧磨削裂纹生成。
如果碳化物细小、分布均匀,则有利于分散磨削应力,从而减少生成磨削裂纹的机率。
零件磨削时显微组织中的残余奥氏体因受磨削热的影响必将发生分解,逐渐转变为马氏体,引起工件表面体积膨胀,而导致组织应力的产生,进而促进裂纹的形成。
因此,工件内部残余奥氏体量较高时,易于产生磨削裂纹。
2、热处理工艺经过淬火而不进行回火的轴件,对磨削裂纹的形成是非常敏感的。
因为磨削时产生的磨削热足以使表层淬火马氏体发生转变,碳化物析出,体积减少。
造成了工件表面与内部的比容差,引起较大的内应力,进而形成裂纹。
轴件有时回火不足,在磨削时也容易形成裂纹。
由此可见,对淬火后的零件必须进行充分地回火。
但是为了保证工件达到一定硬度的要求,回火温度不能任意提高。
因此必须采用合适的磨削工艺,使工件表面受热的温度不超过回火温度。
- 1、下载文档前请自行甄别文档内容的完整性,平台不提供额外的编辑、内容补充、找答案等附加服务。
- 2、"仅部分预览"的文档,不可在线预览部分如存在完整性等问题,可反馈申请退款(可完整预览的文档不适用该条件!)。
- 3、如文档侵犯您的权益,请联系客服反馈,我们会尽快为您处理(人工客服工作时间:9:00-18:30)。
2012年1月内蒙古科技与经济January2012
第2期总第252期InnerMongoliaScienceTechnology&EconomyNo.2TotalNo.252
传动齿轮磨削裂纹原因分析
X
蔡 红
(内蒙古第一机械集团有限公司,内蒙古包头 014030)
摘 要:本文对车辆传动齿轮开裂件进行宏观分析、硬度检测、化学成分分析、显微组织及裂纹分
析,探讨裂纹形成机理,就其裂纹形成原因提出分析意见及改进措施。解剖分析结果表明,零件在磨削过
程中受到了过大的磨削力作用和磨削热作用,使表层发生塑性变形及相变,造成拉应力状态,导致裂纹
源产生,形成表面磨削裂纹。
关键词:齿轮;磨削;裂纹
中图分类号:TG580.6 文献标识码:A 文章编号:1007—6921(2012)02—0140—03
齿轮是车辆传动操纵系统的关键零部件,主要承受接触应力、摩擦力、冲击应力等,用低碳合金结构钢制造,主要工艺流程为:原材料→渗碳淬火回火→磨外圆、端面→装配→使用。生产中准备装配时发现两件齿轮在右端面(靠近长轴的齿轮端面)上有细小裂纹,造成零件失效报废,影响生产和质量。为查明裂纹产生原因,笔者选取其中较典型的一件开裂件解剖分析,对其进行宏观观察、化学成分分析、硬度检测分析、金相组织及裂纹分析,探讨裂纹形成机理,就其开裂原因提出分析意见及改进措施。1 实验结果1.1 宏观分析开裂件宏观形貌及裂纹位置见图1所示,该零件所发现裂纹非常细小,肉眼不易分辨,在HiroxKH-3000三维视频显微系统(美国)下观察,这些
细小条状裂纹均在齿轮右端面(齿轮长轴一侧)上,
裂纹宏观形貌见图2,径向分布,排列较有规则,呈细
小、聚集、断续串接特征,垂直于磨削方向,裂纹长度
约1mm~7mm,多达上百条,部分裂纹已呈网状分
布。
图1 开裂齿轮宏观形貌及裂纹位置
X
收稿日期5作者简介蔡红(6—),女,内蒙古一机集团车辆工程研究院理化室工作,高级工程师,从事金相分析、失效分析及热处理工作二十余年,本项目来源于生产实际。140:2011-11-2
:198
蔚红传动齿轮磨削裂纹原因分析2012年第2期
1.2 化学成分分析在开裂件基体取样进行化学成分分析,分析结果符合图纸技术要求。
1.3 显微组织及裂纹分析1.3.1 垂直于裂纹取金相样,在OlympusGX51倒置式金相显微镜(日本)下观察。裂纹浅而细小,相互平行,排列规则,尾部尖细且沿晶扩展,扩展方向垂直于齿轮端面即磨削平面,为等深裂纹,深度在0.45mm~0.60mm范围,裂纹中间宽两头细,有的裂纹与磨削表面不相通,有的裂纹与基体中的非金属夹杂物连通,见图3、图4。基体(远离裂纹)非金属夹杂物按照GB/T10561-2009标准评为A1.0级、B0.5级。经4%HNO3酒精溶液浸蚀后观察,可见该齿轮经过表面渗碳处理及淬火回火热处理,右端面渗层组织为高碳回火马氏体加碳化物加少量残余奥氏体,渗层磨削表面组织有明显转变,见图5,深度在0.40mm左右,图5中最表面组织为细小二次淬火马氏体,深度在0~0.024mm,随后为被热影响的过渡层,见图6;裂纹两侧及尾部无氧化脱碳现象;心部组织为低碳板条回火马氏体。1.3.2 将齿轮轮齿横向解剖,在OlympusGX51倒置式金相显微镜下观察试样横截面。轮齿无裂纹及其他异常;经4%HNO3酒精溶液浸蚀后观察,可见该轮齿经过表面渗碳处理及淬火回火热处理,节圆及齿顶渗碳层处碳化物、马氏体及残余奥氏体分别评为2级、1级,见图7,符合WJ730-82标准要求,心部组织为低碳板条回火马氏体,见图8。从零件材质来看,零件渗层和基体金相组织、非金属夹杂物均符合图纸技术要求。 硬度及层深检测分析(吴忠洛氏硬度计及日本FM显微硬度计)基体硬度为41.5HRC,符合工艺要求;齿
轮右端面表面硬度为58.5HRC,符合图纸技术要
求;用硬度法检测齿轮右端面有效硬化层深,结果
为CHD550HV0.1=0.63mm,检测轮齿节圆处有效
硬化层深,结果为CHD550HV0.1=0.67mm,符合
图纸技术要求;分别从齿轮右端面及轮齿节圆处
向心部检测显微硬度,硬度梯度曲线见图9、图10,数
据见表1、表2,可以看出,右端面渗层表面0.20
mm
内有明显的硬度降低。
表1 右端面渗层显微硬度
距表面距离(mm)0.030.100.200.300.400.500.600.700.800.901.00
硬度(HV)517512573579586574555539502465452
距表面距离(mm)1.101.201.301.401.501.601.701.801.902.00
硬度(HV)439416409405402402391398398391
图 右端面渗层硬度梯度曲线1.47009
141
总第252期 内蒙古科技与经济
表2 轮齿节圆处渗层显微硬度距表面距离mm)0.030.100.200.300.400.500.600.700.800.901.00硬度(HV)646660661653625592580539512474465距表面距离(mm)1.101.201.301.401.501.601.701.801.902.00硬度(HV)452444431424428425424425415416图10 轮齿节圆处渗层硬度梯度曲线2 分析与讨论磨削裂纹属第一类热处理缺陷,它产生于热处理之后的磨削加工工序。淬硬的工具钢零件,或经渗碳、碳氮共渗并进行淬火的零件,在随后的磨削加工时有时会出现大量的磨削裂纹[1]。笔者所述零件用钢为渗碳钢20Cr2Ni4A,即出现了类似裂纹。一般认为,零件在磨削加工过程中,当形成的残余拉应力超过自身材料的强度极限时,零件表面就会出现裂纹。因此,零件表面的应力状态是磨削裂纹形成的关键。首先,对渗碳钢来说,要求表层硬度高、强度高、耐磨性好,心部应有良好的韧性。只有通过渗碳得到表面和心部成分的差异,进行恰当的热处理,才能强化表层,提高耐磨性,并获得具有良好韧性和一定强度的心部组织[2]。但零件表面渗碳会引起零件应力状态的变化。渗碳淬火后零件心部受压缩应力,渗碳层受拉伸应力,这种拉应力状态是渗碳层产生裂纹的促进因素。其次,磨削加工也会改变零件表面应力状态。磨削表面的残余应力是由于磨削过程金属容积发生变化等因素造成的。其中磨削温度的不均匀将形成热应力,一般为拉应力;由于金属组织的变化将产生相变应力,可能为拉应力或压应力;由于磨削过程塑性变形的不均匀形成塑变应力,一般为压应力。磨削表面的残余应力应是以上三者的复合[3]。一般零件在粗磨或违章条件下,表层0.25mm内会发生硬度改变,0.15mm内会看到金相变化,而零件在精磨或低应力状态下,只会在表层0.04mm和0.013mm内看
到硬度改变和金相变化[1]。本文所述齿轮右端面在
渗碳淬火时整个渗层都得到高碳回火马氏体组织加
少量残余奥氏体,但在随后的周向磨削加工过程中,
表面0~0.024mm内生成了细小二次淬火马氏体说
明,磨削产生的磨削热使零件表面温度达到钢的
AC3点以上,而表面0.40mm内发生了马氏体分解、
残余奥氏体向马氏体转变等相变,则说明该处温度
达到了150℃~200℃,这些相变使表面体积缩小,而
靠近中心的马氏体不受热,体积不变化,这种内外体
积差和温差使表层承受拉应力;另外,比较齿轮右端
面至心部的硬度梯度曲线和轮齿节圆至心部的硬度
梯度曲线可以看出,齿轮右端面表层约0.70mm内
硬度降低,0.20mm内尤为明显,这是由于渗层表面
二次淬火带来金相组织转变,说明零件右端面在磨
削过程中有过大的进刀量并瞬间产生大量的磨削热
量,使表层发生塑性变形,热应力和组织应力综合造
成拉应力状态,它们是裂纹产生的主要原因。
综上分析认为,磨削时较大的磨削应力和磨削
热作用使齿轮表面发生了金相组织变化和硬度变
化,同时也改变了残余应力状态,当产生的拉伸残余
应力超过自身的抗拉强度时,在零件次表层即拉应
力最大处萌生裂纹源,并在应力状态进一步改变的
过程中扩展形成裂纹,为磨削裂纹。
3 结论
笔者所解剖齿轮基体化学成分、层深、硬度、金
相组织、非金属夹杂物等符合图纸技术要求。
齿轮表面裂纹为磨削裂纹,其主要形成原因为
过大的磨削应力和磨削热作用。
4 改进措施及建议
严格执行磨削工艺,防止砂轮过细或过钝,通过
加大磨削冷却液容量和减少磨削进给量,降低磨削
温度,避免相变发生。
改进磨削工艺,采取低应力、小磨削量工艺参
数,防止磨削裂纹。
[参考文献]
[1] 王广生,等.金属热处理缺陷分析及案例[M].
北京:机械工业出版社,1997.
[2] 齐宝森.化学热处理技术[M].北京:化学工
业出版社,2006.
[3] 王国凡.材料成形与失效[M].北京:化学工
业出版社,2002.
(上接第139页) 对GBW01422a硅铁标样按选择的条件进行了10次平行测定,测定结果及RSD见表5。表5 GBW01422a硅铁标样的测定结果元素测定结果平均值(%)标样认定值(%)RSD(%)碳0.0817、0.0821、0.0822、0.0823、0.0815、0.0826、、、33、333硫5、3、、3、、、35、3、6、363 结论
利用正交法对硅铁中碳硫的测定条件进行了优
化,确定了硅铁中碳硫测定的最佳条件,方法准确、
精密度好,能满足生产要求。
[参考文献]
[1] 国内理化检验标准汇编,化学部分(第二辑)中
[M]上海机械电子工业部上海材料研究所,0.08090.08470.080.0820.080.0821.10.0040.0040.00410.0080.00420.00490.000.0070.0040.0090.00420.0049.7.:
1990.
142