振动故障诊断要点汇总一
振动基本知识及其故障诊断综述

振动基本知识及其故障诊断综述引言振动是物体在运动过程中产生的周期性往复运动,广泛应用于工程、地震学、医学等领域。
振动不仅可以用于传递能量和信息,还可以帮助我们了解物体的性能和状态。
因此,对振动的研究和故障诊断具有重要意义。
本文将介绍振动的基本知识以及在故障诊断中的应用。
振动的基本概念振动可以通过物体的周期性往复运动来描述。
它是由物体的固有频率和外部作用力共同决定的。
振动可以是机械的,例如机械系统中的旋转或线性振动;也可以是电磁的,例如电路或天线中的振动。
振动的基本概念包括振动的周期、频率、振幅和相位。
•周期:振动一次完成所需的时间。
周期的倒数称为频率,即振动的次数每秒。
•频率:振动的次数每秒。
•振幅:振动物体在其平衡位置附近的最大偏移量。
•相位:振动物体相对于某参考点的位置关系。
振动的类型振动可以分为自由振动和受迫振动两种类型。
•自由振动:在没有外界干扰的情况下,振动物体按照固有的频率和振幅自由振荡。
自由振动可以用振动系统的质量、刚度和阻尼特性来描述。
•受迫振动:振动物体受到外界作用力的驱动而振动。
外界作用力可以是周期性的或非周期性的。
受迫振动通常会引起共振现象,即振幅随着外界作用力频率的变化而发生显著变化。
振动的故障诊断振动的故障诊断是通过分析振动信号来判断机械设备的工作状态和可能存在的故障。
振动信号可以通过加速度传感器或振动传感器来测量和记录。
常用的故障诊断方法包括频域分析、时域分析和轨迹分析。
•频域分析:通过将振动信号转换为频域信号,可以观察到振动信号在不同频率上的成分。
故障通常会在振动信号的频谱中产生特征频率成分,可以通过寻找这些特征频率来判断故障类型。
•时域分析:通过观察振动信号的时间波形,可以了解振动信号的特征和变化趋势。
时域分析可以帮助识别故障的不稳定和瞬态特征。
•轨迹分析:通过将振动信号的相位信息绘制成轨迹图,可以观察到振动信号在相位空间中的分布。
轨迹图可以帮助发现存在振动现象的故障,例如不平衡、脱离和摩擦等。
振动故障诊断要点总会1

两
两
两 两 两 两 两 两 两
两
两 1 2 两 两 2×两1 ×两 1 2 两 两 1 2 两 两 两 两 两 两 4 两 两 两 3 两 3 两 4 两 3×两 两 两 两 5 两 6 两 两 两 3 两 4 两 5 两 6 两 两 两 两 两 7 8
两
两 两 1 两 , 两 1. 2. 两 2. 2 两 1. , 两 两 1. 2. 两 3 两 两 , , 4
两 1 2 3 4 5 两 两 0.5×两 1 两 两 两 1×两 2 两 两 1 两 两 1. 2. 3. 两 两 两 两 1. 2. 两 3 两 两 2 两 两 两 两 两 两 4 两 两 两 5 两 两 两 两 3 两 , , 4 两 两 两 两 6 两 ω 弓局性 Ω两 两 两 6 两 7 两 8 两
两 两
两
两 1 两 <0.5×; 0.42~0.48×两 两 两 两 1 两 2 两 3 两 4 两 5 两 1. 2. 两 两 4. 两 两 1 两 两 1. 3. 两 2. 两 1. 2 两 2. 两 3 两 两 , 两 , 4 两 两 两 3. , 2 ωn , 两 两 两 6 两 两 两 两 2 两 两 3 两 两 4 两 5 两 两 两 两 两 6 7 8
两
两 弓两 两 弓×两 性两 两 两 两 感两 两 两 两 两 两 弓两 两 两 两 两 两 两 弓两 两 始 始 两 两 两 弓两 两 弓×两 两 两 性两 两 感两 两 两 两 两 两 弓两 两 两 两 两 两 两 弓两 两 两 性两 两 感两 两 或两 两 两 两 性两 两 感两 两 或两 两 持两 两 损两 两 两 或两 持两 两 损两 两 两 两 两 两 操两 明两 两 始 两 两 两 性两 两 感两 两 或两 两 两 两 性两 两 感两 两 或两 两 持两 两 损两 两 或两 持两 两 两 损两 两 两 两 两 两 操两 明两
不对中、不平衡振动诊断要点

不对中的故障诊断要点1)频域:①确认轴向和径向在1、2、3倍频处有稳定的高峰,特别注意2倍频分量。
②径向振动信号以1倍频和2倍频分量为主,轴系不对中越严重,其2倍频分量就越大,多数情况下会超过1倍频。
③轴向振动以1倍频分量幅值较大,幅值和相位稳定。
④联轴节两侧相临轴承的油膜压力反方向变化,一个油膜压力变大,另一个则变小。
相位基本上成180度。
⑤4-10倍频分量较小。
2) 时域:确认以稳定的周期波形为主,每转出现1个、2个或3个峰,没有大的加速度冲击现象。
如果轴向振动径向振动一样大或者比径向还大,则说明情况非常严重。
3)振动信号的原始波形是畸变的正弦波。
4)轴心轨迹呈香蕉形或8字形,正进动。
5)振动对负荷变化较为敏感,一般振动幅值随负荷的增大而升高。
提示:1)在确认不对中的若干特征时,如果出现:轴向振动小且4-10倍频分量较大,则有可能是机械松动。
2)在诊断不对中时,如果1倍频分量比其他分量占优势,可能存在角不对中;2倍频分量比其他分量占优势,可能存在平行不对中。
3)如果时域波形不稳定或出现较大的冲击现象,可能是其他故障。
4)对于电机,如果基频及其他倍频分量大的同时,其振动时域波形有调制现象,或基频处出现边频,可能存在机电故障,如转子断条或轴承倾斜导致的偏心。
5)对于齿式联轴器在2倍频下,还可能出现3、4、5等倍频分量。
6)对于目前使用较多的膜片联轴器可出现N倍频(N为螺栓的个数)。
不平衡的振动诊断1)频域:i.确认频谱中以稳定的基频分量为主,其它倍频幅值很小。
ii.轴向振动比径向小得多。
iii.必要时可以改变转速,在升速过程中当转速小于临界转速时,确认工频幅值随转速升高而增大;当转速大于临界转速后,振幅随转速增大反而减小,并趋向一个较小的稳定值。
当转速接近临界转速时,将产生共振,此时振幅将有最大峰值。
2)时域:i.波形以稳定的单一频率为主,轴每转一周出现一个峰值。
振动信号的原始波形为正弦波。
ii.轴向振动比径向小得多。
现场设备常见振动故障及其一些表现特征(一)

现场设备常见振动故障及其一些表现特征(一)做好故障诊断这项工作,就必须掌握一定量的常见故障原因及其主要表现特征,例如,经频谱分析发现振动为单一的旋转频率,这时候我们会想到,振动原因可能是转子不平衡、是共振、转子中间弯曲、支撑刚度不足等原因,这些故障发生时都将产生绝对的转频振动,我们只能再根据这些故障的其它特征进行排除确定最终找到故障原因,振动方向、振动位置、振动与负荷关系、振动与时间关系、振动与压力关系、振动相位、振动相位差、振动稳定性、相位的稳定性等等,假如我们不知道转频对应的这些原因,或者只知道其中的一两种,而真正的故障原因又不在其中,单从频谱上就无法进行判断,又假如我们知道了上述诸多原因但却不知道每种故障所表现出的特征同样无法进行判断和甄别。
需要强调的是无论是牵引部分振动还是被牵引部分振动,我们都必须将其作为一个整体看待,而不是哪地方振动最大就测哪。
一般情况下振动最大位置往往就是故障部位,但很多情况下却不是这样的,造成这种情况的主要原因是设备整体刚度分布不均,但各部件刚度可能是一样的,但连接成整体以后,刚度可能存在很大差异,往往振动突出在刚度差的部位,另一种情况是共振。
机械松动故障:说到机械松动大家就会想到活动部件,这当然是松动故障之一,比如过盈部件出现了间隙,如轴承内圈与轴的配合、联轴器与轴的配合、叶轮与轴的配合等等,紧固件出现了松动,连接螺栓不紧固等等,但通常配合间隙过大时也会出现以上的松动现象,所以常常也把它列入松动故障之列.松动通常会表现出线性和非线性两种特征,这与松动的程度、转子偏心距的大小、及转速与临界转速之比来确定,也正是这种非线性,致使利用精确平衡减小振动变的极为困难,没有平衡经验工作人员在现场平衡变得几乎不可能完成。
频谱特征,因为松动直接导致的后果是放大不平衡振动,所以松动故障反应在频谱上也就有单一的基频振动或者是基频加丰富倍频的振动,也就形成了是线性与非线性两种振动特征,而且基频几乎总是占有绝对大位置,这种现象在连接松动上表现尤为明显松动故障通常表现出不稳定的振动,一般成周期性变化,比如振动从85um 慢慢涨到110um,又从110um慢慢回到85um,形成一个周期性振动。
机械振动信号的特征分析与故障诊断
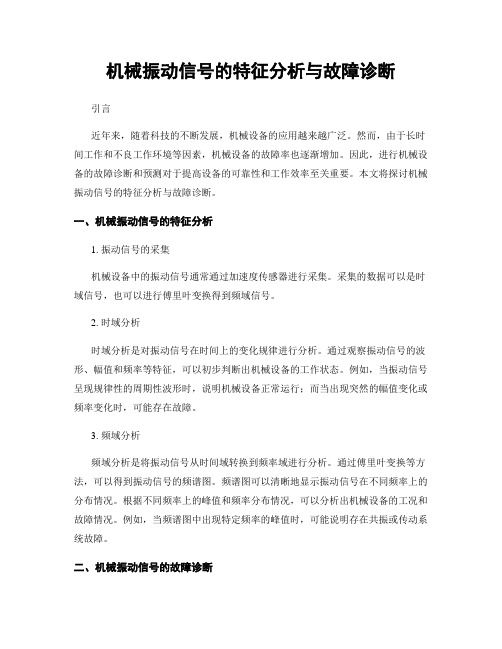
机械振动信号的特征分析与故障诊断引言近年来,随着科技的不断发展,机械设备的应用越来越广泛。
然而,由于长时间工作和不良工作环境等因素,机械设备的故障率也逐渐增加。
因此,进行机械设备的故障诊断和预测对于提高设备的可靠性和工作效率至关重要。
本文将探讨机械振动信号的特征分析与故障诊断。
一、机械振动信号的特征分析1. 振动信号的采集机械设备中的振动信号通常通过加速度传感器进行采集。
采集的数据可以是时域信号,也可以进行傅里叶变换得到频域信号。
2. 时域分析时域分析是对振动信号在时间上的变化规律进行分析。
通过观察振动信号的波形、幅值和频率等特征,可以初步判断出机械设备的工作状态。
例如,当振动信号呈现规律性的周期性波形时,说明机械设备正常运行;而当出现突然的幅值变化或频率变化时,可能存在故障。
3. 频域分析频域分析是将振动信号从时间域转换到频率域进行分析。
通过傅里叶变换等方法,可以得到振动信号的频谱图。
频谱图可以清晰地显示振动信号在不同频率上的分布情况。
根据不同频率上的峰值和频率分布情况,可以分析出机械设备的工况和故障情况。
例如,当频谱图中出现特定频率的峰值时,可能说明存在共振或传动系统故障。
二、机械振动信号的故障诊断1. 故障特征提取在进行机械设备的故障诊断时,首先需要从振动信号中提取故障特征。
根据机械设备的不同类型和工作方式,故障特征可能具有多种形式。
例如,对于滚动轴承故障,常用的特征包括脉冲特征、包络谱特征和细节系数特征等。
2. 故障诊断方法针对不同类型的故障,可以采用不同的诊断方法。
常见的故障诊断方法包括模式识别、神经网络和支持向量机等。
这些方法可以通过对机械振动信号进行特征提取和分析,建立故障诊断模型进行故障判断。
3. 故障诊断系统为了实现机械设备的在线故障诊断和预测,可以搭建故障诊断系统。
故障诊断系统将振动传感器、数据采集模块、信号处理模块和故障诊断模型等部件进行集成,实时监测和分析机械设备的振动信号,并输出故障诊断结果。
设备故障振动分析诊断

PI PO
电机
水泵
本例中最高 出现16X成分
波形出现许多毛刺。
谱图中噪声水平高。
出现精确的倍频2X, 3X…等成分。 松动结合面两边,振幅 有明显差别。
转速的精确 倍频成分
噪声水平高
13
?
松动故障引起的间入谐量
未松动时的频 谱
松动时的频谱
出现0.5X,1.5X, 2.5X,3.5X...等 频率成分
还可用如共振解调、 倒频谱等诊断方法。
基本频率的 四个谐波
17
?
滚动轴承故障的频谱
PI PO
电机
离心泵
轴承每一种零件故障有其 特殊的故障频率。
随着故障发展,会产生故 障频率的谐波和边频带。
多个故障并存时,频谱图 很复杂,难以识别。
1X 2X 故障基本 频 频率6.71X 率
基本频率的 四个谐波
18
转动特征 正进动 正进动 正进动
自 正进动 激
振 动 正进动 类 故 反进动 障
R: 转动频率
7
?
转子不平衡故障的频谱
TO
TI
透平 齿轮箱 风机 波形为简谐波,少毛刺。 轴心轨迹为圆或椭圆。 1X频率为主。 轴向振动不大。 振幅随转速升高而增大。 过临界转速有共振峰。
轴向很小 1X频率(铅垂) 1X频率(水平) 轴向很小 1X频率(铅垂) 1X频率(水平)
综合不对中 e 0, 0
11
?
不同联轴节的情况
联轴节类型 不对中形式
振动特征
刚性联轴节 平行不对中 有2X成分 角度不对中 轴向振动1X成分大
齿式联轴节
轴向振动大,有2X及高次谐波 径向振动可能有2X、3X、4X… 联轴节两侧振动的相位常相反
机械振动学中的振动故障诊断与技术

机械振动学中的振动故障诊断与技术在机械系统中,振动是一种常见的现象。
振动的产生是由于机械系统在运行过程中受到不同力的作用而发生的运动。
正常情况下,机械系统的振动可以帮助我们判断系统是否正常工作。
然而,当机械系统中出现了振动故障时,就需要进行振动故障诊断与技术处理,以确保机械系统正常运行。
下面将介绍机械振动学中的振动故障诊断与技术。
1. 振动故障的种类在机械系统中,振动故障可以分为结构振动故障和非结构振动故障两种。
结构振动故障是由于机械系统结构的设计缺陷或损坏所导致的振动问题,而非结构振动故障则是由于机械系统中其他部件的损坏或松动引起的振动问题。
在进行振动故障诊断时,需要根据振动的特点和机械系统的结构来确定振动故障的种类。
2. 振动故障的诊断方法为了准确诊断机械系统中的振动故障,可以采用多种方法进行振动测量和分析。
常见的振动诊断方法包括频谱分析、时域分析、轨迹分析、阶次分析等。
通过这些方法可以获取机械系统中不同频率和振幅的振动信号,从而判断振动故障的具体原因。
3. 振动故障的处理技术一旦确定了机械系统中的振动故障,就需要采取相应的处理技术来解决问题。
根据振动故障的具体类型,可以采用不同的处理方法,如调整机械系统的平衡性、更换受损部件、加强固定支撑等。
通过有效的处理技术,可以及时消除振动故障,确保机械系统的正常运行。
在机械振动学中,振动故障诊断与技术是非常重要的内容。
只有及时准确地诊断和处理振动故障,才能保证机械系统的稳定运行,延长机械设备的使用寿命,提高生产效率。
因此,掌握振动故障诊断与技术是每位机械工程师必备的技能之一。
希望本文的介绍对您有所帮助,谢谢阅读。
汽轮发电机组振动故障诊断及案例

汽轮发电机组振动故障诊断及案例汽轮发电机组是一种常见的发电设备,其工作过程中可能出现振动故障。
振动故障会对设备的正常运行产生严重影响,因此进行振动故障的诊断和处理具有重要意义。
下面将列举一些关于汽轮发电机组振动故障诊断的案例。
1. 振动频率突然增大:在汽轮发电机组运行过程中,突然出现振动频率增大的情况。
经过检查发现,发电机组的轴承出现损坏,导致轴承摩擦不均匀,进而引起振动频率的增大。
解决方法是更换轴承并进行润滑。
2. 振动频率突然减小:在汽轮发电机组工作中,振动频率突然减小。
经过检查发现,发电机组的风扇叶片出现松动,导致不稳定振动。
解决方法是重新固定风扇叶片。
3. 振动幅值异常增大:在汽轮发电机组运行过程中,振动幅值突然增大。
经过检查发现,发电机组的基础螺栓松动,导致机组整体不稳定,振动幅值增大。
解决方法是重新紧固基础螺栓。
4. 振动频率出现谐振:在汽轮发电机组运行中,出现振动频率与机组自身固有频率相同的谐振现象。
经过检查发现,机组的结构刚度不足,导致谐振频率与机组自身频率相同。
解决方法是增加机组的结构刚度。
5. 振动频率与转速相关:在汽轮发电机组运行中,振动频率与转速呈线性关系,振动频率随转速增加而增加。
经过检查发现,机组的动平衡出现问题,导致振动频率与转速相关。
解决方法是进行机组的动平衡调整。
6. 振动频率与电流相关:在汽轮发电机组运行中,振动频率与电流呈线性关系,振动频率随电流增大而增大。
经过检查发现,机组的电机绝缘出现问题,导致电流异常,并引起振动频率的变化。
解决方法是更换电机绝缘材料。
7. 振动频率与负载相关:在汽轮发电机组运行中,振动频率与负载呈线性关系,振动频率随负载增加而增加。
经过检查发现,机组的轴向间隙不合适,导致振动频率与负载相关。
解决方法是调整轴向间隙。
8. 振动频率与温度相关:在汽轮发电机组运行中,振动频率与温度呈线性关系,振动频率随温度升高而增加。
经过检查发现,机组的冷却系统出现故障,导致温度升高并引起振动频率的变化。
- 1、下载文档前请自行甄别文档内容的完整性,平台不提供额外的编辑、内容补充、找答案等附加服务。
- 2、"仅部分预览"的文档,不可在线预览部分如存在完整性等问题,可反馈申请退款(可完整预览的文档不适用该条件!)。
- 3、如文档侵犯您的权益,请联系客服反馈,我们会尽快为您处理(人工客服工作时间:9:00-18:30)。
杂乱
正进动
突变
旋转分离振动随敏感参数的变化
1
2
3
4
5
6
随转速
随负荷
随油温
随流量
随压力
其它识别方法
明显
很明显
不变
很明显
变化
1.机器出口压力波动大2.机器入口气体压力及流量波动
旋转分离的故障原因
故障来源
1
2
3
4
设计、制造
安装、维修
运行、操作
机器劣化
主要原因
各级流道设计不匹配
1.入口过滤器堵塞2.叶轮或气流流道堵塞
振动故障诊断要点汇总
一、转子不平衡
转子质量偏心的振动特征
1
2
3
4
5
6
7
8
特征频率
常伴频率
振动稳定性
振动方向
相位特征
轴心轨迹
进动方向
矢量区域
1×
稳定
径向
稳定
椭圆
正进动
不变
不变
转子质量偏心振动随敏感参数的变化
1
2
3
4
5
6
随转速
随负荷
随油温
随流量
随压力
其它识别方法
明显
不明显
不变
不变
不变
低速时振动趋于零
转子质量偏心的故障原因
1.管道阻力增大2.管网阻力增大3.管路逆止阀失灵
十二.转子过盈配合件过盈不足
转子过盈配合件过盈不足的振动特征
1
23456 Nhomakorabea7
8
特征频率
常伴频率
振动稳定性
振动方向
相位特征
轴心轨迹
进动方向
矢量区域
<1×次谐波
1×
不稳
径向
杂乱
不稳定
正进动
改变
转子过盈配合件过盈不足振动随敏感参数的变化
1
2
3
4
5
6
随转速
随负荷
主要原因
制造误差造成密封或叶轮在内腔的间隙不均匀
转子或密封安装不当
操作不当,升降速过快,升降压过猛,超负荷运行
转轴弯曲或轴承磨损产生偏隙
七.旋转分离
旋转分离的振动特征
1
2
3
4
5
6
7
8
特征频率
常伴频率
振动稳定性
振动方向
相位特征
轴心轨迹
进动方向
矢量区域
ωs及(Ω-ωs)的成对谐波
组合频率
振幅大幅度波动
径向、轴向
1.润滑油不良2.油温或油压不当
轴承磨损,疲劳损伤,腐蚀及气蚀等
注: 1)ω-涡动频率2)Ω-转子旋转频率3)ωn-转子临界转速
六.密封和间隙动力失稳
密封和间隙动力失稳的振动特征
1
2
3
4
5
6
7
8
特征频率
常伴频率
振动稳定性
振动方向
相位特征
轴心轨迹
进动方向
矢量区域
<0.5×的次谐波
1×,(1/n)×及n×
1.超负荷运行
2.保温不良,轴系各部热变形不同
1.基础沉降不匀,对中又差2.环境温度变化大,机器热变形不同
四、油膜涡动
油膜涡动的振动特征
1
2
3
4
5
6
7
8
特征频率
常伴频率
振动稳定性
振动方向
相位特征
轴心轨迹
进动方向
矢量区域
≤0.5×
1×
较稳定
径向
稳定
双环椭圆
正进动
改变
油膜涡动振动随敏感参数的变化
1
2
3
4
机器劣化
主要原因
结构不合理,制造误差大,材质不均匀
转子预负荷较大
升速过快,加载太大
转子稳定性差
三、转子不对中
转子不对中的振动特征
1
2
3
4
5
6
7
8
特征频率
常伴频率
振动稳定性
振动方向
相位特征
轴心轨迹
进动方向
矢量区域
2×1×
3×
稳定
径向、轴向
较稳定
双环椭圆
正进动
不变
转子不对中振动随敏感参数的变化
1
2
3
4
5
不稳,强烈振动
径向
不稳定
紊乱,扩散
正进动
突变
密封和间隙动力失稳振动随敏感参数的变化
1
2
3
4
5
6
随转速
随负荷
随油温
随流量
随压力
其它识别方法
在某值失稳
很敏感
明显改变
不变
有影响
1.分数谐波及组合频率
2.工作转速到达某值突然振动
密封和间隙动力失稳振动的故障原因
故障来源
1
2
3
4
设计、制造
安装、维修
运行、操作
机器劣化
6
随转速
随负荷
随油温
随流量
随压力
其它识别方法
不明显
明显
有影响
有影响
有影响
1)转子轴向值就大
2)联轴器相临轴承处振动大3)振动随负荷增加而增大4)对环境温度变化敏感
转子不对中的故障原因
故障来源
1
2
3
4
设计、制造
安装、维修
运行、操作
机器劣化
主要原因
热膨胀量不够,对中值误差较大
1.安装精度未达到技术要求2.热态不对中考虑不足
转子弓形弯曲的故障原因
故障来源
1
2
3
4
设计、制造
安装、维修
运行、操作
机器劣化
主要原因
结构不合理,
制造误差大,材质不均匀
1.转子存放不当,永久变形2.轴承安装错位,预负荷大
高速,高温机器,停车后未及时盘车
转子热稳定性差,长期运行自然弯曲
转子临时性弯曲的振动特征
1
2
3
4
5
6
7
8
特征频率
常伴频率
振动稳定性
工作介质流量调整不当,工艺参数不匹配
气体入口或流道异物堵塞
旋转分离与油膜振荡的区别
区别内容
旋转失速
油膜振荡
振动特征频率与工作转速
振动特征频率随工作转速而变
油膜振荡后,频率不随工作转速变化
振动特征频率与机器入口流量压力脉动频率
振动强烈程度随流量而变与工作流速频率相等
振动强烈程度不随流量而变与转子固有频率相近
振动方向
相位特征
轴心轨迹
进动方向
矢量区域
1×
稳定
径向、轴向
稳定
椭圆
正进动
升速矢量时增大,稳定后减小
转子临时性弯曲振动随敏感参数的变化
1
2
3
4
5
6
随转速
随负荷
随油温
随流量
随压力
其它识别方法
明显
不明显
不变
不变
不变
升速过程振幅大,常不能正常启动
转子临时性弯曲的故障原因
故障来源
1
2
3
4
设计、制造
安装、维修
运行、操作
1.热膨胀严重不均匀2.转子位移
基础或壳体变形大
十.转轴横向裂纹
转轴横向裂纹的振动特征
1
2
3
4
5
6
7
8
特征频率
常伴频率
振动稳定性
振动方向
相位特征
轴心轨迹
进动方向
矢量区域
半临界点的2×
2×,3×等高频谐波
不稳
径向,轴向
不规则
双椭圆或不规则
正进动
改变
转轴横向裂纹振动随敏感参数的变化
1
2
3
4
5
6
随转速
随负荷
振动发生后,升高转速,振动不变
不明显
明显
不变
明显
1.工作角频率≥2ωn时突发振动
2.振动强烈,有低沉吼叫
3.振荡前有涡动
4.振动异常,非线性特征
油膜振荡的故障原因
故障来源
1
2
3
4
设计、制造
安装、维修
运行、操作
机器劣化
主要原因
轴承设计或制造不合理
1.轴承间隙不当2.轴承壳体配合过盈不足3.轴瓦参数不当
突变
转子与静止件径向摩擦随敏感参数的变化
1
2
3
4
5
6
随转速
随负荷
随油温
随流量
随压力
其它识别方法
不明显
不明显
不变
不变
不变
时域波形严重削波
转子与静止件径向摩擦的故障原因
故障来源
1
2
3
4
设计、制造
安装、维修
运行、操作
机器劣化
主要原因
转子与静止件(轴承,密封,隔板)的间隙不当
1.转子与定子偏心2.转子对中不良3.转子动挠度大
注:ωs≈0.5Ω为旋转分离角频率.
八.转子支撑系统联接松动
转子支撑系统联接松动的振动特征
1
2
3
4
5
6
7
8
特征频率
常伴频率
振动稳定性
振动方向
相位特征
轴心轨迹
进动方向
矢量区域
基频及分数谐波