氯离子腐蚀混凝土中钢筋的腐蚀
水泥中氯离子对钢筋的腐蚀

氯离子对钢筋腐蚀机理的影响[摘要] 氯化物的侵入是引起混凝土中钢筋腐蚀的最主要原因之一,氯离子能破坏钢筋表面钝化膜而引起钢筋局部腐蚀,对腐蚀过程具有催化作用。
但只有混凝土中氯离子的浓度达到一定的临界值后,钢筋才会发生腐蚀。
由于影响因素多,至今难以确定统一的氯离子浓度临界值。
着重阐述了钢筋腐蚀行为和氯离子的去钝化机理、混凝土中氯离子的来源和保护钢筋的措施及其研究进展。
[关键词] 钢筋混凝土;钢筋;腐蚀;氯离子0 前言钢筋在混凝土高碱性环境中的钝态条件被破坏,便被腐蚀。
钢筋钝化膜破坏机理主要是混凝土的碳化和氯化物侵入,这两种因素既影响混凝土孔隙液的pH值,又影响钢筋的电位值,因而直接影响钢筋的稳定性。
因氯化物的侵蚀引起钢筋混凝土构筑物破坏而造成重大损失的现象非常严重。
北京西直门立交桥于1979年建成投入使用,不到20a钢筋混凝土的腐蚀已十分严重,不得不进行改建。
引起西直门立交桥过早破坏的原因是多方面的,但长期在冬季向立交桥撒含氯化物除冰盐引起钢筋腐蚀使立交桥结构受到破坏是突出的因素。
台湾四面环海,许多钢筋混凝土构筑物受破坏以及不断发生的“海砂屋”事件,也是氯化物侵蚀所引起的。
目前,中国大陆也存在“海砂屋”现象。
氯离子的侵蚀引起钢筋局部腐蚀是最有害的,对此,各国都给予了高度的重视。
由于钢筋混凝土结构的复杂性和研究条件的差异,研究结果和结论并不完全一致,许多问题还有待深入研究。
本工作主要对国内外氯离子与钢筋腐蚀系的研究进展和防止氯化物侵蚀的措施进行评述。
1 钢筋腐蚀与氯离子去钝化机理钢筋混凝土是多相、不均质的特殊复杂体系,钢筋表面具有电化学不均匀性,存在着电位较负的阳极区和电位较正的阴极区;一般钢筋表面总处于混凝土孔隙液膜中,即钢筋表面阳极区和阴极区之间存在电解质溶液;由于混凝土的多孔性,其构筑物总是透气和透水的,即通常氧可以通过毛细孔道达到钢筋表面作为氧化剂接受钢筋发生腐蚀产生的自由电子。
因此,钢筋表面存在活化状态,则可构成腐蚀电池,钢筋就会发生电化学腐蚀。
氯离子对钢筋的锈蚀
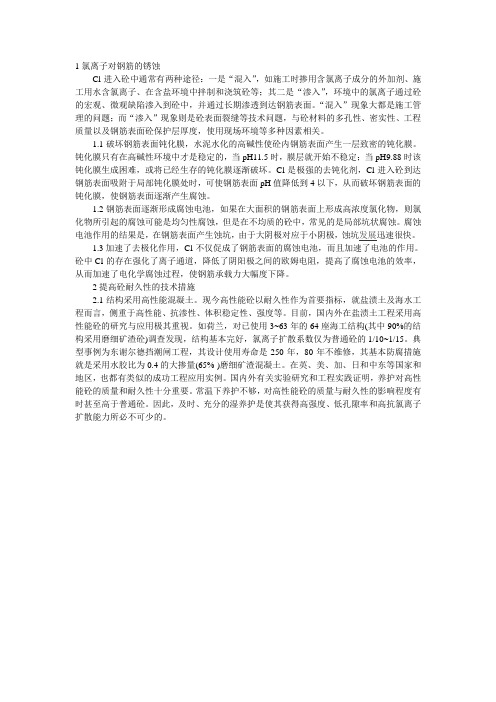
1氯离子对钢筋的锈蚀Cl-进入砼中通常有两种途径:一是“混入”,如施工时掺用含氯离子成分的外加剂、施工用水含氯离子、在含盐环境中拌制和浇筑砼等;其二是“渗入”,环境中的氯离子通过砼的宏观、微观缺陷渗入到砼中,并通过长期渗透到达钢筋表面。
“混入”现象大都是施工管理的问题;而“渗入”现象则是砼表面裂缝等技术问题,与砼材料的多孔性、密实性、工程质量以及钢筋表面砼保护层厚度,使用现场环境等多种因素相关。
1.1破坏钢筋表面钝化膜,水泥水化的高碱性使砼内钢筋表面产生一层致密的钝化膜。
钝化膜只有在高碱性环境中才是稳定的,当pH11.5时,膜层就开始不稳定;当pH9.88时该钝化膜生成困难,或将已经生存的钝化膜逐渐破坏。
Cl-是极强的去钝化剂,Cl-进入砼到达钢筋表面吸附于局部钝化膜处时,可使钢筋表面pH值降低到4以下,从而破坏钢筋表面的钝化膜,使钢筋表面逐渐产生腐蚀。
1.2钢筋表面逐渐形成腐蚀电池,如果在大面积的钢筋表面上形成高浓度氯化物,则氯化物所引起的腐蚀可能是均匀性腐蚀,但是在不均质的砼中,常见的是局部坑状腐蚀。
腐蚀电池作用的结果是,在钢筋表面产生蚀坑,由于大阴极对应于小阴极,蚀坑发展迅速很快。
1.3加速了去极化作用,Cl-不仅促成了钢筋表面的腐蚀电池,而且加速了电池的作用。
砼中Cl-的存在强化了离子通道,降低了阴阳极之间的欧姆电阻,提高了腐蚀电池的效率,从而加速了电化学腐蚀过程,使钢筋承载力大幅度下降。
2提高砼耐久性的技术措施2.1结构采用高性能混凝土。
现今高性能砼以耐久性作为首要指标,就盐渍土及海水工程而言,侧重于高性能、抗渗性、体积稳定性、强度等。
目前,国内外在盐渍土工程采用高性能砼的研究与应用极其重视。
如荷兰,对已使用3~63年的64座海工结构(其中90%的结构采用磨细矿渣砼)调查发现,结构基本完好,氯离子扩散系数仅为普通砼的1/10~1/15。
典型事例为东谢尔德挡潮闸工程,其设计使用寿命是250年,80年不维修,其基本防腐措施就是采用水胶比为0.4的大掺量(65% )磨细矿渣混凝土。
混凝土中钢筋腐蚀防护技术及实例分析

混凝土中钢筋腐蚀防护技术及实例分析一、背景介绍混凝土作为一种常见的建筑材料,在建筑工程中被广泛应用。
但是,在长期的使用过程中,混凝土中的钢筋很容易发生腐蚀,导致混凝土的强度降低、裂缝增加,严重影响建筑物的使用寿命和安全性。
因此,针对混凝土中钢筋腐蚀的问题,开展防护措施是十分必要的。
二、钢筋腐蚀的原因1.水泥碱性混凝土中的水泥具有强碱性,当钢筋暴露在混凝土中时,水泥的碱性会破坏钢筋表面的保护层,使其失去防腐能力,从而导致钢筋腐蚀。
2.氯离子侵蚀氯离子是混凝土中重要的化学成分之一,但是过多的氯离子会加速混凝土中钢筋的腐蚀。
当混凝土中的氯离子浓度达到一定程度时,就会造成钢筋表面的保护层被破坏,从而引起钢筋腐蚀。
3.混凝土中的电化学反应混凝土中的电化学反应也是导致钢筋腐蚀的一个原因。
当混凝土中的水分进入钢筋表面的保护层时,就会引起电化学反应,从而使得钢筋表面的保护层被破坏,导致钢筋腐蚀。
三、混凝土中钢筋腐蚀防护技术1.使用防腐涂料防腐涂料是一种常用的防腐材料,可以有效地保护钢筋不被腐蚀。
在混凝土中使用防腐涂料的方法是,在混凝土浇筑前将钢筋表面涂上防腐涂料,使其形成一层防腐保护层。
2.采用不锈钢钢筋不锈钢钢筋具有很好的抗腐蚀性能,可以有效地防止钢筋腐蚀。
在混凝土中使用不锈钢钢筋的方法是,将不锈钢钢筋代替普通钢筋使用,在混凝土中起到支撑作用。
3.使用防腐混凝土防腐混凝土是一种添加了特殊防腐剂的混凝土,可以有效地防止钢筋腐蚀。
在混凝土中使用防腐混凝土的方法是,在混凝土浇筑前,将特殊防腐剂加入混凝土中,使混凝土具有防腐蚀的能力。
四、实例分析以某高层建筑的混凝土结构为例,该建筑的主体结构使用了普通钢筋混凝土。
由于建筑所处的区域气候潮湿,加之建筑本身的使用年限较长,钢筋腐蚀的问题日益凸显,严重影响了建筑的使用寿命和安全性。
为了解决这个问题,施工方采用了以下措施:1.使用防腐涂料在混凝土浇筑前,先将钢筋表面涂上一层防腐涂料,形成一层防腐保护层。
氯离子含量对混凝土质量的危害及预防措施
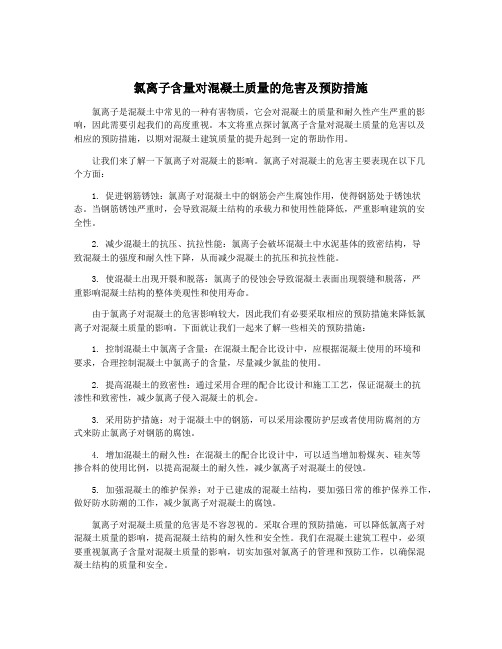
氯离子含量对混凝土质量的危害及预防措施氯离子是混凝土中常见的一种有害物质,它会对混凝土的质量和耐久性产生严重的影响,因此需要引起我们的高度重视。
本文将重点探讨氯离子含量对混凝土质量的危害以及相应的预防措施,以期对混凝土建筑质量的提升起到一定的帮助作用。
让我们来了解一下氯离子对混凝土的影响。
氯离子对混凝土的危害主要表现在以下几个方面:1. 促进钢筋锈蚀:氯离子对混凝土中的钢筋会产生腐蚀作用,使得钢筋处于锈蚀状态。
当钢筋锈蚀严重时,会导致混凝土结构的承载力和使用性能降低,严重影响建筑的安全性。
2. 减少混凝土的抗压、抗拉性能:氯离子会破坏混凝土中水泥基体的致密结构,导致混凝土的强度和耐久性下降,从而减少混凝土的抗压和抗拉性能。
3. 使混凝土出现开裂和脱落:氯离子的侵蚀会导致混凝土表面出现裂缝和脱落,严重影响混凝土结构的整体美观性和使用寿命。
由于氯离子对混凝土的危害影响较大,因此我们有必要采取相应的预防措施来降低氯离子对混凝土质量的影响。
下面就让我们一起来了解一些相关的预防措施:1. 控制混凝土中氯离子含量:在混凝土配合比设计中,应根据混凝土使用的环境和要求,合理控制混凝土中氯离子的含量,尽量减少氯盐的使用。
2. 提高混凝土的致密性:通过采用合理的配合比设计和施工工艺,保证混凝土的抗渗性和致密性,减少氯离子侵入混凝土的机会。
3. 采用防护措施:对于混凝土中的钢筋,可以采用涂覆防护层或者使用防腐剂的方式来防止氯离子对钢筋的腐蚀。
4. 增加混凝土的耐久性:在混凝土的配合比设计中,可以适当增加粉煤灰、硅灰等掺合料的使用比例,以提高混凝土的耐久性,减少氯离子对混凝土的侵蚀。
5. 加强混凝土的维护保养:对于已建成的混凝土结构,要加强日常的维护保养工作,做好防水防潮的工作,减少氯离子对混凝土的腐蚀。
氯离子对混凝土质量的危害是不容忽视的。
采取合理的预防措施,可以降低氯离子对混凝土质量的影响,提高混凝土结构的耐久性和安全性。
氯离子对钢筋混凝土腐蚀机理的影响研究
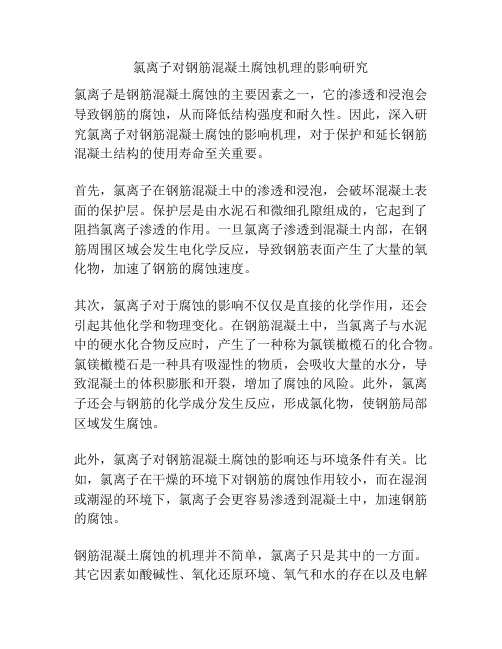
氯离子对钢筋混凝土腐蚀机理的影响研究氯离子是钢筋混凝土腐蚀的主要因素之一,它的渗透和浸泡会导致钢筋的腐蚀,从而降低结构强度和耐久性。
因此,深入研究氯离子对钢筋混凝土腐蚀的影响机理,对于保护和延长钢筋混凝土结构的使用寿命至关重要。
首先,氯离子在钢筋混凝土中的渗透和浸泡,会破坏混凝土表面的保护层。
保护层是由水泥石和微细孔隙组成的,它起到了阻挡氯离子渗透的作用。
一旦氯离子渗透到混凝土内部,在钢筋周围区域会发生电化学反应,导致钢筋表面产生了大量的氧化物,加速了钢筋的腐蚀速度。
其次,氯离子对于腐蚀的影响不仅仅是直接的化学作用,还会引起其他化学和物理变化。
在钢筋混凝土中,当氯离子与水泥中的硬水化合物反应时,产生了一种称为氯镁橄榄石的化合物。
氯镁橄榄石是一种具有吸湿性的物质,会吸收大量的水分,导致混凝土的体积膨胀和开裂,增加了腐蚀的风险。
此外,氯离子还会与钢筋的化学成分发生反应,形成氯化物,使钢筋局部区域发生腐蚀。
此外,氯离子对钢筋混凝土腐蚀的影响还与环境条件有关。
比如,氯离子在干燥的环境下对钢筋的腐蚀作用较小,而在湿润或潮湿的环境下,氯离子会更容易渗透到混凝土中,加速钢筋的腐蚀。
钢筋混凝土腐蚀的机理并不简单,氯离子只是其中的一方面。
其它因素如酸碱性、氧化还原环境、氧气和水的存在以及电解质结构等,都会影响到钢筋的腐蚀。
所以,在对混凝土结构进行设计和施工时,必须综合考虑这些因素,并采取相应措施来减少钢筋的腐蚀。
总之,氯离子对钢筋混凝土腐蚀具有很大的影响。
了解氯离子对钢筋混凝土腐蚀的机理,有助于选择合适的材料和防护方式,保护钢筋混凝土结构的耐久性和使用寿命,从而确保建筑物的安全性和可靠性。
深入研究氯离子对钢筋混凝土腐蚀机理的影响,可以从以下几个方面进行探讨。
首先,氯离子的渗透和浸泡会导致钢筋混凝土的物理性能发生变化。
氯离子进入混凝土中后,会与水泥石和水化硬化产物中碱式氧化钙反应,生成不溶性的氯化钙。
这些反应会增加混凝土中的离子浓度,造成了内部的应力,从而导致混凝土的微裂缝和毛细孔隙增加。
混凝土中氯离子浓度的检测标准

混凝土中氯离子浓度的检测标准一、前言混凝土是建筑工程中广泛使用的一种材料,其性能的优劣直接影响到工程的安全性和耐久性。
然而,混凝土中含有的氯离子可能会导致混凝土的腐蚀和钢筋锈蚀,从而影响混凝土的使用寿命。
因此,对混凝土中氯离子浓度的检测十分重要。
本文将介绍混凝土中氯离子浓度的检测标准。
二、氯离子浓度对混凝土的影响氯离子是混凝土中的一种化学成分,如果混凝土中氯离子的浓度过高,将会对混凝土产生以下影响:1.腐蚀混凝土:氯离子能够破坏混凝土中的保护层,导致混凝土的腐蚀。
2.钢筋锈蚀:当混凝土中的氯离子浓度过高时,将会加速钢筋的腐蚀和锈蚀,从而降低混凝土的使用寿命。
3.降低混凝土的强度:氯离子能够与水泥中的化合物反应,从而影响混凝土的强度和稳定性。
因此,为了保证混凝土的使用寿命和安全性,必须对混凝土中氯离子浓度进行检测。
三、混凝土中氯离子浓度的检测方法混凝土中氯离子浓度的检测方法主要有以下几种:1.离子选择电极法:该方法利用离子选择电极对混凝土中的氯离子进行检测,具有检测速度快、准确度高等优点。
2.电导率法:该方法通过测量混凝土中的电导率来确定氯离子的浓度,具有检测速度快、操作简便等优点。
3.荧光光谱法:该方法利用荧光光谱仪对混凝土中的氯离子进行检测,具有检测精度高、分析速度快等优点。
4.化学分析法:该方法通过化学分析的方式来测定混凝土中的氯离子浓度,具有准确度高、可靠性好等优点。
四、混凝土中氯离子浓度的检测标准根据《钢筋混凝土结构工程施工质量验收规范》(GB 50204-2015)和《混凝土结构工程施工质量验收规范》(GB 50203-2011)的相关规定,混凝土中氯离子浓度的检测标准如下:1.普通混凝土:混凝土中氯离子浓度不得超过0.4%。
2.高性能混凝土:混凝土中氯离子浓度不得超过0.2%。
3.海洋工程混凝土:混凝土中氯离子浓度不得超过0.1%。
4.防水混凝土:混凝土中氯离子浓度不得超过0.1%。
混凝土中钢筋锈蚀的原因及危害和预防措施
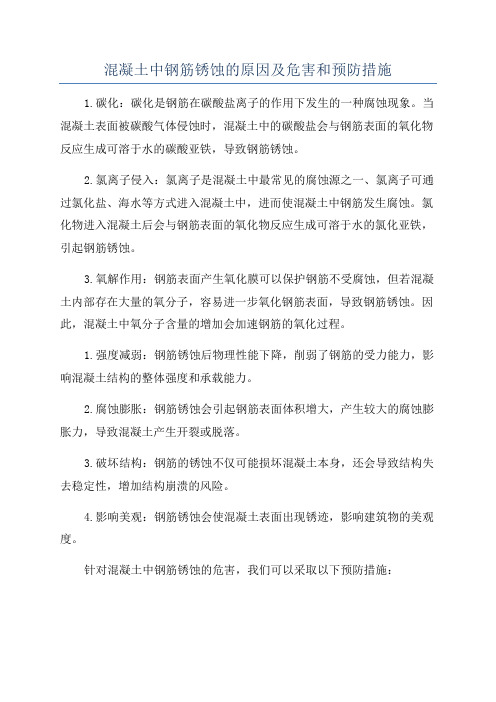
混凝土中钢筋锈蚀的原因及危害和预防措施1.碳化:碳化是钢筋在碳酸盐离子的作用下发生的一种腐蚀现象。
当混凝土表面被碳酸气体侵蚀时,混凝土中的碳酸盐会与钢筋表面的氧化物反应生成可溶于水的碳酸亚铁,导致钢筋锈蚀。
2.氯离子侵入:氯离子是混凝土中最常见的腐蚀源之一、氯离子可通过氯化盐、海水等方式进入混凝土中,进而使混凝土中钢筋发生腐蚀。
氯化物进入混凝土后会与钢筋表面的氧化物反应生成可溶于水的氯化亚铁,引起钢筋锈蚀。
3.氧解作用:钢筋表面产生氧化膜可以保护钢筋不受腐蚀,但若混凝土内部存在大量的氧分子,容易进一步氧化钢筋表面,导致钢筋锈蚀。
因此,混凝土中氧分子含量的增加会加速钢筋的氧化过程。
1.强度减弱:钢筋锈蚀后物理性能下降,削弱了钢筋的受力能力,影响混凝土结构的整体强度和承载能力。
2.腐蚀膨胀:钢筋锈蚀会引起钢筋表面体积增大,产生较大的腐蚀膨胀力,导致混凝土产生开裂或脱落。
3.破坏结构:钢筋的锈蚀不仅可能损坏混凝土本身,还会导致结构失去稳定性,增加结构崩溃的风险。
4.影响美观:钢筋锈蚀会使混凝土表面出现锈迹,影响建筑物的美观度。
针对混凝土中钢筋锈蚀的危害,我们可以采取以下预防措施:1.控制混凝土材料质量:选择合适的水泥、骨料等混凝土材料,确保混凝土的密实性和均匀性,减少表面孔隙的形成,降低钢筋暴露和腐蚀的风险。
2.正确设计:在混凝土结构设计时,根据环境条件和使用要求,合理选择混凝土覆盖层的厚度,保证钢筋能够得到有效的保护。
3.防水措施:采取有效的防水措施,减少混凝土暴露在潮湿环境中的时间和程度,降低钢筋腐蚀的可能性。
4.防止氯离子侵入:加强混凝土中氯离子的阻隔,可以采用减少混凝土中的氯离子含量、加入阻隔氯化物的抗腐蚀剂或使用防腐蚀涂层等方法。
5.确保质量检测:对于混凝土的施工过程,进行质量检测,及时了解混凝土结构中的钢筋腐蚀情况,以便于及时采取措施修复和预防。
总之,混凝土中钢筋锈蚀会对建筑物的使用寿命和结构稳定性造成重大影响,因此,在混凝土的设计、施工和维护过程中应采取有效的预防措施,以延长建筑物的使用寿命和保障建筑结构的安全性。
混凝土中氯离子对钢筋锈蚀的影响原理

混凝土中氯离子对钢筋锈蚀的影响原理混凝土中氯离子对钢筋锈蚀的影响原理混凝土是一种复杂的多相材料,由水泥、水、骨料、细集料和空气组成。
在混凝土结构中,钢筋是起到承受荷载的主要构件,而混凝土则是钢筋的保护层。
然而,混凝土中存在着一些化学物质,如氯离子,它们可能对钢筋的锈蚀产生影响。
钢筋在混凝土里的主要保护机制是氧化钙的形成,它可以保护钢筋不被氧化。
当氯离子进入混凝土中时,它们会与氧化钙反应,生成氯化钙,破坏氧化钙层,使钢筋暴露在外界环境下,容易被氧化而发生锈蚀。
氯离子的来源主要有三种:混凝土原材料中的氯离子、施工时使用的含氯材料以及外部环境中的氯离子。
混凝土原材料中的氯离子主要来自于骨料和水泥中的氯化物,而施工过程中使用的含氯材料包括加速凝结剂、养护剂、脱模剂等,这些材料中含有的氯离子在混凝土中会逐渐释放。
此外,外部环境中的氯离子也可能会进入混凝土结构中,如海水、路面融雪剂等。
混凝土中氯离子的浓度是影响钢筋锈蚀的主要因素之一。
当氯离子的浓度超过一定阈值时,就会对钢筋产生不可逆的损害。
氯离子的浓度受到混凝土的配合比、骨料种类、水泥种类、养护质量等因素的影响。
一般来说,配合比中水灰比越小,氯离子的扩散越慢,混凝土的抗氯离子渗透能力越强。
而使用高抗氯水泥、优质骨料以及严格的养护措施也能够提高混凝土的抗氯离子渗透能力,减少氯离子对钢筋的影响。
此外,混凝土中氯离子的扩散也是影响钢筋锈蚀的重要因素之一。
氯离子的扩散受到混凝土的孔结构、温度、湿度等因素的影响。
孔结构是决定混凝土抗氯离子渗透能力的主要因素之一,孔径越小、孔隙率越小的混凝土抗氯离子渗透能力越强。
温度和湿度也会影响氯离子的扩散速度,一般来说,温度越高、湿度越大,氯离子的扩散速度越快。
综上所述,混凝土中氯离子对钢筋锈蚀的影响是非常复杂的,它受到混凝土的配合比、骨料种类、水泥种类、养护质量、氯离子浓度、氯离子扩散等多种因素的影响。
为了保护混凝土结构中的钢筋,需要从多个方面入手,采取有效的措施,如合理设计混凝土配合比、选用高抗氯水泥和高品质骨料、加强混凝土结构的养护等,以减少氯离子对钢筋的影响,延长混凝土结构的使用寿命。
- 1、下载文档前请自行甄别文档内容的完整性,平台不提供额外的编辑、内容补充、找答案等附加服务。
- 2、"仅部分预览"的文档,不可在线预览部分如存在完整性等问题,可反馈申请退款(可完整预览的文档不适用该条件!)。
- 3、如文档侵犯您的权益,请联系客服反馈,我们会尽快为您处理(人工客服工作时间:9:00-18:30)。
氯离子腐蚀混凝土中钢筋的腐蚀-第1部分:加速和自然环境下的实验研究土木与环境工程学院,威特沃特斯兰德大学,Johannesburg,南非土木工程系,开普顿大学,Rondebosch,南非摘要:平行腐蚀试验已经进行了两年,露出210梁(120×130×长375毫米)的一半在实验室加速腐蚀(干湿循环)另一半在海洋潮湿区接受自然腐蚀。
实验变量是裂缝宽度(0,初始裂缝,0.4、0.7毫米),覆盖面C(20,40毫米),粘结剂类型(PC、PC/矿渣,PC / FA)和水胶比(0.40,0.55)。
结果表明,腐蚀速率(icorr)受以下方式实验变量的影响:腐蚀随裂缝宽度的增加而增加,并随着混凝土的质量和覆盖深度的增加而降低。
研究结果还显示,混凝土在野外环境下的自然腐蚀的腐蚀性能不能推断出其在实验室加速腐蚀的性能。
其他因素,如腐蚀进程也应考虑在内。
关键词:腐蚀速率预测,氯离子侵蚀,加速腐蚀,自然腐蚀,腐蚀,混凝土裂痕1 引言钢筋锈蚀是温度、海洋和工业环境中钢筋混凝土结构的主要破坏机制之一。
对于投资者和工程师来说,它已成为一个主要的耐久性问题。
如果不减弱这种侵蚀性,它会加速钢筋混凝土结构的恶化,可能会导致一系列相关的严重后果,包括但不限于开裂和混凝土保护层剥落,钢筋截面面积损失,降解的钢-混凝土界面粘结,最终减少钢筋混凝土结构的使用寿命。
另外在维护、修理或更换时,需要花费很高的费用,而且会对害公共安全有威胁。
即使在钢筋混凝土结构中钢筋锈蚀的主要因素是二氧化碳入口(碳化引起的)或氯(氯离子引起的),后者是在钢筋混凝土结构中钢筋锈蚀的主要原因。
值得注意的是,氯离子引起的腐蚀对所研究的结构造成的损害是比较大的,并在一个相对较短的时间内(在结构满足其目标服务寿命),有可能成为最终导致失败的因素(根据预先定义的极限状态)。
2、实验细节2.1、实验变量和混合比例平行腐蚀试验露出210束标本(120×130×375毫米)的一半进行加速实验室腐蚀(循环3天用5%的NaCl溶液润湿跟随开普敦4天空气干燥),另一半则被留在的海洋潮汐区自然腐蚀(表湾港)。
使用五种不同的混凝土使我们的横梁的W / B比(0.40和0.55),和三种粘结剂(100% CEM I 42.5 N普通波特兰水泥(PC),50 / 50 / 70 / 30的矿渣微粉和PC的PC / FA)。
0.55w/b比是不能用于电脑制作标本。
高产量强度直径为10毫米的钢筋嵌入在每个光束。
在表1中给出了混凝土配合比的总结和选定的具体性能。
其他实验变量包括盖深度(20和40毫米)和裂缝宽度(0,早期裂缝,0.4和0.7毫米)。
早期裂缝是指由梁试样三点荷载引起的裂缝,然后卸载。
虽然以前的研究已经表明,裂缝宽度≤0.3毫米容易自愈[ 17–19 ],初始裂纹试样由于缺乏AP 适当的测试设备,量化裂缝自愈是不可能的。
此外,对于更深的覆盖面(40毫米)再加上裂纹愈合的敏感性,可以预料的是,早期裂缝会对腐蚀离子的速率有微不足道的影响。
因此,20毫米覆盖面的初期裂痕的标本仅用于实验室和野外标本。
钢棒两端均覆盖有电镀带和环氧树脂—涂层提供了一种有效的暴露的表面面积大约86平方厘米(长约27.5厘米的圆周表面)。
在铸造之前、这种棒将会被清洗并且用一个直径10毫米长150毫米的不锈钢棒放置在每个光束在铸造过程中(见图1)作为反电极的腐蚀速率测量。
2.2活性腐蚀状态的诱导经过28天的水养护(在23°2°C )和10天空气干燥(温度:25°C ,相对湿度为:50°5%)在实验室,并在开裂前的梁试样,阳极电流(IC )是用以启动活性腐蚀率(即消除腐蚀起始阶段)在所有210束标本。
设置用于启动活性腐蚀在标本中使用集成电路如图1所示。
理论时间(t 港水平)和集成电路所需的驱动氯化物通过深度覆盖的钢级量估计使用能斯特-普朗克方程在下面的表格内。
能斯特-普朗克方程:t 钢水平= C [−D (ZF / RT )(∂E /∂x )]−1D 是扩散的离子系数(平方米/秒)在混凝土,Z 离子物种的价(1氯ˉ),F 是法拉第常数(96500℃/mol ),R 是气体常数(8.314 J / mol.k ),T 绝对温度(298 K ),C 是覆盖深度(20或40毫米)和E 是应用电位(V )。
扩散系数(D )得到从测量28天氯电导指数(CCI )基于实证的相关性和CCI 考虑效果海洋环境暴露,混凝土老化和粘结型[ 22 ] 20–即关联模型可以估计时间的曝光依赖于表观氯离子扩散系数一般为USED 粘结剂类型(主要是普通PC ,70/ 30和50 / 50的PC / FA PC /矿渣)和海洋暴露环境(潮、飞溅、喷雾)在南非的20–[ 22 ]。
第二部分,本文给出了更多的细节上的去从CCI 扩散系数的终止。
CCI 是每个表1混凝土从快速氯离子电导率测试[ 21,23 ]获得。
28天和90天的扩散系数诈骗的fficients 克里特用列于表2。
为了确定阳极IC 所需的诱导活性腐蚀速率在一个给定的覆盖深度的标本的五个混凝土混合物,和一系列的迭代后(时间D IC ),当时申请的IC 芯片被固定在1.5小时限制的有效电流小于2安培。
术语“有效的应用电流”是用来指实际应材料(千克/立方米)粘合剂组合物 100 % PC 50/50 PC/GGBS 70/30 PC/FA w/b 比0.40 0.400.55 0.400.55混合标签PC-40SL-40 SL-55 FA-40 FA-55 Portland cement, PC (CEM I 42.5 N) 500231 168 324 236 Ground granulated blastfurnace slag (GGBS) -231 168 - - Fly ash (FA) -- - 139 101 Fine aggregate: Klipheuwel sand (2 mm max.) 529749 855 749 855 Coarse aggregate: Granite (13 mm max.) 9601040 1040 1040 1040 Water 200 185 185 185 185 Superplasticizer a (SP) 2.1b (0.4)c 1.8 (0.4) 0.3 (0.1) 0.4 (0.1) - Slump (mm) 120105 150 85 200 28-day compressive strength (MPa) 58.2 (3.0)d 48.1 (2.0) 35.3 (0.9) 50.7 (0.9) 28.6 (1.9)用的目前考虑到相应的28天测电阻的(水)混凝土。
IC被限制到小于2安培,以确保氯化物达到钢和MInimize钢的质量损失,如果任何。
需要注意的是,所施加的电流理论上不会造成任何的钢的质量损失的重要;即使不通过实际测量确定啊F氯含量在钢的水平,目的是推动氯化物在约1.5小时内钢液面(考虑保护层厚度和混凝土的质量)。
梁在同一粘结剂类型、钨/硼比和盖层深度的串联中,适当的阳极集成电路连续1.5小时。
所施加的集成电路电流如下,在每一种情况下,重新分别为20毫米和40毫米的覆盖深度:(一)pc-40:0.03和0.13,(b)fa-40:0.44和1.67,(C)fa-55:0.25和1.01,(d)sl-40:0.57和1.70,和(e)sl-55:0.44和1.67,1.5个小时后,所有的72根梁进行串联,8.6μ一申请另一个2小时的有效电流–这是E我原以为在一个约0.1μ所有标本/cm2,腐蚀率的结果,即假定整个暴露的钢表面面积86 cm2偏振。
腐蚀速率为0.1μcm2通常采取表示从被动转变为主动(启动)(传播)腐蚀[24,25]。
2.3。
裂纹诱导与监测为便于形成一个预腐蚀的横向(弯曲)的裂纹在机器装载时,一个1毫米厚的4毫米厚的毫米深的聚氯乙烯片材的纵向中心的纵向中心作为放置在每个光束的中心(横向)在铸造过程中,聚氯乙烯片材被嵌入在光束模具,并没有保持在光束后,在24个小时的。
诱导后的活动E腐蚀,梁(除不开裂的)预裂荷载下三点弯曲机。
0.4和0.7毫米的裂纹试样,然后放置在个别装载钻机,他们整个实验的持续时间(图2)。
确保0.4毫米和0.7毫米的裂缝宽度保持不变,可拆卸的机械(demec)螺栓放在展在克里特岛的表面裂纹之间的距离钉监测每周使用100毫米demec计。
在图2所示的装载台,然后用于调整所需的裂缝宽度(通过螺栓和螺母。
2.4暴露环境诱导活性腐蚀后,一半的标本在暴露实验室加速腐蚀,而另一半却被迫在海洋潮汐区接受自然腐蚀。
暴露实验室-加速腐蚀实验室标本(见图3)用5%的NaCl溶液连续润湿3天后紧接着在(温度:25±2°C和相对湿度:50±5%)的条件下进行为期4天的干燥实验。
现场暴露-自然腐蚀该领域的标本在开普敦的潮汐海洋区(表湾海港)被暴露并进行自然腐蚀-见图4。
在暴露的网站上显示的测得的海水的盐度(氯离子含量)大约是2%(在实验期间的随机时间间隔情况下,平均10个样本,标准偏差= 0.02%)。
大气温度和相对湿度暴露领域的湿度范围为1至37°,分别为83%和65。
此类标本被安置在高低潮痕为7行,总长度约5米的外海行(靠近海水)和内地行(靠近陆地的)(见图4)。
因此认为他们的暴露具有相似的海洋潮汐条件。
在此类标本曝光之前,除了有指定的覆盖深度,所有此类标本的外部,都是用环氧涂层从干燥的表面防止腐蚀剂的侵蚀(CLˉ,O2和H2O),干燥的表面。
这确保了氯化物和实验标本一样,只能从指定深度覆盖的表面侵入混凝土。
2.5腐蚀速率和半电池电位测量恒电量技术进行腐蚀速率测量。
这是一个在在短时间内,小开关被用于检测钢铁和潜能的方法,确定极化电阻RP,[26,27]。
RP与腐蚀电流有关,由船尾Geary 系数B即腐蚀电流= B/RP即方法B是斯特恩Geary系数13和52 MV取决于钢的腐蚀状态(即被动或主动)。
腐蚀值为26 mV(主动)钢和52 mV的被动钢在混凝土的情况下,已经被建立并且被大量研究人员使用[ 28,30 ]。
因此,在这项研究中,使用了26个压的值。
腐蚀电流密度仍然被表示为D:icorr =Icorr/A。
这里的A是指约86平方厘米所暴露出的钢表面面积。
我们是用HP 34970A数据采集单元和MATLAB®程序分析来收集数据的。
半电池电位(HCP)的读数,以银/氯化银(Ag/AgCl)为参考电极,是和腐蚀速率测量同时进行的。