基于OPC技术的伺服控制
opc使用举例

opc使用举例OPC(OLE for Process Control,过程控制对象链)是一种用于实现工业自动化系统中数据通信的标准。
它基于OLE(Object Linking and Embedding,对象链接与嵌入)技术,通过使用标准的COM(Component Object Model,组件对象模型)接口,实现了不同厂家的设备和系统之间的数据交换和通信。
下面是关于OPC使用的十个举例。
1. 温度监控系统:在工业生产过程中,温度是一个重要的参数。
使用OPC技术,可以将温度传感器的数据实时传输到监控系统中,实现对温度的监控和控制。
2. 液位控制系统:在储罐或管道中,液位的高低对生产过程有着重要的影响。
通过使用OPC技术,可以将液位传感器的数据传输到监控系统中,实现对液位的实时监测和控制。
3. 压力监测系统:在许多工业过程中,压力的控制是关键。
使用OPC技术,可以将压力传感器的数据传输到监控系统中,实现对压力的实时监测和控制。
4. 流量计量系统:在管道中,准确地测量流体的流量是非常重要的。
通过使用OPC技术,可以将流量计的数据传输到监控系统中,实现对流量的实时测量和控制。
5. 电力监控系统:在电力系统中,使用OPC技术可以将电能仪表的数据传输到监控系统中,实现对电力的实时监测和控制,包括电压、电流、功率等参数。
6. 环境监测系统:在工业场所或实验室中,通过使用OPC技术,可以将各种环境传感器的数据传输到监控系统中,实现对温度、湿度、气压等环境参数的实时监测和控制。
7. 设备故障诊断系统:通过使用OPC技术,可以将设备传感器的数据传输到故障诊断系统中,实时监测设备的状态,发现故障并进行诊断。
8. 能源管理系统:使用OPC技术,可以将各种能源计量仪表的数据传输到能源管理系统中,实现对能源的实时监测和管理,包括电力、燃气、水等能源。
9. 数据采集与分析系统:通过使用OPC技术,可以从各种设备和系统中采集数据,并将其传输到数据分析系统中,进行数据分析和处理,以实现优化生产过程和提高生产效率。
OPC接口技术在工业自动化系统中的应用
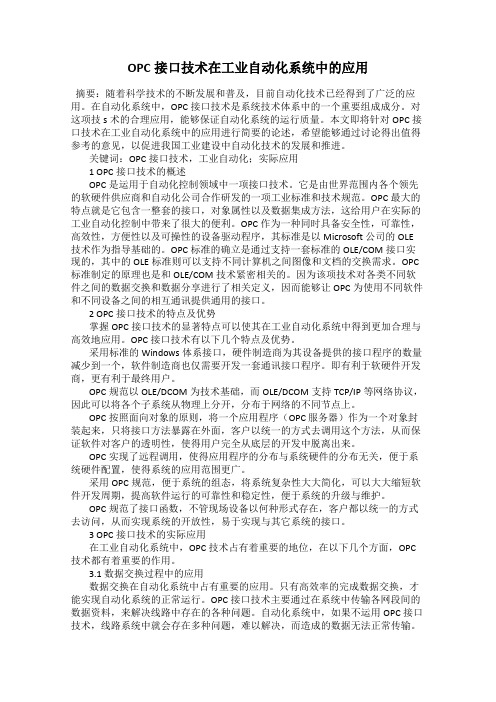
OPC接口技术在工业自动化系统中的应用摘要:随着科学技术的不断发展和普及,目前自动化技术已经得到了广泛的应用。
在自动化系统中,OPC接口技术是系统技术体系中的一个重要组成成分。
对这项技s术的合理应用,能够保证自动化系统的运行质量。
本文即将针对OPC接口技术在工业自动化系统中的应用进行简要的论述,希望能够通过讨论得出值得参考的意见,以促进我国工业建设中自动化技术的发展和推进。
关键词:OPC接口技术,工业自动化;实际应用1 OPC接口技术的概述OPC是运用于自动化控制领域中一项接口技术。
它是由世界范围内各个领先的软硬件供应商和自动化公司合作研发的一项工业标准和技术规范。
OPC最大的特点就是它包含一整套的接口,对象属性以及数据集成方法,这给用户在实际的工业自动化控制中带来了很大的便利。
OPC作为一种同时具备安全性,可靠性,高效性,方便性以及可操性的设备驱动程序,其标准是以Microsoft公司的OLE 技术作为指导基础的。
OPC标准的确立是通过支持一套标准的OLE/COM接口实现的,其中的OLE标准则可以支持不同计算机之间图像和文档的交换需求。
OPC 标准制定的原理也是和OLE/COM技术紧密相关的。
因为该项技术对各类不同软件之间的数据交换和数据分享进行了相关定义,因而能够让OPC为使用不同软件和不同设备之间的相互通讯提供通用的接口。
2 OPC接口技术的特点及优势掌握OPC接口技术的显著特点可以使其在工业自动化系统中得到更加合理与高效地应用。
OPC接口技术有以下几个特点及优势。
采用标准的Windows体系接口,硬件制造商为其设备提供的接口程序的数量减少到一个,软件制造商也仅需要开发一套通讯接口程序。
即有利于软硬件开发商,更有利于最终用户。
OPC规范以OLE/DCOM为技术基础,而OLE/DCOM支持TCP/IP等网络协议,因此可以将各个子系统从物理上分开,分布于网络的不同节点上。
OPC按照面向对象的原则,将一个应用程序(OPC 服务器)作为一个对象封装起来,只将接口方法暴露在外面,客户以统一的方式去调用这个方法,从而保证软件对客户的透明性,使得用户完全从底层的开发中脱离出来。
基于OPC技术实现WINCC与FANUC数控机床的监控系统设计
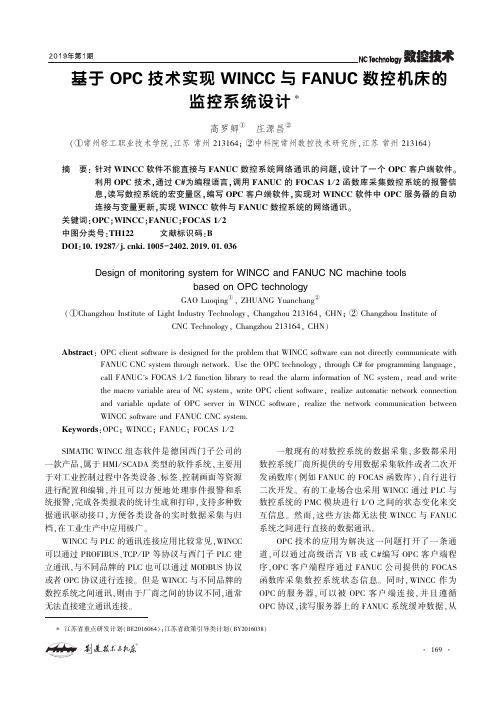
CNC Technologyꎬ Changzhou 213164ꎬ CHN)
∗ 江苏省重点研发计划( BE2016064) ꎻ江苏省政策引导类计划( BY2016038)
������ 169 ������
而实现 WINCC 与 FANUC 系统的数据通讯连接ꎮ
1 系统通讯方案
1������ 1 OPC 标准 OPC 协 议 是 基 于 Microsoft Windows 技 术ꎬ 使 用
关键词:OPCꎻWINCCꎻFANUCꎻFOCAS 1 / 2 中图分类号:TH122 文献标识码:B DOI:10������ 19287 / j������ cnki������ 1005-2402������ 2019������ 01������ 036
Design of monitoring system for WINCC and FANUC NC machine tools based on OPC technology
WINCC 与 PLC 的通讯连接应用比较常见ꎬWINCC 可以通过 PROFIBUS、TCP / IP 等协议与西门子 PLC 建 立通讯ꎬ与不同品牌的 PLC 也可以通过 MODBUS 协议 或者 OPC 协议进行连接ꎮ 但是 WINCC 与不同品牌的 数控系统之间通讯ꎬ则由于厂商之间的协议不同ꎬ通常 无法直接建立通讯连接ꎮ
系统主要通过 WINCC 后台变量管理作为 OPC 的 服务器ꎬ建立内部变量及变量名称ꎬ通过本地网络与本 机上的 OPC 客户端软件通讯ꎬOPC 客户端软件应用 FOCAS 1 / 2 函 数 库 与 FANUC 机 床 通 过 以 太 网 建 立 TCP 连接ꎬ FANUC 数 控 系 统 通 过 FOCAS 接 口ꎬ 接 受 OPC 客户端的读写操作ꎮ 如图 1 所示ꎮ
OPC原理和配置说明书

OPC原理和配置说明书OPC原理和配置说明书第一部分:OPC原理1. 概述OPC (OLE for Process Control——用于过程控制的OLE)是一个工业标准,它是许多世界领先的自动化和软、硬件公司与微软公司合作的结晶。
这个标准定义了应用Microsoft操作系统在基于PC 的客户机之间交换自动化实时数据的方法。
管理该标准的组织是OPC基金会。
该基金会的会员单位在世界范围内超过220个。
包括了世界上几乎全部的控制系统、仪器仪表和过程控制系统的主要供应商。
OPC基金会的先驱——一支由Fisher-Rosemount、Rockwell软件公司、Opto 22、Intellution和Intuitive Technology公司组成的“特别工作组”——在经过一年工作后,开发出一个基本的、可运行的OPC规范。
简化的第一阶段的标准在1996年8月发布。
随着1997年2月Microsoft公司推出Windows95支持的DCOM技术,1997年9月新成立的OPC Foundation对OPC规范进行修改,增加了数据访问等一些标准,OPC规范得到了进一步的完善。
OPC是基于Microsoft公司的Distributed Internet Application (DNA)构架和Component Object Model (COM)技术的,根据易于扩展性而设计的。
OPC规范定义了一个工业标准接口,这个标准使得COM技术适用于过程控制和制造自动化等应用领域。
OPC是以OLE/COM机制作为应用程序的通讯标准。
OLE/COM是一种客户/服务器模式,具有语言无关性、代码重用性、易于集成性等优点。
OPC规范了接口函数,不管现场设备以何种形式存在,客户都以统一的方式去访问,从而保证软件对客户的透明性,使得用户完全从低层的开发中脱离出来。
2. 传统的过程控制系统结构传统的过程控制系统是一对一的系统,任何一种HMI等上位监控软件或其它应用软件(如趋势图软件、数据报表与分析等)在使用某种硬件设备时都需要开发专用的驱动程序。
西门子828D数控机床远程监控系统的研究与应用
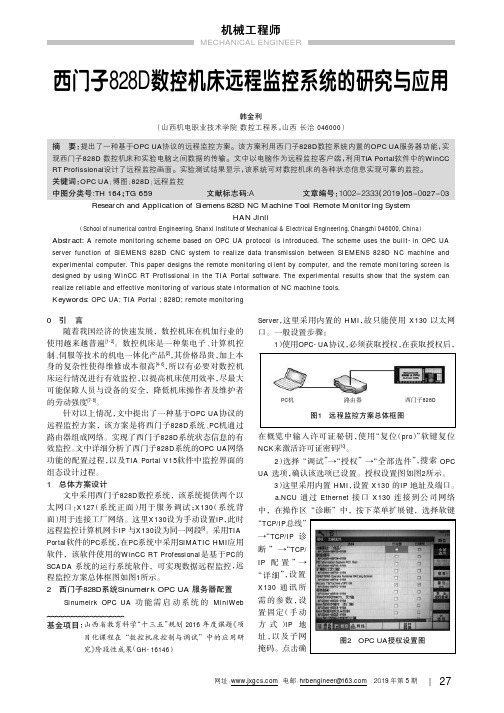
西门子828D数控机床远程监控系统的研究与应用韩金利(山西机电职业技术学院数控工程系,山西长治046000)摘要:提出了一种基于OPC UA协议的远程监控方案。
该方案利用西门子828D数控系统内置的OPC UA服务器功能,实现西门子828D数控机床和实验电脑之间数据的传输。
文中以电脑作为远程监控客户端,利用TIA Portal软件中的WinCC RT Profissional设计了远程监控画面。
实验测试结果显示,该系统可对数控机床的各种状态信息实现可靠的监控。
关键词:OPC UA;博图;828D;远程监控中图分类号:TH164;TG659文献标志码:A文章编号:1002-2333(2019)05-0027-03 Research and Application of Siemens828D NC Machine Tool Remote Monitoring SystemHAN Jinli(School of numerical control Engineering,Shanxi Institute of Mechanical&Electrical Engineering,Changzhi046000,China)Abstract:A remote monitoring scheme based on OPC UA protocol is introduced.The scheme uses the built-in OPC UA server function of SIEMENS828D CNC system to realize data transmission between SIEMENS828D NC machine and experimental computer.This paper designs the remote monitoring client by computer,and the remote monitoring screen is designed by using WinCC RT Profissional in the TIA Portal software.The experimental results show that the system can realize reliable and effective monitoring of various state information of NC machine tools.Keywords:OPC UA;TIA Portal;828D;remote monitoring0引言随着我国经济的快速发展,数控机床在机加行业的使用越来越普遍[1-2]。
《基于模糊控制的高精度伺服速度控制器的设计与实现》
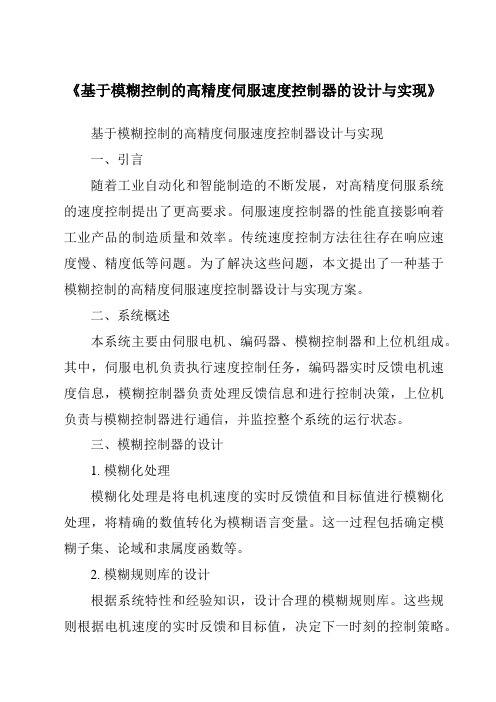
《基于模糊控制的高精度伺服速度控制器的设计与实现》基于模糊控制的高精度伺服速度控制器设计与实现一、引言随着工业自动化和智能制造的不断发展,对高精度伺服系统的速度控制提出了更高要求。
伺服速度控制器的性能直接影响着工业产品的制造质量和效率。
传统速度控制方法往往存在响应速度慢、精度低等问题。
为了解决这些问题,本文提出了一种基于模糊控制的高精度伺服速度控制器设计与实现方案。
二、系统概述本系统主要由伺服电机、编码器、模糊控制器和上位机组成。
其中,伺服电机负责执行速度控制任务,编码器实时反馈电机速度信息,模糊控制器负责处理反馈信息和进行控制决策,上位机负责与模糊控制器进行通信,并监控整个系统的运行状态。
三、模糊控制器的设计1. 模糊化处理模糊化处理是将电机速度的实时反馈值和目标值进行模糊化处理,将精确的数值转化为模糊语言变量。
这一过程包括确定模糊子集、论域和隶属度函数等。
2. 模糊规则库的设计根据系统特性和经验知识,设计合理的模糊规则库。
这些规则根据电机速度的实时反馈和目标值,决定下一时刻的控制策略。
3. 模糊推理机的实现模糊推理机是模糊控制器的核心部分,根据模糊规则库和实时反馈信息,进行模糊推理,得出下一时刻的控制决策。
4. 解模糊化处理解模糊化处理是将模糊推理结果转化为精确的控制量,以驱动伺服电机执行相应的动作。
四、伺服速度控制器的实现1. 硬件实现伺服速度控制器的硬件部分主要包括微处理器、编码器接口、电机驱动器等。
微处理器负责运行模糊控制器程序,编码器接口负责实时获取电机速度信息,电机驱动器根据控制决策驱动伺服电机执行相应的动作。
2. 软件实现软件部分主要包括模糊控制算法的实现、与上位机的通信等。
在微处理器上运行模糊控制算法,实时处理编码器反馈的电机速度信息,并根据模糊推理结果输出相应的控制量。
同时,与上位机进行通信,接收上位机的指令和监控系统的运行状态。
五、实验结果与分析通过实验验证了基于模糊控制的高精度伺服速度控制器的性能。
基于EtherCAT总线的伺服运动监控系统设计

服驱 动器测试监控 系统 。实验 结果表 明 , 系统 能够满足监控 系统大数据量数 传 、 该 高实时处理以及抗 干扰 能力强的要 求。
通 信 周 期 由 主 站 发Байду номын сангаас起 ,主 站 发 出 下 行 数 据 帧 遍 历 从 站 设 备 网
的物 理 特 性 , 导致 了监 控 网 络 监 控 距 离 近 、 干扰 能 力 差 等 各 抗 种 问题 。德 国 倍 福 公 司 开 发 的 实 时 以太 网技 术 Eh rA , teC T 基
fr o t luo t n eh oo y adte eeo met e o ftmatr l e tt nis de .An wtp sro r e n. o n oa tma o cn lg ) n v l c r i t h d p n t d i s /a a o u i mh o s e s v s i s t d e e f ev i r i y o d v mo tt g ytm a zd t itcn lg e eli prt gss m tni T ( at t s n pa om.w i o n s ir l e h t seh ooyo t a t o eai t e es nR x r li e e i ) lt r i s e se i wi h n h R —me n ye x o e me x n o f hc h ibsdo e n o ci c r.E pr narsl o ta timo i r gss m no sh d at e fa e u tyo s ae nt d ws rht t e x e metleuts w t s nti t ejy e vna s l g ai h Wi a eu i sh h h on y e t a g o r qn t f
实现三菱PLC触摸屏控制伺服电机完整版

实现三菱P L C触摸屏控制伺服电机HEN system office room 【HEN16H-HENS2AHENS8Q8-HENH1688】实现三菱PLC触摸屏控制伺服电机在plc行业中一直坚持高规格、高性能,得到很多技术人员的青睐,同时,在与伺服电机中也有很好的应用,下面以作为控制元件,GT1155-QFBD-C作为操作元件直接控制三菱伺服电机的具体程序设计伺服电机又称执行电机,它是控制电机的一种。
它是一种用电脉冲信号进行控制的,并将脉冲信号转变成相应的角位移或直线位移和角速度的执行元件。
根据控制对象的不同,由伺服电机组成的伺服系统一般有三种基本控制方式,即位置控制、速度控制、力矩控制。
本系统我们采用位置控制。
PLC在自动化控制领域中,应用十分广泛。
尤其是近几年PLC在处理速度,指令及容量、单轴控制方面得到飞速的发展,使得PLC在控制伺服电机方面也变得简单易行。
1控制系统中元件的选型的选型因为伺服电机的位移量与输入脉冲个数成正比,伺服电机的转速与脉冲频率成正比,所以我们需要对电机的脉冲个数和脉冲频率进行精确控制。
且由于伺服电机具有无累计误差、跟踪性能好的优点,伺服电机的控制主要采用开环数字控制系统,通常在使用时要搭配伺服驱动器进行控制,而伺服电机驱动器采用了大规模集成电路,具有高抗干扰性及快速的响应性。
在使用伺服驱动器时,往往需要较高频率的脉冲,所以就要求所使用的PLC能产生高频率脉冲。
三菱公司的FX3U晶体管输出的PLC可以进行6点同时100 kHz高速计数及3轴独立100 kHz的定位功能,并且可以通过基本指令μs、PCMIX值实现了以倍的高速度,完全满足了我们控制伺服电机的要求,所以我们选用FX3U-48MT-ES-A型PLC。
伺服电机的选型在选择伺服电机和驱动器时,只需要知道电机驱动负载的转距要求及安装方式即可,我们选择额定转距为 N·m,额定转速为3 000 r/min,每转为131 072 p/rev分辨率的三菱公司HF-KE73W1-S100伺服电机,与之配套使用的驱动器我们选用MR-E-70A-KH003伺服驱动器。
- 1、下载文档前请自行甄别文档内容的完整性,平台不提供额外的编辑、内容补充、找答案等附加服务。
- 2、"仅部分预览"的文档,不可在线预览部分如存在完整性等问题,可反馈申请退款(可完整预览的文档不适用该条件!)。
- 3、如文档侵犯您的权益,请联系客服反馈,我们会尽快为您处理(人工客服工作时间:9:00-18:30)。
上海交通大学硕士学位论文基于OPC技术的伺服控制姓名:姜尚坤申请学位级别:硕士专业:控制理论与控制工程指导教师:陈坚20060101上海交通大学工学硕士学位论文基于OPC技术的伺服控制摘要本论文是基于罗克韦尔自动化的Kinetix系统为对象,开发图形识别程序,OPC客户程序以及伺服控制程序从而实现对两轴绘图工具的精确控制。
本论文首先实现对图形坐标进行读取的:对于实时绘制图形通过用户选择的控件以及用户鼠标的移动来确定,而对于预先画好的图形则通过边缘检测的方法来读取图形的坐标。
然后在论文中通过编写的OPC客户程序,实现将系统读取到的坐标依次写到伺服控制器中。
本文最后实现在Kinetix系统上,根据通过OPC通讯传送来的用户设定的坐标值,编写伺服控制程序来实现对两轴绘图仪的驱动,从而绘制出用户要求的画面。
关键词Kinetix,边缘检测,OPC,现场总线- -VI上海交通大学工学硕士学位论文Servo Control Based on OPC TecnologyABSTRACTThis paper takes the Kinetix system of Rockwell Automation as Object. It mainly introduce how to develop the identification of graphics, OPC client program and Servo Control program to realize the accurate control of two axis drawing device.First, the paper works out the problem which is how to identify the graphics and how to transfer them to coordinates: For the real-time graphics, we get the coordinates by the controls used by users and the movement of mouse; for the completed graphics, we get the coordinates by edge detection.Secondly, the paper develops a OPC client program to communicate with RSLinx OPC Server so that the system can transfer the coordinates from computer to the sevo-controller.Finally, the paper develops a PLC program to drive the two sevo motors to realize the accurate control based on the coordinates transferred from the Computer by OPC technology.Keywords Kinetix, Edge Detection, OPC, Field Bus- -VII上海交通大学工学硕士学位论文上海交通大学学位论文原创性声明本人郑重声明:所呈交的学位论文,是本人在导师的指导下,独立进行研究工作所取得的成果。
除文中已经注明引用的内容外,本论文不包含任何其他个人或集体已经发表或撰写过的作品成果。
对本文的研究做出重要贡献的个人和集体,均已在文中以明确方式标明。
本人完全意识到本声明的法律结果由本人承担。
学位论文作者签名:姜尚坤日期: 2006年 1 月 20日- -III上海交通大学工学硕士学位论文上海交通大学学位论文版权使用授权书本学位论文作者完全了解学校有关保留、使用学位论文的规定,同意学校保留并向国家有关部门或机构送交论文的复印件和电子版,允许论文被查阅和借阅。
本人授权上海交通大学可以将本学位论文的全部或部分内容编入有关数据库进行检索,可以采用影印、缩印或扫描等复制手段保存和汇编本学位论文。
保密□,在年解密后适用本授权书。
本学位论文属于不保密□。
(请在以上方框内打“√”)学位论文作者签名:姜尚坤指导教师签名:陈坚日期: 2006年 1月 20日日期: 2006年 1月20日- -IV第1章绪论1.1现代工业控制技术的发展与现状工业控制自动化技术是一种综合运用控制理论、仪器仪表、传动机械、计算机和网络信息技术的科学技术。
它在工业生产过程中实现检测、控制、优化、调度、管理和决策,达到提高生产效率和产品质量、降低成本消耗、确保安全保护等经济和技术的要求。
工业控制自动化技术主要包括工业自动化软件、硬件和系统集成三大部分,并依赖这三个方面技术的快速发展而不断地取得惊人的成就,同时又因为自动化技术在国民经济中的重要地位,对自动化技术发展的不断要求同时促进了计算机软件技术、硬件技术和系统工程以及计算机通信和网络技术的快速发展。
纵贯工业控制自动化技术的发展历史,我们可以发现在20世界40年代前后,大多数工业生产过程还处于手工操作阶段,因而生产效率十分低下。
而在40年代后,工业控制自动化技术的发展速度加快。
50年代前后,基地式仪表和单元组合式仪表被普遍采用,在过程控制领域,控制的参数主要是液位、温度、压力、流量,工业控制理论主要是利用经典控制中的频率法和根轨迹法,用于解决单输入单输出系统的定值控制和综合分析。
从60年代开始,得益于电子技术的发展,仪表采用气动和电动结合,计算机也开始应用于工业控制领域,同时控制算法中复杂算法例如前馈控制和选择控制在工业中取得了很好得应用,同时现代控制理论也开始产生并不断发展[1]。
到了70年代中期,因大规模集成电路技术和微处理器技术的发展,集散控制系统DCS开始出现,标志着一个新的工业控制时代的开始。
在DCS系统中,以往集中的体系结构的有效性问题得到了很好的解决:一方面,它将控制分散在几个较小型的控制器中,这样一个故障只会影响这个系统的一部分;另一方面,可以更好地组织组态,用户可以分开管理针对各个独立单元地组态和控制器。
一个DCS系统通常有多达4层地不同网络,每层都有其不同地技术,即:设备、I/O子系统、控制器以及商务和全厂地集成。
所有这些硬件及网络地层次使系统变得相当复杂而且昂贵[3][4][5]。
另外,DCS系统虽然被冠名为“分散”的,但按照今天地标志来衡量,应该仍被认为是集中的。
于是,随着数字通信技术的进一步发展,一种新的体系结构FCS(Field Control System)逐渐被广泛地应用到工业控制中。
这种基于现场设备能力的新型体系结构已不再以控制器为核心,不再把每台现场设备看作外设。
可以说FCS的体系结构从DCS的概念演变而来,并且在DCS概念的基础上更进一步,其结果就是系统更加分散,因而降低了在发生故障时系统的脆弱性。
就目前而言,工业控制自动化技术正朝着工厂综合自动化的方向发展,所谓综合自动化,就是指在自动化技术、计算机控制技术、网络通信技术和各种加工技术的基础上,从整个企业的全局出发,实现从车间级到企业管理级的数据透明流动。
车间级的实时信息数据可以传送到企业的商务系统中,由商务系统实现全局的优化、调度和设备管理,然后将控制信息传送到工厂车间级,从而实现整个企业的优化和管理,提高企业的生产效率,增强企业的灵活性和竞争力[2]。
1.2OPC技术在上一节我们提到了,DCS系统是当前工业控制领域应用比较广泛的控制系统,但是我们应该清醒地认识到它们都存在着一些共同的自身难以逾越的局限性。
首先,缺乏互操作性,不同的制造商都独立地创建了各自地协议,因而很多时候只有同一制造商地产品可以一起工作;其次,对于用户来说一家公司的产品往往无法满足其自身的需求。
在这种情况下,人们开始在工控软件的开发上进行相关研发,以期上述问题得到更好地解决。
而在工控软件开发方面,对于早期的工业现场监控系统,为了实现不同的硬件和软件之间的数据交换,监控软件必须提供每一种相连控制设备的通讯驱动程序,目前流行的现场控制设备种类繁多,且产品不断升级换代,往往给监控软件的开发带来了巨大的经济压力和工作负担。
硬件开发商和软件开发商急切需要一种具有高效性、可靠性、开放性、可互操作性的即插即用的设备驱动程序,在这样的大背景下,OPC工业标准应运而生。
OPC(OLE for Process Control)是近年来国际上新推出的与厂商无关的软件数据交换接口标准和规程。
其基本思想是:每个硬件生产厂商为其设备开发一个通用的数据接口供其它系统读写信息〔作为OPC服务器),应用软件也通过OPC 接口来读写硬件设备的信息(作为OPC客户)[6]。
早期的OPC标准是由提供工业制造软件的5家公司所组成的OPC特别工作小组开发的。
Fisher-Rosement, Intellution, Rockwell Software, In tuitive Technology以及Opto22早在1995年开发了原始的OPC标准,1996年9月,OPC 基金会(OPC Foundation, OPC-F )成立,开始了全球范围内的活动。
到目前为止,OPC基金会成员己经超过400家,涵盖了世界上绝大部分的工控设备厂商。
将OPC技术应用于监控软件的设计,那么软件的数据来源将不再是通过专用硬件驱动程序传递的过程数据,而是具有通用数据接口的OPC服务器,从而实现了软件与硬件在异构环境下的开放、高效通信,从而摆脱了对生产厂商的依赖,提高了控制系统的有效性和灵活性。
1.3伺服控制技术伺服控制技术是自动化学科中与产业部门族系最紧密,服务最广泛的一个分支。
随着控制技术的发展,伺服系统的性能也得到了不断地提高。
随着大规模集成电路的飞速发展,以及计算机(特别是微处理器)在伺服控制系统中的普遍应用,近年来,构成伺服控制系统的重要组成部分——伺服元件发生了巨大的变革,并且向着便于计算机控制的方向发展。
为了提高控制精度,便于计算机连接,位置、速度等测量元件趋于数字化、集成化。
即使是模拟式的伺服元件也在向高精度、低噪声的方向发展。
同样随着当前现场总线技术的发展,基于现场总线的伺服控制也逐渐成为伺服控制领域的一个热点。
一方面保证了伺服控制的实时性和准确性,另一方面,通过工业现场总线可以将整个控制过程的数据及组态信息在整个控制网络上共享,从而有利于系统的优化控制,提高生产效率。
基于上述两种要求,基于现场总线的伺服控制系统得以迅速发展起来,其中,以罗克韦尔自动化公司推出的Kinetix系统最为显著,它集运动控制与顺序控制于一身,通过先进的SERCOS接口与高性能的数字伺服驱动器相连,既保证了伺服控制的实时性和准确性,同时也为整个系统提供了完美的网络服务,使得控制信息可以在系统内按用户的需求流动。