磨削裂纹产生的原因是磨削力过大
磨床磨削裂纹原因的分析与对策

磨床磨削裂纹的产生原因分析与对策分析磨削裂纹的产生原因,与磨削前各加工过程所产生的缺陷,如材料表层中存在网状碳化物、非金属夹杂、组织疏松、成分偏析、晶界上的淬火变形等有关;裂纹通常与烧伤同时出现。
当工件表层的残余拉应力超过材料的抗拉强度时,就会产生磨削裂纹。
磨削裂纹的产生原因和减小磨削裂纹的方法如下:1、正确选用砂轮,例如可采用颗粒较粗、较软、组织较疏松的砂轮;保证修整后砂轮的锋利。
2、保证磨削时的冷却条件,设法使冷却液能有效地渗透到工件的磨削区中。
3、合理选择磨削用量,例如提高工件的转速,采用较小的径向进给量等。
磨削时如果磨削工艺参数选择或操作不当,工件表面温度达到150~200度时表面因马氏体分解,体积缩小,而中心马氏体不收缩,使表层承受拉应力而开裂,产生的裂纹会与磨削方向垂直,裂纹相互平行。
当磨削温度在200度以上时,表面由于产生索氏体或托氏体,这时表层发生体积收缩,而中心则不收缩,使表层拉应力超过脆断抗力而出现龟裂现象。
4、工件表面渗层碳浓度过高,会使工件表面产生过多的残余奥氏体.从而容易导致产生烧伤和裂纹。
因此,表面碳浓度增加,则降低了磨削性能,一般表面碳浓度应控制在0.75%-0.95%范围以内。
5、碳化物分布应均匀,粒度平均直径不大于0.001m;碳化物形态应为球状、粉状或细点状沿网分布,不允许有网状或角状碳化物。
6、热处理时.表面或环境保护不当会产生表面氧化,这样在工件上就会产生一层薄的脱碳层,这层软的脱碳层会引起砂轮过载或过热,从而造成表面回火,工件磨削时容易出现裂纹。
7、如果冷却不充分,磨削时零件表面温度有时可能高达820~840度或更高,则由于磨削形成的热量足以使表面薄层重新奥氏体化,并再次淬火而形成淬火马氏体,表面形成二次淬火的金相组织。
此外,磨削形成的热量使零件表面温度升高极快,这种组织应力和热应力导致磨削表面出现磨削裂纹。
8、使用金刚滚轮修整砂轮的内滚道磨床加工的零件有裂纹,还与配置的金刚滚转速、转向、金刚石的粒度、磨损情况、修砂轮时电主轴的转速、修砂轮时与滚轮磨合停留的时间等因素有关。
磨削裂纹产生的原因及措施
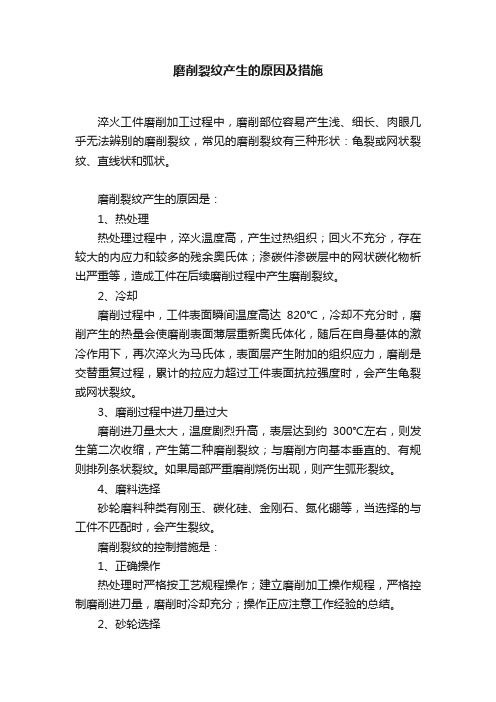
磨削裂纹产生的原因及措施淬火工件磨削加工过程中,磨削部位容易产生浅、细长、肉眼几乎无法辨别的磨削裂纹,常见的磨削裂纹有三种形状:龟裂或网状裂纹、直线状和弧状。
磨削裂纹产生的原因是:1、热处理热处理过程中,淬火温度高,产生过热组织;回火不充分,存在较大的内应力和较多的残余奥氏体;渗碳件渗碳层中的网状碳化物析出严重等,造成工件在后续磨削过程中产生磨削裂纹。
2、冷却磨削过程中,工件表面瞬间温度高达820℃,冷却不充分时,磨削产生的热量会使磨削表面薄层重新奥氏体化,随后在自身基体的激冷作用下,再次淬火为马氏体,表面层产生附加的组织应力,磨削是交替重复过程,累计的拉应力超过工件表面抗拉强度时,会产生龟裂或网状裂纹。
3、磨削过程中进刀量过大磨削进刀量太大,温度剧烈升高,表层达到约300℃左右,则发生第二次收缩,产生第二种磨削裂纹;与磨削方向基本垂直的、有规则排列条状裂纹。
如果局部严重磨削烧伤出现,则产生弧形裂纹。
4、磨料选择砂轮磨料种类有刚玉、碳化硅、金刚石、氮化硼等,当选择的与工件不匹配时,会产生裂纹。
磨削裂纹的控制措施是:1、正确操作热处理时严格按工艺规程操作;建立磨削加工操作规程,严格控制磨削进刀量,磨削时冷却充分;操作正应注意工作经验的总结。
2、砂轮选择1)尽可能选用锋利的砂轮,切削速度快,磨削效率高,磨削表面不易过热。
2)正确选择砂轮结构和硬度级别,以获得自由磨削效应。
3)陶瓷和金属作粘结剂的砂轮,适用于磨削热较高的场合;树脂粘结砂轮,适用磨削热较小的场合。
脆性较大的粘结剂,磨粒容易脱落,有利于使砂轮保持锐利状态。
4)SiC磨料磨削钢和铁基耐热合金时,产生强烈的化学磨损,刚玉类磨料磨削钢时无此反应。
相反,刚玉类磨料磨削玻璃、硅酸盐类陶瓷涂层时,会产生强烈的化学反应,SiC磨料无此反应。
3、如果已产生磨削裂纹,如果未超过加工余量,可进行多次低温回火,去除磨削应力,再按正确的磨削加工方法加工,磨去裂纹深度进行挽救。
齿轮磨削裂纹的产生原因及防止措施

齿轮磨削裂纹的产生原因及防止措施作者:覃发伟来源:《中国科技博览》2013年第09期[摘要]分析了磨削裂纹产生的原因,针对此原因,作者从喷丸强化工艺、磨削工艺、材料及热處理等方面进行分析,提出了防止磨削裂纹产生的措施。
[关键词]磨削裂纹;磨削热;磨削工艺;热处理中图分类号:TG580.6 文献标识码:A 文章编号:1009-914X(2013)09-0019-010 引言随着煤炭工业技术的发展,对煤矿机械中传动齿轮的承载能力、寿命、精度、齿面粗糙度、啮合噪音等方面提出更高的要求,因此越来越多地采用了硬齿面齿轮。
对于重载大功率、高精度要求的齿轮必须有较高的芯部强度和高的表面硬度,因此通常采用渗碳淬火处理的工艺方法来提高齿轮的芯部强度和高的表面硬度,从而提高其承载能力。
齿轮经过渗碳淬火后不可避免地要产生变形,且精度下降2-3级,因此对于高精度的齿轮,热处理后常用磨齿提高其加工精度。
然而,在磨削过程中常产生磨削裂纹,裂纹问题己严重困扰生产的顺利进行,如何消除磨削裂纹是摆在工程技术人员面前的技术难题。
1 磨削裂纹的产生原因磨削裂纹是指发生在磨削面上、深度较浅、并且深度基本一致、方向垂直于齿向、即垂直于砂轮往复运动的方向、规则排列的条状裂纹,用肉眼便可观察到,磨削裂纹产生的根本原因是磨削热。
齿轮在渗碳过程中,其渗层组织中容易形成网状碳化物或过多的游离碳化物,由于这些物质硬度极高,在磨削过程中,砂轮和齿面接触的瞬间,磨削区的温度很高,可能出现局部过热倾向和发生表面回火,使金相组织发生变化。
不同的金相组织比容不同,马氏体比容最大,奥氏体比容最小。
如磨削淬火钢时,表层出现回火组织,则表层金属比容减小,体积收缩受基部金属阻碍,表层产生残余拉应力。
若表层产生二次淬火层,残余奥氏体转变为马氏体,比容增大,体积膨胀受阻,就形成表面压应力,而里层则产生残余拉应力。
在传统的磨削方法中,切削液并不能完全达到磨削区,即冷却并不是很充分,在这种情况下,表面层不会产生二次回火,热塑性变形占主导地位,故磨削后表面产生残余拉应力,而正是由于这种残余拉应力的存在,引起微裂纹,降低其疲劳强度,大大影响了齿轮的使用性能。
磨床磨削裂纹原因的分析与对策

磨床磨削裂纹的产生原因分析与对策分析磨削裂纹的产生原因,与磨削前各加工过程所产生的缺陷,如材料表层中存在网状碳化物、非金属夹杂、组织疏松、成分偏析、晶界上的淬火变形等有关;裂纹通常与烧伤同时出现。
当工件表层的残余拉应力超过材料的抗拉强度时,就会产生磨削裂纹。
磨削裂纹的产生原因和减小磨削裂纹的方法如下:1、正确选用砂轮,例如可采用颗粒较粗、较软、组织较疏松的砂轮;保证修整后砂轮的锋利。
2、保证磨削时的冷却条件,设法使冷却液能有效地渗透到工件的磨削区中。
3、合理选择磨削用量,例如提高工件的转速,采用较小的径向进给量等。
磨削时如果磨削工艺参数选择或操作不当,工件表面温度达到150~200度时表面因马氏体分解,体积缩小,而中心马氏体不收缩,使表层承受拉应力而开裂,产生的裂纹会与磨削方向垂直,裂纹相互平行。
当磨削温度在200度以上时,表面由于产生索氏体或托氏体,这时表层发生体积收缩,而中心则不收缩,使表层拉应力超过脆断抗力而出现龟裂现象。
4、工件表面渗层碳浓度过高,会使工件表面产生过多的残余奥氏体.从而容易导致产生烧伤和裂纹。
因此,表面碳浓度增加,则降低了磨削性能,一般表面碳浓度应控制在0.75%-0.95%范围以内。
5、碳化物分布应均匀,粒度平均直径不大于0.001m;碳化物形态应为球状、粉状或细点状沿网分布,不允许有网状或角状碳化物。
6、热处理时.表面或环境保护不当会产生表面氧化,这样在工件上就会产生一层薄的脱碳层,这层软的脱碳层会引起砂轮过载或过热,从而造成表面回火,工件磨削时容易出现裂纹。
7、如果冷却不充分,磨削时零件表面温度有时可能高达820~840度或更高,则由于磨削形成的热量足以使表面薄层重新奥氏体化,并再次淬火而形成淬火马氏体,表面形成二次淬火的金相组织。
此外,磨削形成的热量使零件表面温度升高极快,这种组织应力和热应力导致磨削表面出现磨削裂纹。
8、使用金刚滚轮修整砂轮的内滚道磨床加工的零件有裂纹,还与配置的金刚滚转速、转向、金刚石的粒度、磨损情况、修砂轮时电主轴的转速、修砂轮时与滚轮磨合停留的时间等因素有关。
磨削裂纹产生的原因是磨削力过大
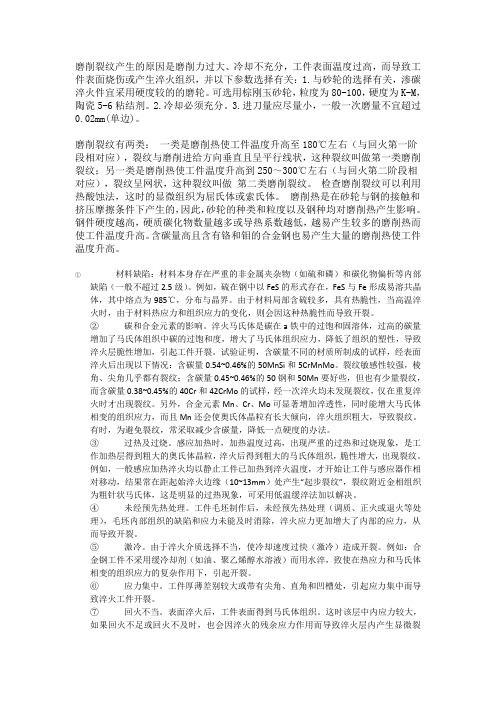
磨削裂纹产生的原因是磨削力过大、冷却不充分,工件表面温度过高,而导致工件表面烧伤或产生淬火组织,并以下参数选择有关:1.与砂轮的选择有关,渗碳淬火件宜采用硬度较的的磨轮。
可选用棕刚玉砂轮,粒度为80-100,硬度为K-M,陶瓷5-6粘结剂。
2.冷却必须充分。
3.进刀量应尽量小,一般一次磨量不宜超过0.02mm(单边)。
磨削裂纹有两类:一类是磨削热使工件温度升高至180℃左右(与回火第一阶段相对应),裂纹与磨削进给方向垂直且呈平行线状,这种裂纹叫做第一类磨削裂纹;另一类是磨削热使工件温度升高到250~300℃左右(与回火第二阶段相对应),裂纹呈网状,这种裂纹叫做第二类磨削裂纹。
检查磨削裂纹可以利用热酸蚀法,这时的显微组织为屈氏体或索氏体。
磨削热是在砂轮与钢的接触和挤压摩擦条件下产生的,因此,砂轮的种类和粒度以及钢种均对磨削热产生影响。
钢件硬度越高,硬质碳化物数量越多或导热系数越低,越易产生较多的磨削热而使工件温度升高。
含碳量高且含有铬和钼的合金钢也易产生大量的磨削热使工件温度升高。
①材料缺陷:材料本身存在严重的非金属夹杂物(如硫和磷)和碳化物偏析等内部缺陷(一般不超过2.5级)。
例如,硫在钢中以FeS的形式存在,FeS与Fe形成易溶共晶体,其中熔点为985℃,分布与晶界。
由于材料局部含硫较多,具有热脆性,当高温淬火时,由于材料热应力和组织应力的变化,则会因这种热脆性而导致开裂。
②碳和合金元素的影响。
淬火马氏体是碳在a铁中的过饱和固溶体,过高的碳量增加了马氏体组织中碳的过饱和度,增大了马氏体组织应力,降低了组织的塑性,导致淬火层脆性增加,引起工件开裂。
试验证明,含碳量不同的材质所制成的试样,经表面淬火后出现以下情况:含碳量0.54~0.46%的50MnSi和5CrMnMo。
裂纹敏感性较强,棱角、尖角几乎都有裂纹;含碳量0.45~0.46%的50钢和50Mn要好些,但也有少量裂纹,而含碳量0.38~0.45%的40Cr和42CrMo的试样,经一次淬火均未发现裂纹,仅在重复淬火时才出现裂纹。
浅析整体硬质合金刀具磨削裂纹的产生及其工艺改进措施

引 言
高效率 高精度硬质合 金刀具是一种 以高性能硬质合金材料
1 . 3 砂轮原 因
整体硬质合金刀具磨刃过程 中, 砂轮 的线速 度和径 向进给量
砂轮硬度越高 、 粒度越细 、 磨损得越厉害 , 都使磨削温度升 为基础的精密刀具 ,是钨材 料产业链 中技术 含量和 附加价值最 越 大, 高得很快, 则越容 易使硬质合金 刀具产生磨削裂纹及磨 削烧伤 。 高的产品之一, 也 是 支 持 先 进 加 工 制造 技术 发 展 的关 键 工 具 。因 砂轮修整 不合格 , 工作表 面产生较大 的跳 动 , 或者在 进行 为硬 质 合 金 刀 具 有 比较 大 的脆 性 , 容易发生裂纹现象 , 所 以 必 须 此 外 , 刃磨时振动过于猛烈 ,那么硬质合金 刀具就很容易产生崩刃等 在刀刃磨削的过程 中注意控 制温度 ,并且选 择合适的砂轮 以及
金磨削表面 的瞬 时温度会 达到很高 ,在温度 的快速增长 下将 导 要求相对较高的加工场合很难进行运用 。使用晶须增韧补强技
致热变形 的产 生。此 外, 又 因为硬 质合金 的抗弯 强度 比较低 , 有 术可 以对这个 问题进行有效 的解 决。在硬质合金刀具材料 中加 很大的刚性模量 , 在正常温度 下根 本没有塑性 , 无法通过 自身的 入晶须能对裂纹扩展 的能量进行 吸收,吸收能量的大小决定于 塑 性 变 形 来 消 除热 应 力 , 因而 在 磨 削 热 的 作 用 下 , 将 使 得 硬 质 合 晶须与基体的结合状 态 。晶须增韧补强技术 能全 面提高整体硬 金刀具的磨削表面产 生局 部热应力值高 于硬 质合金 自身 的强度 质合金刀具材料的硬度、 韧性等综合性能。 极限, 从 而 导 致 裂 纹 的产 生 。 2 . 1 . 1 晶须 的 选 用及 添加 方 式
砂轮磨削出现裂纹的原因
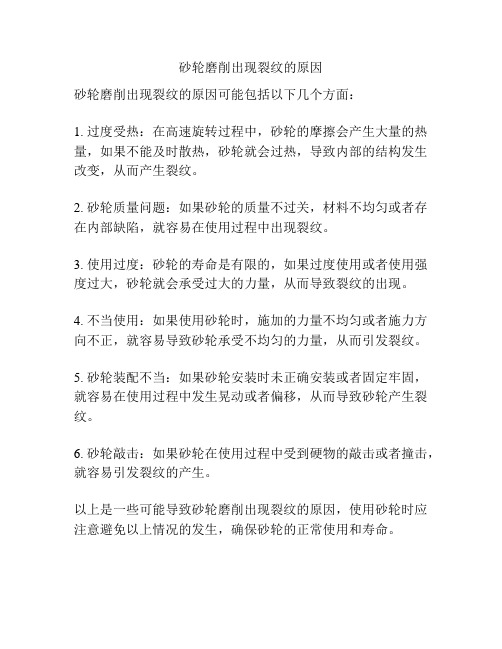
砂轮磨削出现裂纹的原因
砂轮磨削出现裂纹的原因可能包括以下几个方面:
1. 过度受热:在高速旋转过程中,砂轮的摩擦会产生大量的热量,如果不能及时散热,砂轮就会过热,导致内部的结构发生改变,从而产生裂纹。
2. 砂轮质量问题:如果砂轮的质量不过关,材料不均匀或者存在内部缺陷,就容易在使用过程中出现裂纹。
3. 使用过度:砂轮的寿命是有限的,如果过度使用或者使用强度过大,砂轮就会承受过大的力量,从而导致裂纹的出现。
4. 不当使用:如果使用砂轮时,施加的力量不均匀或者施力方向不正,就容易导致砂轮承受不均匀的力量,从而引发裂纹。
5. 砂轮装配不当:如果砂轮安装时未正确安装或者固定牢固,就容易在使用过程中发生晃动或者偏移,从而导致砂轮产生裂纹。
6. 砂轮敲击:如果砂轮在使用过程中受到硬物的敲击或者撞击,就容易引发裂纹的产生。
以上是一些可能导致砂轮磨削出现裂纹的原因,使用砂轮时应注意避免以上情况的发生,确保砂轮的正常使用和寿命。
蜗杆类零件磨削裂纹及对策

2018年 第7期热加工H热处理eatTreatment59蜗杆是机床回转部件中的重要零件,工作时蜗杆螺旋表面与蜗轮齿面相对滑动,容易发生磨损,因此蜗杆常用渗碳钢经渗碳淬火处理,以获得较高的硬度,防止蜗杆螺旋表面发生磨损。
蜗杆类零件的精度要求很高,加工工艺复杂、工序长,如在加工过程中出现问题,将造成重大损失。
我公司一种蜗杆零件在磨削加工时出现磨削裂纹,导致零件报废,严重影响了生产进度。
1. 蜗杆材料及主要工艺流程此蜗杆材料为20CrMnTiH ,形状如图1所示,热处理要求为渗碳淬火,渗碳层深1.1~ 1.5m m ,淬火后表面硬度58HRC 。
蜗杆加工工艺流程:下料→锻造→正火→粗车→除应力→精车→渗碳→螺纹处去碳→淬火→粗磨→无损检测→时效→精磨。
热处理过程:锻件正火→渗碳→淬火→低温回火→矫直→除蜗杆类零件磨削裂纹及对策■ 贾云峰摘要:20CrMnTiH 钢制蜗杆经渗碳淬火后磨削时发现裂纹,经分析认为,淬火温度偏高,淬火后残留奥氏体较多,在回火不充分时,在磨削热的影响下残留奥氏体发生转变,产生较大内应力,导致磨削时形成裂纹。
通过增加回火时间、增加冰冷定性,可有效解决这一现象。
关键词:蜗杆;磨削;裂纹;残留奥氏体扫码了解更多应力→低温时效。
热处理工艺过程曲线如图2所示。
渗碳淬火后,经检验碳化物1级,渗碳层深1.32mm ,表面硬度59~60HRC 。
2. 裂纹现象描述粗磨后蜗杆齿面出现磨削裂纹,裂纹极细,直线状,深度较浅,形态为通常所说的“发纹”,裂纹不平行,呈散射线状,如图3所示。
3. 磨削裂纹产生原因分析磨削裂纹与一般淬火裂纹明显不同,淬火裂纹粗而深,数量少;磨削裂纹只发生在磨削面上,数量较多,深度较浅,且深度基本一致。
较轻的磨削裂纹垂直于或接近垂直于磨削方向呈条状裂纹。
此蜗杆齿面是螺旋状曲面,磨削方向如图3中箭头所图 1图 22018年 第7期 热加工H热处理eatTreatment60示,裂纹垂直于磨削方向,符合磨削裂纹的特征。
- 1、下载文档前请自行甄别文档内容的完整性,平台不提供额外的编辑、内容补充、找答案等附加服务。
- 2、"仅部分预览"的文档,不可在线预览部分如存在完整性等问题,可反馈申请退款(可完整预览的文档不适用该条件!)。
- 3、如文档侵犯您的权益,请联系客服反馈,我们会尽快为您处理(人工客服工作时间:9:00-18:30)。
磨削裂纹产生的原因是磨削力过大、冷却不充分,工件表面温度过高,而导致工件表面烧伤或产生淬火组织,并以下参数选择有关:1.与砂轮的选择有关,渗碳淬火件宜采用硬度较的的磨轮。
可选用棕刚玉砂轮,粒度为80-100,硬度为K-M,陶瓷5-6粘结剂。
2.冷却必须充分。
3.进刀量应尽量小,一般一次磨量不宜超过0.02mm(单边)。
磨削裂纹有两类:一类是磨削热使工件温度升高至180℃左右(与回火第一阶段相对应),裂纹与磨削进给方向垂直且呈平行线状,这种裂纹叫做第一类磨削裂纹;另一类是磨削热使工件温度升高到250~300℃左右(与回火第二阶段相对应),裂纹呈网状,这种裂纹叫做第二类磨削裂纹。
检查磨削裂纹可以利用热酸蚀法,这时的显微组织为屈氏体或索氏体。
磨削热是在砂轮与钢的接触和挤压摩擦条件下产生的,因此,砂轮的种类和粒度以及钢种均对磨削热产生影响。
钢件硬度越高,硬质碳化物数量越多或导热系数越低,越易产生较多的磨削热而使工件温度升高。
含碳量高且含有铬和钼的合金钢也易产生大量的磨削热使工件温度升高。
①材料缺陷:材料本身存在严重的非金属夹杂物(如硫和磷)和碳化物偏析等内部
缺陷(一般不超过2.5级)。
例如,硫在钢中以FeS的形式存在,FeS与Fe形成易溶共晶体,其中熔点为985℃,分布与晶界。
由于材料局部含硫较多,具有热脆性,当高温淬火时,由于材料热应力和组织应力的变化,则会因这种热脆性而导致开裂。
②碳和合金元素的影响。
淬火马氏体是碳在a铁中的过饱和固溶体,过高的碳量
增加了马氏体组织中碳的过饱和度,增大了马氏体组织应力,降低了组织的塑性,导致淬火层脆性增加,引起工件开裂。
试验证明,含碳量不同的材质所制成的试样,经表面淬火后出现以下情况:含碳量0.54~0.46%的50MnSi和5CrMnMo。
裂纹敏感性较强,棱角、尖角几乎都有裂纹;含碳量0.45~0.46%的50钢和50Mn要好些,但也有少量裂纹,而含碳量0.38~0.45%的40Cr和42CrMo的试样,经一次淬火均未发现裂纹,仅在重复淬火时才出现裂纹。
另外,合金元素Mn、Cr、Mo可显著增加淬透性,同时能增大马氏体相变的组织应力,而且Mn还会使奥氏体晶粒有长大倾向,淬火组织粗大,导致裂纹。
有时,为避免裂纹,常采取减少含碳量,降低一点硬度的办法。
③过热及过烧。
感应加热时,加热温度过高,出现严重的过热和过烧现象,是工
作加热层得到粗大的奥氏体晶粒,淬火后得到粗大的马氏体组织,脆性增大,出现裂纹。
例如,一般感应加热淬火均以静止工件已加热到淬火温度,才开始让工件与感应器作相对移动,结果常在距起始淬火边缘(10~13mm)处产生“起步裂纹”,裂纹附近金相组织为粗针状马氏体,这是明显的过热现象,可采用低温缓淬法加以解决。
④未经预先热处理。
工件毛坯制作后,未经预先热处理(调质、正火或退火等处
理),毛坯内部组织的缺陷和应力未能及时消除,淬火应力更加增大了内部的应力,从而导致开裂。
⑤激冷。
由于淬火介质选择不当,使冷却速度过快(激冷)造成开裂。
例如:合
金钢工件不采用缓冷却剂(如油、聚乙烯醇水溶液)而用水淬,致使在热应力和马氏体相变的组织应力的复杂作用下,引起开裂。
⑥应力集中。
工件厚薄差别较大或带有尖角、直角和凹槽处,引起应力集中而导
致淬火工件开裂。
⑦回火不当。
表面淬火后,工件表面得到马氏体组织。
这时该层中内应力较大,
如果回火不足或回火不及时,也会因淬火的残余应力作用而导致淬火层内产生显微裂
纹,严重时会由于工件的脆性增大而开裂。
裂纹方向规则,是在磨削过程中产生的
预防:1保证粗糙度尽可能选择大粒度砂轮
2选择中软硬度砂轮,能保证精度,越软越好
3钛合金选绿色碳化硅磨料
4较低的砂轮速度和较小的磨削深度
5适当提高工件速度
6选用柔和的20号机油做冷却液
7选择20CrMo代替20CRMnTi钛合金粘度大
8严格控制渗碳层浓度,防止过多奥氏体和马氏体,充分回火,回火温度不宜过低9适当降低渗碳量(0.45%或更低)。