表面处理知识
冲压模具的表面处理技术

冲压模具的表面处理技术1. 引言冲压模具是在工业生产中广泛应用的一种工具。
它用于将金属板材等材料加工成所需形状的零件。
冲压模具的表面处理技术对于提高模具的耐磨性、延长使用寿命、增加工件的精度和减少摩擦阻力等方面起着至关重要的作用。
本文将介绍几种常用的冲压模具表面处理技术及其优缺点。
2. 高温气体渗氮高温气体渗氮是一种常用的冲压模具表面处理技术。
该技术通过在高温下将氮气渗入模具表面,使其形成氮化层。
这种氮化层具有高硬度、良好的耐磨性和抗腐蚀性能。
同时,氮化层能够降低摩擦系数,减少摩擦损失,提高模具的使用寿命。
然而,高温气体渗氮技术存在一些缺点。
首先,该技术的成本较高,需要投资大量的设备和材料。
其次,渗氮过程中需要严格控制温度和氮气流量,以保证氮化层的质量。
因此,该技术在应用中需要一定的专业知识和技术支持。
3. 离子氮化离子氮化是另一种常用的冲压模具表面处理技术。
该技术通过在真空环境中施加高电压,使模具表面形成氮化层。
离子氮化技术具有渗层速度快、渗氮层厚度均匀等优点。
此外,离子氮化过程中还可以控制温度和离子能量,以调节氮化层的硬度和结构。
然而,离子氮化技术也有一些局限性。
首先,该技术对模具材料的要求较高,只有一些特定的金属材料才能通过离子氮化得到理想的氮化层。
其次,由于离子氮化需要在真空环境下进行,因此设备的成本较高,操作难度较大。
4. 涂层涂层技术是一种简单且广泛应用的冲压模具表面处理技术。
该技术通过在模具表面涂覆一层特殊的涂层材料,以提高模具的表面硬度、耐磨性和抗腐蚀性能。
常见的涂层材料包括钛、钨、碳化物等。
涂层技术具有成本较低、适用性广等优点。
此外,涂层技术还可以根据不同的需求选择不同的材料和涂层厚度,以满足不同工艺要求。
然而,涂层技术也存在一些问题。
首先,涂层的附着力和耐磨性较低,容易剥落或磨损。
其次,涂层的加工工艺复杂,需要控制好涂层的厚度和均匀性。
5. 表面喷丸处理表面喷丸处理是一种常用的冲压模具表面处理技术。
不锈钢表面处理知识
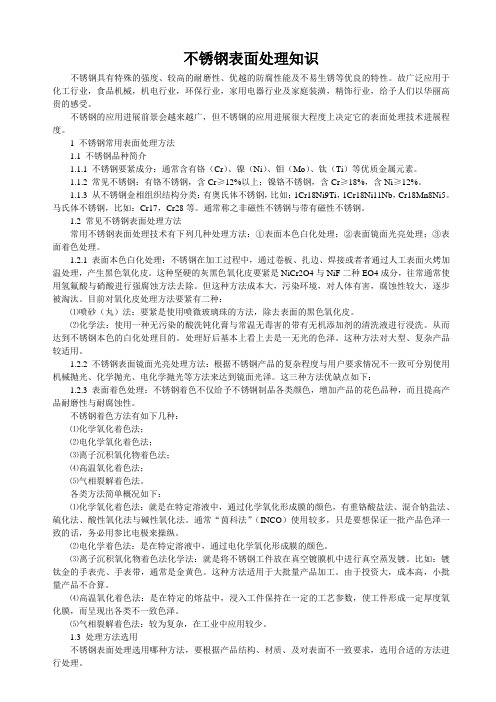
不锈钢表面处理知识不锈钢具有特殊的强度、较高的耐磨性、优越的防腐性能及不易生锈等优良的特性。
故广泛应用于化工行业,食品机械,机电行业,环保行业,家用电器行业及家庭装潢,精饰行业,给予人们以华丽高贵的感受。
不锈钢的应用进展前景会越来越广,但不锈钢的应用进展很大程度上决定它的表面处理技术进展程度。
1 不锈钢常用表面处理方法1.1 不锈钢品种简介1.1.1 不锈钢要紧成分:通常含有铬(Cr)、镍(Ni)、钼(Mo)、钛(Ti)等优质金属元素。
1.1.2 常见不锈钢:有铬不锈钢,含Cr≥12%以上;镍铬不锈钢,含Cr≥18%,含Ni≥12%。
1.1.3 从不锈钢金相组织结构分类:有奥氏体不锈钢,比如:1Cr18Ni9Ti,1Cr18Ni11Nb,Cr18Mn8Ni5。
马氏体不锈钢,比如:Cr17,Cr28等。
通常称之非磁性不锈钢与带有磁性不锈钢。
1.2 常见不锈钢表面处理方法常用不锈钢表面处理技术有下列几种处理方法:①表面本色白化处理;②表面镜面光亮处理;③表面着色处理。
1.2.1 表面本色白化处理:不锈钢在加工过程中,通过卷板、扎边、焊接或者者通过人工表面火烤加温处理,产生黑色氧化皮。
这种坚硬的灰黑色氧化皮要紧是NiCr2O4与NiF二种EO4成分,往常通常使用氢氟酸与硝酸进行强腐蚀方法去除。
但这种方法成本大,污染环境,对人体有害,腐蚀性较大,逐步被淘汰。
目前对氧化皮处理方法要紧有二种:⑴喷砂(丸)法:要紧是使用喷微玻璃珠的方法,除去表面的黑色氧化皮。
⑵化学法:使用一种无污染的酸洗钝化膏与常温无毒害的带有无机添加剂的清洗液进行浸洗。
从而达到不锈钢本色的白化处理目的。
处理好后基本上看上去是一无光的色泽。
这种方法对大型、复杂产品较适用。
1.2.2 不锈钢表面镜面光亮处理方法:根据不锈钢产品的复杂程度与用户要求情况不一致可分别使用机械抛光、化学抛光、电化学抛光等方法来达到镜面光泽。
这三种方法优缺点如下:1.2.3 表面着色处理:不锈钢着色不仅给予不锈钢制品各类颜色,增加产品的花色品种,而且提高产品耐磨性与耐腐蚀性。
表面处理知识

活塞环表面处理知识自从内燃机问世以来,其心脏部件活塞环一汽缸套这对摩擦付就一直为人所关注,想方设法提高其使用寿命。
这对磨擦付既要耐磨、又要减磨,还得磨合性能好。
耐磨、减磨、磨合这三者是互有矛盾、互相联系的一个统一体,因此完全依靠材质本身来达到这一目的是不可能的,改善环和缸套的结构也只能缓解矛盾,而不能根本解决矛盾。
但表面处理特别是复合表面处理可采用不同表面处理层去解决好各个时期不同的矛盾,确保活塞环—汽缸套的服役期达到整车的大修期。
活塞环表面处理发展速度很快,以理研(RiKen)活塞环株式会社为例,到二十一世纪初其表面处理技术有DVD;复合镀;HVOF高速氧火焰喷涂;等离子喷涂;固体润滑薄膜;气体氮化。
其中离子镀有Cr-n系和Ti-N系,复合分散镀(Cpn-200)Ni-P-co+si3N4系。
NPR 表面处理生产线有:激光处理;等离子喷涂;火焰淬火等。
如果把活塞环生产分作热加工、机加工、表面处理三个部分,则表面处理相比之下与国外先进的差距较大,好在国内这方面部分进展较快,来势较好,有待努力赶上。
一、发蓝我国上世纪六十年代初,活塞环表面处理一直以磷化、镀锡、发蓝为主,当时采用老工艺,生产率低、质量不稳定,其中发蓝工艺是将水玻璃作粘结剂的铁粉采用喷涂或滚动镀层的方法,把铁粉填入活塞环外圆面的沟槽中,随后在压力蒸气中加热至500℃左右,使之形成四氧化三铁。
它本身相当于软磨粒能帮助磨合,又能保持润滑油。
现在发蓝工艺用氧化剂加在高浓度的苛性钠水溶液中,温度为130°-150℃,活塞环浸泡5-30分钟。
它比老工艺简单、质量可靠,活塞环外圆也不用加工凹槽,且防止氧化生锈,改善初期磨合的作用有所增强。
发蓝溶液配制应控制NaOH 550-650g/L.Nano2200-250g/L工作温度147-152℃,处理时间10-20分钟。
发蓝溶液配制应先向槽中加入2/3(容积)的水。
缓慢加入计量的氢氧化纳到槽中,搅拌使之溶解,要防止氢氧化纳放热溅出。
关于铜表面钝化处理技术知识

关于铜表面钝化处理技术知识目前,铜产品在生产、储存、运输过程中发生变色,给产品的质量和外观带来了影响,因此对铜表面钝化处理已成为其加工当中的一个重要环节。
一、铜材合金表面钝化、防变色处理1.钝化处理:凯盟牌铜材钝化剂是传统酸洗工艺的高新技术,无论油垢、氧化物的厚薄,都能彻底钝化,形成镜面效果,操作起来极为方便,浸泡或超声波均可,去氧化物一次性完成而不残留,水基环保配方,符合SGS 环保要求,适合所有的黄铜、紫铜、白铜等铜合金表面的油污和氧化物的钝化。
钝化后的铜件,恢复到铜件原来的本色,且光亮如新。
2.铜材钝化防变色处理:目前,很多铜材及铜材合金本身呈碱性,极易失去电子发生氧化。
特别是铜材合金本身各种元素间存在电位差异,因而在湿热环境中极易腐蚀变色,因此铜材钝化后防止变色是表面钝化的一个重要工序。
凯盟牌铜材钝化液适用于所有铜、铜合金(黄铜、紫铜、磷铜、白铜、红铜等)、电镀铜等各种铜产品表面的防变色处理,适用于工序间或最终产品钝化处理。
使您的铜产品易变色,防氧化难的大难题得到解决,钝化处理后的铜产品在外观、颜色、光泽、尺寸、不影响导电和焊接上面不会改变这些性能,铜处理后的性能提高5-30倍,完全裸露在空气中能保持6个月至3年,根据材料不同,会有一些差异。
(中性盐雾测试标准,但因为它的材料特性不同,防蚀效果或许会有差异,)增强工件的使用寿命,配套凯盟牌铜材化学抛光液产品使用效果更佳。
二、铜及铜合金钝化技术发展当前铜材及铜材合金钝化技术的主要技术进步表现在:1.退火,钝化连续化生产技术;2.高表面质量、无污染、高效率钝化技术;3.高精度钝化后处理清刷、磨洗控制技术;4.防变色钝化技术;5.高效烘干、冷却技术;以上就是“关于铜合金与铜表面处理技术知识”的·内容,该版权最终归东莞凯盟所有,如需转载,请标明出处。
表面处理安全技术操作规程模版(三篇)

表面处理安全技术操作规程模版一、任务目标本操作规程旨在确保表面处理作业过程中的安全,预防事故及伤害的发生,并保障员工与设备的安全。
二、作业前的准备2.1. 核实表面处理作业的具体要求及技术规范。
2.2. 参与作业的所有人员须完成安全培训,并持有有效证书。
2.3. 配备个人防护装备及安全设施,如手套、护目镜、安全帽等,并确保其达到国家标准。
2.4. 检验表面处理设备及工具的完整性与安全性。
2.5. 识别作业现场的风险点和隐患,并实施相应的控制措施。
三、作业流程3.1. 表面处理作业前,应划设作业区域并设置警示标志,防止无关人员进入。
3.2. 确保表面处理设备可靠地接地,并检查其电气线路和控制系统。
3.3. 化学表面处理作业时,须选用恰当的化学品,并遵循安全操作规程进行配制及使用。
3.4. 机械表面处理作业时,要保证设备和工具的正常运转,并定期进行检查与维护。
3.5. 高温表面处理作业时,严格控制作业环境温度,并实施防火防爆措施。
3.6. 高压表面处理作业时,必须使用符合标准的高压设备,并遵守相关操作规程。
四、废弃物处理4.1. 及时分类并妥善存放废弃物,指派专人负责处理。
4.2. 含有有害物质的废弃物应存放在特殊容器中,并按照法规规定进行处理。
4.3. 废弃物处理需通过环保部门的审核与批准,禁止私自倾倒或处理。
五、事故和应急处理5.1. 若在表面处理作业过程中发生意外或紧急情况,应立即停止作业,并通知相关负责人。
5.2. 迅速组织人员疏散至安全地带,并提供必要的急救与救援。
5.3. 对事故及其原因进行详细记录和调查,并实施防止类似事故再次发生的措施。
六、定期检查与维护6.1. 定期检查和维护表面处理设备和工具,确保其安全运行。
6.2. 进行环境安全巡查,检查风险点和隐患,并及时采取控制措施。
6.3. 定期对操作人员进行培训和考核,提升他们的安全意识和操作技能。
七、符合与执行7.1. 所有参与表面处理作业的人员必须遵守本操作规程,执行安全操作流程。
关于铜表面钝化处理防护知识

关于铜表面钝化处理防护知识
针对铜表面存在的缺陷, 表面处理是一项行之有效的保护措施,因此,铜的表面处理技术不是一项单一技术, 而切切实实是一项系统工程。
表面处理的方法很多,可根据材料的不同用途采用相应的表面处理方法。
常用的工业化表面处理方法介绍如下:
一、铜清洗
清洗目的是除掉铜表面清除顽固的污垢和氧化层,还铜一个明净、光亮的表面。
二、铜抛光
铜电解抛光的表面可以轻松达到镜面效果,且因为装饰面与非装饰面的一致性,使铜档次提高,这种技术在欧洲,尤其在土耳其应用比较广泛。
三、铜保护
经过铜钝化液处理后能使铜表面及时形成一层保护性能较强的均匀的钝化膜,可适用于铝合金及铝压铸件的防腐蚀处理,有效保护金属基体、延长铜防锈或抗氧化的能力、至少可以提高10倍以上的防锈能力、提高耐盐雾测试时间、延长工件的使用寿命,本品不含六价铬、环保、安全无毒、操作、废水处理简单,使用单位成本低。
东莞市凯盟表面处理技术开发有限公司专注于铜酸洗,铜抛光,铜酸洗液,铜酸洗钝化,铜抛光液,铜钝化处理,铜表面钝化处理等服务。
以上就是对关于铜表面钝化处理防护知识的相关介绍,如需转载,请标明出处。
金属表面处理基础知识

光源照射
- 铝合金
材料厚度 (mm)
0.3
0.4
0.5
0.6
- 不锈钢
材料厚度 (mm) 0.2 0.2 0.3 0.4 0.5 0.6
打孔参数
微孔正面直径 (μm)
25-35 60-65 95-100 25-35 60-65 95-100 20-30 60-65 95-100 20-30 60-65 95-100
PVD 新颜色
Pantone 7c Pantone 405c Light silver Light gold Black Peacock blue
Light blue
Light pink
-T1 passed; - In T1 verification; - T1 preparation; - Color improvement
金属表面处理基础知识
目录 1
材料表面处理技术分类
2
冲压基础知识概述
3
金属表面处理技术介绍
材料对应表面技术概况
铝合 金
不锈钢 镁合 金 锌 合金 钛合金
液态金属
抛光、喷砂、拉丝 阳极氧化、微弧氧化、喷涂、CNC 蚀刻、激光、焊接、电镀、锻造
抛光、喷砂、拉丝、高光、漏花 PVD、电镀、ED、喷涂、CNC 蚀刻、激光、焊接
冲床
示
模具
整平送料 机
电阻焊
攻牙机
表面处理技术
前处理:抛光、喷砂、拉丝、漏花 电镀 阳极氧化 微弧氧化(MAO) 微加工(激光、蚀刻、焊接、CNC) PVD 电泳涂装(ED) 喷涂(AFP、Soft Touch、特氟龙等) 液态金属 复合金属 锻造 笔记本外壳装饰演示
抛光
喷砂
电镀原理高三知识点
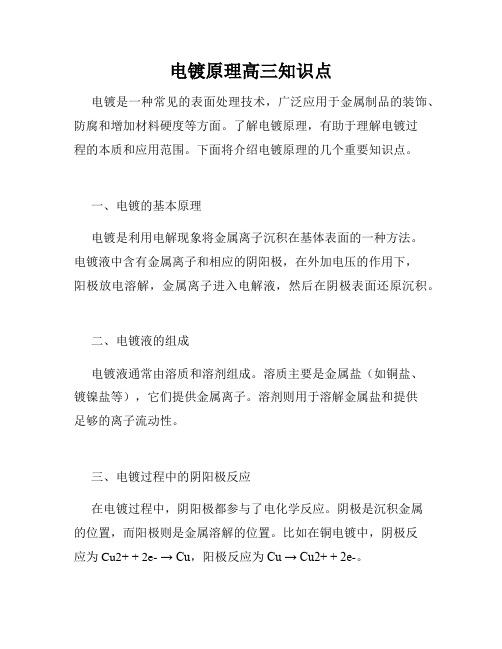
电镀原理高三知识点电镀是一种常见的表面处理技术,广泛应用于金属制品的装饰、防腐和增加材料硬度等方面。
了解电镀原理,有助于理解电镀过程的本质和应用范围。
下面将介绍电镀原理的几个重要知识点。
一、电镀的基本原理电镀是利用电解现象将金属离子沉积在基体表面的一种方法。
电镀液中含有金属离子和相应的阴阳极,在外加电压的作用下,阳极放电溶解,金属离子进入电解液,然后在阴极表面还原沉积。
二、电镀液的组成电镀液通常由溶质和溶剂组成。
溶质主要是金属盐(如铜盐、镀镍盐等),它们提供金属离子。
溶剂则用于溶解金属盐和提供足够的离子流动性。
三、电镀过程中的阴阳极反应在电镀过程中,阴阳极都参与了电化学反应。
阴极是沉积金属的位置,而阳极则是金属溶解的位置。
比如在铜电镀中,阴极反应为Cu2+ + 2e- → Cu,阳极反应为Cu → Cu2+ + 2e-。
四、电镀条件的影响因素电镀过程中,有许多因素会影响沉积质量和性能。
其中包括电流密度、温度、电镀液中金属离子浓度、PH值等。
合理调节这些因素可获得良好的电镀效果。
五、电镀的应用电镀在日常生活中有广泛的应用。
例如,汽车零件经常进行镀铬处理以增加光泽和耐腐蚀性;珠宝首饰上常见的镀金和镀银工艺,也是运用了电镀技术;另外,电子器件的制造和修复过程中也会用到金属电镀等。
六、电镀的环保问题虽然电镀技术有广泛应用,但也伴随着环境污染的问题。
电镀液中的某些物质对环境和人体健康有害。
因此,在电镀过程中,要注意环境保护和安全操作,合理使用和处理电镀液等。
总结:电镀原理是现代工业中常用的表面处理技术之一,了解电镀原理对于正确使用和应用电镀技术非常重要。
通过理解电镀的基本原理、电镀液的组成、阴阳极反应、影响电镀质量的条件、电镀的应用和环保问题等知识点,可以更好地掌握电镀技术的实质和应用范围。
希望以上内容能够对高三学生们理解电镀原理有所帮助。
- 1、下载文档前请自行甄别文档内容的完整性,平台不提供额外的编辑、内容补充、找答案等附加服务。
- 2、"仅部分预览"的文档,不可在线预览部分如存在完整性等问题,可反馈申请退款(可完整预览的文档不适用该条件!)。
- 3、如文档侵犯您的权益,请联系客服反馈,我们会尽快为您处理(人工客服工作时间:9:00-18:30)。
1 活塞环表面处理知识 自从内燃机问世以来,其心脏部件活塞环一汽缸套这对摩擦付就一直为人所关注,想方设法提高其使用寿命。这对磨擦付既要耐磨、又要减磨,还得磨合性能好。耐磨、减磨、磨合这三者是互有矛盾、互相联系的一个统一体,因此完全依靠材质本身来达到这一目的是不可能的,改善环和缸套的结构也只能缓解矛盾,而不能根本解决矛盾。但表面处理特别是复合表面处理可采用不同表面处理层去解决好各个时期不同的矛盾,确保活塞环—汽缸套的服役期达到整车的大修期。 活塞环表面处理发展速度很快,以理研(RiKen)活塞环株式会社为例,到二十一世纪初其表面处理技术有DVD;复合镀;HVOF高速氧火焰喷涂;等离子喷涂;固体润滑薄膜;气体氮化。其中离子镀有Cr-n系和Ti-N系,复合分散镀(Cpn-200)Ni-P-co+si3N4系。NPR表面处理生产线有:激光处理;等离子喷涂;火焰淬火等。如果把活塞环生产分作热加工、机加工、表面处理三个部分,则表面处理相比之下与国外先进的差距较大,好在国内这方面部分进展较快,来势较好,有待努力赶上。
一、发蓝 我国上世纪六十年代初,活塞环表面处理一直以磷化、镀锡、发蓝为主,当时采用老工艺,生产率低、质量不稳定,其中发蓝工艺是将水玻璃作粘结剂的铁粉采用喷涂或滚动镀层的方法,把铁粉填入活塞环外圆面的沟槽中,随后在压力蒸气中加热至500℃左右,使之形成四氧化三铁。它本身相当于软磨粒能帮助磨合,又能保持润滑油。现在发蓝工艺用氧化剂加在高浓度的苛性钠水溶液中,温度为130°-150℃,活塞环浸泡5-30分钟。它比老工艺简单、质量可靠,活塞环外圆也不用加工凹槽,且防止氧化生锈,改善初期磨合的作用有所增强。 发蓝溶液配制应控制NaOH 550-650g/L.Nano2200-250g/L工作温度147-152℃,处理时间10-20分钟。发蓝溶液配制应先向槽中加入2/3(容积)的水。缓慢加入计量的氢氧化纳到槽中,搅拌使之溶解,要防止氢氧化纳放热溅出。然后在搅拌下,缓慢加入计量的亚硝酸钠,待全部溶解后,补充水至液位,升温至工作温度。 溶液管理方法;根据沸腾情况,每天调整槽液:补加一定量的氢氧化纳及亚硝酸钠,一般NaOH : NaNO2约为3 :1,并及时补充液位,经常打捞槽液上的浮渣,补加水时要缓慢小心,避免产生暴沸现象。 四氧化三铁膜(发蓝)由晶体组成,它能去除钝化膜,防锈。改善初期磨合性,提高耐蚀性和润滑性。在磨合过程中,它比磷化膜磨掉要慢,具有帮助防止拉缸的作用。 发蓝对活塞环的典型用途目前为:顶环硅铬钢外圆面镀铬,侧面发蓝;刮片环外圆面镀铬,侧面发蓝,螺旋撑簧油环环体外圆面镀铬,侧面发蓝。 由上可见发蓝的典型用途为活塞环侧面的表面处理。 以镀铬后的刮片环的发蓝为例,其工艺过程为:除油 酸洗 发蓝 封闭(皂液封闭进一步提高耐蚀性和润滑性)。发蓝所用槽液:亚硝酸纳(NaNO3)150-200g/L;苛性钠(NaoH)600-800g/L,温度140-150℃,时间10-20分钟,发生下述反应: 3Fe+5NaoH+NaNo2 3Na2FeO2+H2O+NH3 亚铁酸纳进一步与氧化剂反应 6Na2FeO2+NaNO2+5H2O 3Na2Fe2O4+7NaOH+NH3 亚铁酸钠和铁酸纳在溶液中反应: Na2FeO2+Na2Fe2O4+2H2O Fe3O4+4NaOH 反应生成 四氧化三铁,当浓度超过饱和时,结晶堆积在活塞环表面,形成黑褐色厚约 2
0.5-1.5um的四氧化三铁膜。 四氧化三铁膜的检验主要是外观,要求膜层光泽均匀、颜色呈黑褐色、蓝色或黑色均可,但要一致,膜层无花斑条纹、无红色挂灰、无绿色挂霜。氧化处理代号FE,一般最小厚度为0.003um,膜层常为0.5-1.5μm。
二、磷化 1、 活塞环磷化是将活塞环放在磷酸盐溶液中浸泡,使环的表面获得一薄层不溶于水的磷酸盐膜,它的多孔结构具有吸附保油性、耐蚀性,起到防锈及易于初期磨合的作用。近代磷化层可作为某些喷涂表面处理的过渡层,也用于某些化学镀前的预处理。磷化操作方便、成本低、效果还可以,一直是活塞环常用的表面处理之一。磷化工艺分为高温磷化(>80℃)),中温磷化(50-70℃),低温磷化(<45℃=。中温磷化有冷磷化和高温磷化的一部份优点,国内外活塞环企业常采用中温磷化,目前少数活塞环企业保留着高温磷化,冷磷化是发展趋向。主要是冷磷化节约能源,降低成本、提高工作效率。磷化处理方法将从浸渍法发展为喷淋、浸喷组合法的自动化生产。磷化膜厚度从上世纪七、八十年代逐步规范为2-6μm。磷化对活塞环的典型用途目前为顶环球铁材质外圆面镀铬侧面磷化;顶环马氏体不锈钢材质外圆面气体氮化侧面磷化;二道球铁环外圆面镀铬侧面磷化;二道碳化物铸铁合成铸铁外圆面侧面均磷化;刮片环外圆面镀铬侧面磷化;螺旋撑簧油环环体马氏体不锈钢外圆面气体氮化侧面磷化。由上可见磷化的典型用途主要为活塞环侧面的表面处理。 2、 评价活塞环磷化膜应针对磷化膜不同功能用不同的评价方法进行: (1)贮油性;磷化膜由一系列大小不同的晶体组成,在晶体的连接点上形成细小裂纹的多孔结构,它使环表面具有吸附保油性,能改善初期磨合,其评价方法可借鉴缸套磷化膜的评价方法;规定每平方米磷化膜上形成一定数量和深度大小不同的微细孔,单位面积磷化膜的贮油量、承载系数等指标,具体参数待试验及多次实验修正后确定。 (2)耐蚀性;采用硫酸铜溶液点滴法或食盐水浸泡法,活塞环磷化耐蚀性的测定常采用硫酸铜溶液点滴法,因为食盐水浸泡花费时间长,硫酸铜溶液点滴的时间短。硫酸铜溶液成分为:CuSO4.5H2O 4lg/L, Nacl 33g/L, 盐酸(0.1md/L)1.3ml/L或0.5N CuSO4.5H2O 4OML.10%NaCl 20ml.0.1N HCl 0.8ml. 测定方法为:先将磷化膜用脱脂棉蘸上酒精擦洗干净,待酒精挥发后,在擦净的磷化膜上滴几滴硫酸铜溶液,溶液由天蓝色变成土黄色或土红色的时间,按时间长短评定该磷化膜耐蚀性的优劣。一般0.5-1分钟为合格;5分钟以上为优。有特殊要求的另定。凭经验外观结晶均匀细密的耐蚀性较好。采用食盐浸泡使用3%Nac溶液浸泡磷化环,一般24小时内不生锈为合格;60小时内不生锈为优,特殊要求的另定。 (3)磷化膜厚度的测量;检测仪表HCC-24电脑涂层厚度测量仪,数显式磁仪.MlkroTESTJO 显微测厚仪(分辨度为1um);也可采用脱膜称重法:试样磷化后重一试样脱膜后重/试样表面积,其中Mn系脱膜剂:H2CrO4 5og/L工作温度为75± 5℃.处理时间15分钟;Zn系脱膜剂:NaOH100g/L NaCl EDTA四钠90g/L.三乙醇胺4g/L. 工作温度75±5°.处理时间5分钟;采用千分尺测量前后环高尺寸的粗略测试。 (4)磷化膜-基材的结合强度.采用擦试法:用手擦抹不掉磷化膜为合格。 (5)外观包括色泽.致密及均匀性:要求较致密.色泽均匀,不能有挂灰.色斑.色变.沉渣.黄锈.红锈.磷化不上(花脸).磷化膜疏松.粗厚.磷化膜太薄等。 关于磷化膜作为球铁环进行复合分散镀前将石墨孔封闭的预处理及磷化作为过渡层的评价方法及标准尚末见有报导,有待研究、试验。 3活塞环磷化一般工艺流程如下: 3
除油 除锈 水洗 表调 磷化 水洗 烘干 3.1除油;活塞环在磷化前经机加工热处理,其表面或多或少沾有油污,如不清除干净,磷化溶液与环表面接触不良,影响磷化膜生成,为此磷化前应除油,一般不用强腐蚀剂,它会腐蚀环的表面,使磷化膜不致密。活塞环行业常采用化学除油剂FC-302S溶解于处理槽中,加入量控制游离碱度10-15PT,温度为50-65℃,活塞环浸泡时间视环的油污程度为5-15分钟;此外活塞环行业少量企业还采用把环放置在锯木屑中来回擦动,直到擦净油污为止。 3.2除锈;去除环表面的氧化层,以免磷化膜有锈斑。活塞环的除锈方法有喷砂及酸洗法,喷砂提高基材表面积,增加磷化结晶活性点,有利于形成致密磷化膜;酸洗法简单、成本低,但酸洗过度破坏环表面,使磷化膜粗糙,活塞环行业大都采用酸洗法,一般采用磷酸溶液,其浓度为H3PO40.8-1.2N Fe2+<20g/L.温度为室温,酸洗废液应加入工业用Na2CO3中和至PH值为6-8才能排放。活塞环酸洗时间为5-15分钟。 3.3水洗;如碱性除油剂带进磷化液,会中和游离酸产生残渣,造成磷化膜挂灰;除锈剂带进磷化液,会使游离酸升高,成膜离子减少,磷化膜粗糙不匀,甚至造成锈膜。所以要彻底水洗,一般采用二道水洗:除油 水洗 酸洗 水洗 表调……,每道洗两次。(一次流动冷水洗,一次热水洗。表调的不经水洗,直接进入磷化)。 3.4表调;活塞环经除油、酸洗,其表面受到或多或少的腐蚀,减少了磷化结晶的活性中心,使磷化膜粗糙。经过表面调整(表调),使环表面形成许多活性中心,容易形成均匀致密的磷化膜,同时可降低磷化工作温度和缩短磷化时间,对磷化膜外观、膜重、晶粒大小、耐蚀性等都有较重要的作用。活塞环磷化常用的表调剂:PL-Z剂控制PH值7.5-8,PH值过低用10%的氢氧化钠溶液调整;PH值过高用水稀释,温度<40℃,时间>15S搅拌机搅拌;PL-VMA剂先按1L40℃的水配50g剂量调成浆状,加入处理槽的清水中,搅拌机搅拌,活塞环下槽后不断摆动,温度<50℃,时间30-50秒。定时更新槽液。表调剂PL-Z用于锌系磷化;PL-VMA用于锰系磷化,使用过程中应适时补充一定量的表调剂。 上述表调剂中,以草酸(H2C2O4溶液)为主,表调后的环不经水洗,直接进入磷化液,带入的草酸对磷化质量没有妨害。活塞环不经上述表调也可采用皂化处理,皂化液配方为:20-30g/L肥皂或5g/L洗衣粉.10-15g/L碳酸钠,温度80℃,皂化时间2-3分钟。当环表面有一薄层肥皂膜时,肥皂膜阻碍生成的晶体再长大,促使新的晶核不断形成,造成磷化膜结晶细密,同时肥皂膜本身持有的碱性物质和磷化液中游离酸的作用,促使磷酸盐水解,加快了磷化过程。皂化后应洗去环表面上多余的肥皂,一般采用流水清洗+热水预热,热水温度与磷化温度相当,当环达到水温即可取出进入磷化,操作中应注意在挂具上的环不能相互碰撞损伤肥皂膜。 3.5磷化;磷化是用含有磷酸、磷酸盐和其他金属盐的溶液处理环的表面,通过化学反应产生完整的、有一定耐蚀性的磷酸盐层-磷化膜。目前用于活塞环磷化的主要是锰系磷化、锌钙系磷化、锌锰系磷化,其化学反应式主要为: 在磷化液中存在以下离子平衡:H3PO=H++H2PO4-;H2PO4-=H++HPO42-。活塞环浸入磷化液后,在环表面发生阳极Fe+2H+=Fe2++H2 ;阴极Fe2++HPO42-=FeHPO4 。 在锰系磷化中:Mn(H2PO4)2=Mn2++2H2PO4-;Mn2++HPO42-=MnHPO4 。 锰系磷化膜为密集颗粒状晶粒,磷化膜主体组成;(Mn.Fe)5H2(PO4)4.4H2O,磷化膜较厚、孔隙小。 在锌钙系磷化中;Zn(NO3)2=Zn2++2NO3-;Ca(NO3)2=Ca2++2NO3-;Zn2++HPO42-=ZnHPO4 ; ca2++HPO42-=CaHPO4 。 锌钙系磷化膜为圆柱形晶体,有时有大的针状晶粒,孔隙较少,结晶细密,有较好的耐蚀性,其磷化膜主体为;Zn2Ca(PO4)2.4H2O,Zn2Fe(po4)2.4H2O,Zn3(PO4)2.4H2O。