冷处理裂纹酸洗裂纹及磨削裂纹等三
关于冷处理裂纹的4问

关于冷处理裂纹的4问1、什么是冷处理裂纹?原则上冷处理是在淬火后立即进行的。
淬火后的零件放在常温下,其残余奥氏体发生稳定化(stabilization),残余奥氏体的转变非常缓慢,难以进行马氏体化。
但若在淬火后立即进行冷处理,由于淬火产生的应力与残余奥氏体的马氏体化产生的应力相叠加,会发生与淬火裂纹相同的裂纹。
这种裂纹就是冷处理裂纹(sub-zerocrack)。
小型零件应力小,所以不易发生冷处理裂纹。
大型零件或厚璧零件等可以说必定要发生冷处理裂纹.要防止冷处理裂纹,最好在冷处理前,在100~130C稍微回火一下.使残余奥氏体稳定化一些,在降低由于淬火所发生的应力之后,再进行冷处理。
这样虽说能防止冷处理裂纹的发生,但是,稳定化了的残余奥氏体就会原封不动地残存下来,该残余奥氏体大约有5%左右,且处于稳定化状态,起到缓冲的作用,这是个大优点。
在冷处理之前,在100个的开水中回火是个关键。
有时由于测量淬火硬度,在压痕处也会发生冷处理裂纹,这是测试硬度后遗留的残余应力,此残余应力会成为裂纹发生的诱因。
从冷处理温度回升到室温,通常的作法是将冷处理后的零件放在空气中、投入水中或热水中。
这种方法称为冷处理急热法{up一hillquenching)。
冷处理急热法对消除低温快速冷却所发生的热应力是有用的。
冷处理后的零件若在空气中放置,往往会发生裂纹(称为冷处理升温裂纹),利用冷处理急热法可防止这种裂纹。
冷处理有两种,使用干冰(一78C)的普通冷处理和使用液氮(一196℃)的超冷处理。
其中以超冷处理的效果最好。
但是,关键的问题是,不管哪种冷处理都得在冷处理前把零件放入100C的开水中回火,在冷处理后将零件投入水或热水中进行冷处理急热。
以防止冷处理了裂纹。
2.为什么会发生冷处理裂纹?淬过火的钢内潜伏着很大的淬火应力(热应力和相变应力),还存在10~30%的残余奥氏体(Ar).将这样的钢进行冷处理,残余奥氏体的马氏体化会产生相变应力。
金属热处理产生的组织缺陷

金属热处理产生的组织缺陷
金属热处理缺陷指在热处理生产过程中产生的使零件失去使用价值或不符合技术条件要求的各种补助,以及使热处理以后的后续工序工艺性能变坏或降低使用性能的热处理隐患。
最危险的缺陷为裂纹,其中最主要的是淬火裂纹,其次是加热裂纹、延迟裂纹、冷处理裂纹、回火裂纹、时效裂纹、磨削裂纹和电镀裂纹等。
导致淬火裂纹的原因:(1)原材料已有缺陷(冶金缺陷扩展成淬火裂纹);(2)原始组织不良(如钢中粗大组织或魏氏组织倾向大);(3)夹杂物;(4)淬火温度不当;(5)淬火时冷却不当;(6)机械加工缺陷;(7)不及时回火。
最常见的缺陷是变形,其中淬火变形占多数,产生的原因是相变和热应力。
残余应力、组织不合格、性能不合格、脆性及其他缺陷发生的频率和严重性较低。
内应力来源有两个方面:(1)冷却过程中零件表面与中心冷却速率不同、其体积收缩在表面与中心也不一样。
这种由于温度差而产生的体积收缩量不同所引起的内用力叫做“热应力”;(2)钢件在组织转变时比体积发生变化,如奥氏体转变为马氏体时比体积增大。
由于零件断面上各处转变的先后不同,其体积变化各处不同,由此引起额内应力称作“组织应力”。
热处理常见缺陷分析与对策-学习总结
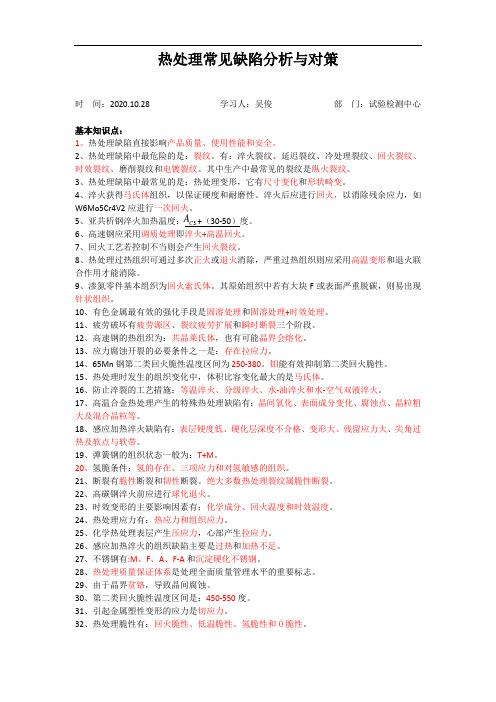
热处理常见缺陷分析与对策时 间:2020.10.28 学习人:吴俊 部 门:试验检测中心基本知识点:1、热处理缺陷直接影响产品质量、使用性能和安全。
2、热处理缺陷中最危险的是:裂纹。
有:淬火裂纹、延迟裂纹、冷处理裂纹、回火裂纹、时效裂纹、磨削裂纹和电镀裂纹。
其中生产中最常见的裂纹是纵火裂纹。
3、热处理缺陷中最常见的是:热处理变形,它有尺寸变化和形状畸变。
4、淬火获得马氏体组织,以保证硬度和耐磨性。
淬火后应进行回火,以消除残余应力,如W6Mo5Cr4V2应进行一次回火。
5、亚共析钢淬火加热温度: +(30-50)度。
6、高速钢应采用调质处理即淬火+高温回火。
7、回火工艺若控制不当则会产生回火裂纹。
8、热处理过热组织可通过多次正火或退火消除,严重过热组织则应采用高温变形和退火联合作用才能消除。
9、渗氮零件基本组织为回火索氏体。
其原始组织中若有大块F 或表面严重脱碳,则易出现针状组织。
10、有色金属最有效的强化手段是固溶处理和固溶处理+时效处理。
11、疲劳破坏有疲劳源区、裂纹疲劳扩展和瞬时断裂三个阶段。
12、高速钢的热组织为:共晶莱氏体,也有可能晶界会熔化。
13、应力腐蚀开裂的必要条件之一是:存在拉应力。
14、65Mn 钢第二类回火脆性温度区间为250-380。
钼能有效抑制第二类回火脆性。
15、热处理时发生的组织变化中,体积比容变化最大的是马氏体。
16、防止淬裂的工艺措施:等温淬火、分级淬火、水-油淬火和水-空气双液淬火。
17、高温合金热处理产生的特殊热处理缺陷有:晶间氧化、表面成分变化、腐蚀点、晶粒粗大及混合晶粒等。
18、感应加热淬火缺陷有:表层硬度低、硬化层深度不合格、变形大、残留应力大、尖角过热及软点与软带。
19、弹簧钢的组织状态一般为:T+M 。
20、氢脆条件:氢的存在、三项应力和对氢敏感的组织。
21、断裂有脆性断裂和韧性断裂。
绝大多数热处理裂纹属脆性断裂。
22、高碳钢淬火前应进行球化退火。
23、时效变形的主要影响因素有:化学成分、回火温度和时效温度。
电机支架挡板自攻螺钉断裂原因分析
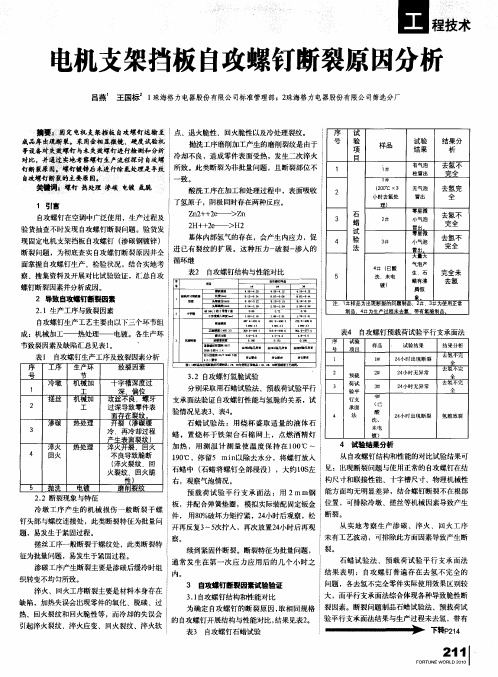
21 I 1
F ORT E WORL 0 0 UN D 2 1 l
曰
需要少得 多的制冷剂 ,而且可以更好地处理制 冷保证供冷 的可 靠性 在9 .%以上 ,正是 因为 从国外的经验来看一 个社区集中供冷供热系统 97 冷剂在 工作及回收时的泄漏问题 。一旦特 殊的 如此高的可 靠性 ,连一般的医院和食 品冷 冻厂 是否成功有以下 因素决定 :冬冷夏热 ,人 1稠 3
腾假
完全 未 去氢
象 注 :1 样 品 为出 现 断裂 的 问题 制 品 .2 3 # # #为 使 用正 常
制品 4 #为生产过程未去氢 带有氢脆制品
成 :机 械加 工—— 热处理—— 电镀 。各生产环
节致裂 因素及缺陷汇总见表 1 。
序
口
表4 自 螺钉预载荷试验平行支承面法 攻
序 1
‘
号
试 验
项目
样品
l #
试验 结果
2 4时 出现 断 裂 4,
结果分析
去 氢 不 完
表 1 自攻螺钉生产工序及致裂因素分析
工 序 生产 环
1)
致 裂 因素
十 字 槽深 度 过 深 偏位 攻 丝 不 良 ,螺 牙
.
2
预 载
2 # 荷试
去 氢不 完 全
大 量 大
4 ( # 已酸
气泡产
察、搜集资料及开展对 比试验验证 ,汇总 自攻 螺钉 断裂因素并分析成 因。 2 导致自攻螺钉断裂因素 2 1生产工序与致裂 因素 .
自 攻螺钉生产 工艺主要 由以下三个 环节组
5
洗 未电 镀)
生 石 蜡有 沸
3
高速钢属莱氏体钢(2)

高速钢属莱氏体钢,含有大量合金元素,冶炼后形成大量一次共晶碳化物和二次碳化物(约占成分总量的18%~22%),这对高速钢刀具的淬火质量及使用寿命有很大影响。
高速钢淬火温度接近熔点,淬火后组织中仍有25%~35%的残余奥氏体,致使高速钢刀具容易产生裂纹和腐蚀。
下面分析影响高速钢刀具淬火裂纹和腐蚀的原因,并提出相应预防措施。
1 高速钢原材料的冶金缺陷高速钢中所含大量碳化物硬而脆,为脆性相。
一次共晶碳化物呈粗大骨骼状(或树枝状)分布于钢基体内。
钢锭经开坯压延和轧制后,合金碳化物虽有一定程度的破碎和细化,但碳化物偏析依然存在,并沿轧制方向呈带状、全网状、半网状或堆积状分布。
碳化物不均匀度随原材料直径或厚度的增加而增加。
共晶碳化物相当稳定,常规热处理很难消除,可导致应力集中而成为淬火裂纹源。
钢中硫、磷等杂质偏析或超标也是导致淬裂的重要原因。
高速钢的导热性和热塑性差、变形抗力大,热加工时易导致金属表层和内层形成微裂纹,最终在淬火时因裂纹扩展而导致材料报废。
大型钢锭在冶炼、轧制或锻造等热加工过程中形成的宏观冶金缺陷如疏松、缩孔、气泡、偏析、白点、树枝状结晶、粗晶、夹杂、内裂、发纹、大颗粒碳化物及非金属夹渣等均易导致淬火时应力集中,当应力大于材料强度极限时便会产生淬火裂纹。
预防措施为:①选用小钢锭开坯轧制各种规格的刀具原材料;②选用二次精炼电渣重熔钢锭,它具有纯度高、杂质少、晶粒细、碳化物小、组织均匀、无宏观冶金缺陷等优点;③对不合格原材料进行改锻,击碎材料中的共晶碳化物,使共晶碳化物不均匀度≤3级;④采取高温分级淬火、再高温回火的预处理工艺,通过精确控温等措施,可有效避免高速钢原材料冶金缺陷引起的淬火裂纹。
2 高速钢过热、过烧组织高速钢过热、过烧组织的特点为晶粒显着粗化,合金碳化物出现粘连、角状、拖尾状及沿晶界呈全网状、半网状或连续网状分布;钢组织内部局部熔化出现黑色组织或共晶莱氏体,形成过烧组织,显着降低晶间结合力和钢的强韧性。
冷酸洗检验规程
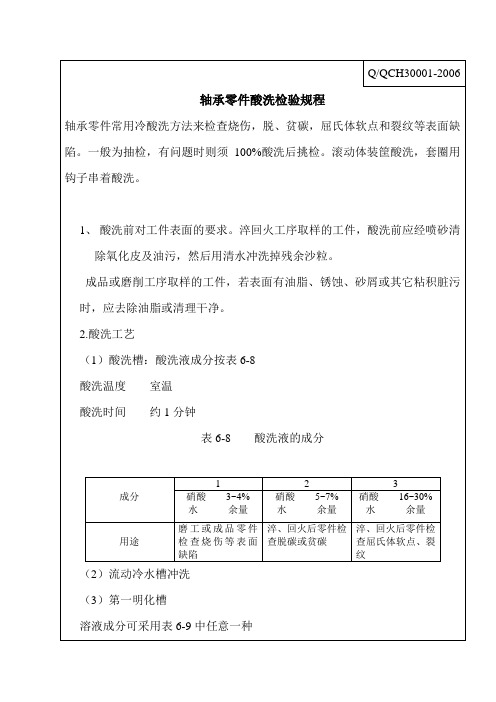
(2)流动冷水槽冲洗
(3)第一明化槽
溶液成分可采用表6-9中任意一种
表6-9第一明化槽溶液成分
名称
1
2
3
铬酐
8~15%
_
_
磷酸(H3PO4)
_
_
10~15%
氢氧化钠(NaOH)
_
3~5%
_
高锰酸钾(KMnO4)
_
3~5%
3~5%
磷酸三钠(Na3PO4)
_
6~9%
_
硫酸(H2SO4)
Q/QCH30001-2006
轴承零件酸洗检验规程
轴承零件常用冷酸洗方法来检查烧伤,脱、贫碳,屈氏体软点和裂纹等表面缺陷。一般为抽检,有问题时则须100%酸洗后挑检。滚动体装筐酸洗,套圈用钩子串着酸洗。
1、酸洗前对工件表面的要求。淬回火工序取样的工件,酸洗前应经喷砂清除氧化皮及油污,然后用清水冲洗掉残余沙粒。
0.3~0.4
_
_
水
余量
余量
余量
温度室温
时间10~20秒
(4)流动冷水槽冲洗
(5)第二明化槽
溶液成分盐酸(比重1.19)10~15%
二氯化锡0.2%
金属锡每槽(约100kg)加100g
水余量
温度室温
时间1~2min
(6)流动冷水槽冲洗
(7)中和槽
溶液成分碳酸钠4~6%
水余量
温度室温
时间约1分钟
(8)流动冷水槽冲洗
成品或磨削工序取样的工件,若表面有油脂、锈蚀、砂屑或其它粘积脏污时,应去除油脂或清理干净。
2.酸洗工艺
(1)酸洗槽:酸洗液成分按表6-8
酸洗温度室温
热处理淬火工艺过程中产生的缺陷

热处理淬火工艺过程中产生的缺陷热处理淬火工艺过程中产生的缺陷热处理淬火工艺过程中产生的缺陷1:淬火畸变与淬火裂纹:热处理过程中淬火畸变是不可避免的现象,只有超过规定公差或产生无法矫正时才构成废品,通过适当选择材料,改进结够设计,合理选择淬火,回火方法及规范等可有效的减小与控制淬火畸变,可采用冷热效直,热点校直和加热回火等加以休正。
裂纹是不可补救的淬火缺陷,只有采取积极的预防措施,如减小和控制淬火应力方向分布,同时控制原材料质量和正确的结构设计等。
2:氧化-脱碳-过热-过烧零件加热过程中,若不进行表面防护,将发生氧化脱碳等缺陷,其后果是表面淬硬性降低,达不到技术要求,或在零件表面形成网状裂纹,并严重降低零件外观质量,加大零件粗糙度,甚至超差,所以精加工零件淬火加热需要在保护气氛下或盐浴炉内进行,小批量可采用防氧化表面涂层加以防护。
过热导致淬火后形成粗大的马氏体组织将导致淬火裂纹形成或严重降低淬火件的冲击韧度,极易发生沿晶短裂,应当正确选择淬火加热温度,适当缩短保温时间,并严格控制炉温加以防止,出现的过热组织如有足够的加工余地余量可以重新退火,细化晶粒再次淬火返修。
过烧常发生在淬火高速钢中,其特点是产生了鱼骨状共晶莱氏体,过烧后使淬火钢严重脆性形成废品。
3:硬度不足淬火回火后硬度不足一般是由于淬火加热不足,表面脱碳,在高碳合金钢中淬火残余奥氏体过多,或回火不足造成的,在含CR轴承钢油淬时还经常发现表面淬火后硬度低于内层现象,这是逆淬现象,主要由于零件在淬火冷却时如果淬入了蒸汽膜期较长,特征温度低的油中,由于表面受蒸气膜的保护,孕化期比中心长,从而比心部更容易出现逆淬现象。
4:软点淬火零件出现的硬度不均匀叫软点,与硬度不足的主要区别是在零件表面上硬度有明显的忽高忽低现象,这种缺陷是由于原始组织过于粗大不均匀,(如有严重的组织偏析,存在大块状碳化物或大块自由铁素体)淬火介质被污染,零件表面有氧化皮或零件在淬火液中未能适当的运动,致使局部地区形成蒸气膜阻碍了冷却等因素,通过晶相分析并研解工艺执行情况,可以进一步判明究竟是什么原因造成废品。
渗碳淬火的问题和对策
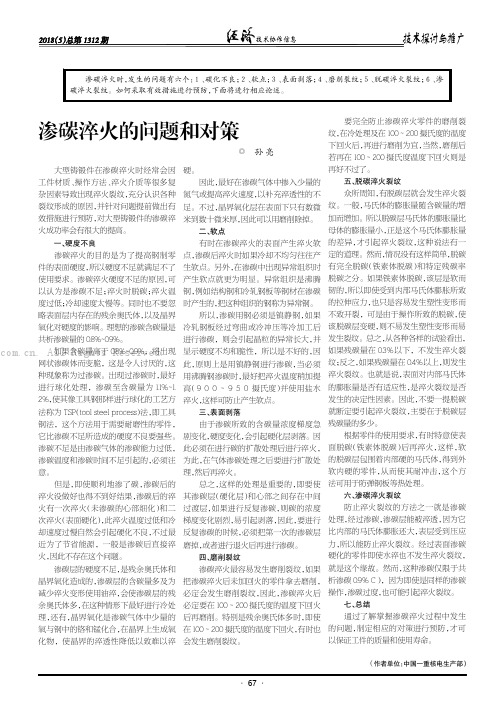
大型铸锻件在渗碳淬火时经常会因工件材质、操作方法、淬火介质等很多复杂因素导致出现淬火裂纹,充分认识各种裂纹形成的原因,并针对问题提前做出有效措施进行预防,对大型铸锻件的渗碳淬火成功率会有很大的提高。
一、硬度不良渗碳淬火的目的是为了提高钢制零件的表面硬度,所以硬度不足就满足不了使用要求。
渗碳淬火硬度不足的原因,可以认为是渗碳不足;淬火时脱碳;淬火温度过低;冷却速度太慢等。
同时也不要忽略表面层内存在的残余奥氏体,以及晶界氧化对硬度的影响。
理想的渗碳含碳量是共析渗碳量的0.8%~0.9%。
如果含碳量高于0.8%~0.9%,将出现网状渗碳体而变脆,这是令人讨厌的,这种现象称为过渗碳。
出现过渗碳时,最好进行球化处理,渗碳至含碳量为1.1%~1.2%,使其像工具钢那样进行球化的工艺方法称为TSP (tool steel process )法,即工具钢法,这个方法用于需要耐磨性的零件,它比渗碳不足所造成的硬度不良要强些。
渗碳不足是由渗碳气体的渗碳能力过低,渗碳温度和渗碳时间不足引起的,必须注意。
但是,即使顺利地渗了碳,渗碳后的淬火没做好也得不到好结果,渗碳后的淬火有一次淬火(未渗碳的心部细化)和二次淬火(表面硬化),此淬火温度过低和冷却速度过慢自然会引起硬化不良,不过最近为了节省能源,一般是渗碳后直接淬火,因此不存在这个问题。
渗碳层的硬度不足,是残余奥氏体和晶界氧化造成的,渗碳层的含碳量多及为减少淬火变形使用油淬,会使渗碳层的残余奥氏体多,在这种情形下最好进行冷处理,还有,晶界氧化是渗碳气体中少量的氧与钢中的铬和锰化合,在晶界上生成氧化物,使晶界的淬透性降低以致难以淬硬。
因此,最好在渗碳气体中掺入少量的氮气或提高淬火速度,以补充淬透性的不足。
不过,晶界氧化层在表面下只有数微米到数十微米厚,因此可以用磨削除掉。
二、软点有时在渗碳淬火的表面产生淬火软点,渗碳后淬火时如果冷却不均匀往往产生软点。
另外,在渗碳中出现异常组织时产生软点就更为明显。
- 1、下载文档前请自行甄别文档内容的完整性,平台不提供额外的编辑、内容补充、找答案等附加服务。
- 2、"仅部分预览"的文档,不可在线预览部分如存在完整性等问题,可反馈申请退款(可完整预览的文档不适用该条件!)。
- 3、如文档侵犯您的权益,请联系客服反馈,我们会尽快为您处理(人工客服工作时间:9:00-18:30)。
3、可以采用磁力探伤法及荧光探伤法检查零件是 否有裂纹,需要有一定检测设备。
五、淬火过热与淬火裂纹
工件一旦过热,则奥氏体晶粒和马氏体针粗大,容易 产生显微裂纹。这种显微裂纹是淬火裂纹激发源,并发 展成为淬火裂纹。因此。过热容易淬火裂纹。 生产现场中淬火过热引起的淬火裂纹在工具钢中很 常见,特别是高合金工模具钢因淬火过热造成工件裂纹 的事例最多。
防止工模具零件因淬火过热开裂主要措施:
2、定期检查校对和维修测温仪表和控温仪表, 保证仪表运转正常用。保证测温、定温、调温时准 确无误; 3、要随时观察炉温的情况,采用二重或多重控 温,发现炉温异常变化时,及时解决,必要时立即 停产,重新测温,待炉温恢复正常后再进行生产;
4、设备要保证工艺要求。
锻造裂纹还是磨削裂纹等是很重要的,这 样便于准确查找裂纹发生在哪一工序,有 利于分析裂纹产生的原因。
淬火裂纹和磨削裂纹形态特征区别
淬火时未发现而在磨削发现 的裂纹,要区别是淬火裂纹 还是磨削裂纹,未污染时比 较容易,此时要看裂纹形态, 特别是裂纹发展方向,磨削 裂纹垂直于磨削方向,呈平 行线形态(如图1)或呈龟甲 状裂纹(如图2)。磨削裂纹 深度浅,而淬火裂纹一般都 比较深,与磨削方向无关, 多呈直线刀割状开裂。
六、加热速度过快、加热不均匀与淬火裂纹
高合金工模具工件多采用两段预热,减缓工件内外温差, 得到充分均匀加热,减少加热应力,缩短工件高温加热时间; 高合金工模具因成分中合金元素含量高,导热率低,加热 速度必须缓慢,加热过快容易导致开裂; 因炉渣温度高,工件接触到炉渣使工件局部温度升高,淬 火前要对盐浴炉认真清氧捞渣;
裂纹断口的显微形貌特征
在显微组织中,淬火裂纹沿晶界发展,若 不是晶界断裂而是晶内断裂,不是淬火裂纹。 如果裂纹周围有脱碳层存在,不是淬火 裂纹,裂纹淬火前就存在,因为淬火裂纹是 淬火冷却时产生的,不会发生脱碳现象。
四、检查裂纹的方法
1、可以肉眼或低倍放大直接观察,进一步还可用 浸油探伤法探查,即将零件浸入到煤油或汽油中, 稍后取出零件擦拭干净,再涂以石灰粉或其他白 粉,如有裂纹,则在白色部分有油渗出。 2、可以用锤击辨声方法检查是否开裂,锤击零件 时如果发出清脆的金属声音,尾音较长,即没有 裂纹;反之,若发出重浊声音,就出现裂纹。
电炉加热元件布置要均匀合理,以保证炉内温度均匀一致, 避免引起工件加热不均匀。
七、淬火冷却速度与淬火裂纹
加热零件高温急冷淬火,产生的热应力使零件外 层受压,内层受拉,对防止淬火有利。在马氏体Ms 至Mf温度区间发生相变应力,与热应力相反,在此
区域内冷却速度越大,则相变应力越大,表面层的
拉应力越大,容易导致淬火裂纹的发生。 零件在钢的马氏体转变Ms至Mf温度区间冷却速度 过大,使热应力与组织应力叠加,拉应力达到最大 值,容易发生裂纹。
工模具零件热处理开裂 分析与对策
一、 零件热处理裂纹产生的原因
零件在热处理过程中会产生很大的内应力(组织 应力和热应力),超过钢的屈服强度时,会引起零件 变形;超过钢的抗拉强度时,则会造成零件开裂。 零件内应力有两种:压应力和拉应力。拉应力是 引起淬火裂纹的基本原因。
淬火裂纹的形成部位往往具备两个条件:一是具 有组织缺陷导致抗拉强度降低(原材料缺陷、设计及 机械加工不当造成的缺陷等);二是该部位拉应力较 高,超过该处材料抗拉强度。
图l 平行线状磨削裂纹
图2 龟甲状磨削裂纹
裂纹发生的部位印 处、打钢印处及机械加工造成的表面缺 陷等部位,在这些部位发生的裂纹多属 淬火裂纹。
裂纹断口的宏观形貌特征
通过观察零件断口区分淬火裂纹还是淬火前的锻 造裂纹或其他情况造成的裂纹。
若断口呈白色或暗白色或浅红色(水淬造成的水 锈),均可断定为淬火裂纹;若断口呈深褐色,甚 至有氧化色出现,就不是淬火裂纹,是淬火前存 在的裂纹,如锻造或压延时形成的裂纹,这些裂 纹都会因淬火而被扩大。因淬火裂纹形成温度低, 断口不会被氧化的。
实际生产对零件采用双液淬火、分级淬火和等温淬 火等,其目的就是为了在马氏体转变区域内缓冷,尽 量使零件内外层同时发生组织转变,力求使组织应力 达到最小值,以避免裂纹的发生。表1是某厂生产的 高速钢制弧形键槽铣刀,由于采用的冷却方式不同则 产生裂纹的数量和百分率也不同。
八、清洗过早引起的淬火裂纹
尺寸较大的工件,淬火冷却后表面看 上去冷的差不多了,但其心部温度仍比较 高,仍在进行着马氏体转变。此时若将工 件放入冷水中(特别在冬季的冷水中)清 洗,等于在马氏体转变区域内加速冷却, 产生的内应力将会增加,使工件发生开裂, 这种裂纹仍为淬火裂纹。因此,工件必须 完全冷透后再清洗。
二、裂纹的类型
按裂纹的方向区分:有纵向裂纹、横向 裂纹、弧形裂纹和网状裂纹(又称龟裂)等;
按裂纹发生的位置区分:有表层裂纹 (或称表面裂纹)和内部裂纹; 按裂纹发生在不同的工序区分:有锻造 裂纹、焊接裂纹、淬火裂纹、回火裂纹、 冷处理裂纹、酸洗裂纹及磨削裂纹等。
三、裂纹的分辨方法
如何区分究竟是淬火裂纹、回火裂纹、
图3 m=12、外径 Φ170mm的 W18Cr4V钢盘形 齿轮铣刀裂纹
防止工模具零件因淬火过热开裂主要措施:
1、制定正确合理的加热温度和加热方法。如对 一些大规格碳化物偏析较严重的高合金钢工模具, 应采取下限的淬火加热温度,为保证加热充分,可 适当延长加热时间,对一些带尖角的零件应离炉内 加热体远一些,在盐浴炉中工件距电极距离不得小 于50mm,以免引起尖角过热;
九、萘状断口与淬火裂纹
萘状断口是一种具有与萘的闪光相似的粗糙断口,是高速钢 零件常见缺陷。产生萘状断口零件显微组织特点是奥氏体晶 粒很大且不均匀,个别粗大晶粒尺寸可达0.1~1mm。 萘状断口对钢性能影响:其淬火回火后硬度和红硬性与正常 零件基本相当,但强度明显降低,特别是韧性更低。用高速 钢模具一旦产生萘状断口,在淬火时容易形成淬火裂纹,校 直时易压断,易崩刃和折断。 萘状断口的形成:一是钢在锻、轧等热塑性变形时终了温度 过高(1050~1000℃)时;二是重复淬火时无中间退火或退 火不充分造成。 萘状断口防止措施:①严格控制终锻温度,使其≤1000℃。 ②锻件毛坯充分退火。③返修零件在重新淬火前必须进行充 分退火, 退火硬度≤HRC28。