05 加热炉的生产率和热效率
影响加热炉效率因素分析与整改措施
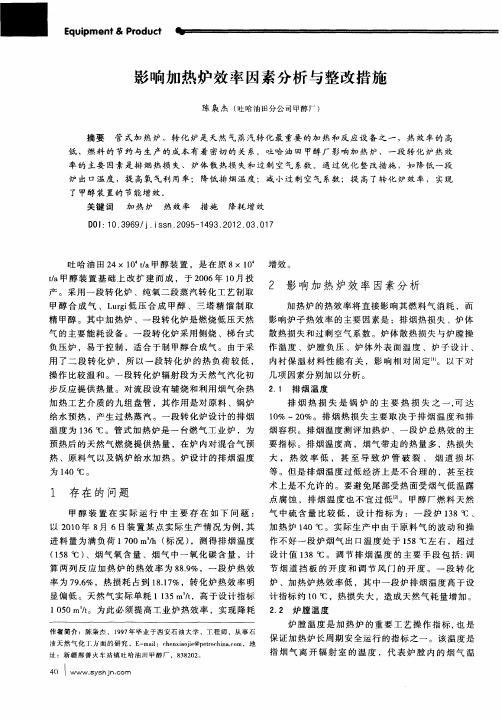
预热 后 的天然 气燃 烧提 供热 量 ,在 炉 内对混 合气 预 要指 标 。排 烟温 度高 ,烟 气带走 的热量 多 ,热损 失 热 、原料 气 以及 锅炉 给水加 热 。炉设计 的排 烟 温度 大 ,热 效 率 低 , 甚 至 导 致 炉 管 破 裂 、 烟 道 损 坏
为 1 0℃。 4
作 者 简 介 :陈 枭 杰 , 19 年 毕 业 于 西 安 石 油 大 学 ,工 程 师 ,从 事 石 97 油 天 然 气 化 工 方 面 的 研 究 ,E ma : hn ine 0hn . m,地 — i exaj @p ciae l i o
址 :新疆 鄯 善 火 车 站 镇 吐 哈 油 } 甲 醇 厂 ,8 8 0 。 f i 3 2 2
. 步反 应提 供热 量 。对流 段设 有辅 烧 和利 用烟 气余 热 2 1 排 烟 温 度
加热 工艺 介质 的九组盘 管 ,其作 用 是对 原料 、锅 炉
排 烟 热 损 失 是 锅 炉 的 主 要 热汽 。一 段转 化炉设 计 的排 烟 1% ~2 %。排烟 热 损 失 主要 取 决 于排 烟 温度 和 排 0 0 温度 为 16o 3 C。管式 加热 炉是 一 台燃 气工 业 炉 ,为 烟容 积 。排 烟温 度测评 加 热炉 、一 段炉 总热 效 的主
率的 主要 因素 是排 烟 热损 失 、 炉体 散 热损 失和 过 剩 空气 系数 。通 过优 化 整改措 施 ,如 降低 一段 炉 出 E温 度 ,提 高氧 气 利用 率; 降低排 烟温度 ; 减 小过 剩空 气 系数 ; 提 高 了转 化 炉 效率 , 实现 / 了甲醇 装 置的节 能增效 。 关键 词 加 热 炉 热 效率 措 施 降耗 增效
等 。但 是排 烟温 度过 低经 济上 是不 合 理 的 ,甚 至技
提高炼油作业五区加热炉热效率解析
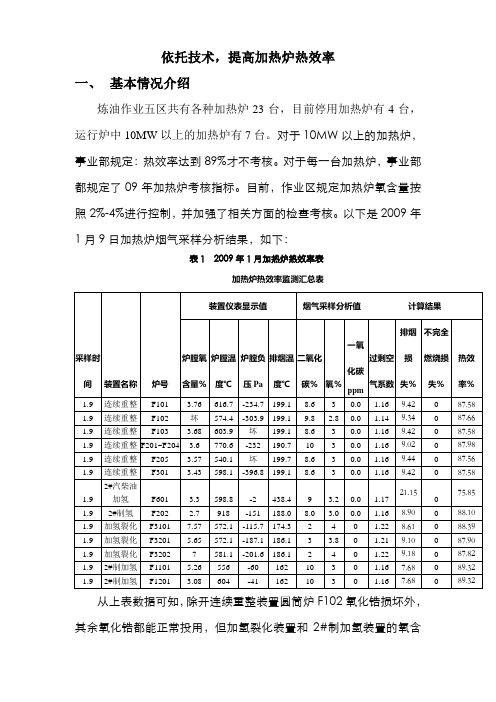
依托技术,提高加热炉热效率一、基本情况介绍炼油作业五区共有各种加热炉23台,目前停用加热炉有4台,运行炉中10MW以上的加热炉有7台。
对于10MW以上的加热炉,事业部规定:热效率达到89%才不考核。
对于每一台加热炉,事业部都规定了09年加热炉考核指标。
目前,作业区规定加热炉氧含量按照2%-4%进行控制,并加强了相关方面的检查考核。
以下是2009年1月9日加热炉烟气采样分析结果,如下:表1 2009年1月加热炉热效率表加热炉热效率监测汇总表从上表数据可知,除开连续重整装置圆筒炉F102氧化锆损坏外,其余氧化锆都能正常投用,但加氢裂化装置和2#制加氢装置的氧含量都已超标。
连续重整装置所有加热炉炉膛负压显示问题较多,不是显示损坏便是负压值过大。
各套装置加热炉的排烟温度普遍过高,导致没有一台加热炉符合事业部考核指标。
二、存在问题由上可知,目前作业区加热炉存在以下几个问题:一是部分氧化锆损坏,有待维护保养单位进行修复投用;二是存在内操对加热炉调节不及时,当操作工况发生变化时,会出现DCS氧含量指示超标;三是连续重整装置炉膛负压计指示都有问题,不是负压显示过大就是指示坏,需要对加热炉负压计进行仔细检查,通过核对负压指示值来判断是负压计损坏还是加热炉确实操作上存在着问题。
四是各个炉子的排烟温度普遍超高,最终加热炉热效率没有一台是合格的。
总而言之,最需要解决一个问题是各个加热炉的氧含量和排烟温度是否还有继续降低的空间。
四、改进方向根据加热炉热效率反平衡计算公式,热效率η=1-q1-q2-q3-q4,式中q1、q2、q3、q4分别为排烟热损失、化学不完全燃烧热损失、机械不完全燃烧热损失和炉墙散热损失。
其中排烟热损失主要由过剩空气系数α和排烟温度t决定,α和t越低,排烟损失相对越小,热效率越高;同时过剩空气系数还和不完全燃烧热损失有关;炉墙散热损失和炉衬好坏密切相关,但只有通过检修才能彻底改进。
而对于运行中的加热炉来说,降低α和t才是提高加热炉热效率的主要方向。
浅谈提高加热炉热效率的方法
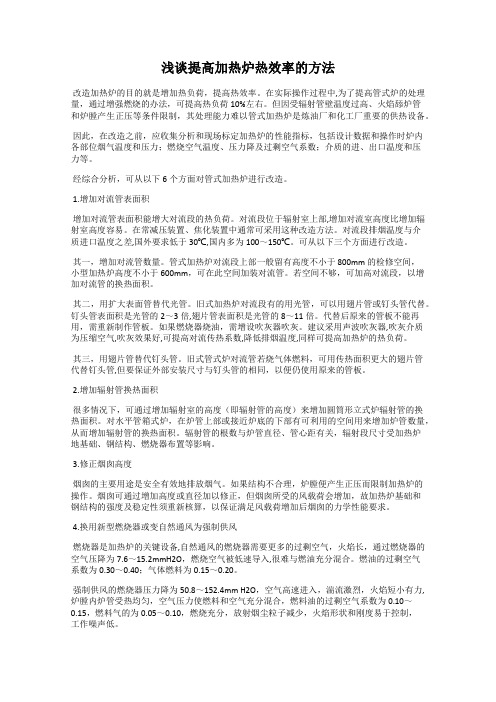
浅谈提高加热炉热效率的方法改造加热炉的目的就是增加热负荷,提高热效率。
在实际操作过程中,为了提高管式炉的处理量,通过增强燃烧的办法,可提高热负荷10%左右。
但因受辐射管壁温度过高、火焰舔炉管和炉膛产生正压等条件限制,其处理能力难以管式加热炉是炼油厂和化工厂重要的供热设备。
因此,在改造之前,应收集分析和现场标定加热炉的性能指标,包括设计数据和操作时炉内各部位烟气温度和压力;燃烧空气温度、压力降及过剩空气系数;介质的进、出口温度和压力等。
经综合分析,可从以下6个方面对管式加热炉进行改造。
1.增加对流管表面积增加对流管表面积能增大对流段的热负荷。
对流段位于辐射室上部,增加对流室高度比增加辐射室高度容易。
在常减压装置、焦化装置中通常可采用这种改造方法。
对流段排烟温度与介质进口温度之差,国外要求低于30℃,国内多为100~150℃。
可从以下三个方面进行改造。
其一,增加对流管数量。
管式加热炉对流段上部一般留有高度不小于800mm的检修空间,小型加热炉高度不小于600mm,可在此空间加装对流管。
若空间不够,可加高对流段,以增加对流管的换热面积。
其二,用扩大表面管替代光管。
旧式加热炉对流段有的用光管,可以用翅片管或钉头管代替。
钉头管表面积是光管的2~3倍,翅片管表面积是光管的8~11倍。
代替后原来的管板不能再用,需重新制作管板。
如果燃烧器烧油,需增设吹灰器吹灰。
建议采用声波吹灰器,吹灰介质为压缩空气,吹灰效果好,可提高对流传热系数,降低排烟温度,同样可提高加热炉的热负荷。
其三,用翅片管替代钉头管。
旧式管式炉对流管若烧气体燃料,可用传热面积更大的翅片管代替钉头管,但要保证外部安装尺寸与钉头管的相同,以便仍使用原来的管板。
2.增加辐射管换热面积很多情况下,可通过增加辐射室的高度(即辐射管的高度)来增加圆筒形立式炉辐射管的换热面积。
对水平管箱式炉,在炉管上部或接近炉底的下部有可利用的空间用来增加炉管数量,从而增加辐射管的换热面积。
提高加热炉效率措施及改造思路

提高加热炉效率措施及改造思路摘要:油田加热系统是油田的耗能大户,提高加热炉的效率是实施油田节能战略的关键。
油田开发20余年,由于产能递减,早期安装的加热炉部分出现负荷偏低、加热效率下降、腐蚀结垢严重等问题,因此,探讨加热系统的特点及寻求对应的效率措施成为当下油田必须实行的重要任务。
结合加热系统现状,对影响加热炉效率的因素进行分析,通过对近年在油田加热炉所采用的提高炉效措施的探讨和总结,对加热炉提高炉效潜力及技术的应用提出初步思路。
关键词: 加热炉;提高效率;措施;技术改造1 加热炉运行现状目前,大庆油田建有各类燃气加热装置包括有管式加热炉(高效炉)、火筒式直接加热炉(二合一、四合一、五合一、脱水加热炉、水套炉)、真空加热炉及锅炉等。
2 影响加热炉效率因素分析加热炉是油田的主要耗能设备。
因此,尽可能地提高加热炉的效率是油田节能的重要目标之一。
造成部分加热炉炉效偏低的因素主要有以下几个方面。
2.1 部分加热炉使用时间较长,加热炉损耗较大,热效率较低据统计,加热炉中运行时间在 11 年以上的有59台,占集输系统加热炉总数的47.2%,其中火筒炉42台,占该部分加热炉的71.1%。
该部分加热炉经过长时间的运行,普遍存在火筒及烟管腐蚀老化严重,各类故障发生频率高,导致加热炉损耗较大,炉效偏低。
2.2 无法保证加热炉的运行状态达到最佳1)部分加热炉的参数设置不合理,空气过剩系数大,带走的热量也大,加热炉效率低;空气过剩系数小,燃料不能充分燃烧,加热炉效率低。
大部分加热炉燃烧器属于自动控制,只能依靠厂家调设,导致不能及时调整合理的燃气配比,影响了加热炉的效率。
2)个别加热炉排烟温度过高时,由于缺乏加热炉检测仪器及相关的技术人员,不能及时调节烟道挡板,影响了加热炉的效率。
3)由于加热炉工况的特殊性决定其需要定期维护保养,其中对燃烧器火嘴的维护工作是保证加热炉燃烧效果的重要环节,尤其是使用湿气的加热炉燃烧器火嘴,长时间运行火嘴容易结焦或腐蚀,如不及时清理或维修,必然会导致燃烧效果差,甚至偏烧,影响加热炉的系统效率,同时造成能源浪费。
炉子热效率计算说明

公司加热炉热效率组态说明
热效率=(1-q 烟-q 散)×100%
其中:
q 散—散热损失百分比,在本式中取3%;
q 烟—排烟热损失百分比,通过计算求得,计算公式如下
q 烟=———————————————————————————
其中: a —过剩空气系数,通过计算求得,计算公式如下
a =———— 其中:O 2—烟气中氧含量百分数,本数值从氧化锆仪表中读取,
如为5%,则式中代入5。
标准规定烟气氧含量测量位置应该为空预器出口,但公司生产实际中氧化锆全部装在辐射段出口,因此本测试以辐射段出口近似代替。
t g —排烟温度,本数值从温度仪表中读取,单位℃。
CO —烟气中CO 含量,单位ppm ,本数值无现场测量仪表,请仪表组态设置人工输入,由装置工程师输入初值,可参照上月公司热效率监测数据中的CO 含量,每月输入一次。
(0.006549+0.032685a )(t g +1.3475×10-4 t g 2)-1.10+(4.043a-0.252)×10-4
CO 100 21+0.116O 2 21—O 2。
管式加热炉的热量各参数的计算和确定

管式加热炉的热量各参数的计算和确定在前面我们已经介绍了管式加热炉的一些基本概念和热量参数的计算与确定,包括燃气燃烧热效率、传导传热系数和辐射传热系数的计算方法。
接下来继续介绍其他热量参数的计算与确定。
首先是管式加热炉的热损失。
热损失指的是炉壁和烟道中的热量损失,它们会导致加热炉的热效率下降。
炉壁的热损失可以通过炉壁的传导传热计算得到,公式如下:炉壁热损失=(T_f-T_a)/R_w其中,T_f为炉内壁温度(K),T_a为炉外壁温度(K),R_w为炉壁导热系数(W/m^2K)。
烟道的热损失可以通过烟道的散热公式计算得到,公式如下:烟道热损失=Q_g*C_g*(T_g-T_a)其中,Q_g为燃气流量(kg/s),C_g为燃气的比热容(J/kgK),T_g为燃气出口温度(K),T_a为大气温度(K)。
其次是管式加热炉的燃气进口温度。
燃气进口温度对加热炉的热效率影响较大。
一般来说,燃气进口温度越高,炉壁会受到更高的温度冲击,容易造成炉膛内部结构的破坏。
因此,燃气进口温度一般控制在一定范围。
最后是管式加热炉的炉膛温度。
炉膛温度对加热炉的生产效率和产品质量有很大影响。
一般来说,炉膛温度过低会导致加热不均匀,产品质量下降;而炉膛温度过高则会导致燃烧不完全,燃气的利用率降低。
炉膛温度的确定可以通过燃气进口温度、燃气流量和传热时间计算得到,公式如下:炉膛温度=[(Q_g*H_c*T_g)+(Q_p*H_p*T_p)]/(Q_g*H_c+Q_p*H_p)其中,Q_p为介质流量(kg/s),H_c为燃气的比热容(J/kgK),T_p为介质进口温度(K),H_p为介质的比热容(J/kgK)。
综上所述,管式加热炉的热量各参数的计算和确定需要考虑燃气燃烧热效率、传导传热系数、辐射传热系数、热损失、燃气进口温度和炉膛温度等因素。
通过对这些参数的计算和调整,可以提高加热炉的热效率和生产效率,同时保证产品质量。
运转中的炼油厂加热炉热效率及燃料用量的计算
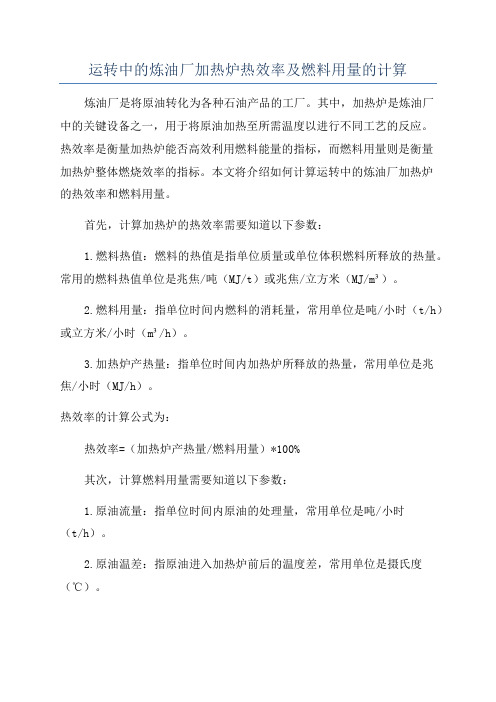
运转中的炼油厂加热炉热效率及燃料用量的计算炼油厂是将原油转化为各种石油产品的工厂。
其中,加热炉是炼油厂中的关键设备之一,用于将原油加热至所需温度以进行不同工艺的反应。
热效率是衡量加热炉能否高效利用燃料能量的指标,而燃料用量则是衡量加热炉整体燃烧效率的指标。
本文将介绍如何计算运转中的炼油厂加热炉的热效率和燃料用量。
首先,计算加热炉的热效率需要知道以下参数:1.燃料热值:燃料的热值是指单位质量或单位体积燃料所释放的热量。
常用的燃料热值单位是兆焦/吨(MJ/t)或兆焦/立方米(MJ/m³)。
2.燃料用量:指单位时间内燃料的消耗量,常用单位是吨/小时(t/h)或立方米/小时(m³/h)。
3.加热炉产热量:指单位时间内加热炉所释放的热量,常用单位是兆焦/小时(MJ/h)。
热效率的计算公式为:热效率=(加热炉产热量/燃料用量)*100%其次,计算燃料用量需要知道以下参数:1.原油流量:指单位时间内原油的处理量,常用单位是吨/小时(t/h)。
2.原油温差:指原油进入加热炉前后的温度差,常用单位是摄氏度(℃)。
3.加热炉效率:指加热炉将燃料的热能转化为原油的热能的比例,常用百分比表示。
燃料用量的计算公式为:燃料用量=原油流量*原油温差*加热炉效率*燃料热值最后,我们来举一个计算实例来说明如何根据以上参数计算炼油厂加热炉的热效率和燃料用量。
假设炼油厂的加热炉每小时处理1000吨原油,原油进入加热炉前后的温度差为100℃,燃料的热值为35MJ/m³,加热炉效率为75%。
首先,我们计算燃料用量:燃料用量=1000t/h*100℃*75%*35MJ/t=1000t/h*100℃*0.75*35MJ/t然后,我们计算加热炉的产热量:最后,我们计算热效率:热效率=(加热炉产热量/燃料用量)*100%=100%所以,该炼油厂的加热炉热效率为100%,即能够高效利用燃料能量。
需要注意的是,以上计算结果仅为理论值,实际情况可能还受到其他因素的影响,如设备磨损、能量损失等。
提高加热炉热效率的方法论析
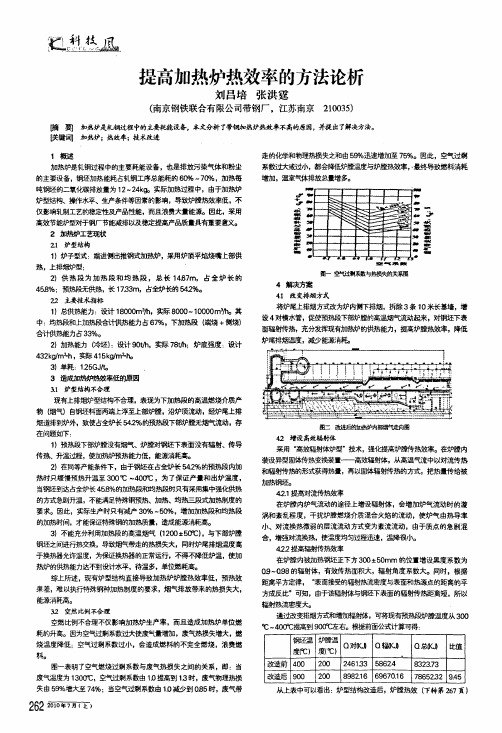
跫塑龃提高加热炉热效率的方法论析刘昌培张洪霆(南京钢铁联合有限公司带钢厂,江苏南京210035)c}i眚訇加热炉是轧钢过程中的主要耗能设备,奉文分析了带钢加热炉热效率不高的原因,并提出了解决方法。
鹾-攘词加热炉;熟效率;技术改进1概述加热炉是轧钢过程中的主要耗能设备,也是排放污染气体和粉尘的主要设备,钢坯加热能耗占轧钢工序总能耗的60%-70%,加热每吨钢坯的二氧化碳排放量为12—24kgo实际加热过程中,由于加热炉妒型结构、操作水平、生产条件等因素的影响,导致炉膛热效率f匠,不仅影响轧制工艺的稳定性及产品性能,而且浪费大量能源。
因此,采用高效节能炉型对于钢厂节能减排以及稳定提高产品质量具有重要意义。
2加热炉工艺现状21炉型结构1)炉子型式:端迸侧出推钢式加热炉,采用炉顶平焰烧嘴上部供热,上排魍《户型;2)供熟段为加热段和均热段,总长14.67m。
占全炉长的45B%:预热段无供热,长1733m,占全炉长的542%。
2.2主要教术指标1)总供热能力:设计18000m狮,实际8000一10000m3/ho其中:均热段和上加热段合计供热能力占67%,下加热段(端烧+侧烧)舍{十供热能力占33%。
2)加热能力(冷坯):设计90t/h,实际78t/h:炉底强度:设计432kg/mⅫ,实际415kg/m2.ho3)单耗:125G J/t o3造成加热炉热皴j孽f氏的原因3L1炉型结构不合理现有上排烟炉型结构不合理,表现为下加热段的高温燃烧介质产物(烟气)自钢坯料面两端上浮至上部炉膛,沿炉顶流动,经炉尾上排烟道排到炉外,致使占全炉长542%的预热段下部炉膛无烟气流动,存在问题如下:1)预热段下部炉膛没有魉气、炉膛对钢坯下表面没有辐射、传导传热、升温过陧’使加靴燃能力低,能源消耗高。
2)在同等产能条'FI T,由于钢坯在占全妒长542%的预热段内加热时只缓慢预热升温至300℃一400佗,为了保证产量和出炉温度,当钢坯到达占全炉长458%的加热段和均热段时只有采用集中强化供热的方式急剧升温,不能满足特殊钢预热、加热、均热三段式加热制度的要求。
- 1、下载文档前请自行甄别文档内容的完整性,平台不提供额外的编辑、内容补充、找答案等附加服务。
- 2、"仅部分预览"的文档,不可在线预览部分如存在完整性等问题,可反馈申请退款(可完整预览的文档不适用该条件!)。
- 3、如文档侵犯您的权益,请联系客服反馈,我们会尽快为您处理(人工客服工作时间:9:00-18:30)。
热支出 出炉废气带走热 化学不完全燃烧热 机械不完全燃烧热 砌体散热
KJ/h
%
燃料化学热
燃料物理热 空气物理热 金属氧化放热 金属物理热
Q1
二、炉膛对流给热的分析 炉气以对流方式传给金属的热量 Q=α (tg-tm) Am 在高温炉中,如一般钢坯的加热炉,辐射传热占主要的地位,对 流所占的比例小得多,大约只有5%。但是在低温炉中(700~800℃ 以下),辐射传热大大减弱,如在540℃时的辐射给热量不及1200℃ 时的1/10,这时对流起着主要作用。 当气体与固体表面发生对流换热时,由于固体表面附近有层流边 界层,边界层内的传热只是传导,热阻较大,要强化对流给热,必须 减小边界层的热阻。加大流速是使边界层厚度减小的根本措施。为此, 出现了称为喷流加热(或冲击加热) 在中低温的炉子内,加强对流换热的方法是借助与鼓风机或风扇, 加强炉气的循环流动。例如带钢退火的罩式炉内,带钢成卷放在罩内 加热与冷却,即使带钢卷得很紧,层与层之间仍有气隙,加热速度很 慢,但如果把带钢卷用框架架空,让热量也能沿轴向传递,并在内罩 引入可控气氛安装风扇,进行强制循环,则加热时间都可以大大缩短。
5.3 炉子热平衡
编制炉子热平衡,对于炉子设计和管理都是不可缺少的。在设计中 可以通过热平衡计算,确定炉子的燃料消耗量;在工作中的炉子,也可 以根据实测数据编制热平衡,来检验炉子的热效率。 热平衡的编制对于连续操作的炉子(如连续加热炉),是按单位时 间来计算的,单位是KJ/h;对于间歇操作的炉子(如一些室状炉),可 以按一个周期来计算。 热平衡包括热量的收入和支出。 一、热量的收入 ①燃料的化学热 Q=BQ低用 B--燃料消耗量,Kg/h或Kg/m3 ② 空气预热带入的物理热 Q=BC燃t燃 ③空气预热带入的物理热 Q=BnL0C空t空 ④金属氧化放出的热量 Q=5652Ga G--炉子产量;a--金属烧损率 ⑤金属带入的物理热 Q=GC金t金
二、热量的支出 ①金属加热所需的热 Q = G ( H2-H1 ) ②出炉废气带走的热 Q= BVnC废t废 ③燃料的化学不完全燃烧热损失
Q BV n ( Q CO p co 100 QH PH
2 2
...)
100
④燃料的机械不完全燃烧损失
Q=KBQ低用
K--机械不完全燃烧系数
⑤经过炉子砌体的散热损失
Q2 Q3 Q4 Q5
70~100 金属加热所需热
Q1’
Q2 ’ Q3 ’ Q4 ’ Q5 ’
10~50
30~80 0.5~3 0.2~5 2~10
炉门及孔的辐射热
炉门及孔逸气的热 水冷构件的吸热 其它热损失 热收入总和 ∑Q收入 100 热支出总和
Q6’
Q7 ’ Q8 ’ Q9 ’ ∑Q支出
0~4
0~5 0~15 0~10 100
5.4 加热炉的燃耗和热效率
加热炉的燃耗和热效率,是评价炉子加热工作的重要指标。
一、单位燃料消耗量
单位燃料消耗量,是指加热单位质量产品所消耗的燃料量。由于燃 料的发热量不同,不便于比较,因此常用单位燃耗的概念来表示。
b BQ G
低
(kJ/h)
有时也把燃耗折算成标准燃料消耗量,即每单位质量产品所用标准燃料
P 1000 G A G 炉子的小时产量, A --炉底布料面积。 t / h;
加热炉是服务于轧机的, 一般炉子的设计产量总要稍大 于轧机的产量,以免经常出现 不能及时供给热坯的待热现象。
二、影响炉子生产率的因素
1. 炉型结构的影响 加热炉总的发展趋势是向大型化、多段化、机械化、自动化方 向发展。 旧炉型的改造一般要从以下方面着手:①扩大炉膛,增加产量; ②改进炉型尺寸,使之更合理,加快钢的供热,提高炉子的生产率 ; ③减少炉子的热损失。如采用耐火可塑料包扎水管、采用无水冷滑轨 等。 2. 燃烧条件和供热条件 ①热负荷(炉子的供热强度,KJ/h)增大,产量必然增大; ②连续式加热炉提高供热强度的重要措施是增加供热点,扩大 加热段和提高加热段炉温,缩短预热段使废气出炉温度相应 提高
Q C gwn [( Tg 100 ) (
4
Tm 100
) ]
4
g (1 g )[ m g (1 m )]
一、炉膛辐射热交换分析 ①金属的黑度(εm)不是人们可以控制的因素,无法通过它去影响 炉子Cgwm; ②由图3-26可以明显地看出,在εg=0.4以下,随炉气黑度的增 长,到来辐射系数值明显增加,但εg>0.4, εg对Cgwm影响越 来越小。一般炉子条件下,燃烧天然气、重油、烟煤时都是辉 焰,所以不必考虑如何提高炉气黑度去影响炉膛热交换。
三、提高炉子热效率降低燃耗的途径 1. 减少出炉废气从炉膛带走的热量 ①在保证燃料完全燃烧的前提下,应尽可能地降低空气消耗系 数,以提高燃烧温度,减少废气量; ②要注意炉子的密封问题,控制炉底微正压,防止吸入冷风,增 加烟气量并降低温度;
③要控制合理的废气温度。在生产率、热效率和单位燃耗之间,有 一个合理热负荷的问题,这个特征如图所示。 2. 回收废热用以预热空气、煤气; 3. 减少冷却水带走的热量; 5. 加强管理与合理调度。 4. 减少砌体散热;
第五章 加热炉的 生产率和热效率
铜 陵 学 院
5.1 加热炉的生产率
一、炉子的生产率
单位时间内所加热出来的温度达到要求的金属锭或金属坯的产量 称为炉子生产率。其单位为:t/h。 对于连续加热炉和大多数室状炉,单位生产率指每平方米布料 面积上每小时的产量,单位是Kg/(m2·h)。加热炉的单位生产率(P) 也称为炉底强度,它是炉子最重要的生产指标之一。
Q 3 . 6 ( t1 t 2 ) A s1 s2
1
2
... 0 . 06
⑥炉门及开孔的辐射热损失 Q=qAψ ψ--炉门开启时间的比例 q--单位面积炉门向外辐射的热量 ⑦炉门及开孔逸气的热损失 Q=V0tC ⑧炉子水冷构件的吸热损失 Q=G水(H’-H) 这些项目有的可以计算,有的则很难计算,只能作大致的估算。 三、热平衡方程和热平衡表 根据能量不灭原则,热收入各项的总和应等于热支出各项的总和。 即 ∑Q收入= ∑Q支出
③角度系数φ对Cgwm也有影响,实际上φ的变化不大,一般在0.3~
0.5。
④金属受热面积; ⑤平均辐射温压
( Tg 100 ) (
4
Tm 100
)
4
连续加热炉炉气温度和金属温度的变 化如图所示。 钢坯入炉温度tm’和出炉温度tm’’,取决 于具体条件和加热工艺要求,变化的余 地不大,对炉子生产率难以施加多少影 响。因此影响因素只剩下燃烧温度tg’和 废气温度tg’’ 废气温度越高,平均辐射温压越大, 金属获得的差额热量也越大。生产上提 高废气温度一靠加大热负荷,二是减少 炉膛散热损失。但是废气温度越高,带 走的热量越多,炉子的热效率降低
b BQ
低
(Kg 标准燃料
/h)
29270 G
一些常见的钢加热炉的燃耗指标参见表5-3
二、炉子的热效率 炉子的热效率,指加热金属的有效热占供给炉子的热量的百分率
金属加热所需的热 燃料燃烧的化学热 100 %
一般加热炉的热效率大致的波动范围如下: 均热炉 η =30~40%; 室状炉 η =20~40%; 连续加热炉 热处理炉 η =30~50%; η =5~20%;
③提高热负荷的一个重要先决条件是必须保证燃料完全燃烧; ④应当注意改进燃烧装置。 3. 钢料入炉条件 ①所加热的钢坯越厚,所需的加热时间越长,炉子生产率越低; ②为了提高生产率应设法增加钢坯的受热面积; ③钢料入炉温度越高,加热时间越短,炉子生产率越高,所以应 设法提 高炉子的热装比; 4. 工艺条件的影响
在制定加热工艺时,要考虑选择合理的加热温度、加热速度和温 度的均匀性。
热处理工艺多半要求有严格的升温速度与冷却速度,此外为了相 变的需要,常常要有保温时间,所以热处理炉生产率都比较低。
5.2 炉膛热交换的分析
金属在炉膛辐射热交换中所得到的热量为:
C gwn 5 . 67 g m [1 (1 g )]