钒钛磁铁矿竖炉气基还原工艺的基础研究
气基竖炉直接还原低碳炼铁方案(一)
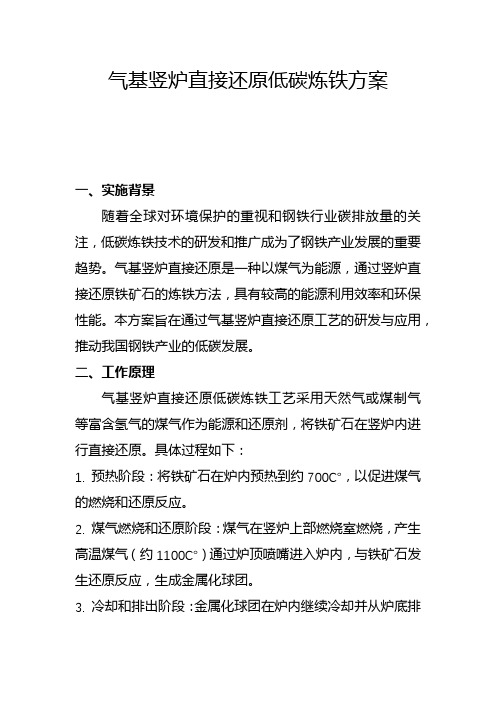
气基竖炉直接还原低碳炼铁方案一、实施背景随着全球对环境保护的重视和钢铁行业碳排放量的关注,低碳炼铁技术的研发和推广成为了钢铁产业发展的重要趋势。
气基竖炉直接还原是一种以煤气为能源,通过竖炉直接还原铁矿石的炼铁方法,具有较高的能源利用效率和环保性能。
本方案旨在通过气基竖炉直接还原工艺的研发与应用,推动我国钢铁产业的低碳发展。
二、工作原理气基竖炉直接还原低碳炼铁工艺采用天然气或煤制气等富含氢气的煤气作为能源和还原剂,将铁矿石在竖炉内进行直接还原。
具体过程如下:1. 预热阶段:将铁矿石在炉内预热到约700℃,以促进煤气的燃烧和还原反应。
2. 煤气燃烧和还原阶段:煤气在竖炉上部燃烧室燃烧,产生高温煤气(约1100℃)通过炉顶喷嘴进入炉内,与铁矿石发生还原反应,生成金属化球团。
3. 冷却和排出阶段:金属化球团在炉内继续冷却并从炉底排出。
4. 成品处理阶段:对金属化球团进行破碎、筛分、磁选等处理,得到最终产品。
三、实施计划步骤1. 研发与设计:开展气基竖炉直接还原工艺的基础研究和应用研究,设计适合我国钢铁产业的气基竖炉直接还原工艺流程和设备。
2. 设备制造与安装:根据设计要求,制造设备并在现场安装调试。
3. 工业试验:在制造和安装完成后,进行工业试验,验证工艺流程和设备的可行性和稳定性。
4. 生产调试:根据工业试验结果,对工艺流程和设备进行优化调整,逐步达到设计产能。
5. 技术服务与培训:提供相关技术服务和培训,确保企业能够自主运行和维护气基竖炉直接还原生产线。
四、适用范围本方案适用于大型钢铁企业和中小型民营钢铁企业。
特别是对于具有丰富铁矿资源和煤气资源的钢铁企业,气基竖炉直接还原低碳炼铁工艺具有较高的适用性和优势。
此外,对于地处环保要求较高地区或面临转型升级压力的钢铁企业,该工艺也具有较大的应用潜力。
五、创新要点1. 竖炉结构优化设计:通过对竖炉内部结构的优化设计,提高煤气与铁矿石的接触面积和热交换效率,降低能源消耗。
《气基直接还原竖炉炉型研究》范文

《气基直接还原竖炉炉型研究》篇一一、引言气基直接还原(DRI)作为钢铁行业中的关键工艺之一,一直受到行业内外专家学者的关注。
而作为实施气基直接还原的主要设备之一,竖炉的设计和优化对提高DRI生产效率、降低能耗、保证产品质量等具有重要意义。
本文将就气基直接还原竖炉的炉型进行研究,探讨其结构特点、操作性能以及优化方向。
二、气基直接还原竖炉概述气基直接还原技术是一种将铁矿石在高温下与还原性气体(如天然气、煤制气等)反应,将铁矿石还原成铁粉(DRI)的技术。
竖炉作为实施这一工艺的主要设备,其结构包括炉体、供气系统、排烟系统等。
通过竖炉内矿石与还原性气体的化学反应,达到将铁矿石转变为金属铁的目的。
三、竖炉结构及工作原理(一)炉体结构竖炉主要由进料系统、主体部分、排料系统等组成。
主体部分呈竖直筒形,其内壁需进行耐高温处理,以承受高温和化学反应的侵蚀。
(二)工作原理在竖炉内,铁矿石与高温还原性气体接触并发生化学反应。
在一定的温度和压力条件下,矿石中的氧化铁逐渐被还原成金属铁。
该过程需要在控制良好的气氛、温度和反应时间下进行,以保障产品的质量和生产效率。
四、气基直接还原竖炉炉型研究(一)不同炉型的特点根据进料方式、反应室设计、排料方式等因素,气基直接还原竖炉的炉型有多种类型。
不同类型竖炉在生产效率、能耗、产品质量等方面存在差异。
例如,对于进料方式,可采用连续进料或分批进料;反应室设计上,需要考虑气流分布、热能利用等因素。
(二)关键因素分析在炉型设计中,需考虑的主要因素包括矿石性质、还原性气体种类及来源、生产规模、环境因素等。
不同因素对竖炉的结构设计、操作性能和产品质量均有影响。
例如,矿石的粒度、化学成分将影响反应的速率和产品的质量;而还原性气体的种类和纯度则影响反应的效率和产品的性能。
(三)优化方向与案例分析针对当前存在的问题和需求,对竖炉进行优化和改进。
首先,提高竖炉的热能利用效率,通过优化气流分布、增加热回收装置等方式降低能耗;其次,改善矿石的还原效果,通过改进进料方式、调整反应温度等方式提高产品质量;最后,加强环保措施,减少排放,实现绿色生产。
第三章+钒钛磁铁矿直接还原基本原理
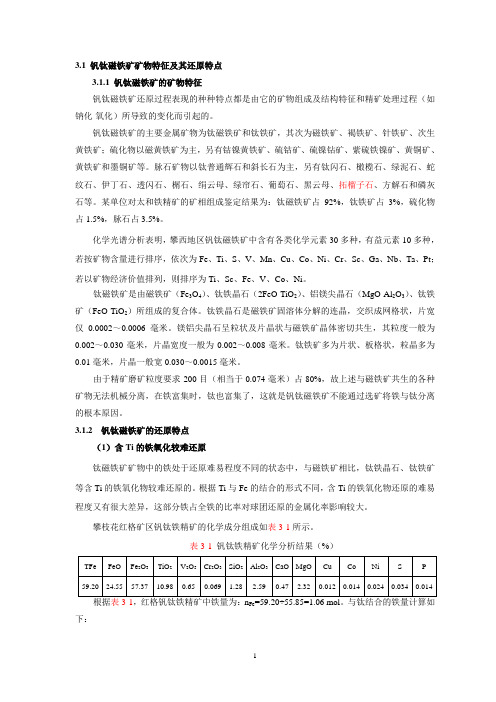
3.1 钒钛磁铁矿矿物特征及其还原特点3.1.1 钒钛磁铁矿的矿物特征钒钛磁铁矿还原过程表现的种种特点都是由它的矿物组成及结构特征和精矿处理过程(如钠化-氧化)所导致的变化而引起的。
钒钛磁铁矿的主要金属矿物为钛磁铁矿和钛铁矿,其次为磁铁矿、褐铁矿、针铁矿、次生黄铁矿;硫化物以磁黄铁矿为主,另有钴镍黄铁矿、硫钴矿、硫镍钻矿、紫硫铁镍矿、黄铜矿、黄铁矿和墨铜矿等。
脉石矿物以钛普通辉石和斜长石为主,另有钛闪石、橄榄石、绿泥石、蛇纹石、伊丁石、透闪石、榍石、绢云母、绿帘石、葡萄石、黑云母、拓榴子石、方解石和磷灰石等。
某单位对太和铁精矿的矿相组成鉴定结果为:钛磁铁矿占92%,钛铁矿占3%,硫化物占1.5%,脉石占3.5%。
化学光谱分析表明,攀西地区钒钛磁铁矿中含有各类化学元素30多种,有益元素10多种,若按矿物含量进行排序,依次为Fe、Ti、S、V、Mn、Cu、Co、Ni、Cr、Sc、Ga、Nb、Ta、Pt;若以矿物经济价值排列,则排序为Ti、Sc、Fe、V、Co、Ni。
钛磁铁矿是由磁铁矿(Fe3O4)、钛铁晶石(2FeO·TiO2)、铝镁尖晶石(MgO·Al2O3)、钛铁矿(FeO·TiO2)所组成的复合体。
钛铁晶石是磁铁矿固溶体分解的连晶,交织成网格状,片宽仅0.0002~0.0006毫米。
镁铝尖晶石呈粒状及片晶状与磁铁矿晶体密切共生,其粒度一般为0.002~0.030毫米,片晶宽度一般为0.002~0.008毫米。
钛铁矿多为片状、板格状,粒晶多为0.01毫米,片晶一般宽0.030~0.0015毫米。
由于精矿磨矿粒度要求-200目(相当于0.074毫米)占80%,故上述与磁铁矿共生的各种矿物无法机械分离,在铁富集时,钛也富集了,这就是钒钛磁铁矿不能通过选矿将铁与钛分离的根本原因。
3.1.2 钒钛磁铁矿的还原特点(1)含Ti的铁氧化较难还原钛磁铁矿矿物中的铁处于还原难易程度不同的状态中,与磁铁矿相比,钛铁晶石、钛铁矿等含Ti的铁氧化物较难还原的。
电炉熔分工艺处理钒钛磁铁矿

电炉熔分工艺处理钒钛磁铁矿电炉熔分工艺处理钒钛磁铁矿一、引言钒钛磁铁矿是一种重要的钛资源,广泛应用于冶金、化工、建材等领域。
然而,由于其复杂的化学成分和矿物结构,其加工和利用一直面临着挑战。
电炉熔分工艺是一种被广泛采用的处理钒钛磁铁矿的方法。
该方法通过利用电炉的高温和电能,将钒钛磁铁矿矿石在还原气氛下进行熔融和分离,以获得钛铁合金和钒铁合金等有价值的产品。
本文将深入探讨电炉熔分工艺处理钒钛磁铁矿的原理、技术及其在实际应用中的优势和发展前景。
二、电炉熔分工艺的原理及技术(1)原理概述电炉熔分工艺是利用电炉高温和电能的特点,将钒钛磁铁矿在还原条件下进行熔融和分离的过程。
在这个过程中,钒和铁进入钒铁合金,而钛则进入钛铁合金。
这种工艺的基本原理是根据各元素的熔点和还原性能的不同,通过合理的炉内温度和还原气氛控制,实现钒、铁、钛的分离和提取。
(2)技术要点在电炉熔分工艺中,关键的技术要点包括矿石预处理、还原条件控制、温度控制和产物分离等。
矿石预处理是为了提高矿石中有价值元素的回收率和产物质量。
常见的矿石预处理方法包括碎石、磁选和浸出等。
还原条件控制对于熔分工艺的成功与否至关重要。
合理的还原条件能够保证有价值元素的还原率和产物质量。
常用的还原条件包括还原剂种类和用量,还原温度和还原时间等。
温度控制是电炉熔分工艺中一个关键的环节。
适当的温度能够保证矿石充分熔化和元素的分离,同时避免产生不良的副反应。
温度控制的方法包括调整电炉电极的位置和电流强度等。
产物分离是电炉熔分工艺中的一项重要工作。
通过合理的分离装置,将钒铁合金和钛铁合金等产品分离出来,以提高产品质量和价值。
三、电炉熔分工艺的优势和发展前景电炉熔分工艺作为一种兼具深度和广度的处理钒钛磁铁矿的方法,具有以下优势和发展前景。
电炉熔分工艺对于复杂矿石的处理能力强。
由于钒钛磁铁矿的化学成分和矿物结构多样复杂,传统的处理方法存在着诸多限制。
而电炉熔分工艺通过熔融和分离的方式,能够有效地处理各种类型的矿石,实现有价值元素的高效提取。
《2024年气基直接还原竖炉炉型研究》范文
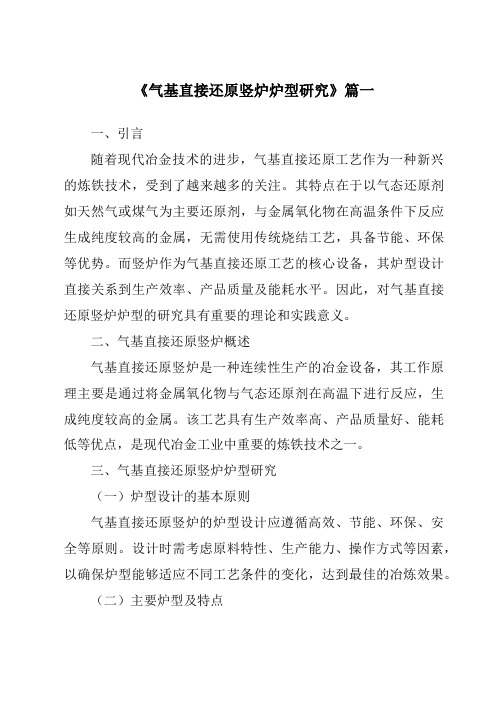
《气基直接还原竖炉炉型研究》篇一一、引言随着现代冶金技术的进步,气基直接还原工艺作为一种新兴的炼铁技术,受到了越来越多的关注。
其特点在于以气态还原剂如天然气或煤气为主要还原剂,与金属氧化物在高温条件下反应生成纯度较高的金属,无需使用传统烧结工艺,具备节能、环保等优势。
而竖炉作为气基直接还原工艺的核心设备,其炉型设计直接关系到生产效率、产品质量及能耗水平。
因此,对气基直接还原竖炉炉型的研究具有重要的理论和实践意义。
二、气基直接还原竖炉概述气基直接还原竖炉是一种连续性生产的冶金设备,其工作原理主要是通过将金属氧化物与气态还原剂在高温下进行反应,生成纯度较高的金属。
该工艺具有生产效率高、产品质量好、能耗低等优点,是现代冶金工业中重要的炼铁技术之一。
三、气基直接还原竖炉炉型研究(一)炉型设计的基本原则气基直接还原竖炉的炉型设计应遵循高效、节能、环保、安全等原则。
设计时需考虑原料特性、生产能力、操作方式等因素,以确保炉型能够适应不同工艺条件的变化,达到最佳的冶炼效果。
(二)主要炉型及特点目前,国内外气基直接还原竖炉的炉型主要分为固定床炉型、半连续式炉型和连续式炉型。
其中,固定床炉型结构简单,操作方便,但生产效率较低;半连续式炉型则通过优化炉体结构,提高了生产效率;连续式炉型则实现了连续性生产,具有更高的生产效率和产品质量。
各类型炉型均具有其独特的优点和适用范围,可根据实际生产需求进行选择。
(三)新型炉型研究针对传统炉型的不足,近年来学者们提出了一些新型的炉型设计。
如通过优化炉体结构、调整进料方式、改进排烟系统等措施,提高竖炉的热效率和还原效率。
同时,还研究了采用新型材料作为竖炉的保温材料和内衬材料,以提高竖炉的耐高温性能和耐腐蚀性能。
这些新型炉型的研究和应用,为气基直接还原竖炉的进一步发展提供了新的思路和方法。
四、研究方法与实验结果(一)研究方法本研究采用理论分析、数值模拟和实验研究相结合的方法。
首先通过查阅文献资料和实地考察,了解国内外气基直接还原竖炉的最新发展动态和趋势;然后运用数值模拟软件对不同炉型进行模拟分析,得出各炉型的优缺点及适用范围;最后通过实验研究验证模拟结果的准确性,并进一步优化炉型设计。
《气基直接还原竖炉流场研究及优化》范文

《气基直接还原竖炉流场研究及优化》篇一一、引言随着钢铁工业的快速发展,气基直接还原技术作为一种重要的炼铁技术,因其高效率、低能耗、环保等优点受到了广泛关注。
而竖炉作为气基直接还原技术中的核心设备,其流场性能直接影响着整个工艺的效率和产品质量。
因此,对气基直接还原竖炉流场的研究及优化具有重要意义。
本文将针对气基直接还原竖炉流场进行研究,分析其特点及存在的问题,并提出相应的优化措施。
二、气基直接还原竖炉流场概述气基直接还原竖炉流场主要由气体和固体颗粒组成。
在炼铁过程中,还原气体(如天然气、煤气等)与氧化铁矿石在高温条件下发生还原反应,生成铁水和其他物质。
同时,固体颗粒(如焦炭、石灰石等)在流场中起到传递热量和参与反应的作用。
气基直接还原竖炉流场的复杂性主要表现在气体和固体颗粒的相互作用以及反应过程中产生的各种物理化学变化。
三、气基直接还原竖炉流场研究1. 流场特性分析通过对气基直接还原竖炉流场的实际观察和数值模拟,可以发现在竖炉内部存在明显的气流分布不均现象。
由于气流在炉内的流动受到多种因素的影响,如炉内结构、气体性质、操作条件等,导致气流速度和方向在炉内发生较大变化。
此外,固体颗粒在流场中的运动也对流场特性产生影响。
2. 存在问题及原因分析在气基直接还原竖炉流场中存在的主要问题包括气流分布不均、温度波动大、能耗高等。
这些问题主要源于以下几个方面:一是炉内结构不合理,导致气流无法均匀分布;二是气体性质和组成影响气流的流动;三是操作条件不当,如风量、风压等参数设置不合理。
四、气基直接还原竖炉流场优化措施1. 优化炉内结构针对气流分布不均的问题,可以通过优化炉内结构来实现。
例如,改进风口设计,使气体更加均匀地进入炉内;优化炉体高度和直径比例,以改善气流在炉内的流动状况;在炉内增设导流板等装置,以引导气流流向。
2. 调整气体性质和组成通过调整气体性质和组成,可以改善气流的流动性能。
例如,调整还原气体的组成比例,使其更加适应反应的需要;对气体进行预处理,如除尘、脱硫等,以降低气体对炉内流场的影响。
《气基直接还原竖炉流场研究及优化》范文

《气基直接还原竖炉流场研究及优化》篇一一、引言气基直接还原法作为一种新兴的冶金工艺,已成为当今工业生产中的热门领域。
在此背景下,对于竖炉内流场的研究变得至关重要。
本论文将重点研究气基直接还原竖炉的流场特性,并通过优化手段提高其工作效率和产品质量。
二、竖炉流场研究背景及意义气基直接还原竖炉是冶金工业中重要的设备之一,其工作原理主要是通过高温和还原气氛将铁矿石进行还原反应,从而得到铁产品。
流场特性对竖炉的还原效率、产品质量以及能耗等方面具有重要影响。
因此,对竖炉流场的研究具有重要的理论意义和实际应用价值。
三、竖炉流场特性研究3.1 实验方法与设备本部分采用数值模拟和实验相结合的方法,对气基直接还原竖炉的流场特性进行研究。
通过搭建物理模型,结合数值模拟软件进行仿真分析。
3.2 流场特性分析通过仿真分析和实验数据,我们可以发现竖炉内部流场存在多种流动现象,如气体的快速流动、回流以及漩涡等。
这些现象都会对还原过程产生一定影响,如造成物料的不均匀还原、能耗增加等问题。
四、流场优化策略4.1 优化目标与原则针对竖炉流场存在的问题,我们提出以下优化目标:提高还原效率、降低能耗、保证产品质量。
在优化过程中,应遵循科学、合理、可操作的原则,确保优化措施的有效性。
4.2 具体优化措施(1)改进原料配比:根据竖炉的实际情况,调整原料的配比,使物料在炉内分布更加均匀,提高还原效率。
(2)优化风速控制:通过调整风速和风量,使气体在炉内分布更加均匀,减少涡流和回流现象,降低能耗。
(3)强化热工制度:通过调整炉温、加热速度等参数,使炉内温度分布更加均匀,提高还原反应的速率和效率。
(4)引入智能控制系统:通过引入智能控制系统,实时监测炉内温度、压力等参数,自动调整风速、风量等操作参数,实现自动化控制,提高工作效率和产品质量。
五、优化效果评估与展望5.1 优化效果评估经过一系列的优化措施后,我们对竖炉的流场特性进行了再次分析和评估。
《气基直接还原竖炉炉型研究》范文

《气基直接还原竖炉炉型研究》篇一一、引言随着钢铁工业的不断发展,对高效率、低能耗、环保型炼铁技术的需求日益增强。
气基直接还原法作为一种新型炼铁技术,以其高效率、低能耗和环保等优点,逐渐成为国内外研究的热点。
气基直接还原竖炉作为该技术的重要设备,其炉型的研究和优化对提高生产效率和产品质量具有重要意义。
本文将针对气基直接还原竖炉的炉型进行研究,为工业应用提供理论支持。
二、气基直接还原竖炉的工作原理及特点气基直接还原竖炉是一种以气体为还原剂,将铁矿石直接还原成海绵铁的设备。
其工作原理主要是通过高温和还原气氛,使铁矿石中的铁氧化物与气体中的氢气或一氧化碳等还原剂发生化学反应,生成海绵铁。
气基直接还原竖炉具有以下特点:1. 高温操作:炉内温度可达到1300-1500℃,有利于铁氧化物的还原反应。
2. 气体还原:以气体为还原剂,反应速度快,还原效率高。
3. 环保:无烟尘排放,减少了对环境的污染。
4. 灵活性:可以处理多种类型的铁矿石,适应性强。
三、气基直接还原竖炉的炉型研究炉型是气基直接还原竖炉的重要参数之一,合理的炉型设计对提高生产效率和产品质量具有重要意义。
目前,国内外对气基直接还原竖炉的炉型进行了大量研究,主要涉及以下几个方面:1. 炉体结构:包括炉身、炉腰、炉腹和炉底等部分的形状和尺寸。
合理的结构可以提高炉内温度分布的均匀性,降低能耗。
2. 风口布置:风口是气体进入炉内的通道,其布置方式对炉内气氛的均匀性和还原效率有很大影响。
研究不同风口布置方式对炉内气氛和还原效率的影响,为优化风口布置提供依据。
3. 排烟系统:排烟系统对炉内气氛的稳定性和能耗有很大影响。
研究不同排烟方式对炉内气氛和能耗的影响,为优化排烟系统提供依据。
4. 炉料分布:炉料在炉内的分布对反应速度和产品质量有很大影响。
研究不同炉料分布方式对反应速度和产品质量的影响,为优化炉料分布提供依据。
四、实验研究及结果分析为了研究气基直接还原竖炉的炉型,我们进行了大量的实验研究。
- 1、下载文档前请自行甄别文档内容的完整性,平台不提供额外的编辑、内容补充、找答案等附加服务。
- 2、"仅部分预览"的文档,不可在线预览部分如存在完整性等问题,可反馈申请退款(可完整预览的文档不适用该条件!)。
- 3、如文档侵犯您的权益,请联系客服反馈,我们会尽快为您处理(人工客服工作时间:9:00-18:30)。
攀枝花钒钛磁铁矿竖炉气基还原工艺的基础研究可行性研究报告1. 课题背景攀枝花钒钛磁铁矿是一种铁、钒、钛等多种有价元素共生的复合矿,传统的“高炉—转炉”流程仅回收了其中的铁,钒和钛资源没有有效回收利用,并且存在生产成本过高、环境污染严重等难以克服的问题。
近年来,随着优质含铁原料供应日趋紧张、环保要求日益严格,炼铁工艺由单一高炉流程逐步转变为高炉流程、熔融还原以及直接还原流程共同发展的局面,一些新的工艺如转底炉直接还原技术发展迅速。
2010年,攀枝花市明确提出了“打造中国钒钛之都,建设特色经济强市”的发展战略,力将攀枝花建设成为具有国际影响力的钒钛之都。
如何充分利用资源优势,采用清洁、环保、高效的工艺处理攀西钒钛磁铁矿显得尤为重要。
2. 钒钛矿直接还原工艺现状2.1 直接还原工艺发展现状近年来,世界直接还原工艺仍然保持较快的发展势头,直接还原铁产量总体呈增加趋势。
表1为2010年世界还原铁生产概况。
在几种主要工艺中,气基直接还原法仍占主导地位,其产量约占世界总产量的74.3%。
表1 世界直接还原生产概况工艺方法2010年产量Mt/Y占总产量%现有装置数运行装置数生产能力利用率%气基竖炉MIDREX 42.01 59.7 57 57 105.2HYL 9.90 14.1 22 14 95.5 其它0.34 0.5 / / 15.4 煤基18.12 25.7 / / ~70.0世界总计70.4 100.00直接还原工艺中,气基法以天然气为能源,由于还原气与原料接触条件、传热条件好,还原气循环利用,因而能耗远低于煤基法。
气基法尾气可循环利用,而煤基法中煤直接燃烧或制气后燃烧,尾气量大,烟气硫化物脱除困难,环境污染较严重。
隧道窑、回转窑、转底炉的单机生产能力不高,适合中小规模的生产,而气基竖炉可实现大型工业化生产。
2.2 典型气基竖炉直接还原工艺(1)Midrex工艺Midrex工艺以天然气为原料气生产还原气,其发展局限于天然气资源丰富的地区。
天然气经催化裂化制取还原气,裂化剂为炉顶煤气。
混合气预热后送入转化炉中的镍质催化反应管组,转化成含CO和H2共95%左右,温度为850~900℃的还原气。
炉料经炉顶料仓、下料管进入还原炉。
还原气从竖炉的中部周边喷口进入,参加反应后从炉顶排出,炉顶气经冷却和洗涤后( H2+CO)含量约为70%。
还原后的物料可用从底部气体分配器送入的冷却气冷却到100℃以下排出炉外,获得海绵铁产品。
(2)HYL工艺基于HYL-III法发展而来的天然气“零重整”的HYL-ZR,现已成为HYL/energiron工艺。
HYL工艺使用球团矿和天然块矿为原料,以水蒸汽为裂化剂,制取以H2和CO为主的合成气;合成气脱水后与经过脱水和脱CO2的竖炉炉顶煤气混合送入还原系统。
还原气从竖炉还原段底部进入炉内,铁矿石从竖炉炉顶加入。
还原气和铁矿石在逆向运动中发生化学反应,生成海绵铁。
海绵铁在冷却段中温度降低到50℃左右排出竖炉,产品直接还原铁的金属化率可达92%~95%。
2.3煤气化工艺应用现状煤制气技术已是化工生产中的成熟技术。
目前国外应用较多的煤制气技术有鲁奇碎煤加压气化技术、德士古水煤浆气化技术、循环流化床粉煤气化技术、循环流化床粉煤气化技术等。
鲁奇碎煤加压气化技术生产能力大、煤种适应性广。
但鲁奇气化炉生产煤制气时,气体成分中甲烷含量高(8%-10%),且含气生产流程长、投资大。
德士古气化工艺对煤种的适应性较宽,对煤的活性没有严格的限制;单炉生产能力大;碳转化率高,达96%-98%,排水中不含焦油、酚等污染物;煤气质量好,有效气(CO+H2)高达80%左右,甲烷含量低,但对煤的灰熔点有一定的要求(一般要低于1400℃)。
2.4 钒钛磁铁矿直接还原法处理现状目前冶炼钒钛磁铁矿主要有高炉和非高炉两种流程。
高炉流程资源利用率低,有用元素的回收率低(铁~54%、钒~47%、钛~15%,其它元素未实现有效回收)。
高炉大比例配入普通铁矿时,炉渣中TiO2含量仅有20%左右,从这种炉渣中回收钛的技术难度大且成本很高,因而大量钛资源丢失。
另外,该流程以焦炭为主要能源,攀西地区焦煤资源与钒钛磁铁矿资源的储量不匹配,焦煤成本压力日益增大。
在非高炉流程处理钒钛磁铁矿的工艺中,先提钒后提铁的“北方流程”由于原料处理量、三废产生量较大而未能得到大规模推广。
南方流程以直接还原-电炉熔分或还原为主要工艺环节,应用较多,其代表流程有南非流程、新西兰流程、攀钢流程等。
典型的南非流程使用TFe 53%~57%,TiO2 12%~15%,V2O5 1.4%~1.7%,SiO21.5%~2%的矿石,在回转窑预还原率50%~70%条件下,获得了含V2O5 25%,SiO2 16%,Cr2O3 5%的钒渣。
四川龙蟒集团以铁钒精矿为原料,以转底炉为还原反应器—电炉为深度还原及熔化分离实现工业化生产,取得了良好的效果,铁、钒、钛的回收率分别达到95%、85%、90%,并通过省级鉴定。
但是,上述流程都必须使用球团,由于造球加入粘结剂、还原剂,钛渣TiO2品位降低,增加了钛渣后续利用的难度。
鉴于隧道窑产能过低,流化床技术发展尚未有明显突破,竖炉工艺成为攀西地区直接还原处理钒钛磁铁矿的突破点。
3. 研究条件和前期成果3.1 前期研究及现有研究条件本研究团队自上世纪60年代以来,一直参与攀枝花钒钛磁铁矿的科研攻关,并取得了多项重大成绩;所在单位是中国金属学会炼铁分会非高炉委员会的主任单位。
多年来,在非高炉炼铁理论和方面积累了丰富的研究经验。
代表成果有:1.攀枝花高炉冶炼钒钛磁铁矿科研试验,获1979年国家发明一等奖(集体)。
2.钒钛磁铁矿高炉冶炼新技术,获1999年国家科技进步一等奖。
申请者所在院校经过数十年的工作积累以及国家“211工程”及“985工程”的重点建设,已建成配套的冶金科研装备体系和先进的冶金综合检测体系。
与本研究有关的设备或仪器有:各种型号和尺寸的自动化电加热炉,真空感应炉,离心分离器,真空干燥器,数字光学显微镜,EPMA,差热-热重分析仪、高温X 射线分析仪,S710 气体分析仪。
本单位测试中心可以提供相关ICP、SEM等分析手段和其它辅助试验研究设备。
3.2 近年相关科研成果相关科研项目:1. 印尼钒钛磁铁矿混合配矿造块的试验研究,2010.07-09,企业联合项目;2. 沙钢高炉冶炼钒钛磁铁矿的可行性研究,2010.08-10,企业联合项目;发表的论文:1. 直接还原铁在我国钢铁工业中的作用及前景展望,攀枝花科技与信息,2010/042. 电炉炼钢原料及直接还原铁生产技术,中国冶金,2010/043. 中国发展非高炉炼铁的现状及展望,中国冶金2008/094. 铁矿石含碳球团中碳的气化反应速度对球团熔融的影响,钢铁研究学报2007/125. 钒钛磁铁矿直接还原的工艺选择浅析,2010年非高炉炼铁学术年会暨钒钛磁铁矿综合利用技术研讨会,2010,265-2706. 印尼黑珍珠钒钛磁铁矿配矿造球的试验研究,2010年非高炉炼铁学术年会暨钒钛磁铁矿综合利用技术研讨会,2010,353-3574. 新工艺的提出与高炉流程类似,多数直接还原法处理钒钛磁铁矿亦可以产出含钛炉渣、含钒铁水,在一定程度上实现铁、钒、钛资源的利用。
但是,由于工艺本身的限制,直接还原法也存在一些问题。
若将气基竖炉用于处理钒钛磁铁矿,具有能耗低、碳排放低、对环境的负面影响小,生产规模可以大型化等优势,且对后期处理钛的影响最小。
另外,煤制气技术的成熟,也为竖炉发展提供了有利条件。
在以往对钒钛磁铁矿研究中,很多科研工作者认为发现,钒钛磁铁矿球团在低温下粉化严重,中温还原时会出现灾难性膨胀,并将影响高炉炉况的正常运行。
但本研究团队研究发现,钒钛磁铁矿球团在还原过程中会发生还原粉化、膨胀的现象,但粉化、膨胀的程度与还原气组成和温度有较密切的关系;而在碱金属存在条件下,会出现球团的“灾难性膨胀”。
可见,对于竖炉而言,若采取有效措施,可以避免出现上述问题。
综上,本研究团队综合自身的技术优势,提出了气基还原法处理攀枝花钒钛磁铁矿的工艺流程路线。
流程路线如图1所示。
图1 气基还原法处理钒攀枝花钛磁铁矿新工艺的流程示意图本研究提出的新工艺符合促进社会经济增长方式转变、产业结构调整的国家重大战略需求和国际学科发展综合化的趋势,有利于促进我国钒钛磁铁矿资源利用科研和产业整体水平的提升、推动行业技术进步、变资源优势为技术和经济优势,具有重要的学术价值和广阔的应用前景。
气基竖炉直接还原新工艺能够摆脱焦煤资源依赖,减少能源消耗,为攀枝花钒钛磁铁矿资源的高效清洁化综合利用提供了新方法。
通过本课题的研究,为气基竖炉工艺处理攀枝花钒钛磁铁矿选择煤制气工艺、制定直接还原工艺参数提供理论依据,明确工艺参数直接还原产品质量的影响规律,为气基竖炉直接还原攀枝花钒钛磁铁矿-电炉熔分-富钒钛渣提取钒钛工艺的开发利用打下良好基础。
5. 新工艺研究目标和内容5.1 研究目标近年来,相关配套技术的发展为气基还原法处理攀枝花钒钛磁铁矿新工艺的实施提供了可行性。
但新工艺距离实施仍然有许多问题需要解明。
根据前期研究结果,可将该工艺概括为三部分内容:(1)煤制气工艺及技术选择;(2)钒钛磁铁矿球团竖炉还原工艺制度的确定;(3)富钒、富钛渣中提取钒钛的工艺及技术研究。
鉴于煤制气工艺和富钒、富钛渣提取钒钛工艺比较成熟,本课题的研究将重点围绕钒钛磁铁矿球团的气基还原工艺展开。
通过实验室研究,掌握攀枝花钒钛磁铁矿氧化球团还原过程的基本规律,为攀枝花钒钛磁铁矿气基竖炉直接还原工艺的开发提供依据和基础参数。
5.2 研究内容本研究将以攀枝花钒钛磁铁矿为原料,开展球团制备、气基直接还原规律的研究。
主要内容包括:(1) 攀枝花钒钛磁铁矿制备竖炉直接还原用生球的试验研究。
参照国际直接还原球团标准,对攀西钒钛磁铁精矿进行粒度和化学成分分析,配加适量膨润土造球得到钒钛磁铁生球,检测生球的落下强度和抗压强度,并考察造球工艺参数如膨润土加入量、水分等对球团物理性能的影响;(2) 攀枝花钒钛磁铁矿制备竖炉直接还原用球团的焙烧试验研究。
在氧化性气氛下对干燥后生球进行高温焙烧,得到钒钛磁铁矿氧化球团,考察不同的焙烧温度和焙烧时间对氧化性球团各项性能的影响,研究其焙烧固结机理从而得到最佳焙烧条件;(3) 攀枝花钒钛磁铁矿球团的还原试验研究。
在实验室条件下模拟气基竖炉对钒钛磁铁氧化球团进行直接还原,考察不同还原气氛(CO/H2比)和温度条件下钒钛磁铁矿氧化球团的还原行为及还原后球团的物理性质和还原膨胀率。
从而为攀枝花钒钛磁铁矿氧化球团气基竖炉直接还原工艺提供相关参数;5.3 技术关键(1) 通过实验室造球试验,确定适合攀枝花钒钛磁铁矿的成球工艺参数:膨润土加入量、水分、成球时间等,得到满足要求的生球;(2) 通过实验室高温焙烧试验,确定适合攀枝花钒钛磁铁矿的焙烧工艺条件:适宜预热和干燥温度、时间,适宜焙烧温度和焙烧时间,得到最佳焙烧条件;(3) 在实验室条件下模拟气基竖炉对攀枝花钒钛磁铁氧化球团进行直接还原,比较不同还原气氛和温度条件下钒钛磁铁矿氧化球团的还原行为,还原后球团的物理性质和还原膨胀率,得到球团不粉化且还原良好的条件,为确定攀枝花钒钛磁铁矿氧化球团气基竖炉直接还原的工艺参数和流程提供理论指导。