活性氧化铝的生产工艺过程
活性氧化铝的制备—1

活性氧化铝的制备活性氧化铝(Al2O3)是一种具有优异性能的无机物质,不仅能做脱水吸附剂、色谱吸附剂,更重要的是做催化剂载体,并广泛用于石油化工领域。
它涉及到重整、加氢、脱氢、脱水、脱卤、歧化、异构化等各种反应。
所以能如此广泛地被采用,主要原因是它结构上有多种形态及物化性质上千差万别。
学习有关Al2O3的制备方法,对掌握催化剂制备有重要意义。
一、实验目的1、通过铝盐与碱性沉淀剂的沉淀反应,掌握氧化铝催化剂和催化剂载体的制备过程。
2、了解制备氧化铝水合物的技术和原理。
3、掌握活性氧化铝的成型方法。
二、合成方法及原理1、以铝盐为原料用AlCl3·6H2O,Al2(SO4)3·18H2O,Al(NO3)3Cl3·9H2O,KAl (SO4)4·24H2O等的水溶液与沉淀剂—氨水、NaOH、Na2CO3等溶液作用生成氧化铝水合物。
球状活性氧化铝以三氯化铝为原料有较好的成型性能。
实验多使用该法制备水合氧化铝。
2、以偏铝酸钠为原料偏铝酸钠可在酸性溶液作用下分解沉淀析出氢氧化铝。
此原料在工业生产上较经济,是常用的生产活性氧化铝的路线,但常因混有不易脱除的Na+ ,故常用通入CO2的方法制各种晶型的Al(OH)3。
制备过程中有Al3+ 和OH—存在是必要的,其他离子可经水洗被除掉。
另外还有许多方法,它们都是为制取特殊要求的催化剂或载体而采用的。
制备催化剂或载体时,都要求除去S、P、As、Cl等有害杂质,否则催化活性较差。
本实验采用铝盐与氨水沉淀法。
将沉淀物在pH=8~9范围内老化一定时间,使之变成α—水铝石,再洗涤至无氯离子。
将滤饼用酸胶溶成流动性能较好的溶胶,用滴加法滴入油氨柱内,在油中受表面张力作用收缩成球,再进入氨水中,经中和和老化后形成较硬的凝胶球状物(直径在1~3mm之间),经水洗油氨后进行干燥。
也可将酸化的溶胶喷雾到干燥机内,生成40~80μm的微球氢氧化铝。
活性氧化铝的制备
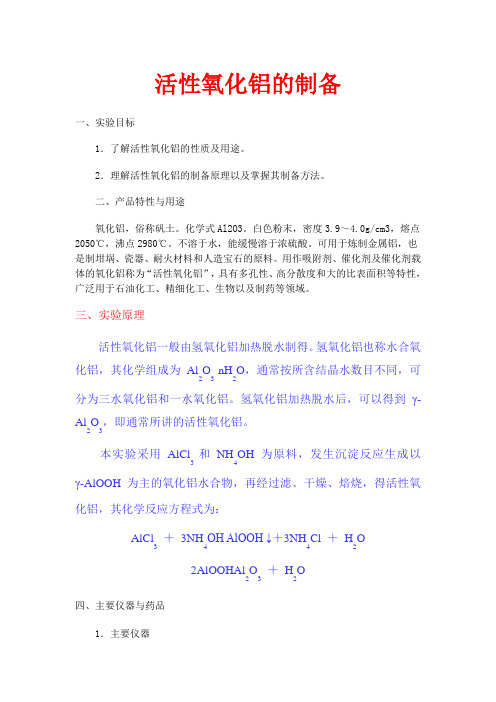
活性氧化铝的制备一、实验目标1.了解活性氧化铝的性质及用途。
2.理解活性氧化铝的制备原理以及掌握其制备方法。
二、产品特性与用途氧化铝,俗称矾土。
化学式Al2O3。
白色粉末,密度3.9~4.0g/cm3,熔点2050℃,沸点2980℃。
不溶于水,能缓慢溶于浓硫酸。
可用于炼制金属铝,也是制坩埚、瓷器、耐火材料和人造宝石的原料。
用作吸附剂、催化剂及催化剂载体的氧化铝称为“活性氧化铝”,具有多孔性、高分散度和大的比表面积等特性,广泛用于石油化工、精细化工、生物以及制药等领域。
三、实验原理活性氧化铝一般由氢氧化铝加热脱水制得。
氢氧化铝也称水合氧化铝,其化学组成为Al2O3·nH2O,通常按所含结晶水数目不同,可分为三水氧化铝和一水氧化铝。
氢氧化铝加热脱水后,可以得到γ-Al2O3,即通常所讲的活性氧化铝。
本实验采用AlCl3和NH4OH为原料,发生沉淀反应生成以γ-AlOOH为主的氧化铝水合物,再经过滤、干燥、焙烧,得活性氧化铝,其化学反应方程式为:AlCl3+3NH4OH AlOOH ↓+3NH4Cl +H2O2AlOOHAl2O3+H2O四、主要仪器与药品1.主要仪器马弗炉、电热恒温干燥箱、水浴锅、电动搅拌器、布氏漏斗、水泵。
2.主要药品三氯化铝,AR ;氨水,AR ;碳酸氢铵,AR 。
五、实验内容与操作步骤1.γ-AlOOH 的制备将四口烧瓶固定在水浴锅中,并安装好电动搅拌器。
用两个分液漏斗作为加料器,分别固定在铁架台上。
在烧瓶的两个边口上,塞上带有玻璃短管的橡皮塞,再用乳胶管将两个分液漏斗的出口分别与烧瓶的这两个边口相连。
在烧瓶的另一边口插上温度计。
称取6.5克AlCl3放至烧杯中,用150mL 蒸馏水溶解,倒入其中一个分液漏斗中。
配制5.2%的NH4OH 溶液150mL ,倒入另一个分液漏斗中。
称取0.5克碳酸氢铵并用100mL 蒸馏水溶解,倒入烧瓶中,作为稳定pH 值的缓冲溶液。
接通电源加热到85℃,开动搅拌器,缓慢滴加氨水及AlCl3溶液,两者滴加速度均控制约3mL/min ,约50分钟滴加完毕。
活性氧化铝的制备及改性..

3.5.2 助挤剂的影响
• 工业上常用3种助挤剂:田菁粉、多元羧酸及二者复合助挤剂。草酸 、酒石酸、柠檬酸等多元酸助挤成型的载体,孔径分布较集中,孔径大 于10 nm的孔明显减少,强度相应提高,不过载体磨损率和挤出速度的 改善不明显。现在多采用复合助挤剂。采用乙酸与田菁粉复合使用效果 比较理想,其用量影响见表6。
3.5 添加剂对活性氧化铝性能的影响
•
•
3.5.1 胶溶剂的影响
为增加氧化铝粒子间的粘结性,提高载体强度,改善孔结构,选 择酸性胶溶剂在混捏中使胶溶剂与氢氧化铝干胶粉发生胶溶作用,生 成假溶胶,使粒子粘结起来,便于成型。硝酸、盐酸、乙酸、甲酸、 柠檬酸、三氯乙酸等酸性胶溶剂对载体物理性能的影响见表5。
注:成胶PH为1.8-8.5
3.2 pH摆动法制备拟薄水铝石
• 酸碱中和制备拟薄水铝石时,使pH反复摆多次,会 使生成拟薄水铝石的孔径增加、孔容增加、孔径分布更 集中。随往复次数的增加,拟薄水铝石含量可提高,结 晶颗粒也会增大,颗粒度也会更趋于一致,从而得到结 晶纯度高、孔径分布集中的拟薄水铝石 • 实验以以偏铝酸钠与硝酸铝为原料,采用pH摆动法 ,考察了酸侧终点pH、碱侧终点pH、停留时间、摆动次 数对氧化铝物化性能的影响,结果见表3
2.2.1 拟薄水铝石的制备
以铝盐为原料:用Alcl3· 6H2o等的水溶液与碱性沉淀剂 --- 氨水、NaoH、Na2co3生成氧化铝水合物 Alcl3+ 3NH4oH → Al(oH )3 ↓ +3NH4cl
以偏铝酸钠为原料:在酸性溶液作用下分解沉淀 2NaAlco2+co2+H2o→Na2co3+2 Al(oH )3↓ NaAlco2+HNo3+H2o→NaNo3+ Al(oH )3↓
活性氧化铝的制备实验
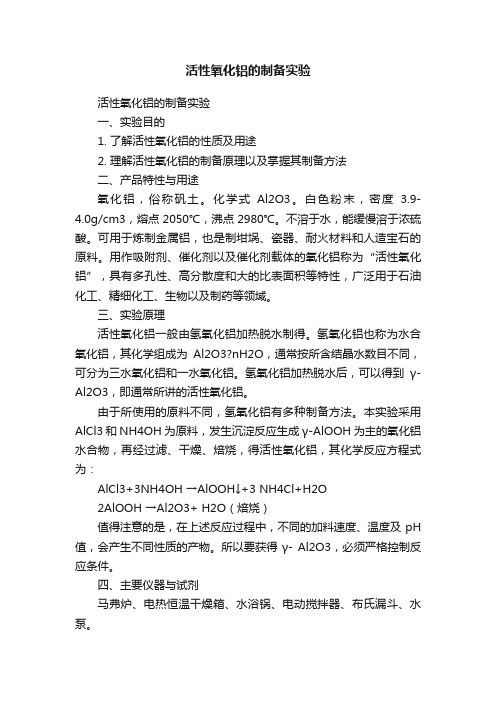
活性氧化铝的制备实验活性氧化铝的制备实验一、实验目的1. 了解活性氧化铝的性质及用途2. 理解活性氧化铝的制备原理以及掌握其制备方法二、产品特性与用途氧化铝,俗称矾土。
化学式Al2O3。
白色粉末,密度3.9-4.0g/cm3,熔点2050℃,沸点2980℃。
不溶于水,能缓慢溶于浓硫酸。
可用于炼制金属铝,也是制坩埚、瓷器、耐火材料和人造宝石的原料。
用作吸附剂、催化剂以及催化剂载体的氧化铝称为“活性氧化铝”,具有多孔性、高分散度和大的比表面积等特性,广泛用于石油化工、精细化工、生物以及制药等领域。
三、实验原理活性氧化铝一般由氢氧化铝加热脱水制得。
氢氧化铝也称为水合氧化铝,其化学组成为Al2O3?nH2O,通常按所含结晶水数目不同,可分为三水氧化铝和一水氧化铝。
氢氧化铝加热脱水后,可以得到γ- Al2O3,即通常所讲的活性氧化铝。
由于所使用的原料不同,氢氧化铝有多种制备方法。
本实验采用AlCl3和NH4OH为原料,发生沉淀反应生成γ-AlOOH为主的氧化铝水合物,再经过滤、干燥、焙烧,得活性氧化铝,其化学反应方程式为:AlCl3+3NH4OH →AlOOH↓+3 NH4Cl+H2O2AlOOH →Al2O3+ H2O(焙烧)值得注意的是,在上述反应过程中,不同的加料速度、温度及pH 值,会产生不同性质的产物。
所以要获得γ- Al2O3,必须严格控制反应条件。
四、主要仪器与试剂马弗炉、电热恒温干燥箱、水浴锅、电动搅拌器、布氏漏斗、水泵。
三氯化铝,氨水,碳酸氢铵五、实验内容与操作步骤1. AlOOH的制备将四口烧瓶固定在水浴锅中,并安装好电动搅拌器。
用两个分液漏斗作为加料器,分别固定在铁架台上。
在烧瓶的两个边口上,塞上带有玻璃短管的橡皮塞,再用乳胶管将两个分液漏斗的出口分别与烧瓶的这两个边口相连。
在烧瓶的另一边口插上温度计。
称取6.5g AlCl3放至烧杯中,用150mL蒸馏水溶解,倒入烧杯中,作为稳定pH值的缓冲溶液。
氧化铝生产工艺

氧化铝生产工艺氧化铝是一种广泛应用的重要非金属材料,具有高熔点、高硬度、耐酸碱腐蚀等特点,在工业生产中有着重要的作用。
氧化铝的生产工艺包括矿石选矿、矿石破碎、矿石浸出、过滤、溶液纯化、氧化、沉淀、过滤、洗涤、干燥等多个环节。
首先,在氧化铝的生产过程中,要选取合适的矿石作为原料。
常用的氧化铝矿石有硬铝石、泡沫铝石等。
选矿过程中,需要进行矿石的破碎和磨矿操作,将矿石分解成适合生产的颗粒大小。
接下来,经过破碎后的矿石进行浸出处理。
将矿石放入酸性浸出液中,通过化学反应将氧化铝从矿石中溶解出来。
浸出过程中,需要控制浸出液的温度、浸出时间和浸出液的酸碱度等参数,以保证氧化铝的溶解率和纯度。
在浸出过程中,得到的氧化铝溶液需要进行过滤,将固体杂质分离出来。
过滤后的溶液进一步进行纯化处理,去除其中的杂质和铝矾土。
随后,对纯化后的氧化铝溶液进行氧化处理。
将溶液导入反应器,在一定的温度和压力下,氧气与铝离子发生氧化反应,生成氧化铝颗粒。
氧化反应过程中,要控制反应温度和氧气的流量等,以使氧化铝颗粒具有所需的形貌和粒径。
氧化反应完成后,需要将生成的氧化铝颗粒进行沉淀。
将反应体系中的氧化铝颗粒沉淀到底部,与溶液分离。
然后,通过过滤等工艺步骤,将沉淀物进行分离和干燥,得到粗氧化铝。
最后,对粗氧化铝进行洗涤和干燥处理,将其中的杂质和水分去除。
洗涤过程中,可以使用水或其他洗涤剂进行清洗,以提高氧化铝的纯度。
干燥过程中,通过加热等方式将氧化铝颗粒中的水分和挥发物去除,以得到最终的氧化铝产品。
综上所述,氧化铝的生产工艺涉及矿石选矿、矿石破碎、矿石浸出、过滤、溶液纯化、氧化、沉淀、过滤、洗涤和干燥等多个环节。
每个环节都需要严格控制操作条件和参数,以保证氧化铝产品的质量和产量。
随着科学技术的不断进步,氧化铝生产工艺也在不断改进和优化,以提高生产效率和降低生产成本。
氧化铝制造工艺流程

氧化铝制造工艺流程氧化铝是一种重要的高纯度无机化合物,广泛用于陶瓷、电子、光学等领域。
下面将介绍氧化铝制造的工艺流程,希望对读者有所指导。
氧化铝的制造主要包括矿石选矿、碱法制碱、氧化铝制取和后续精炼等环节。
首先是矿石选矿阶段。
常见的氧化铝矿石主要有波特兰矾土、熔融矾土等。
选矿的目的是除去矿石中的杂质,得到纯度较高的氧化铝矿石。
选矿后,接下来是碱法制碱。
制碱过程中主要使用氢氧化钠或氢氧化铅等碱性物质,与选矿后的矿石反应生成铝矾土。
其中的杂质物质随反应生成的铝酸盐沉淀一并去除,以提高铝矾土的纯度。
制碱后,进行氧化铝制取阶段。
首先将铝矾土煅烧,使其脱水、硫酸根离去,转化为氧化铝。
煅烧条件需要控制得当,通常在高温高压下进行。
随后将煅烧后的产物与稀碱溶液进行浸出,得到氢氧化铝溶液。
再经过过滤、脱硫、脱硅等处理,最终得到纯度较高的氢氧化铝。
氢氧化铝溶液经过过滤、浓缩,产生氢氧化铝尾液。
而尾液中仍含有少量铝酸盐等有价值的金属盐,经过进一步处理后可回收利用。
同时,还有一部分氢氧化铝溶液经过结晶、离心等操作,得到固体氢氧化铝。
固体氢氧化铝可以用作原料,用于生产高纯度氧化铝。
最后是氧化铝的精炼阶段。
通过将氢氧化铝溶液重新进行煅烧,去除其中的杂质物质,得到纯度更高的氧化铝。
在精炼过程中,还可以根据特定需求,加入适量的其他金属元素或化合物,来制备含有特定功能的氧化铝产品。
综上所述,氧化铝的制造工艺流程较为复杂,包括矿石选矿、碱法制碱、氧化铝制取和后续精炼等环节。
每个环节都需要合理控制条件和操作,以提高氧化铝的纯度和质量。
制造过程中还有很多细节和技术难题需要克服,因此需要在实践中不断摸索和改进。
希望通过这篇文章,读者对氧化铝制造工艺有更全面的了解。
氧化铝生产工艺简介

氧化铝生产工艺简介氧化铝(Aluminium oxide,简称Al2O3)是一种广泛应用的工程材料,具有耐高温、耐腐蚀、绝缘性能良好等特点,广泛用于电子、陶瓷、建筑、化工等行业。
氧化铝的生产工艺主要分为两种,即碳酸铝法和氨铝石法。
以下将对这两种生产工艺进行详细介绍。
碳酸铝法是一种常用的氧化铝生产工艺。
具体步骤如下:1.起始原料准备:将铝酸盐(如氢氧化铝)和碳酸盐(如氢碳酸铝)作为起始原料。
碳酸盐是还原剂,可以将铝酸盐还原为氧化铝。
2.溶液制备:将起始原料溶解在水或其他溶剂中,形成氧化铝浆料。
3.沉淀反应:通过加入碱液或调整溶液pH值,使溶液中的铝离子发生沉淀反应,生成氢氧化铝沉淀物。
4.过滤和洗涤:将沉淀物过滤得到固体,然后进行洗涤,去除杂质。
5.烘干和焙烧:将洗涤后的固体烘干,然后进行焙烧处理,将氢氧化铝转化为氧化铝。
6.磨碎和筛分:将焙烧后的氧化铝块磨碎成粉末,并进行筛分,调整粒度和颗粒形状。
氨铝石法是另一种常用的氧化铝生产工艺。
具体步骤如下:1.起始原料准备:将铝金属或铝化合物作为起始原料。
铝金属是常用的起始原料,可以通过冶炼等方法获得。
2.粉碎和磨矿:将起始原料粉碎和磨细,以增大其表面积,有利于反应进行。
3.水解反应:将粉碎后的铝原料与氨气在一定温度下反应,发生水解反应,生成氨铝石。
4.过滤和洗涤:将水解后的氨铝石过滤得到固体,然后进行洗涤,去除杂质。
5.烘干和焙烧:将洗涤后的固体烘干,然后进行焙烧处理,将氨铝石转化为氧化铝。
6.磨碎和筛分:将焙烧后的氧化铝块磨碎成粉末,并进行筛分,调整粒度和颗粒形状。
以上是氧化铝的两种常用生产工艺的简介。
在实际应用中,根据不同的需求,还可以对生产工艺进行调整和改进,以提高产品质量和生产效率。
活性氧化铝的生产工艺过程
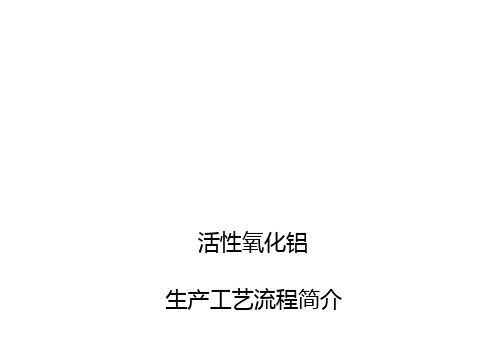
活性氧化铝生产工艺流程简介和检查混匀效果。
细碎碎铝土矿均化堆场铝土矿均化堆场至液碱贮存工段。
去原料磨去石灰消化2、石灰消化从石灰贮仓运来的石灰卸入本工序的石灰缓冲仓内,经溜槽直接入化灰机。
在消化工序,石灰和水同时加入化灰机,化灰机排出的石灰乳自流入石灰乳槽,由泵送往叶滤、排盐苛化等各用点,消化渣用汽车送往堆场堆存。
灰渣汽车运出厂去叶滤3、原矿浆磨制从均化堆场来的铝土矿和石灰贮仓来的石灰,经胶带输送机用卸料小车分别送入各自的磨头仓,磨头仓出料设有电子皮带称计量装置,按规定的配料比与经过计量的循环母液加入磨机。
磨矿过程采用双仓溢流型中心传动球磨机配水力旋流器流程,水旋器底流返回磨机再磨,水旋器溢流作为合格的原矿浆进入原矿浆槽。
循环母液中间泵池原矿浆槽4 、管道化溶出由原料磨工序送来的原矿浆进入预脱硅槽,进行加热预脱硅,然后用压力为10~12MPa的高压隔膜泵送入溶出系统,料浆首先经脉冲缓冲器进入一 ~ 九级用二次蒸汽间接加热的套管预热器和第十一级用熔盐间接加热的套管加热器,温度从85℃预加热至280℃,再经保温停留罐保温停留45分钟,使矿石中的氧化铝充分溶出。
溶出矿浆经十级矿浆自蒸发器闪蒸,使温度从280℃降至126℃,十级自蒸发器产生的二次蒸汽分别进入相应的一至九级预热器中,用来预热矿浆,末级自蒸发器出来的矿浆与一洗沉降槽来的洗液在稀释槽内汇合,稀释后的铝酸钠溶液浓度Na2O K 160g/l,用泵送往溶出后槽停留4小时,以便脱除溶液中的硅、铁、锌等杂质,再用出料泵送往赤泥沉降车间。
一次洗液10#自蒸发器1#保温停留罐9#自蒸发器4#保温停留罐1#自蒸发器去分离沉降槽稀释槽E2回水池E1熔盐罐重油预热器溶出料浆停留罐重油重油罐溶出料浆停留罐溶出料浆停留罐稀释槽矿浆母液溶出料浆停留罐去沉降图例水蒸汽重油熔盐管道化流程图5、赤泥沉降分离及洗涤由溶出车间送来的稀释矿浆进入Φ18m 的高效深锥分离沉降槽,部分分离沉降槽溢流循环返回沉降槽与进料混合稀释,其余分离沉降溢流即粗液用溢流泵送往控制过滤的立式叶滤机,在此加入少量石灰乳(或苛化渣)作为助滤剂。
- 1、下载文档前请自行甄别文档内容的完整性,平台不提供额外的编辑、内容补充、找答案等附加服务。
- 2、"仅部分预览"的文档,不可在线预览部分如存在完整性等问题,可反馈申请退款(可完整预览的文档不适用该条件!)。
- 3、如文档侵犯您的权益,请联系客服反馈,我们会尽快为您处理(人工客服工作时间:9:00-18:30)。
活性氧化铝
生产工艺流程简介
和检查混匀效果。
细碎
碎铝土矿均化堆场
铝土矿均化堆场
至液碱贮存工段。
去原料磨
去石灰消化
2、石灰消化
从石灰贮仓运来的石灰卸入本工序的石灰缓冲仓内,经溜槽直接入化灰机。
在消化工序,石灰和水同时加入化灰机,化灰机排出的石灰乳自流入石灰乳槽,由泵送往叶滤、排盐苛化等各用点,消化渣用汽车送
往堆场堆存。
灰渣汽车运出厂去叶滤
3、原矿浆磨制
从均化堆场来的铝土矿和石灰贮仓来的石灰,经胶带输送机用卸料小车分别送入各自的磨头仓,磨头仓出料设有电子皮带称计量装置,按规定的配料比与经过计量的循环母液加入磨机。
磨矿过程采用双仓溢流型中心传动球磨机配水力旋流器流程,水旋器底流返回磨机
再磨,水旋器溢流作为合格的原矿浆进入原矿浆槽。
循环母液
中间泵池原矿浆槽
4 、管道化溶出
由原料磨工序送来的原矿浆进入预脱硅槽,进行加热预脱硅,然后用压力为10~12MPa的高压隔膜泵送入溶出系统,料浆首先经脉冲缓冲器进入一 ~ 九级用二次蒸汽间接加热的套管预热器和第十一级用熔盐间接加热的套管加热器,温度从85℃预加热至280℃,再经
保温停留罐保温停留45分钟,使矿石中的氧化铝充分溶出。
溶出矿浆经十级矿浆自蒸发器闪蒸,使温度从280℃降至126℃,十级自蒸发
器产生的二次蒸汽分别进入相应的一至
九级预热器中,用来预热矿浆,末级自
蒸发器出来的矿浆与一洗沉降槽来的洗
液在稀释槽内汇合,稀释后的铝酸钠溶
液浓度Na2O K 160g/l,用泵送往溶出后
槽停留4小时,以便脱除溶液中的硅、铁、
锌等杂质,再用出料泵送往赤泥沉降车间。
一次洗
液
10#
自
蒸
发
器
1#
保
温
停
留
罐9#
自
蒸
发
器
4#
保
温
停
留
罐
1#
自
蒸
发
器
去分离沉降槽稀释槽
E2
回水池E1
熔盐罐
重
油
预
热
器
溶
出
料
浆
停
留
罐
重
油
重
油
罐
溶
出
料
浆
停
留
罐
溶
出
料
浆
停
留
罐
稀
释
槽
矿浆
母液
溶
出
料
浆
停
留
罐
去沉降
图例水
蒸汽
重油
熔盐管道化流程图
5、赤泥沉降分离及洗涤
由溶出车间送来的稀释矿浆进入Φ18m 的高效深锥分离沉降槽,部分分离沉降槽溢流循环返回沉降槽与进料混合稀释,其余分离沉降溢流即粗液用溢流泵送往控制过滤的立式叶滤机,在此加入少量石灰乳(或苛化渣)作为助滤剂。
过滤机滤液称为精液,经精液槽再用泵送往分解车间。
叶滤机的滤饼流入滤饼槽加上二次洗液及加入氢氧化铝洗
液经底流泵送往Φ22m的高效深锥洗涤沉降槽。
一洗沉降槽的溢流称为赤泥洗液送往溶出车间稀释槽。
一洗沉降槽底流用底流泵送二洗,赤泥共四次洗涤,设计采用反向洗涤流程。
最后一次洗涤沉降槽底流送到赤泥泵房,用高压泵送至赤泥压滤车间,经压滤机压干后用汽车运输至赤泥堆场堆存。
合成絮凝剂在絮凝剂制备车间制备
后用计量泵送到相应的沉降槽。
赤泥贮槽
返回三洗、四洗槽
滤液槽板框压滤机
干赤泥
去赤泥堆场
粗
液
去
叶
滤
滤饼槽
精液槽立式
叶滤机
滤饼槽
精液槽
斜溜槽
去精液板式热交换器
6、分解、分级及种子过滤
由控制过滤来的精液温度约105℃,进入板式热交换器与分解母液进行热交换。
分解母液温度从50~55℃升至70~72℃后,送到蒸发车间的原液槽。
精液从105℃降至60~62℃,送至晶种槽中与AH晶种混合。
混合浆液送至分解首槽。
从分解首槽经槽间溜槽依次自流到最后一个分解槽,从而完成氢氧化铝的结晶长大过程。
最后一个分解槽
则作为浆液缓冲槽,多余的浆液用小循环泵返回到前一个槽中。
分解倒数第三槽的部分分解浆液经母液稀释后送至槽顶的水力旋流器进行分级,分级底流作为产品送到氢氧化铝成品过滤工段,分级溢流返回最后两个分解槽。
氢氧化铝浆液从倒数第二槽上部自流到种子过滤机过滤,浆液经立盘过滤机分离,滤饼卸入晶种槽中。
分解母液
进入真空系统,经真空受液槽分离后进入到锥形母液槽中,
母液在锥形槽中进一步澄清使溶液中的固体悬浮物降到2g/l以下。
锥形槽溢流进入母液贮槽,经母液泵送到精液热交换器提温后再送往蒸发车间。
分解时间45小时以上,为了提高精液产出率,在分解槽中部设有宽流道板式热交换器,作为中间降温装置。
6#
分解分
级
5# 1#
来自晶种槽的AH料浆
精板式热交换器
液循循
环环
水水
母液去蒸发
去晶种槽与AH晶种混合来自过滤工序的分解母液
锥形母液槽
返回分解末槽
晶种槽
母液槽去旋流器调整
进料固含
去精液板式热交换
氢氧化铝仓
氢氧化铝成品AH
强滤液槽
去赤泥洗涤一洗槽
7、蒸发
经板式热交换器提温后的分解母液(本车间称为蒸发原液)进入蒸发车间的锥形原液槽,原液槽锥底沉积的氢氧化铝细颗粒用料浆泵送回分解车间过滤处理。
原液槽中大部分母液(约78%)用蒸发进料泵送入Ⅳ效、Ⅵ效蒸发器的循环泵入口,Ⅳ效、Ⅵ效分离器的蒸发原液进料量相同。
另有22%。