油井腐蚀及防护技术
油井的腐蚀原因与防护措施研究

油井的腐蚀原因与防护措施研究摘要:随着油田的持续开发,油井综合含水逐年上升,目前采油厂处于高含水开发生产阶段,综合含水达到94.3%。
由于后期含水上升,同时受高矿化度、管杆材质等综合因素影响,油井腐蚀现象日趋严重。
油井腐蚀是指井下金属设备与产出液直接接触形成腐蚀电池而产生的腐蚀现象,能够造成管漏、杆断、泵漏而躺井。
随着油管配套的完善,井筒腐蚀问题逐步向抽油杆与抽油泵上转移,其中腐蚀杆断的井数和比例都逐年升高。
油井腐蚀现象是多因素交互作用下的结果,因此,对其形成的原因、腐蚀的程度及防腐的措施进行全方位的把控相当困难。
因此加强油井的腐蚀原因与防护措施研究至关重要。
关键词:油井;腐蚀;机理分析;防腐措施1油井腐蚀研究现状腐蚀是材料与环境反应引起的材料破坏与变质,它存在于各行各业,引起经济损失也是引人注目的。
腐蚀是造成石油工业中金属设备的主要原因之一,它加剧了设备及管道的损坏和人员伤亡,造成了石油生产中停工、停产和跑、冒、滴、漏等事故;并且污染环境,损害人民健康;导致产品流失,增加了石油产品的成本,有的已影响正常的石油生产。
我国很早便开始着手对油气田井下油管的腐蚀展开研究,主要包括腐蚀的环境、影响因素及防腐措施等几个方面。
王明辉等人通过室内实验,针对某油井中的套管在H2S与CO2共存条件下的腐蚀情况开展了研究,精确评估了管材的使用寿命。
贺海军等人结合灰色关联法,对油井套管开展了防腐模拟评价室内实验,通过定量分析管材的安全服役寿命对其进行了优选。
赵健等人提出了深层油井管材阴极保护计算公式,通过计算和推导得出,在一定的误差范围内,这种计算方法能够为深层油井管材保护提供可靠的数据,具有一定的实用性和可靠性。
当前,我国对不同储层物性油田的腐蚀问题进行了大量的研究,在防腐技术方面已相当成熟,当然,这只是油井防腐万里长征的第一步,要想真正意义上把油井防腐工作搞扎实,必须对其腐蚀的影响因素、腐蚀环境、形成原因及腐蚀监控等相关工艺技术进行更深人的分析和研究。
高深度油井、气井腐蚀环境与对策及高耐蚀井用管的开发

在油、气开发环境下,源自产物中所含的CO2、H2S的碳酸气腐蚀、硫化物应力腐蚀裂纹(SSC)及在与井上填充液接触部分所产生的应力腐蚀裂纹(SCC)都是大问题。
为了提高材料的耐碳酸气腐蚀性,向钢中加Cr是有效的;而为了提高耐SSC性,则加Mo是有效的。
作为适应上述恶劣环境的材料,JFE所开发的UHP13Cr钢管因低C、加入了Ni、Mo而改善了耐碳酸气腐蚀性及耐SSC性;所开发的UHP15Cr钢管因高Cr化而进一步提高了耐蚀性能。
这两类开发钢管在原API-13Cr钢管不能使用的100~200℃高温CO2及少量H2S环境下耐蚀性优良。
1、前言近年对石油、天然气的需求连年增加,随之进行了原未进行过的高深度恶劣环境下的油、气开发。
因其多含CO2或H2S等腐蚀性气体,有时会产生腐蚀及腐蚀裂纹等问题。
在润湿CO2环境下,存在全面或选择性腐蚀等问题;而在H2S环境下,有时会发生氢致裂纹。
因这些腐蚀问题可能引发重大事故,故对井用管的耐蚀性要求越来越严。
在润湿CO2环境下,一般使用高耐蚀性高Cr钢,其中所占比例高的是13Cr马氏体不锈钢。
由于此类钢耐碳酸气腐蚀性优良,故其需求量也在连年增长。
然而,若油井温度高于100℃,13Cr钢管的耐蚀性就会劣化,由于CO2分压而造成其使用寿命的下降。
随着近年对深井的开发,高温、高CO2分压、高氯离子浓度的腐蚀性严重的深油、气井增多,超过13Cr钢管使用范围的环境也一直在增多。
并且,即使油井开始仅为CO2环境,因注水法的使用而产生H2S或开始就会有H2S的油井也增多了,由H2S引起的硫化物应力裂纹(SSC)就成了问题。
普通的13Cr钢管没有充分的耐SSC性。
在如此恶劣环境中使用的油井管,原来使用22Cr系双相钢管或耐蚀性更高的高合金钢管,但要求耐蚀性比22Cr系更高的场合也多。
另外,由于冷拔油井管须有必要的强度,故成本也高。
因此,进行了具有比普通13Cr 钢管耐蚀性高且成本比双相不锈钢低的新油井管开发。
油气田气田腐蚀与防腐技术
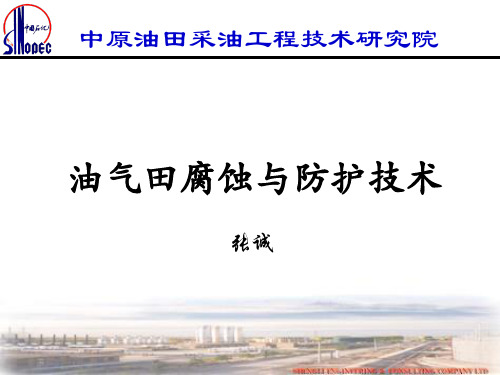
中原油田采油院
二、油气田腐蚀腐蚀机理、现象及分类
(5)氧腐蚀 • 在注入水或者注入的其他工作液中,不可避免的要混 入氧。发生吸氧腐蚀。
2Fe+2H2O+O2=2Fe(OH)2
4Fe(OH)2+O2+2H2O=4Fe(OH)3 Fe(OH)3 Fe2O3· xH2O
钢铁的吸氧腐蚀示意图 中原油田采油院
中原油田采油院
二、油气田腐蚀腐蚀机理、现象及分类 (7)腐蚀性组分相互作用及对腐蚀的影响
(a)硫化氢和二氧化碳共存对腐蚀的影响 • H2S和CO2共同存在下具有协同作用,CO2的存 在可以降低pH值,提高硫化物应力腐蚀的敏感性; H2S可以破坏CO2腐蚀产生的保护膜,使得腐蚀速 度持续增加,并作为毒化剂,加速CO2腐蚀过程中 产生的氢原子进入钢材基体。 同时具有H2S和CO2腐蚀的特点,也包括一些 共同作用下的特点。但最重要的还是需要防止H2S 引起的脆性开裂。
中原油田采油院
一、腐蚀简介 氢与腐蚀:
金属基体 氢进入
表面能降低
原子键合力降低 晶格膨胀
更易断裂 更易腐蚀
浅谈油田管道腐蚀及防腐应对措施

浅谈油田管道腐蚀及防腐应对措施随着石油工业的迅速发展,埋设在地下的油、气、水管道等日益增多。
地埋管道会因为土壤腐蚀形成管线设备穿孔,从而造成油、气、水的跑、冒、滴、露。
这不仅造成直接经济损失,而且可能引起爆炸、起火、环境污染等,产生巨大的经济损失。
本文对管道腐蚀危害做了简要说明,并结合日常生产中管道腐蚀的情况,对其腐蚀机理做了进一步的阐述。
结合腐蚀机理提出防腐应对措施,并进一步介绍了新型防腐技术,为今后油田管道设备防腐工作提供了一定的工作方向。
标签:腐蚀;腐蚀危害;腐蚀机理;防腐措施一、石油管道腐蚀的危害我们把石油生产过程中原油采出液、伴生气等介质在集输过程中对油井油套管、油站内、回注管网等金属管线、设备、容器等形成的内腐蚀以及由于环境,例如土壤、空气、水分等造成的外腐蚀统称为油气集输系统腐蚀。
油气集输系统腐蚀中的内腐蚀一般占据腐蚀伤害的主要地位。
针对腐蚀研究,在整个生产系统中,不同的位置及生产环节其所发生的的腐蚀也有所不同,并且腐蚀特征及腐蚀影响因素也有所不同。
因此防腐工作是油田生产中的重要措施。
据不完全统计截止目前,我国输油管道在近20年的时间里,共发生大小事故628起,其中包括线上辅助设备故障190 起,其它自然灾害70 起,有368 起属管体本身的事故。
根据近年的调查发现:影响管线寿命和安全性的因素中,腐蚀占36.4%,机械和焊缝损伤占14.4%,操作失误占35.0%,第三方破坏占14.2%.因此,腐蝕是事故的主要原因。
[1]二、管道腐蚀的机理理论(1)土壤腐蚀土壤腐蚀是电化学腐蚀的一种,土壤的组成比较复杂,其多为复杂混合物组成。
并且土壤颗粒中充满了空气、水及各类盐从而使土壤具有电解质的特征,根据土壤腐蚀机理,我们将土壤腐蚀电池大致分为两类:第一种为微电池腐蚀,也就是我们常说的均匀腐蚀。
均匀腐蚀是因为微阳极与微阴极十分接近,这样的距离在腐蚀过程中不依赖土壤的电阻率,只是由微阳极与微阴极决定电极过程。
国内外油气管道腐蚀及防护技术研究现状及进展_胡鹏飞

0 前言
随着石油天然气开采量的日益扩大 , 油气管道的腐蚀及防护也越来越受到重视。 CO2 作为石油、 天然 气或地层水的组分存在于油气层中, 采用 CO2 混相技术提高原油采收率时, 也会将 CO2 带入原油生产系 统。CO2 溶于水后, 在相同 PH 值时其总酸度比盐酸高, 故对井内管材的腐蚀比盐酸更严重
[ 10]
。
文献 [ 18] 报道了管道外防腐绝缘层与阴极保护的联合使用是最经济、 最合理的防腐措施 , 还报道了燕 山石化公司对埋地管道采用防腐涂层结合牺牲阳极的阴极保护法, 对管道的防腐起到了良好的效果。 3. 7 镀铝钢在管道防腐技术上的应用 早在 1893 年 , 德国人就发明了钢材热浸镀铝技术, 随后法国、 美国也公布了热浸镀铝的技术专利 , 20 世纪 50 年代到 60 年代 , 国外钢带热浸镀技术处于迅速发展时期 几个镀铝生产厂家
第 24 卷 第 2 期 2003 年 6月
河 南 科 技 大 学 学 报 ( 自 然 科 学 版 ) Journal of Henan University of Science and T echnology ( Natural Science)
Vol. 24 No. 2 June 2003
文章编号: 1000- 5080( 2003) 02- 0100- 04
3 常用的腐蚀防护技术
3. 1 采用缓蚀剂 采用缓蚀剂防腐主要是利用缓蚀剂的防腐作用来达到减缓油管腐蚀的目的。其防腐效果主要与井 [ 12] 况、 缓蚀剂类型、 注入周期、 注入量等有关。该技术成本低, 初期投资少 , 但工艺复杂, 对生产影响较大 。 此外 , 不同井况要求缓蚀剂的类型也不尽相同 , 通常情况下 , 中性介质中多使用无机缓蚀剂, 以钝化型和沉 淀型为主 ; 酸性介质使用的缓蚀剂大多为有机物, 以吸附型为主。但现在的复配缓蚀剂根据需要在用于中 性介质的缓蚀剂中也使用有机物, 而在用于酸性水介质的缓蚀剂中也添加无机盐类。不同金属的原子外 层电子排布、 电位序列、 化学性质等有所不同 , 它们在不同介质中的吸附和成膜特性也不相同
腐蚀监测技术在油井生产中的运用与完善

腐蚀监测技术在油井生产中的运用与完善腐蚀监测技术是指利用各种手段对油井生产过程中的管道、设备等金属部件进行实时或定期检测,及早发现腐蚀问题,采取相应的措施,确保油井生产的安全性和经济性。
在油井生产中,腐蚀问题是一个经常发生的问题,对设施和生产造成了很大的影响,因此腐蚀监测技术在油井生产中的运用和完善是非常关键的。
1. 电化学腐蚀监测技术电化学腐蚀监测技术是指利用电化学方法监测金属材料在特定环境下的腐蚀率和腐蚀行为的技术。
采用电化学监测技术可以实时或定期监测金属材料的腐蚀程度,判断设备的腐蚀状况,便于采取相应的措施进行腐蚀防护或修复。
尤其在油气输送、储存等设备中,电化学腐蚀监测技术可以有效地预防腐蚀事故的发生,提高设施的使用寿命和安全性。
腐蚀超声监测技术是利用超声波技术对金属材料进行非接触式的在线监测,检测材料表面腐蚀状况。
超声波腐蚀监测技术可以快速、准确地检测管道、设备预制装配时的腐蚀情况,检测到的腐蚀信号可以进行实时显示,同时对信号进行处理和分析,准确判定材料的腐蚀状况。
超声波腐蚀监测技术可以实现非破坏性的在线监测,确保设备的完整性和安全性。
腐蚀电泳监测技术是指利用基于涂覆技术的悬浮涂料进行定期腐蚀监测。
该技术的优势在于它可以对微小缺陷或不可见的腐蚀进行检测,可广泛应用于油井设备及其它环境腐蚀环境监测领域。
腐蚀电泳监测技术的方案是将一种悬浮型涂料涂于试片(样品、设备等)表面,在涂层内加入具有电导性的粉末,在涂层表面产生电场和离子运动,对涂层和试片进行定期测量,以获取试片表面的腐蚀情况并判定其腐蚀状态。
总体而言,腐蚀监测技术在油井生产中的运用已经越来越广泛,而且技术进步也越来越快速。
尤其是在新型材料的不断研发和运用方面,腐蚀监测技术也随之不断地进行完善和更新。
腐蚀监测技术的应用,不仅可以及早发现腐蚀问题,减少设施故障的风险,提高油井生产的效率和准确性,而且还可以节约维护费用,推动整个油井领域的可持续发展。
试论钻井工程对油井套管腐蚀损坏原因及预防措施

钻井液的pH值
钻井液的pH值是影响套管腐蚀 的重要因素之一。一般情况下, 酸性钻井液比碱性钻井液更容易
导致套管腐蚀。
钻井液中的微生物
某些微生物在钻井液中繁殖,可 能对套管造成腐蚀损害。
钻井过程中的物理化学因素对套管腐蚀的影响
压力与温度
钻井过程中,地层压力和钻井液的压力变化可能导致套管 内外产生压力差,从而加速套管腐蚀。同时,温度也是影 响套管腐蚀的重要因素之一。
套管材质
不同材质的套管对腐蚀的抵抗 力不同。
井液成分
井液中的酸、碱、盐等成分对 套管腐蚀有重要影响。
流速和冲刷
流速快、冲刷力强的区域更容 易导致套管腐蚀。
防腐措施
采取有效的防腐措施可以降低 套管的腐蚀速度。
01
钻井工程对油井套管腐蚀 损坏的影响
钻井液对套管腐蚀的影响
钻井液的化学性质
钻井液中通常含有多种化学成分 ,如无机盐、有机溶剂等,这些 成分可能对套管产生腐蚀作用。
工程实例三:采用缓蚀剂防护的套管防护
缓蚀剂防护是一种绿色、高效的防护方法。
缓蚀剂防护通过向油井中注入缓蚀剂,减缓或阻止套 管的腐蚀。该方法具有成本低、操作简便、环保等优 点。在实际应用中,需要根据油气田的实际情况选择 合适的缓蚀剂。
01
结论与展望
研究结论
套管材质的影响
不同材质的套管对腐蚀的敏感性不同。
摩擦与磨损
钻井过程中,钻头与套管壁之间的摩擦和磨损可能导致套 管表面损伤和腐蚀。
电化学腐蚀
在某些情况下,钻井液中的电解质可能引起电化学腐蚀, 导致套管损坏。
钻井过程中的微生物对套管腐蚀的影响
硫酸盐还原菌
这类微生物在缺氧条件下能将钻井液中的硫酸盐还原为硫化 氢,从而加速套管的腐蚀。
油水井腐蚀原因分析及防护

油水井腐蚀原因分析及防护随着我国经济的发展,对石油的需求量也越来越大,使得我国的石油行业面临越来越大的压力和挑战。
石油公司不断研发石油开采技术,增加石油的开采量。
目前,我国的石油开采技术在国际上已经属于领先的地步,但是,开采技术仍然存在不足之处,需要进行改进。
本文主要介绍了石油开采中油水井腐蚀的原因以及一些防护措施。
标签:石油开采;油水井;腐蚀原因;防护措施前言油水井即是依靠油机和井下有杆泵将油从地表才到地面的油井。
油水井在使用过程中会逐渐地堆积水垢,又由于油井的工作环境复杂恶劣。
油井中的水垢会越积越多,最后形成腐蚀,腐蚀后会在井管上留下垢物。
当油井遭到腐蚀后,会影响油井的使用效果,降低开采效率,以及油田的经济效益。
所以针对油水井的腐蚀,应该采取合理有效的防护措施,使油水井免遭腐蚀侵蚀,从而可以延长油水井的使用寿命,提高油水井的开采效率,增加经济效益。
要想找到合适的防护措施,首先必须找到油水井腐蚀的原因,从而根据油水井腐蚀的原因找到相应的防护措施,才能使油水井免受腐蚀。
1、油水井的腐蚀现象通过对油水井腐蚀现象进行研究可以得出油水井腐蚀的原因。
目前,从我国已经腐蚀的油水井井下的腐蚀现象中发现油水井腐蚀的现象最为严重。
油水井的腐蚀情况主要有以下几种,油管抽油杆遭到腐蚀,严重者还会断裂,使石油开采工作难以进行。
套管上腐蚀物卡泵,影响油水井的使用效果,还有一种就是套管穿孔。
据相关考察资料发现油水井的井管随着井下的深度增加腐蚀程度也在逐渐增加。
当深度超过3000米,油井井管的内壁上几乎都是垢物,几乎快完全堵塞了井管。
井管中的腐蚀物主要是铁的氧化物。
垢物在井管上给油田的开采带来了困难,不但降低了油田开采的效率,还会浪費能量,增加成本。
而且还会损失油水井自身,更换油水井的井管不仅浪费时间依然会增加成本。
2、油水井的腐蚀原因油水井的腐蚀原因从腐蚀的现象中可以看出,也可以从腐蚀物的化学成分中分析出来。
油水井的腐蚀原因主要有以下几个方面。
- 1、下载文档前请自行甄别文档内容的完整性,平台不提供额外的编辑、内容补充、找答案等附加服务。
- 2、"仅部分预览"的文档,不可在线预览部分如存在完整性等问题,可反馈申请退款(可完整预览的文档不适用该条件!)。
- 3、如文档侵犯您的权益,请联系客服反馈,我们会尽快为您处理(人工客服工作时间:9:00-18:30)。
油井的腐蚀及防护技术
[摘要]:目前文南油田综合含水已高达80.3%,油井在严重腐蚀的环境条件下生产,井下工具、油管、抽油杆、套管等都存在不同程度的腐蚀,影响油田的正常生产。
通加研究并推广应用固体防腐剂技术、阴极保护器与井口加药技术等多种防腐蚀技术,在一定程度上减轻了管、杆的腐蚀现象。
从应用效果来看,油井加缓蚀剂技术是目前应用比较成熟的防腐蚀技术。
[关键词]:腐蚀缓蚀剂
中图分类号:o346.2+1 文献标识码:o 文章编号:1009-914x (2012)20- 0050 -01
随着油田的不断开发和利用,综合含水率不断上升,目前文南油田综合含水已高达80.3%,产出液大多为游离水,且矿化度为6~16×104mg/l不等,油井在严重腐蚀的环境条件下生产,井下工具、油管、抽油杆、套管等都存在不同程度的腐蚀,有的腐蚀还相当严重,直接影响油田的正常生产。
油井腐蚀已是制约油田生产开发的一个重要因素。
因此,如何依靠新工艺新技术遏制腐蚀,最大限度的减少和避免因腐蚀造成的各项经济损失,是油田防腐蚀工作面临的重要课题。
1.文南油田油井的腐蚀现状
文南油田产出液呈弱酸性,ph值为6,成酸性腐蚀,2010年1月~2011年5月,文南油田抽油井开井435口,通过对躺井的腐蚀情况的调查统计,存在腐蚀现象的躺井多达96口,因腐蚀造成躺
井25井次,腐蚀躺井共影响产量180余吨,管杆损坏更换费用90余万元,合计经济损失140余万元。
因此,治理油井的腐蚀是文南油田迫切需要解决的问题。
(1)抽油杆的腐蚀:
由于介质的腐蚀性和冲刷作用,抽油杆及接箍出现不同程度的腐蚀现象。
抽油杆接箍偏磨腐蚀严重,抽油杆腐蚀后呈现麻斑,严重的有深坑。
抽油杆偏磨破坏其表面的保护层,而抽油杆表面腐蚀后材质变得疏松,又使得磨损更容易,腐蚀与偏磨相互促进,使得腐蚀加剧。
在含水高且成酸性腐蚀的油井中,由于腐蚀疲劳、氢脆、应力腐蚀等原因,经常出现抽油杆断裂。
(2)井下工具的腐蚀:
油井井下工具是在油井出现游离水后腐蚀才严重的。
由于活塞、阀等处于运动状态,因此损坏程度更大。
抽油泵腐蚀主要发生在凡尔球和球座,占95%以上,其中又以固定凡尔球和球座最严重,被腐蚀的球座表面有麻点。
这是因为球座始终处于受磨损状态,而凡尔球受流体的冲击,易形成涡流导致腐蚀。
(3)油管的腐蚀:
油管的腐蚀大致上可分为均匀腐蚀和局部腐蚀,其中影响最严重的是局部腐蚀造成的腐蚀穿孔。
油管腐蚀大部分呈圆形或椭圆形,外小内大,呈八字形,油管的腐蚀是从管内开始的。
一旦油管外壁发现腐蚀现象,那么对应内壁会有更大面积的腐蚀。
油管内壁既有腐蚀又有结垢,甚至发生垢下腐蚀。
2.防腐蚀技术
文南油田自2005年以来,加大了油井腐蚀的治理力度,先后研究并推广应用了多种防腐蚀技术,如固体防腐剂技术、阴极保护器与井口加药技术等,在一定程度上减轻了管、杆的腐蚀现象。
但随着油田综合含水的上升,油井的腐蚀仍在继续。
从应用效果来看,油井加缓蚀剂技术是目前应用比较成熟的防腐蚀技术,它不但可以保护油管、套管及井下设备,而且可以起到保护集油管线和设备的作用,是一项成本低、容易实施、见效快的措施。
(1)固体防腐剂技术
将防腐药剂固化成一定形状,装在油管短节内,安装在筛管以下,通过药剂缓慢释放于井内流体中,延长药剂的作用有效期。
当油井作业时,将防腐药剂放在泵下尾管或油层顶界以上,防腐效果更好。
文南油田的腐蚀主要是高矿化度的弱酸性溶液的co2引起的,选用能有效降低环境中co2含量的咪唑啉类缓蚀剂作为固体缓蚀剂的主要成分。
在油井生产过程中,固体活性物质从固体缓蚀剂中缓慢释放,随产出液通过油管不断上升,对接触井内流体的油管进行防护。
特点:该项技术具有效果平稳、易控制,适用于油气比较高或产液量较大的油井。
但是防腐药剂(主要针对高clˉ腐蚀)耐温只有80℃,在泵挂较深的井上应用时,可溶性固体缓蚀剂在较短时间内就会溶解消耗完,不能在整个生产周期内起到有效的保护作用。
(2)液体缓蚀剂的应用
文南油田在用的普通缓蚀剂(zsy92-1缓蚀剂)是以合成的炔氧甲基胺及其衍生物和醚类化合物复配而成,为水溶油分散吸附成膜型的缓蚀剂。
该缓蚀剂主要适用于高clˉ、高矿化度的腐蚀介质的油井。
油井加缓蚀剂采用冲击式预膜处理周期性加药,用泵将缓蚀剂注入到油套管环形空间,靠缓蚀剂的自重降到井底,随产出液从油管内返出,在这一过程中,缓蚀剂大部分溶解于产出水中,少量分散在油中,随着上返,缓蚀剂在金属表面被吸附而形成保护膜,由此起到了防护作用。
为遏制油井腐蚀的日益恶化,对文33块腐蚀严重的频繁检泵井进行了腐蚀机理研究,根据多种合成与复配的缓蚀剂的室内及现场试验,经过多轮次的试验筛选出适合的缓蚀剂类型。
确定利用咪唑啉、酰胺基、有机阳离子、炔基进行改性,具有较高缓蚀率的缓蚀剂为适用于文33块的新型缓蚀剂。
通过应用新型缓蚀剂,有效的提高了腐蚀严重油井的治理效果,腐蚀得到有效控制。
3.结论与建议
(1)固体防腐器在一定程度上减轻了油井的腐蚀,对于套压较高、卡封油井、低液面油井,不能采用(或应用效果差)井口加药装置投加缓蚀剂的油井,可考虑使用固体防腐器;可将现用的效果较好的液体缓蚀剂固化制成固体防腐剂,增强油井防腐蚀针对性,改善固体防腐器的应用效果。
(2)缓蚀剂技术是油井防腐蚀的最有效的手段,它不但可以保
护油管、套管及井下设备,而且可以起到保护集油管线和设备的作用,是一项成本低、容易实施、见效快的措施。