磨削裂纹
中频淬火凸轮轴磨削裂纹产生原因及对策
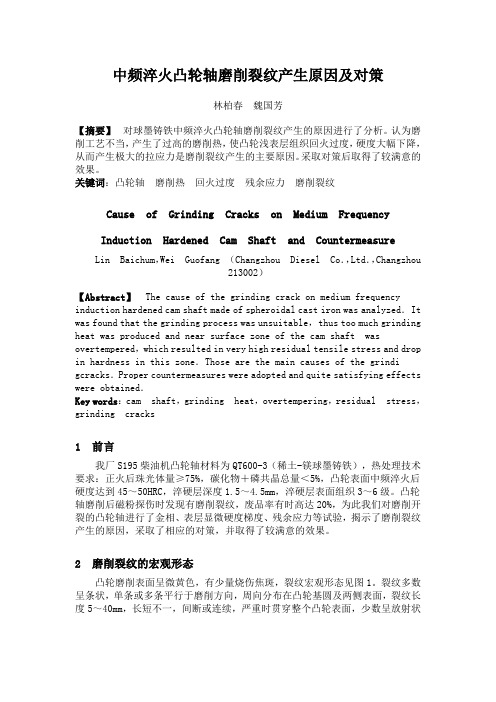
中频淬火凸轮轴磨削裂纹产生原因及对策林柏春魏国芳【摘要】对球墨铸铁中频淬火凸轮轴磨削裂纹产生的原因进行了分析。
认为磨削工艺不当,产生了过高的磨削热,使凸轮浅表层组织回火过度,硬度大幅下降,从而产生极大的拉应力是磨削裂纹产生的主要原因。
采取对策后取得了较满意的效果。
关键词:凸轮轴磨削热回火过度残余应力磨削裂纹Cause of Grinding Cracks on Medium FrequencyInduction Hardened Cam Shaft and CountermeasureLin Baichum,Wei Guofang (Changzhou Diesel Co.,Ltd.,Changzhou213002)【Abstract】The cause of the grinding crack on medium frequency induction hardened cam shaft made of spheroidal cast iron was analyzed.It was found that the grinding process was unsuitable,thus too much grinding heat was produced and near surface zone of the cam shaft was overtempered,which resulted in very high residual tensile stress and drop in hardness in this zone.Those are the main causes of the grindi gcracks.Proper countermeasures were adopted and quite satisfying effects were obtained.Key words:cam shaft,grinding heat,overtempering,residual stress,grinding cracks1 前言我厂S195柴油机凸轮轴材料为QT600-3(稀土-镁球墨铸铁),热处理技术要求:正火后珠光体量≥75%,碳化物+磷共晶总量<5%,凸轮表面中频淬火后硬度达到45~50HRC,淬硬层深度1.5~4.5mm,淬硬层表面组织3~6级。
磨床磨削裂纹原因的分析与对策

磨床磨削裂纹的产生原因分析与对策分析磨削裂纹的产生原因,与磨削前各加工过程所产生的缺陷,如材料表层中存在网状碳化物、非金属夹杂、组织疏松、成分偏析、晶界上的淬火变形等有关;裂纹通常与烧伤同时出现。
当工件表层的残余拉应力超过材料的抗拉强度时,就会产生磨削裂纹。
磨削裂纹的产生原因和减小磨削裂纹的方法如下:1、正确选用砂轮,例如可采用颗粒较粗、较软、组织较疏松的砂轮;保证修整后砂轮的锋利。
2、保证磨削时的冷却条件,设法使冷却液能有效地渗透到工件的磨削区中。
3、合理选择磨削用量,例如提高工件的转速,采用较小的径向进给量等。
磨削时如果磨削工艺参数选择或操作不当,工件表面温度达到150~200度时表面因马氏体分解,体积缩小,而中心马氏体不收缩,使表层承受拉应力而开裂,产生的裂纹会与磨削方向垂直,裂纹相互平行。
当磨削温度在200度以上时,表面由于产生索氏体或托氏体,这时表层发生体积收缩,而中心则不收缩,使表层拉应力超过脆断抗力而出现龟裂现象。
4、工件表面渗层碳浓度过高,会使工件表面产生过多的残余奥氏体.从而容易导致产生烧伤和裂纹。
因此,表面碳浓度增加,则降低了磨削性能,一般表面碳浓度应控制在0.75%-0.95%范围以内。
5、碳化物分布应均匀,粒度平均直径不大于0.001m;碳化物形态应为球状、粉状或细点状沿网分布,不允许有网状或角状碳化物。
6、热处理时.表面或环境保护不当会产生表面氧化,这样在工件上就会产生一层薄的脱碳层,这层软的脱碳层会引起砂轮过载或过热,从而造成表面回火,工件磨削时容易出现裂纹。
7、如果冷却不充分,磨削时零件表面温度有时可能高达820~840度或更高,则由于磨削形成的热量足以使表面薄层重新奥氏体化,并再次淬火而形成淬火马氏体,表面形成二次淬火的金相组织。
此外,磨削形成的热量使零件表面温度升高极快,这种组织应力和热应力导致磨削表面出现磨削裂纹。
8、使用金刚滚轮修整砂轮的内滚道磨床加工的零件有裂纹,还与配置的金刚滚转速、转向、金刚石的粒度、磨损情况、修砂轮时电主轴的转速、修砂轮时与滚轮磨合停留的时间等因素有关。
磨削裂纹产生原因及预防措施

技术讲座二磨削裂纹产生机理与防止措施1 磨削裂纹的特征磨削裂纹形状特别,仅发生在磨削面上,与淬火裂纹在宏观上观察明显不同,且磨削裂纹深度较浅。
较轻的磨削裂纹垂直于或接近垂直于磨削方向呈平行分布,称之为第Ⅰ类裂纹。
较严重的裂纹呈龟甲状,称之为第Ⅱ类裂纹,习惯上叫做龟裂。
其深度大致为0.03-0.20mm。
用酸浸蚀后裂纹更加明显易见。
2 磨削裂纹的产生机理磨削裂纹的产生皆由内部应力诱发所致,磨削裂纹产生的主要原因是磨削热引起的。
工件磨削时磨削接触区温度高达400℃,磨削接触点的温度更是高达800℃以上。
磨削热导致工件表面产生热应力和组织相变而引起体积变化的相变应力。
渗碳淬火钢的表面组织是高碳马氏体和一定数量的残余奥氏体,处于膨胀状态(未经回火处理尤为严重);磨削热尤其是砂轮和工件接触区的高热会迅速使接触区表面温度升高,当表面温度升高到100℃~200℃左右离开接触区被冷却液迅速冷却时,必然将产生收缩,这是第一次收缩。
这种收缩仅发生在表面,由于其基体马氏体仍处于膨胀状态,从而使表面层承受拉应力而产生微裂纹,这就是第Ⅰ类裂纹。
随着磨削加工的继续当表面温度升至300℃~400℃时,表面层发生相引起变体积缩小,导致表面再次产生收缩,从而产生第Ⅱ类裂纹。
由于马氏体的膨胀收缩是随着钢中含碳量的增加而增大,故渗碳淬火钢(高碳工具钢)表面产生磨削裂纹尤为严重和常见。
渗碳淬火工件表面的残余奥氏体,在磨削时受磨削热的影响即发生分解,逐渐转变为马氏体,这种新生的马氏体集中于表面,引起零件局部体积膨胀,加大了零件表面应力,导致磨削应力集中,继续磨削则容易加速磨削裂纹的产生;此外,新生的马氏体脆性较大,继续磨削也容易加速磨削裂纹的产生。
另一方面,在磨床上磨削工件时,对工件既是压力,又是拉力,助长了磨削裂纹的形成。
如果在磨削时冷却不充分,则由于磨削而产生的热量,足以使磨削表面薄层重新奥氏体化(727℃以上),随后再次淬火转变为淬火马氏体。
磨削裂纹的典型特征
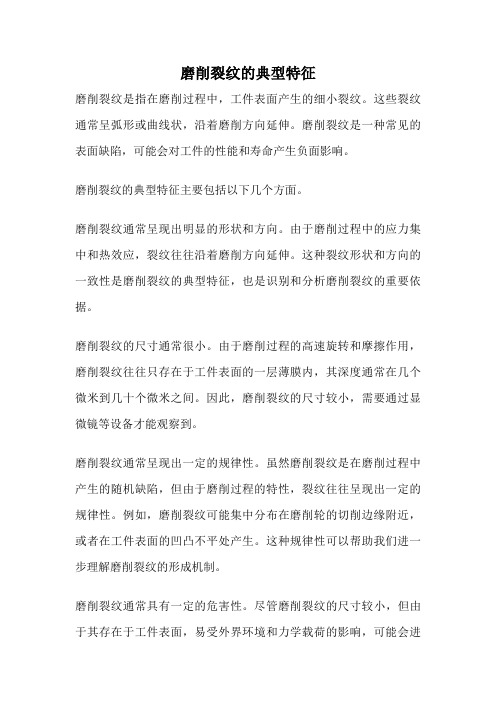
磨削裂纹的典型特征磨削裂纹是指在磨削过程中,工件表面产生的细小裂纹。
这些裂纹通常呈弧形或曲线状,沿着磨削方向延伸。
磨削裂纹是一种常见的表面缺陷,可能会对工件的性能和寿命产生负面影响。
磨削裂纹的典型特征主要包括以下几个方面。
磨削裂纹通常呈现出明显的形状和方向。
由于磨削过程中的应力集中和热效应,裂纹往往沿着磨削方向延伸。
这种裂纹形状和方向的一致性是磨削裂纹的典型特征,也是识别和分析磨削裂纹的重要依据。
磨削裂纹的尺寸通常很小。
由于磨削过程的高速旋转和摩擦作用,磨削裂纹往往只存在于工件表面的一层薄膜内,其深度通常在几个微米到几十个微米之间。
因此,磨削裂纹的尺寸较小,需要通过显微镜等设备才能观察到。
磨削裂纹通常呈现出一定的规律性。
虽然磨削裂纹是在磨削过程中产生的随机缺陷,但由于磨削过程的特性,裂纹往往呈现出一定的规律性。
例如,磨削裂纹可能集中分布在磨削轮的切削边缘附近,或者在工件表面的凹凸不平处产生。
这种规律性可以帮助我们进一步理解磨削裂纹的形成机制。
磨削裂纹通常具有一定的危害性。
尽管磨削裂纹的尺寸较小,但由于其存在于工件表面,易受外界环境和力学载荷的影响,可能会进一步扩展和发展。
这些裂纹扩展可能导致工件的强度和耐久性下降,甚至引发工件的断裂和失效。
因此,磨削裂纹的存在需要引起足够的重视,并采取相应的措施进行控制和修复。
磨削裂纹具有明显的形状和方向、小尺寸、一定的规律性和一定的危害性等典型特征。
对于工程师和磨削加工人员来说,了解和掌握这些特征,可以帮助他们更好地识别和分析磨削裂纹,从而采取相应的措施进行预防和处理。
通过合理选择磨削参数、优化磨削工艺和采用适当的工艺控制措施,可以最大程度地降低磨削裂纹的发生率,提高工件的质量和性能。
陶瓷材料磨削裂纹成因分析
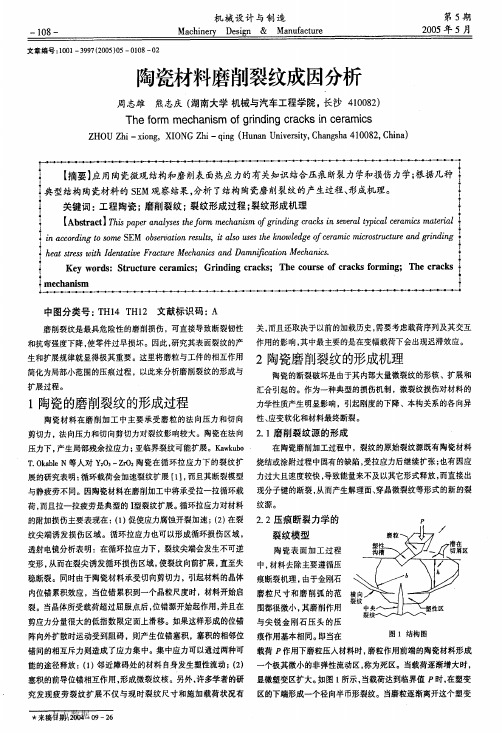
万方数据第5期周志雄等:陶瓷材料磨削裂纹成因分析一109一区时,作用其上的载荷也逐渐减少,在这个显微塑变及其产生的残余应力的作用下,沿径向裂纹的横向出现横向裂纹,并延伸至材料表面形成裂纹区的断裂从基本剥落【2]。
2.3疲劳裂纹的扩展动力对于弹塑性陶瓷材料而言,疲劳裂纹的扩展不是一个连续过程,而是一个钝化启裂与稳定扩展交替进行的过程。
疲劳裂纹的扩展,实际上是裂尖局部区域即断裂过程区内材料的不断分离。
因此,它首先必须满足切断裂尖原子或分子结合的条件,另外,裂纹的稳定扩展除受裂尖前缘局部条件控制外,还受裂尖前端耗散区能流的全局状态控制。
随着裂纹的扩展,一些输入能量转变成储存在弹性卸载区内的残余应力能;一些因发热和材料的再组织而被耗散;其余则转变为材料的表面能。
2.4磨削热裂纹的扩展动力由于陶瓷的散热能力差,即使磨削时使用冷却液进行冷却;磨削区的显微塑变和摩擦会在磨削表面引起很高的磨削温度。
由此在表面产生的热压应力为毋,,且有毋,=竺{掣。
当这p部分热影响区的表面冷却,不可恢复的表面塑性变形将产生残余拉应力∞r,以rm盯sr如果达到材料的断裂极限,磨削表面就产生热裂纹。
该微裂纹与磨痕方向没有确定的取向关系。
裂纹的主要形式有:表面尺寸较小,向次表面延伸较深的压痕效应;表面尺寸较大的细长网状热裂纹;沿晶粒扩展的晶界间隙裂纹;不连续显微塑变裂纹。
3实验结果及分析王西彬等在常用磨削用量条件下得到以下SEM观测结果【4】:3.12Y—PSz的磨削热裂纹(如图2)部分稳定相变增韧z曲:陶瓷2Y—PSZ的晶粒细小,含有较高的亚稳态四方相t’(c+£’含量达45%),具有良好的增韧效果,在实验陶瓷中断裂韧性‰值较大,强度盯s较高,磨削表面平整光滑,为典型的显微塑变磨削特征。
没有发现明显的径向裂纹和不连续显微塑变裂纹。
当磨削速度提高到30m/s时。
磨削温度升高,在光整的磨痕周围会出现如图所示的裂纹,是一种典型的磨削热裂纹。
整体硬质合金刀具磨削裂纹的原因分析及其工艺改进

整体硬质合金刀具磨削裂纹的原因分析及其工艺改进1 引言整体硬质合金刀具在航空航天业、模具制造业、汽车制造业、机床制造业等领域得到越来越广泛的应用,尤其是在高速切削领域占有越来越重要的地位。
在高速切削领域,由于对刀具安全性、可靠性、耐用度的高标准要求,整体硬质合金刀具内在和表面的质量要求也更加严格。
而随着硬质合金棒材尤其是超细硬质合金材质内在质量的不断提高,整体硬质合金刀具表面的质量情况越来越受到重视。
众所周知,硬质合金刀具的使用寿命除了与其耐磨性有关外,也常常表现在崩刃、断刃、断裂等非正常失效方面,磨削后刀具的磨削裂纹等表面缺陷则是造成这种非正常失效的重要原因之一。
这些表面缺陷包括经磨削加工后暴露于表面的硬质合金棒料内部粉末冶金制造缺陷(如分层、裂纹、未压好、孔洞等)以及磨削过程中由于不合理磨削在磨削表面造成的磨削裂纹缺陷,而磨削裂纹则更为常见。
这些磨削裂纹,采用肉眼、放大镜、浸油吹砂、体视显微镜和工具显微镜等常规检测手段往往容易造成漏检,漏检的刀具在使用时尤其是在高速切削场合可能会造成严重的后果,因此整体硬质合金刀具产品磨削裂纹缺陷的危害很大。
因此对整体硬质合金刀具磨削裂纹的产生原因进行分析和探讨,并提出有效防止磨削裂纹的工艺改进措施具有很重要的现实意义。
2 整体硬质合金刀具磨削裂纹的原因分析1.整体硬质合金刀具的磨削加工特点硬质合金材料由于硬度高,脆性大,导热系数小,给刀具的刃磨带来了很大困难,尤其是磨削余量很大的整体硬质合金刀具。
硬度高就要求有较大的磨削压力,导热系数低又不允许产生过大的磨削热量,脆性大导致产生磨削裂纹的倾向大。
因此,对硬质合金刀具刃磨,既要求砂轮有较好的自砺性,又要有合理的刃磨工艺,还要有良好的冷却,使之有较好的散热条件,减少磨削裂纹的产生。
一般在刃磨硬质合金刀具时,温度高于600℃,刀具表面层就会产生氧化变色,造成程度不同的磨削烧伤,严重时就容易使硬质合金刀具产生裂纹。
磨削裂纹产生的原因及措施

淬火工件磨削加工过程中,磨削部位容易产生浅、细长、肉眼几乎无法辨别的磨削裂纹,常见的磨削裂纹有三种形状:龟裂或网状裂纹、直线状和弧状。
磨削裂纹产生的原因是:
1、热处理
热处理过程中,淬火温度高,产生过热组织;回火不充分,存在较大的内应力和较多的残余奥氏体;渗碳件渗碳层中的网状碳化物析出严重等,造成工件在后续磨削过程中产生磨削裂纹。
3、如果已产生磨削裂纹,如果未超过加工余量,可进行多次低温回火,去除磨削应力,再按正确的磨削加工方法加工,磨去裂纹深度进行挽救。
2)正确选择砂轮结构和硬度级别,以获得自由磨削效应。
3)陶瓷和金属作粘结剂的砂轮,适用于磨削热较高的场合;树脂粘结砂轮,适用磨削热较小的场合。脆性较大的粘结剂,磨粒容易脱落,有利于使砂轮保持锐利状态。
4)SiC磨料磨削钢和铁基耐热合金时,产生强烈的化学磨损,刚玉类磨料磨削钢时无此反应。相反,刚玉类磨料磨削玻璃、硅酸盐类陶瓷涂层时,会产生强烈的化学反应,SiC磨料无此反应。
2、冷却
磨削过程中,工件表面瞬间温度高达820℃,冷却不充分时,磨削产生的热量会使磨削表面薄层重新奥氏体化,随后在自身基体的激冷作用下,再次淬火为马氏体,表面层产生附加的组织应力,磨削是交替重复过程,累计的拉应力超过Байду номын сангаас件表面抗拉强度时,会产生龟裂或网状裂纹。
3、磨削过程中进刀量过大
磨削进刀量太大,温度剧烈升高,表层达到约300℃左右,则发生第二次收缩,产生第二种磨削裂纹;与磨削方向基本垂直的、有规则排列条状裂纹。如果局部严重磨削烧伤出现,则产生弧形裂纹。
4、磨料选择
砂轮磨料种类有刚玉、碳化硅、金刚石、氮化硼等,当选择的与工件不匹配时,会产生裂纹。
磨削裂纹的控制措施是:
浅析整体硬质合金刀具磨削裂纹的产生及其工艺改进措施

引 言
高效率 高精度硬质合 金刀具是一种 以高性能硬质合金材料
1 . 3 砂轮原 因
整体硬质合金刀具磨刃过程 中, 砂轮 的线速 度和径 向进给量
砂轮硬度越高 、 粒度越细 、 磨损得越厉害 , 都使磨削温度升 为基础的精密刀具 ,是钨材 料产业链 中技术 含量和 附加价值最 越 大, 高得很快, 则越容 易使硬质合金 刀具产生磨削裂纹及磨 削烧伤 。 高的产品之一, 也 是 支 持 先 进 加 工 制造 技术 发 展 的关 键 工 具 。因 砂轮修整 不合格 , 工作表 面产生较大 的跳 动 , 或者在 进行 为硬 质 合 金 刀 具 有 比较 大 的脆 性 , 容易发生裂纹现象 , 所 以 必 须 此 外 , 刃磨时振动过于猛烈 ,那么硬质合金 刀具就很容易产生崩刃等 在刀刃磨削的过程 中注意控 制温度 ,并且选 择合适的砂轮 以及
金磨削表面 的瞬 时温度会 达到很高 ,在温度 的快速增长 下将 导 要求相对较高的加工场合很难进行运用 。使用晶须增韧补强技
致热变形 的产 生。此 外, 又 因为硬 质合金 的抗弯 强度 比较低 , 有 术可 以对这个 问题进行有效 的解 决。在硬质合金刀具材料 中加 很大的刚性模量 , 在正常温度 下根 本没有塑性 , 无法通过 自身的 入晶须能对裂纹扩展 的能量进行 吸收,吸收能量的大小决定于 塑 性 变 形 来 消 除热 应 力 , 因而 在 磨 削 热 的 作 用 下 , 将 使 得 硬 质 合 晶须与基体的结合状 态 。晶须增韧补强技术 能全 面提高整体硬 金刀具的磨削表面产 生局 部热应力值高 于硬 质合金 自身 的强度 质合金刀具材料的硬度、 韧性等综合性能。 极限, 从 而 导 致 裂 纹 的产 生 。 2 . 1 . 1 晶须 的 选 用及 添加 方 式
- 1、下载文档前请自行甄别文档内容的完整性,平台不提供额外的编辑、内容补充、找答案等附加服务。
- 2、"仅部分预览"的文档,不可在线预览部分如存在完整性等问题,可反馈申请退款(可完整预览的文档不适用该条件!)。
- 3、如文档侵犯您的权益,请联系客服反馈,我们会尽快为您处理(人工客服工作时间:9:00-18:30)。
提高工件转速可以防止烧伤.
烧伤的主要几个原因及解决方法:
1.砂轮太硬选择稍软的砂轮
2.背吃刀量大减少背吃刀量,增加光磨时间
3.切削液不充足切削液要充分
4.粗磨烧伤过深进给量要小,切削液要充分
5.磁力不足,工件停转调整磁力
6.工件转速过低调整工件转速
7.砂轮主轴振摆大检修主轴
8.金刚石不锐利反转金刚石,以锐利尖角修整,或换金刚石
9.砂轮修整不好重新修整,稍放慢修整速度
10.定时支承磨损情况,如果磨损过大,会产生支承烧伤.
11,检查工件和砂轮电机扭矩选用是否足够,不足工件会产生短暂停留,会产生竖条烧伤.
另外提醒一点:
工件转速过高和过低都会产生烧伤,只有在合理范围内才是效果最佳的.
磨削烧伤机理:
当磨削表面产生高温时,如果散热措施不好,很容易在工件表面(从几十um到几百um)发生二次淬火及高温回火。
如果磨削工件表面层的瞬间温度超过钢种的AC1点,在冷却液的作用下二次淬火马氏体,而在表层下由于温度梯度大,时间短,只能形成高温回火组织,这就使在表层和次表层之间常山拉应力,而表层为一层薄而脆的二次淬火马氏体,当承受不了时,将产生裂纹。
预防磨削烧伤的措施
1.尽量减少磨削时产生的热量。
2.尽量加速热量的散发。
以上摘自邢镇寰吴宗彦主编的《轴承零件磨削和超精加工技术》。
砂轮工件转速比,最好是在60:1
可以尝试使用大气孔或者小气孔的砂轮。
主要在以下几方面分析调整:
1.磨削回跳时是否可能撞砂轮;
2.磨削进给速度,一般粗磨1.0-1.5MM/MIN.,精磨0.3-0.6mm/min.,光摩0.1mm/min;
3.工件转速,在可能的情况下尽可能快一些,以利于散热;
4.砂轮转速,适当调慢;
5.冷却液的浓度;
6.冷却液的喷溅流量及喷溅部位。
1)损伤的原因
(1)热处理的影响
a)残余奥氏体磨削时残余奥氏体由于砂轮磨削时产生的热和压力而转变,同时可能伴随出现表面回火和磨削裂纹。
残余奥氏体量应控制在30%以内。
b)渗层碳浓度渗层碳浓度过高,在渗层组织中容易形成网状碳化物或过多的游离碳化物。
由于这种物质极硬,在磨削过程中可能出现局部过热倾向和发生表面回火。
渗层碳浓度过高,会使轮齿表面产生过多的残余奥氏体.从而导致烧伤和裂纹。
因此,表面碳浓度增加,则降低了磨削性能,一般表面碳浓度应控制在0.75%-0.95%范围以内。
c)碳化物分布及形态碳化物分布应均匀,粒度平均直径不大于lμm;碳化物形态应为球状、粉状或细点状沿网分布,不允许有网状或角状碳化物。
d)脱碳热处理时.表面或环境保护不当会产生表面氧化,这样在齿面上就会产生一层薄的脱碳层,这层软的脱碳层会引起砂轮过载或过热,从而造成表面回火。
e)回火在保证硬度的前提下,回火温度尽可能高一些,回火时间尽可能长一些。
这样可以提高渗碳淬硬表面的塑性,而且使残余应力得以平衡或降低.改善表面应力的分布状况。
这样可以降低出现磨齿裂纹的机率,从而提高磨齿效率。
f)变形应尽可能减少热处理变形.这样可以减小磨齿余量。
若热处理变形过大,如果磨齿操作不是在齿圈径向圆跳动最大处开始磨削,则每次磨削在这些点上去除的磨削余量将是不正常的,从而导致烧伤及裂纹。
(2)磨削条件的影响磨齿时砂轮的切削速度很高,砂轮与轮齿的接触面积又很小,产生的热量可能在接触区域形成很高的温度,从而导致磨齿损伤。
a)磨齿余量磨齿余量过大会产生过多的磨削热,从而导致磨齿损伤。
应尽可能减小磨齿余量,为此必须:
①减少热处理变形。
②淬火后按齿田精确找正,然后加工定位基准,以便齿面余量分布均匀。
③磨前采用硬质合金滚刀半精滚齿,去除热处理变形,
b)切削规范磨齿时产生的热量大致与砂轮单位时间内切除的金属量成正比,因此为了避免磨齿损伤,必要时适当减少切深,降低展成进给量或纵向进给量。
c)砂轮
①砂轮的选择渗碳钢硬度高,砂粒易磨钝,为了避免砂粒磨钝而产生大量磨削热,砂轮硬度宜选软些,以便磨钝的砂粒及时脱落,保持砂轮的自锐性。
宜选择组织较软的砂轮。
组织较软的砂轮气孔多,其中可以容纳切屑.避免砂轮堵塞,又可将冷却液或空气带入磨削区域,从而使磨削区域温度降低。
在保证齿面粗糙度要求的前提下,宜选择较粗粒度的砂轮,以达到较高的去除量比率。
②砂轮的平衡及修整砂轮必须精细地平衡,以便砂轮工作时处于良好的平衡状态。
砂轮必须及时修整以保持其锋利。
影响砂轮修整频次的因素很多.包括被磨材料的纯度和类型、冷却液的净度等。
修整砂轮的金刚石支座必须牢固。
若金刚石表面上有0.5-0.6m m的磨损量,标志金刚石已磨钝了,应及时更换。
③严格控制砂轮传动系统及砂轮心轴的间隙。
砂轮传动带松紧调整合适。
d)冷却液磨削上艺中,冷却的控制是一个重要因素。
①冷却必须有效充分,冷却液必须喷到磨削区域;流量一般为40~45L/min,以实现充分冷却;压力一般为0.8~1.2N/mm2,以冲去粘在砂轮上的切屑;
②保持冷却液的纯净,妥善地过滤,以清除冷却液的切屑、磨粒等脏物;冷却液的容器要足够大,以免掺入过多的气体或泡沫,
③防止冷却液的温度急剧升高或降低,一般控制冷却系统的容积和工作间的室温,就足以
控制冷却液的温度,然而在特殊储况下应当使用散热器
2)磨齿损伤的检查
(1)可采用硝酸腐蚀法检查烧伤。
(2)磨齿后必须检查是否产生裂纹。
可用下列方法之一进行检查:
a)磁粉探伤,
b)荧光渗透探伤,
c)着色渗透探伤。
3)磨齿损伤对承载能力的影响
齿面的烧伤和裂纹,在轮齿承受脉冲负荷时将影响其疲劳强度和使用寿命,甚至造成齿轮早期失效。
烧伤将导致齿面过早地磨损。
沿齿长方向的裂纹会导致齿根疲劳断齿,这是绝对不允许的。
沿齿高方向的裂纹会导致单方向断裂。
这种裂纹是最常见的。
当裂纹深度较浅时.可采用硬质合金滚刀将裂纹去除,再重新磨齿。
当沿齿高方向和沿团长方向的裂纹同时出现时,可能形成网状裂纹,它会导致齿面剥落.这当然是绝对不允许的。