磨削裂纹的典型特征
20CrMnTi渗碳齿轮磨削裂纹的分析与解决
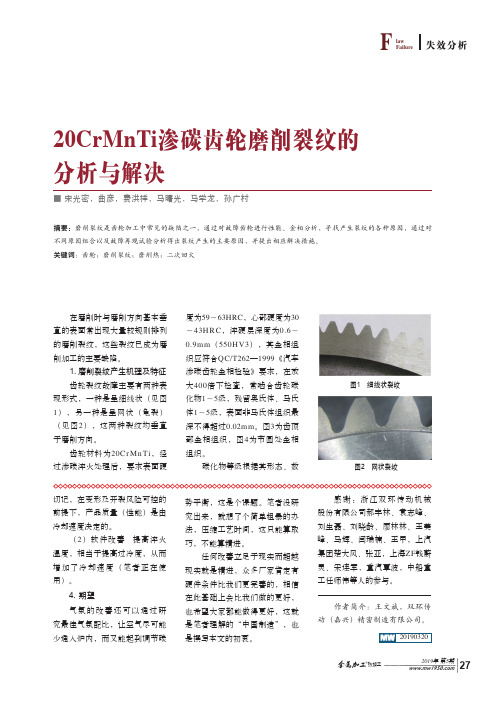
图1 细线状裂纹
图2 网状裂纹
感谢:浙江双环传动机械股份有限公司郝丰林、袁志峰、刘生磊、刘晓龄、廖林林、王美峰、马辉、闫瑞楠、王甲,上汽集团楚大风、张亚,上海ZF钱蔚灵、宋连军,重汽覃波,中船重
图3 齿顶部金相组织
图4 节圆处金相组织
量、大小、分布情况确定,具体
说明如表1所示。
残留奥氏体等级按其含量多
少确定,马氏体等级按其针体大
小确定,具体说明如表2所示。
通过对故障齿轮进行金相、
性能分析,齿轮金相组织及热处
图5 裂纹齿轮金相
图6 导致磨削裂纹的鱼骨图分析。
典型工程陶瓷的组成及磨削特点
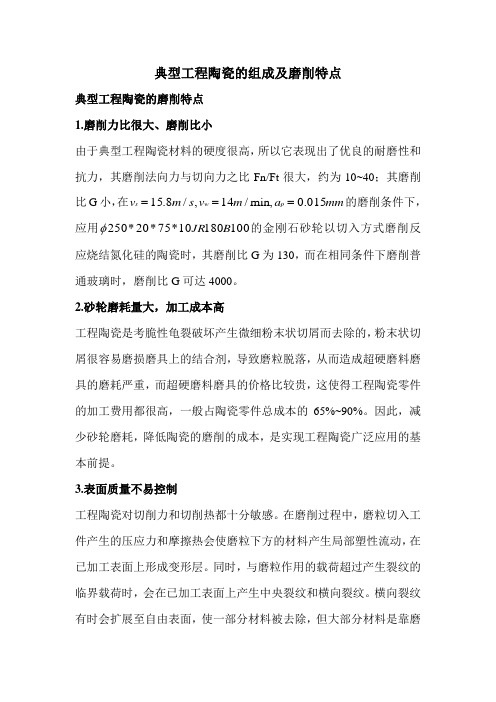
典型工程陶瓷的组成及磨削特点典型工程陶瓷的磨削特点 1.磨削力比很大、磨削比小由于典型工程陶瓷材料的硬度很高,所以它表现出了优良的耐磨性和抗力,其磨削法向力与切向力之比Fn/Ft 很大,约为10~40;其磨削比G 小,在mm a m v s m v p w s 015.0m in,/14,/8.15===的磨削条件下,应用10018010*75*20*250B JR φ的金刚石砂轮以切入方式磨削反应烧结氮化硅的陶瓷时,其磨削比G 为130,而在相同条件下磨削普通玻璃时,磨削比G 可达4000。
2.砂轮磨耗量大,加工成本高工程陶瓷是考脆性龟裂破坏产生微细粉末状切屑而去除的,粉末状切屑很容易磨损磨具上的结合剂,导致磨粒脱落,从而造成超硬磨料磨具的磨耗严重,而超硬磨料磨具的价格比较贵,这使得工程陶瓷零件的加工费用都很高,一般占陶瓷零件总成本的65%~90%。
因此,减少砂轮磨耗,降低陶瓷的磨削的成本,是实现工程陶瓷广泛应用的基本前提。
3.表面质量不易控制工程陶瓷对切削力和切削热都十分敏感。
在磨削过程中,磨粒切入工件产生的压应力和摩擦热会使磨粒下方的材料产生局部塑性流动,在已加工表面上形成变形层。
同时,与磨粒作用的载荷超过产生裂纹的临界载荷时,会在已加工表面上产生中央裂纹和横向裂纹。
横向裂纹有时会扩展至自由表面,使一部分材料被去除,但大部分材料是靠磨粒前刀面压溃去除的。
因此,典型工程陶瓷的磨削过程及磨削表面质量既不同于塑性金属材料,也不同于普通脆性材料,具有特殊的规律。
4.磨削生产率低由于工程陶瓷的韧性不足,而且磨削抗力很大,使得磨削加工层的厚度受到特定条件的约束,加之优良的磨削性,造成了工程陶瓷材料的切削加工性很差,生产效率低。
典型工程陶瓷的组成及用途工程陶瓷材料主要包括金属与硼、碳、硅、氮、氧等非金属元素组成的化合物,以及由非金属元素所组成的化合物,如硼和硅的碳化物、氮化物。
根据其元素组成的不同,工程陶瓷可分为氧化物陶瓷、氮化物陶瓷、碳化物陶瓷等。
金相检验员考试:金相检验员考试试题预测四
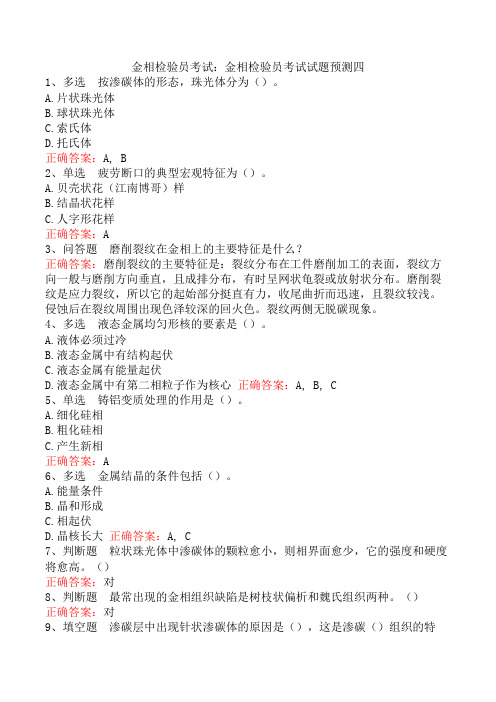
金相检验员考试:金相检验员考试试题预测四1、多选按渗碳体的形态,珠光体分为()。
A.片状珠光体B.球状珠光体C.索氏体D.托氏体正确答案:A, B2、单选疲劳断口的典型宏观特征为()。
A.贝壳状花(江南博哥)样B.结晶状花样C.人字形花样正确答案:A3、问答题磨削裂纹在金相上的主要特征是什么?正确答案:磨削裂纹的主要特征是:裂纹分布在工件磨削加工的表面,裂纹方向一般与磨削方向垂直,且成排分布,有时呈网状龟裂或放射状分布。
磨削裂纹是应力裂纹,所以它的起始部分挺直有力,收尾曲折而迅速,且裂纹较浅。
侵蚀后在裂纹周围出现色泽较深的回火色。
裂纹两侧无脱碳现象。
4、多选液态金属均匀形核的要素是()。
A.液体必须过冷B.液态金属中有结构起伏C.液态金属有能量起伏D.液态金属中有第二相粒子作为核心正确答案:A, B, C5、单选铸铝变质处理的作用是()。
A.细化硅相B.粗化硅相C.产生新相正确答案:A6、多选金属结晶的条件包括()。
A.能量条件B.晶和形成C.相起伏D.晶核长大正确答案:A, C7、判断题粒状珠光体中渗碳体的颗粒愈小,则相界面愈少,它的强度和硬度将愈高。
()正确答案:对8、判断题最常出现的金相组织缺陷是树枝状偏析和魏氏组织两种。
()正确答案:对9、填空题渗碳层中出现针状渗碳体的原因是(),这是渗碳()组织的特征。
正确答案:实际渗碳温度过高,过热10、判断题金相试样细磨使用砂纸更换原则应是粒度逐渐由粗到细。
()正确答案:对11、问答题磨抛渗层组织试样的特别要求是什么?为什么?正确答案:渗层试样磨抛时的特别要求,试样磨面平整,边缘不能倒角。
如试样边缘倒角,在显微镜下观察时,边缘组织必然会模糊不清,从而影响对表层组织的鉴别和渗层深度的正确测定,同时也得不到清晰的金相照片。
12、填空题锻造过热是由于加热温度过高而引起的()现象,碳钢以出现()为特征,工模具钢以()为特征。
正确答案:晶粒粗大,魏氏组织,一次碳化物角状化13、判断题锡基轴承合金的组织是由黑色的锡基α固溶体和白色的Sn、SB.方块及白色星形或针状的Cu、SB,或Cu、Sn相所组成。
车、磨、削裂纹产生机理与防止方法

车、磨、削裂纹产生机理与防止方法作者:郑好友许斌来源:《中国科技博览》2018年第16期[摘要]车、磨、削加工在机械制造行业中广泛地被应用,经过热处理淬火的碳素工具钢和渗碳淬火钢零件,在磨削时与磨削方向基本垂直的表面常常出现大量的较规则排列的裂纹——磨削裂纹,它不但影响零件的外观,更重要的是还直接影响零件的质量。
[关键词]车、磨、削裂纹;机理;防治措施中图分类号:S265 文献标识码:A 文章编号:1009-914X(2018)16-0301-01磨削加工一般是作为宫颈肩加工的最终工序,其任务就是要保证产品零件能够达到图纸上所要要求的精度和表面质量。
1、磨削裂纹的产生机理磨削加工在广泛的被应用,经过热处理淬火的碳素工具钢和渗碳淬火钢零件,在磨削时与磨削方向基本垂直的表面常常出现大量的较规则排列的裂纹——磨削裂纹,它不但影响零件的外观,更重要的是还直接影响零件的质量。
磨削裂纹的产生是磨削热和循环应力引起的,磨削时零件表面的温度可能高达820—840度或更高产生微裂纹后,以及磨粒刮出的微裂纹,后续的循环应力将为裂纹扩展开来形成宏观裂纹。
淬火钢的组织是马氏体和一定数量的残余奥氏体,处于膨胀状态(未经回火处理尤为严重)。
如果将其表面快速加热至100摄氏度左右并迅速冷却时,必然将产生收缩,这是第一次收缩。
这种收缩仅仅发生在表面,其基体仍处于膨胀状态,从而使表面层承受拉应力而产生裂纹,这是第一种裂纹。
当温度升高至300摄氏度时,表面再次收缩,从而产生第二种裂纹。
马氏体的膨胀收缩随着钢中含碳量的增加而增大,故碳素工具钢和渗碳淬火钢产生削裂纹尤为严重。
淬火钢中的残余奥氏体,在磨削时受磨削热的影响即发生分解,逐渐变成马氏体,这种新生的马氏体集中于表面,引起零件局部体积膨胀,加大了零件表面应力,导致磨削应力集中,继续磨削则容易加速磨削裂纹的产生。
此外,新生的马氏体脆性较大,磨削也容易加速磨削裂纹的产生。
另一方面,在上磨削工件时,对工件既是压力,又是拉力,助长了磨削裂纹的形成。
整体硬质合金刀具磨削裂纹的原因分析及其工艺改进

整体硬质合金刀具磨削裂纹的原因分析及其工艺改进1 引言整体硬质合金刀具在航空航天业、模具制造业、汽车制造业、机床制造业等领域得到越来越广泛的应用,尤其是在高速切削领域占有越来越重要的地位。
在高速切削领域,由于对刀具安全性、可靠性、耐用度的高标准要求,整体硬质合金刀具内在和表面的质量要求也更加严格。
而随着硬质合金棒材尤其是超细硬质合金材质内在质量的不断提高,整体硬质合金刀具表面的质量情况越来越受到重视。
众所周知,硬质合金刀具的使用寿命除了与其耐磨性有关外,也常常表现在崩刃、断刃、断裂等非正常失效方面,磨削后刀具的磨削裂纹等表面缺陷则是造成这种非正常失效的重要原因之一。
这些表面缺陷包括经磨削加工后暴露于表面的硬质合金棒料内部粉末冶金制造缺陷(如分层、裂纹、未压好、孔洞等)以及磨削过程中由于不合理磨削在磨削表面造成的磨削裂纹缺陷,而磨削裂纹则更为常见。
这些磨削裂纹,采用肉眼、放大镜、浸油吹砂、体视显微镜和工具显微镜等常规检测手段往往容易造成漏检,漏检的刀具在使用时尤其是在高速切削场合可能会造成严重的后果,因此整体硬质合金刀具产品磨削裂纹缺陷的危害很大。
因此对整体硬质合金刀具磨削裂纹的产生原因进行分析和探讨,并提出有效防止磨削裂纹的工艺改进措施具有很重要的现实意义。
2 整体硬质合金刀具磨削裂纹的原因分析1.整体硬质合金刀具的磨削加工特点硬质合金材料由于硬度高,脆性大,导热系数小,给刀具的刃磨带来了很大困难,尤其是磨削余量很大的整体硬质合金刀具。
硬度高就要求有较大的磨削压力,导热系数低又不允许产生过大的磨削热量,脆性大导致产生磨削裂纹的倾向大。
因此,对硬质合金刀具刃磨,既要求砂轮有较好的自砺性,又要有合理的刃磨工艺,还要有良好的冷却,使之有较好的散热条件,减少磨削裂纹的产生。
一般在刃磨硬质合金刀具时,温度高于600℃,刀具表面层就会产生氧化变色,造成程度不同的磨削烧伤,严重时就容易使硬质合金刀具产生裂纹。
磨削裂纹产生的原因及措施

淬火工件磨削加工过程中,磨削部位容易产生浅、细长、肉眼几乎无法辨别的磨削裂纹,常见的磨削裂纹有三种形状:龟裂或网状裂纹、直线状和弧状。
磨削裂纹产生的原因是:
1、热处理
热处理过程中,淬火温度高,产生过热组织;回火不充分,存在较大的内应力和较多的残余奥氏体;渗碳件渗碳层中的网状碳化物析出严重等,造成工件在后续磨削过程中产生磨削裂纹。
3、如果已产生磨削裂纹,如果未超过加工余量,可进行多次低温回火,去除磨削应力,再按正确的磨削加工方法加工,磨去裂纹深度进行挽救。
2)正确选择砂轮结构和硬度级别,以获得自由磨削效应。
3)陶瓷和金属作粘结剂的砂轮,适用于磨削热较高的场合;树脂粘结砂轮,适用磨削热较小的场合。脆性较大的粘结剂,磨粒容易脱落,有利于使砂轮保持锐利状态。
4)SiC磨料磨削钢和铁基耐热合金时,产生强烈的化学磨损,刚玉类磨料磨削钢时无此反应。相反,刚玉类磨料磨削玻璃、硅酸盐类陶瓷涂层时,会产生强烈的化学反应,SiC磨料无此反应。
2、冷却
磨削过程中,工件表面瞬间温度高达820℃,冷却不充分时,磨削产生的热量会使磨削表面薄层重新奥氏体化,随后在自身基体的激冷作用下,再次淬火为马氏体,表面层产生附加的组织应力,磨削是交替重复过程,累计的拉应力超过Байду номын сангаас件表面抗拉强度时,会产生龟裂或网状裂纹。
3、磨削过程中进刀量过大
磨削进刀量太大,温度剧烈升高,表层达到约300℃左右,则发生第二次收缩,产生第二种磨削裂纹;与磨削方向基本垂直的、有规则排列条状裂纹。如果局部严重磨削烧伤出现,则产生弧形裂纹。
4、磨料选择
砂轮磨料种类有刚玉、碳化硅、金刚石、氮化硼等,当选择的与工件不匹配时,会产生裂纹。
磨削裂纹的控制措施是:
磨削裂纹的形成与分析

磨削裂纹的形成:发动机上用的各种轴类零件如驱动轴、凸轮轴、曲轴、摇臂轴等在加工过程中需要热处理,但热处理后淬硬或经过渗碳淬火的轴类零件,在磨削过程中由于表面显微组织发生转变而形成大量的裂纹,即磨削裂纹。
下面就磨削裂纹的形成及特征加以阐述。
一、磨削裂纹的产生:(一)磨削裂纹的生成轴类零件在磨削过程中要产生大量的热量,这些热量只限于表面极薄的区域内,它足以使其表面温度达到800℃以上,而且升温极快。
如果磨削时冷却不够充分,将导致表面层的显微组织重新奥氏体化,并再次淬火成为马氏体。
因而使工件表面层产生极大的附加组织应力,同时由于表面温升极快,造成很大的热应力,当组织应力和热应力叠加超过了材料的强度极限时,被磨削的表面就会出现磨削裂纹。
(二)磨削裂纹形成的影响因素:1、组织结构所谓组织结构方面的影响因素有碳化物的形态与分布,残余奥氏体的数量以及非金属夹杂物。
显微组织中碳化物的形态、分布影响着磨削裂纹的生成,如果碳化物数量较多,颗粒较大,分布不均或集聚存在时,将明显地分割金属的基体,降低其强度。
尤其当以断续网状析出时,则会严重地削弱晶间结合力,明显地影响热传导,从而加剧磨削裂纹生成。
如果碳化物细小、分布均匀,则有利于分散磨削应力,从而减少生成磨削裂纹的机率。
零件磨削时显微组织中的残余奥氏体因受磨削热的影响必将发生分解,逐渐转变为马氏体,引起工件表面体积膨胀,而导致组织应力的产生,进而促进裂纹的形成。
因此,工件内部残余奥氏体量较高时,易于产生磨削裂纹。
2、热处理工艺经过淬火而不进行回火的轴件,对磨削裂纹的形成是非常敏感的。
因为磨削时产生的磨削热足以使表层淬火马氏体发生转变,碳化物析出,体积减少。
造成了工件表面与内部的比容差,引起较大的内应力,进而形成裂纹。
轴件有时回火不足,在磨削时也容易形成裂纹。
由此可见,对淬火后的零件必须进行充分地回火。
但是为了保证工件达到一定硬度的要求,回火温度不能任意提高。
因此必须采用合适的磨削工艺,使工件表面受热的温度不超过回火温度。
摆线齿轮磨削加工产生龟裂原因分析

比如现代钟表、 仪表中就广泛地采用
摆线齿轮, 而其变化形式——摆线针 轮传动也获得越来越广泛的应用。
某厂采 用 GC 1 制 造摆 线 齿 r5
接成网状 ,裂纹方向多与磨削方向
垂直 。
磨削裂纹的成因
磨削裂纹是多种应力的叠加,
轮,加工工艺流程为:备料一锻造
一
尤其是拉应力的产物。磨削裂纹与
6 左右 O 大干6 2
将同样的材料经过同样的锻造一球化退火一粗加工之后,采用 40 预 0 ̄ C 热,80 保温 1 n 5 ̄ C 5 油冷, mi 随后加热到 20 保温 6mn 2 ̄ C, 0 i空冷,其硬度达 到规定要求5 ~ 2 R , 8 6H C 经磨削加工后表面未出现龟裂现象 , 这说明适当提
显微组织分析
针对以上原因分析 , 我们沿裂纹齿廓上取样, 用金相显微镜进行微观组
织是马氏体和一定数量的残余奥氏
体,处于膨胀状态 ( 未经回火处理
织观察。金相组织为隐晶状马氏体+ 碳化物 + 残余奥氏体,奥氏体含量约为
1%, 5 超出规定的5 %~1%允许值 , 0 裂纹四周无脱碳现象, 表面组织与心部
磨削应力和热处理应力密切相关。
球化退火一机械加工一淬火、低
温 回火、喷丸 一磨 齿 ,要求热处 理
后硬度定为5 ~6 H C 其尺寸如 8 2R ,
图l 所示 。
1 . 磨削应力
磨削过程实质是磨粒切削刃切
削金属的过程 , 刃具 切削一样 , 与 被
磨削的金属也经受了弹性变形、塑
图 2
热处理工艺作了些改进 。第一 种方案: 将回火温度提高到20 保温时间6r n 2 ̄ C, 0 i。第二种方案:回火温度 a 不变 ,将保温时间延长到 10 i。 2m n
- 1、下载文档前请自行甄别文档内容的完整性,平台不提供额外的编辑、内容补充、找答案等附加服务。
- 2、"仅部分预览"的文档,不可在线预览部分如存在完整性等问题,可反馈申请退款(可完整预览的文档不适用该条件!)。
- 3、如文档侵犯您的权益,请联系客服反馈,我们会尽快为您处理(人工客服工作时间:9:00-18:30)。
磨削裂纹的典型特征
磨削裂纹是指在磨削过程中,工件表面产生的细小裂纹。
这些裂纹通常呈弧形或曲线状,沿着磨削方向延伸。
磨削裂纹是一种常见的表面缺陷,可能会对工件的性能和寿命产生负面影响。
磨削裂纹的典型特征主要包括以下几个方面。
磨削裂纹通常呈现出明显的形状和方向。
由于磨削过程中的应力集中和热效应,裂纹往往沿着磨削方向延伸。
这种裂纹形状和方向的一致性是磨削裂纹的典型特征,也是识别和分析磨削裂纹的重要依据。
磨削裂纹的尺寸通常很小。
由于磨削过程的高速旋转和摩擦作用,磨削裂纹往往只存在于工件表面的一层薄膜内,其深度通常在几个微米到几十个微米之间。
因此,磨削裂纹的尺寸较小,需要通过显微镜等设备才能观察到。
磨削裂纹通常呈现出一定的规律性。
虽然磨削裂纹是在磨削过程中产生的随机缺陷,但由于磨削过程的特性,裂纹往往呈现出一定的规律性。
例如,磨削裂纹可能集中分布在磨削轮的切削边缘附近,或者在工件表面的凹凸不平处产生。
这种规律性可以帮助我们进一步理解磨削裂纹的形成机制。
磨削裂纹通常具有一定的危害性。
尽管磨削裂纹的尺寸较小,但由于其存在于工件表面,易受外界环境和力学载荷的影响,可能会进
一步扩展和发展。
这些裂纹扩展可能导致工件的强度和耐久性下降,甚至引发工件的断裂和失效。
因此,磨削裂纹的存在需要引起足够的重视,并采取相应的措施进行控制和修复。
磨削裂纹具有明显的形状和方向、小尺寸、一定的规律性和一定的危害性等典型特征。
对于工程师和磨削加工人员来说,了解和掌握这些特征,可以帮助他们更好地识别和分析磨削裂纹,从而采取相应的措施进行预防和处理。
通过合理选择磨削参数、优化磨削工艺和采用适当的工艺控制措施,可以最大程度地降低磨削裂纹的发生率,提高工件的质量和性能。